Die Industrialisierung von thermoplastischem Epoxid
Cecence (Salisbury, Großbritannien) wurde 2014 von drei Gründern mit jahrzehntelanger Erfahrung in Verbundwerkstoffen gegründet. Direktor Mike Orange hatte eine lange Erfahrung in der Takelage und Masten für Yachten aus kohlenstofffaserverstärktem Polymer (CFK). Head of Innovation Humphrey Bunyan war zuvor Head of Innovation bei Future Fibers (Valencia, Spanien). „Sie [Future Fibres] stellten Komplett-Komposit-Rigging für den America’s Cup und andere Rennschiffe her, sowie CFK-Tether, um die Räder von Formel-1-Autos zu halten“, sagt Orange (siehe „Yachtbuilding Composites:Rigged for success“). „Wir haben die Vorteile des Leichtbaus verstanden, haben uns aber mit anderen Sektoren beschäftigt, die unsere Erfahrung nicht hatten und mit den Kosten zu kämpfen hatten, die Produktion hochgefahren und die Brandschutzbestimmungen erfüllt.“
So wurde Cecence (ausgesprochen „see-sense, wie im gesunden Menschenverstand bei Kohlefaserverbundwerkstoffen“) gegründet, um sich auf Feuerbeständigkeit, industrialisierte Fertigung und Nachhaltigkeit zu konzentrieren. Dies führte zu Entwicklungen wie einer gepressten Sitzlehne aus Kohlefaser/Bioharz-Verbundstoff für Passagierflugzeuge mit einem Gewicht von nur 7,5 Kilogramm, einer reduzierten Sitzdicke auf weniger als 20 Millimeter und einem vergrößerten Passagierraum und Komfort, während alle Feuer-, Rauch- und Toxizitätsanforderungen (FST) erfüllt werden.
„In einem früheren Projekt hatte Cecence eine Heißpress-Herstellungsmethode entwickelt, die die Zykluszeit von 2,5 Stunden auf 7 Minuten für eine Economy-Class-Rückenlehne unter Verwendung von Snap-Cure-Phenolverbindungen verkürzte. mit UK Prepregger FTI (Somerset) entwickelt“, sagt Orange. Für diese neueste oben beschriebene Rückenlehne, die mit Design Q (Redditch, Großbritannien) entwickelt wurde, erweiterte Cecence sein FST-Portfolio durch die Verwendung eines von SHD Composites (Sleaford, Großbritannien) entwickelten Polyfurylalkohol-(PFA)-Harz-Prepregs. PFA ist ein aus Biomasse gewonnenes duroplastisches Polymer, das sich wie ein Phenol mit hervorragender Oberflächenverarbeitung und Nachhaltigkeit verhält (siehe „Feuer ohne Gewicht standhalten“). „Wir haben mit SHD Composites zusammengearbeitet und deren Chemie für eine schnellere Aushärtung optimiert“, sagt Orange. „Das ist, was wir tun:Materialien, Prozesse und Designs zu nehmen und sie weiterzuentwickeln, damit Verbundprodukte in großem Maßstab wirtschaftlich und dennoch nachhaltig hergestellt werden können.“
