Composite-3D-Druck ermöglicht Schadenserkennung in der Luft- und Raumfahrt und im Bauwesen
Brightlands Materials Center (Geleen, Niederlande) hat 3D-gedruckte Verbundteile mit selbsterfassender Funktionalität entwickelt. Self-Sensing bietet Möglichkeiten zur Überwachung kritischer Strukturen in Bereichen wie Luft- und Raumfahrt, Bauwesen und Gesundheitswesen.
Was ist Selbsterkennung?
Self-sensing ist die Fähigkeit eines Materials, als Sensor zu fungieren und Informationen über seinen eigenen Zustand zu sammeln. Kohlenstoffaser-verstärkte Polymer-Matrix-Verbundwerkstoffe haben sich bereits als Self-Sensing-Fähigkeiten etabliert, die auf messbaren Änderungen des elektrischen Widerstands der Endlosfasern basieren. Solche Materialien werden für die Überwachung des strukturellen Zustands (SHM) in Flugzeugen und Bauanwendungen einschließlich Brücken und Gebäuden entwickelt und demonstriert.
Traditionell wurden solche selbsterfassenden Verbundmaterialien unter Verwendung von Techniken hergestellt, die mehrere Stufen, komplexere Vorgänge und spezielle Ausrüstung beinhalten. Das Brightlands Materials Center kombiniert die Selbsterkennung von Endlos-Kohlenstofffasern mit der Herstellung mittels additiver Fertigung, um SHM-Anwendungen kosteneffektiver zu machen und eine breitere Nutzung und Ausweitung auf neue Anwendungen zu ermöglichen.
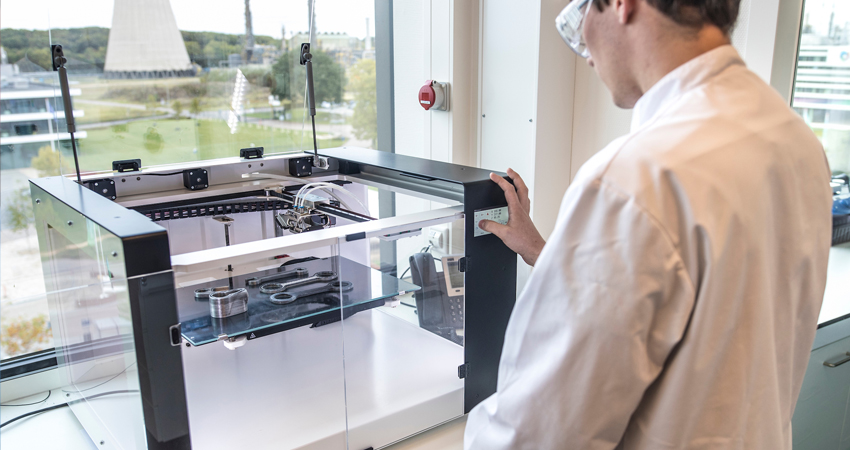
Endlosfaser-3D-Druck eröffnet neue Horizonte
Die additive Fertigung ermöglicht eine sehr genaue Positionierung und Ausrichtung von Carbon-Endlosfasern. Somit ist es möglich, die Fasern an ausgewählten Stellen innerhalb des Produkts zu platzieren, um die erforderliche Festigkeit und Steifigkeit entlang bestimmter Lastpfade bereitzustellen und einen integralen Bestandteil der Struktur zu bilden. Dies bedeutet, dass die Kohlefasern dort platziert sind, wo sie als „Sensoren“ zur Überwachung der Struktur benötigt werden, und mehrere Fasern können eine Reihe von Sensoren im gesamten Teil bilden.
