Composites-intensives Meisterwerk:2020 Corvette, Teil 2
Anfang des Jahres die erste Ausgabe der Chevrolet Corvette . der achten Generation Sportwagen (C8s) von General Motors Co. (GM, Detroit, Michigan, USA) rollten vom GM-Montageband in Bowling Green, Ky., USA. Beschrieben als „schnellster, leistungsstärkster Eintrag Corvette ” in der 67-jährigen Geschichte des Modells ist es auch die verbundstoffintensivste Corvette , und der erste mit einer Mittelmotorkonfiguration. Die 2020 Corvette Stingray . ist nicht nur schön und schnell, aber mit einer Vielzahl von Luxusfunktionen ausgestattet. Lassen Sie sich jedoch nicht vom guten Aussehen und den schnellen Rennzeiten täuschen:Dieses Auto bietet viele Innovationen bei Verbundwerkstoffen. CW Die zweiteilige Berichterstattung von Composites in diesem Fahrzeug begann in der Ausgabe Juli 2020. Dies ist Teil 2.
Körperstruktur:Teil B
Die neue Corvette verfügt nicht über einen, sondern über zwei Kofferräume, die zusammen 12,6 Kubikfuß/0,36 Kubikmeter Fracht fassen. Beide Stämme werden aus 42 Gew.-% gehacktem Glasfaser/Vinylester-ungesättigtem Polyester (VE-UP)-Harz hergestellt, verwenden jedoch unterschiedliche Verfahren, die von Geometrie und mechanischen Anforderungen abhängig sind. Der vordere Kofferraum (frunk ) besteht aus einer „float“-Sheet-Moulding-Masse (SMC) mit einer spezifischen Dichte von 0,95, während der hintere Kofferraum durch das proprietäre PRiME-Verfahren (Prepositioned Reinforcement Warranty Manufacturing Excellence) geformt wird, eine Liquid Compression Moulding (LCM)-Variante. Das Float-SMC- und das PRiME-Verfahren wurden vom Verarbeiter Molded Fiber Glass Co. (MFG, Ashtabula, Ohio, USA) entwickelt. MFG produzierte alle strukturellen SMC- und LCM-Teile am Auto.
