Abscheidungsprozess und Eigenschaften von stromlosen Ni-P-Al2O3-Verbundbeschichtungen auf Magnesiumlegierung
Zusammenfassung
Zur Verbesserung der Korrosionsbeständigkeit und Verschleißfestigkeit von stromlosen Nickel-Phosphor (Ni-P)-Beschichtungen auf Magnesium (Mg)-Legierungen. Ni-P-Al2 O3 Beschichtungen wurden auf einer Mg-Legierung aus einem Verbundplattierungsbad hergestellt. Das optimale Al2 O3 Die Konzentration wurde durch die Eigenschaften des Plattierungsbades und der Beschichtungen bestimmt. Morphologische Wachstumsentwicklung von Ni-P-Al2 O3 Verbundbeschichtungen zu verschiedenen Zeiten wurden unter Verwendung eines Rasterelektronenmikroskops (REM) beobachtet. Die Ergebnisse zeigen, dass Nano-Al2 O3 Partikel können die Austauschreaktion von Mg und Ni 2+ . verlangsamen in der frühen Phase des Abscheidungsprozesses, hat jedoch fast keinen Einfluss auf die Geschwindigkeit des autokatalytischen Ni-P-Reduktionsprozesses. Die Korrosionsschutz- und Mikrohärtetests von Beschichtungen zeigen, dass das Ni-P-Al2 O3 Verbundbeschichtungen weisen aufgrund des geeigneteren Kristallebenenabstands und der Korngröße von Ni-P-Al2 . eine bessere Leistung im Vergleich zu Ni-P-Beschichtungen auf O3 Beschichtungen. Der Thermoschocktest zeigt, dass das Al2 O3 Partikel haben keinen Einfluss auf die Haftung von Beschichtungen. Darüber hinaus beträgt die Lebensdauer des Verbundbeschichtungsbads 4,2 Metallumsätze, was darauf hindeutet, dass es eine potenzielle Anwendung im Bereich der Magnesiumlegierungen hat.
Hintergrund
Magnesium (Mg)-Legierungen haben aufgrund der geringen Dichte, der hohen spezifischen Festigkeit und der hervorragenden Bearbeitbarkeit große Aufmerksamkeit und wissenschaftliche Forschung auf sich gezogen [1, 2]. Daher werden Mg-Legierungen normalerweise in den Bereichen Luft- und Raumfahrt, Elektronik und Automobil verwendet [3, 4]. Die Anwendung von Mg-Legierungen ist jedoch aufgrund der unerwünschten Mängel bei Korrosionsschutz und Verschleißfestigkeit eingeschränkt [5, 6]. Daher wurden für Mg-Legierungen Oberflächen-Korrosions- und Anti-Reibungsmethoden entwickelt, wie z. 10,11,12,13].
Die stromlose Nickel-Phosphor-(Ni-P)-Beschichtung ist eine der effektivsten Oberflächentechnologien für Mg-Legierungen, da sie hervorragende umfassende Vorteile in Bezug auf niedrige Kosten, Effizienz, Korrosionsbeständigkeit und Verschleißfestigkeit bietet [14, 15]. Daher spielt die stromlose Ni-P-Beschichtung eine wichtige Rolle im Korrosionsschutzbereich von Mg-Legierungen. Um die Leistung der Ni-P-Beschichtung weiter zu verbessern, werden Nanopartikel, zum Beispiel SiC, ZrO2 , TiO2 , SiO2 , und Al2 O3 , usw. werden normalerweise in ein stromloses Plattierungsbad gegeben, um Ni-P-Nanopartikel-Verbundbeschichtungen herzustellen [16,17,18,19,20]. Nach früheren Studien [20,21,22,23] wird die Leistung der Ni-P-Beschichtung durch Nanopartikel effektiv verbessert. Obwohl die Ni-P-Nanopartikel-Verbundbeschichtungen im Vergleich zur Ni-P-Beschichtung eine relativ hohe Leistung aufweisen, müssen drei Probleme beachtet werden. Erstens sind Nanopartikel leicht zu aggregieren und bilden das aktive Zentrum im stromlosen Plattierungsbad, was die Stabilität der Plattierungslösung verringert. Zweitens bestimmen Prozessparameter von Verbundbeschichtungsbädern in der Regel den Gehalt und die Verteilung von Nanopartikeln in den Beschichtungen und sind auch Schlüsselfaktoren für die Verbesserung der Eigenschaften von Beschichtungen. Drittens ist der Prozess der gleichzeitigen Abscheidung von Nanopartikeln mit Ni-P ein weiterer Einflussfaktor auf die Beschichtungseigenschaften. Daher sind diese Faktoren die Aufmerksamkeit wert. Nano-Al2 O3 Partikel sind ein billiges Schleifmittel, das eine hohe Härte und eine gute chemische Stabilität aufweist [24, 25]. Es lässt sich gut im stromlosen Vernickelungsbad dispergieren. Daher Ni-P-Al2 O3 Verbundbeschichtungen werden normalerweise als Korrosions- und Verschleißschutzbeschichtungen zum Schutz von Stahl- oder Kupfersubstraten verwendet. Allerdings konzentrierten sich nur wenige Berichte auf das stromlose Ni-P-Al2 . O3 Plattieren auf einem Magnesiumlegierungssubstrat [20, 22, 26]. Darüber hinaus ist die Untersuchung des Wachstumsprozesses von Ni-P-Al2 O3 Beschichtung auf Mg-Legierungen und die Stabilität von Verbundbeschichtungsbädern ist eher selten. Daher mehr Details zur Leistung des Verbundbads und des gleichzeitigen Abscheidungsprozesses von Ni-P-Al2 O3 müssen studiert werden.
