Statistische Optimierung der Sol-Gel-Elektrospinnprozessbedingungen zur Herstellung von Polyamid 6/66-Nanofaserbündeln
Zusammenfassung
Polymere Nanofasern werden in der Textilindustrie intensiv untersucht, da mit ihnen eine Vielzahl von Funktionalitäten erreicht werden kann. In diesem Artikel wurden Polyamid 6/66 (PA 6/66)-Lösungen in verschiedenen Konzentrationen (12, 17 und 22 Gew.-%) hergestellt, um Nanofasern durch den grundlegenden Elektrospinnprozess zu erhalten, der durch Rasterelektronenmikroskop (REM) charakterisiert wurde. und Produktivität. Anschließend wurden im Elektrospinning-Sol-Gel-Verfahren Nanofaserbündel hergestellt, die durch REM und Zugversuche charakterisiert wurden. Aus den Ergebnissen der statistischen Optimierung auf der Grundlage einer Einweg-Varianzanalyse (ANOVA) mit Post-hoc-Tukey-HSD wurde festgestellt, dass Nanofaserbündel mit höherer Produktivität (1,39 ± ± 0,15 mg/min), Ziehverhältnis (9,0 ± ± 1,2) und Zugfestigkeit (29,64 ± 7,40 MPa) wurden mit einer Konzentration von 17 % erhalten. Schließlich wurde eine thermische Charakterisierung durch Differential Scanning Calorimetry (DSC) durchgeführt, wobei Hinweise auf ein T . gefunden wurden g und T m Reduktion der Nanofasern gegenüber PA 6/66 Pellets und Nanofaserbündeln.
Hintergrund
Nylon ist ein als Polyamid klassifiziertes Polymer, das 1934 von Wallace Hume Carothers entdeckt wurde; es wird je nach Verarbeitungsbedingungen als Faser und Kunststoff hergestellt [1]. Kommerziell gibt es verschiedene Arten von Nylon, Nylon 6, Nylon 66, Nylon 6, 10 usw., die die funktionelle Amidgruppe (–CO-NH-) gemeinsam haben [2]. Dieses Polymer wird zur Herstellung von Blasfolien und Monofilamenten durch Spinnverfahren verwendet und kann copolymerisiert werden. Dies ist der Fall bei Nylon 6/66, das im Vergleich zu Nylon 6 mit einer niedrigeren Schmelztemperatur hergestellt wird. In den letzten Jahren wurde Nylon in zahlreichen Anwendungen wie Damenstrümpfen, Fallschirmen, Reißverschlüssen, Angelschnüren, Brautschleiern, Teppichen verwendet , Musiksaiten und Seile [3].
Konventionelle Filament- und Nylonfaden-Transformationsverfahren sind Nassspinnen, Trockenspinnen und Gelspinnen und ermöglichen die Herstellung von Filamenten zwischen 20 und 400 μm Durchmesser [4]. Diese Prozesse, die aus polymeren Lösungen durchgeführt werden, sind konzentrationsabhängig, da ihre Variation das Streckverhältnis und damit die mechanischen Eigenschaften der Fasern beeinflusst [5].
Das Elektrospinnverfahren [6] wird auch im Nanometerbereich verwendet, um Nylonfasern mit kleinerem Durchmesser zu erhalten [7]. Es ermöglicht auch die Herstellung polymerer Nanofasern mit Polaritäten, Porositäten und einstellbaren Durchmessern, die zusätzlich an eine Vielzahl von Größen und Formen angepasst werden können. Außerdem ist es mit dieser Technik möglich, die Eigenschaften, Funktionalität und Zusammensetzung der Nanofasern über die Polymerkonzentration und die Elektrospinnparameter zu steuern [8]. Ramkrisnaet al. [9] bestätigen, dass das morphologische Ergebnis des Elektrospinnverfahrens eine hohe Konzentrationsabhängigkeit aufweist, ähnlich wie bei konventionellen Spinnverfahren [5]; da eine höhere Konzentration zu einer höheren Viskosität in der Polymerlösung führt, bewertet die Studie dieses Artikels aus diesem Grund die Konzentration des Polymers als einzigartige Variable in einem einfaktoriellen Design. Dies ist wichtig, um die Möglichkeit einer Durchführung im industriellen Maßstab zu bewerten.
