Beschleunigtes RTM mit Wärmestromsensoren
Fahrwerke machen 3-5% des Gewichtes eines Flugzeugs aus und werden seit langem zur Gewichtsreduzierung eingesetzt, um die Effizienz von Flugzeugen zu verbessern. Dies ist mit der bevorstehenden Umstellung auf energie- und emissionsreduzierende Elektroantriebe noch kritischer geworden.
Safran Landing Systems (Vélizy, Frankreich) wird beispielsweise ein elektrisches Rollen mit ausgeschalteten Triebwerken über in die Fahrwerksräder von Flugzeugen integrierte Elektromotoren ermöglichen, wodurch NOx und CO2 . reduziert werden , CO und unverbrannte Kohlenwasserstoffe um 51 %, 61 %, 73 % bzw. 62 %. Dies ist ein großer Gewinn für eine nachhaltigere Luftfahrt, aber Elektromotoren benötigen Strom, und die Batterien, die für die Bereitstellung dieses Stroms benötigt werden, sind schwer.
Somit scheint die Nachfrage nach leichten Fahrwerksstrukturen bis auf einen Punkt perfekt für die Anwendung von Verbundwerkstoffen geeignet zu sein. „Da es sich bei dem Fahrwerk um eine Einzellastpfadstruktur handelt, kann der Ausfall einer Strukturkomponente zu einer ernsthaften Notlandung führen“, sagt Peet Vergouwen, Technologe bei GKN Fokker Landing Gear (Helmond, Niederlande). GKN Fokker Landing Gear hat mehr als ein Jahrzehnt daran gearbeitet, die technische Machbarkeit von Verbundfahrwerksstrukturen zu demonstrieren, einschließlich der Entwicklung von kohlenstofffaserverstärkten Polymer (CFK) Bremsstrebenstreben für die F-35 Lightning II . „Aufgrund ihrer Kritikalität gehören Fahrwerksstrukturen zu den konservativsten in Verkehrsflugzeugen.“ Daher wurden sie meist aus hochfesten Metallen hergestellt.
Das Blatt beginnt sich jedoch zu wenden. Clean Sky 2 strebt eine Gewichtsreduktion von 30 % an, allerdings über CFK-Komponenten im HECOLAG-Projekt (High Efficiency Composites LANding Gear) für zwei Anwendungen. In der ersten Anwendung wurde eine CFK-Alternative für die bestehende Aluminium obere Bremsstrebe entwickelt für das Bugfahrwerk A350-1000, das ursprünglich von Liebherr-Aerospace (Lindenberg, Deutschland) entwickelt und hergestellt wurde. Die HECOLAG-Partner Royal Netherlands Aerospace Center (NLR, Marknesse) und GKN Fokker Landing Gear haben diese CFK-Bremsstrebe nach den Anforderungen von Liebherr konstruiert. Mit selbstentwickelter automatisierter Preforming-Technologie hat NLR funktionale Prototypen der CFK-Bremsstrebe gebaut, die von GKN Fokker Landing Gear getestet wurden.
In der zweiten von HECOLAG evaluierten Anwendung haben NLR und GKN Fokker Landing Gear auch eine untere Seitenstrebe aus CFK entwickelt in Verbindung mit Safran Landing Systems für das elektrifizierte Hauptfahrwerk. CW wird später im Jahr 2021 konkret über die Gesamtergebnisse des HECOLAG-Projekts berichten, hier liegt der Fokus jedoch auf dem Teilprojekt INNOTOOL 4.0, das von Themenmanager GKN Fokker Landing Gear geleitet wird, um die hochautomatisierte Produktion von CFK-Fahrwerksstrukturen mittels Resin Transfer Moulding (RTM) voranzutreiben. . Insbesondere zielt INNOTOOL 4.0 darauf ab, sensorintegrierte Werkzeuge zu demonstrieren, die den Weg zu kleineren Werkzeugen mit weniger Masse für schnellere Produktionszyklen, einfachere Handhabung und reduzierten Energieverbrauch sowie eine erhöhte Automatisierung für niedrigere Kosten und eine intelligente Prozesssteuerung für Verbundwerkstoffe 4.0 ebnen. Das Projekt INNOTOOL 4.0 wird vom Clean Sky 2 Joint Undertaking im Rahmen des EU-Forschungs- und Innovationsprogramms Horizon unter der GAP-Nr. 821261 finanziert.
