Thermoplastische Verbundwerkstoffe:Auf dem Weg nach vorne
Thermoplastische Verbundwerkstoffe (TPC) sind in der Luft- und Raumfahrt nicht neu, aber in den letzten Jahren hat die Verwendung von Thermoplasten in Verkehrsflugzeugen einen Wendepunkt erreicht. Während TPCs schon seit einiger Zeit für kleinere Teile wie Clips und Halterungen oder kleinere Interieurkomponenten verwendet werden, haben Thermoplaste sukzessive ihren Weg in größere Flugzeugstrukturen gefunden und scheinen nun eine größere Rolle in der Zukunft von Verkehrsflugzeugen zu spielen.
Im März 2018 erwarb Toray Industries Inc. (Tokio, Japan), der weltweit größte Hersteller von Kohlefasern, TenCate Advanced Composites (Morgan Hill, Kalifornien, USA und Nijverdal, Niederlande) für 930 Millionen Euro (TenCate hat seitdem seinen Namen geändert in .) Toray Advanced Composites). Der Schritt schien ein Versuch zu sein, die thermoplastischen Fähigkeiten von Toray in Vorbereitung auf die nächste Welle der Entwicklung von Verkehrsflugzeugen zu stärken. Kurz nach dieser Ankündigung gaben Hexcel (Stamford, Connecticut, USA) und Arkema Inc. (König von Preußen, Pennsylvania, USA) eine strategische Allianz zur Entwicklung thermoplastischer Verbundwerkstofflösungen für die Luft- und Raumfahrt bekannt (PEKK) Harzkompetenz. Und im Laufe des Jahres schienen sich mehrere andere Teile des Thermoplast-Puzzles zu fügen.
Im April 2018 stellte die Premium Aerotec GmbH (Augsburg, Deutschland) einen Demonstrator für ein von ihr entwickeltes und gefertigtes A320-Druckschott von Airbus (Toulouse, Frankreich) aus Kohlefaser in einer thermoplastischen Matrix vor. Der aus acht geschweißten Segmenten bestehende Demonstrator veranschaulicht, wie die Schweißbarkeit von Thermoplasten das Potenzial hat, größere Flugzeugkomponenten zu ermöglichen. (Erfahren Sie mehr über den A320-Druckschott-Demonstrator von Premium Aerotec).
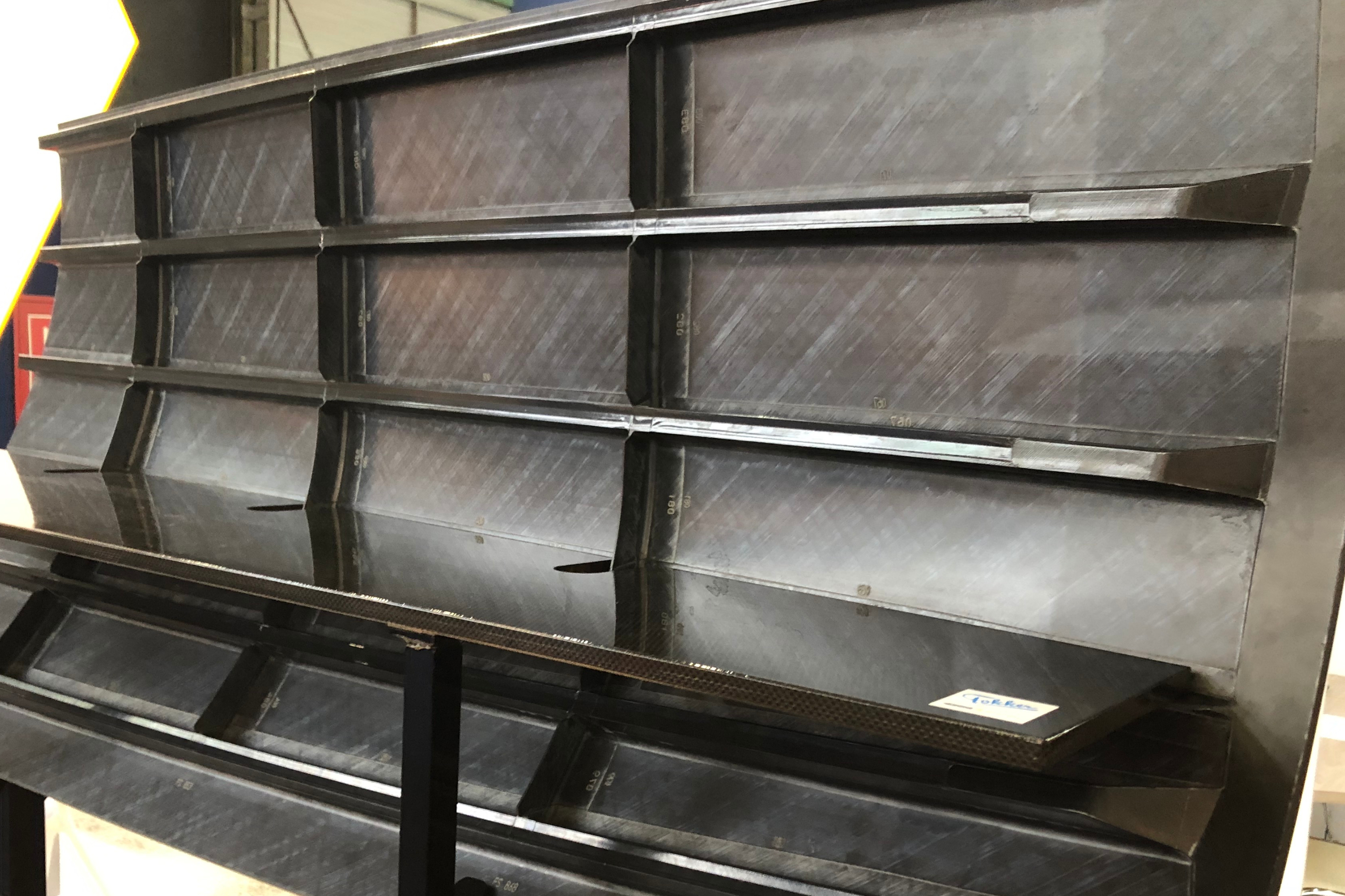
