Video:Machine Shop erstellt Roboter-Bearbeitungszelle, bevor es Arbeit dafür gab
Diese Roboter-Bearbeitungszelle produziert Rohre für ein Kraftstoffsystem für Kraftfahrzeuge. Entdecken Sie, was diese Zelle bei Custom Tool in Cookeville, Tennessee, umfasst, einschließlich Werkstückhalterung, Teilespender, Sicherheitsscanner und Teilesammler.
Haben Sie Ausrüstung gekauft, in dem Wissen, dass sie irgendwann sinnvoll eingesetzt werden würde, aber zu diesem Zeitpunkt gab es keinen anderen Grund, sie zu kaufen, als dass es etwas war, das Sie beäugt hatten? Ich hatte die Gelegenheit, eine Maschinenwerkstatt zu besuchen, die diese Frage mit Ja beantworten kann und die Investition keinesfalls bereut. Tatsächlich konnte der Durchsatz für einen hochvolumigen Bearbeitungsauftrag gesteigert werden, und das Automatisierungsteam hat eine neue Fähigkeit erlernt, von der es glaubt, dass sie für viele zukünftige automatisierte Maschinenbeschickungsprojekte von Vorteil sein wird.
Im Jahr 2018 war das Management von Custom Tool Inc. (Cookeville, Tennessee) neugierig auf eine Technologie, die den Teammitgliedern fremd war. Obwohl die Werkstatt mit einer automatisierten Schweißzelle der Automatisierung nicht fremd war, hatte sie keine Erfahrung mit der Selbstintegration eines Maschinenbeschickungsroboters. Aus diesem Grund kaufte das Team mit der alleinigen Absicht, etwas über die Roboterintegration für zukünftige Jobs zu lernen, bei denen Automatisierung von Vorteil sein könnte, einen Roboterarm und nahm sich Zeit, um sich damit vertraut zu machen, wie man ihn programmiert, Endeffektorkomponenten hinzufügt und ihn mit einer Maschine verbindet Werkzeug.
Die Prognose des Teams erwies sich nicht nur als klug, sondern auch als zeitgemäß. Kurz nach der Investition in den Roboter erhielt die Maschinenwerkstatt einen Auftrag, von dem das Team glaubte, dass er von der Automatisierung profitieren würde. Die Vision des Managements wurde schließlich bestätigt, als dieses Automatisierungsprojekt mehr als effizient war und mehr Konsistenz, Zeiteinsparungen, eine Steigerung des Durchsatzes und die Möglichkeit bot, Bediener an anderen Werkzeugmaschinen in der Fertigung einzusetzen, wo das menschliche Gehirn erforderlich ist.
War es Glück oder Schicksal?
Einige mögen sagen, dass die Details dieser Geschichte so gut zusammenpassten, dass der Laden „Glück“ haben muss. Allerdings schwingt hier das Zitat „Du machst dein eigenes Glück“ mit. Bob Young, Vizepräsident von Custom Tool, und sein Bruder und Präsident des Unternehmens, Gillen Young, halten Ausschau nach Automatisierungsmöglichkeiten. Daher ist es zu weit hergeholt zu sagen, dass diese Geschichte, die ich gleich erzählen werde, Glück war. Aber man könnte schlussfolgern, dass die Sterne für den Shop gut stehen, auch wenn einige Hindernisse auf dem Weg der Roboterselbstintegration auf das Team warteten.
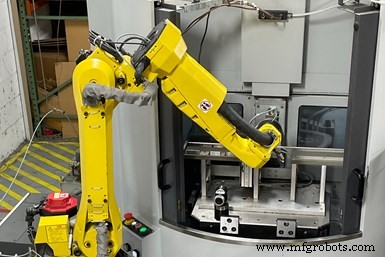
Diese Roboter-Bearbeitungszelle besteht aus einem sechsachsigen FANUC M-10-Roboter, der einen Hardinge Bridgeport V480 VMC bedient. Die Automatisierung entfernt die meisten Elemente der menschlichen Interaktion, obwohl eine gewisse Überwachung durch den Bediener erforderlich ist. Dieses Setup gibt Bedienern die Möglichkeit, andere notwendige Aufgaben in der Werkstatt von Custom Tool zu erledigen.