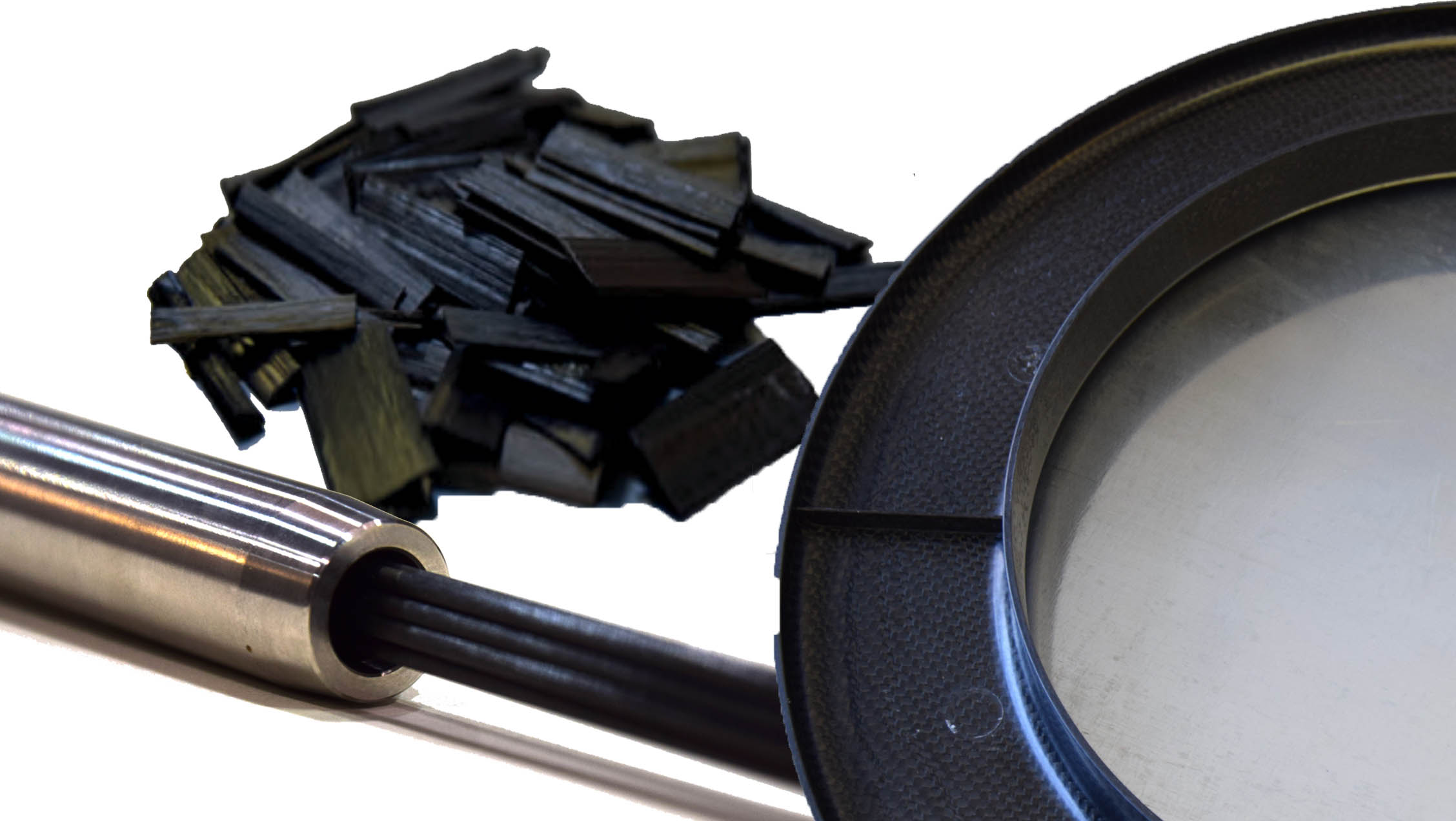
Fertigungsgeschwindigkeit und Nachhaltigkeit waren Schlüsselfaktoren, als Cecence vor einigen Jahren auf ein thermoplastisches Epoxidharzsystem stieß. „Dieser Thermoplast mit Epoxidkomponenten am Ende seiner Polymerketten wurde von einem Stoffhersteller verwendet, der sein Potenzial in Verbundwerkstoffen nicht erkannte“, erklärt Orange.
„Wir haben sofort die Vorteile eines dünnflüssigen Thermoplasts verstanden, der Fasern sehr gut imprägnieren und gleichzeitig ein thermoformbares Epoxid ermöglichen kann“, sagt Humphrey Bunyan. Cecence entwickelte ein auf dieser thermoplastischen Epoxidtechnologie basierendes Prepreg und anschließend eine Produktfamilie unter der Marke K_Series:aufwickelbare K_Rod, 0,25 bis 1,98 Millimeter dicke Semipreg K_Plate und K_Chip Molding Compound (Abb. 1). „Wir konnten Bauteile in weniger als drei Minuten pressen“, sagt Orange, „und haben eine FR-Variante demonstriert, die die FST-Anforderungen für den Flugzeuginnenraum erfüllt.“ Cecence hat das Material auch verwendet, um ein Verbund-Overheadline-Equipment-System (COHLE) für elektrische Bahnstrecken zu entwickeln, das die Anzahl der Stützmasten/-masten um die Hälfte reduziert und die Gesamtinstallations- und Betriebskosten um 100.000 £ (124.200 $) pro Kilometer reduziert.
Thermoformbares Epoxid
„Bei typischen Thermoplasten hat man ein hochviskoses Matrixpolymer, das sich nur schwer in die Fasern pressen lässt“, erklärt Bunyan. „Daher ist es schwierig, eine gute Imprägnierung der Kabel oder Stoffe zu erreichen. Aber das thermoformbare Epoxidharz der K_Serie hat eine sehr niedrige Viskosität – 80 Centipoise bei 100°C. Dies ermöglicht uns, Glas-, Carbon- und Naturfaserverstärkungen mit hervorragender Harz-Faser-Verteilung und typischerweise 60 Gew.-% Faseranteil vorzuimprägnieren. Wir können auch Fasern mit einer Schlichte für Epoxid verwenden, die normalerweise nicht mit Thermoplasten kompatibel ist.“ Und doch ist dieses System ein echter Thermoplast, der das Umformen fertiger Teile bei 180-200°C ohne chemische Reaktion oder Exothermie ermöglicht.