Im August 2018 gründeten Solvay (Alpharetta, Georgia, USA), Premium Aerotec und Faurecia Clean Mobility (Columbus, Ohio, USA) die IRG CosiMo (Industry Research Group:Composites for Sustainable Mobility), ein Konsortium, das sich auf die Entwicklung von Materialien und Prozesstechnologien, die darauf abzielen, die Massenproduktion von thermoplastischen Verbundwerkstoffen für die Luft- und Raumfahrt- und Automobilmärkte zu ermöglichen. Das Konsortium vereint Unternehmen entlang der gesamten Prozesskette thermoplastischer Verbundwerkstoffe vom Werkstoff über die Maschine bis hin zu Anwendungen in der Automobil- und Luftfahrtindustrie. (Erfahren Sie hier mehr über das IRG CosiMo-Konsortium).
Solvay arbeitet seit Juni 2017 mit GKN Fokker (Hoogeveen, Niederlande) zusammen, um die Technologie und die weitere Einführung von TPCs für große Luft- und Raumfahrtstrukturen voranzutreiben. Das Unternehmen startete im September 2017 die Produktion von PEKK-Polymeren und verdoppelte dann seine Kapazität für qualifizierte UD-Thermoplastbänder im Jahr 2018. Zuvor 2019 hat Solvay ein spezielles TPC-Forschungslabor in Alpharetta, Georgia, USA, in Auftrag gegeben, das auf die Entwicklung von Materialien der nächsten Generation abzielt. Solvay plant, Ende 2019 mit der Qualifizierung einer neuen UD-Bandlinie zu beginnen.
Teijin Ltd. (Tokio, Japan) gab im Januar 2019 bekannt, dass sein unidirektionales vorimprägniertes Klebeband TENAX aus Kohlefaser und Kohlefaser/thermoplastischem Kunststoff (TENAX TPUD) von Boeing (Chicago, Illinois, USA) für die Verwendung als Zwischenprodukt qualifiziert wurde Verbundmaterial für primäre Strukturteile (Lesen Sie hier die vollständige Meldung).
Im Zuge der Weiterentwicklung dieser und ähnlicher Technologien und Materialien zeichnet sich allmählich ein Bild davon ab, wie die Luft- und Raumfahrtindustrie in den kommenden Jahren und Jahrzehnten aussehen könnte. Die Rolle von TPCs wird ein immer wichtigerer Bestandteil dieses Bildes.
Hersteller sind daran interessiert, die Fertigungsvorteile und schnellen Verarbeitungszeiten von Thermoplasten zu nutzen und TPCs zu verwenden, um größere Strukturen wie Rumpfpaneele und -rippen herzustellen. Darüber hinaus zeichnen sich Thermoplaste durch eine hohe Bruchzähigkeit aus; gute mechanische Eigenschaften; Recyclingfähigkeit; niedrige Flamme, Rauch und Toxizität (FST) und kann bei Raumtemperatur gelagert werden. Und da OEMs und Zulieferer der Luft- und Raumfahrtindustrie mit Thermoplasten vertrauter werden, werden sie für komplexere Teile, Schweißbaugruppen und Primärstrukturen verwendet.
