Numerische Optimierung für die geometrische Konfiguration von Keramiken in verschleißfesten HCCI/ZTAP-Verbundwerkstoffen basierend auf dem tatsächlichen Partikelmodell
Zusammenfassung
Um die thermische Belastung in hochchromhaltigen Gusseisen-(HCCI)-Matrix-Verbundwerkstoffen zu reduzieren, die durch Zirkonoxid-gehärtete Aluminiumoxid-(ZTA)-Keramikpartikel verstärkt sind, wird eine Finite-Elemente-Simulation durchgeführt, um die geometrische Konfiguration der Keramikleistung zu optimieren. Das vorherige Modell vereinfacht die Gesamtstruktur der Keramikpartikel-Vorform und fügt Randbedingungen hinzu, um die Partikel zu simulieren, was zu unkontrollierbaren Fehlern in den Ergebnissen führt. In dieser Arbeit werden die äquivalenten Kornmodelle verwendet, um den tatsächlichen Vorformling zu beschreiben, wodurch die Simulationsergebnisse näher an den tatsächlichen experimentellen Ergebnissen angenähert werden. Der Erstarrungsprozess von Verbundwerkstoffen wird simuliert und die Infiltration zwischen geschmolzenem Eisen und Keramikpartikeln realisiert. Thermische Spannungen im Erstarrungsprozess und Druckspannungsverteilung werden erhalten. Die Ergebnisse zeigen, dass das Hinzufügen von 10-mm-Rundlöchern in der Vorform die Leistung des Verbundwerkstoffs verbessern kann, was hilfreich ist, um Risse zu vermeiden und die Plastizität des Materials zu erhöhen.
Einführung
Mit der kontinuierlichen Weiterentwicklung des Industrialisierungsprozesses ist es immer schwieriger geworden, die Leistungsanforderungen von verschleißfesten Teilen in den Bereichen Metallurgie, elektrische Energie und Baustoffe mit traditionellen verschleißfesten Einzelmaterialien zu erfüllen [1, 2]. Mit Keramikpartikeln verstärkte Metallmatrix-Verbundwerkstoffe, wie z. B. High-Chrom-Gusseisen-(HCCI)-Matrix-Verbundwerkstoffe, verstärkt durch Zirkonoxid-gehärtete Aluminiumoxid-(ZTA)-Keramikpartikel (bezeichnet als HCCI/ZTAP Verbundwerkstoffe), sind eines der beliebtesten verschleißfesten Materialien, das die hohe Härte der ZTA-Keramik mit der herausragenden Zähigkeit von HCCI perfekt kombiniert und die komplementäre Beziehung zwischen den beiden voll ausnutzt, was der Metallmatrix eine hervorragende Verschleißfestigkeit verleiht Verbundwerkstoffe [3, 4].
HCCI/ZTAP Verbundwerkstoffe haben immer noch eine gewisse Rissneigung, die das Aussehen und die Stabilität der Produktion beeinträchtigen kann [5,6,7]. Die Rissbildung von Verbundwerkstoffen hängt mit der Plastizität und dem Spannungszustand zusammen. Ausgezeichnete Plastizität und geringere thermische Belastung können die Rissbildung von Verbundwerkstoffen verringern [8]. Ist die Differenz des Wärmeausdehnungskoeffizienten zwischen Keramikpartikeln und Metall zu groß, erhöht sich die Wärmespannung in Verbundwerkstoffen entsprechend. Bei hoher thermischer Belastung können Risse im Inneren des Verbundwerkstoffs entstehen, insbesondere an der Grenzfläche zwischen den Keramikpartikeln und dem Metall. Die kontinuierliche Ausdehnung und Ausbreitung von Rissen kann schließlich zum Bruch des Verbundmaterials oder sogar zum Ablösen der gesamten Schicht führen [9, 10]. HCCI/ZTAP Verbundmaterialien weisen auch die obigen Probleme auf. Wenn das geschmolzene Metall in die aggregierten Partikel eindringt, nimmt die Temperatur ab, was zu einer schlechten Kombinationsfähigkeit von Metall mit Keramikpartikeln führt. Um die Leistung von HCCI/ZTAP . weiter zu verbessern, Verbundwerkstoffe ist es wichtig, deren Rissneigung zu untersuchen und zu reduzieren [11, 12].
In HCCI/ZTAP Verbundwerkstoffen ist die Verbundschicht als Ortsbrust ausgelegt und die restliche Matrix ist Metall, was dem Verbund eine hohe Verschleißfestigkeit und gleichzeitige Plastizität verleiht [13]. Die Verbundschicht wird nach dem Infiltrationsverfahren in HCCI/ZTAP . hergestellt zusammengesetzt. Eine der bemerkenswerten Eigenschaften von Verbundwerkstoffen ist ihre Gestaltungsfähigkeit [14]. Je nach tatsächlichem Bedarf werden die Keramikpartikel zu einem Vorformling mit einer speziellen Struktur und Größe verarbeitet, und dann wird der Vorformling eng mit dem geschmolzenen Metall verbunden, um einen ZTAP . herzustellen /HCCI-Komposit [15].
Um die thermische Belastung zu reduzieren, wählen wir die Keramikpartikel-Vorform aus Hexagon. Bei der hexagonalen Vorform ist die maximale Eindringtiefe des geschmolzenen Metalls in die Vorform unabhängig von der Richtung gleich, sodass die Gleichmäßigkeit der Metalldurchdringung verbessert und die Spannungskonzentration in der Vorform verringert wird [16, 17]. Obwohl der hexagonale Vorformling verwendet wird, um die Rissneigung des Materials zu verringern, bleibt die thermische Belastung im Materialformprozess bestehen. Eine Verbesserung der Struktur der Keramikpartikel-Vorform kann die Spannungskonzentration effektiv reduzieren.