Durch Elektrospinnen gewonnene polymere Nanofasern können in vielen Bereichen der Industrie eingesetzt werden:Gerüste, Sensoren, Filter, Membranen, Batterien, Schutzkleidung, Wundauflagen und Katalysatoren [10]. Im Textilbereich werden Nanofasern verwendet, um spezifische Funktionalitäten wie selbstreinigende Stoffe, Viren- und Bakterienabwehr, Temperaturkontrolle, Sensoren und Filter zu erhalten [11]. Aufgrund ihrer chemischen Eigenschaften und mechanischen Festigkeit wurden auch einige andere Textilanwendungen als antibakterielle Kleidung [12], Wundverbände [13] und Schutzkleidung [14] beschrieben.
Einige andere Forschungen, die sich auf den Elektrospinnprozess bezogen, passten ihn an ein Koagulationsbad und Zugzylinder an, um den Elektrospinn-Sol-Gel-Prozess zu entwickeln (siehe Abb. 1). Mit letzterem wurden Polyvinylalkohol (PVA)-Nanofaserbündel charakterisiert, hergestellt und als sekundäre Verstärkung in ultrafeinen Portlandzementpasten aufgebracht, um die Retraktion und Breite von Fissuren im frühen Alter des Abbindens zu reduzieren [15]. In einem von Wu et al. [16] stellten und charakterisierten sie aggregierte Nanofasern aus Polyamid 6/66 durch das Elektrospinnverfahren unter Verwendung von zwei Sammelwalzen, die sich mit einer Geschwindigkeit von 300 U/min drehten. Sie gaben an, dass die erhaltenen Fasern ein breites Anwendungsspektrum in Gewebegerüsten, Verbundverstärkungen und ultraempfindlichen Sensoren haben [17]. Unter Verwendung einer ähnlichen Methodik präsentieren wir hier die Ergebnisse und die statistische Optimierung unter Verwendung von ANOVA mit Post-hoc-Tukey-HSD-Test der morphologischen, mechanischen und thermischen Charakterisierung von Polyamid 6/66 (PA 6/66)-Nanofaserbündeln, die durch einen solchen Prozess erhalten wurden, wobei der Einfluss der Polymerkonzentration auf die Endeigenschaften der resultierenden Fasern für deren spätere Verwendung im Textilbereich wurde untersucht.
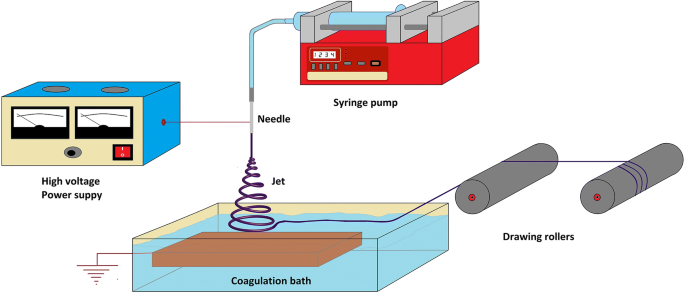
Elektrospinn-Sol-Gel-Prozess
Methoden
Materialien
Es wurde PA 6/66, Referenz Ultramid C40 L, Marke Basf verwendet. Als Lösungsmittel wurde eine Mischung aus Ameisensäure und Essigsäure und als Fällbad destilliertes Wasser verwendet.
Herstellung von Polyamidlösungen
Es wurden Lösungen in unterschiedlichen Konzentrationen von 12 Gew.-%, 17 Gew.-% und 22 Gew.-% hergestellt, wobei ein Gemisch aus Ameisensäure und Essigsäure als Lösungsmittel im Massenverhältnis 4:1 verwendet wurde [18], bei Raumtemperatur und kontinuierliches Rühren.