Laut Steve Mead, Managing Director bei Toray Advanced Composites (ehemals TenCate), „suchen [große Flugzeughersteller] wirklich nach einer Materiallösung, die die Geschwindigkeitsfähigkeiten von Aluminium und die Gewichtsfähigkeiten von kohlenstofffaserbasiertem Material aufweist – eine Art thermoplastische Brücke diese Lücke.“
Verarbeitbarkeit von TPCs
Ein großer Teil der Gründe, warum TPCs ihren Platz in Flugzeugprogrammen finden, ist ihre Verarbeitbarkeit. Da Thermoplaste bereits vollständig polymerisiert sind, haben sie schnellere Produktionsraten als Duroplaste, die gehärtet werden müssen.
„Wenn man sich die Zeit ansieht, die heute für die Herstellung eines duroplastischen Teils benötigt wird, und sie mit der Zeit vergleicht, die für die Herstellung eines thermoplastischen Verbundteils benötigt wird, ist [thermoplastisch] etwa zehnmal schneller“, sagt Mike Favaloro, Präsident und CEO von CompositeTechs LLC (Amesbury, Massachusetts, USA), einem Beratungsunternehmen für die Verbundwerkstoffindustrie.
Ein großer Vorteil der thermoplastischen automatisierten Faserplatzierung (AFP) im Vergleich zu duroplastischem AFP – insbesondere angesichts des fehlenden Härtungszyklus – sind höhere Produktionsraten aufgrund der schnelleren Verarbeitungszeit. Es gibt Kosteneinsparungen bei der In-Situ-Laminierung und der Nachverfestigung außerhalb des Autoklaven (OOA). Außerdem ermöglicht das Herausnehmen des Autoklaven aus der Gleichung die Entwicklung größerer Strukturen.
David Leach, Director of Business Development bei ATC Manufacturing (Post Falls, Idaho, USA), räumt ein, dass die Stückkosten von Thermoplasten die Kosten von Duroplasten übersteigen, argumentiert jedoch, dass die TPC-Materialpreise sinken werden. Darüber hinaus bietet die Effizienz der Verarbeitung heute die Möglichkeit, Kosten zu senken. Der allgemeine Konsens in der Verbundwerkstoffindustrie ist, dass thermoplastische OOA-Prozesse derzeit Kosteneinsparungen von mehr als 30 Prozent im Vergleich zu Duroplasten bieten.
„Thermoplaste halten auch nach der Produktion von Flugzeugen Einzug in die Programme“, betont Leach. „Es ist ein Beweis für die Kostenvorteile von Thermoplasten.“
Das Potenzial leistungsstarker Matrixpolymere geht über das derzeit auf dem Markt erhältliche hinaus. Doug Brademeyer, Leiter des Bereichs Ultra-Polymers Materials bei Solvay, sagt, dass das Unternehmen sowohl intern als auch mit Partnern daran arbeitet, maßgeschneiderte Polymere zu entwickeln, die auf die verschiedenen Herstellungsverfahren zugeschnitten sind.
„Wir sind von diesen maßgeschneiderten PAEK-Lösungen begeistert und können diese basierend auf den Kundenbedürfnissen schnell zur Kommerzialisierung in unseren weltweiten Anlagen bringen“, sagt Brademeyer.
Niedrigschmelzendes PAEK
Da Flugzeug-OEMs und -Zulieferer nach höheren Produktionsraten und kürzeren Zykluszeiten streben, ist die Verarbeitbarkeit entscheidend. Polyetheretherketon (PEEK) ist seit langem das bevorzugte thermoplastische Polymer, da es die größte Datenbank hat und am weitesten qualifiziert ist. Aber laut Favaloro bietet Low-Melt-Polyarlyetherketon (LM PAEK) einige Vorteile, insbesondere für automatisierte Verarbeitungsverfahren wie ATL.
„PEEK ist durch Stanzformen und kontinuierliches Formen verarbeitbar, aber LM PAEK lässt sich bei einer niedrigeren Temperatur verarbeiten, hat eine niedrigere Arbeitsviskosität, die eine bessere automatisierte Verarbeitung ermöglicht, und hat einen niedrigeren Kristallinitätsgrad, der die Restspannungen beim Formen reduziert“, sagt er.„Das ultimative Ziel ist es, eine ATL-Maschine zu verwenden, um [das Band] abzulegen und fertig zu sein – Sie benötigen den richtigen Kristallinitätsgrad, ein gutes Fenster und gute Ablegegeschwindigkeiten.“
LM PAEK hat ein breites Prozessfenster von 350-385 °C. Als Referenz:Die Verarbeitungstemperaturen für Polyphenylensulfid (PPS) reichen von 330-350 °C, während die Verarbeitungstemperaturen für Polyetherketonketon (PEKK) und PEEK 380 °C bzw. 400 °C betragen.