Um die Eigenschaften der Ni-P-Beschichtung auf einem Mg-Legierungssubstrat weiter zu verbessern, verwendeten wir in der vorliegenden Arbeit Nickelsulfat und Milchsäuresystem als Hauptsalz bzw. Komplexbildner im Plattierungsbad. Inzwischen Nano-Al2 O3 Pulver wurde in das stromlose Ni-P-Beschichtungsbad gegeben. Um ein geeignetes Bad zum stromlosen galvanischen Plattieren für die Mg-Legierung AZ91D zu erhalten, wurden die Prozessparameter dieses Bades anhand der Abscheidungsrate und der Beschichtungseigenschaften bewertet. Darüber hinaus wurde ein periodischer Zyklustest durchgeführt, um die Lebensdauer und Stabilität des Beschichtungsbades bei optimalen Prozessbedingungen zu bewerten. Um die Wirkung von Nano-Al2 . zu untersuchen O3 Partikel auf den Wachstumsprozess der Schichten, das Abscheidungsverhalten und die Phasenstruktur der Ni-P-Schicht wurden diskutiert. Darüber hinaus wurden die Eigenschaften, einschließlich Korrosionsbeständigkeit, Mikrohärte und Haftung von Beschichtungen, basierend auf Morphologie und Struktur analysiert. Die Ergebnisse zeigten, dass die Eigenschaften von Ni-P-Al2 O3 Verbundbeschichtungen waren der Ni-P-Beschichtung vorzuziehen, und das stromlose Verbundbeschichtungsbad hatte eine gute Standzeitstabilität. Daher sind unsere Ergebnisse in dieser Arbeit eine nützliche Referenz für die Anwendung von stromlosen Ni-P-Nanopartikel-Verbundbeschichtungen auf Mg-Legierungen.
Methoden
Vorbereitung der Verbundbeschichtungen
In dieser Arbeit wurde eine AZ91D-Druckguss-Mg-Legierung mit einer Größe von 2 cm × 1 cm × 0.5 cm als Versuchsmaterial verwendet, das die chemische Zusammensetzung in Gew.-% enthält:8.5 Al, 0.34 Zn, 0.1 Si, 0.03 Cu, 0.002 Ni , 0,005 Fe und 0,02 andere und Rest Mg. Das AZ91D-Substrat wurde nacheinander ohne Polieren poliert. 500 und 1000 SiC-Papier, mit entionisiertem Wasser gespült und 5 min in alkalische Lösung bei 65 °C getaucht, gefolgt von einer Säurebeizung in einer Chromsäurelösung (CrO3 200 g/L) für 60 s. Danach wurde das Mg-Legierungssubstrat in eine Fluorwasserstoffsäurelösung mit einer Konzentration von 380 ml/l zur Aktivierungsbehandlung etwa 10 min eingetaucht. Das Mg-Substrat wurde bei jedem Schritt mit entionisiertem Wasser gereinigt. Die grundlegende Badzusammensetzung und die Betriebsbedingungen des stromlosen Vernickelns von Magnesiumlegierungen wurden wie folgt dargestellt:35 g/L NiSO4 ⋅6H2 O, 35 g/L Milchsäure, 30 g/L Na2 H2 PO2 ⋅H2 O, 10 g/l NH4 HF2 , 3 mg/L Stabilisierungsmittel, pH 4,5~7,0 und Temperatur 70~90 °C. Das stromlose Plattierungsbad wurde in einem Becherglas aufbewahrt, das in ein thermostatgesteuertes Wasserbad gestellt wurde. Ein elektrischer Rührer mit digitaler Anzeige wurde verwendet, um die Rührkraft bereitzustellen. Die durchschnittliche Partikelgröße des Nano-Al2 O3 Teilchen beträgt etwa 50 nm. Das Nano-Al2 O3 Partikel wurden vor dem stromlosen Plattieren im Bad unter den Bedingungen von Ultraschallwellen angemessen dispergiert.
Tests für Abscheidungsrate und Stabilität von Beschichtungsbädern
Um die Wirkung von Nano-Al2 . zu untersuchen O3 Partikel auf die Abscheidungsrate des stromlosen Vernickelungsbades, die Abscheidungsrate wird in Gl. (1).
$$ v=\frac{\Delta w\times {10}^4}{\rho St} $$ (1)wo v , ρ , S , t , und △w repräsentieren Abscheiderate (μm/h), Dichte der Ni-P-Beschichtung (~ 7,9 g/cm 3 ), Oberfläche des Mg-Substrats (cm 2 ), Abscheidungszeit (h) bzw. Beschichtungsgewicht (g). Außerdem ist der Gehalt an Nano-Al2 O3 Partikel in der Beschichtung wurden durch Wägeverfahren unter Verwendung einer elektronischen Waage (AR2140, Ohaus) abgeschätzt. Um die Stabilität des stromlosen Plattierungsbades zu bewerten, wurde ein periodischer Zyklustest (oder Metal Turnover, MTO) verwendet, um die Lebensdauer und Stabilität des Bades zu bewerten. Hier hat 1 MTO definiert, dass das Abscheidungsgewicht von Ni der Anfangskonzentration von Ni 2+ . entspricht im Bad. Nimmt man 1 L Galvanisierbad als Beispiel, erhält man etwa 7,8 g Ni aus dem Bad \( \left({C}_{{\mathrm{Ni}}^{2+}}=7,8\kern0.5em \mathrm {g}/\mathrm{L}\right) \) als 1 MTO. Zusätzlich eine frische Mischlösung (\( {\mathrm{Ni}}^{2+}:{\mathrm{H}}_2{\mathrm{PO}}_2^{2-}=1:3 \) im Molverhältnis) wurde in das Plattierungsbad gegeben, wenn das Bad eine niedrige Abscheidungsrate aufwies. Der Stabilitätstest wurde bis zur Zersetzung des Plattierungsbades beendet. Somit kann der Ausdruck von MTO als Gl. (2).
$$ \mathrm{MTO}=M/m $$ (2)M und m repräsentieren das kumulative Abscheidungsgewicht von Ni und die Konzentration von Ni 2+ jeweils im Galvanisierbad.