„Obwohl beide Räume durch flache, langgezogene Wände gekennzeichnet sind, ist der frunk ist kleiner als der hintere Kofferraum und könnte formgepresst werden“, erklärt Chris Basela, Corvette Leitender Ingenieur der Karosseriestruktur. „Der hintere Kofferraum benötigte eine höhere mechanische Leistung und war eine schwierige Geometrie, die mit einer SMC-Ladung gefüllt werden konnte. Da wir mit dem PRiME-Prozess die Faserlänge ändern können, könnten wir längere vorpositionierte Verstärkungen in unserem Vorformling verwenden. Das Fließen des Harzes [nicht des Glases] erwies sich als der beste Ansatz.“
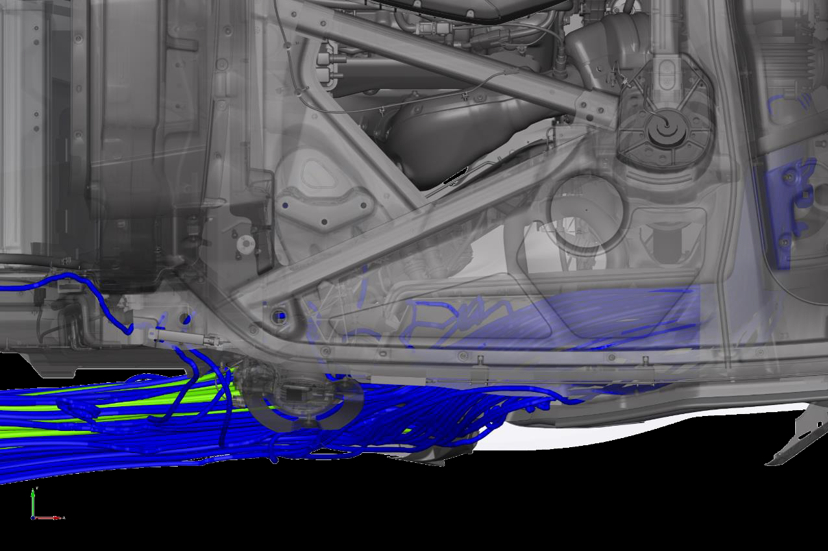
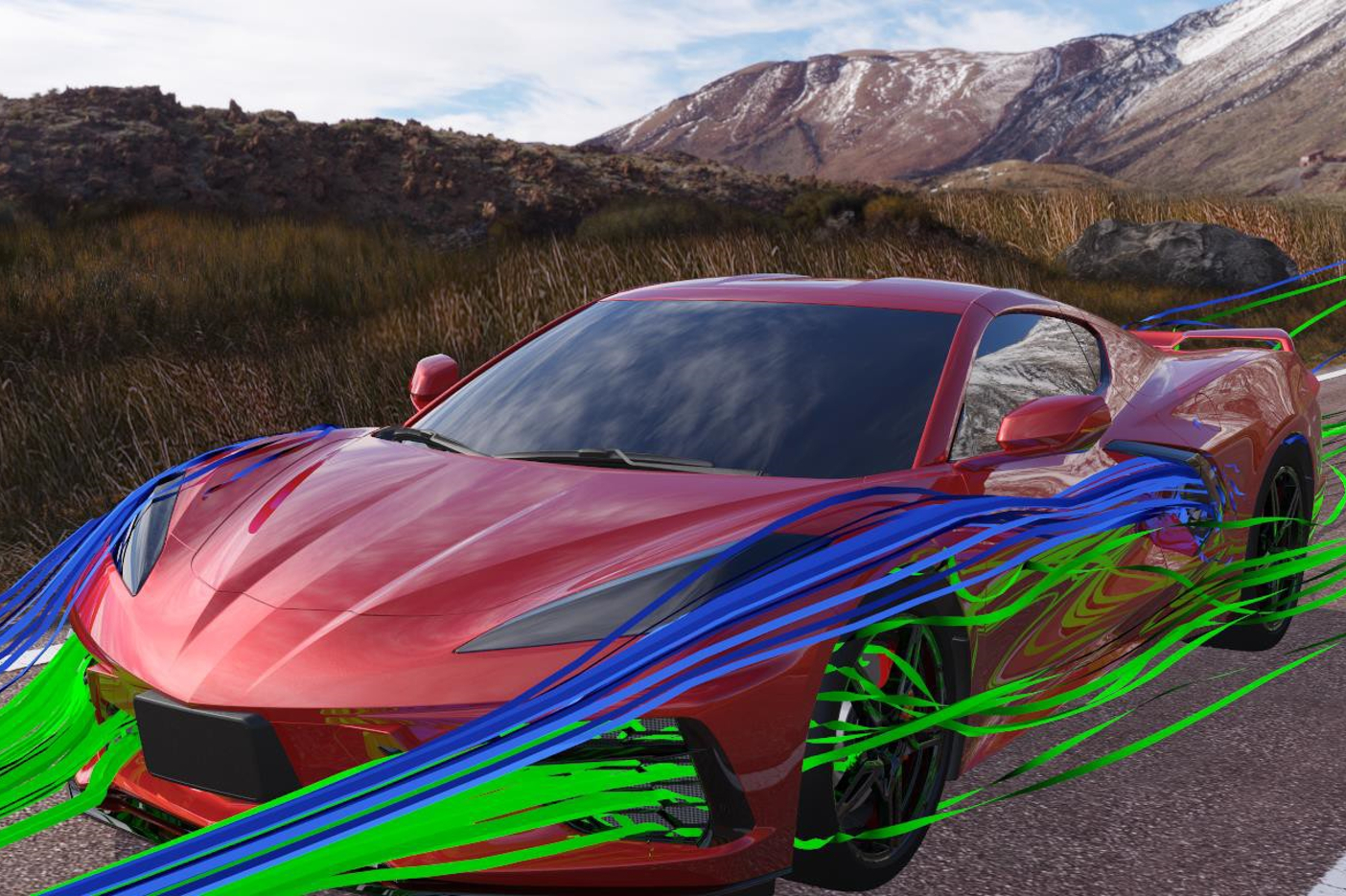
Clevere Technik und ein neues Material waren der Schlüssel zur Kühlung des Motors des C8. Mehrere primäre Kühlpfade (hintere Einlässe hinter jeder Tür, vordere Radkastenentlüftungen und äußere Kühleinlässe) führen hochkomplexe Ansaugkanäle, die Luft durch das Fahrzeug und durch den Motor leiten, bevor sie durch Aluminiumgitter-Entlüftungsöffnungen und SMC-Applikationen auf beiden Seiten des die Glastrennwand, die die Corvette präsentiert Motor. Die Applikationen werden mit MFGs Float (0,95-SG) SMC (Chacked Glass/UP-VE Resin) hergestellt. Das Material ist arm an flüchtigen organischen Verbindungen (VOCs), reduziert Emissionen und macht Resonatoren an hinteren Induktionskanälen überflüssig, während Kosten und Masse (2,4 Kilogramm) im Vergleich zu alternativen Technologien reduziert werden.