Grundlegender Elektrospinnprozess
Bei allen Verfahren, die mit den Lösungen in unterschiedlichen Konzentrationen durchgeführt wurden, wurde eine Spannung von 27,5 kV verwendet, die von einem Gerät von Gamma High Voltage Research Inc. Modell E30 geliefert wurde, das mit einer Metallnadel verbunden war, die 12 cm vom Kollektor entfernt angeordnet war. Der Fluss der Lösung wurde durch eine Spritzenpumpe von Braintree Scientific Syringe Pump Brand Inc. gesteuert, die zwischen 0,3 und 1 ml/h eingestellt war.
Elektrospinnender Sol-Gel-Prozess
Dieser Prozess wurde mit einem Fällbad aus destilliertem Wasser und einem Zugzylindersystem mit Geschwindigkeitsregelung durchgeführt. Wir erhielten Nanofaserbündel von PA 6/66 in drei Konzentrationen (12, 17 und 22%), nach einem vollständig zufälligen unifaktoriellen Design mit drei Replikaten und einem Signifikanzniveau von α = 0,05. Untersuchte Variablen waren die Produktivität bei der Abscheidung von Nanofasern, das Ziehverhältnis und die Zugfestigkeit des Nanofaserbündels. Es ist wichtig anzumerken, dass Konzentrationen unter 12 Gew.-% nicht bewertet wurden, da diese Bedingung in Vorversuchen die Bildung von elektrospinnenden Nanofasern nicht zuließ; in gleicher Weise wurden keine Konzentrationen über 22 Gew.-% bewertet, da die resultierende Viskosität sehr hoch war, was das Rühren bei der Herstellung der Lösung und das anschließende Fließen beim Elektrospinnverfahren behinderte. Außerdem wurden nur extreme Konzentrationen und der Mittelpunkt untersucht.
Charakterisierungstechniken
Für das grundlegende Elektrospinnverfahren wurde für jede Konzentration die Produktivität (mg/min) bei der Abscheidung von elektrogesponnenen Nanofasermatten aus PA 6/66 bestimmt. Anschließend wurden diese durch das Rasterelektronenmikroskop (REM) morphologisch charakterisiert.
Für den Sol-Gel-Elektrospinnprozess wurde nach Anpassung der Prozessvariablen (Spannung, Fluss, Nadel-Kollektor-Abstand), um einen stabilen und kontinuierlichen Elektrospinnstrahl zu erhalten, das Ziehverhältnis des Prozesses bestimmt, dann die erhaltenen PA 6/66-Nanofaserbündel wurden durch SEM und Zugversuch charakterisiert. Schließlich wurde der optimale Prozesszustand durch Differentialscanningkalorimetrie (DSC) charakterisiert.
SEM
Die Proben wurden in einer Vakuumbeschichtungsmaschine [Denton Vacuum Desk IV] etwa 200 s lang mit Gold beschichtet. Am Ende wurden sie in den Probenhalter eines Rasterelektronenmikroskops (JEOL JSM 6490 LV, Japan), ausgestattet mit Wolframfaden, abgelegt. Anschließend haben wir in der Kammer ein Vakuum von 30 Pa erzeugt, um Elektronen zu erzeugen, zu scannen und Bilder zu erhalten. Dann wurden mit der Bildsoftware die durchschnittlichen Nanofaserdurchmesser gemessen.
Zugversuch
Dreihundert Fäden von Nanofaserbündeln wurden mit einer Prüfmaschine (EZ-Test L, Shimadzu, Japan) bei einer Versuchsgeschwindigkeit von 30 mm/min und einer Referenzlänge von 50 mm gemäß den Standards ASTM D3822 getestet.
