Verbundwerkstoffe tragen dazu bei, das Batteriegewicht für Elektromüllwagen auszugleichen
Das Fraunhofer-Institut für Werkstoff- und Strahltechnik IWS Dresden hat sich kürzlich mit fünf weiteren mitteldeutschen Forschungsinstituten und Unternehmen für das Projekt UTILITAS (»Ultralight Structures for Commercial Vehicles in Municipal Service Operation«) zusammengeschlossen, das auf nachhaltige und kostengünstige effektive Lösungen, die Kommunen dabei unterstützen, ihre Klimaschutzziele mit lokal verfügbaren Ressourcen zu erreichen. Gemeinsam wollen die Unternehmen bessere Sammelbehälter aus Leichtmetallen und faserverstärkten Verbundkunststoffen bauen. Diese Lösungen werden die schweren Stahlaufbauten klassischer Müllwagen durch eine um ein Drittel leichtere Alternative ersetzen.
„Diese neue Generation von Elektrofahrzeugen könnte dann pro Ladung so viel Abfall transportieren wie ein klassischer kleiner Müllwagen“, betont Annett Klotzbach, Leiterin der Gruppe Kleb- und Faserverbundtechnik am Fraunhofer IWS Dresden.
Das übergeordnete Ziel des Projekts bedeutet jedoch mehr, als nur besser zu konstruieren Fahrzeuge verweigern. „Deshalb entwickelt die Allianz nicht nur den Behälter, sondern auch die dazugehörigen praxisgerechten Produktionstechnologien“, erklärt Klotzbach. „Wichtig ist hier, dass die neuen Container auch in Kleinserien gewinnbringend gebaut und in lokalen Werkstätten schnell repariert werden können.“ Die Projektpartner setzen dabei auf Containerkonstruktionen aus Aluminiumrahmen und glasfaserverstärkten Thermoplastplatten und testen zudem verschiedene Fügeverfahren.
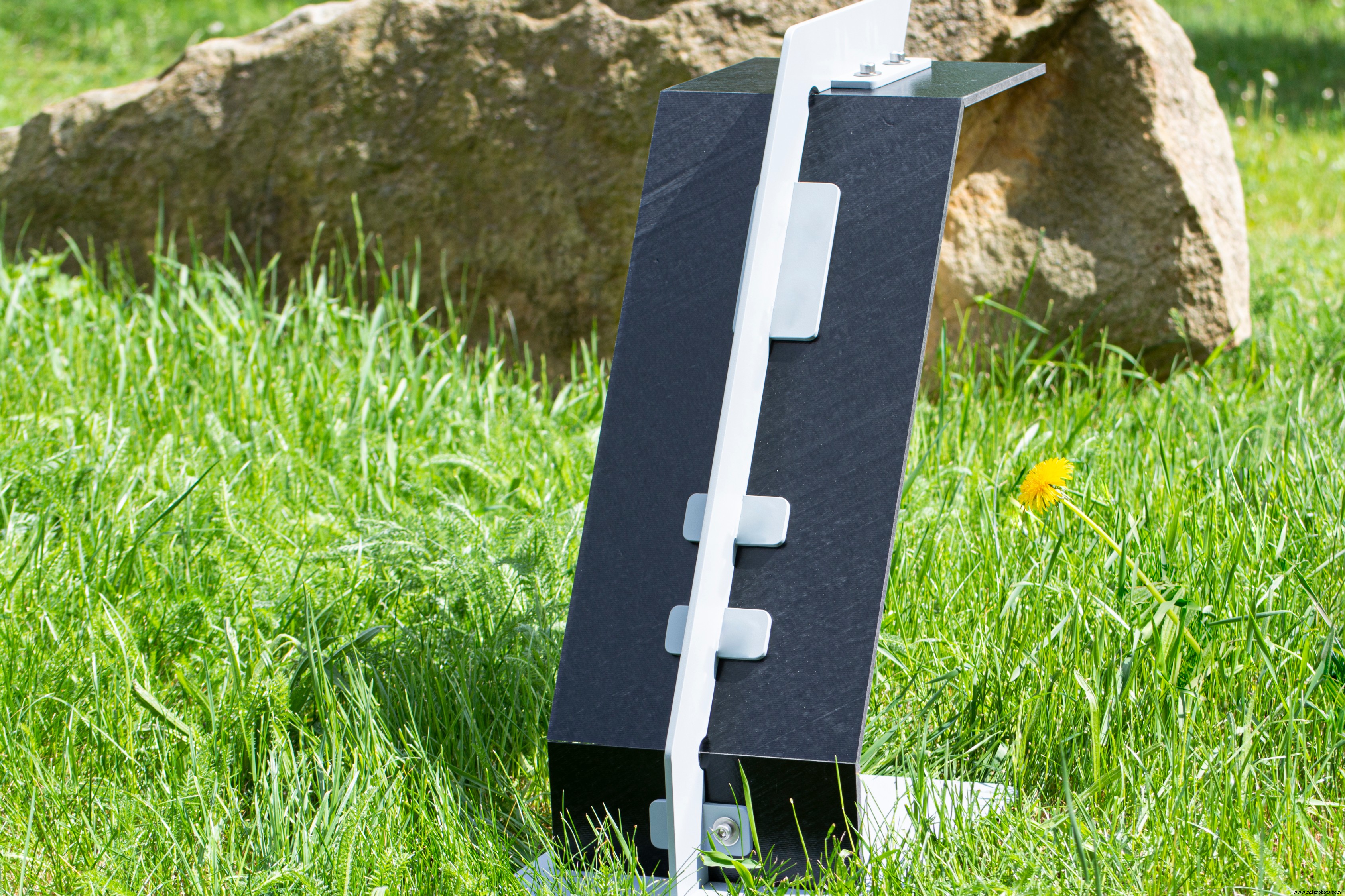