„Wie Epoxidharz haftet es gut an der Faser, sodass sich die Faser nicht von der Matrix ablöst, selbst wenn Sie beim Formen höhere Drücke anwenden“, bemerkt Orange. Dies bezieht sich auf ein Problem, das er bei kurzfaserverstärkten Polyamiden (PA) und Polypropylen-Compounds beobachtet hat. „Wir arbeiteten mit einer PA-Schicht, die durch Heißpressen auf ein Gewebe aufgeschmolzen wurde, um eine flache Platte herzustellen. Die Matrix klebte nicht an den Fasern, sondern umgab sie nur. Wenn es also in ein Teil gepresst wurde, kam es zu einem Faserauszug.“
K_Plate, das bei 150-220 °C verarbeitet wird, bietet eine Betriebstemperatur von 100 °C für kurze Einwirkungen und eine kontinuierliche Nutzung bei 90 °C. Gehackte unidirektionale Kabel K_Chip Compounds werden bei 240°C gepresst. „Der Tg [Glasübergangstemperatur] und Beginn der Wärmeverformung sind bei der K_Serie niedriger als bei typischen Epoxiden, aber dies macht auch das Umformen und Recycling möglich“, sagt Orange. Auch die Prozesse der K_Series sind schnell. „Cecence hat auf der JEC 2016 mit RocTool [Le Bourget du Lac, Frankreich] zusammengearbeitet, um den sich am schnellsten formenden Thermoplast zu demonstrieren, den sie je gesehen haben“, sagt er und nennt eine Zykluszeit von 2 Minuten und 40 Sekunden für eine Automobilhaube. „Die Verweilzeit betrug nur 25 Sekunden bis zum Abkühlen bei 8-9 bar Druck über der Vakuummembran. Sie waren auch mit dem Finish sowohl der matten als auch der glänzenden Oberflächen zufrieden [siehe Eröffnungsbild] und stellten fest, dass unser Material das beste Finish von allen getesteten Oberflächen bot.“
Außerdem machen die Epoxidkomponenten in den Produkten der K_Series das Lackieren und Verkleben von Verbundteilen einfach, ohne die speziellen Grundierungen und Vorbereitungen, die für herkömmliche Thermoplaste erforderlich sind. „Sie können sie mit Standardklebstoffen sekundär verkleben“, fügt Bunyan hinzu. „Außerdem erhält man gute interlaminare Schereigenschaften und insgesamt ergeben diese dank des Thermoplasts zähe, energieabsorbierende Strukturen.“
CFK-Oberleitung für kostengünstigere elektrische Bahnen
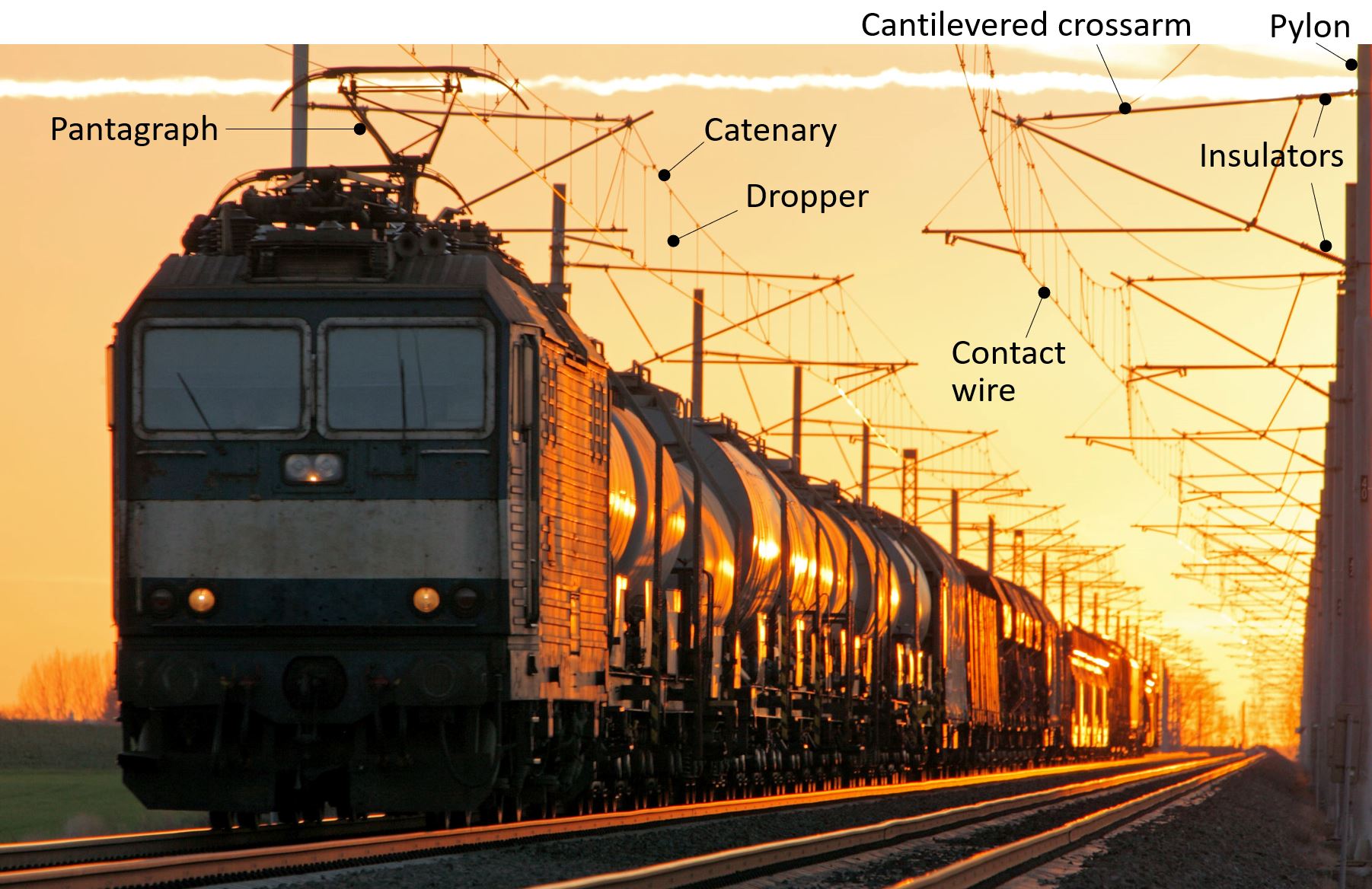
Die duale Natur dieses thermoplastischen Epoxids wird in einem von Cecence entwickelten Overhead Line Equipment (OHLE)-System unter Verwendung einer CFK-Oberleitung aus K_Rod veranschaulicht. Die Fahrleitung und der stromführende Fahrdraht sind die beiden Hauptdrähte im OHLE einer Elektrobahn (Abb. 2). Der Strom wird der Lokomotive eines Zuges durch einen Stromabnehmer zugeführt, der sich von der Oberseite der Lokomotive erstreckt, um gegen den Fahrdraht zu drücken. „Die Oberleitung wirkt wie eine Hängebrücke zwischen Pylonen (Masten, Masten), die alle 25 Meter entlang der Gleise angeordnet sind“, erklärt Orange. Der Kupferfahrdraht wird an der Oberleitung durch vertikale Falldrähte oder Fallrohre aufgehängt, ähnlich wie die Fahrbahn von Seilen in einer Hängebrücke getragen wird.