DSC
Um Phasenübergänge zu bestimmen, wurde die Technik der Differentialscanningkalorimetrie (DSC) gemäß dem Standard ASTM D3418-08 verwendet, der auf die Polymermaterialanalyse angewendet wird. Wir verwendeten ein Differentialscanningkalorimeter (DSC) (TA Instruments, Q20, USA) mit 5-mg-Proben, die in hermetisch verschlossenen Aluminiumtiegeln deponiert und zwei aufeinanderfolgenden Heizzyklen von 25 bis 250 °C bei 10 °C/min unterzogen wurden Geschwindigkeit mit 5 Minuten-Isothermen zwischen jedem Zyklus. Die an das Gerät angepasste TA Universal Analyzer® Software ermöglichte es, die Thermogramme zu erhalten, um die Glasübergangstemperaturen und die Materialverschmelzung zu bestimmen.
Ergebnisse und Diskussion
Produktivität des grundlegenden Elektrospinnprozesses
Abbildung 2 zeigt die Produktivitätsergebnisse (mg/min) in der Nanofaserabscheidung während des grundlegenden Elektrospinnprozesses bei verschiedenen Konzentrationen. Für diese Variable generierte die ANOVA ein p Wert von 0,015. Dies weist darauf hin, dass zumindest ein Median unterschiedlich ist. Dann wurde der Post-hoc-Tukey-Test angewendet und es zeigte sich, dass für diese Variable die Produktivitätswert-Durchschnittswerte bei Konzentrationen von 17 und 22% untereinander äquivalent sind, jedoch höher sind als die, die bei einer Konzentration von 12% erhalten wurden.
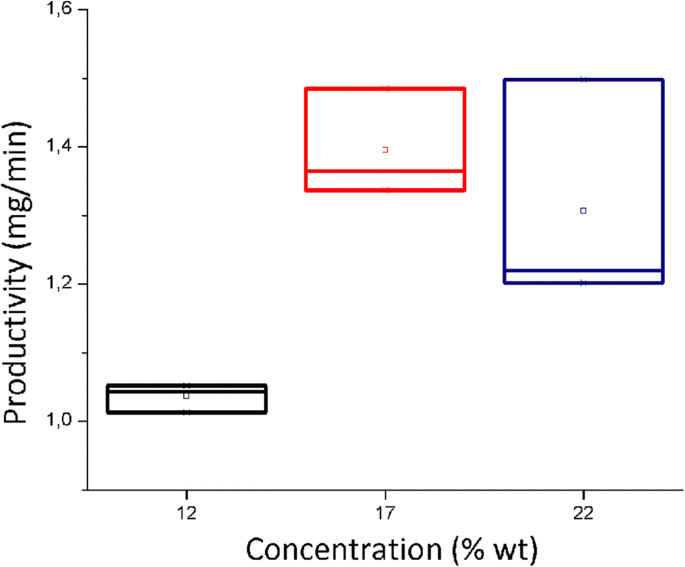
Produktivität des grundlegenden Elektrospinnprozesses
Morphologie/Morphologische Charakterisierung von PA 6/66 Nanofasern
Unter Verwendung des grundlegenden Elektrospinnverfahrens wurden PA 6/66 Nanofasern in unterschiedlichen Konzentrationen hergestellt. Die Ergebnisse zeigten, dass durch Erhöhung der Konzentration der Polymerlösung der Nanofaserdurchmesser zunahm, wie in REM-Mikrographien in Abb. 3 beobachtet. Dies liegt daran, dass eine Erhöhung der Konzentration einen rheologischen Verdickungseffekt auf die Lösung hat [19], der macht es aufgrund des Viskositätsanstiegs schwierig, Durchmesser zu reduzieren. Dieses Verhalten stimmt mit dem von Guerrini et al. [20], die PA 6/66-Nanofasern mit unterschiedlichen Molekulargewichten elektrosponnen. Darüber hinaus wurde festgestellt, dass die durchschnittlichen Durchmesser von Nanofasern mit einer Konzentration von 17% im Vergleich zu Nanofasern, die mit einer Konzentration von 12% erhalten wurden, um etwa 85% und für die Nanofasern, die mit einer Konzentration von 22% erhalten wurden, um 204% im Vergleich zu denen mit einer Konzentration von 17% anstiegen. .
