Unterhaltungselektronik:Hybrid-Verbundabdeckungen
SABIC hat in einer aktuellen Studie gezeigt, dass eine 1 Millimeter dicke Abdeckung alle relevanten Leistungsspezifikationen der Branche für sehr dünne Notebooks oder Tablets erfüllen kann. Quelle, alle Bilder | SABIC
Unterhaltungselektronik ist ein dynamischer Markt mit recht kurzen Zykluszeiten zwischen Produktgenerationen. Verbraucher wünschen sich von ihren Smartphones, Smartwatches, Tablets und Notebooks/Laptops höhere Betriebsgeschwindigkeiten, langlebigere Batterien, längere Lebensdauer und mehr Funktionen bei geringeren Kosten und Gewicht. Um der Verbrauchernachfrage gerecht zu werden, verlangen OEMs von den Lieferanten Materialien mit hoher Ästhetik und Designfreiheit, hervorragender Schlagzähigkeit und hoher Steifigkeit – was in diesem Markt für Qualität steht – bei geringem Gewicht und dünnwandigen Abschnitten. Sie wollen auch kostengünstige, hoch wiederholbare Verarbeitungsmethoden, die die weltweite Produktionsnachfrage in Höhe von mehreren zehn Millionen Einheiten jährlich decken. Dieser Druck hat den Markt zuerst zu Leichtmetallen für Abdeckungen/Koffer und Rahmen getrieben und treibt ihn nun zu Metall-/Verbundwerkstoff- und Vollverbundlösungen.
Eine von SABIC (Bergen op Zoom, Niederlande) durchgeführte Machbarkeitsstudie umfasste die Verwendung von zwei Arten thermoplastischer Verbundwerkstoffe zur Herstellung einer 1 Millimeter dicken Notebook-/Tablet-Abdeckung. Die Studie zeigte, dass das Design eines hybriden thermoplastischen Verbundwerkstoffs eine praktikable Lösung für den anspruchsvollen Markt der Unterhaltungselektronik sein könnte.
Testfall
Seit 2012 hat SABIC eine Reihe von Investitionen in die Entwicklung eigener unidirektionaler (UD)-faserverstärkter thermoplastischer Verbundbänder (siehe „Weiterentwicklung zu Endlosfaserverstärkungen“) getätigt, die die Kernkompetenz des Unternehmens im Bereich Kurzfaserinjektion und faserthermoplastische (LFT) Materialien und ermöglichte es SABIC, zu thermoplastischen Verbundwerkstoffen mit höherer Leistung zu expandieren. Im Jahr 2015 erwarb das Unternehmen die Mehrheitsbeteiligung am Bandhersteller Fiber Reinforced Thermoplastics BV (FRT, Lelystad, Niederlande) und wurde 2017 eine Partnerschaft mit Airborne (Den Haag, Niederlande), einem Maschinenhersteller und Entwickler von Verbundwerkstoffen, und wurde ein Minderheitsinvestor. Zeilen.
Da SABIC und Airborne eine Technologie entwickelt und gebaut haben, um schnell und kosteneffektiv netzförmige, hochwertige thermoplastische Laminate auf Bandbasis für wirklich volumenstarke Märkte herzustellen (siehe „Hochgeschwindigkeits-Herstellung von thermoplastischen Verbundwerkstoffen“), hat das Team begann mit der Suche nach einem Testfall. Dieser Demonstrator wäre ein wichtiges Marketinginstrument, um Designkonzepte für thermoplastische Verbundlaminate zu beweisen, die aus Verbundbändern hergestellt werden, die mit diskontinuierlich faserverstärkten Compounds umspritzt sind. Es wäre auch wichtig, prädiktive Engineering-Tools zu testen, die das Team für beide Materialtechnologien entwickelt hat, und den sich in den Niederlanden entwickelnden Hochgeschwindigkeits-Fertigungsprozess zu präsentieren.