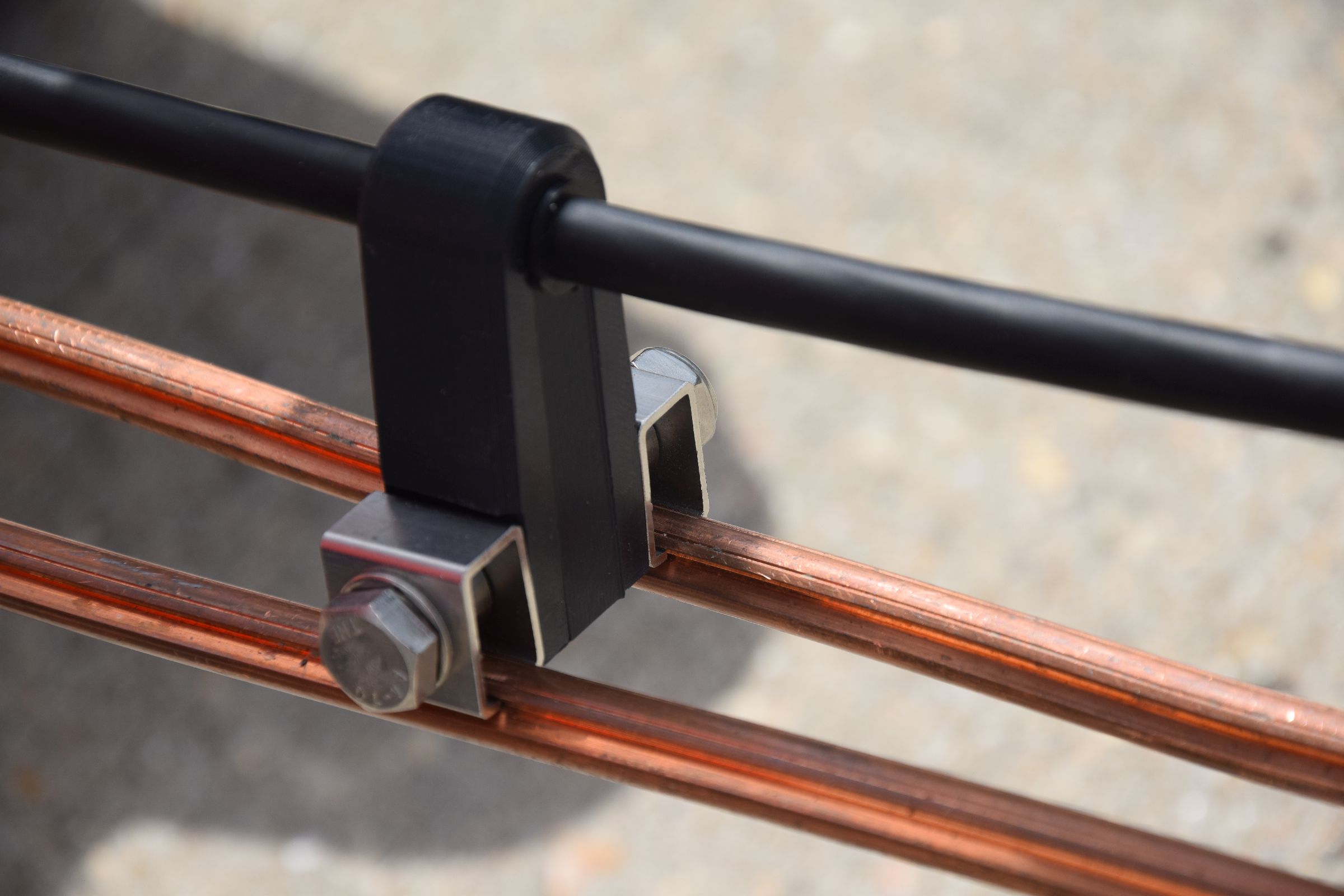
„Durch die Verwendung eines K_Rod-Zugseils als Oberleitung kann es nur 70 Millimeter über dem Kupferfahrdraht sitzen“, betont Orange (Abb. 3). „Das gesamte System ist kompakter und hat eine viel geringere visuelle Auswirkung auf die Umwelt.“ Aktuelle OHLE-Systeme verwenden Stahlfahrdrahtseile, deren Länge sich mit Temperaturänderung ändert. „Im Sommer verlängern sie sich um bis zu 400 Millimeter pro Kilometer“, stellt er fest. Um diesem Durchhängen der Leitungen entgegenzuwirken, werden Betongegengewichte an Umlenkrollen als selbstspannendes System installiert, erhöhen jedoch die Gesamtkosten.
