3D-Druck-CFK-Formen für RTM-Flaperons, Exoskelette und mehr
Photo Credit:TU München Lehrstuhl für Carbon Composites (LCC) und QPoint Composite
Der Lehrstuhl für Carbon Composites (LCC) wurde 2009 am Fachbereich Maschinenbau der Technischen Universität München (TUM, München, Deutschland) mit Förderung der SGL Carbon (Wiesbaden, Deutschland) eingerichtet. Seine Mission ist die Durchführung von Forschung und Entwicklung in kohlenstofffaserverstärkten Polymermaterialien (CFK), Prozessen und Anwendungen, einschließlich Simulations- und Testprojekten. Ein „Lehrstuhl“ im deutschen Hochschulsystem ist die kleinste Einheit aus einem Professor und seinem Team. Das LCC-Team wird geleitet von Prof. Dr.-Ing. Klaus Drechsler und beschäftigt derzeit 30 hauptamtliche Forscher. Obwohl die SGL-Finanzierung 2016 ausgelaufen ist, hat das LCC seine Führungsrolle in der F&E im Bereich Verbundwerkstoffe fortgesetzt, einschließlich des Baus der Form für die untere Hälfte des Multifunctional Fuselage Demonstrator (MFFD), siehe Seitenleiste unten, und umfasst jetzt auch 3D-Druck/Additiv Herstellung.
Dieser Blog begann, als mir CEAD (Delft, Niederlande) mitteilte, dass LCC eines seiner extruderbasierten AM-Flexbot-Systeme für den 3D-Druck mit einem Roboterarm gekauft hatte. Mein anschließendes Interview mit dem LCC-Forscher Patrick Consul enthüllte jedoch eine Fundgrube an Projekten, darunter COMBO3D innerhalb von Clean Sky 2 zum 3D-Drucken einer thermoplastischen Composite-RTM-Form für die Herstellung einer duroplastischen Composite-Flugzeugklappe und EMOTION zur Herstellung des Werkzeugs zum Formen der unteren Hälfte des thermoplastischen Composite-Multifunktionalen Rumpfdemonstrators (MFFD) von Clean Sky 2 sowie als sekundäres Teilwerkzeug, um zu demonstrieren, wie derselbe Rumpf durch direkte in-situ-Konsolidierung (aus dem Autoklaven) hergestellt werden könnte. Interessant fand ich die ganze Diskussion, wie die TUM an diesem Punkt angekommen ist und wohin die Reise gehen soll.
MMFD untere Werkzeughälfte
Siehe meinen Blog vom Februar 2020:„Nachweisen des LM PAEK-Schweißens für den multifunktionalen Rumpfdemonstrator“. Diese Seitenleiste stammt aus dem Papier „Development of a Multifunctional Fuselage Demonstrator“ vom Februar 2020 von Bas Veldman, Programmmanager für das MFFD bei GKN Fokker (Hoogeveen, Niederlande).
Die Schale der unteren Hälfte des MFFD besteht aus einer thermoplastischen Haut, die mit geschweißten Stringern, Clips und Spanten versteift ist. Der zu demonstrierende Herstellungsprozess umfasst drei wesentliche Schritte:
- Prepreg-Band für die große Haut des Demonstrators wird von der bestehenden Laser-AFP-Maschine von NLR auf einem flachen, geneigten Tisch aufgebracht.
- Layups werden robotergesteuert mit Saugnäpfen zu einer weiblichen Konsolidierungsform transportiert und dort ohne Erhitzen drapiert.
- Nach dem Vakuumieren wird die Haut in einem Autoklaven konsolidiert.
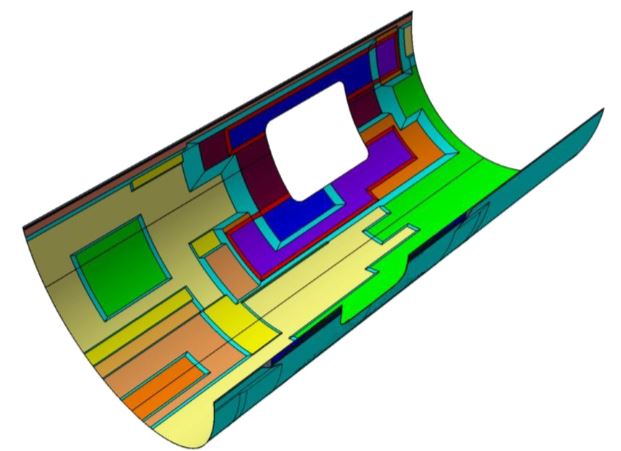
Die Verwendung einer weiblichen Konsolidierungsform bietet eine viel einfachere (flache) Oberfläche als bei einem männlichen Werkzeug, während die aerodynamischen Einschränkungen der äußeren Oberflächenqualität der Haut direkt kontrolliert werden.
Das MFFD-Projekt fordert auch außerhalb des Autoklaven zu untersuchende Prozesse – beginnend parallel zum großen multifunktionalen Rumpfdemonstrator – in einem nachfolgenden kleineren Demonstrator. Insbesondere in-situ thermoplastischer Verbundwerkstoff Herstellung, bei der eine Konsolidierung während des Laminierens erreicht wird, in Betracht gezogen, da sie den Autoklavenschritt vollständig eliminieren und somit die Herstellung auf ein einstufiges Verfahren reduzieren kann.