Eine der am Fraunhofer IWS entwickelten neuartigen Fügetechnologien, die »HeatPressCool-integrative« (HPCi), kommt zusätzlich zum Einsatz. Ein Laser raut zunächst die Aluminiumbauteile auf, wodurch Rillen im Metall entstehen, die dünner als ein Stift und nur etwa 200 Mikrometer tief sind. Anschließend presst das Werkzeug das Kunststoffteil gegen die Aluminiumstrebe und erhitzt das Metall kurzzeitig. Dabei schmilzt der Thermoplast auf der Aluminiumoberfläche, fließt in die lasergeformten Rillen und wird dort beim Abkühlen verankert. Nach wenigen Sekunden sollen Aluminium und Verbundkunststoff dauerhaft und fest verbunden sein.
Im Zuge der Entwicklungszusammenarbeit wollen die IWS-Ingenieure auch die Langzeitbeständigkeit des gefügten Leichtbaubehälters im Vergleich zu Schraub- oder Klebelösungen ermitteln. Laut Fraunhofer IWS wird der Container im täglichen Einsatz hohen Belastungen standhalten müssen, etwa wenn die Kfz-Mechaniker den gesammelten Müll verdichten. In früheren Versuchen erwiesen sich die HPCi-verbundenen Behälter als besonders langlebig und wesentlich reparaturfreundlicher als geklebte Konstruktionen. Messungen haben gezeigt, dass die HPCi-Verbindungen Zugkräften widerstehen können, die dem Druck eines hydraulischen Arms von bis zu 25 Megapascal entsprechen.
Die Experten des IWS sind überzeugt, dass sich das neue Fügeverfahren nicht nur für Müllcontainerkonstruktionen eignet, sondern auch für Leichtbaukonstruktionen in Flugzeugen, Bahnen, Industrieanlagen oder Schiffen. Industriekunden wollen HPCi auch bei der Herstellung von Geschirrspülern und anderen Haushaltsgeräten einsetzen. Um die breite praktische Anwendung der neuen Fügetechnologie des Projekts zu unterstützen, haben die Dresdner Forscher unterdessen kompakte HPCi-Fügezangen entwickelt, die nicht viel größer sind als eine Standard-Handbohrmaschine. Sie können beispielsweise modular an Robotern montiert werden, um schnell eine kleine Leichtbauserie zu starten. Da dieses neue Werkzeug so vielversprechend ist, wollen die Fraunhofer-Wissenschaftler auch bald eine Firma gründen, die die HPCi-Fügezangen in Serie produzieren wird.