Materialcharakterisierung
Die Oberflächenmorphologie der Beschichtung wurde unter Verwendung eines Rasterelektronenmikroskops (SEM, Hitachi S-4800) beobachtet. Die Struktur der Beschichtung wurde mit dem Röntgendiffraktometer (XRD, D/Max-2200, Japan) mit einem CuKα . untersucht Strahlung (γ = 0,154 nm).
Elektrochemische Messung
Ein potentiodynamischer Polarisationstest wurde an einem elektrochemischen Analysator (CHI800, Chenhua, China) durchgeführt. Das elektrochemische Experiment wurde in einer 3,5 Gew.-% wässrigen NaCl-Lösung unter Verwendung einer klassischen Drei-Elektroden-Konfiguration durchgeführt, die aus einer Arbeitselektrode (Probe, 1 cm 2 ), eine Gegenelektrode (Platin) und eine Referenzelektrode (gesättigte Kalomelelektrode). Während des potentiodynamischen Sweep-Experiments wurde die Probe zunächst 30 min in die Elektrolytlösung getaucht, um das Leerlaufpotential (E 0 ). Der Tafel-Plot wurde aus den aufgezeichneten Daten transformiert und die Korrosionsstromdichte (i korr ) wurde durch Extrapolation des geraden Abschnitts der anodischen und kathodischen Tafel-Linien bestimmt. Die Sweep-Rate des Experiments betrug 5 mV/s und wurde bei 25 °C durchgeführt. Die Mikrohärten der Magnesiumlegierung mit verschiedenen Verbundbeschichtungen wurden unter Verwendung eines HXD-1000 Mikrohärtetesters mit einem Vicker-Eindringkörper bei einer Belastung von 100 g und einer Haltbarkeit von 15 s bewertet. Zur Bewertung der Haftung von Beschichtungen wurde ein Thermoschocktest durchgeführt [23]. Es wurde wie folgt beschrieben:in einer Luftatmosphäre das Mg-Substrat mit Ni-P-Beschichtung oder Ni-P-Al2 O3 Die Beschichtung wurde in einen Hochtemperatur-Kastenwiderstandsofen eingebracht und mit einer Aufheizrate von 20 °C min −1 . auf 250 ± 10 °C erhitzt dann in kaltem Wasser abgeschreckt. Dieser Vorgang wurde 20 Mal wiederholt.
Ergebnisse und Diskussion
Abbildung 1 zeigt die Auswirkungen der Konzentration von Nano-Al2 O3 Partikel, Rührgeschwindigkeit, pH und Temperatur auf die Abscheidungsrate und Al2 O3 Gehalt an Verbundbeschichtungen. Wie in Fig. 1a zu sehen ist, nimmt die Abscheidungsrate mit der Zunahme von Al2 . leicht ab O3 Partikelkonzentration von 0 bis 15 g/L. Andererseits ist das Al2 O3 Gehalt der Verbundbeschichtungen steigt allmählich an, während die Konzentration von Al2 O3 Partikel steigt von 0 auf 10 g/L. Sie nimmt jedoch stattdessen ab, wenn die Konzentration von Al2 O3 Partikel ist höher als 10 g/L. Diese Änderung ist auf die Aggregation von Partikeln bei hohen Konzentrationen zurückzuführen, die das gemeinsame Abscheidungsverhalten von Ni-P mit Al2 . schwächt O3 . In 1b werden, wenn die Rührgeschwindigkeit auf 300–400 U/min eingestellt ist, die Abscheidungsrate und der Al 2 O3 Der Gehalt an Verbundbeschichtungen beträgt 18 µm/h bzw. 3,6 %. Die Ergebnisse zeigen, dass die Dispersivität von Al2 O3 Partikel im Plattierungsbad ist bei diesem Rührgeschwindigkeitsbereich am besten. Wie bei einem sauren Verbundbeschichtungsbad, der Einfluss des pH-Werts auf die Abscheidungsrate und Al2 O3 Gehalt an Beschichtungen ist in Abb. 1c dargestellt. Die maximale Abscheidungsrate beträgt bis zu 18,5 μm/h, wenn der pH-Wert im Bereich von 6,0 bis 6,5 liegt, während der Al2 O3 Der Gehalt an Beschichtungen steigt mit dem pH-Wert fast an. Abbildung 1d zeigt, dass sowohl die Abscheidungsrate als auch der Al2 O3 Der Gehalt an Verbundbeschichtungen nimmt mit der Temperatur zu, da die Aktivität von Ionen und Partikeln verbessert wird und auch die Reaktionsgeschwindigkeit des Verbundbades bei hoher Temperatur beschleunigt wird. Allerdings werden die Stabilität des Galvanisierbades und die Porosität der Beschichtungen bei hohen Temperaturen (> 85 °C) schlechter [13, 22]. Basierend auf den obigen Analyseergebnissen werden die vorläufigen Prozessparameter und Betriebsbedingungen des Verbundbades für Magnesiumlegierung bestimmt, d. h. 35 g/L NiSO4 ⋅6H2 O, 35 g/L Milchsäure, 30 g/L Na2 H2 PO2 ⋅H2 O, 10 g/l NH4 HF2 , 10 g/l Nano-Al2 O3 Partikel, 3 mg/L Stabilisierungsmittel, pH = 6.0~6.5, T = 85 °C und Rührgeschwindigkeit bei 350 U/min.