Enhanced Mold for Thermoplastic Fuselage in and out of Autoclave Consolidation oder EMOTION (https://cordis.europa.eu/project/id/864474) ist das Clean Sky 2-Projekt zur Herstellung der MFFD-Unterschale. „Das klingt einfach“, sagt Patrick Consul vom Koordinator des Projekts an der TU München, „aber es ist ziemlich anspruchsvoll, da es auf 400 °C erhitzt werden muss. Dies liegt weit über dem Temperaturbereich, in dem Invar36 keinen signifikanten CTE [Wärmeausdehnungskoeffizient] hat.“ Invar wird aufgrund seiner geringen Ausdehnung während der Hochtemperatur-Härtungszyklen häufig für Verbundformwerkzeuge verwendet. Der CTE von Invar steigt jedoch mit der Temperatur. „Die Herausforderung“, bemerkt Consul, „besteht darin, die Wärmeausdehnung während des Aufheizens und Abkühlens für die 8 mal 4 Meter große Form und die Rumpfhaut während der Aushärtung zu kontrollieren.“
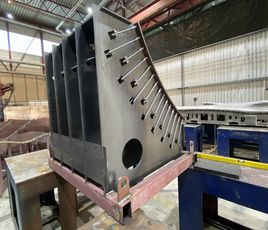
Fortschritt in der additiven Fertigung
„Wir sind 8-9 Personen, die innerhalb des LCC an der additiven Fertigung arbeiten“, sagt Consul. Er beginnt die Geschichte dieser Arbeit mit dem Kauf einer lasergestützten Klebebandbestückungsmaschine für thermoplastische Verbundwerkstoffe durch das LCC im Jahr 2012 von AFPT (Dörth, Deutschland). Später kam eine Maschine von Coriolis Composites (Quéven, Frankreich) hinzu, um eine automatisierte Faserplatzierung (AFP .) zu ermöglichen ) von duroplastischen Prepregs. Die ersten Desktop-Drucker auf Filamentbasis wurden 2017 gekauft. „Ich bin auch 2017 dazugekommen, um bei der Entwicklung neuer Anwendungen und Forschungsprojekte zu helfen, einschließlich der Angebotserstellung beispielsweise für Clean Sky 2. Er erklärt, dass Clean Sky 2-Projekte auf der Grundlage von Vorschlägen vergeben werden, die Themenmanagern als Reaktion auf öffentlich veröffentlichte Aufforderungen zur Einreichung von Vorschlägen (CFP) vorgelegt werden. LCC war mit seinen Vorschlägen für das COMBO3D-Projekt CFP08 und das EMOTION-Projekt CFP09 erfolgreich. Beides wird weiter unten diskutiert.
„Wir haben einige andere Projekte, von denen einige den 3D-Druck mit Endlosfaserverstärkungen untersuchen“, sagt Consul. „Andere verwenden einen laserintegrierten Druckkopf, um das Verbundsubstrat vorzuwärmen, um auf bereits konsolidierte CFK-Teile zu drucken oder um die interlaminare Scherfestigkeit (ILSS) zwischen gedruckten Schichten zu erhöhen. Ein weiteres Projekt untersucht beispielsweise Werkzeuganwendungen, bei denen nur eine geringe Anzahl spezialisierter Verbundteile vorhanden ist.“
„Diese Projekte werden kontinuierlich durch numerische Simulationen unterstützt, um das Verhalten der additiv gefertigten Teile während und nach dem Druckprozess vorherzusagen“, fährt er fort. „Das LCC ist auch an einem Projekt mit dem Imperial College of London beteiligt, das die Herstellung von Exoskeletten aus 3D-gedrucktem CFK zum Ziel hat. Ein weiteres Projekt erforscht Gitterstrukturen, um die Eigenschaften von 3D-gedruckten Teilen hinsichtlich Steifigkeit, Festigkeit oder Energieaufnahme zu optimieren.“
Fortschritt bei Druckern

„Wir begannen mit einem einfachen 3D-Drucker auf Basis von FDM (Fused Deposition Modeling) von Apium (Karlsruhe, Deutschland), um spezielle Testvorrichtungen zu drucken, die eine hohe Steifigkeit erfordern“, erklärt Consul. „Der Drucker war 3 Meter lang und 1 Meter breit und hatte eine hohe Materialleistung, um die Druckzeit zu verkürzen. Obwohl es keine Endlosfasern verwenden konnte, war es für das Drucken mit PEEK, PEKK und geschnittenem kohlenstofffaserverstärktem PEEK gut ausgelegt. Es verwendete nicht nur ein beheiztes Bett, sondern auch eine beheizte Platte um den Druckkopf, die dazu beitrug, eine homogene Temperaturverteilung in den Drucken zu erzeugen, die thermische Belastung zu reduzieren und die Kristallisation sicherzustellen.“
„Wir hatten auch eine Zeit lang einen Markforged-Drucker (Cambridge, Massachusetts, USA) und bekamen dann einen Anisoprint [Esch-sur-Alzette, Luxemburg]“, sagt Consul. Obwohl der Markforged-Drucker FDM mit Endlosfasern ermöglichte, entschied sich das LCC-Team, es nicht beizubehalten. „Das Problem, das wir hatten, war, dass das System sehr geschlossen war“, erklärt Consul. „Die Slicer-Software von Markforged war für die Forschung zu schwierig zu verwenden, da sie unsere Möglichkeiten stark einschränkte. Wir konnten nur eine Lage aus Endlosfasermaterial und dann eine Lage aus kurzfaserverstärktem thermoplastischem Filament darüber drucken. Der Slicer, der den Code generiert, würde keinen G-Code von uns akzeptieren. Es gab also keine Möglichkeit, der Maschine zu sagen, dass sie es so drucken soll, wie wir es wollten, mit Endlosfasern in jeder Schicht usw.“
Darauf angesprochen erklärt Markforged, dass seine Systeme nie für Forschungszwecke gedacht waren, sondern einfach und robust für den weit verbreiteten Einsatz in der Teileherstellung konzipiert wurden, regelbasierte Faserpfade verwenden und einen geringen Aufwand und Zeitaufwand für die Konfiguration des Slicers erfordern . Es ist Die Eiger-Software ermöglicht es Benutzern, Ebenen individuell zu konfigurieren, und Markforged freut sich über Feedback und priorisiert die Verbesserung der Benutzererfahrung für seine Kunden.