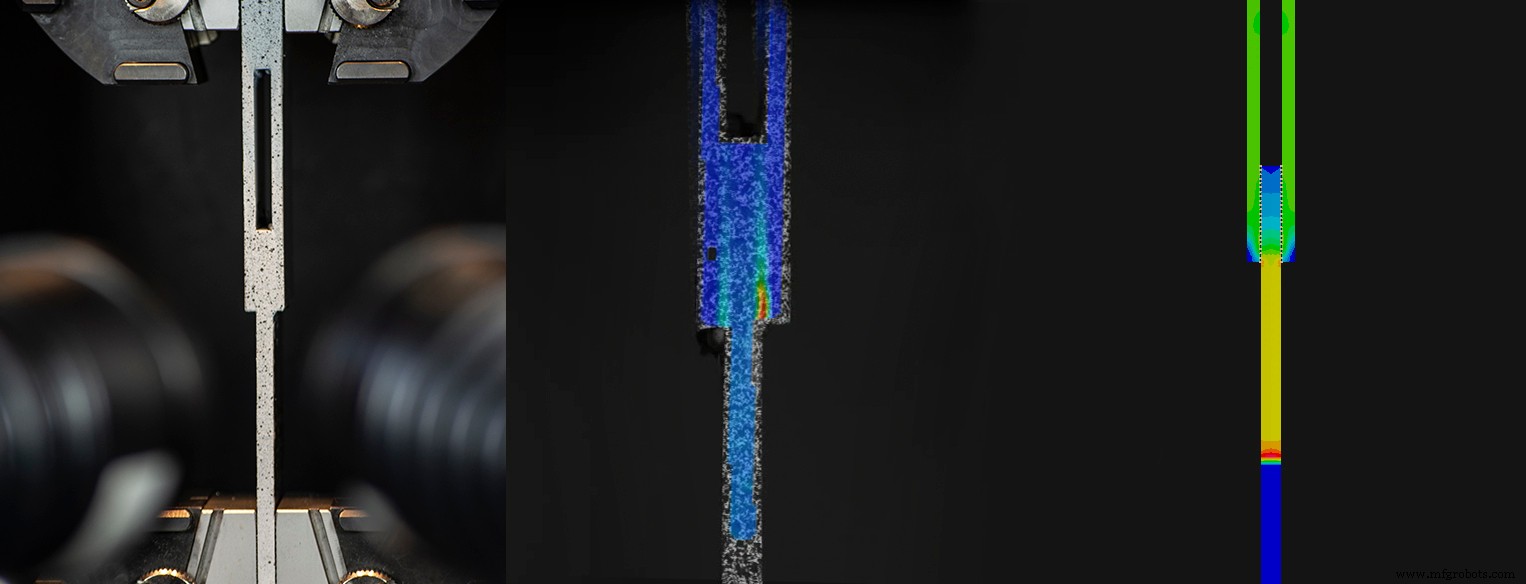
Mit dem aktuellen Stand der Entwicklungen, so das Unternehmen weiter, werden die ersten Elektro-Müllwagen mit neuen Leichtbau-Containern schon bald das urbane Bild vieler Großstädte prägen. „Bis Anfang 2021 sollen die Container-Prototypen fertig sein“, kündigt Klotzbach an. „Wir gehen davon aus, dass innerhalb von zwei Jahren die ersten Abfallsammelfahrzeuge auf den Straßen sein werden.“ Als Hauptkunden sehen die Entwickler kommunale Unternehmen.
Am Projekt UTILITAS sind sechs Partner beteiligt:Fraunhofer IWS Dresden, Lehrstuhl für Strukturleichtbau und Kunststoffverarbeitung der TU Chemnitz (Chemnitz), Marko Pfaff &Co. Spezialfahrzeugbau GmbH (Bad Lausick), Car systems Scheil GmbH &Co. KG, der PROFIL Verbindungstechnik GmbH &Co. KG (Friedrichsdorf) und der EBF Dresden GmbH (Dresden).
Faser
- Einführung in Batteriesysteme für Elektrofahrzeuge
- Auf was man bei Herstellern von Verbundwerkstoffen achten sollte
- Intelligentes Abfallmanagement könnte den USA helfen, die Regierungsziele für das Recycling zu erreichen
- Chancen für Hersteller von Lithium-Ionen-Batterien
- RS Electric Boats wählt Norco für die Herstellung von Verbundwerkstoffen
- Vollverbundrad für Elektrofahrzeuge erhält Finanzierung
- Exel Composites liefert Glasfaserprofile für Elektrobusse
- Rockwood Composites, Leonardo produziert das 10.000ste Blatt für den Eurofighter Typhoon
- SGL Carbon fertigt Batteriegehäuse aus Verbundwerkstoff für die BMW Group
- YG-1-Vollhartmetall-Fräser für die schnellere Bearbeitung von Verbundwerkstoffen