INNOTOOL 4.0-Ziele
Der Demonstrator für diesen zweiten Teil von HECOLAG (siehe Anfangsbild) ist eher ein generischer Teil, erklärt Vergouwen. „Es dient der Demonstration von Teilekonstruktions-, Simulations- und Herstellungsmethoden, die die Leistung, Produktionsrate und Kosten liefern, die für Single-Aisle-Flugzeuge erforderlich sind.“ Bis Ende 2017 hatte das HECOLAG-Konsortium das erste CFK-Demonstratorteil und Produktionswerkzeug definiert, das thermische Verhalten des Werkzeugs analysiert und Leistungstests durchgeführt. Dieses große und komplexe Produkt bestand die vorläufige Designprüfung und erreichte später in diesem Jahr einen Technologiereifegrad (TRL) von 4. „Auf der Grundlage der Probleme und Erkenntnisse aus diesem ersten Demonstrator suchten wir nach Partnern für die Entwicklung der RTM-Werkzeugtechnologie zur Optimierung und Verkürzung des Aushärtungszyklus“, sagt Vergouwen. Ein Clean Sky 2 Call for Partners wurde 2018 veröffentlicht und an das Konsortium INNOTOOL 4.0 vergeben, das sich aus dem Ausrüstungs- und Automatisierungsanbieter Techni-Modul Engineering (TME, Coudes, Frankreich) und dem Harzinjektionsspezialisten Isojet Equipements (Corbas, Frankreich) zusammensetzt. Sie haben im April 2019 mit der Arbeit begonnen und die ersten Meilensteine im März 2021 abgeschlossen.
„Das Verbundteil muss mit geschmiedetem Stahl und Aluminium wettbewerbsfähig sein“, bemerkt Vergouwen von GKN Fokker Landing Gear. „Das ist nur mit Automatisierung möglich, die einen sehr geringen Arbeitsaufwand und kostengünstigere Materialien ermöglicht als das derzeitige autoklavgehärtete CFK in Luft- und Raumfahrt.“
Daher suchte INNOTOOL 4.0 nach der Integration von Sensoren in die RTM-Werkzeuge, die die Injektions- und Aushärtungsprozesse einschließlich der Erkennung der Harzfließfront überwachen und verwalten. „Das Ziel ist eine vollständige Automatisierung – laden Sie den Vorformling, drücken Sie einen Knopf, und die Spritzgussausrüstung regelt die Temperatur, den Druck, das Vakuum und die Aushärtung“, sagt Stéphane Besson, Commercial Director bei TME. Dies ist jedoch das erste Mal, dass GKN Fokker Landing Gear und TME mit der Heilungsüberwachung arbeiten. „Wir haben schon früher mit Temperatur- und Drucksensoren gearbeitet“, sagt Besson, „aber nicht mit Sensoren für Harzfluss und Polymerisation.“
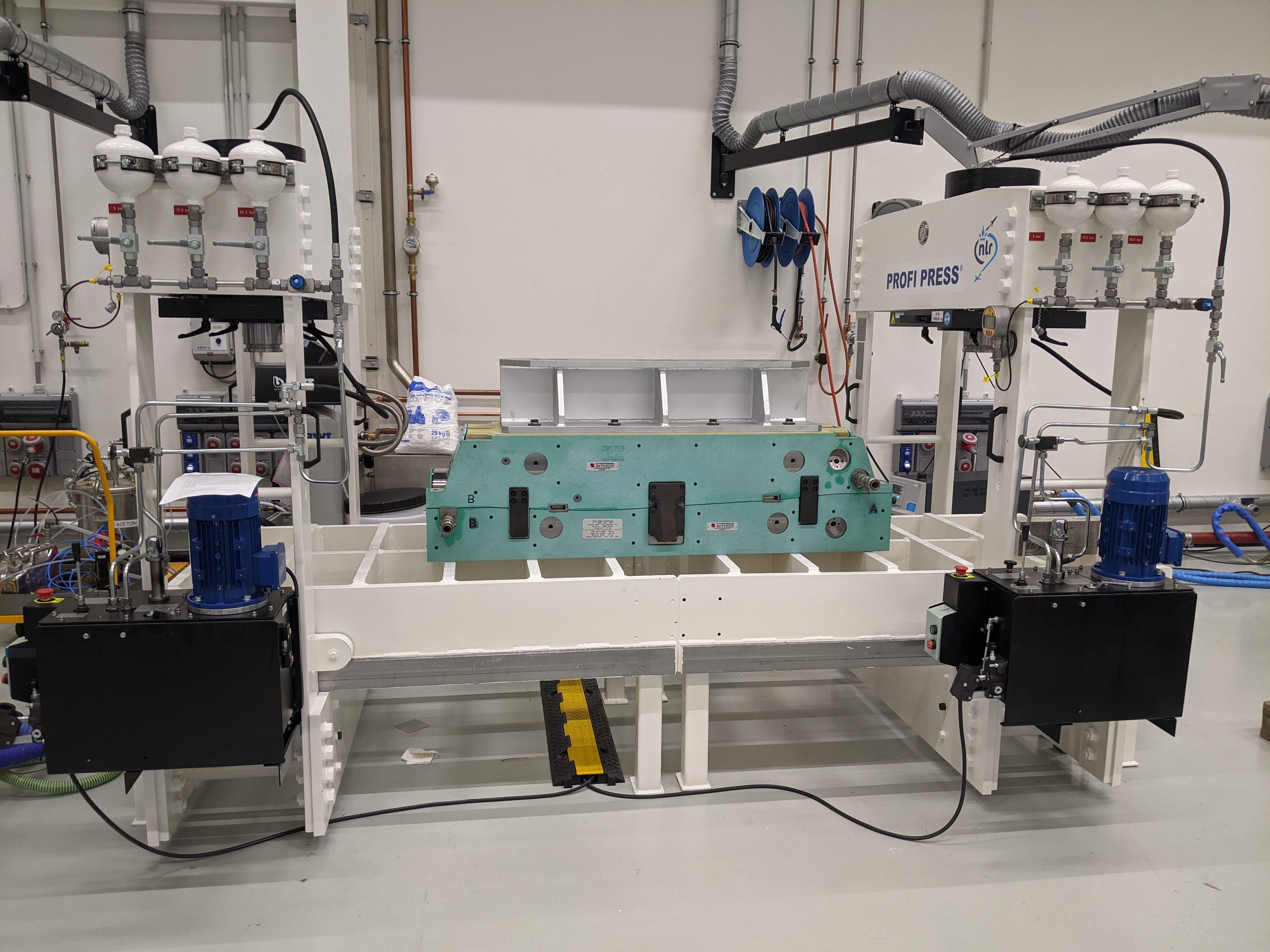
Die ersten Meilensteine des Projekts INNOTOOL 4.0 erforderten, dass TME und Isojet ein mit Sensoren ausgestattetes Spritzgusswerkzeug und ein Spritzgusssystem an das NLR liefern, das im März und April 2021 zur Herstellung von Demonstratorteilen verwendet werden sollte. Parallel dazu würde TME ein vorhandenes Werkzeug für die Produktion von CFK-Platten – Größe 600 x 600 Millimeter mit einer Dicke von 1-8 Millimetern – modifiziert mit den gleichen Sensoren für Prozesskontrollversuche in ihrem Werk. „Das macht man beim ersten Mal lieber im kleinen Maßstab als direkt an einem großen Werkzeug mit einem teuren Teil“, sagt Vergouwen. Daher verwendete TME ein anderes Werkzeug, aber die gleichen Sensoren, um ihre Fähigkeiten und Tiefe zu zeigen. Nach Abschluss dieser Tests würde das NLR das HECOLAG-Haupttool wiederverwenden, um eine neue Runde von CFK-Demonstratoren zu produzieren, um die Prozesssteuerung an tatsächlichen Teilen weiter zu optimieren.