„Wir haben uns entschieden, uns auf Anwendungen in der Unterhaltungselektronik zu spezialisieren“, erklärt Gino Francato, der weltweit führende Anbieter von Verbundwerkstoffen bei SABIC. „Dieser Markt ist sehr interessant, weil wir echte Ambitionen haben, auf leichte Materialien umzusteigen, um unsere Mobiltelefone und Notebooks leichter und dünner zu machen. Und da sie Millionen und Abermillionen davon herstellen, haben wir uns entschieden, die Herausforderung dieses Marktes anzunehmen.“
„Wir haben uns entschieden, mit etwas zu beginnen, das einigermaßen komplex war, aber nicht zu komplex“, erklärt Scott Davis, SABIC Staff Scientist-Global Application Technology. Die obere Abdeckung eines sehr dünnen Notebook-Computers oder sogar eines Tablets – von dem das Team hoffte, dass es schließlich in Smartphone-Komponenten übersetzt werden würde – schien ein guter Ausgangspunkt zu sein. „Wir arbeiteten mit einer einfachen Gesamtgeometrie, einem Rechteck, das dennoch eine hohe Ästhetik beibehalten und auf seiner B-Seite viel Komplexität bieten musste, einschließlich Befestigungsfunktionen“, fährt Davis fort. „Wir mussten die Abdeckung sehr dünn halten, aber dennoch die in der Branche üblichen anspruchsvollen Durchbiegungsanforderungen erfüllen. Und natürlich mussten wir über einen komplexen neuen Herstellungsprozess ein sehr konsistentes Produkt liefern.“
Da sie nicht mit einem tatsächlichen Kundendesign arbeiteten und nur die Schutzhülle für einen Bildschirm erstellten, verwendeten sie eine generische Geometrie. Tatsächlich, bemerkt Davis, waren sie sich, als sie anfingen, Spritzgusswerkzeuge für die interne Entwicklung zu schneiden, nicht einmal sicher, ob sie ein Tablet- oder Notebook-Cover herstellen würden, also war das Cover für beide geeignet. „Es gab viele Herausforderungen, um eine Verbundlösung für die Massenproduktion vorzubereiten“, fügt Davis hinzu. „Tatsächlich geschah viel gleichzeitig – Bandentwicklung, Laminatentwicklung und Prozessentwicklung – und wir konnten es kaum erwarten, bis all diese Dinge fertig waren, um mit unserem Werkzeugbau zu beginnen, und so kamen wir zu diesem Design.“ Nachdem das grundlegende Design abgeschlossen war, konzentrierte sich das Team auf andere Details, wie die beste Art des Angusses, welche Arten von Überlappungen zwischen Laminateinlage und Umspritzmasse erforderlich waren, wie die automatische Platzierung im Werkzeug gehandhabt wird, wie der Koeffizient von ( lineare) Fehlanpassung der thermischen Ausdehnung (CLTE oder CTE) zwischen den beiden Verbundwerkstoffen und wie man ein leicht wiederholbares Teil erzeugt.
Herausfordernde Anforderungen erfüllen
Ziel war es, eine 1 Millimeter dicke obere Abdeckung zu entwickeln, die eine hohe Steifigkeit bietet und alle Leistungs- und ästhetischen Anforderungen erfüllt – insbesondere den Center-Point-Deflexion-Test wird regelmäßig auf Laptopabdeckungen angewendet, um die Belastungen zu bewerten, die erforderlich sind, um den darunter liegenden Bildschirm zu beschädigen. Die Last-/Durchbiegungsanforderungen variieren je nach OEM, Gerät und Modell, aber normalerweise sind bei einem Druck von 40-120 Newton nicht mehr als 3-5 Millimeter Durchbiegung zulässig – eine Situation, die die Belastung simuliert, die durch einen Finger oder Ellbogen ausgeübt wird, der in die Abdeckung gedrückt wird, wie ein menschlicher Benutzer steht auf. In vielen Branchen besteht die Strategie zum Bestehen solcher Tests darin, die Schnittdicke zu erhöhen, aber dieser Markt schätzt dünnere Designs, die Platz für größere Batterien und andere Komponenten schaffen, ohne die Gerätegröße oder das Gewicht zu erhöhen. Daher musste das Team eine andere Designstrategie anwenden, um Schäden am Bildschirm zu verhindern – nämlich die Auswahl steiferer Materialien (über eine Laminateinlage) und die Verwendung der Geometrie (z. B. Verrippung durch Spritzgießen). Aber zuerst mussten sie Materialien angeben.