„Das Gewicht der Stahlleine und ihr Durchhangprofil sind auch der Grund, warum so viele Stöcke benötigt werden“, bemerkt Orange. „Unser CFK-Kabel ändert im Sommer die Länge nur um 7 Millimeter pro Kilometer, weil die vernachlässigbare Wärmeausdehnung der Kohlefaser einen thermisch stabilen Verbund erzeugt. Außerdem ist es 80 Prozent leichter als Stahlseile, hängt nicht durch und ermöglicht einen Abstand von 50 Metern zwischen den Masten, was die Anzahl der erforderlichen Masten halbiert.“ Dies ermöglicht weitere Kosteneinsparungen, denn für jeden Pylon gibt es eine freitragende Traverse, die von einem Schrägseil getragen wird.
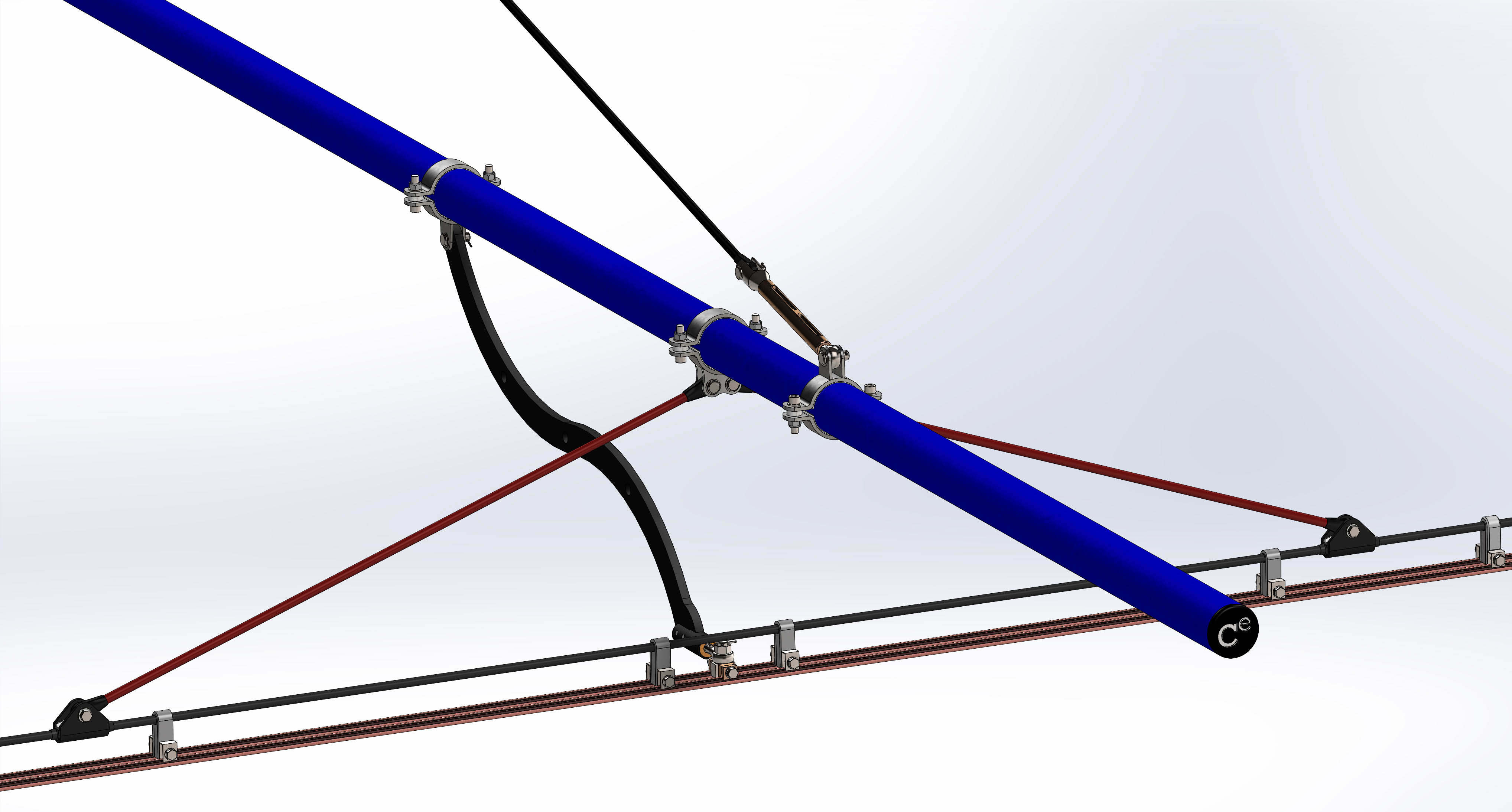
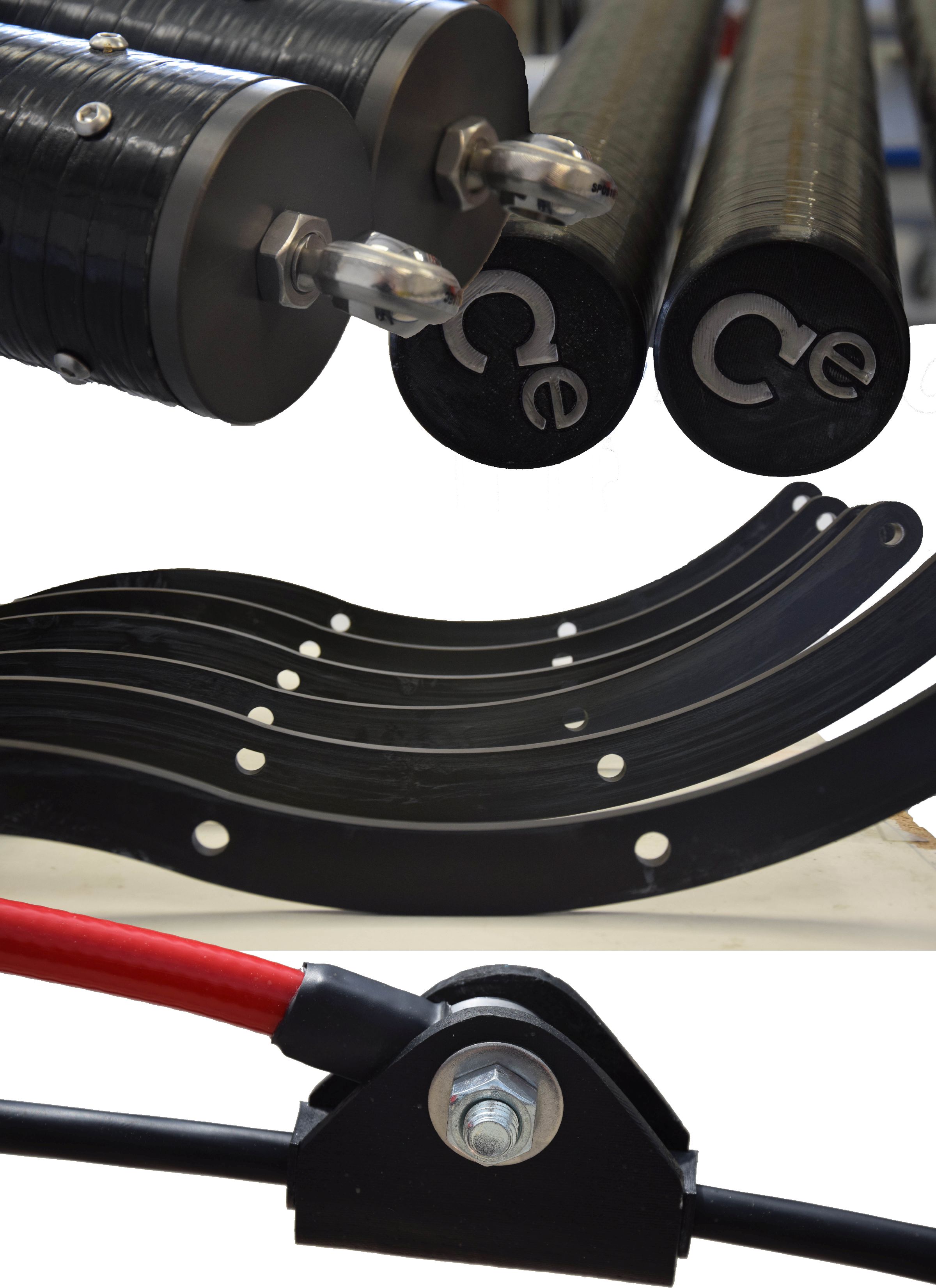