Design von RTM-Produktionstools
TME begann mit der Produktion des RTM-Werkzeugdesigns mit der CATIA V5-Software von Dassault Systèmes (Vélizy-Villacoublay, Frankreich) für die mechanische und elektrische Konstruktion und ANSYS (Canonsburg, Pennsylvania, USA) für die thermische und mechanische Simulation. Dieses Werkzeug würde mit dem kolbenbasierten 1K-2K-System von Isojet (für ein- und zweikomponentige Harze) kombiniert, um Hexcel (Stamford, Connecticut, US) HexFlow 2K RTM 6 und Solvay (Alpharetta, Georgia, US) 1K . zu injizieren PRISM EP 2400 einkomponentige Epoxidharze in Luft- und Raumfahrtqualität bei einem Injektionsdruck von bis zu 20 bar.
„Die Form dieses Formwerkzeugs ist sehr komplex“, bemerkt Besson, „indem es unterschiedliche Dicken in der 3D-Trockenvorform mit einer geschlossenen, röhrenförmigen Form kombiniert. Dies führt zu komplexen Dickenübergängen mit Problemen bezüglich der Preform-Montage, Lagenendgenauigkeit, internen Temperaturgradienten und Harzschrumpfung sowie der Optimierung des Heizverfahrens und der Heizkapazität des internen Dorns, um eine kurze Zykluszeit zu ermöglichen. Um kurze Taktzeiten zu ermöglichen, müssen alle Elemente des Werkzeugs einfach zu bedienen, robust sein und ein schnelles Aufheizen und Abkühlen ermöglichen.“ Obwohl das Projekt INNOTOOL 4.0 kurzzeitig nichtmetallische Formlösungen erforderte, wurde aufgrund des Drucks, der erforderlich ist, um Falten zu minimieren und die Faserausrichtung während der Umformung sicherzustellen, ein typischer aufeinander abgestimmter Satz von oberen und unteren Stahlformen entwickelt.
Die aufeinander abgestimmten oberen und unteren Formen und der Dorn werden erhitzt und gekühlt. „Die aufeinander abgestimmten Formen nutzen einen integrierten Wasserkreislauf, während der Dorn elektrisch beheizt wird“, erklärt Besson. „Die Wasserzirkulation sorgt für schnelles Aufheizen und Abkühlen, um die Teilezykluszeit zu verkürzen, und die elektrische Heizung erreicht das gleiche im Dorn, wo der Platz begrenzt ist.“
„Eine weitere Herausforderung war die Anzahl der Teile im Dorn“, sagt Besson. „Aufgrund der komplexen Form und der Notwendigkeit, den Dorn nach dem Formen zu entfernen, bestand er aus sechs selbsterwärmenden Komponenten und zwei Trägerelementen, durch die die Sensoren hindurchgehen, um die Innentemperatur der Dornstücke zu kontrollieren. Im Einsatz werden diese Elemente mit Hilfe eines Grundträgers, der den Bediener führt, von Hand montiert.“ Die Arbeit mit einem aufblasbaren Dorn als Lösung wird im Rahmen des größeren HECOLAG-Projekts abgeschlossen, das jedoch nicht im Teilprojekt INNOTOOL 4.0 enthalten war.