Der massive, für den Kunden sichtbare Heckrahmen — 64 x 69 x 24 Zoll (163 x 175 x 61 Zentimeter) — das die hintere Hälfte des Fahrgastraums umgibt, ist formgepresst aus gehärtetem 1,2-SG SMC. Dieses hybridverstärkte Material besteht aus Kohlefasern mit 15 % Faservolumenanteil (FVF) und Glasfasern mit 30 % FVF, mit einem VOC-armen UP-Harz, das so formuliert ist, dass es der Hitze im Motorraum standhält. Der Rahmen bildet die maßliche Grundlage für alle hinteren Außen- und Innenverkleidungen, ermöglicht jedoch durch seine flexible Gestaltung den Einsatz für mehrere Modellvarianten. Dank der erheblichen Teilekonsolidierung wurden sekundäre Anbauteile eliminiert, was den Innenraum vergrößert, Geräusche/Vibrationen/Härte (NVH) reduziert, eine bessere Karosseriestruktur und Dichtungsleistung bietet, die Sicht auf die Heckklappe verbessert und Masse (15 %) und Kosten gegenüber dem ausgehender Rahmen. „Angesichts der Größe dieses Teils, das fast 2 mal 6 Fuß hoch und 2 Fuß tief ist, mussten wir das Material in der Form tatsächlich bergauf fließen lassen, also waren wir alle bei diesem ersten Schuss ein wenig besorgt“, erinnert sich Basela.

Ebenso interessant ist die Trennwand (Mittelfensterrahmen), die von MFG speziell entwickelt wurde, um hohe Hitze- und Lärmherausforderungen zu lösen, da dieser Teil der Kabine direkt über dem V8-Motor sitzt. Glasfaserverstärkung in Kombination mit Beryllium-Graphit-Füllstoff in VE-UP-Harz mit niedrigem VOC-Gehalt dämpft die Schallübertragung in den Fahrgastraum so effektiv, dass sekundäre Gegenmaßnahmen zur Schalldämmung überflüssig sind. Das wiederum senkte die Kosten, vergrößerte den Innenraum und den Fahrgastkomfort sowie verbesserte Karosserieabdichtung und NVH. „Mit einem spezifischen Gewicht von 2,2 ist dies das erste Verbundteil, das ich jemals gebeten habe, Masse hinzuzufügen, anstatt sie herauszunehmen “, lacht Basela.
Verschlüsse und Beschnitt
Karosserieaußenbleche sind alle verklebt (innen/außen), lackiert, gehärtetes 1,2-SG SMC (22-28% FVF-Glasfaser/UP-Harz, je nach Komponente) von Continental Structural Plastics (CSP), einem Unternehmen der Teijin-Gruppe (Auburn Hills, Michigan, USA). Durch das Anschrauben von Verbundverschlüssen erreicht GM das aggressive Styling, die Aerodynamik und die funktionale Kühlintegration des C8 mit kosteneffektivem Leichtbau bei mehreren Modellvarianten unter Verwendung von Gleichteilen. Alle Karosserieteile werden mit dem innovativen Roboter-Nassschleifverfahren von Bowling Green inline auf einem „Skuk-System“ in Fahrzeugposition lackiert.