Obwohl Custom Tool vor 2018 keinen Roboter selbst integriert hatte, begann das Unternehmen, das hauptsächlich die Luft- und Raumfahrt-, Verteidigungs-, Medizin- und Automobilmärkte bedient, mit der Automatisierung, als es 2008 einen Stangenlader zu einem bestehenden CNC-Drehzentrum in seiner Fertigung hinzufügte Seitdem glaubt das Unternehmen fest an die Lights-out-Bearbeitung auf vielen seiner Maschinen. Darüber hinaus
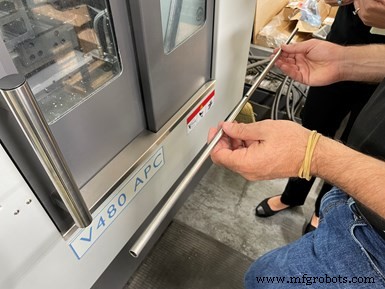
Das Automatisierungsteam für benutzerdefinierte Tools muss flexibel bleiben, da es erfährt, dass sich Teilebestellspezifikationen schnell ändern können. Die Roboter-Maschinenzelle produzierte ursprünglich 27 Zoll lange Rohre mit einer 5,5-mm-Bohrung auf einer Seite, aber dann änderte der Kunde seine Bestellung auf ein 34-Zoll-Rohr. Außerdem wurde dem Geschäft gesagt, dass die Löcher keine Grate haben könnten, nachdem es bereits mit der Fertigung der Bestellung begonnen hatte.
hat einige Messroutinen für mehrere Teile, die über Nacht bearbeitet wurden, sowie die Datenerfassung (siehe Seitenleiste) für seine selbstentwickelte Planungsstrategie für Produktionsprotokolle automatisiert. Obwohl der Großteil der Arbeit des Shops Teile mit einem Durchmesser von 2 Zoll und kleiner umfasst, verzweigt er sich manchmal, um die Bedürfnisse eines Kunden zu erfüllen. Zum Beispiel besitzt es auch eine Roboterschweißzelle, die einmal gekauft wurde, um einen bestimmten Reparaturauftrag für einen Kunden auszuführen.
Das nächste Automatisierungsprojekt bot sich an, als die Werkstatt 2018 einen Auftrag von einem Zulieferer eines Tier-1-Automobilunternehmens zum Bohren von Edelstahlrohren für ein Kraftstoffsystem für Kraftfahrzeuge erhielt. Bob Young und das Automatisierungsteam unter der Leitung des Fertigungsleiters des Unternehmens und ein 2020 Produktionsbearbeitung Der aufstrebende Leader Clay Adcock entschied, dass der Roboter, den sie Anfang des Jahres gekauft hatten, nur um zu lernen, wie man ihn integriert, an ein vertikales Bearbeitungszentrum angeschlossen werden könnte, um eine Zelle zu schaffen, die perfekt für den hochvolumigen Teileauftrag wäre, den sie erhalten hatten. Das Team bestellte einen Hardinge Bridgeport V480 APC VMC mit einem Palettenwechsler, der mit dem vorab gekauften FANUC M-10-Roboter gekoppelt werden sollte. Der Roboter, so dachten sie, würde sich gut zum Be- und Entladen der Werkstücke für diese Anwendung eignen, die Konsistenz erfordert.
Obwohl die Idee dieser Automatisierungszelle die Lösung zu sein schien, war das Erlernen der Einzelheiten der Zelle kein schneller oder einfacher Prozess. Die Lernkurve hatte für das Team gerade erst begonnen, gefolgt von Trial and Error. Das Ergebnis war die Mühe jedoch wert; Das Management hätte es nicht anders gemacht.
Selbstintegrationsprozess und Herausforderungen
Nach der Lieferung des VMC benötigte das Automatisierungsteam von Custom Tool etwa acht Monate, um den Integrationsprozess mit dem FANUC-Roboter zu verstehen und die Zelle so zum Laufen zu bringen, wie es erforderlich war, um die Teileanforderungen des Kunden zu erfüllen. Aber während der Lernphase musste das Unternehmen noch den Auftrag erfüllen, der darin bestand, ein 5,5-mm-Loch auf einer Seite von Edelstahlrohren mit einem Durchmesser von 3/8 Zoll, einer Länge von 27 und 34 Zoll und einem Volumen von bis zu 250.000 zu bohren Teile pro Jahr.
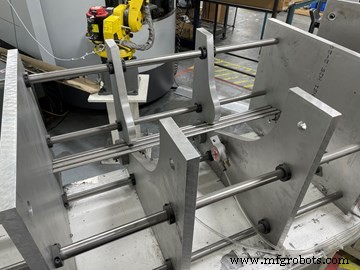
Das System benötigt eine präzise Teilepräsentation von „ Zahnstocherspender“, den Custom Tool entworfen und entwickelt hat. Der Behälter verfügt über Sensoren, die der Steuerung mitteilen, wenn der Behälter fast leer ist.