Darüber hinaus verwenden herkömmliche OHLE-Systeme Ganzmetallkomponenten, was das Hinzufügen von Isolatoren erfordert, um eine ungewollte Leitung des elektrischen Stroms zu verhindern. „Der Cecence COHLE benötigt nicht alle Isolatoren, da er nichtleitende Glasfaser(GF)-Verbundstangen und -Traversen mit nichtleitenden Verbundschrägseilen verwendet“, erklärt Orange. „Wir verwenden auch Zwischentropfer aus 3D-gedruckter Polymilchsäure (PLA). Im Gegensatz zu einem Metallsystem müssen die Masten nicht regelmäßig lackiert werden und die korrosionsbeständigen Verbundwerkstoffe erfordern weniger Wartung.“
„Das thermoplastische Epoxid spielt eine Schlüsselrolle in der CFK-Oberleitung“, fährt er fort. „Cecence verwendet es sowohl im Kohlefaser-K_Rod-Kern als auch im umsponnenen GF-Verbundmantel. Das Ergebnis ist ein leichtes, hochfestes, isoliertes Kabel, das aufrollbar ist und sich gut verkleben lässt, wenn es in eine Buchse geklebt wird, wodurch das normalerweise knifflige Anschlussproblem für Kohlefaser-Verbundkabel gelöst wird. Dank der erstaunlichen Lastübertragung vom Kern in die Muffe durch das Übergeflecht benötigen wir keine große Muffenlänge und dieses System ist einfach, so dass es von Bahntechnikern im Feld praktisch installiert werden kann.“
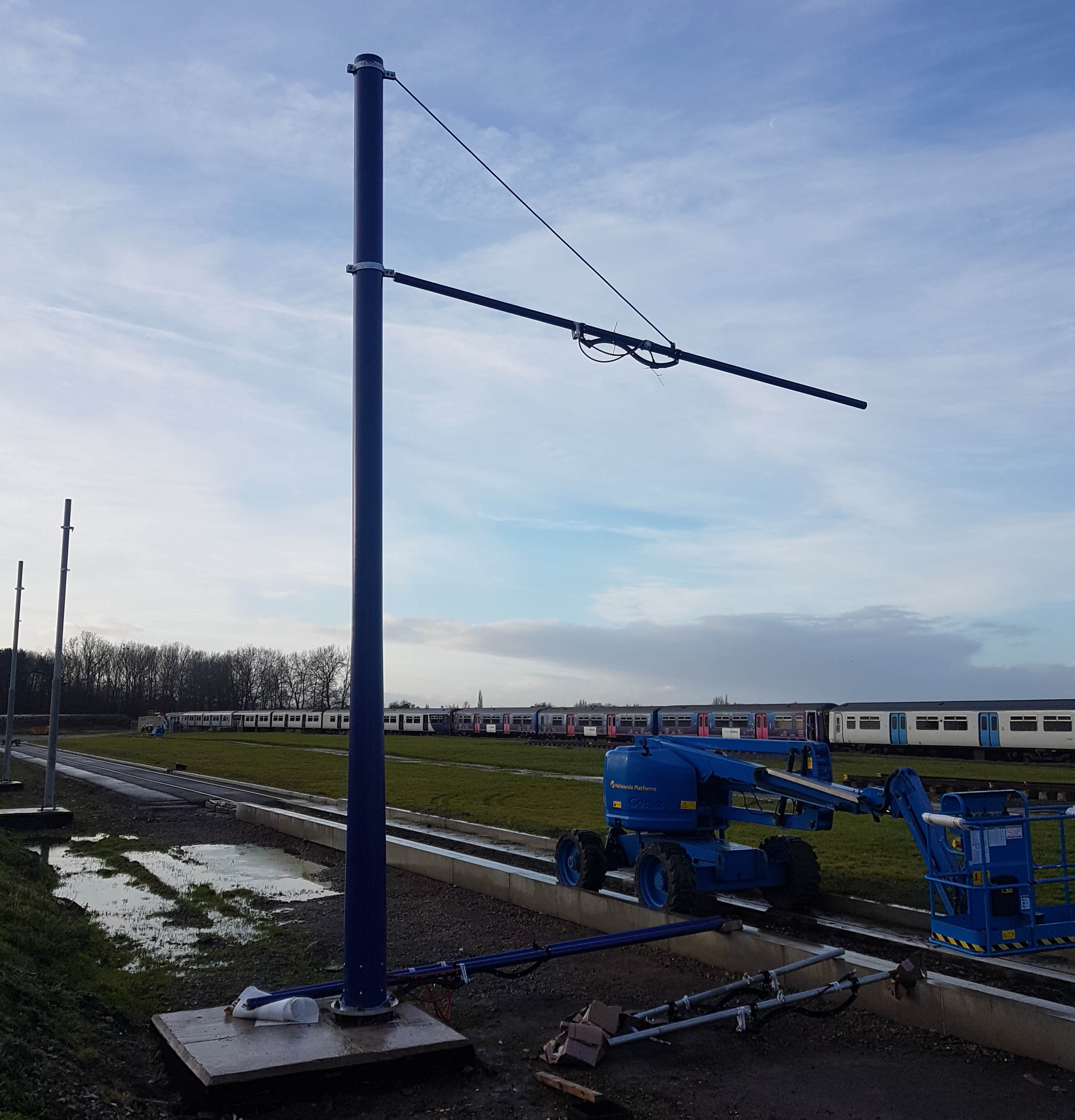
Obwohl das CFK-Kabel dreimal so viel kostet wie eine Stahlfahrleitung, sinken die Gesamtsystemkosten von 512.000 Pfund auf 413.000 Pfund pro Kilometer, sagt Orange. Diese Kosten, die mit dem multinationalen Ingenieur- und Infrastrukturunternehmen Atkins (London, Großbritannien) berechnet wurden, umfassen Betriebs-/Wartungseinsparungen von 400.000 bis 3,4 Millionen GBP pro Kilometer während der Systemlebensdauer.