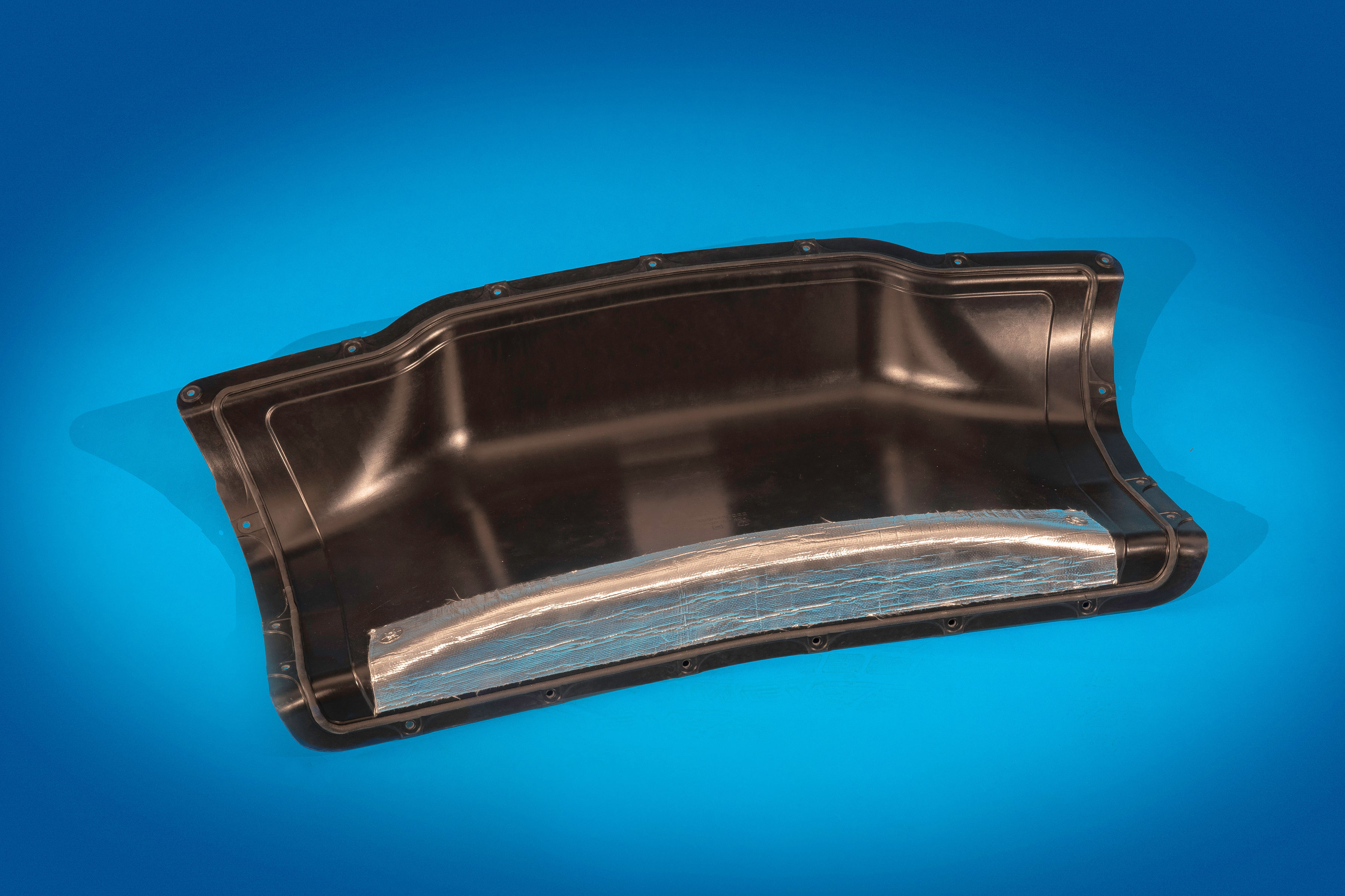
Eine weitere Innovation ist die Verwendung einer einteiligen, thixotropen Silikon-Elastomerschaumdichtung, die auf der Rückseite der SMC-Servicetüren angebracht wird, die sich im hinteren Kofferraum (eine bei Coupés, zwei bei Cabrios) befinden und dem Kunden den Zugang zur Luft ermöglichen. Filtersystem. Aufgrund der Nähe zum Motorraum wurde das Hochleistungs-Foam-in-Place-(FIP)-Elastomer (Silastic 3-8186 von Dow, Inc., Midland, Michigan, USA) für Dauergebrauchstemperaturen von bis zu 392 °C spezifiziert °F/200°C und bietet gleichzeitig eine dauerhafte Dichtung mit ausgezeichneter Druckverformungsbeständigkeit, selbst nach wiederholten Öffnungs-/Schließzyklen. GM berichtet, dass die meisten anderen gestanzten Schaumstoffe und Dichtungen entweder geschmolzen oder zerfallen wären, wenn sie solchen Temperaturen ständig ausgesetzt würden. Nach dem Auftragen wird die aufgebrachte Dichtung 10 Minuten lang bei 167 °F/75 °C wärmebehandelt, um den Schaum zu expandieren, wodurch Stanzkosten und Abfall vermieden werden. Die Türen selbst sind aus gehärtetem SMC (42% FVF-Glas in einer VE-UP-Matrix). Hitzeschilde, hergestellt von Gentex Corp. (Carbondale, Pennsylvania, USA) aus hitze- und abriebfesten aluminisierten Kevlar-Aramid-Geweben (Faser von DuPont de Nemours, Inc., Wilmington, Del., USA) verleihen Türinnenräumen zusätzliche Wärmeschutz.