Bei der Optimierung der Verbundvorformstruktur kann die Finite-Elemente-Methode wiederholte Experimente reduzieren. In früheren Studien wurde aufgrund der Komplexität des Zeichnens und Berechnens von Keramikpartikeln die Keramikpartikel-Vorform normalerweise als Ganzes vereinfacht. Gründliche Untersuchungen haben ergeben, dass das vereinfachte Modell einige Mängel aufweist und nicht in einem größeren Bereich verwendet werden kann. Die Etablierung eines äquivalenten Partikelmodells kann das Modell weiter mit der tatsächlichen Situation kombinieren und den durch das Modell verursachten Fehler reduzieren [18]. Die Finite-Elemente-Analysesoftware COMSOL Multiphysics Methode dient zur Modellierung der Spannungsfelder im Erstarrungsprozess und Kompressionsprozess des HCCI/ZTAP Verbundmaterial [19]. COMSOL Multiphysics ist eine umfangreiche, fortschrittliche numerische Simulationssoftware [20, 21].
In der Arbeit verwenden wir Finite-Elemente-Software, um die Belastung von Verbundwerkstoffen unter verschiedenen Bedingungen zu simulieren. Die in diesem Dokument verwendete Version von COMSOL Multiphysics ist 4.5a. Diese Studie analysiert systematisch den Einfluss des geometrischen Modells in der Finite-Elemente-Software auf die Berechnungsergebnisse, was der Auslegung und Entwicklung von porösen Materialien zugute kommt. Simulation und Experiment werden miteinander verglichen und das Modell kontinuierlich optimiert.
Methoden
Eines der Hauptprobleme bei der Herstellung von Verbundwerkstoffen ist die Spannungskonzentration, die sich direkt auf die Verschleißfestigkeit und Plastizität von Verbundwerkstoffen auswirkt. Eine Verbesserung der Struktur der Keramikpartikel-Vorform kann die Spannungskonzentration effektiv reduzieren. Der Zweck dieser Studie besteht darin, den Einfluss der Preform-Struktur auf die Spannungsverteilung zu untersuchen und die Leistung von Verbundwerkstoffen zu verbessern.
Die Etablierung und Optimierung des geometrischen Modells
Während des Erstarrungsprozesses ist die Temperatur der Form und des flüssigen Metalls unterschiedlich und das flüssige Metall erstarrt schnell, sodass die Wärmeübertragung zwischen den einzelnen Positionen im Gießprozess unbeständig ist und die Wärmeübertragungsgleichung als [22] geschrieben werden kann:
$$\rho C_{{\text{P}}} \frac{\partial T}{{\partial x}} =\frac{\partial }{\partial x}\left( { \lambda \frac{\ partielle T}{{\partial x}}} \right) + \frac{\partial }{\partial y}\left( { \lambda \frac{\partial T}{{\partial y}}} \right) + \frac{\partial }{\partial z}\left( { \lambda \frac{\partial T}{{\partial z}}} \right) + \rho Q$$ (1)wobei \(\rho\) Dichte ist; \(C_{{\text{P}}}\) ist die Wärmekapazität; \(\lambda\) ist die Wärmeleitfähigkeit; T eine Übergangstemperatur ist; Q ist Hitze; die Koordinaten x , y , und z werden die relativen Koordinaten des Subsystems genannt.
Da die Temperatur an jedem Punkt beim Erstarrungsprozess unterschiedlich ist, gibt es im Gussstück eine variable innere Spannung. Wenn das Gussstück als Körper mit linearer Elastizität betrachtet werden kann, wenn die innere Spannung kleiner als die Fließgrenze ist, können wir mit dem Prozess der elastischen Verformung das Hookesche Gesetz verwenden, um es zu beschreiben.
$$\left\{ {\begin{array}{*{20}l} {\varepsilon_{xx} =\frac{1}{E}\left[ {\sigma_{xx} - v\left( {\ sigma_{yy} + \sigma_{zz} } \right)} \right]} \hfill \\ {\varepsilon_{yy} =\frac{1}{E}\left[ {\sigma_{yy} - v\ left( {\sigma_{xx} + \sigma_{zz} } \right)} \right]} \hfill \\ {\varepsilon_{zz} =\frac{1}{E}\left[ {\sigma_{zz } - v\left( {\sigma_{xx} + \sigma_{yy} } \right)} \right] \to \varepsilon_{ij} =\frac{1 + v}{E}\sigma_{ij} - \frac{v}{E}\delta_{ij} \sigma} \hfill \\ {\varepsilon_{xy} =\frac{1}{2G}\sigma_{x} } \hfill \\ {\varepsilon_{yz } =\frac{1}{2G}\sigma_{yz} } \hfill \\ {\varepsilon_{zx} =\frac{1}{2G}\sigma_{zx} } \hfill \\ \end{array} } \right.$$ (2)wo E ist der Elastizitätsmodul; \(\sigma =\sigma_{{ii + \sigma_{11}}} + \sigma_{22 + } \sigma_{33}\); \(v\) ist die Poisson-Zahl; Einheitstensor \(\varepsilon_{ij} =\frac{1}{2}\gamma_{ij}\); Schubmodul \(G =\frac{E}{{2\left( {1 + v} \right)}}\).