Wärmestromsensoren
TME plante ursprünglich, dielektrische Sensoren zur Überwachung des Harzflusses und der Aushärtung zu verwenden (siehe „Die Kombination von dielektrischen Wechsel- und Gleichstrommessungen zur Überwachung der Aushärtung von Verbundwerkstoffen“), wechselte jedoch zu Wärmeflusssensoren von TFX (Boncourt, Schweiz). „Im Zuge der Entwicklung wollten wir Sensoren, die eine Messung ohne direkten Kontakt mit dem Polymer und den zu kontrollierenden Verbundwerkstoffen ermöglichen“, erklärt Jorge Lopez Torres, Projektleiter bei TME. „Die TFX-Sensoren haben dies ermöglicht, weil sie den Wärmefluss messen, der sich durch die Materialien ausbreitet.“ Er weist darauf hin, dass dies im Wesentlichen die gleiche Messung ist, die bei der Differential Scanning Calorimetry (DSC) verwendet wird, einer Labortechnik, die den Aushärtungszustand eines Polymers oder Komposits analysiert. Insbesondere messen sowohl TFX-Sensoren als auch DSC-Tests die während der Polymerisation/Härtung freigesetzte Wärme und führen zu einer Kurve des Wärmeflusses über Temperatur und Zeit.
Bei TFX-Sensoren stammen die Temperaturdaten von einem internen Temperatursensor innerhalb der Wärmestromsensoren. Obwohl dielektrische Sensoren ebenfalls mit einem internen Temperatursensor ausgestattet sind, unterscheiden sich die beiden Sensoren stark. „Dielektrische Sensoren messen direkt die Polymereigenschaften während der Aushärtung“, erklärt TFX-Manager Dr. Fabien Cara. „Wärmestromsensoren geben nicht den Zustand des Materials zu einem bestimmten Zeitpunkt an. Die Messung der während des Harzflusses und der Polymerisation erzeugten Wärme bietet jedoch einen guten Überblick darüber, wie sich der Prozess verhält und wie wiederholbar der Härtungszyklus für jedes produzierte Teil ist. Und wie bei DSC müssen wir die gesamte Kurve des Härtungsprozesses sehen, aber unsere Fähigkeit, die Härtung zu überwachen, ist sehr zuverlässig.“
Jahrzehntelange Erfahrung
TFX-Sensoren wurden im Jahr 2000 als Thermoflux gegründet und wurden von mehr als 100 Kunden weltweit in Forschungs- und Entwicklungszentren und in industriellen Anwendungen eingesetzt. „Wir haben vor mehr als 15 Jahren mit RTM zusammengearbeitet“, sagt Cara, „zuerst mit BMW für Automobilteile und auch für das technische Zentrum, das heute als Institute de Soudure [(Saint-Avold, Frankreich)] bekannt ist. In den Jahren 2006 und 2012 haben wir zwei große Projekte zur Überwachung der Aushärtung von Fanschaufeln von Flugzeugtriebwerken gestartet, die aus RTM- und 3D-gewebten Preforms hergestellt wurden. Safran hat ein Datenerfassungssystem, das wir für sie in ihrem Verbundwerkstofflabor in der Nähe von Paris entwickelt haben. Sie können bis zu 100 Signale gleichzeitig [(Wärmefluss, Temperatur und Druck]) aufzeichnen und diese für die Aushärtung und Überwachung von Prozessabläufen auswerten.“ TFX hat auch mit Hexcel in seinem Labor in Les Avenières, Frankreich, zusammengearbeitet, um die Qualität und die Verarbeitungszyklen mit Duroplasten zu überwachen, die in trockene Vorformlinge eingespritzt werden. TFX-Sensoren wurden auch in einem Projekt mit IRT-M2P (Porcelette, Frankreich) verwendet, um Compression RTM zu demonstrieren (Weitere Informationen). „Unsere Sensoren sind sehr effizient für schnelle Prozesse wie das Formpressen, auch bei SMC- und BMC-Formmassen“, sagt Cara. „Wir haben 2016 mit Huntsman Advanced Materials [(Basel, Schweiz)] auch einen JEC-Innovationspreis für eine Entwicklung mit dem Titel ‚Strukturelle Epoxidteile mit Autoklavenqualität in weniger als 1 Minute‘ gewonnen.“
TFX bietet Sensoren für jede Art von Composite-Spritzgussverfahren, basierend auf der Methode der Wärmeübertragung zum Sensor:Leitung (RTM, Press- und Spritzguss), Konvektion (Autoklav, Ofen) und Strahlung (Filament Winding, AFP). Die im Projekt INNOTOOL 4.0 verwendeten Sensoren waren leitfähig und für die Einbettung in Metall-RTM-Formen ausgelegt. „Sie liefern ein außergewöhnlich wiederholbares Signal in einem Abstand von bis zu 1 Millimeter von der Werkzeugoberfläche und dem Verbundmaterial“, bemerkt Cara.