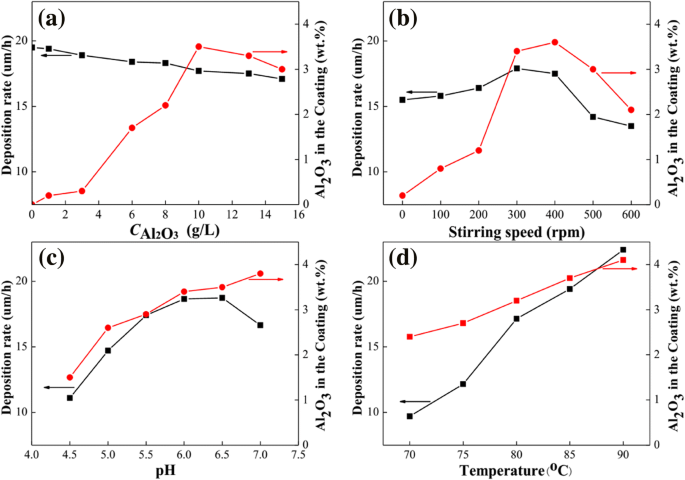
Auswirkungen von Prozessparametern auf die Abscheidungsrate und Al2 O3 Gehalt an Beschichtungen
Untersuchung des Abscheidungsprozesses von Ni-P-Al2 O3 Beschichtungen, die Änderung der Oberflächenmorphologiebilder von Magnesiumlegierungen mit der Abscheidungsreaktionszeit ist in Abb. 2 dargestellt. Zur vergleichenden Analyse stellen Abb. 2a–c den Abscheidungsprozess einer Ni-P-Beschichtung dar, während Abb. 2d–f den co -Abscheidungsprozess von Ni-P-Al2 O3 (3,6 Gew.-%) Verbundbeschichtungen. Abbildung 2a ist das Morphologiebild des Eintauchens des Mg-Substrats in das Beschichtungsbad für 0,5 min, wobei eine große Anzahl von Partikeln mit kubischer Struktur auf seiner Oberfläche verteilt ist. Diese kubischen Partikel werden als MgF2 . bestätigt , das sich hauptsächlich im HF-Aktivierungsprozess bildet, in Übereinstimmung mit den Literaturberichten [23, 27]. Die Morphologie des Bildes von Fig. 2d unterscheidet sich jedoch deutlich von Fig. 2a. Der Hauptunterschied zeigt, dass das MgF2 Partikel in Fig. 2d sind geringer als in Fig. 2a. Darüber hinaus sind viele Nano-Al2 O3 Partikel werden auf der Oberfläche des Mg-Substrats beobachtet. Die Morphologieänderung geht auf Al2 . zurück O3 Partikel, die bei hoher Temperatur und Rührprozess kontinuierlich auf die Oberfläche der Magnesiumlegierung auftreffen. Wenn die stromlose Ni-P-Plattierungszeit bis zu 5 min beträgt, wie in Fig. 2b zu sehen, wachsen die Ni-Partikel allmählich und bedecken dann die gesamte Oberfläche der Magnesiumlegierung. Aber für die stromlose Verbundbeschichtung (siehe Abb. 2e), die größeren Ni-Partikel und Nano-Al2 O3 Partikel werden auf der Oberfläche der Magnesiumlegierung beobachtet, und das Ni-P-Al2 O3 Beschichtungen bedecken das Mg-Substrat innerhalb von 5 min nicht vollständig. Dies weist darauf hin, dass die Wachstumsrate von Ni-P-Al2 O3 Beschichtungen im Verbundbad ist geringer als bei Ni-P-Beschichtungen im Bad ohne Al2 O3 Partikel. Dies ist ein Beweis, der die Ursache der geringen Abscheidungsrate im Verbundbeschichtungsbad unterstützt. Wenn die stromlose Plattierungszeit 30 Minuten lang durchgeführt wird, wird die Morphologie der Ni-P-Beschichtung und des Ni-P-Al2 O3 Beschichtungen ist in Fig. 2c bzw. f gezeigt. Bei der Ni-P-Beschichtung weist die Oberfläche eine dichte und knötchenförmige Struktur mit einer durchschnittlichen Größe von 3 µm auf. Aber in Abb. 2f ist die gemittelte Knollengröße von Ni-P-Al2 O3 Verbundbeschichtungen ist anscheinend kleiner als die von Ni-P-Beschichtungen. Darüber hinaus ist deutlich zu beobachten, dass das Nano-Al2 O3 Partikel eingebettet in Ni-P-Beschichtung. Wichtig aus Sicht der Oberflächenverteilung von Al2 O3 Partikel, die Verteilung von Al2 O3 Partikel in Fig. 2f ist deutlich geringer als in Fig. 2c, e. Dieses Ergebnis zeigt, dass die Abscheidung von Ni-P dominant ist, während die Abscheidung von Al2 O3 Partikel werden nach einer Abscheidungsreaktionszeit von 5 min untergeordnet. Ähnliche Schlussfolgerungen können auch aus dem relativen Gehalt von Al2 . gezogen werden O3 Partikel in den Beschichtungen (Abb. 1). Mit anderen Worten, die Wirkung von Al2 O3 Partikel auf dem Abscheidungsprozess sind hauptsächlich in der Anfangsphase der stromlosen Vernickelung vorhanden.