„Das Material hat aufgrund seiner Verarbeitbarkeit so viel Traktion erlangt“, sagt Scott Unger, Chief Technical Officer bei Toray Advanced Composites. Toray Advanced Composites hat mit Victrex (Lancashire, Großbritannien) zusammengearbeitet, um Cetex TC1225 herzustellen, ein unidirektionales Band mit LM PAEK.
„Die Absicht bei der Entwicklung von TC1225 war, ein Produkt zu schaffen, das sich bei Temperaturen in der Nähe von PPS leicht verarbeiten lässt, eine günstige Kostenposition für den Endverbraucher hat und die mechanischen und flüssigkeitsbeständigen Eigenschaften von PEEK aufweist“, sagt Unger. „Mit TC1225 LM PAEK habe ich das Gefühl, dass wir all diese Ziele erreicht haben.“
Cetex TC1225 wird derzeit vom National Center for Advanced Materials Performance (NCAMP, Wichita, Kan., USA) qualifiziert. Darüber hinaus sind laut Toray zwei wichtige flugzeuggestützte Qualifikationen für das Material in Arbeit sowie einige Qualifikationsprogramme, die auf aufstrebenden Märkten wie Lufttaxis und urbaner Luftmobilität basieren.
Bänder, die LM PAEK verwenden, liefern Berichten zufolge verbesserte Ablegegeschwindigkeiten. Tim Herr, Direktor der SBU Aerospace bei Victrex, sagt:„Die Ablagerungsraten, die wir sowohl für in-situ-AFP als auch für konsolidiertes AFP außerhalb des Autoklaven erreichen können, sind beispiellos.“ Er gibt an, dass auf ofenverfestigten Platten 60 Meter pro Minute erreicht werden können; Berichten zufolge sind 20 Meter pro Minute mit In-Situ-Konsolidierung möglich.
In Bezug auf die Qualität behauptet Unger, dass niedrigschmelzendes PAEK die Möglichkeit bietet, die gleiche Laminatqualität durch in-situ-Faserplatzierung zu erzielen wie mit einem faserplatzierten Laminat, das einer Konsolidierung im Ofen nach der Faserplatzierung unterzogen wurde.
Verbundwerkstoffe
Die Schweißbarkeit von TPCs ist ein großer Vorteil des Materials für den Einsatz in der Flugzeugentwicklung. Das Schmelzkleben/Schweißen bietet eine Alternative zur mechanischen Befestigung und dem Einsatz von Klebstoffen, beides Verfahren zum Fügen von duroplastischen Verbundteilen.
Stephen Heinz, Produktentwicklungsleiter bei Solvay, sagt:„Fügen und Schweißen spielen eine wichtige Rolle in der Montage der Zukunft und haben das Potenzial, Kosten zu senken und die Zuverlässigkeit von Flugzeugstrukturen zu verbessern. Unternehmen wie GKN Fokker sind führend bei der Demonstration von Schweißen.“