Daher be- und entluden die Bediener das VMC während dieser Zeit manuell, was die Arbeit erledigte, aber nicht so effizient war, wie sich die Automatisierung später herausstellte. Nachdem das Selbstintegrationsprojekt abgeschlossen war und die Automatisierungszelle betriebsbereit war, stellte das Management eine Steigerung der Konsistenz und eine 20 %ige Steigerung des Durchsatzes fest.
„Wir verfolgen viele Zahlen, nicht weil wir versuchen, Big Brother zu spielen, sondern weil wir nur versuchen, von diesem Standpunkt aus zu lernen“, erklärt Young. „Und wir wissen die harte Arbeit zu schätzen, die der Bediener am vorderen Ende dieser Maschinen leistet, aber es ist körperliche Arbeit. Selbst nach bestem Bemühen konnten wir immer noch nicht die Konsistenz erkennen, die wir durch den Automatisierungsaspekt erzielen konnten.“ Er beschreibt die neu entdeckte Konsistenz, die die Automatisierung „wie am Schnürchen“ bereitstellt.
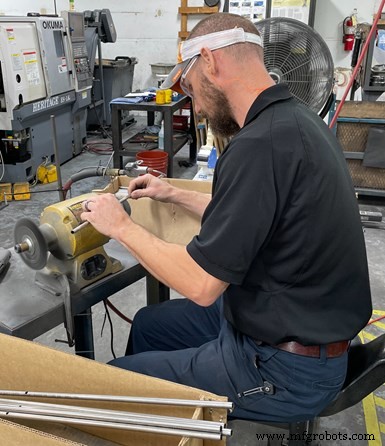
Bediener Andy Paul entgratet Löcher in Edelstahlrohren nach dem Verlassen der Roboter-Bearbeitungszelle. Das Teil wird in einem Kraftfahrzeug-Kraftstoffsystem verwendet.
Das System benötigt eine präzise Teilepräsentation von dem, was Young liebevoll als „Zahnstocherspender“ bezeichnet hat. Dieser Aluminiumbehälter, der vom Custom Tool-Team entworfen und hergestellt wurde, richtet die Rohre aus, um das Aufnehmen für den Roboter zu erleichtern. Der Roboter lädt dann Rohre auf eine Vorrichtung auf der Palette außerhalb der Bearbeitungszone des VMC, während das VMC die befestigten Rohre auf der anderen Palette bohrt.
Sobald alle Rohre auf der Palette in der Maschine gebohrt sind, dreht sich der Palettenwechsler, um fertige Teile aus der Maschine und neue Werkstücke in die Maschine zu bringen. Der Roboter nimmt dann jedes fertiggestellte Teil, entfernt es aus der Halterung und legt es in einen Materialbehälter, während die Maschine mit dem Bohren der frischen Werkstücke beginnt. Von dort aus wird jedes fertiggestellte Teil inspiziert und entgratet und dann zum Verpacken transportiert.
Obwohl die Aufgaben des Roboters einfach klingen, sagte Young, sein Team habe mehrere große Hürden für eine ordnungsgemäße Integration gefunden:Spannvorrichtung, Teilepräsentation für den Roboter und Programmierung der SPS der Zelle.
Diese Hürden können und wurden überwunden, aber es kann hilfreich sein, die Herausforderungen im Voraus zu kennen. Er sagt, dass die kleinste Bewegung einer Vorrichtung dazu führen kann, dass der Roboter ein Teil nicht richtig greift. Auch die Teilepräsentation für den Roboter ist wichtig, aber nicht einfach genau so zu machen, wie es der Roboter verlangt. Jedes kleine Detail des Prozesses muss berücksichtigt werden, erklärt er. Zum Beispiel, wie der Roboter das Material bekommt und was der Roboter dann damit macht, wenn es fertig ist.
Für die SPS erklärt Young, dass der Kauf der Software und das Verständnis ihrer Funktionsweise ebenfalls ein großes Unterfangen sind.
Auswahl der richtigen Ausrüstung
Als Young mit der Suche nach dem End-of-Arm-Werkzeug begann, entschieden er und sein Team sich für ein elektrisch betätigtes Greifsystem von Schunk Inc.