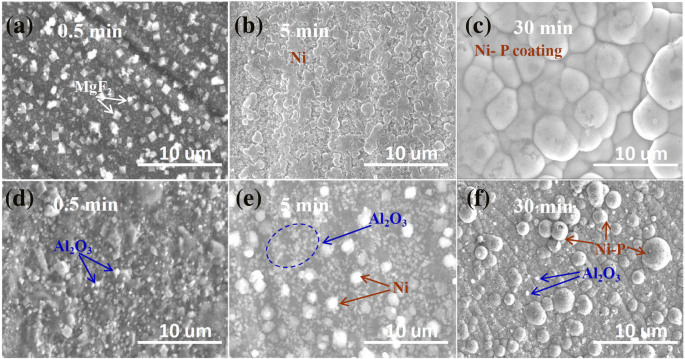
Oberflächenmorphologie der Ni-P-Beschichtung (oben, a -c ) und Ni-P-Al2 O3 Verbundbeschichtungen (unten, d -f ) zu unterschiedlichen Abscheidungszeiten
Um die Wirkung von Nano-Al2 . zu erforschen O3 Partikel auf der Struktur der Ni-P-Beschichtung, die XRD-Muster der AZ91D Mg-Legierung, Ni-P-Beschichtung und Ni-P-Al2 O3 Verbundbeschichtungen werden in Abb. 3 analysiert. Wie in Abb. 3 zu sehen ist, konzentriert sich der Beugungswinkel der Kristallebenen der Magnesiumlegierung hauptsächlich im Bereich von 30°~70°, zum Beispiel α (10\( \overline{1} \)0) 32,2°, α (0002) 34,2°, β (10\(\overline{1}\)1) 36,8° usw. Bei einer mit einer Ni-P-Beschichtung beschichteten Mg-Legierung zeigt das Beugungsmuster der Ni-P-Beschichtung einen sich verbreiternden Peak und eine hochintensive Beugung bei 44,7°, dass kann der (111)-Kristallebene einer kubisch-flächenzentrierten (fcc) Phase von Nickel zugeschrieben werden (Tabelle 1) [28]. Darüber hinaus weist die Existenz eines solch breiten Peaks auf die Bildung einer Ni-P-Beschichtung mit einer gemischten amorphen Kristallstruktur hin. Nach dem Plattieren des Ni-P-Al2 O3 (3,6 Gew.-%) Verbundbeschichtungen, drei neue Beugungspeaks sind offensichtlich bei 25,6°, 43,5° und 73,2° zu finden. Diese Peaks werden den charakteristischen Beugungspeaks von Al2 . zugeschrieben O3 verglichen mit der PDF-Karte Nr. 88-0826. Daher Ni-P-Al2 O3 Verbundbeschichtungen werden auf der Oberfläche der Mg-Legierung abgeschieden. Darüber hinaus verschiebt sich der Beugungspeak der (111)-Kristallebene von Ni auf 45,2° (siehe Tabelle 1) in Ni-P-Al2 O3 Verbundbeschichtungen, was auf Nano-Al2 . hindeutet O3 Partikel haben einen gewissen Einfluss auf den (111) Kristallebenenabstand von Ni. Nach der Bragg-Formel ist nλ = 2d Sündeθ (n = 1, 2, 3, ..., λ = 0,154 nm, d und θ Interplanarabstand bzw. Beugungswinkel darstellen), wird der (111)-Kristallebenenabstand von Ni um etwa 3% durch Al2 . verringert O3 Partikel. Darüber hinaus sind sowohl die (111)-Beugungspeaks von Ni in der Ni-P-Beschichtung als auch Ni-P-Al2 O3 Verbundbeschichtungen wurden jeweils durch die Gauss-Funktion angepasst. Das Ergebnis zeigt, dass die Halbwertsbreite (FWHM) dieses Beugungspeaks in Ni-P-Al2 O3 Verbundbeschichtungen ist breiter als bei der Ni-P-Beschichtung (Tabelle 1). Nach der Scherrer-Formel ist D = Kγ /B cosθ (D , K , B kristallines Korn, Scherrer-Konstante bzw. FWHM darstellen), das kristalline Korn von Ni-P-Al2 O3 Verbundbeschichtungen werden durch Al2 . um ca. 8% reduziert O3 Partikel im Vergleich zur Ni-P-Beschichtung. Dies impliziert, dass Nano-Al2 O3 Partikel verfeinern die Größe des Ni-Kristallkorns, was mit dem oben beobachteten Ergebnis der SEM übereinstimmt.