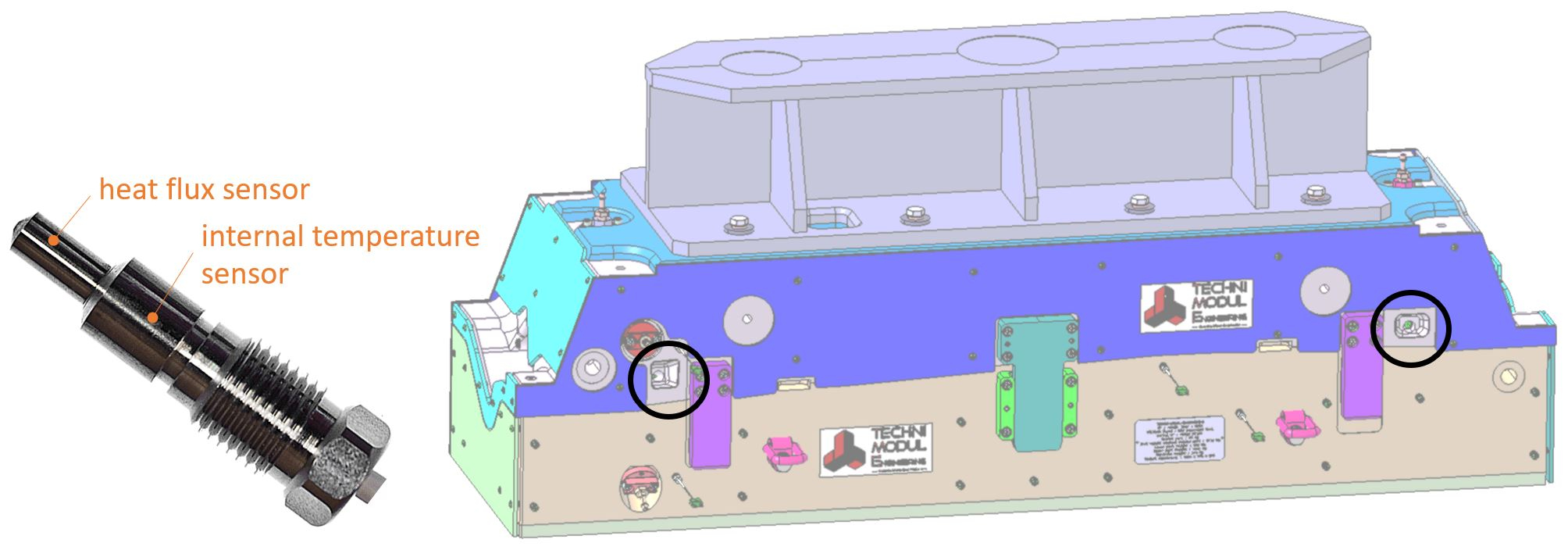
TME installierte zwei TFX-191-Sensoren – einen am Harzeingang und einen am Harzausgang – in der oberen Form des angepassten Produktionswerkzeugsatzes, den es dann an NLR schickte (Abb. 1, 2). Mit diesem Produktionswerkzeug fertigte das NLR im März und April 2021 HECOLAG-Demonstratorteile. Die TFX-191-Sensoren sind für dicke Metallwerkzeuge gedacht.
Parallel dazu hat TME ein kleineres hauseigenes Werkzeug zur Herstellung von Muster-CFK-Platten genommen und mit zwei kürzeren TFX-224-Sensoren für dünnere Werkzeuge modifiziert (Bild 3). Dieses RTM-Platten-Toolset wurde dann verwendet, um Sensor-Demonstrationsversuche gemäß den oben beschriebenen Zielen von INNOTOOL 4.0 durchzuführen. „Diese Sensoren ähneln denen, die wir für Safran verwendet haben“, sagt Cara, „aber sind jetzt viel kompakter und empfindlicher.“ Die Sensoren wurden in der Nähe der Mitte des Teils und des Harzausgangs platziert. Zusätzlich zu den Wärmestromsensoren hat TFX zwei Datenerfassungssysteme entwickelt und geliefert – eines geliefert an Isojet und eines, das von TME für die CFK-Plattenversuche verwendet wird.