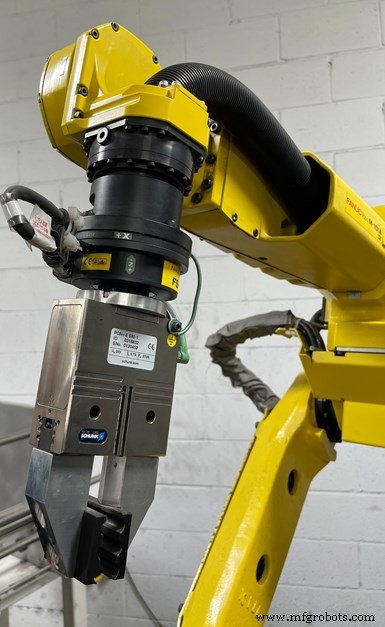
Custom Tool verwendet ein elektrisch betätigtes Greifsystem von Schunk Inc. gegenüber einem pneumatischen. Obwohl jeder Typ Vor- und Nachteile hat, glaubt Bob Young, dass die elektrische Version die klügere Wahl für den Laden war.
gegenüber einem pneumatischen. Obwohl jeder Typ Vor- und Nachteile hat, glaubt er, dass die elektrische Version die klügere Wahl für Custom Tool war. Die Tatsache, dass ein elektrisch betätigtes System weniger Zubehör benötigt, war attraktiv, da sein Ziel darin bestand, die Konfiguration so einfach wie möglich zu halten. Zum Beispiel beschreibt er den FANUC M-10 mit elektrisch betätigtem Greifen als „sauber“ mit nur wenigen Kabeln, während ein pneumatisches System eine Luftleitung benötigt, was die Konfiguration erschwert.
Der M-10 ist ein sechsachsiger Roboter, der speziell für kleine Arbeitszellen entwickelt wurde und bis zu 12 kg heben kann. Young hat den Roboter mit einem Kraftsensor gekauft, den er sehr empfiehlt. Kraftsensoren ermöglichen es Robotern, auf den Endeffektor ausgeübte Kräfte und Drehmomente zu erkennen. Dadurch erhält es einen fast menschlichen Tastsinn. Überraschend für Young und sein Team war der Kraftsensor nicht schwer einzurichten und zu verwenden.
„Wir dachten, der Kraftsensor wäre einer der herausfordernderen Aspekte, aber es war ziemlich einfach“, sagt er. „Manchmal müssen wir die Barriere überwinden, von der wir denken, dass sie nicht funktionieren wird.“
Nach dem Kauf des Roboters und dem Auftragseingang ging es an die Suche nach der passenden Werkzeugmaschine für den Auftrag. Der Hardinge Bridgeport V480 APC VMC war für Young wegen seines Palettenwechselsystems attraktiv, das die Spindelverfügbarkeit maximiert.
„Es war nicht die Größe der Maschine, die die treibende Kraft war, weil wir meistens Teile herstellen, die man in der Hand halten kann“, erklärt Young. „Es war die Fähigkeit der Maschine, weiterhin zu takten, zu indexieren und zu verarbeiten. Es macht einen sehr vorhersehbaren Prozess und eignet sich hervorragend für die Zeitplanung und Planung.“
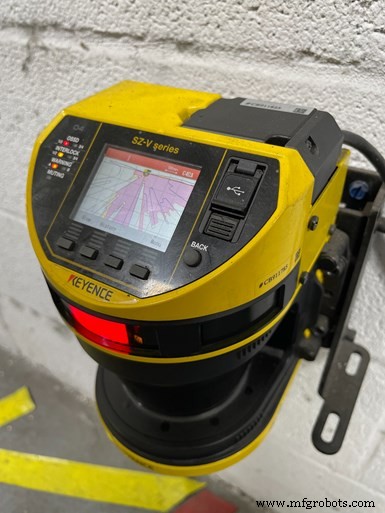
Die Bereichsscanner der Keyence SZ-V-Serie bieten ein 27,56-Fuß. Schutzzone um die Roboter-Bearbeitungszelle bei Custom Tool. Es bietet eine beeindruckende Empfindlichkeit, die dafür bekannt ist, eine Motte zu erkennen, die durch den Bereich fliegt, der den Roboter zum Abschalten veranlasst hat.