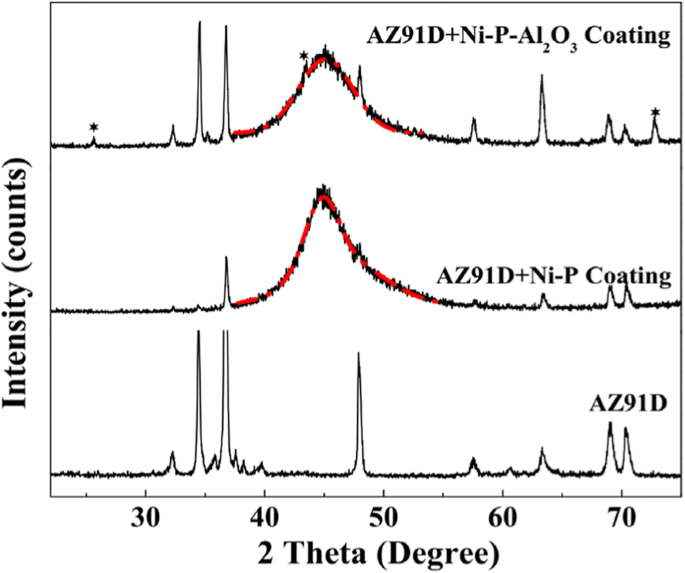
XRD-Muster des AZ91D-Substrats, der Ni-P-Beschichtung und Ni-P-Al2 O3 (3,6 Gew.-%) Verbundbeschichtungen
Abbildung 4 und Tabelle 2 zeigen die Polarisationskurven und Korrosionsschutzparameter von AZ91D Mg-Legierungssubstrat, Ni-P-Beschichtung und Ni-P-Al2 O3 Verbundbeschichtungen in einer 3,5 Gew.-% wässrigen NaCl-Lösung bei Raumtemperatur, bzw.. Die Kathodenreaktion in den Polarisationskurven entspricht der Wasserstoffentwicklung, während die anodischen Polarisationskurven die wichtigsten charakteristischen Reaktionsprozesse der Korrosionsbeständigkeit sind [29]. Für das AZ91D Mg-Legierungssubstrat wird ein aktivierungsgesteuerter anodischer Prozess beobachtet, wenn das angelegte Potenzial in den anodischen Bereich ansteigt. Darüber hinaus wird es in Elektrolytlösung ernsthaft gelöst und sein Korrosionspotential (E korr ) wird bei − 1,47 V gelesen. Aber für das E korr der Ni-P-Beschichtung zeigt sie eine signifikante positive Verschiebung auf − 0,51 V im Vergleich zu der des Mg-Legierungssubstrats (− 1,47 V) und die Korrosionsstromdichte (i korr ) sinkt offensichtlich von 1,4 × 10 −4 A/cm 2 des Substrats auf 3,1 × 10 –6 A/cm 2 der Ni-P-Beschichtung (siehe Tabelle 2). Wie für Ni-P-Al2 O3 (1,7~4,2 Gew.-%) Verbundbeschichtungen, hier das Al2 O3 Der Gehalt an Beschichtungen wird durch das Wiegeverfahren ermittelt. Wie in Tabelle 2 zu sehen, sind alle E korr der Verbundbeschichtung positive Verschiebung und i korr der Verbundbeschichtungen nehmen im Vergleich zur Ni-P-Beschichtung ab, was darauf hindeutet, dass Ni-P-Al2 O3 Beschichtungen haben eine höhere Leistung in der Korrosionsbeständigkeit. Hier ist die Ni-P-Beschichtung mit 3,6 Gew.-% Al2 O3 zeigt das höchste E korr (− 0.35 V) und niedrigstes i korr (4,5 × 10 −7 A/cm 2 ). Das E korr und i korr von Ni-P-Al2 O3 (4,2 Gew.-%) ändern sich auf − 0,41 V und 1,0 × 10 −6 A/cm 2 , bzw. Es kann sein, dass Al2 O3 Partikel erhöhen die Porosität der Ni-P-Beschichtung und verringern die Leistung von Verbundbeschichtungen. Daher ist das Al2 O3 Der Gehalt an Verbundbeschichtungen hat einen wichtigen Einfluss auf die Korrosionsbeständigkeit der Verbundbeschichtungen. Es hängt auch mit der Struktur zusammen, einschließlich der Kristallebenenabstände und der Korngröße der Beschichtungen (Abb. 3).
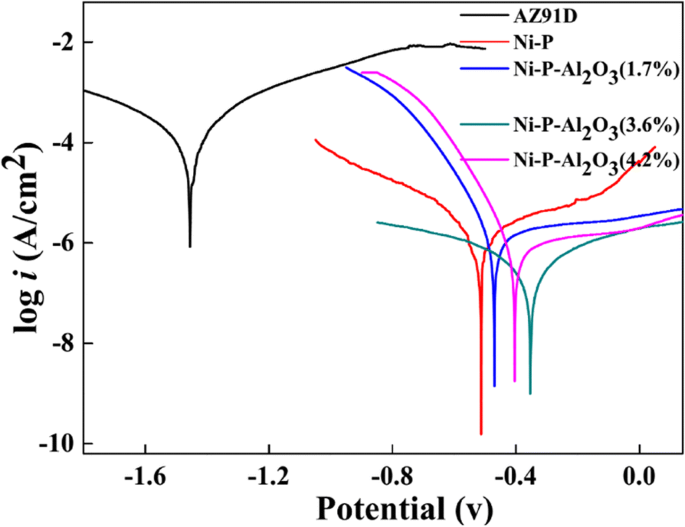
Polarisationskurven des AZ91D-Substrats, der Ni-P-Beschichtung und des Ni-P-Al2 O3 Verbundbeschichtungen
Zur Prüfung der Mikrohärte der Beschichtungen wurde die durchschnittliche Dicke aller Beschichtungen mit 18 µm bestimmt, die aus Abscheiderate und Abscheidezeit abgeschätzt wurde. Die Ergebnisse von Mikrohärtetests des Mg-Legierungssubstrats und der Beschichtungen mit verschiedenen Al2 O3 Der Inhalt ist in Abb. 5 dargestellt. Wie in Abb. 5 zu sehen ist, beträgt die Mikrohärte der blanken AZ91D Mg-Legierung nur etwa 120 HV, während die Mikrohärte des mit einer Ni-P-Beschichtung beschichteten Mg-Legierungssubstrats bis zu beträgt 520 HV. Sie ist um 400 HV höher als das Substrat, was darauf hinweist, dass die Ni-P-Beschichtung die Härte der Substratbeschichtung effektiv verbessern kann. Als Ergebnis wird die Verschleißfestigkeit des Mg-Legierungssubstrats durch die Ni-P-Beschichtung verbessert. Darüber hinaus ist das Ni-P-Al2 O3 Verbundbeschichtungen zeigen eine deutliche Zunahme der Mikrohärte, wenn der Gehalt an Al2 O3 in der Beschichtung von 0 auf 3,6 Gew.-% erhöht. Daher Ni-P-Al2 O3 (3,6 %) Verbundbeschichtungen weisen den höchsten Härtewert bei 638 HV auf. Der Grund liegt in Nano-Al2 O3 Partikel optimieren die Phasenstruktur (siehe Abb. 3) der Ni-P-Legierung und erhöhen die Mikrohärte von Beschichtungen. Der Inhalt von Al2 O3 in den Verbundbeschichtungen erreicht 4,2 Gew.-%, und die Mikrohärte der Beschichtungen nimmt stattdessen auf 576 HV ab. Dies bedeutet, dass ein höherer Gehalt an Nanopartikeln die Ni-P-Kristallstrukturen beeinträchtigen kann, was zu einer ungünstigen Leistung der Verbundbeschichtungen führt.