GM hat beim C8 auch sein vollautomatisches Präzisions-Radwuchtsystem der zweiten Generation verwendet. Entwickelt mit The 3M Co. (St. Paul, Minn., USA) und ESYS Automation (Auburn Hills, Michigan, USA), ersetzten die hochverdichteten (5,8-SG) Verbundradgewichte mit maßgeschneiderten magnetischen Eigenschaften herkömmliche gestanzte Metallgewichte aus lackiertem Stahl, Zink oder Blei, die eine bestimmte Masse haben und von Hand auf die Räder aufgebracht werden müssen. Das neue System verwendet große Spulen extrudierten Klebebands mit selbstklebender Rückseite, die 67 Volumen-% postindustrielle, korrosionsbeständige, vollständig recycelbare Stahllegierung auf Fluorpolymerbasis enthalten. Das automatisierte System untersucht jedes Rad, schneidet und appliziert dann maßgefertigte Klebebandsegmente in kleineren, präziseren Schritten, um das Fahrverhalten zu verbessern und den Reifenverschleiß zu reduzieren. Es reduziert auch Montagezeit und -kosten, vereinfacht die Lagerhaltung, eliminiert Ausschuss und Arbeit und wird in mehr Farben als Metallgewichten angeboten.
Coupé-Dächer sind in drei Ausstattungsvarianten erhältlich:lackiertes, gehärtetes Low-Density-SMC (ab CSP); klares, hartbeschichtetes Polycarbonat (PC); und klarbeschichteter/exponiert gewebter Kohlefaserverbundstoff mit lackierten Kanten (von deBotech Inc., Mooresville, N.C.). CSP liefert auch mehrere gehärtete 1,2-SG-SMC-Platten der Klasse A für Cabrio-Modelle mit einziehbaren Dachsystemen.
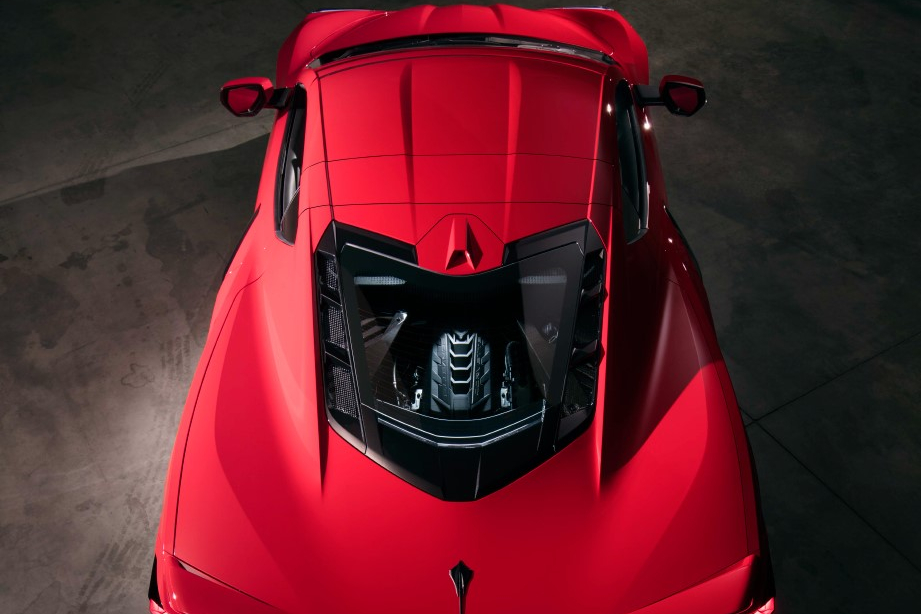
Andere Außenverkleidungen umfassen lackierte Frontschürze aus thermoplastischem Polyolefin (TPO) oben und unten, letztere mit integrierten Kanälen, um Luft zu den Bremsen (nur Z51-Paket) und den außenliegenden Wärmetauschern zu leiten. Kühlergrill und Lüftungsöffnungen der Bremsen sind aus lackiertem Acrylnitril-Butadien-Styrol (ABS).
