Thermoplastische Bänder zeigen weiterhin Potenzial für Verbund-Flugzeugstrukturen
Die Produktion von Flugzeugstrukturen wurde von der COVID-19-Pandemie stark beeinträchtigt, aber die Bemühungen in der Luft- und Raumfahrt folgten nicht unbedingt, zumindest nicht für Web Industries (Marlborough, Massachusetts, USA), ein Unternehmen, das Dienstleistungen zum Schneiden von thermoplastischen Bändern für eine Vielzahl von Kunden anbietet Anwendungen. Laut Grand Hou, globaler Direktor für Forschung und Technologie, Luft- und Raumfahrt, Forschung im Weltraum, urbane Luftmobilität (UAM) und Militär haben Vollgas gegeben, um die nächste Generation von Flugzeugen zu ermöglichen – und Verbundwerkstoffe, insbesondere thermoplastische Bänder, wurden Schlüssel zu vielen dieser Bemühungen.
Thermoplastische Klebebänder sind natürlich nicht neu (siehe CW "Ich möchte Ihnen zwei Worte sagen:'Thermoplastische Bänder'" von Chefredakteur Jeff Sloan für mehr Hintergrundgeschichte aus den 1960er Jahren), aber in den letzten Jahren ist ihr Interesse gestiegen, insbesondere für kommerzielle Zwecke Luft- und Raumfahrt und andere Hochleistungsanwendungen (wie unter anderem Rippen für das Wing of Tomorrow-Programm und das Multifunctional Fuselage Demonstrator-Programm). Thermoplaste bieten gegenüber duroplastischen Bändern Vorteile wie höhere Zähigkeit, leichtere Recyclingfähigkeit, Verarbeitbarkeit aus dem Autoklaven (OOA) und Lagerfähigkeit bei Raumtemperatur.
Web Industries steht an vorderster Front bei der Entwicklung und Anwendung von Thermoplasten, insbesondere mit seinen vielfältigen Formatierungsfunktionen, die das Schneiden von duroplastischen und thermoplastischen Bändern von Lieferanten in verschiedene Formen und Formate umfassen, um spezifische Kundenanforderungen zu erfüllen. Mit Produktionslinien zum Längsschneiden von Bändern in US-amerikanischen und europäischen Einrichtungen umfasst Webs Fähigkeiten die Formatierung von thermoplastischen Hochleistungsbändern aus Polyetheretherketon (PEEK), Polyetherketonketon (PEKK) und Polyaryletherketon (PAEK), die am häufigsten in Luft- und Raumfahrtanwendungen verwendet werden.
TP-Bänder für sekundäre Flugzeugstrukturen – und Herausforderungen bei primären Strukturen
Hou merkt an, dass sich die meisten Flugzeugstrukturaktivitäten in thermoplastischen Prepregs derzeit auf Sekundärstrukturen wie Clips, Zugangsplatten oder Unterstrukturen konzentrieren, während flugkritische Primärstrukturen wie Flügel und Rümpfe aus duroplastischen Verbundwerkstoffen oder Metallen hergestellt werden.