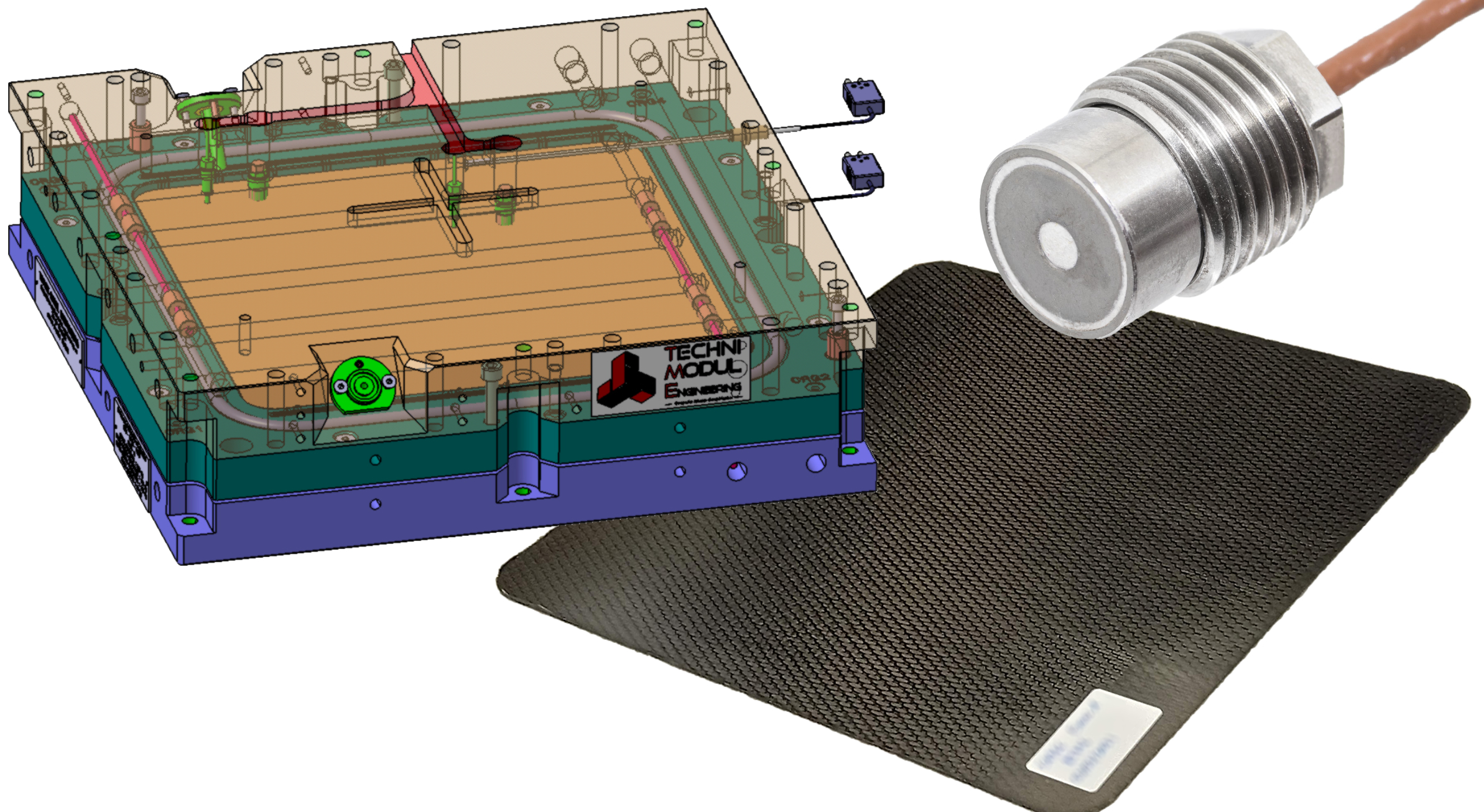
INNOTOOL 4.0-Testergebnisse
Die Versuche, die TME mit seinem mit TFX-Sensoren modifizierten Plattenwerkzeug durchführte, testeten zwei verschiedene Harze – HexFlow RTM 6 und PRISM EP 2400 – sowie den Einfluss der Teiledicke und der Gesamthärtungszeit. „Die Sensoren lieferten schöne Signale, um den Aushärtungszyklus zu überwachen“, sagt Cara. „Das Team analysierte dann die Härtungskurven und zeigte, dass die Härtungszeit für RTM 6 um mindestens 30 Minuten gegenüber der vorgeschriebenen zweistündigen Härtung reduziert werden konnte.“
Dies ist in der folgenden Kurve zu sehen, wobei t =0 Stunden der Beginn der Injektion ist. Beachten Sie, dass die Aushärtungszeit beginnt, wenn die Temperatur 180 °C erreicht und das Ende der Aushärtung 99% des relativen Aushärtungsgrades entspricht (siehe vertikale Achse rechts). Das Ende der Aushärtung fällt auch mit der Stabilisierung des Rohwärmestroms zusammen.