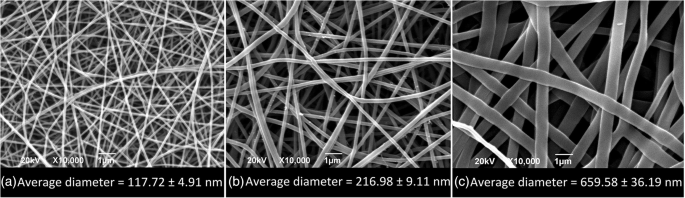
REM-Aufnahmen von elektrogesponnenen PA 6/66-Nanofasern bei unterschiedlichen Konzentrationen. a 12 Gew.-%, b 17 Gew.-% und c 22 Gew.-%
Ziehverhältnis im Elektrospinn-Sol-Gel-Prozess
Abbildung 4 zeigt die Ergebnisse des Ziehverhältnisses, die während des Elektrospinn-Sol-Gel-Prozesses bei verschiedenen Konzentrationen gemessen wurden. Für diese Variable generierte die ANOVA ein p Wert von 0,000, der anzeigt, dass mindestens ein Median unterschiedlich ist. Dann wurde der Post-hoc-Tukey-Test angewendet, der zeigt, dass für diese Variable der bei einer Konzentration von 17% erhaltene Ziehverhältnis-Median höher ist als der, der sich aus 12- und 22%-Konzentrationen ergibt, die untereinander äquivalent sind.
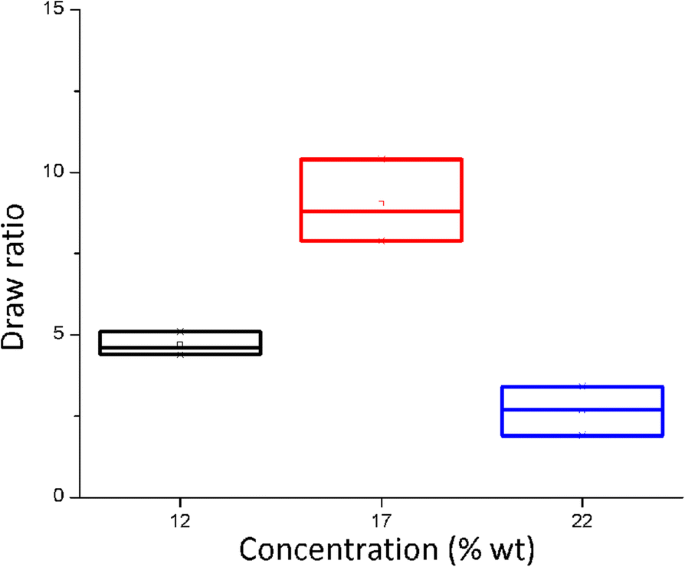
Ziehverhältnis des Elektrospinn-Sol-Gel-Prozesses
PA 6/66 Nanofaserbündel Morphologie/morphologische Charakterisierung
Unter Verwendung des Elektrospinn-Sol-Gel-Prozesses wurden Polyamid-Nanofaserbündel in unterschiedlichen Konzentrationen in der Lösung hergestellt. Nach Messung ihrer Durchmesser wurde festgestellt, dass der kleinere Durchschnitt bei einer Konzentration von 17 % erreicht wurde, wie in den REM-Mikrographien in Abb. 5 beobachtet. Die resultierenden Nanofaserbündel mit einer Konzentration von 17 % erreichten Durchmesser von fast der Hälfte der mit 12 bzw. 22% Konzentrationen. Dies liegt daran, dass der Prozess mit einer höheren Faserrückgewinnungsgeschwindigkeit und einem größeren Streckverhältnis durchgeführt wurde.