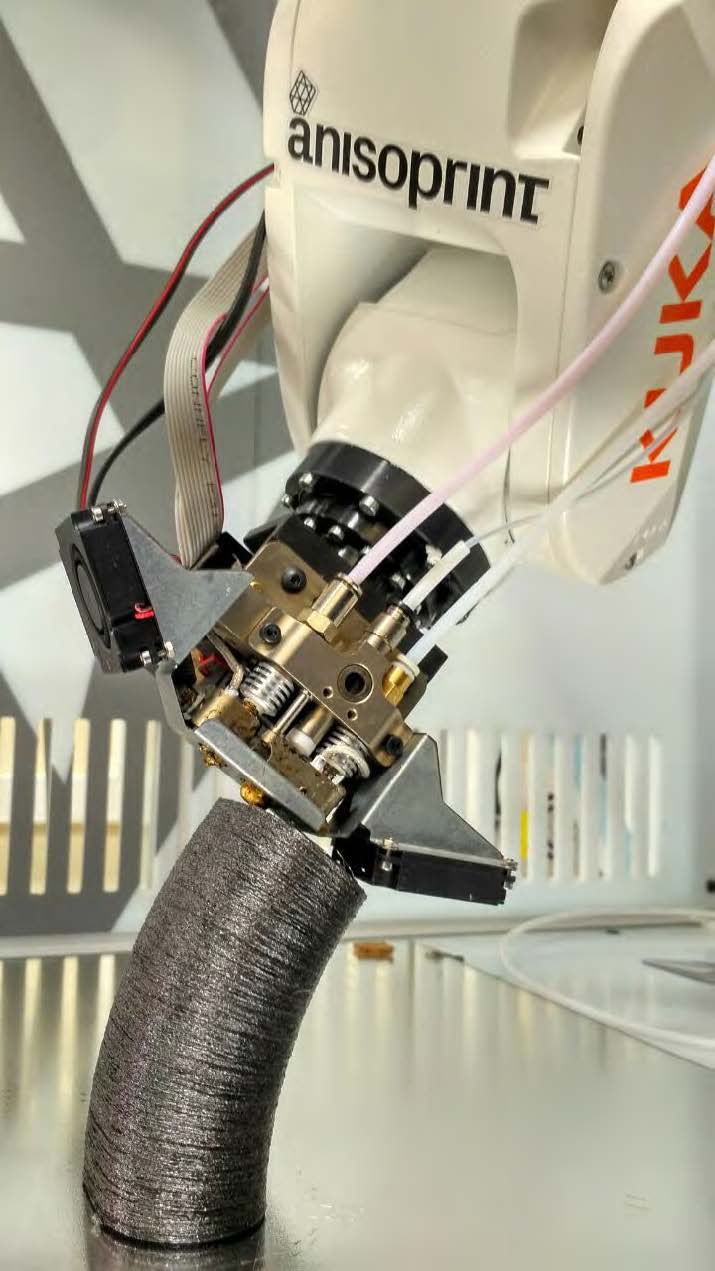
„Anisoprint, das einen vollständig offenen G-Code-Slicer verwendet, hat uns einen besseren Zugang zu dem Prozess ermöglicht“, sagt Consul. „Es ist auch in der Lage, Endlos-Carbonfasern zu drucken, und zwar nicht nur in 2D-Schichten, sondern auch außerhalb der Ebene, in 3D-Kurven. Wir haben einen Anisoprint-Druckkopf für einen kleinen Kuka-Roboter, der 1 Meter mal 1 Meter große Teile produzieren kann. Er ist größer als die meisten Desktops, aber klein für ein Robotersystem."