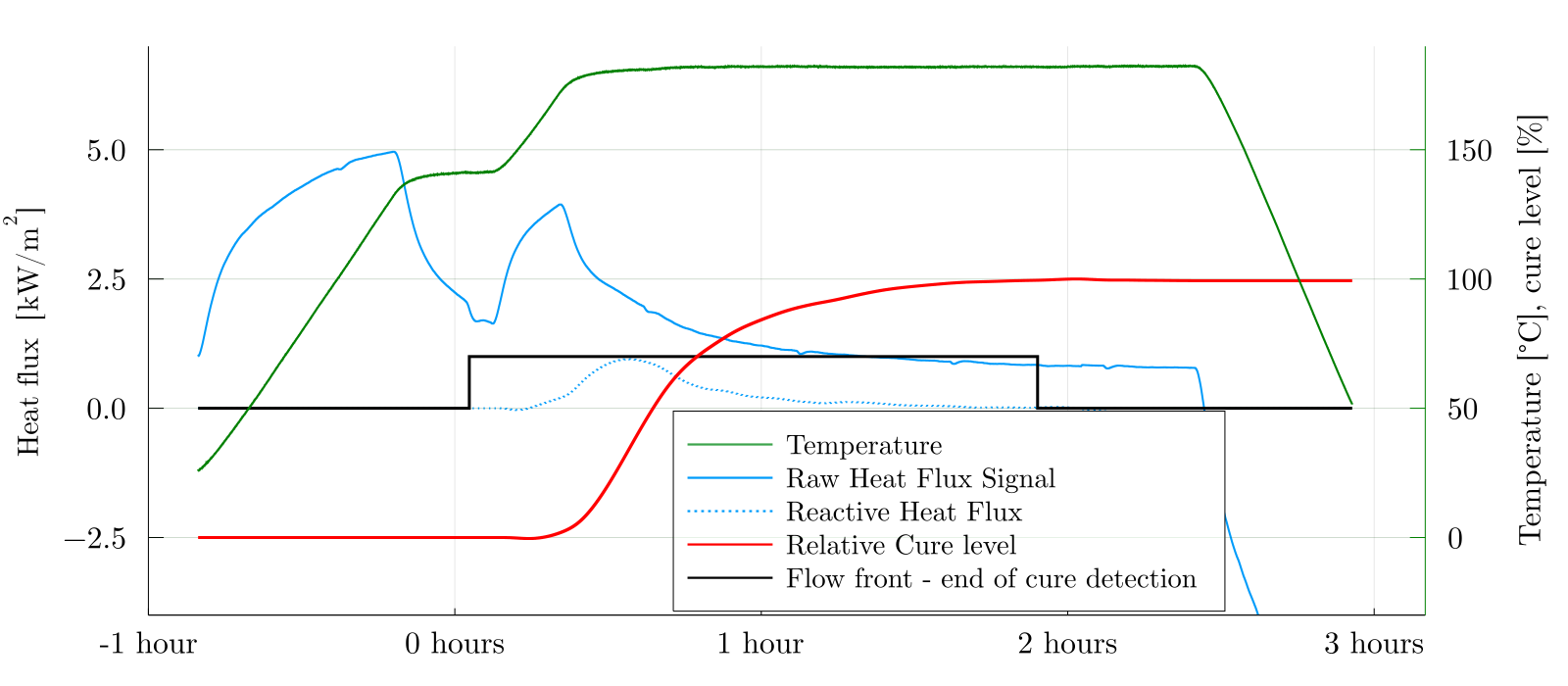
Dies wurde durch Messungen des Härtungszustands von entformten Teilen mit dynamischer mechanischer Analyse (DMA) verifiziert, einer alternativen Labortechnik zur DSC, die die Glasübergangstemperatur (Tg .) misst ) für Verbundwerkstoffe. „Die DMA-Ergebnisse bestätigten, dass für RTM 6-Harz der Tg bleibt nach 90 Minuten Aushärten bei 180 °C unverändert“, fügt er hinzu.
Auch der Einfluss der Dicke wurde untersucht. „Die ersten CFK-Platten, die TME in ihren Sensor-Demonstrationsversuchen getestet hat, waren weniger als 2 Millimeter dick“, bemerkt Cara. „Diese Platten hatten auch ein hohes Faservolumen (50–60 %) und einen langsamen Härtungszyklus, um Exothermie und potenzielle Probleme mit thermischer Belastung und Teilequalität zu vermeiden. All dies ist für Luft- und Raumfahrtteile ganz normal, aber es bedeutet, dass sehr wenig Harz vorhanden ist und daher die durch die Harzreaktion freigesetzte Wärmestrommenge gering war. Wir suchten also faktisch nach der Nadel des Wärmeflusses aufgrund der Harzhärtung in einem Ozean des Erhitzens des Werkzeugs und des Teils.“
Mit anderen Worten, wie Cara erklärt:„Die meisten RTM-Härtungszyklen in der Luft- und Raumfahrt beinhalten das Einspritzen von Harz bei einer Temperatur und das anschließende Aushärten bei einer zweiten, höheren Temperatur. So heizt man nach dem Einspritzen das Werkzeug auf Aushärtetemperatur auf, was einen großen Wärmestrom im Gesamtsystem erzeugt.“ Wie bei DSC-Tests besteht der Schlüssel zur Überwachung der Härtung mit Wärmeflusssensoren jedoch darin, die während der Polymerisation/Härtung freigesetzte Wärme zu messen und diese Messungen in einer Kurve des Wärmeflusses gegenüber der Temperatur im Formsystem und der Zeit anzuzeigen. „Also haben wir eine Methode erfunden, die uns hilft, die Grundlinie der Erwärmung der Form und die Weiterleitung dieser Wärme an das Teil zu subtrahieren, sodass es möglich ist, den Wärmefluss der Harzreaktion zu identifizieren.“
Obwohl die Prozessbedingungen in den anfänglichen dünnen Platten sehr anspruchsvoll waren, sagt Cara, „konnten wir immer noch den Wärmefluss durch die Harzreaktion sehen. Da wir jedoch auch dickere Teile herstellten, konnten wir genau den Unterschied in den Wärmeflussniveaus je nach Teiledicke sehen und dies bestätigte unsere Überwachung der Härtung bei den dünnen Teilen.“ Beachten Sie, dass die obige Kurve (auch im Eröffnungsfoto gezeigt) unter Verwendung von RTM 6-Harz in einer 3,2 Millimeter dicken Platte erhalten wurde.