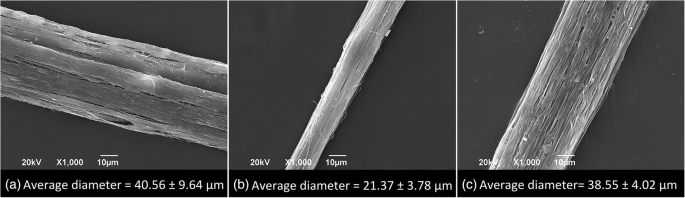
SEM-Aufnahmen von Polyamid-6/66-Nanofaserbündeln, die durch Elektrospinnen eines Sol-Gel-Prozesses bei verschiedenen Konzentrationen erhalten wurden. a 12 Gew.-%, b 17 Gew.-% und c 22% Gew.
Zugfestigkeit des Nanofaserbündels
Abbildung 6 zeigt das Kastendiagramm der Zugfestigkeit, gemessen über die Nanofaserbündel, die während des Elektrospinn-Sol-Gel-Prozesses bei verschiedenen Konzentrationen erhalten wurden. Für diese Variable generierte die ANOVA ein p Wert von 0,005, der anzeigt, dass mindestens ein Median unterschiedlich ist. Anschließend wurde der Post-hoc-Tukey-Test durchgeführt, der zeigte, dass für diese Variable die durchschnittliche Zugfestigkeit von Nanofaserbündeln, die bei einer Konzentration von 17% erhalten wurde, höher ist als das Ergebnis aus den 12 und 22% Konzentrationen, die untereinander äquivalent sind.
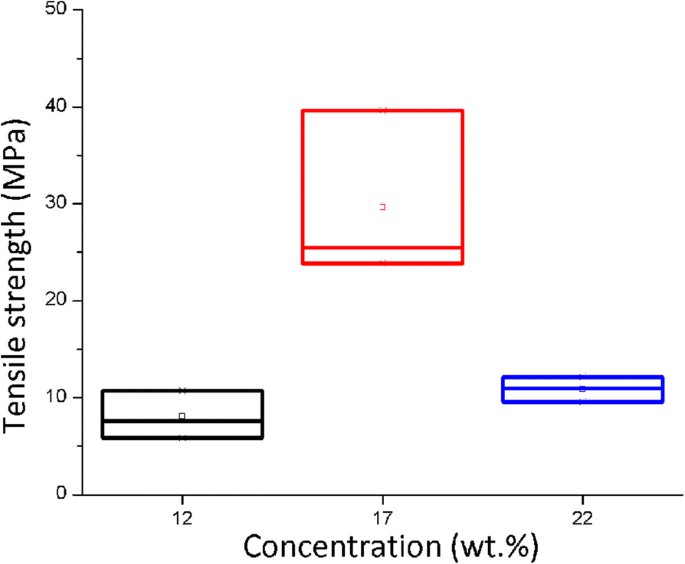
Zugfestigkeit von Polyamid 6/66 Nanofaserbündeln in unterschiedlichen Konzentrationen
Darüber hinaus war das durchschnittliche Ergebnis der Zugfestigkeit, das mit einer Konzentration von 17% Nylon (29,64 MPa) erhalten wurde, ähnlich dem von Wu et al. [16] in ihrer Forschung, die Ergebnisse von 66 Polyamid-Nanofasern präsentiert, die zuerst elektrogesponnen und dann mit Festigkeitswerten nahe 30 MPa gebogen wurden.
Optimale Prozessbedingungen
Frühere Ergebnisse zeigen, dass die Entwicklung des Elektrospinn-Sol-Gel-Prozesses aus einer PA 6/66-Lösung mit 17 Gew.-%. Konzentration ermöglicht die Herstellung von Nanofaserbündeln mit einer höheren Produktivität, einem höheren Ziehverhältnis und einer höheren Zugfestigkeit. Darüber hinaus zeigt Abb. 7 die Nanofaserbündel genauer, wodurch ein Anstieg der Oberflächenrauheit beobachtet werden kann. Dies ist wichtig, wenn diese Fasern als Verbundmaterialverstärkung verwendet werden sollen, da sie eine bessere mechanische Fixierung an der Matrix ermöglichen als herkömmliche synthetische Fasern, die normalerweise eine glatte Oberfläche haben. Darüber hinaus haben diese Fasern ein hohes Verhältnis von Fläche zu Volumen und ein hohes Aspektverhältnis, was ihnen Potenzial für Anwendungen im Design von Kleidung, Filtern und Nanokompositen verleiht [21].