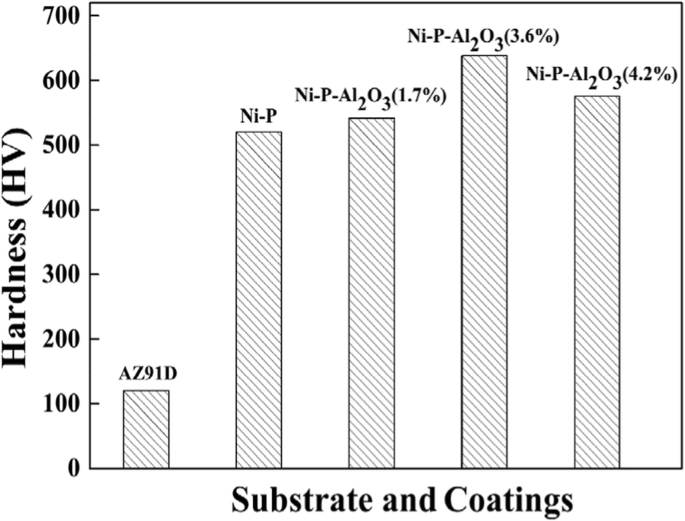
Härte des AZ91D-Substrats, der Ni-P-Beschichtung und des Ni-P-Al2 O3 Verbundbeschichtungen
Die Haftung zwischen den Beschichtungen und dem Mg-Legierungssubstrat wurde durch einen Thermoschocktest gemäß dem Versuchsabschnitt durchgeführt. In 20 Zyklentests wurden sowohl die Ni-P-Beschichtung als auch Ni-P-Al2 O3 Verbundbeschichtungen hafteten gut an dem Mg-Legierungssubstrat. Die Defekte wie Risse, Blasenbildung und Abplatzungen wurden während des Testprozesses nicht beobachtet, was darauf hindeutet, dass das Ni-P oder Ni-P-Al2 O3 Beschichtungen hatten eine gute Haftung mit dem Mg-Legierungssubstrat gegen den Thermoschockprozess. Darüber hinaus wurden auch Querschnittsmorphologiebilder zwischen den Beschichtungen und dem Mg-Legierungssubstrat unter Verwendung von SEM beobachtet. Wie in Fig. 6 zu sehen ist, zeigt es ferner, dass es keinen offensichtlichen Defekt zwischen den Beschichtungen und dem Substrat im Thermoschocktest gibt. Wichtig ist, dass der Thermoschocktest und die Querschnittsbeobachtung darauf hindeuten, dass Nano-Al2 O3 Partikel haben keinen Einfluss auf die Haftung von Verbundbeschichtungen.
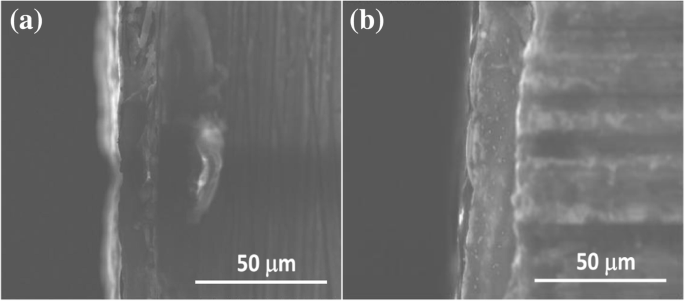
Querschnittsmorphologiebilder der Ni-P-Beschichtung (a ) und Ni-P-Al2 O3 (3,6 Gew.-%) Verbundbeschichtungen (b )
In der vorliegenden Arbeit 1-L-Beschichtungsbäder ohne und mit Nano-Al2 O3 Partikel (10 g/l) wurden jeweils hergestellt. Hier wurde der anfängliche Gehalt an Nickelquelle im Plattierungsbad mit 7,8 g berechnet und die Beladungskapazität des Bades wurde auf 0,5 dm 2 . eingestellt /L. Nach den Regeln des periodischen Zyklustests (siehe experimenteller Abschnitt) wurde zuerst die MTO des stromlosen Ni-P-Beschichtungsbades bewertet, und es wurden etwa 48,2 g Ni-P-Legierung erhalten. Hier wurde mittels EDS-Analyse ein Nickelgehalt von 90 % in der Ni-P-Beschichtung identifiziert (siehe Abb. 7). Somit kann der Nickelgehalt in der Beschichtung mit 43,4 g berechnet werden. Das heißt, das MTO des Plattierungsbades ohne Al2 O3 Teilchen ist 5,6 unter Verwendung von Gl. (2). Wie für das stromlose Ni-P-Al2 O3 Verbundbeschichtungsbad, insgesamt 38,8 g Ni-P-Al2 O3 Beschichtungen wurden aus dem Verbundbad abgeschieden. Ebenso wurden 86,45 % Ni, 9,84 % P, 1,96 % Al und 1,75 % O durch EDS-Analyse bestimmt (Abb. 7). Daher kann der Nickelgehalt in den Verbundbeschichtungen mit 33,5 g berechnet werden und das MTO des Verbundbades beträgt 4,2. Aus den Ergebnissen des periodischen Zyklustests geht hervor, dass der Betriebszyklus des Verbundbeschichtungsbades 1,4 MTO weniger ist als der des stromlosen Ni-P-Beschichtungsbades. Das bedeutet, dass Nano-Al2 O3 Partikel reduzieren die Lebensdauer des stromlosen Beschichtungsbades. Trotzdem ist das Ni-P-Al2 O3 Verbundbeschichtungen haben noch eine potenzielle Anwendung im Bereich der Magnesiumlegierungen.