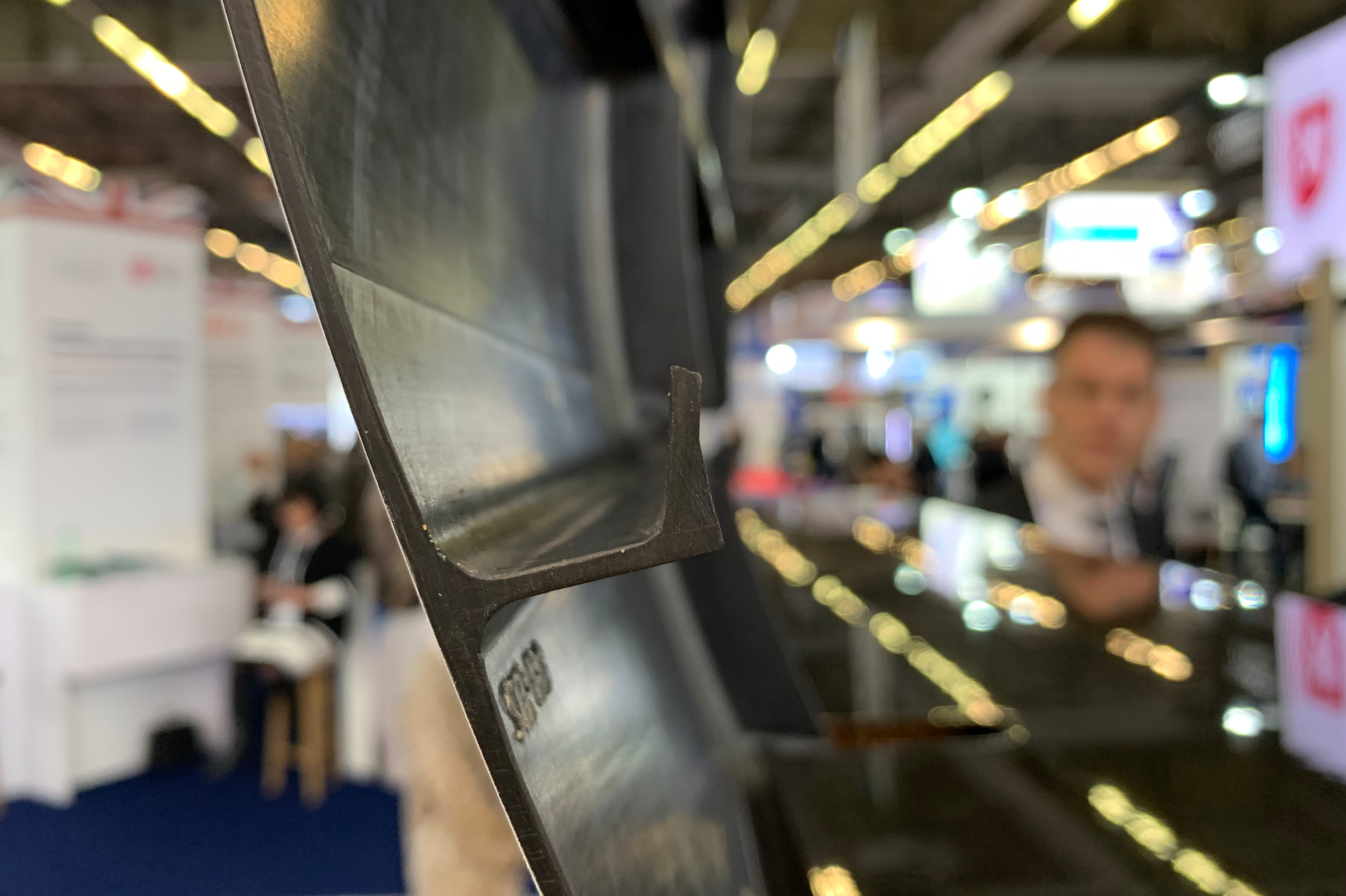
GKN Fokker (Hoogeveen, Niederlande) arbeitet seit einiger Zeit an der Entwicklung von TPCwelding und hat in den 1990er Jahren begonnen, mit dem Widerstandsschweißen von Thermoplasten zu experimentieren. Das Unternehmen verwendet thermoplastische Schweißverfahren, um hochmoderne Innenrippen und -häute zu verbinden. Auf der JEC World 2019 präsentierte das Unternehmen eine flächenregulierte Rumpfplatte aus thermoplastischem Verbundwerkstoff, die mit dem UD-Band APC (PEKK-FC) von Solvay hergestellt wurde. Das Panel ist das Ergebnis eines gemeinsamen F&E-Projekts von GKN Fokker und Gulfstream Aerospace (Savannah, Georgia, USA). Das Teil ist angeblich die kostengünstigste Verbundplatte, aufgrund der einfachen "stumpfverbundenen" orthogonalen Versteifung und der vollständig geschweißten Rahmen.
„Bei Thermoplasten kann ein Orthogrid stark vereinfacht werden, indem das Gitter mit der Haut ‚stumpf verbunden‘ wird“, erklärt Arnt Offringa, Leiter der Technologieentwicklung Thermoplastische Verbundwerkstoffe bei GKN Fokker. „Das Gitter besteht jetzt nur noch aus einfachen, flachen Preforms, die zusammen mit dem Skin-Laminat zu einer kostengünstigen, integral versteiften Schale verfestigt werden. Rahmen werden auf das Gitter geschweißt. Diese Schweißnähte werden auf Scherung belastet, sodass alle Schrauben weggelassen werden können.“
Während geschweißte thermoplastische Strukturen schon seit einiger Zeit bei Flugzeugen verwendet werden, scheint die Technologie nun für den Einsatz in Primärstrukturen gut geeignet zu sein. Mike Favaloro ist der Ansicht, dass Hersteller und OEMs in der Luft- und Raumfahrtindustrie mit TPCs, insbesondere mit der Prozesssteuerung, Vertrauen gewinnen. „Auf einen 10-Jahres-Horizont werden wir feststellen, dass es viel mehr angenommen wird“, sagt er.
Lesen Sie mehr über die Schweißtechnologie im Artikel von Ginger Gardiner „Welding thermoplastischer Verbundwerkstoffe“.
Werkzeuglos arbeiten
Eine weitere Innovation am Horizont, die den Einsatz von Thermoplasten beschleunigen könnte, ist die werkzeuglose Herstellung von Verbundwerkstoffen. Das Konzept macht, wie der Name schon sagt, traditionelle Formen und Werkzeuge überflüssig und ersetzt sie durch Roboter.