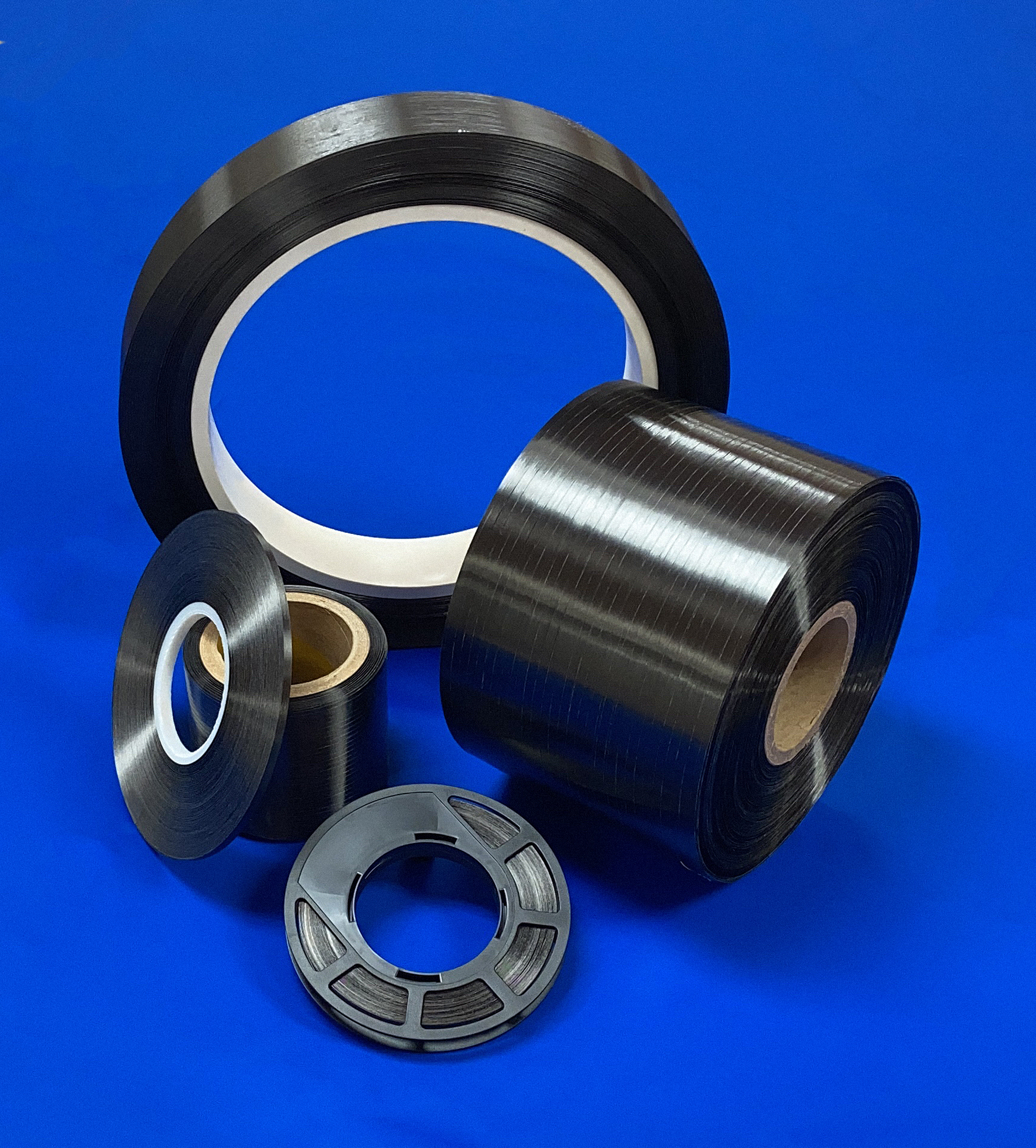
„Bei vielen Herausforderungen geht es um das Management von Risiken“, sagt er, und ein Teil des Problems waren in der Vergangenheit die wachsenden Probleme mit thermoplastischen Prepregs von Zulieferern. Thermoplastische Materialien sind weniger ausgereift als duroplastische Bänder. Während duroplastische Bänder jahrzehntelang maßstabsgetreu und perfektioniert wurden, stecken laut Hou thermoplastische Materialien in den Kinderschuhen, um in automatisierten Prozessen für die Großserienproduktion eingesetzt zu werden.
Web Industries arbeitet jedoch mit einer Vielzahl von Verbundwerkstofflieferanten zusammen, und Hou sagt, dass sich die allgemeine Materialkonsistenz und -größe in den letzten Jahren stark verbessert hat. Materialbreite, Länge, Dicke, Faserspannung und Harzgleichmäßigkeit seien heute viel konstanter und von höherer Qualität, sagt er.