Die Ergebnisse für die Erkennung der Harzfließfront waren jedoch problematischer. „Für den Sensor in der Nähe des Ausgangs konnten wir den Fluss sehr gut sehen, aber nicht für den Sensor in der Nähe des Zentrums, wo das Harz sehr spät ankam“, sagt Cara. „Die Fließfronterkennung mit Wärmeflusssensoren erfordert, dass der Harzfluss eine Änderung des lokalen thermischen Felds hervorruft. Dies tritt auf, wenn das Harz nicht die gleiche Temperatur wie der Vorformling hat.“ Er stellt fest, dass ΔT größer als 0,1°C für den Nachweis ausreichend ist. „Bei den Versuchen mit dünnen CFK-Platten war die Temperatur in der Form jedoch sehr gleichmäßig und das Harz kam sehr langsam an. Somit reichte der thermische Kontrast nicht aus, um die Harzankunft gegenüber dem thermischen Rauschen im Gesamtsystem zu erkennen. Die Harzankunft am Ausgang war jedoch aufgrund von Angusskanälen [Lücken zwischen der Vorform und der Formkante, siehe „Herstellung der Teile mit komplexer Geometrie von RAPM“] schneller, was zu einem größeren thermischen Kontrast beiträgt, der leichter zu erkennen und zu überwachen ist. ”
Cara schlägt vor, dass diese Überwachung der Harzflussfront mit neuen aktiven Sensoren verbessert werden könnte, die TFX entwickelt hat und die eine integrierte Heizfunktion innerhalb des Sensors verwenden. „Auf diese Weise können die Sensoren dazu beitragen, den erforderlichen thermischen Kontrast in Teilen und Prozessen bereitzustellen, bei denen dies von Natur aus schwierig ist“, erklärt er.
Erweiterung der kombinierten Prozesssteuerungsfunktionen
„Wir sind mit der bisherigen Arbeit zufrieden“, sagt Torres, „aber dies ist nur ein erster Schritt. Das Ziel ist es, diese Wärmeflusssensoren für die Steuerung der Verarbeitung von Verbundwerkstoffen in Produktionsumgebungen zu verwenden.“ Dies sei möglich, so Cara, indem automatisch ein Signal vom Sensorsystem an die Injektionsanlage basierend auf der Harzankunft und an die Presse basierend auf einer Nullsteigung der Aushärtekurve gesendet wird. Torres fügt hinzu, dass TME über Prozesssteuerungssysteme für die Spritzgussmaschine und die RTM-Presse verfügt, die Temperatur und Druck steuern. „Der nächste Schritt“, sagt er, „ist, die TFX-Sensoren in diese Steuerungssysteme zu integrieren und den Gesamtprozess vom Laptop aus zu steuern.“ Cara stellt fest, dass TFX-Sensoren und die Datenerfassung auch mit Drucksensoren (z. B. Kistler, Winterthur, Schweiz) arbeiten, um diese Gesamtprozesssteuerung zu unterstützen, und sein Unternehmen entwickelt einen Sensor, der den Wärmefluss, die Temperatur und Druck in einem einzigen integrierten Gerät.
Aber ist diese Prozesskontrolle bezahlbar? Cara sagt, dass sich die anfängliche Investition von 10 bis 30.000 US-Dollar für das Überwachungssystem im Allgemeinen in der Entwicklungsphase rentiert und Trial-and-Error durch ein verbessertes Prozess- und Teileverständnis reduziert. „Das System sorgt dann für Einsparungen während der Produktion, verkürzt die Zykluszeit, gewährleistet die Wiederholbarkeit und ermöglicht eine frühzeitige Erkennung von Drifts oder Nichtkonformitäten.“
Bei GKN Fokker glaubt Vergouwen, dass, sobald die Fähigkeit zur Reduzierung der Zykluszeit und zur Verbesserung der Kosten nachgewiesen ist, sich Verbundwerkstoffe nicht nur in der Art von Fahrwerkskomponenten vorstellen können, die in den Projekten INNOTOOL 4.0 und HECOLAG demonstriert wurden, sondern in allen Arten von Teile. Das würde unseren Designraum öffnen und es uns ermöglichen, die Grenzen von Leichtbaufahrwerken noch weiter zu verschieben.“ Besson sieht eine noch breitere Anwendung:„Diese Art der Prozesskontrolle kann für alle Arten von Formen und Verbundteilen entwickelt werden.“
Harz
- Sensortypen mit ihren Schaltplänen
- ams beleuchtet die Sensors Expo 2019 mit innovativen Demonstrationen
- Kartierung des Temperaturflusses in Haushalten mit billigen Sensoren
- Messen Sie Temperaturen mit einem 1-Draht-DS18B20-Sensor und Raspberry Pi
- Kontrollieren eines Effekts mit echten Sensoren
- Lesen analoger Sensoren mit einem GPIO-Pin
- Auslesen von analogen Sensoren mit Raspberry Pi und Zabbix Supervisor
- Win10 IOT-Bewässerungssteuerung mit Feuchtigkeitssensoren
- Verbesserte Überwachung der Luftverschmutzung mit IoT-Sensoren
- Vereinfachte Sensorherstellung mit Klebeverbindungen