Der Luft- und Raumfahrthersteller General Atomics Aeronautical Systems Inc. (GA-ASI, San Diego, Kalifornien, USA) entwickelt ein solches Verfahren zur Herstellung thermoplastischer Verbundstrukturen. Composite Automation LLC (Cape Coral, Florida, USA) arbeitete mit Geräten von Mikrosam (Prilep, Mazedonien) mit GA-ASI an der Entwicklung der Automatisierung. Der Prozess verwendet zwei 6-Achs-Roboter, die zusammenarbeiten, um thermoplastisches Klebeband zu platzieren. Ein Roboter besteht aus einem standardmäßigen unidirektionalen Tape-Placement-System, das eine Lasererwärmung bereitstellt, um eine in-situ-Verfestigung des thermoplastischen Materials durchzuführen. Der zweite Roboter bietet Unterstützung, indem er gegenüber der automatisierten Bandschicht (ATL) arbeitet, um eine bewegliche Werkzeugoberfläche bereitzustellen, gegen die die ATL das Band legt. (Weitere Informationen finden Sie unter „General Atomics Aeronautical Entwicklung werkzeugloser thermoplastischer Verbundwerkstoffe.“)
Recyclingfähigkeit
Ein weiterer Vorteil von TPCs ist die Recyclingfähigkeit. Da thermoplastische Polymere umgeschmolzen und umgeformt werden können, suchen mehrere Unternehmen nach TPCs, um Materialien wiederzuverwenden.
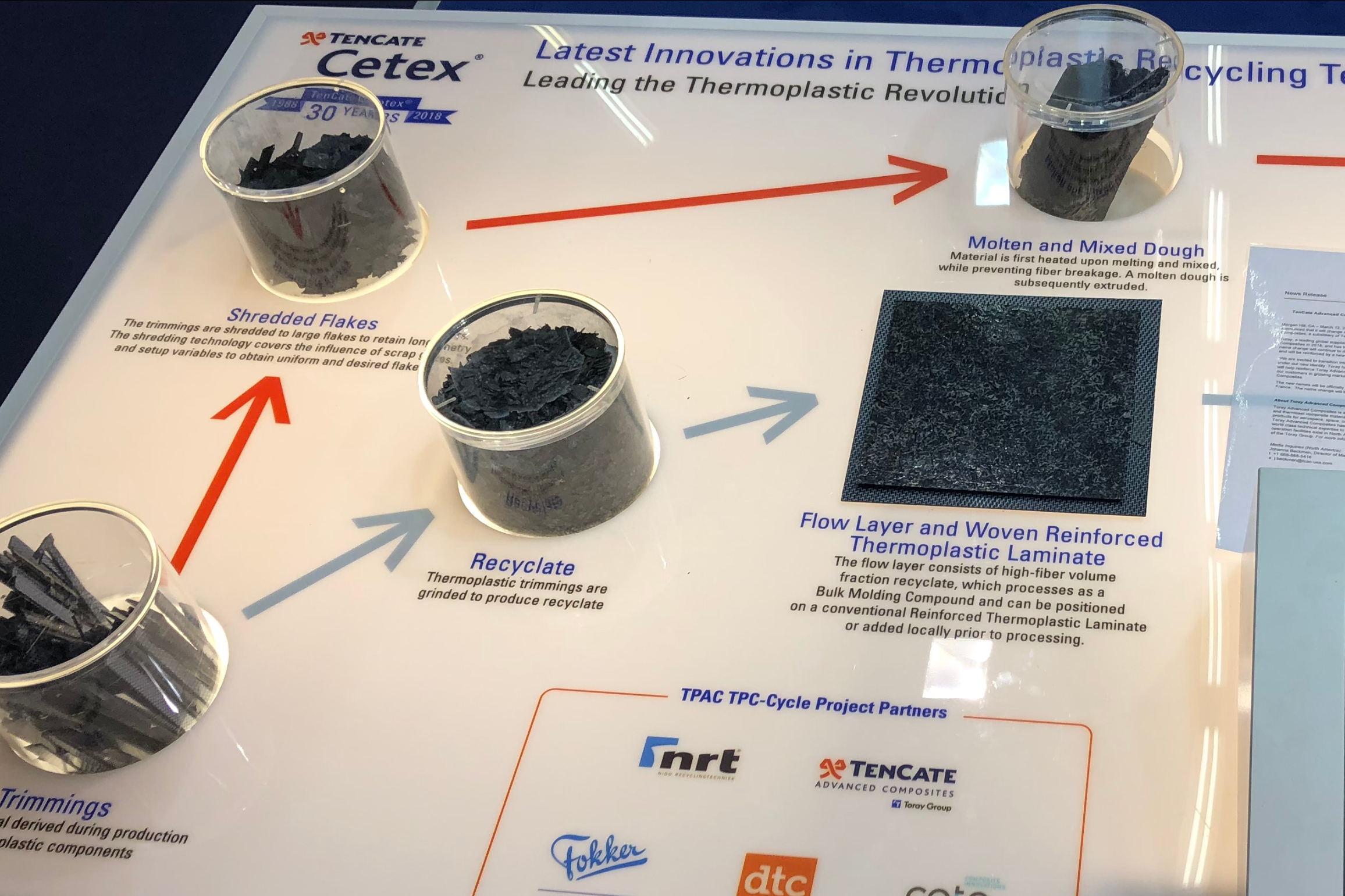
Eine solche Recyclinginitiative, die vom Thermoplastic CompositesApplication Center (TPAC, Enschede, Niederlande) und dem Thermoplastic Composites Research Center (TPRC, Enschede, Niederlande) betrieben wird, konzentriert sich auf die Wiederverwendung von Produktionsabfällen aus der TPC-Verarbeitung, von der Sammlung bis zur Zerkleinerung und Aufbereitung bis zur Anwendung. Das Projekt TPC-Cycle arbeitet daran, einen erschwinglichen, umweltfreundlichen Recyclingweg für High-End-Märkte mit hohem Volumen zu entwickeln – und gleichzeitig ein Material herzustellen, das so viele mechanische Eigenschaften wie möglich der ursprünglichen thermoplastischen Materialien behält. Das Projekt zeichnet sich durch kurze Zykluszeiten, eine Nettoformfertigung aus und soll die Herstellung komplexer Formen ermöglichen.