Das Brightlands Materials Center hat dieses Konzept demonstriert, indem es die Verformung in einem maßstabsgetreuen Modell einer Fußgänger-Verbundbrücke und in einem einfachen Biegebalken überwacht hat. Beide wurden mit dem Composer A4 Composite-3D-Drucker Anisoprint (Esch-sur-Alzette, Luxemburg) gedruckt. „Wir freuen uns besonders über unsere neuen Anisoprint-Systeme, da sie eine so hohe Freiheit bei der Wahl der Druckmaterialien sowie die vollständige Kontrolle der Faserablage bieten“, sagt Guy Bex, Forschungsingenieur am Brightlands Materials Center. Die Freiheit bei der Faserpositionierung ist auch für die Sensorik entscheidend, da die durchgehenden Kohlefasern aus dem Teil herausragen müssen, um Verbindungen mit der für die Überwachung verwendeten elektronischen Hardware herzustellen.
Präzise 3D-Druckergebnisse
Da der 3D-Druck keine Werkzeuge oder Formen erfordert, bietet er einen einstufigen Prozess zur Herstellung von endlosfaserverstärkten Verbundwerkstoffen jeder Form und ersetzt traditionelle mehrstufige Techniken, die komplexer, zeitaufwendiger und teurer sind. Die Optimierung des Herstellungsprozesses für 3D-gedruckte Strukturen kann jedoch mehrere Iterationen erfordern. 3D-gedruckte Verbundwerkstoffe mit Selbsterkennung können Informationen über ihre realen Nutzungsbedingungen sammeln, die für die Design- und Prototypenphase neuer Produkte wichtig sind.
Während dieser Tests registriert das selbsterkennende 3D-gedruckte Teil die realen Bedingungen und Kräfte, die im Betrieb erfahren werden, was Konstrukteuren und Ingenieuren ein genaueres Verständnis der tatsächlichen Anforderungen gibt, denen gedruckte Teile standhalten müssen.
Eine solche Erfassung kann es auch ermöglichen, dass Teile als Diagnosewerkzeug dienen. So können beispielsweise 3D-gedruckte selbsterkennende Orthesen- oder Prothesenteile Patienten leiten und Ärzten wertvolle Informationen über Stressverteilung und Bewegungsmuster liefern.
Forschungspartner
Das Brightlands Materials Center ist ein unabhängiges Forschungszentrum, das von der niederländischen Organisation für angewandte wissenschaftliche Forschung TNO (Den Haag) und der Provinz Limburg gegründet wurde. Es unterstützt Innovationen in der Industrie mit einem starken Anwendungsfokus und bietet engagierte Auftragsforschung und Beteiligung, einschließlich einer Forschungs-Roadmap zu 3D-gedruckten selbstsensorischen Verbundwerkstoffen.
Anisoprint ist Erfinder des Anisodruckens – der Technologie für das Design und die Herstellung optimaler Verbundstrukturen durch kontinuierliche 3D-Faserabscheidung. Das Unternehmen stellt 3D-Drucker, Materialien (auf Basis von Kohlenstoff- und Basaltfasern) und Software für die Herstellung von anisogedruckten Verbundteilen her, um Wissenschaftlern dabei zu helfen, Forschungsprobleme auf neue, effektivere Weise zu lösen und Fertigungsunternehmen zu ermöglichen, ihre Kosten zu senken.
Harz
- 3D-Druck und Formel 1:5 Trends im Motorsport
- Experteninterview:Roboze-CEO Alessio Lorusso zum Hochleistungs-3D-Druck von Verbundwerkstoffen
- DSM und Nedcam entwickeln neue Anwendungen für den großformatigen 3D-Druck
- Impossible Objects arbeitet mit BASF für den 3D-Verbunddruck zusammen
- Victrex- und Bond-Partner für den 3D-Druck von PAEK-Teilen
- SABIC bringt Verbundplatten für Bau und Konstruktion auf den Markt
- Materialien und Konstruktion für flexible Schaltkreise
- 3D-Druck von Verbundwerkstoffen:Eine Einführung
- Die erstaunliche Entwicklung des 3D-Drucks in Luft- und Raumfahrt und Verteidigung
- Häufige Bauunfälle und Verletzungen