Aber was ist mit der Dual-Matrix von Anisoprint Duroplast-Thermoplast (TS-TP) Materialien? Wie in meinem 2019-Blog zu Anisoprint erklärt:„… es imprägniert zuerst die Endlosfaserverstärkung mit einem Duroplast Polymer und extrudiert dieses dann beim Drucken in das geschmolzene thermoplastische Filament.“ Consul antwortet, dass die Haftung zwischen dem TS-Filament und dem TP ziemlich gut ist. „Bei unseren ersten Versuchen konnten wir im Vergleich zum Markforged-Drucker einen höheren Faservolumengehalt erzielen, aber das lag daran, dass wir den G-Code modifizieren konnten. Der Anisoprint-Druckkopf schiebt das TS-Filament in das TP und legt dieses dann ab. Wir planen, diesen Drucker für Exoskelettteile zu verwenden. Es ist eine einfache Möglichkeit, höherfeste Fasern zu integrieren."
Drucker für extrudierte Pellets
Der nächste Schritt war ein Großdrucker, zuerst mit kurzfaserverstärktem TP und dann mit Endlosfaser-TP. „Wir haben zuerst einen Extruder entwickelt, der auf einem Roboter montiert ist, und dann folgte schnell unser Interesse an der CEAD-Maschine. Wir hoffen, im nächsten Jahr Endlosfasern in diese beiden Systeme integrieren zu können.“
Aber wozu brauchten Sie die CEAD-Maschine, wenn Sie bereits einen Extruder an einem Roboterarm hatten? „Der ursprüngliche Extruder war die Beta-Version eines Dyze Pulsar Pellet-Extruders, der mit PAEKs maximal etwa 2 kg/h und etwa 1 kg/h ausgibt, aber mit mehr als 20 % Kohlefaserbeladung zu kämpfen hat“, sagt Consul. „Allerdings ist die durchschnittliche Leistung geringer, weil der Roboter während des Druckens oft beschleunigt und verlangsamt. Bei COMBO3D benötigten die ersten Formhälften im Kleinformat bereits mindestens 36 Kilogramm, sodass wir für den Druck einer einzelnen Hälfte rund 48 Stunden benötigten. Außerdem mussten wir immer jemanden dabei haben, denn Fehler, wie eine blockierte Materialzuführung oder ein Verziehen von Teilen, konnten jederzeit passieren.“
Da der endgültige Demonstrator von COMBO3D etwa zehnmal größer ist als die anfänglichen Kleinteile, war das Drucken mit diesem ersten Extrudersystem nicht möglich, sagt Consul. „Außerdem hatten einige der von Victrex gelieferten Materialien eine höhere Viskosität und dieser erste Extruder konnte nicht genug Drehmoment bereitstellen, um diese Polymere zu extrudieren. Mit dem CEAD-Drucker haben wir eine maximale Leistung von ca. 12,5 kg/h und nach einigen Teststunden hatten wir eine stabile durchschnittliche Leistung von ca. 5-6 kg/h. Dadurch konnten wir die kleine Formhälfte in weniger als 8 Stunden drucken und können höhere Fasergehalte verwenden, um den Verzug zu reduzieren, wodurch der Prozess insgesamt einfacher zu kontrollieren ist.“