Die Zusammenarbeit umfasst mehrere Industriepartner in der Wertschöpfungskette von Material, Herstellung, Design und Anwendung, darunter GKN Fokker, Toray Advanced Composites, Cato Composite Innovations (Rheden, Niederlande), Dutch Thermoplastic Components (Almere, Niederlande) und Nido RecyclingTechniek (Nijverdal .). , Niederlande).
Das richtige Material für den richtigen Job
Inmitten der Aufregung um diese Materialien stellt sich also die Frage, sind TPCs angekommen? Tier-1- und Tier-2-Luft- und Raumfahrtlieferanten investieren in Thermoplaste. Es gibt mehr Interesse und Investitionen von kleineren und mittleren Anbietern. Konsortien wie IRG CosiMo untersuchen sowohl den Luft- und Raumfahrt- als auch den Automobilmarkt, um Prozesstechnologien voranzutreiben, um eine Großserienproduktion zu erreichen.
„Es ist die Trifecta“, sagt Mead, „OEMs investieren, Maschinenhersteller investieren, das richtige Material wurde entwickelt. Alle Komponenten des Rezepts kommen zusammen.“
Was bedeutet dies im weiteren Sinne für den Materialeinsatz bei Flugzeugen der nächsten Generation? Schließlich konkurrieren zahlreiche Materialien um einen Platz im Flugzeug der Zukunft, und die Innovation lässt nicht nach – duroplastische Verbundwerkstoffe entwickeln sich weiter; Aluminium und Titan werden weiterhin eine Rolle spielen.