Die obere Heckverkleidung ist aus TPO in Farbe (MIC) geformt, aber die untere Heckverkleidung ist Klasse A lackiert, 1,2-SG SMC (Glas/UP-Harz), aufgrund der Nähe des Teils zu heißen Auspuffblenden. Die hervorragende mechanische Leistung von SMC ermöglichte es GM, einen nicht unterstützten kurzen hinteren Überhang zu konstruieren und verwenden Sie größere Abstände zwischen den Anbauteilen, ohne durchzuhängen. SMC verteilt auch Lasten bei Heckcrashs mit niedriger Geschwindigkeit effizient über eine größere Fläche als Thermoplaste. Halterungen und Einparkhilfe-Sensoren hinten sind mit dem SMC verklebt. Dies soll das erste Mal sein, dass SMC-Stoßfängerverkleidungen bei Großserienfahrzeugen verwendet werden.
Heckklappenapplikationen mit lackiertem PC/ABS für die obere Verkleidung, SMC mit Aluminiumgitter für die seitlichen Lüftungsöffnungen und eine untere SMC-Applikation zur Aufnahme der thermischen Belastung direkt über dem Motor. Diese SMC-Platten werden von LyondellBasells Quantum Composites Inc. (Bay City, Michigan, USA) hergestellt. Die Türgriffentriegelungsschalter sind aus PC/ABS, während die hintere Lufteinlassöffnung aus SMC besteht. Das Basisfahrzeug ist mit einem blasgeformten, lackierten ABS-Spoiler ausgestattet und das hintere Luftauslassgitter ist aus spritzgegossenem lackiertem ABS. A-Säulen- und Kopfleistenapplikationen sind in ABS lackiert, ebenso wie Außenspiegelkappen und Kühlereinlassgitter. Je nach Optionspaket ein gehärteter SMC-Frontunterflügel und entweder ein Frontsplitter/Diffusor aus blasgeformtem TPO oder Kohlefaser-Verbundstoff – klar beschichtetes/sichtbares Carbon/Epoxid, hergestellt von deBotech unter Verwendung von Prepreg von Solvay Composite Materials (Alpharetta, Georgia, US) — tragen zu zusätzlicher aerodynamischer Stabilität bei. Ein Heckdiffusor aus gehärtetem SMC passt zur unteren SMC-Heckschürze in Klasse A lackiertem SMC von MFG.
Das Premium-Kohlefaser-Ausstattungspaket verfügt über verschiedene klar beschichtete/sichtbare Kohlefaser-Akzente innen und außen, darunter Spiegelkappen, Frontgrilleinsatz, Frontsplitter, Zubehörflügel, Motorraumabdeckungen, Innentürschalterplatten, Schwellerleisten, Instrumenten- Panel-Cluster-Lünette, Türgriffabdeckungen, Viertelapplikationen und Ride-Control-Platte. Diese Komponenten werden von deBotech, SMI Composites LLC (Comer, Georgia, USA) und Plasan Carbon Composites (Wixom, Michigan, USA) hergestellt.