Dann ist die Eigenspannung größer als die Streckgrenze und das Gussstück weist mehr Verformung auf. Die Gesamtdehnung setzt sich aus der elastischen Dehnung und der plastischen Dehnung zusammen, \(\sigma_{ij} =\sigma_{ij}^{e} + \sigma_{ij}^{p}\). Diese Gleichung kann als elastisch-plastisches lineares Verfestigungsmodell behandelt werden. Elastische Verformung und plastische Verformung sind linear, und die konstitutive Gleichung kann geschrieben werden als [23]:
$$\sigma =\left\{ {\begin{array}{*{20}l} {E\varepsilon } \hfill &{\varepsilon \le \varepsilon_{{\text{s}}} } \hfill \ \ {\sigma_{{\text{s}}} + E_{1} \left( {\varepsilon - \varepsilon } \right)} \hfill &{\varepsilon> \varepsilon_{{\text{s}}} } \hfill \\ \end{array} } \right.$$ (3)wobei \(\sigma\) Dehnung ist; E ist der Elastizitätsmodul; \(\varepsilon\) ist Stress; \(\varepsilon_{{\text{s}}}\) ist die Streckgrenze.
Die Lebensdauer von Werkstücken aus Gusseisen mit hohem Chromanteil ist aufgrund der geringen Verschleißfestigkeit kürzer. Verbundmaterialien haben viele Vorteile gegenüber Einzel-HCCI. Im Herstellungsprozess von HCCI/ZTAP Kompositen werden die ZTA-Keramikpartikel vorab zu einer porösen Vorform präpariert. Durch die Vorform werden die ZTA-Keramikpartikel und das HCCI fester verbunden, und die Keramikpartikel fallen nicht leicht ab, wenn sie einem Aufprall ausgesetzt sind. Um die Leistung des HCCI/ZTAP . weiter zu verbessern Composites ist es notwendig, die Struktur der Preforms zu optimieren.
Während des Gießprozesses kann die Metallschmelze die kreisförmigen Löcher füllen und den Metallanteil erhöhen. Im Bewerbungsprozess von HCCI/ZTAP Verbundwerkstoffen wurde festgestellt, dass die Position der Partikelaggregation anfälliger für Risse ist, sodass das kreisförmige Loch an dieser Position hinzugefügt wird.
Die Form der ZTA-Keramikpartikel ist willkürlich polygonal, und es gibt viele Partikel in der Vorform. Wenn alle Partikel gezeichnet sind, ist die Arbeitsbelastung groß. In früheren Simulationen von Keramik-Metall-Matrix-Verbundwerkstoffen wurden die meisten Vorformen aus Keramikpartikeln als Ganzes betrachtet. Wie in Abb. 1 gezeigt, erstellt das Papier Modelle auf der Makro- bzw. Mikroskala. Die Etablierung eines vernünftigen Modells erfordert eine wiederholte gegenseitige Überprüfung durch Experimente. Im Optimierungsmodell stimmen die berechneten Ergebnisse gut mit den experimentellen Ergebnissen überein. Die Simulationsergebnisse umfassten thermische Spannung, Temperaturfeld, Phasenübergangsfeld während der Erstarrung und Spannungsdehnung des Gussstücks unter Last. Nehmen Sie sinnvolle und effektive Anpassungen am etablierten Finite-Elemente-Modell vor, damit das optimierte Finite-Elemente-Modell in einem größeren Bereich verwendet werden kann.
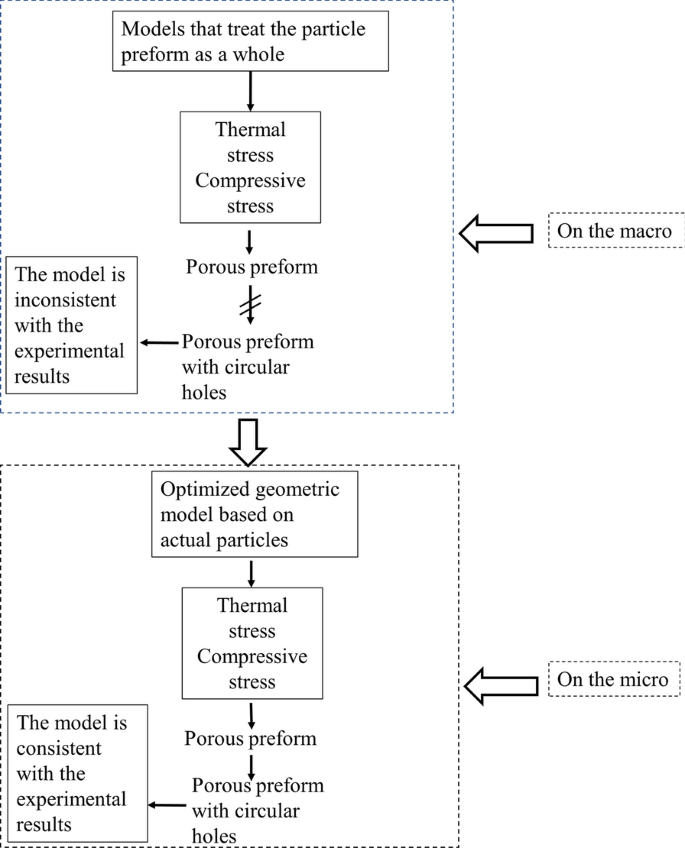
Das Flussdiagramm der geometrischen Modelloptimierung für HCCI/ZTAP Materialien
Bei der Erstellung des geometrischen Modells mit Hilfe der Finite-Elemente-Software wird häufig das vereinfachte geometrische Modell verwendet, um die Rechenzeit und den Modellierungsaufwand zu reduzieren. Wie in Fig. 2 gezeigt, gibt es Lücken zwischen den Partikeln, da die dreidimensionale hexagonale poröse Vorform zu einem zweidimensionalen Modell vereinfacht wird und nur eine Partikelschicht ausgewählt wird, um das zweidimensionale Modell zu projizieren. Auf diese Weise kann das Stapeln von Partikeln im dreidimensionalen Raum den Einfluss auf das zweidimensionale geometrische Modell effektiv vermeiden und das Modell angemessen vereinfachen und die Berechnungseffizienz verbessern.