Nach der Integration der Roboter-/Werkzeugmaschinenzelle wurde der Roboter zunächst eingesperrt. Als das Automatisierungsteam jedoch erkannte, dass es bessere Optionen für Benutzerfreundlichkeit und Maschinenzugang gab, entschied es sich nach etwa einem Jahr der Verwendung des Käfigs, als Alternative in einen Bereichsscanner der SZ-V-Serie von Keyence zu investieren.
Young erklärt, dass der Scanner eine ihrer besten Anschaffungen war, weil er Platz und Zeit spart, die zum Ausschalten des Roboters, zum Öffnen und Schließen der Käfigtür benötigt wurden, und die Bearbeitungsumgebung im Allgemeinen verbessert.
Auch die Empfindlichkeit des Scanners beeindruckt das Team. Young war erstaunt, als er Zeuge wurde, wie der Roboter einen Tag, nachdem eine Motte in den Bereich des Scanners geflogen war, abgeschaltet wurde.
Die Young-Brüder wissen auch, wie wichtig es ist, Daten von ihren Werkzeugmaschinen zu sammeln. Als sie diese Zelle implementierten, implementierten sie also auch MT Connect als Schnittstelle für das Sammeln von Informationen daraus, die in ihr Produktionsprotokoll-Planungssystem eingespeist wurden.
Vorteile der Selbstintegration
Aufgrund der Zeit, der Fähigkeiten und der Arbeit, die für die Selbstintegration einer Roboterzelle erforderlich sind, könnte man sich fragen, warum Custom Tool den „harten“ Weg gewählt hat, anstatt einen Integrator für diese herausfordernde Arbeit einzustellen. Young beschreibt das Engagement für die interne Integration als Investition in zukünftige Projekte und als Möglichkeit, Bearbeitungsintelligenz zu erlangen. Er strebt nicht nur danach, dass das Team in der Lage ist, mehr Roboter für zukünftige Jobs in der Fertigung selbst zu integrieren, sondern er sagt, dass ihr Do-it-yourself-Ansatz sie dazu gezwungen hat, sich mit den Maschinen und Robotern vertraut zu machen und zu verstehen, was befindet sich im Bedienfeld, einschließlich M-Codes und wie alle Komponenten zusammen funktionieren.
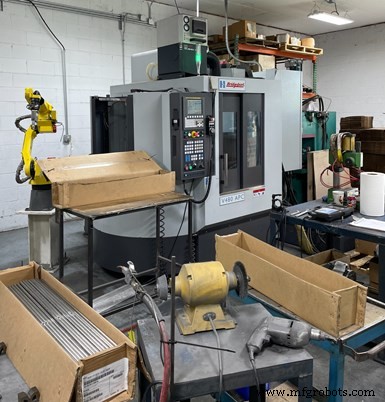
Obwohl bei einigen Geräten von Custom Tool das Licht ausfällt , entschied Young, diese Roboter-Bearbeitungszelle nicht auszuschalten. Denn der Auftrag wird mit dem Material des Kunden abgewickelt. Wenn also beim Lichtausfall ein Fehler auftritt, der Ausschuss verursacht, riskiert das Unternehmen, das Material des Kunden zu verschwenden.
Wenn sich das Unternehmen alternativ für die Zusammenarbeit mit einem Roboterintegrator entscheidet, gibt es immer noch eine Lernkurve, erklärt Young. Zusammen mit Überlegungen zur Integration, an denen das Management beteiligt wäre, sowie den Mühen und Herausforderungen, sich mit der Ausrüstung vertraut zu machen, ist es nach der Genehmigung der Integration die Aufgabe des Shops, die Zelle am Laufen zu halten. Daher dachten sie, dass es ihre Energie wert war, sich Zeit zu nehmen und sich selbst zu integrieren, um alle Systeme in- und auswendig zu kennen. Diese Option spart Geld bei der Einstellung eines externen Integrators.
Da Custom Tool weiter wächst und in Investitionsgüter investiert, kauft Young nur Werkzeugmaschinen, die mit einer Roboterschnittstelle ausgestattet sind, um die Integration eines Roboters zu erleichtern, wenn sich wieder die Gelegenheit bietet.
Auf Wachstum vorbereitet
Mit der vollen Absicht, das Automatisierungssegment von Custom Tool auszubauen, ist Young jetzt der Meinung, dass sein Unternehmen aufgrund seiner jüngsten Investitionen in Maschinen mit Roboterschnittstellen bereit ist, mehr dieser Jobs zu übernehmen. „Wenn die Maschine bereit ist, müssen wir nur noch den Roboter programmieren und die Materialhandhabung herausfinden“, sagt Young. „Wir sind bereits für eine Integration gerüstet.“ Er fügt hinzu, dass er in seinem Geschäft nie weiß, welcher Job als nächstes kommt.