Ein weiterer unerschwinglicher Faktor bei der Herstellung größerer thermoplastischer Primärstrukturen besteht darin, dass thermoplastische Materialien tendenziell teurer sind als Duroplaste. „Es wird nicht weiter verbreitet, wenn es keinen Gesamtkostenvorteil gibt“, räumt Hou ein und weist darauf hin, dass Zusammenarbeit und technische Hilfe entscheidend sind, um die Prozesskosten zu senken. „Wir können bessere Lösungen erzielen, wenn alle von den frühen Phasen des Projekts bis zum Ende zusammenarbeiten, um gemeinsame Ziele zu erreichen.“
Prozessflexibilität und Materialanpassung
Insgesamt sieht Hou jetzt und in Zukunft viel Potenzial und zunehmende Aktivität für thermoplastische Bänder, wobei Flexibilität einer der wichtigsten Kipppunkte für Kunden ist.
Derzeit sind duroplastische Bänder hauptsächlich auf die automatisierte Faserplatzierung (AFP) beschränkt, mit den Einschränkungen der Autoklavenhärtung und der Anforderungen an die Lagertemperatur. Thermoplaste können einen flexibleren Prozessansatz sowie die OOA-Verarbeitung ermöglichen, sagt Hou, einschließlich Bandformaten für das automatisierte Tapelegen (ATL) und Filamenten für die additive Fertigung.
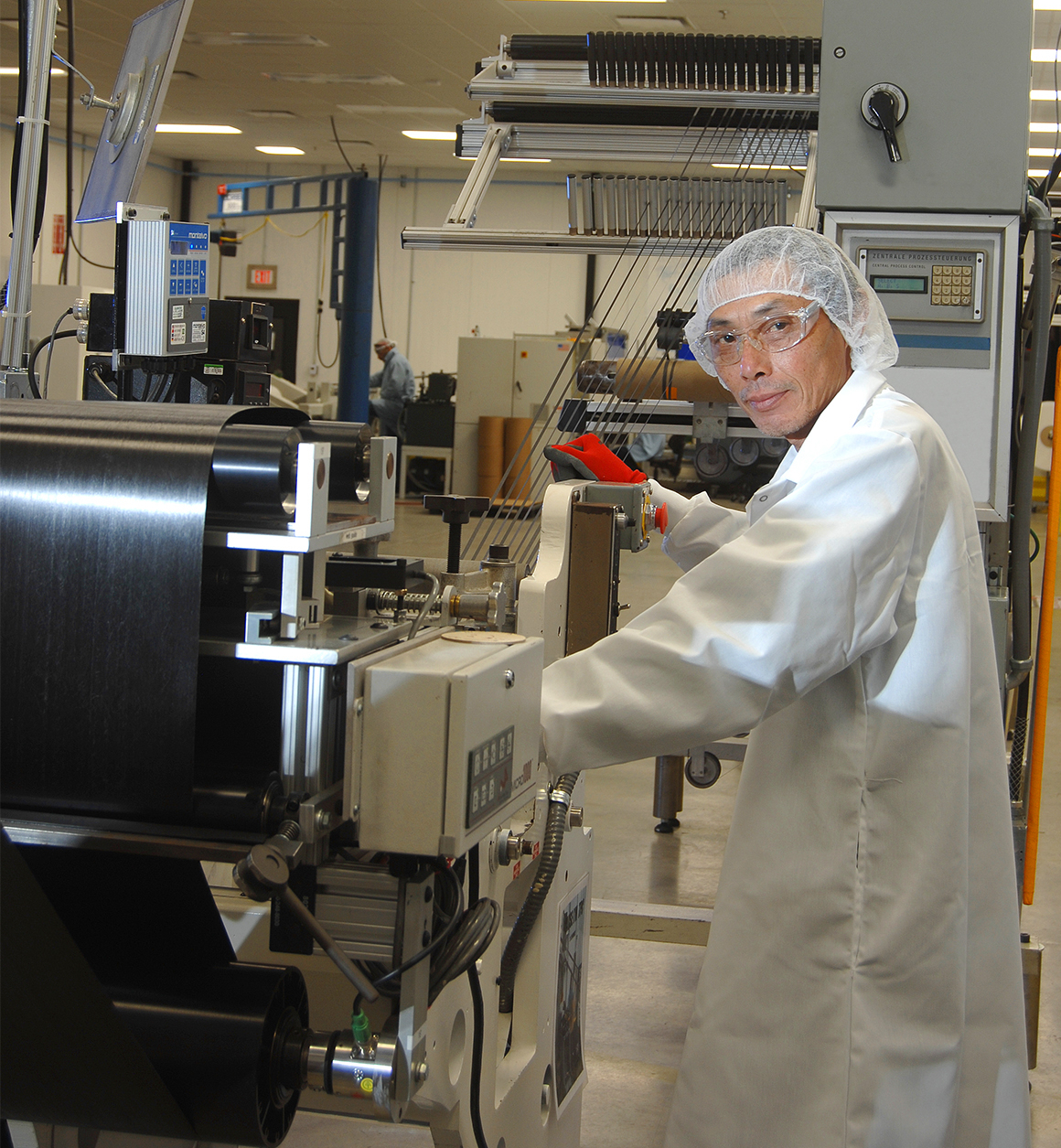
Laut Web Industries werden Formatierungs- und Lieferkettenlösungen im kommerziellen Maßstab entscheidend sein, um den Herstellern von Flugzeugstrukturen die thermoplastischen Schlitzbänder zur Verfügung zu stellen, die erforderlich sind, um die prognostizierten Fertigungsraten der Industrie zu unterstützen.
Thermoplastische Prepregs können auch für spezielle Anwendungen maßgeschneidert werden. Laut Hou suchen Endverbraucher nach Materialien für jede Anwendung. Da Thermoplaste sehr anpassungsfähig sind, kann für ein bestimmtes Teil ein bestimmtes Format entwickelt werden, was den Materialeinsatz maximiert und die Folgekosten des Kunden reduziert. Ashley Graeber, Director Sales and New Business Development, stellt fest, dass Aktivitäten wie UAM, Raumfahrt und Militär auf das jeweilige Projekt und nicht auf das Flugzeugprogramm zugeschnitten sind.