„Während der Pulsar uns bereits ermöglicht hat, Pellets zu verwenden, eine hohe Materialleistung zu erzielen und die Freiheitsgrade eines Roboters zu nutzen“, fährt er fort, „erweitert der CEAD-Drucker unsere Fähigkeiten in Richtung größerer Teile, höherer Fasergehalte und einer breiteren Palette von Polymeren . Der Pulsar schließt die Lücke zwischen unseren filamentbasierten Druckern und dem CEAD, nicht nur in Bezug auf die Ausgabe, sondern auch in Bezug auf die Düsengröße und die resultierenden Details der Drucke.“
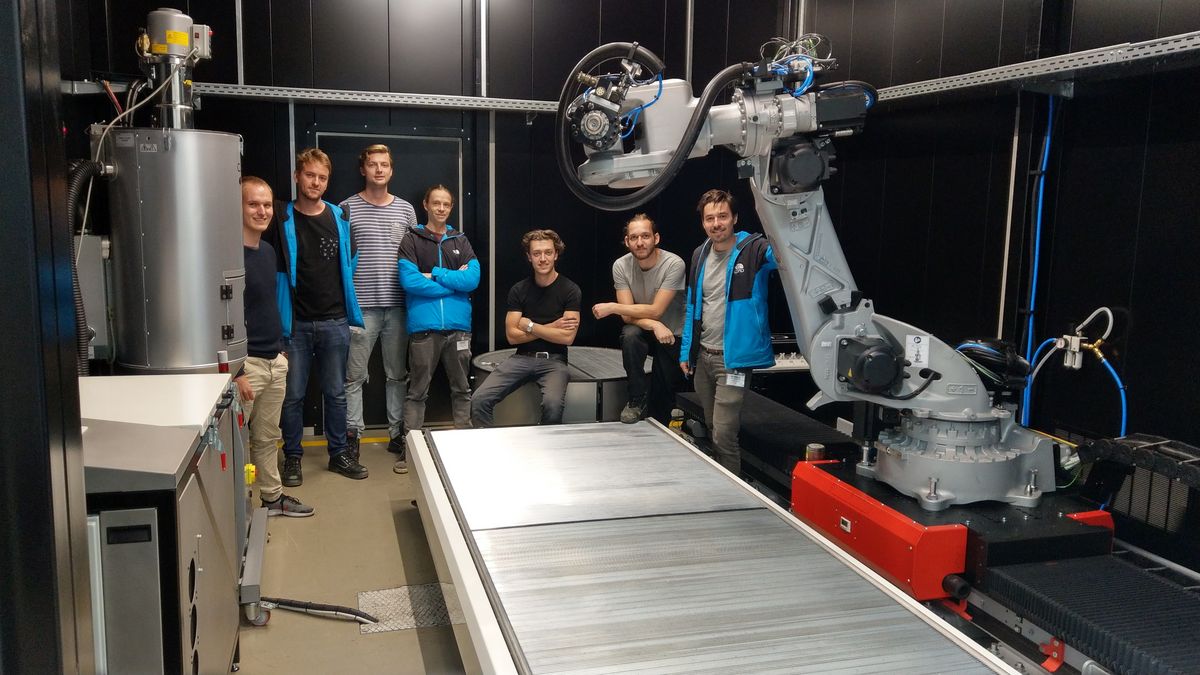
Technische Daten von CEAD AM Flexbot:
- Technische Daten von AM Flexbot:
- Pelletsbasierte Extrusionsdrucke bis zu 12,5 kg/h (unverstärkt und kurzfaserverstärkt)
- Materialbearbeitung bis 450°C
- Bauvolumen 3000 x 1200 x 1700 Millimeter
- Bauplatte auf Drehtisch oder Flachtisch (beheizbar)
- Nachbearbeitung mittels Fräskopf.
COMBO3D
Das Ziel dieses Clean Sky 2-Projekts ist der 3D-Druck einer Form zur Herstellung eines Demonstrator-Verbundstoff-Flaperons (1,5 x 3 Meter) für ein großes Passagierflugzeug, Teil des Arbeitspakets A-3.1:Multidisziplinärer Flügel für hohe und niedrige Geschwindigkeit. Ziel des Einsatzes der additiven Fertigung ist es, die Vorlaufzeit für die Werkzeugherstellung zu verkürzen. Das Projekt startete im Januar 2019 und endet im März 2021. Zu den Partnern zählen Alpex Technologies (Mils bei Hall, Österreich), Leichtmetallspezialist Leichtmetallkompetenzzentrum Ranshofen (Ranshofen, Österreich) und Victrex (Thornton Cleveleys, UK), Lieferant des Hochleistungsthermoplasten Polyaryletherketon (PAEK).
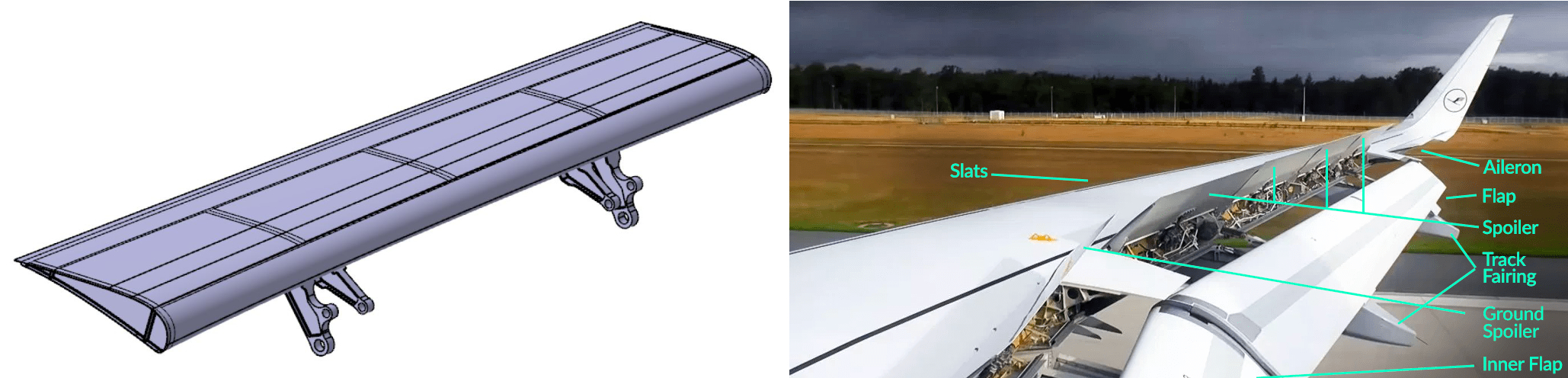
Ein weiterer wichtiger Teil des Projekts besteht darin, zu demonstrieren, dass dieses Kohlefaser-/Epoxid-Flaperon mit Resin Transfer Moulding (RTM) anstelle von autoklavgehärtetem Prepreg hergestellt werden kann. Das RTM-Teil härtet bei denselben 180 °C wie die Autoklaventeile. Um die thermische Stabilität zu gewährleisten, wird das Werkzeug mit kurzem carbonfaserverstärktem PAEK bedruckt, das eine Schmelzetemperatur von 305°C hat.