„Da Flugzeugbauer mit Thermoplasten eine Qualifikationsbasis aufbauen, haben sie jetzt die Wahl“, sagt Unger. „Und diese Wahl basiert auf der Auswahl des richtigen Materials für eine bestimmte Anwendung, das die Produktionsgeschwindigkeit und die Kostenanforderungen für das jeweilige Bauteil oder die jeweilige Struktur erfüllt. Wenn Sie sich die kommerzielle Luftfahrt in der Zukunft ansehen, werden Sie sehen, dass Flugzeughersteller das richtige Material für die richtige Aufgabe verwenden. Wenn ein Material die am besten geeignete Struktur zu den geringsten Kosten ermöglicht und die Anforderungen an die Baugeschwindigkeit des Programms erfüllt, wird es sich im Flugzeug durchsetzen.“
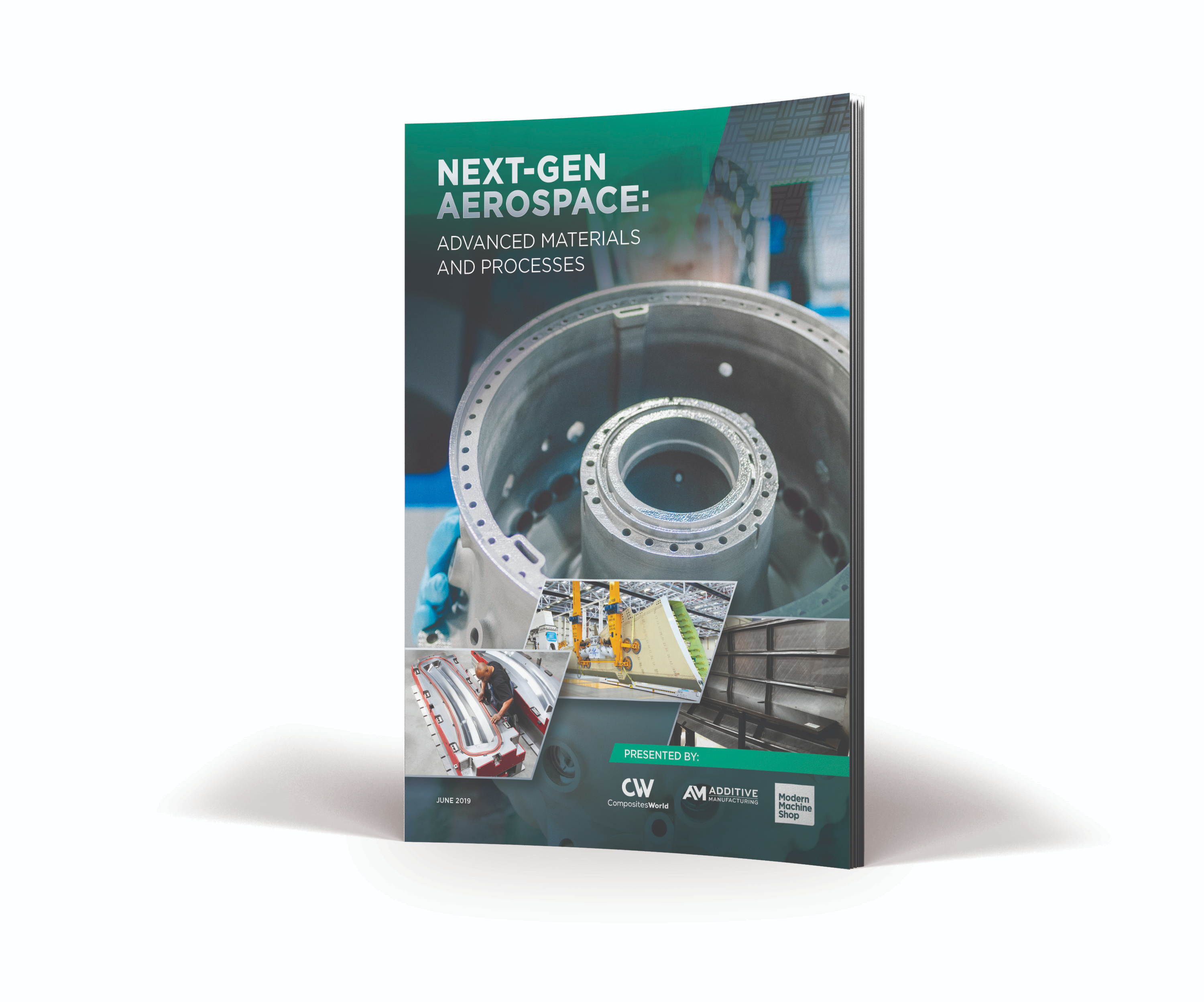
Die nächste Generation der Luft- und Raumfahrtfertigung
Da sich die kommerzielle Luftfahrtindustrie in den nächsten 20 Jahren voraussichtlich verdoppeln wird, erfordert die Deckung der Nachfrage nach Passagier- und Frachtflugzeugen neue Technologien und beispiellose Fertigungsraten.
Erfahren Sie mehr über die Materialien und Prozesse, die Flugzeuge der nächsten Generation prägen werden, in einer Sammlung von Geschichten von CompositesWorld, Modern Machine Shop und Additive Fertigung , verfügbar zum kostenlosen Lesen oder Herunterladen . Holen Sie es hier.
Harz
- Covestro verstärkt Investitionen in thermoplastische Verbundwerkstoffe
- Thermoplastische Verbundwerkstoffe bei Oribi Composites:CW Trending, Episode 4
- Fehlerbehebung beim Thermoformen von thermoplastischen Verbundwerkstoffen
- Thermoplastische Verbundwerkstoffe:Strukturelle Stoßstangenhalterung
- Toray Advanced Composites erweitert seine Fähigkeiten im Bereich thermoplastischer Verbundwerkstoffe
- ACMA veröffentlicht Programm der Konferenz für Thermoplastische Verbundwerkstoffe 2020
- Thermoplastische Tür eine Premiere für Automobilverbundwerkstoffe
- Thermoplastische Verbundwerkstoffe:Malerische Aussicht
- CAMX 2018-Vorschau:TenCate Advanced Composites
- Schweißen von thermoplastischen Verbundwerkstoffen