Das Formatieren thermoplastischer Materialien für bestimmte Anwendungen trägt auch zur Reduzierung von Abfall bei, sagt Jason Surman, VP Sales, Aerospace. In der Luft- und Raumfahrtindustrie ist die Buy-to-Fly-Ratio, also das Verhältnis des Rohmaterials zur Masse des fertigen Teils, ein zentrales Anliegen. Ziel ist ein Buy-to-Fly-Verhältnis von möglichst 1:1, also wenig Abfall. Das richtige Material im richtigen Format für die richtige Anwendung kann den Abfall drastisch reduzieren, bemerkt Surman. In der Luft- und Raumfahrtindustrie seien 30 % Abfall „verrückt üblich“, sagt er, und um den Abfall unter dieses Niveau zu bringen, bedarf es einer gemeinsamen Anstrengung aller Seiten.
„Die Verbindung des Materials mit dem Prozess ist von entscheidender Bedeutung“, fügt Surman hinzu, „und thermoplastische Klebebänder entwickeln sich als förderliche Lösung für Flugzeugstrukturhersteller.“
Harz
- Thermoplastisches Biomaterial „Feinabgestimmt“ für medizinische Anwendungen
- Solvay erweitert die Kapazität von thermoplastischen Verbundwerkstoffen
- Oribi Composites, Packard Performance-Partner für Offroad-Powersports-Thermoplast-Verbundrad
- Fraunhofer nimmt automatisierte Engel-Produktionszellen für F&E thermoplastischer Verbundwerkstoffe in Betrieb
- Konsortium sucht Lösungen für thermoplastische Kohlefaser-Verbundstrukturen
- Karl Mayer startet Produktionslinie für thermoplastische UD-Bänder
- INEOS Styrolution baut Produktionsstätte für thermoplastischen Verbundwerkstoff StyLight
- Polyscope Polymers gewinnt JEC Innovation Award für Führungsschienen aus thermoplastischem Verbundwerkstoff
- Thermoplastische Tür eine Premiere für Automobilverbundwerkstoffe
- Rhodes Interform fertigt Verbundpresse für AMRC