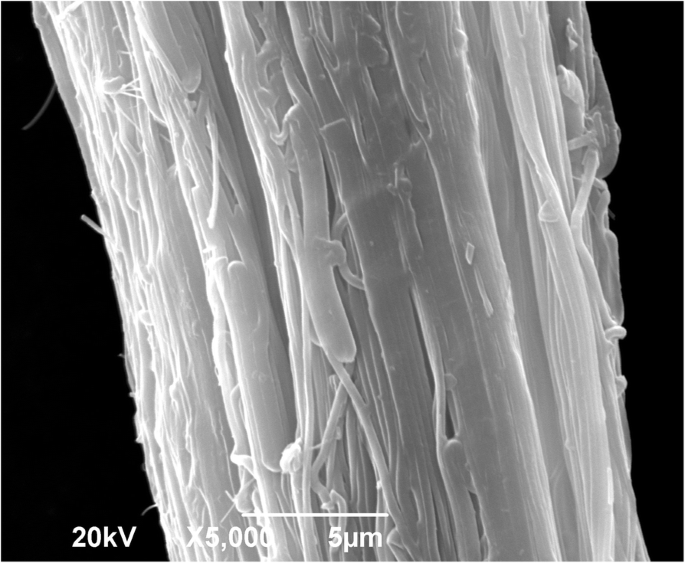
REM-Aufnahme der Oberfläche von PA 6/66 Nanofaserbündeln
Thermische DSC-Analyse der Nanofaserbündel im optimalen Zustand
Ausgehend vom optimalen Zustand bei einer Konzentration von 17% haben wir eine thermische Analyse jeder der Umwandlungsstufen durchgeführt, da das Material in Pellets vorliegt, sich in Nanofasern verwandelt und schließlich in Nanofaserbündel umgewandelt wird. Abbildung 8 zeigt die Kalorimetrie-Testergebnisse, die durch DSC für jede Stufe erhalten wurden.
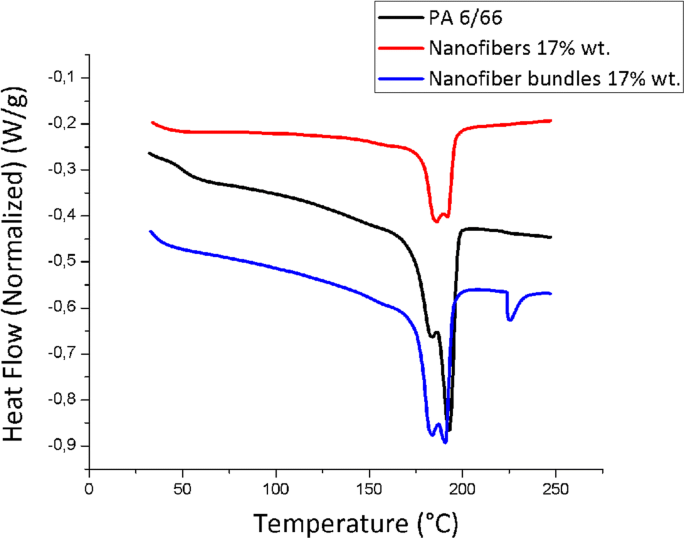
Resultierende Nanofaserbündel-Thermogramme mit optimalem Zustand, erhalten durch DSC
Basierend auf diesen Thermogrammen haben wir die Glasübergangstemperatur (T g ), die Schmelztemperatur (T m ), die Schmelzwärme (ΔH m ) und den Kristallinitätsgrad (X c ). Diese Ergebnisse können in Tabelle 1 eingesehen werden.