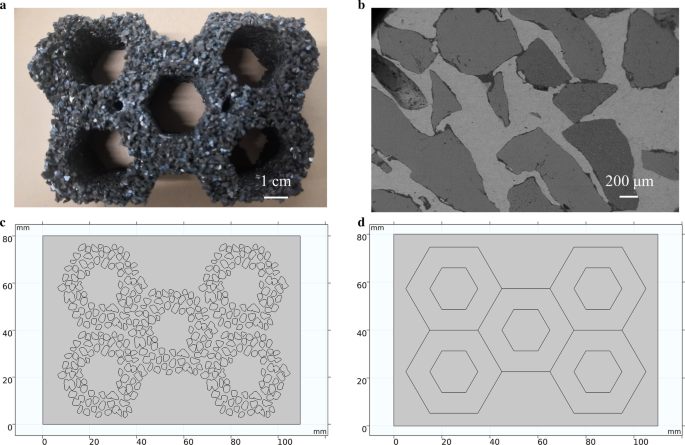
ZTA-Keramikpartikel und geometrisches Modell von HCCI/ZTAP Verbundstoffe. a Poröser Auftritt, b die zusammengesetzte Zone von HCCI/ZTAP Verbundwerkstoffe, c optimiertes geometrisches Modell basierend auf tatsächlichen Partikeln, d geometrisches Ausgangsmodell
In dieser Arbeit werden ZTA-Keramikpartikel als verstärkende Phase des Verbundwerkstoffs ausgewählt. ZTA-Keramikpartikel sind eine mehrphasige Strukturkeramik, die durch Zugabe von Zirkonoxid zu Aluminiumoxid und anschließendes Sintern hergestellt wird, wobei der Zirkonoxid-Massenanteil 18 % und der Aluminiumoxid-Massenanteil 82 % beträgt. Gusseisen mit hohem Chromgehalt ist die Matrix des Verbundmaterials, das mehr als 12% Chrom enthält und ein ausgezeichnetes verschleißfestes Material ist.
Die Materialparameter haben großen Einfluss auf das Ergebnis der Finite-Elemente-Berechnung. Die für die Simulationsrechnung in dieser Arbeit benötigten Materialparameter werden durch Experimente und Literatur ermittelt. Die Materialparameter von ZTA-Keramikpartikeln und HCCI sind in Tabelle 1 aufgeführt.
Experimente
Zur Prüfung der Plastizität und Verschleißfestigkeit des HCCI/ZTAP Verbundwerkstoff wurde ein systematischer Test am Verbundstoff durchgeführt, um den Einfluss der Preform-Struktur weiter zu bestimmen. Mit der Universalprüfmaschine SHT4305 wurden die Kompressionseigenschaften von HCCI/ZTAP . gemessen Verbundstoffe. Die Größe der Kompressionstestprobe beträgt 10 × 10 × 25 mm, die aufgebrachte Last beträgt 30 Tonnen und die Kompressionsgeschwindigkeit beträgt 0,5 mm/min.
Der Verschleißfestigkeitstest von HCCI/ZTAP zusammengesetzt ist notwendig. Exzellente Abriebfestigkeit ist das wichtigste Kriterium für die Leistungsprüfung von verschleißfesten Verbundwerkstoffen. HCCI/ZTAP Verbundwerkstoffe werden hauptsächlich in der Mineralverarbeitung, der Zementherstellung und der Papierherstellung verwendet, und die meisten Arbeitsbedingungen sind Drei-Körper-Schleifverschleiß. Um die Serviceleistung von HCCI/ZTAP . zu simulieren Verbundwerkstoffe unter realen Arbeitsbedingungen so weit wie möglich, getestet der HCCI/ZTAP Verbundwerkstoffe mit dem Dreikörper-Schleifverschleißtester MMH-5. Das Schienenmaterial des Testers ist M2 Werkzeugstahl, Härte 820–860 Hv, Außendurchmesser 380 mm, Breite 20 mm. Die Art und Größe der Schleifmittel werden entsprechend den unterschiedlichen Arbeitsbedingungen ausgewählt. In diesem Artikel wird Quarzsand für Schleifmittel verwendet, die Härte beträgt 1000–1200 Hv, die Prüflast beträgt 40 N und die Rotationsgeschwindigkeit der Probe beträgt 30 U/min.
Ein Nanoindenter wird verwendet, um einen 100-Punkte-E-Modul-Test im ausgewählten 100 × 100 μm 2 . durchzuführen Mikroregion. Das Modell des Nanoindenters ist iMicro.
Die Verschleißfestigkeit von Materialien kann mit Massenreduktion, Volumenreduktion usw. gemessen werden. Der von einem Messzylinder gemessene Volumenverlust mit kleinen Änderungen kann leicht zu Fehlern in der menschlichen Ablesung führen. Daher wird unter den gleichen Verschleißbedingungen der Massenverlust Δm verwendet, um das Verschleißverhalten des Materials zu bewerten. Die Formel zur Berechnung des Materialverlusts lautet wie folgt:
$$\Delta m =m_{1} - m_{2}$$ (4)wo m 1 und m 2 , stellen die Masse der Proben vor und nach dem Verschleiß dar.