Eines dieser Materialien, Polycarbonat (PC), wird in dieser Branche aufgrund seiner hervorragenden Ästhetik und hohen Schlagzähigkeit bereits häufig für Abdeckungen und andere Komponenten verwendet. Die größten Schwächen des Polymers sind die chemische Beständigkeit und das Verkratzen der Oberfläche, aber die Beschichtung, Farbe oder Kombinationen aus beiden, die auf die meisten Abdeckungen aufgetragen werden, überwinden diese potenziellen Probleme im Allgemeinen.
„Weil ultraleichte Computer so dünn sind, ist der Platz im Inneren sehr knapp, sodass Durchbiegungen und Mechanik wirklich kritisch werden“, betont Francato. „Während Sie aus Kostengründen Glas [Verstärkung] verwenden möchten, mussten wir Carbon [Faser] verwenden, um die erforderliche Steifigkeit zu erreichen.“ Als Ergebnis waren alle bewerteten bandbasierten Laminate Variationen von kohlenstofffaserverstärktem Polycarbonat – Typen, die damals von der SABIC-Tochter FRT entwickelt wurden.
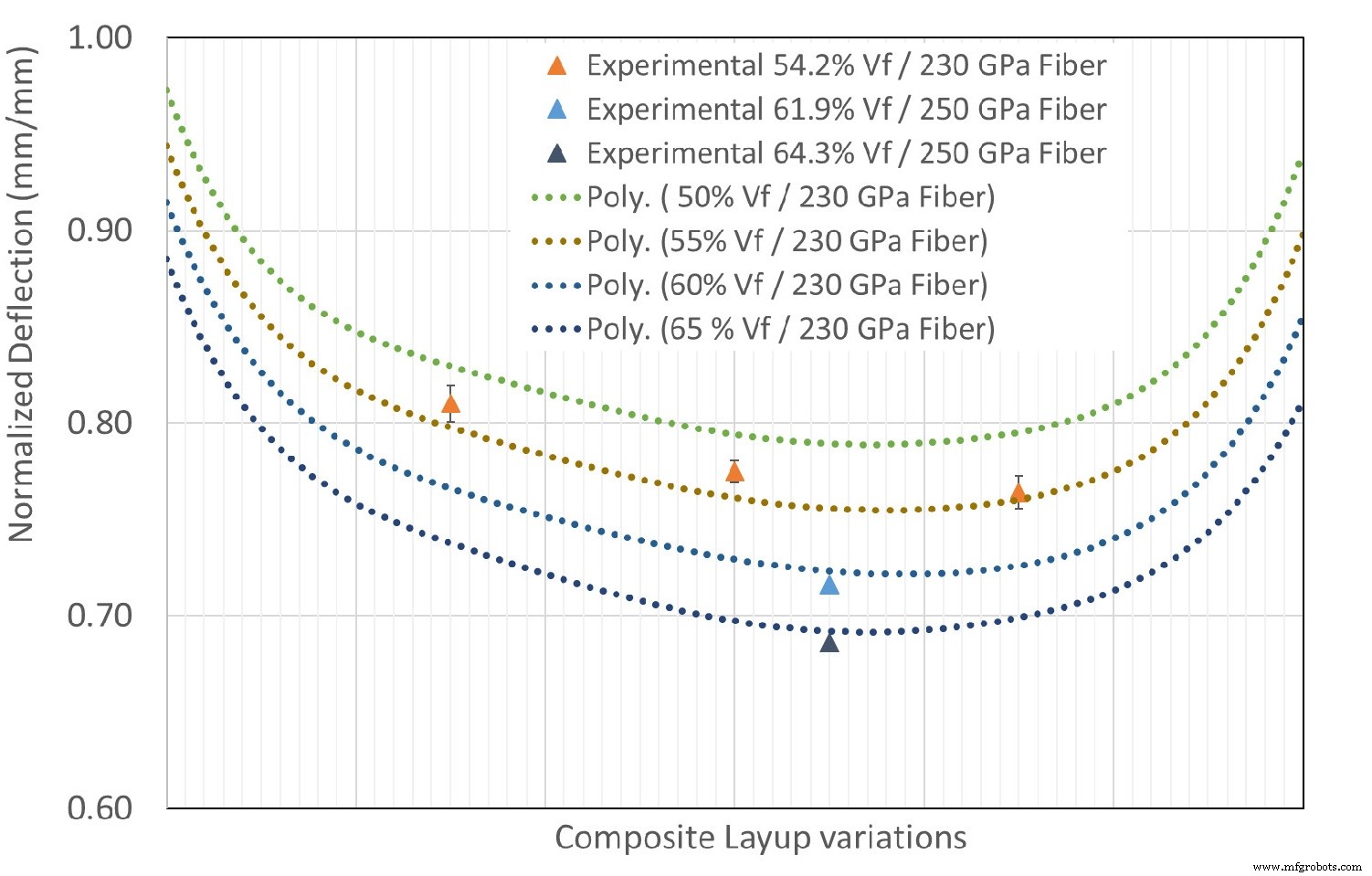
SABIC hat Vorhersagemodelle entwickelt, um Laminattyp und -architektur (mit und ohne Overmolding Compounds) im Vergleich zur Formteilleistung zu simulieren und berichtet, dass eine starke Korrelation zwischen Vorhersagen und experimentellen Ergebnissen erzielt wurde. Die Predictive Engineering Tools sollen die Materialentwicklung beschleunigen.
Die Umspritzmasse erforderte einen anderen Ansatz. Ursprünglich bestand die Strategie darin, ein längerfaseriges LFT-Compound zu verwenden, aber aus einer Reihe von Gründen – einschließlich hoher ästhetischer Anforderungen, Teilegröße und Angussstrategie – erfüllten Kurzfaser-Compounds die Projektanforderungen besser. Ein weiteres Problem war die Art der zu verwendenden Faser. „Kurzkohlenstoff-Spritzgussmassen sind wirklich schwer zu verarbeiten und erzielen trotzdem eine hohe Ästhetik“, fährt Francato fort, „deshalb haben wir uns für unser Overmolding-Material kurzglasverstärkte Typen angesehen.“ Die SABIC-Tochter LNP Engineering Plastics, Inc. (Exton, Pennsylvania, USA) bietet viele Glasfaser-/PC-Typen mit guter Ästhetik und Steifigkeit an, die bei Geräte-OEMs beliebt sind. Daher konzentrierte sich das Team auf diese.