Es kann vom T . aus beobachtet werden g ergeben, dass Nanofasern bei einer Konzentration von 17% eine höhere intermolekulare Mobilität aufweisen als die Nanofaserbündel bei gleicher Konzentration. Letzteres wird damit erklärt, dass die erhöhte molekulare Mobilität durch einen Anstieg des Polymerkettenraums, der als freies Volumen bezeichnet wird, verursacht wird, wodurch die Wechselwirkungen zwischen ihnen verringert werden. Auf diese Weise benötigen Ketten mit größerer Mobilität eine niedrigere Temperatur für den Übergang vom glasartigen Feststoff zu gummiartig, was zu einem niedrigeren T . führt g Werte.
Der Wert der Schmelztemperatur hängt mit der erforderlichen Temperatur zusammen, um die geordneten Strukturen (Kristalle) in das Polymer einzuschmelzen, und seine Variation hängt von der Kristallgröße ab. Es ist anzumerken, dass Nanofasern bei einer Konzentration von 17% den niedrigsten Wert in der Schmelztemperatur im Vergleich zu den PA- und Nanofaserbündeln bei der gleichen Konzentration aufwiesen. Dies deutet darauf hin, dass der grundlegende Elektrospinnprozess und das Elektrospinnen von Sol-Gel die Menge der kristallinen Bereiche des Polymers im Verhältnis zu den Pellets reduzierten und sie in Fibrillenstrukturen umwandelten [22], die durch das Spinnen und das angewendete Streckverhältnis die Polymerketten orientierten und zeigte eine Erholung des Kristallinitätsgrads der Nanofaserbündel um 44,71% im Vergleich zu Nanofasern. Schließlich zeigt die Schmelzenthalpie den Kristallinitätsbetrag im analysierten Polymer [23], und ihr Wert ist mit der erforderlichen Energie bei der kristallinen Strukturschmelze verbunden. Dies beweist, dass Nanofasern bei einer Konzentration von 17 % weniger Energie zum Schmelzen benötigen als die kristallinen Strukturen aus den Nanofaserbündeln und den PA 6/66-Pellets.
Schlussfolgerungen
Der 6/66-Polyamid-Elektrospinn-Sol-Gel-Prozess zeigte eine signifikante Steigerung der Produktivität (1,39 ± 0,15 mg/min), des Ziehverhältnisses (9,0 ± ± 1,2) und der Zugfestigkeit (29,64 ± 7,40 MPa) bei einer Gewichtskonzentration von 17 % im Vergleich zu den anderen beiden getesteten Konzentrationen (12 Gew.-% und 22 Gew.-%). Diese statistisch optimierte Prozessbedingung ermöglichte es uns, einheitliche PA 6/66-Nanofaserbündel aus einem stabilen und kontinuierlichen Prozess zu erhalten.
Abkürzungen
- DSC:
-
Differenzkalorimetrie
- PA 6/66:
-
Polyamid 6/66
- PVA:
-
Polyvinylalkohol
- SEM:
-
Rasterelektronenmikroskop
Nanomaterialien
- Überdenken des Softwareintegrationsprozesses für additive Fertigungsverfahren
- Sind Nylonverschlüsse chemikalienbeständig?
- 3 Hauptgründe für den Mangel an Nylon 6/6
- Tauchbeschichtungsverfahren und Leistungsoptimierung für elektrochrome Drei-Zustands-Bauelemente
- Die Herstellung einer Au@TiO2-Dotter-Schale-Nanostruktur und ihre Anwendungen für den Abbau und den Nachweis von Methylenblau
- Die Optimierung des Spacer-Engineerings für einen kondensatorlosen DRAM basierend auf dem Dual-Gate-Tunneling-Transistor
- Ein einfacher Ansatz zur Herstellung von Zinkoxid in Nanogröße in Wasser/Glycerin mit extrem konzentrierten Zinkquellen
- Elektrospinnen von Carboxymethylchitosan/Polyoxyethylenoxid-Nanofasern zur Frischhaltung von Obst
- Felddaten zur Prozessoptimierung sammeln
- Vorbereitung für den Prototypen-zu-Produktion-Fertigungsprozess