Ergebnisse und Diskussion
Simulation basierend auf vereinfachtem Gesamtmodell
Bei der Simulation thermischer Spannungen im Erstarrungsprozess von HCCI/ZTAP Verbundwerkstoffe in dieser Studie wird für alle Simulationsergebnisse die Wärmespannungsverteilung bei 10 s gewählt, da sich die Wärmespannung vor und nach 10 s signifikant ändert. Verglichen mit der Skala rechts in Abb. 3 weist die rote Farbe auf eine höhere Belastung und die blaue Farbe auf eine niedrigere Belastung hin. In Abb. 3a trat eine Spannungskonzentration am Rand des Vorformlings auf, insbesondere in der mittleren Position, die Oberseite und die Unterseite des Vorformlings erschienen rot. Im Vergleich zum rechten Maßstab von Abb. 3a zeigt sich, dass die Belastung hier enorm ist. Die blaue Farbe erscheint an der Stelle, an der sich die Partikel sammeln, dh am Schnittpunkt der hexagonalen Lochwände, was darauf hindeutet, dass die Spannung hier gering ist. Im geometrischen Modell in Abb. 3c werden den Partikelaggregaten der Vorform kreisförmige Löcher hinzugefügt. Die Spannungsverteilung in Abb. 3c ist ähnlich zu Abb. 3a, außer dass um die kreisförmigen Löcher eine deutlichere Spannungskonzentration auftritt. Die Spannungsverteilung um das kreisförmige Loch der Darbietung in Fig. 4 ist ähnlich der in Fig. 3
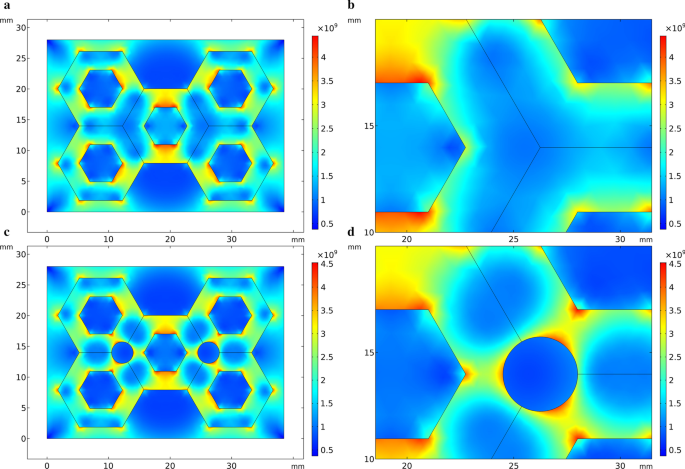
Thermische Spannungsverteilung während der Erstarrung im vereinfachten Modell. a Erster Auftritt, b teilweise vergrößerte Ansicht des ersten Auftritts, b Vorformling mit hinzugefügten runden Löchern, d teilweise vergrößerte Ansicht der Darbietung mit hinzugefügten kreisförmigen Löchern
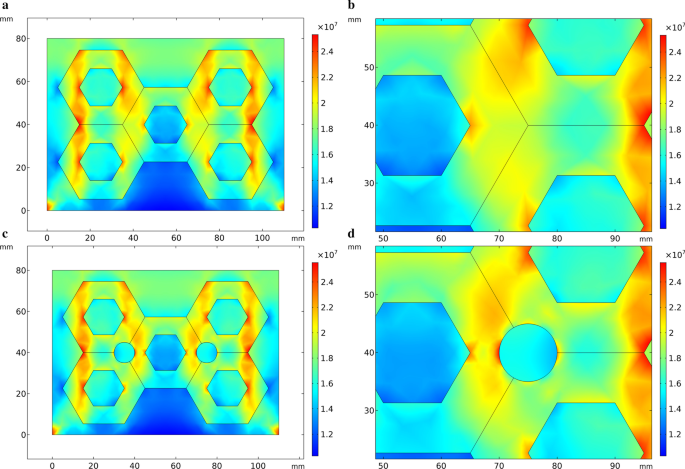
Druckspannung im vereinfachten Modell. a Erster Auftritt, b teilweise vergrößerte Ansicht des ersten Auftritts, b Vorformling mit hinzugefügten runden Löchern, d teilweise vergrößerte Ansicht der Darbietung mit hinzugefügten kreisförmigen Löchern
Die endgültigen Berechnungsergebnisse müssen intuitiv sein, daher wurden die Ergebnisse nachbearbeitet und ein Spannungsquervergleichsdiagramm erstellt. Zeichnen Sie zuerst eine 2D-Transversale in das geometrische Modell, da sich der Hauptbeobachtungsteil um das kreisförmige Loch herum befindet, dh dort, wo sich die Partikel ansammeln, sodass die 2D-Transversale durch das kreisförmige Loch verläuft. Die Ordinate des Spannungsdiagramms ist der Spannungswert auf der Schnittlinie und die Abszisse ist das x -Achsenkoordinate des Modells, wie in Abb. 5 gezeigt. Im vereinfachten Modell lauten die kreisförmigen Lochkoordinaten (12, 14), (27, 14). Abbildung 5c ist ein Liniendiagramm der Erstarrungsspannung. In Fig. 5c weist der Vorformling mit kreisförmigen Löchern einen signifikanten Anstieg der Spannung an den Abszissen 12 und 27 auf, verglichen mit dem Vorformling ohne kreisförmige Löcher. Abbildung 5d ist ein Vergleichsdiagramm der Druckspannung. Der allgemeine Trend der Kurve ist der gleiche wie in Abb. 5c, und die Positionsspannung des kreisförmigen Lochs wird erheblich zunehmen.