Während vollständig amorphes PC weniger anfällig für Verzug ist als teilkristalline Polymere, machte sich das Team dennoch Sorgen über die CLTE-Unterschiede zwischen den hochverstärkten und anisotropen UD-Kohlefaserbändern und den isotroperen, diskontinuierlichen Kurzglasfaser-Umspritzungstypen bei niedrigeren Faserbeladungen. „Bei so dünnen Wänden gibt es nur sehr wenig Spielraum für Fehler, daher mussten wir die geringfügigen Unterschiede bei CLT sorgfältig berücksichtigen“, erklärt Davis. „Und das berührt noch nicht einmal all die normalen Probleme, mit denen Sie beim Spritzgießen beschäftigt sind, wie Angusspositionen, Füllmuster, Packungsdrücke und Stricklinien. All diese Faktoren wurden simuliert und durch physikalische Tests verifiziert.“
Nachdem die Materialien ausgewählt waren, führten die SABIC-Ingenieure mehrere Iterationen der Formfüllung, Strukturanalyse und Verzugssimulation durch, um Laminataufbau, Geometrie und Materialkombinationen zu bewerten, um die Steifigkeit für den Belastungs-/Durchbiegungstest sowie andere Leistungs- und Kostenanforderungen zu optimieren. Das Unternehmen sagt, dass es umfassende und genaue Modellierungswerkzeuge für Verbundwerkstoffe entwickelt hat (für Kunden verfügbar und in gängigen Struktur- und Verarbeitungscodes ausgeführt), die die Laminatarchitektur, die Zusammensetzung der Umspritzmasse und verschiedene Verarbeitungs- und Werkzeugoptionen im Vergleich zur Leistung des Formteils schnell modellieren und simulieren können. Diese Tools sollen eine starke Korrelation zwischen Vorhersagen und gemessener Leistung erreichen und sind ideal, um die Entwicklung kundenspezifischer Materialien zu beschleunigen.