Eine Automatisierungsmentalität bedeutet, dass das Unternehmen die Automatisierung immer als Möglichkeit für jeden Auftrag betrachtet. Tatsächlich sagt Young, dass er fest davon ausgeht, dass er in 12 Monaten über ein weiteres Integrationsprojekt sprechen wird, wenn sich die Jobtrends, die er jetzt sieht, fortsetzen.
Da sich die selbstintegrierte Zelle inzwischen gut etabliert hat, kann das Unternehmen sie 14 bis 16 Stunden am Tag, fünf Tage die Woche betreiben, wobei nur ein leichter Operator die Aufgabe überwacht. Wird das Team sein Ziel erreichen, die Zelle täglich 18 bis 20 Stunden zu betreiben? Das ist abhängig von der Materialverfügbarkeit beim Kunden.
Custom Tool Inc. | 931-432-6609 | customtoolinc.com
Harding Inc. | 800-843-8801 | hardinge.com
FANUC Amerika | 800-477-6268 | fanucamerica.com
Automatisiertes Datenerfassungssystem erstellt Informationen alle 20 Minuten
Das automatisierte Datenerfassungs- und Berichtssystem von Custom Tool, das von Gillen Young, dem Präsidenten des Unternehmens, entwickelt wurde, verwendet eine webbasierte, Industrial Internet of Things (IIoT)-Plattform, um Daten von Maschinen abzurufen, die über Agenten für das Open-Source-Kommunikationsprotokoll MTConnect verfügen Enterprise Resource Planning (ERP)-Software JobBoss des Unternehmens. Die Plattform ist Devicewise for Factory von Telit, einem Unternehmen, das IIoT-Module, Software und Konnektivitätsdienste sowie Software anbietet.
Laut Gillen liegen die Vorteile dieses Systems darin, dass es mit einer Vielzahl von Steuerungen verbunden werden kann und keine kundenspezifische Programmierung für die Datenerfassung erforderlich ist. Es ist so konfiguriert, dass alle Daten, die zuvor manuell von der Maschine erfasst wurden (Teileanzahl, Maschinencode und mehr) sowie ERP-Daten (Auftragsnummer, Auftragsbeschreibung, Bestelldatum, Bestellmenge, Lieferdatum usw.) automatisch abgerufen und abgerufen werden speichert es in der Cloud. Die Daten sind über ein Web-Dashboard zugänglich. Berichte können dann erstellt werden, um grafisch darzustellen, was zuvor in der Produktionsprotokolltabelle verfügbar war.
Seit Anfang Juni 2018 sammelt das System alle 20 Minuten Daten, ohne dass einer laufenden Maschine ein Eintrag entgeht. Derzeit sind drei Drehzentren und ein Walzwerk angeschlossen. Bei einer anderen Mühle muss noch ein MTConnect-Agent installiert werden, bevor sie verbunden werden kann. Laut Gillen gibt es viele gute Maschinenüberwachungsprodukte. Sein technischer Hintergrund bot jedoch die Gelegenheit, eine interne Lösung zu erkunden, die die Geschäftsinformationen anspricht, an denen das Geschäft am meisten interessiert ist. Er ist außerdem der Ansicht, dass diese Datenerfassungsfunktion auch zu noch fortschrittlicheren Analysen führen könnte, wie z. B. die Verknüpfung der Schnittzeit mit bestimmten Arten von Schneidwerkzeugen oder Einsätzen.
Industrielle Ausrüstung
- Mitsubishi Electric Automation stellt neue LoadMate-Roboterarbeitszelle vor
- 6 Fragen, die Sie beantworten sollten, bevor Sie nach einer Arbeitsbühne suchen
- 7 Tipps zur Auswahl einer Maschinenwerkstatt
- Kann dieser neue CNC-Mehrspindler für Ihre Werkstatt funktionieren?
- Gang-Tool-Drehmaschine für komplexe Stangenarbeiten
- Multitasking-Maschine für mittelgroße Bararbeiten
- Vierachsige Drehmaschine für Ölleitungen
- Video:Was bedeutet 5G für die maschinelle Bearbeitung?
- Video:Die Auswirkungen der künstlichen Intelligenz (KI) auf Fertigung und Bearbeitung
- Sondieren für Setup und Lights-Out-Bearbeitung – The One-Person Shop Episode #2