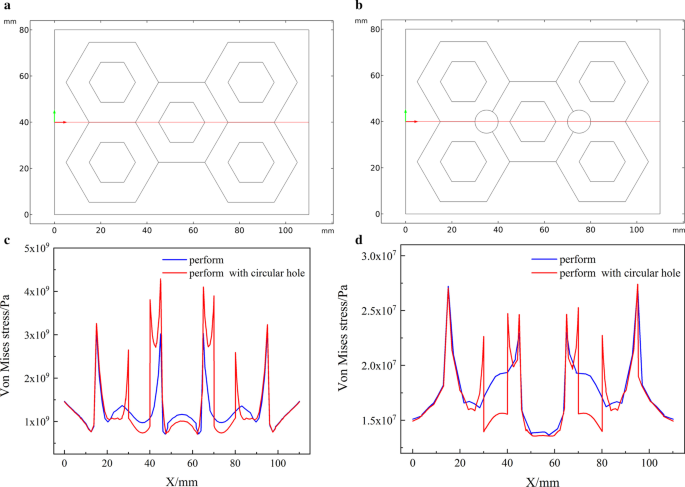
Die Position der 2D-Querschnitt des vereinfachten Modells und der Spannungsquervergleich. a Erster Auftritt, b teilweise vergrößerte Ansicht des ersten Auftritts, c Vorformling mit hinzugefügten runden Löchern, d teilweise vergrößerte Ansicht der Darbietung mit hinzugefügten kreisförmigen Löchern
Simulation basierend auf einem äquivalenten Kornmodell
Abbildung 6 zeigt die Wärmespannungsverteilung von HCCI/ZTAP Composites-Modell basierend auf tatsächlichen Partikeln, ähnlich Abb. 3. In Abb. 6 sind die ZTA-Keramikpartikel jedoch nicht mehr als ganze Vorform vereinfacht, sondern als einzelne Partikel etabliert, und es ist zu beobachten, dass die meisten Partikel um erscheinen rote Farbe. Die Form der ZTA-Keramikpartikel ist nicht einheitlich und die Spannung ist höher als der Umgebungswert, insbesondere an der scharfen Spitze der Partikel. Die thermischen Spannungsverteilungen in den Fign. 3b und 6b sind offensichtlich unterschiedlich. Das kreisförmige Loch des Vorformlings in Abb. 6b erscheint in blauer Farbe, was darauf hinweist, dass die Spannung hier gering ist. Die Berechnungsergebnisse der Spannungskonzentration um das kreisförmige Loch sind entgegengesetzt. Der Vereinfachungsgrad und die Zeichenmethoden geometrischer Modelle führen zu unterschiedlichen Berechnungsergebnissen.
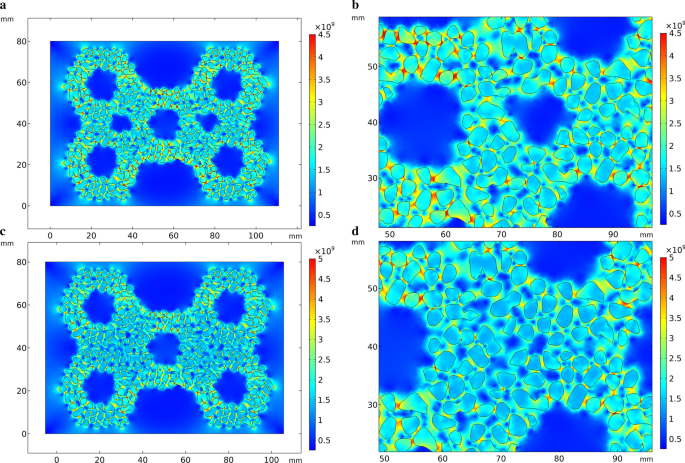
Thermische Spannungsverteilung während der Erstarrung im optimierten Modell. a Erster Auftritt, b teilweise vergrößerte Ansicht des ersten Auftritts, c Vorformling mit hinzugefügten runden Löchern, d teilweise vergrößerte Ansicht der Darbietung mit hinzugefügten kreisförmigen Löchern
Das zur Simulation der Druckspannung verwendete geometrische Modell in Abb. 7 ist ähnlich wie in Abb. 6. In Abb. 7 konzentriert sich die Belastung im Vergleich zur rechten Skala auf den oberen Teil des Modells und die Vorform, insbesondere die Ränder auf beiden Seiten des Keramikvorformlings, die gelbgrün sind. Im Partikelaggregationsteil des Vorformlings ist diese Zone in Abb. 7a grün dargestellt, was darauf hinweist, dass die Spannung hier gering ist. In Abb. 7b werden runde Löcher an den Aggregaten des Vorformlings hinzugefügt. Die Farbe der kreisförmigen Lochzone ist grün und gelb, was darauf hinweist, dass keine offensichtliche Spannungskonzentration vorliegt.
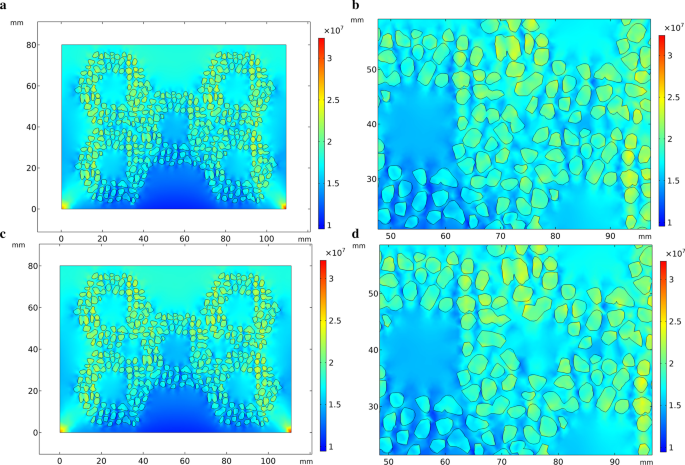
Druckspannung im optimierten Modell. a Erster Auftritt, b teilweise vergrößerte Ansicht der optimierten Leistung, c Vorformling mit hinzugefügten runden Löchern, d teilweise vergrößerte Ansicht der Darbietung mit hinzugefügten kreisförmigen Löchern
In dem auf tatsächlichen Partikeln basierenden Modell lauten die kreisförmigen Lochkoordinaten (12, 14) (27, 14). Abbildung 8 ist ein Vergleichsdiagramm der Erstarrungsspannung, in dem die Auswirkungen des Vorhandenseins oder Fehlens von kreisförmigen Löchern auf die Spannung verglichen werden. Die Spannung des Vorformlings mit kreisförmigen Löchern zeigte eine signifikante Verringerung an den Abszissen 12 und 27 und seine Position stimmte im Wesentlichen mit der Position der kreisförmigen Löcher überein. Die Spannung der restlichen Koordinaten des Vorformlings mit kreisförmigen Löchern nimmt geringfügig zu. In Fig. 8a, b fallen die beiden Kurven im Wesentlichen zusammen, außer in der Vorform mit kreisförmigen Löchern; die Spannung in der Nähe der kreisförmigen Lochkoordinaten sinkt erheblich.