„Cecence hat die Prototypkomponenten im Mai 2019 geliefert“, sagt Orange, „und unsere Entwicklungspartner hatten geplant, die Stromleitungen bis Februar 2020 zu verlegen, aber das verzögerte sich aufgrund von COVID-19. Das gesamte System wurde 2019 auf der Advanced Engineering Show gezeigt und gewann den Composites UK Innovation Award.“
Weitere Anwendungen und Entwicklung der K_Serie
Über die OHLE-Anwendung hinaus verfolgt Cecence weitere Möglichkeiten zur Anwendung seiner K_Series-Produkte. „Cecence hat auch an Projekten gearbeitet, bei denen die K_Rod-Kabel als Anker für eine steinerne Felswand in einem Bauprojekt in der Schweiz verwendet wurden“, sagt Orange. „Unsere Projektpartner sollten 80 Meter tiefe Löcher in den Fels bohren, die CFK-Kabel einlegen und dann mit Beton verfüllen. Es gab einige erstaunliche Testergebnisse, aber der akademische Partner hat sich nie mit der Industrie verbunden, um das Projekt über den Labormaßstab hinaus zu entwickeln . Wir verfolgen andere Demonstrationen, jedoch ist dieses System korrosionsbeständig und bietet eine gute Lastübertragung. Es könnte auch als Bodenanker für verschiedene Bausysteme verwendet werden, beispielsweise für hurrikansichere Gebäude.“
Videos auf YouTube und der Cecence-Website demonstrieren die Thermoformbarkeit der K_Plate-Produkte. „Es gab auch Gespräche mit einem britischen Luft- und Raumfahrtunternehmen, um Anwendungen für variable Geometrie/Morphing-Profile zu untersuchen“, sagt Orange. Cecence demonstrierte ein kosteneffektives Automobilmaterial unter Verwendung von K_Chip, das mit zerhackten Verbundkabeln als Hybridmaterial aus CF/GF/thermoplastischem Epoxid hergestellt wurde, das . beibehält ein 2:1 Verhältnis von Kohlenstoff zu Glas, bestätigt durch Tests. ."
Das Unternehmen hat auch eine Hochtemperatur-K_Serie mit einem Tg . entwickelt von 250-300°C, die bei 360-400°C verarbeitet werden. „Dies wurde für einen Automobilhersteller verwendet, der wollte, dass die CFK-Teile ihren 180 °C-E-Coat-Lackierungsprozess überstehen“, sagt Orange. „Wir haben auch das K-FR-Material, das die FST-Anforderungen für vertikale Verbrennung, Wärmefreisetzung und Rauchtoxizität von Flugzeugen erfüllen kann, und wir prüfen, wie wir die Vibrationsdämpfung zur Reduzierung des Flugzeugkabinenlärms unterstützen können. Wir können den Thermoplast abstimmen und elastomere Materialschichten hinzufügen, um eine signifikante Geräuschreduzierung zu erreichen.“
Samantha Bunyan, die dritte Cecence-Gründerin und Head of Industry Engagement, weist darauf hin, dass auch die Recyclingfähigkeit ein wichtiger Entwicklungsbereich ist. Cecence ist Teil des ReDisCover Composites-Konsortiums, das vom National Composites Center (Bristol, Großbritannien) betrieben wird. Es wurde im April 2019 gegründet und verfolgt 24 Projekte entlang der vier Ströme:Recycling, Demontage, Kreislaufmaterialien und Wiederverwendung. „Im Rahmen dieser Projekte beschäftigen wir uns mit der Demontage von Komponenten und dem Nachweis der echten Recyclingfähigkeit von thermoplastischen Verbundwerkstoffen“, sagt Bunyan. „Die Branche ist endlich gezwungen, beweisen die seit vielen Jahren behauptete Recyclingfähigkeit. Cecence sieht die Vorteile, thermoplastische Epoxidprodukte der K_Serie recyceln zu können, muss aber auch die Prozesse und die Wirtschaftlichkeit dafür demonstrieren.“
„Wir glauben, dass es im Massenverkehr viel mehr Platz für nachhaltige Verbundwerkstoffe gibt, einschließlich der Innenausstattung von Flugzeugen, Sitzen und Schienenanwendungen“, sagt Orange und fügt hinzu, dass Cecence nicht nur Partner in der Entwicklung, sondern auch in der Fertigung ist. „Wir haben bisher 2.500 Sitzlehnen aus Verbundwerkstoff für Flugzeuge des Typs A320 hergestellt und waren auf dem besten Weg, die leichtesten und dünnsten Sitzlehnen der Branche vor dem Ausbruch von COVID-19 herzustellen. Reste von Verbundsitzen können in Fußstützen und Armlehnen wiederverwendet werden. Rezyklat kann auch in anderen Hilfsteilen verwendet werden, die derzeit Neukunststoffe verwenden. All dies kann dazu beitragen, den Verbrauch und die Emissionen fossiler Brennstoffe zu senken, die Elektrifizierung zu erleichtern und die Nachhaltigkeit zu erhöhen.“
Bei Verbundwerkstoffen, so Samantha Bunyan, „besteht Nachhaltigkeit aus drei Aspekten:Materialien, Verarbeitung (schnell und energiesparend) und Lieferkette. Wir stören all dies und arbeiten mit Innovatoren aus der ganzen Welt zusammen, die nicht gesehen werden, weil die meisten Leute nur auf die großen Unternehmen schauen. Die Welt braucht neue Lösungen, die für die Industrie funktionieren. Das macht Cecence.“
Harz
- Verbundwerkstoffherstellung:Die Herstellung von Verbundwerkstoffen
- Covestro verstärkt Investitionen in thermoplastische Verbundwerkstoffe
- Die Geschichte des Epoxidharzes
- Thermoplastische Verbundwerkstoffe bei Oribi Composites:CW Trending, Episode 4
- Fehlerbehebung beim Thermoformen von thermoplastischen Verbundwerkstoffen
- Die Entwicklung additiver Verbundwerkstoffe
- Thermoplastische Verbundwerkstoffe:Strukturelle Stoßstangenhalterung
- Mar-Ball, Lattice Composites fusionieren zur Erweiterung der Epoxidfähigkeiten
- Thermoplastische Verbundwerkstoffe:Malerische Aussicht
- Schweißen von thermoplastischen Verbundwerkstoffen