Um den Aushärtungszyklus zu verkürzen, integriert die 3D-gedruckte Form eine aktive Temperaturregelung. „Wir müssen die Form im Vergleich zum Autoklaven schneller aufheizen und abkühlen können“, stellt Consul fest. „Wir werden ein Netz aus elektrischen Heizelementen 3 Millimeter unter der Werkzeugoberfläche verwenden und auch gedruckte Kanäle für erhitztes Öl oder Luft 6 Millimeter unter der Werkzeugoberfläche integrieren. Auf diese Weise können wir die Werkzeugoberfläche sehr schnell erwärmen, aber auch die Kanäle zur Erwärmung des gesamten Werkzeugvolumens nutzen. Wir streben eine um 50 % schnellere Heiz- und Kühlrate als beim Autoklaven an und sind zuversichtlich, dass wir eine um mindestens 30 % schnellere Rate erreichen können.“
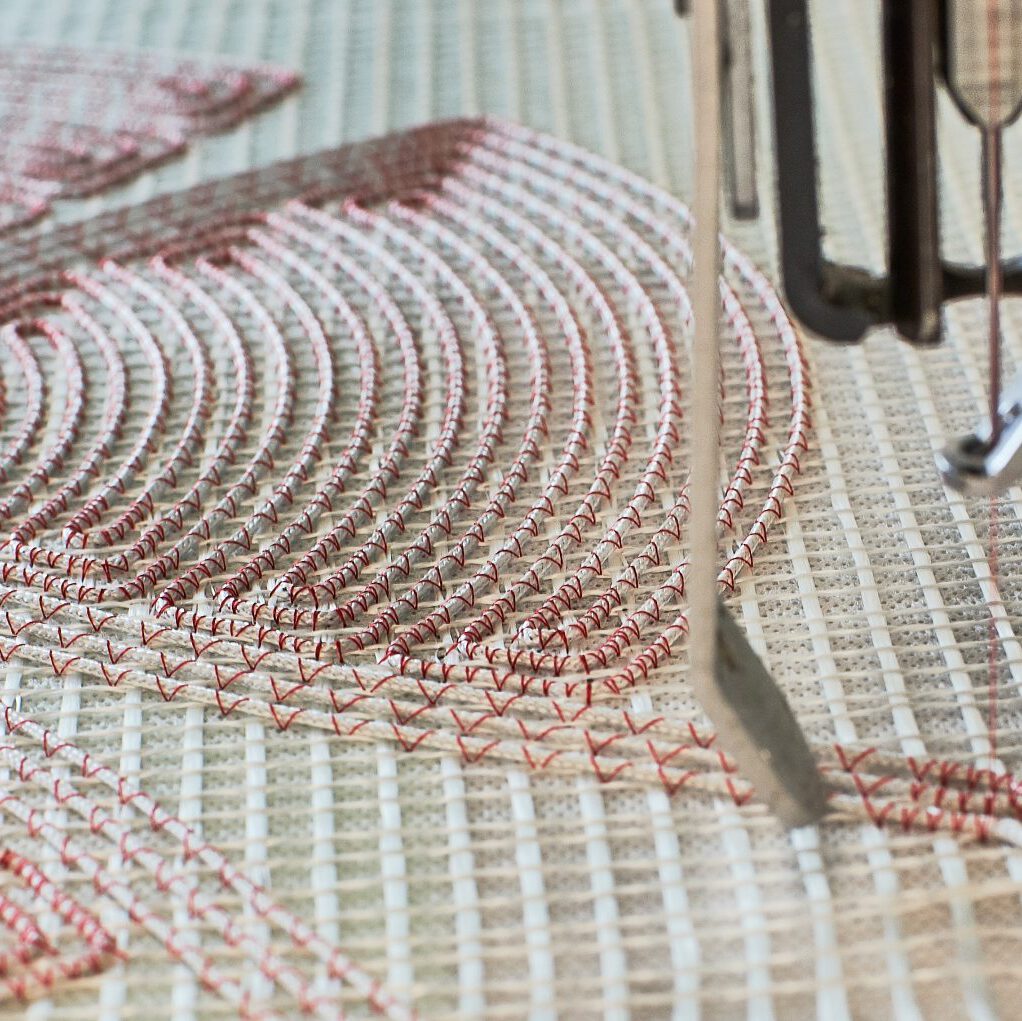
Welche Heizelemente sollen in den 3D-Druck integriert werden? „Wir haben mit Tailored Fiber Placement (TFP) von Carbon-Rovings auf einem Glasfasertextil als Heizelemente unterschiedliche Heizzonen in einer CFK-Form für ein Hubschrauber-Rotorblatt realisiert“, erklärt Consul. „Dies war für ein Clean Sky 1-Projekt, das wir in Zusammenarbeit mit QPoint Composite (Dresden, Deutschland) abgeschlossen haben. Wir werden mit einem ähnlichen Konzept an der COMBO3D-Form arbeiten.“
Die gesamte Entwicklung des gedruckten Werkzeugs wird durch Simulation unterstützt. Durch die Implementierung des Heiz- und Kühlsystems in eine thermische Simulation wird das Werkzeugdesign optimiert. Außerdem wird der Herstellungsprozess simuliert, der den Druckprozess unterstützt, indem Wissen über die Temperaturverteilung während des Drucks generiert und mit der Bahnplanung korreliert wird.