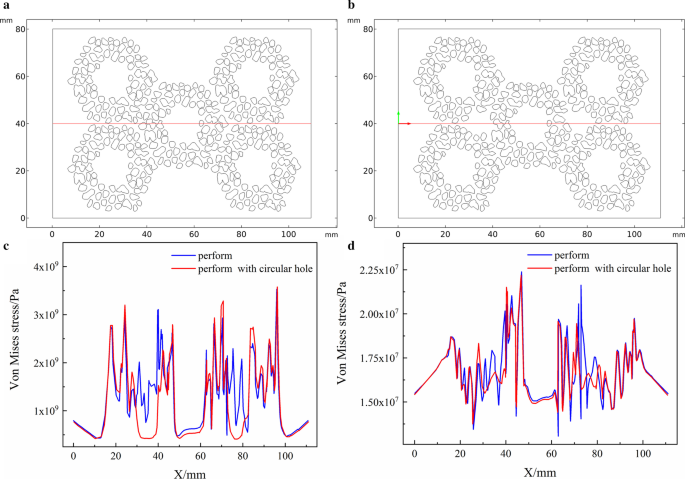
Die Position der 2D-Querschnitt des optimierten Modells und der Spannungsquervergleich. a Erster Auftritt, b Vorformling mit hinzugefügten runden Löchern, c Erstarrungsspannung, d Druckbelastung
Experimentelle Validierungen
Wie aus Abb. 9 ersichtlich ist, unterscheidet sich der Massenverlust der Verbundwerkstoffe mit der optimierten Vorform und der Verbundwerkstoffe mit der ursprünglichen Vorform im Verschleißtest nicht wesentlich, was darauf hindeutet, dass die Verschleißfestigkeit nicht wesentlich geopfert wird und auch die Gesamtplastizität des HCCI/ZTAP Verbundwerkstoffe.
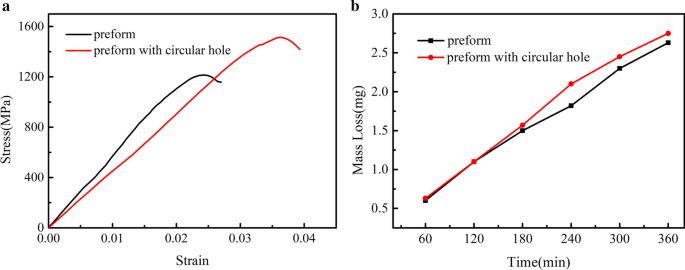
Druckspannungs-Dehnungs-Kurve von HCCI/ZTAP Verbundmaterial und Massenverlust von Dreikörper-Schleifmittel an der Verbindung von Verbundwabenwänden
Die poröse Vorform wurde durch Hinzufügen kleiner zylindrischer Löcher in den Partikelaggregationszonen optimiert, was den Volumenanteil der Keramikpartikel in der HCCI/ZTAP . veränderte Verbundstoffe. Der Gehalt an ZTA-Keramikpartikeln im Verbundmaterial ist ein wichtiger Faktor, der seine mechanischen Eigenschaften beeinflusst. Wie in Abb. 9 gezeigt, nehmen die Druckfestigkeit und die Druckverformung einer Probe mit Vorformen mit runden Löchern im Vergleich zu der Probe mit der ursprünglichen Vorform deutlich zu, was darauf hindeutet, dass kleine kreisförmige Löcher in den Aggregationszonen der ZTA-Keramikpartikel der Verbesserung förderlich sind die Festigkeit und Plastizität des HCCI/ZTAP Verbundstoffe. Das Hinzufügen kleiner zylindrischer Löcher in den Agglomerationszonen der porösen Vorform erhöht den Gehalt der Metallmatrix und erhöht somit die Druckspannung des HCCI/ZTAP Verbundwerkstoffe unter Druckspannung und beeinflusst auch ihre Druckfestigkeit. Wenn die Spannung den Spitzenwert erreicht, kann davon ausgegangen werden, dass die Beschädigung bereits in der Probe aufgetreten ist. Mit der kontinuierlichen Zunahme der Dehnung häufen sich auch die inneren Schäden des Materials an, der Dehnungswiderstand nimmt allmählich ab und schließlich tritt das Scherversagen auf.
Die Mikroanalysen der Härte aller Proben sind in Abb. 10 dargestellt. Wie in Abb. 10a, b gezeigt, wird der Testbereich um die abgerundeten Partikel bzw. um die scharfkantigen Partikel herum ausgewählt, um den Simulationsergebnissen besser zu entsprechen. Abbildung 10c, d wird mit der vergrößerten Teilansicht der Belastung verglichen. In der Simulation tritt die Spannungskonzentration tendenziell um scharfe Ecken der Partikel auf. In den Testergebnissen ist der Modul in der Nähe der Partikel mit scharfen Ecken größer als die Metallmatrix in der Nähe der runden Ecken, was die Rationalität des Modells basierend auf den tatsächlichen Partikeln weiter bestätigt.