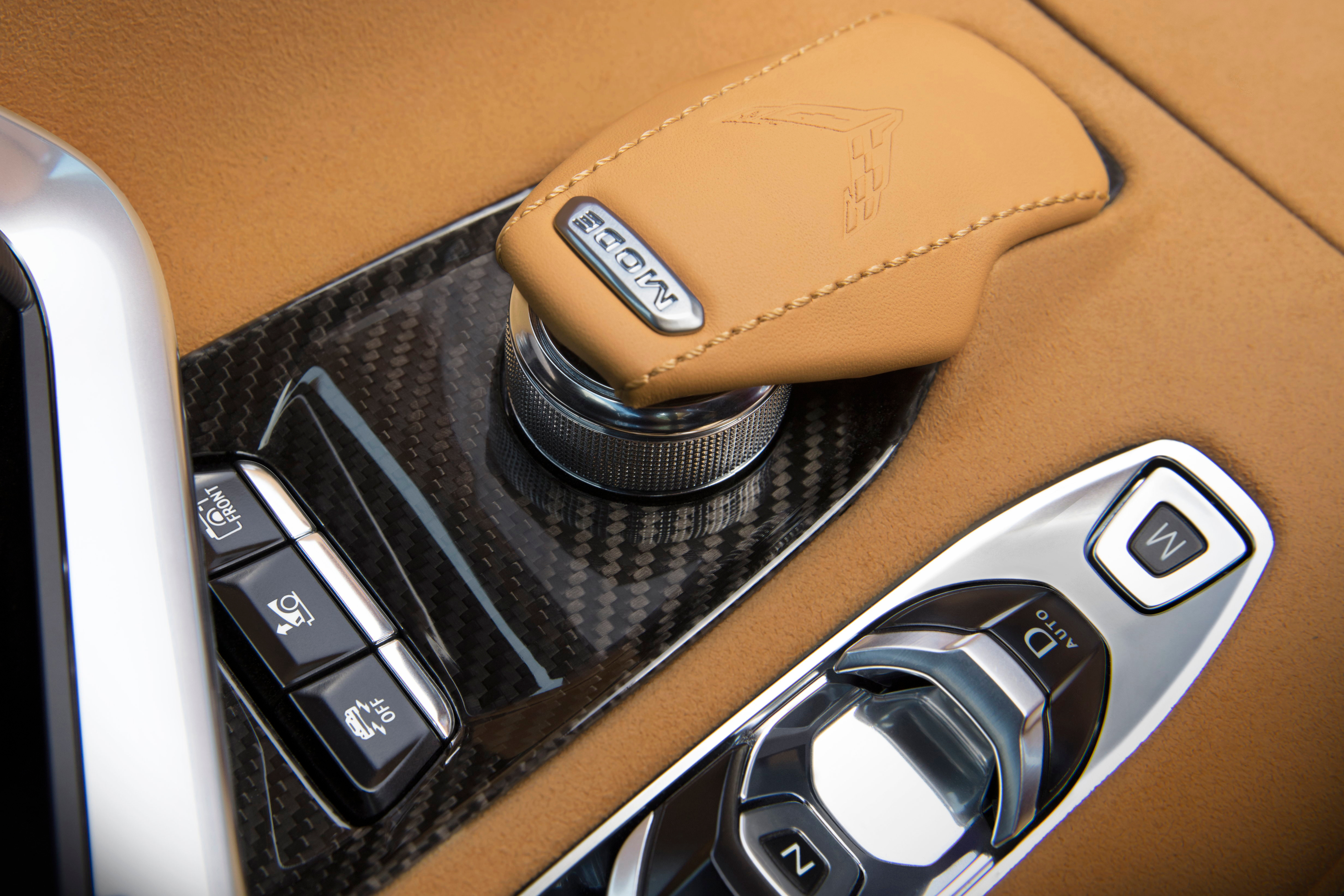
Fortschrittliche Technologie
Die 2020 Korvette hat bereits viele renommierte Branchenauszeichnungen gewonnen, darunter den 2020 MotorTrend Car of the Year, den 2020 Automotive News PACE (Premier Automotive Supplier Contributions to Excellence) Partnership Award und mehrere Auszeichnungen der Society of Plastics Engineers (SPE), darunter den 2019 Vehicle Engineering Team Award . „Obwohl die neuen Stingrays Die Mittelmotor-Architektur dominiert seit acht Generationen die Schlagzeilen, egal wo sich der Motor befindet – vor oder hinter dem Fahrer – Corvettes haben immer den neuesten Stand der Automobilwerkstofftechnologie vorangebracht“, fügt Tadge Jüchter, Executive Chief Engineer bei Global Corvette, hinzu. „Der technologische Fortschritt steht im Mittelpunkt unserer Arbeit.“
Harz
- 10 Vorteile von Cloud Computing im Jahr 2020
- Die Zukunft des 3D-Drucks:12 wichtige Erkenntnisse der AMFG-Digitalkonferenz AM Landscape 2020 (Teil 1)
- Instandhaltungsleitung, Teil 3
- Einführung in Harmonische:Teil 1
- Nachhaltigkeit in der Fertigung – Teil 3
- 2020 Trends und Herausforderungen, die von Covid-19 beeinflusst werden:Teil I
- Drehen ist optional
- Was ist eine Teilenummer?
- Kleinteilbearbeitung
- Zylindrizität in GD&T