CEAD-Maschineninstallation und Projektfortschritt
„Das CEAD-System wurde sehr schnell geliefert – von der Bestellung bis zur Installation vergingen nur 6 Monate“, sagt Consul. „Zu diesem Zeitpunkt hatten wir die Materialprüfung abgeschlossen, die Plattenwerkzeuge entworfen und mit dem Drucken kleiner Teile begonnen. Wir befürchteten, dass es lange dauern würde, bis der Prozess mit dem CEAD AM Flexbot gut läuft, aber bei den ersten Versuchen hat es gut funktioniert.“
Plattenwerkzeug? „Es ist ein kleines Werkzeug, in das bereits Kühlkanäle und Heizelemente integriert sind, um CFK-Platten für Coupon-Tests herzustellen“, erklärt er. „Dieser Test sollte sicherstellen, dass die Qualität unserer 3D-gedruckten CFK-RTM-Form mit der aktuellen CFK-Form vergleichbar ist, die Saab im Autoklavenprozess herstellt.“
Leider wurde das Projekt durch COVID-19 unterbrochen, "aber jetzt läuft alles gut und wir holen auf", sagt Konsul. Und wie sieht es mit der Verwendung von PAEK für die 3D-gedruckte Form aus? „Das einzige Problem ist derzeit, dass die Tg [Glasübergangstemperatur] für PAEK 130-140 °C beträgt, was niedriger ist als die 180 °C-Härtung für das Demonstrationsteil“, bemerkt Consul. „Wir müssen also noch sehen, wie viele Zyklen wir bei der Härtungstemperatur abschließen können, bevor Kriechen auftritt oder die Oberfläche beschädigt wird.“
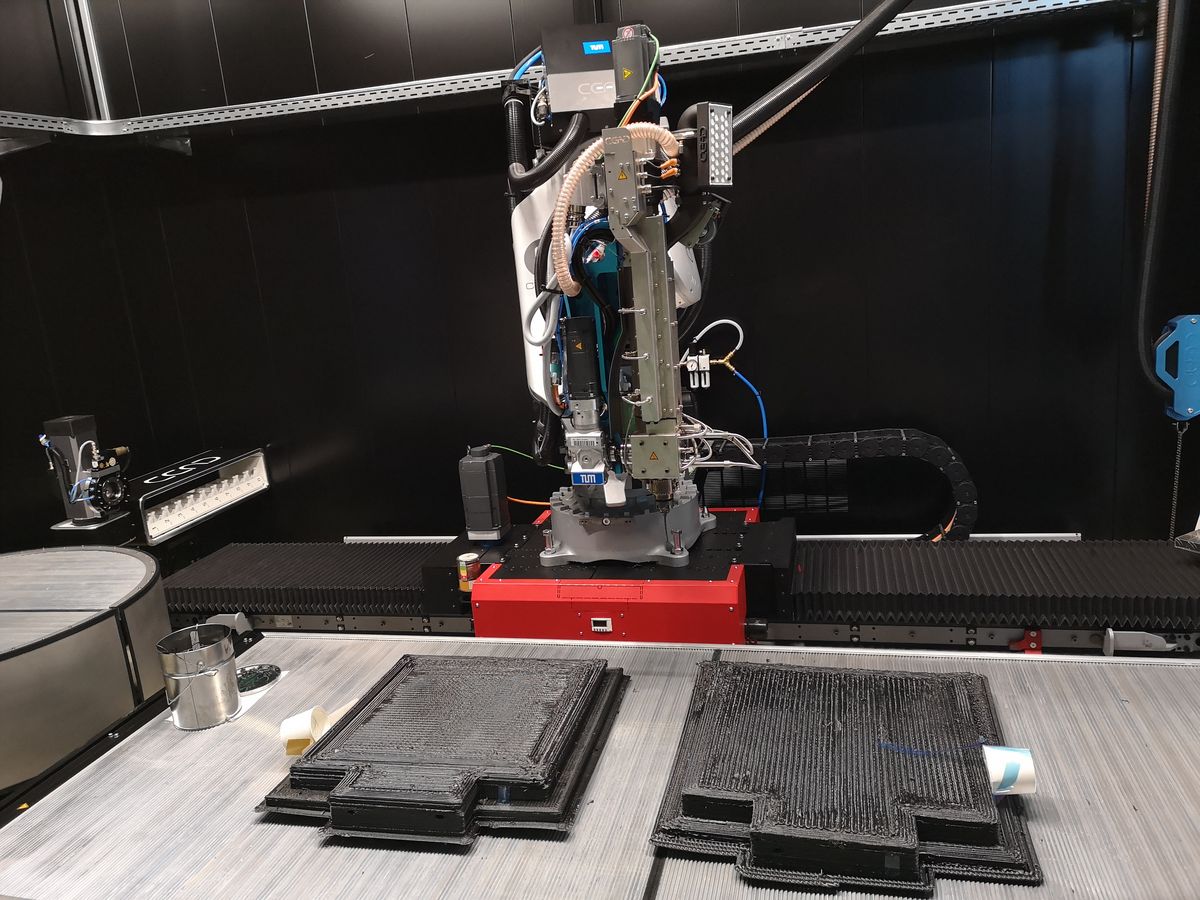
CEAD-Maschine in anderen Projekten?