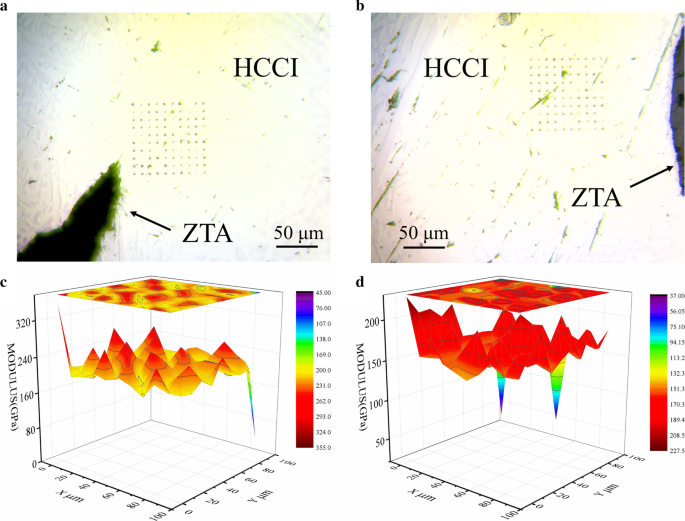
Eindruckverteilung von Verbundwerkstoffen und die Verteilung des Youngschen Moduls um die Partikel von Verbundwerkstoffen. a Die Form der Partikel ist scharf, b die Form der Partikel ist abgerundet, c die Form der Partikel ist scharf, d die Form der Partikel ist abgerundet
Den Partikelaggregationszonen der Vorformlinge wird ein kreisförmiges Loch hinzugefügt, das drei Funktionen hat. Die erste Funktion besteht darin, den Volumenanteil der Keramikpartikel im HCCI/ZTAP . zu reduzieren Verbundmaterial und reduzieren die Eigenspannung; die zweite Funktion besteht darin, die Agglomeration der Keramikpartikel des Vorformlings zu reduzieren; die dritte Funktion besteht darin, den Volumenanteil der Metallmatrix mit besserer Plastizität zu erhöhen, um die Rissausbreitung zu verhindern. Die Plastizität von HCCI/ZTAP Verbundwerkstoffe nimmt mit zunehmender Eigenspannung ab. Der Volumenanteil an Keramikpartikeln nimmt ab und die Eigenspannung wird relativ klein. Das Hinzufügen von kreisförmigen Löchern in der ZTA-Keramikpartikel-Vorform kann Risse reduzieren, da die Rissinstabilität dazu neigt, sich entlang einer geraden Linie zu erstrecken. Wenn Risse in der Verbundzone von HCCI/ZTAP . entstehen Verbundwerkstoff, werden die Risse leicht entlang der sechseckigen Lochwand in der Vorform verlängert, um eine Rissausbreitung zu erzeugen. Das runde Loch erhöht den Gehalt an HCCI-Matrix am Übergang der hexagonalen Lochwand, behindert die Rissausbreitung und spielt somit eine Rolle bei der Zähigkeit der Struktur.
Schlussfolgerung
Der große Unterschied im Wärmeausdehnungskoeffizienten zwischen HCCI und ZTAP verursacht Risse im Verbundmaterial. Der Erstarrungs- und Kompressionsprozess von HCCI/ZTAP Verbundwerkstoffe werden unter Verwendung der Finite-Elemente-Software simuliert und die numerischen Werte und Spannungsverteilungen basierend auf einem vereinfachten Gesamtmodell und einem äquivalenten Kornmodell für die Vorform analysiert. Nach den Berechnungsergebnissen wird die Preform-Struktur optimiert. Durch die Analyse der Simulations- und experimentellen Ergebnisse kann geschlossen werden, dass das Hinzufügen von kreisförmigen Löchern zu der hexagonalen porösen Vorform zu einer Verringerung der thermischen Spannungen und Druckspannungen während der Erstarrung führt. Nach der Optimierung und Anpassung des Modells stimmen die Simulationsergebnisse tendenziell mit den experimentellen Ergebnissen überein. Die Methoden in diesem Papier können die wichtige Referenz für die Simulation und Optimierung von Verarbeitungsparametern in Gießsystemen der verschiedenen Metallmatrix-Verbundwerkstoffe sein.
Verfügbarkeit von Daten und Materialien
Die Datensätze, die die Schlussfolgerungen dieses Artikels unterstützen, sind im Artikel enthalten.
Abkürzungen
- HCCI:
-
Gusseisen mit hohem Chromgehalt
- ZTA:
-
Zirkonoxid gehärtetes Aluminiumoxid
- HCCI/ZTAP :
-
Verbundwerkstoffe aus Gusseisen mit hohem Chromgehalt, verstärkt durch Verbundwerkstoffe aus gehärteten Aluminiumoxid-Keramikpartikeln mit Zirkonoxid
Nanomaterialien
- AODD-Pumpen können die beste Lösung für eine verbesserte Keramikproduktion sein
- Tipps zur Verwendung von Duroplast-Verbundwerkstoffen in der HLK-Branche
- Wie man im IIoT-Reifemodell für die Fertigungsindustrie aufsteigt
- IBM-Wissenschaftler erfinden ein Thermometer für die Nanoskala
- Drei Möglichkeiten, wie Unternehmen Verbundwerkstoffe in der Luft- und Raumfahrt für die Zukunft einsetzen
- Der Wert von Cloud-basiertem Slicing und Dateimanagement für den 3D-Druck
- Hochreflektierende Dünnschicht-Optimierung für Vollwinkel-Mikro-LEDs
- Das Design der Emissionsschicht für Elektronenvervielfacher
- Die elektrischen Eigenschaften von Hybridverbundwerkstoffen basierend auf mehrwandigen Kohlenstoffnanoröhren mit Graphit-Nanoplättchen
- Die Pandemie treibt ein neues Modell für die Entscheidungsfindung in der Lieferkette