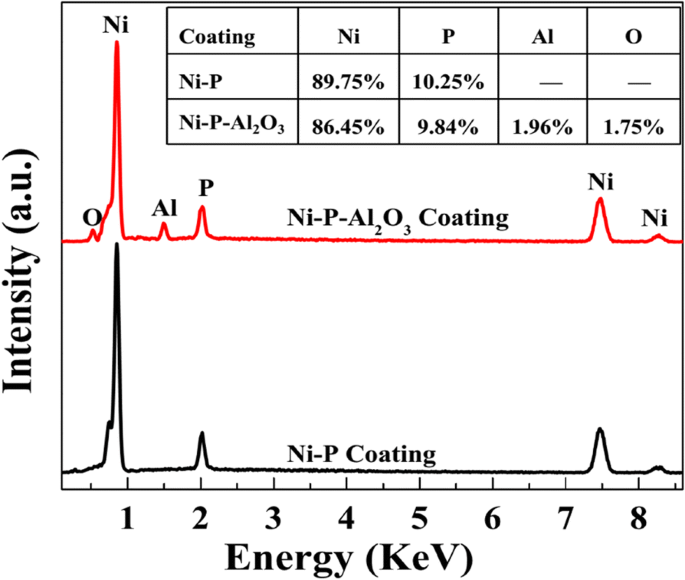
Die EDS-Spektren der Ni-P-Beschichtung und des Ni-P-Al2 O3 Verbundbeschichtungen
Schlussfolgerungen
Zusammenfassend haben wir ein stromloses Verbundbeschichtungsbad und Betriebsbedingungen für die gemeinsame Abscheidung von Ni-P-Al2 . erhalten O3 Beschichtungen auf Magnesiumlegierung, d. h. 35 g/L NiSO4 ⋅6H2 O, 35 g/L Milchsäure, 30 g/L Na2 H2 PO2 ⋅H2 O, 10 g/l NH4 HF2 , 10 g/l Nano-Al2 O3 Partikel, 3 mg/L Stabilisierungsmittel und pH = 6.0~6.5, T =85 °C und Rührgeschwindigkeit bei 350 U/min. Morphologische Charakterisierung und Phasenstrukturanalyse der Verbundbeschichtungen zeigten, dass Nano-Al2 O3 Partikel hatten einen wichtigen Einfluss auf den Wachstumsprozess und die Phasenstrukturen (Kristallebenenabstand und Korngröße) der Beschichtungen. 3,6 Gew.-% Al2 O3 -Gehalt verbesserte effektiv die Mikrohärte und Korrosionsbeständigkeit der Ni-P-Beschichtung. Darüber hinaus zeigte der Adhäsionstest, dass es fast keinen Unterschied zwischen Ni-P-Beschichtung und Ni-P-Al2 . gab O3 Glasur. Der Lebensdauertest ergab, dass die MTO des stromlosen Verbundbeschichtungsbads etwa 4 betrug. Kurz gesagt, stromloses Ni-P-Al2 O3 Verbundbeschichtung ist eine wichtige Technologie, um die Anwendung von Magnesiumlegierungen zu erweitern.
Abkürzungen
- E 0 :
-
Leerlaufpotential
- i korr :
-
Korrosionsstromdichte
- Mg:
-
Magnesium
- MTO:
-
Metallumschlag
- Ni-P:
-
Nickel-Phosphor
- SEM:
-
Rasterelektronenmikroskopie
- XRD:
-
Röntgenbeugung
Nanomaterialien
- Eigenschaften und Verwendung von Gegengewichten aus Wolframlegierung
- Eigenschaften und Verwendung von Kugeln aus Wolframlegierung
- Eigenschaften und Anwendungen von Wolfram-Kupfer-Legierung
- Anwendungen und Eigenschaften von Wolfram-Nickel-Eisen-Legierung
- Was ist eine Kobaltlegierung und was sind die Eigenschaften der Kobaltlegierung?
- Aluminiumeigenschaften und Legierungseigenschaften
- Herstellung und magnetische Eigenschaften von kobaltdotierten FeMn2O4-Spinell-Nanopartikeln
- Auf dem Weg zu TiO2-Nanofluiden – Teil 1:Vorbereitung und Eigenschaften
- Eigenschaften und Anwendungen von Kupfer-Nickel-Legierungen
- VDM® Legierung 40 B