„Wir bewerben uns für ein Projekt im Bereich Aerospace Tooling, das im nächsten Jahr bei GKN Aerospace Deutschland (München) mit der CEAD-Maschine und Polyethersulfon (PESU) startet“, sagt Consul. [Anmerkung:GKN in Deutschland fertigt Flügelklappen aus Verbundwerkstoff für die A330 und A350 sowie Querruder für die Business-Jet-Familie von Bombardier Global.] „CEAD wird hier für die Maschinenentwicklung für Endlos-Carbonfasern verantwortlich sein. Wir planen auch, die CEAD-Maschine intern zu verwenden, um Prototypformen für RTM herzustellen, die sonst an Subunternehmer vergeben worden wären. Dadurch können wir die Arbeit beschleunigen.“
Der Konsul stellt fest, dass PESU eine höhere Tg als PAEK hat. „Außerdem ist es amorph, nicht halbkristallin, daher sollte es einfacher zu drucken sein, obwohl die Kriechfestigkeit ein Problem sein könnte. Was wir versuchen, ist PEI (Polyetherimid) zu vermeiden. In der Vergangenheit haben wir uns mit dem Thema PEI-Verklebung auf Epoxidharz beschäftigt. RTM6 [Epoxid für RTM] löst PEI auf, was eine gute Haftung zwischen den beiden bewirkt. Das ist genau das, was Sie bei 3D-gedruckten Formen nicht wollen, die die Teile lösen und nicht daran kleben müssen.“
Zukünftige industrielle (und fliegende) 3D-gedruckte Verbundwerkstoffe
Bei der Diskussion einiger anderer Projekte, die LCC in der additiven Fertigung verfolgt, frage ich Consul, was CFK in Exoskeletten zurückgehalten hat. „Weil Exoskelette an jeden Träger angepasst werden müssen, sind die Teile spezialisiert, damit das Volumen nicht groß ist“, antwortet er. „Unser Projekt zielt darauf ab, die Produktion patientenspezifischer Exoskelettkomponenten der unteren Extremität zu ermöglichen, um die Produktion eines patientenspezifischen Exoskeletts in weniger als 24 Stunden zu ermöglichen. Diese Exoskelette werden die Rehabilitation von Schlaganfallpatienten basierend auf ihren biophysikalischen Profilen und ihren einzigartigen medizinischen Rehabilitationsbedürfnissen unterstützen.“ (Siehe den CW-Artikel „C-FREX-Exoskelett hängt von CFK ab …“)
„Die Leute haben das Konzept, dass 3D-Druck jedes Teil drucken kann, aber man muss zuerst Erfahrung mit 3D-Druck und mit Verbundwerkstoffen haben. Zum Beispiel gibt es oft Probleme mit der Adhäsion von Schicht zu Schicht und der Anisotropie, die verstanden werden müssen. 3D-gedruckte Verbundteile werden nicht das gleiche Design haben wie die derzeit aus Kunststoff und Metall hergestellten.“
Er weist darauf hin, dass es beim Einsatz von 3D-gedruckten Verbundwerkstoffen für die Produktion von Hochleistungs-Flugzeugteilen noch einige Probleme zu lösen gibt, zum Beispiel:Wie konstruiert man diese Teile für die additive Fertigung? Wie identifizieren Sie Teile, bei denen die additive Fertigung einen Mehrwert bietet? „Der Werkzeugbau in der Luft- und Raumfahrt ist das Hauptanwendungsgebiet, das unser Team derzeit untersucht“, sagt Consul. „Der 3D-Druck der Form passt gut. Diese Formen müssen den gleichen Härtungsbedingungen standhalten wie die Teile, aber es besteht ein geringeres Risiko im Zusammenhang mit Formen gegenüber fliegenden Teilen. Ein gutes Beispiel sind Rippensteifen für Flügel, bei denen es eine hohe Anzahl verschiedener Teile, aber nicht viele Zyklen pro Teil gibt. Dies ist also eine gute Möglichkeit, Erfahrungen mit der Technologie zu sammeln. Für fliegende Bauteile ist es noch zu früh. Wir streben dies langfristig an, aber Druckwerkzeuge werden es uns ermöglichen, den 3D-Druckprozess mit Hochleistungseigenschaften stabil genug zu gestalten und auch die Fähigkeit zu entwickeln, diese Teile und Prozesse in der Simulation genau vorherzusagen.“
Harz
- Warum 3D-Druck und Software für die digitale Transformation entscheidend sind
- 3D-Drucklösungen für Öl- und Gasunternehmen
- DSM und Nedcam entwickeln neue Anwendungen für den großformatigen 3D-Druck
- Acetal-Farb-Masterbatches für Automobile und mehr auf Basis emissionsarmer Träger
- Automatisierung für IML und Stapelformen
- Victrex- und Bond-Partner für den 3D-Druck von PAEK-Teilen
- Tipps für 3D-Druckformen
- Tipps für die CNC-Bearbeitung von Titan:Luft- und Raumfahrt und mehr
- Formlabs, um den 3D-Druck für KMU zugänglicher zu machen
- SIGRABOND® Chemical CFK für Komponenten und Baugruppen