Bereit für die Hauptsendezeit
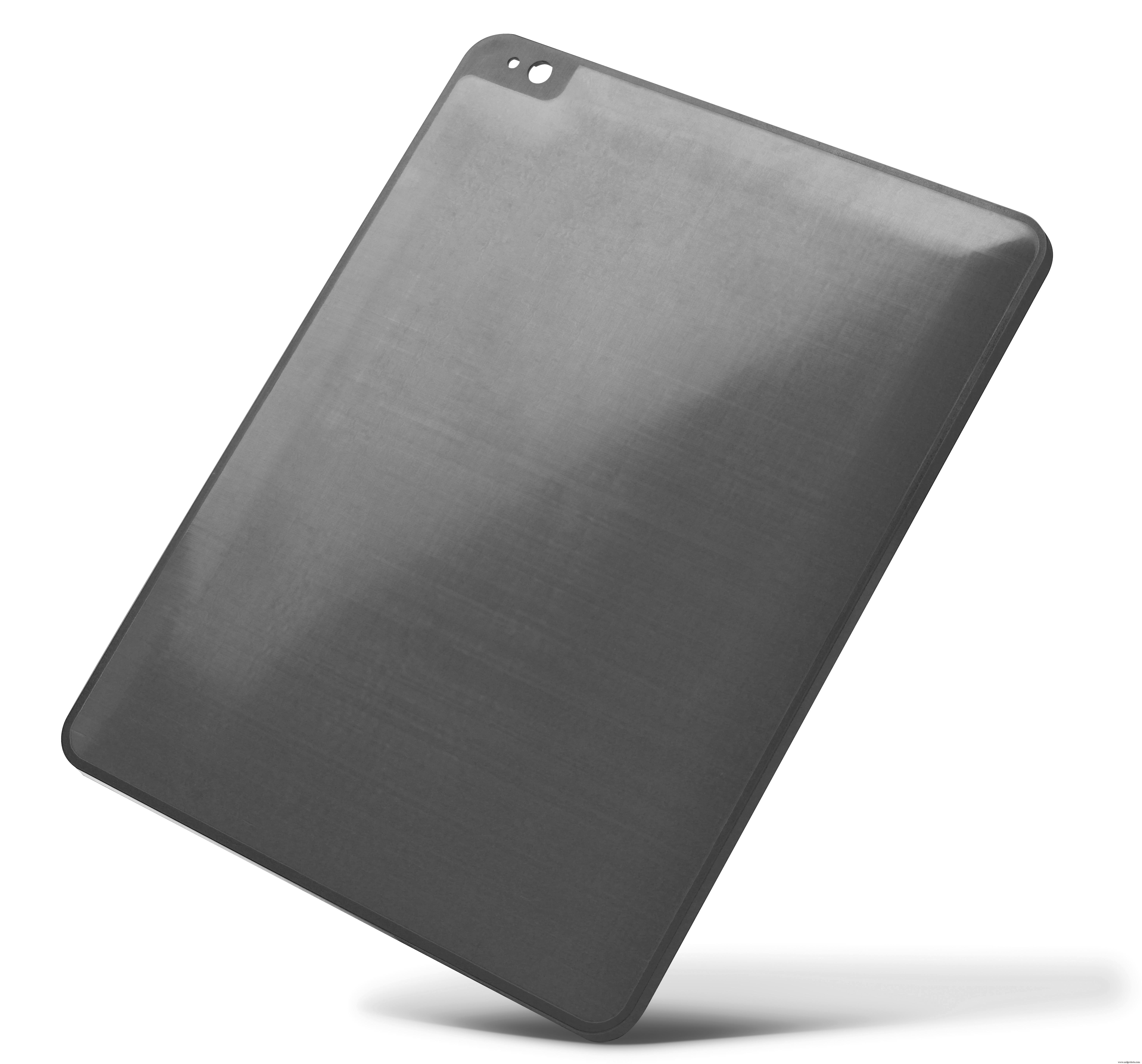
Vorderseite der finalen Laptop-/Tablet-Hülle, die aus einer kohlefaserverstärkten Laminateinlage auf Polycarbonat-Tape-Basis hergestellt wurde, die mit einem Kurzglas-/Polycarbonat-Copolymer-Compound umspritzt wurde, eine Kombination, die alle relevanten mechanischen und ästhetischen Anforderungen in einem 1- Millimeter dickes Teil.
Der letzte Demonstrator verfügt über eine Laminateinlage, die aus sieben Schichten entwicklungsbezogener UDMAX-Kohlefaser/PC-Bänder (55 % Faservolumenanteil) hergestellt, dann konsolidiert, zugeschnitten, vorgeformt und erneut auf die endgültige Nettoform zugeschnitten wird, bevor sie mit 40 % Fasern spritzgegossen wird -Gewichtsanteil THERMOCOMP D452 Kurzglasfaser/PC-Copolymer (eine auf hohe Fließfähigkeit und hohe Ästhetik optimierte Sorte, die in diesem Segment bereits weit verbreitet ist). Die Kombination ergibt eine Abdeckung mit hoher Steifigkeit und Festigkeit bei geringer Masse und Profildicke, die zahlreiche 3D-Designdetails, Befestigungsmerkmale und eine gute Ästhetik umfasst, wodurch das Beste aus jedem Material genutzt wird. Die Abdeckung hat angeblich alle erforderlichen Branchentests bestanden und wird derzeit von Geräte-OEMs evaluiert.
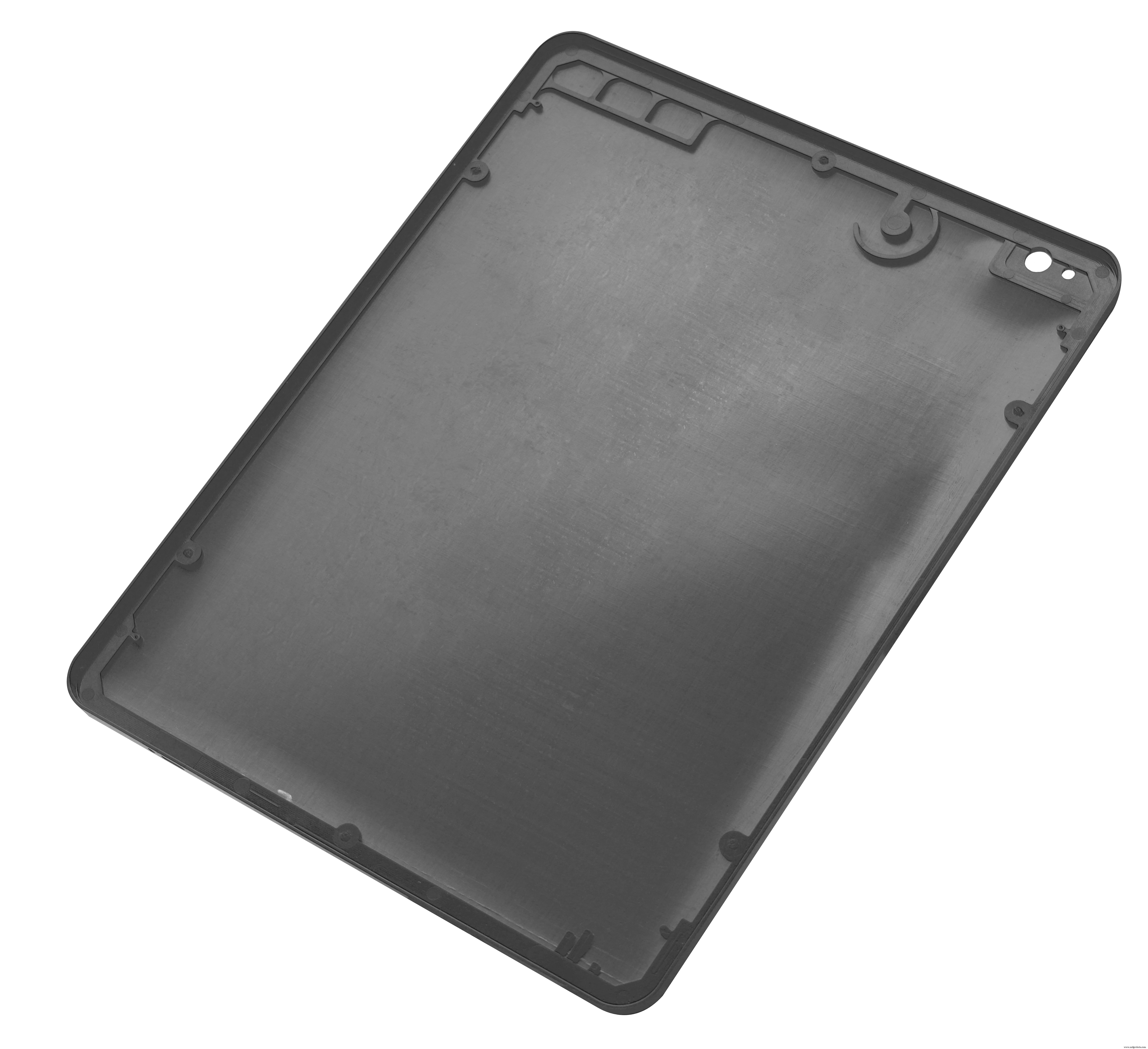
Rückseite des fertigen Covers.
Die Zusammenarbeit zwischen Airborne und SABIC hat auch für die Ziele des Unterhaltungselektronikmarktes von SABIC Früchte getragen. Die Partnerschaft wurde 2018 bekannt gegeben, und in diesem Jahr wurden weitere Details zu ihrer sogenannten Digital Composites Manufacturing Line bekannt gegeben, die vier konsolidierte Laminateinlagen in Nettoform aus thermoplastischen Verbundbändern pro Minute oder 1,5 Millionen Laminate pro Jahr produzieren kann eine einzige Produktionslinie. Das System soll flexibel (in Bezug auf Layup-Architektur und Materialien) und schnell sein. Ab 2020 wird Airborne die Linie zur Herstellung von Laminaten für den kommerziellen Einsatz in der Unterhaltungselektronik nutzen und zu einer Ressource werden, von der beide Unternehmen hoffen, dass sie die Durchdringung thermoplastischer Verbundwerkstoffe in diesem hart umkämpften und schnelllebigen Segment erheblich steigern wird.
Faser
- Materialien:Einschichtiger flexibler Graphit für die Unterhaltungselektronik
- Solvay erweitert die Kapazität von thermoplastischen Verbundwerkstoffen
- Thermoplastisches Rad nimmt die raue Straße
- Fraunhofer nimmt automatisierte Engel-Produktionszellen für F&E thermoplastischer Verbundwerkstoffe in Betrieb
- Thermoplastische Bänder zeigen weiterhin Potenzial für Verbund-Flugzeugstrukturen
- Avient bringt feuchtigkeitsbeständigen, thermoplastischen Nylon-Langfaser-Verbundwerkstoff auf den Markt
- INEOS Styrolution baut Produktionsstätte für thermoplastischen Verbundwerkstoff StyLight
- Xenia führt thermoplastische CF/PP-Composite-Compounds ein
- NIARs NCAMP-qualifizierender TenCate thermoplastischer Verbundwerkstoff
- Verbundwerkstoff + Metall:Hybridtechnologie mit Hohlprofil