CETMA:F&E und Innovation im Bereich Verbundwerkstoffe in Italien
Centro di Ricerche Europeo di Technologie, Design e Materiali (CETMA, Brindisi, Italien) wurde 1994 gegründet und ist eine der größten unabhängigen Forschungs- und Technologieorganisationen in Italien mit einer 4.000 Quadratmeter großen Einrichtung und 75 Mitarbeitern. CETMA investiert seit mehr als 20 Jahren stark in Verbundwerkstoffe, was zu einem breiten Know-how geführt hat:
- Komponentendesign und Prototyping
- Neue Verbundprozesse
- Recyclingprozesse für Verbundstoffe und Kunststoffe
- Prozessoptimierung für Kosten, Nachhaltigkeit, Rate usw.
- Prozessüberwachung in Echtzeit
- Zerstörungsfreie Prüfung (NDT)
- Structural Health Monitoring (SHM) in Echtzeit und aus der Ferne während Produktion und Service
- REACH-Beratung
- Thermoplastisches Stanzen, Continuous Compression Moulding (CCM) und Prepreg Compression Moulding (PCM)
- Flüssiginfusion, Resin Transfer Moulding (RTM) und gleich qualifiziertes RTM (SQRTM)
- Prepreg außerhalb des Autoklaven (OOA)
- Induktionsschweißen
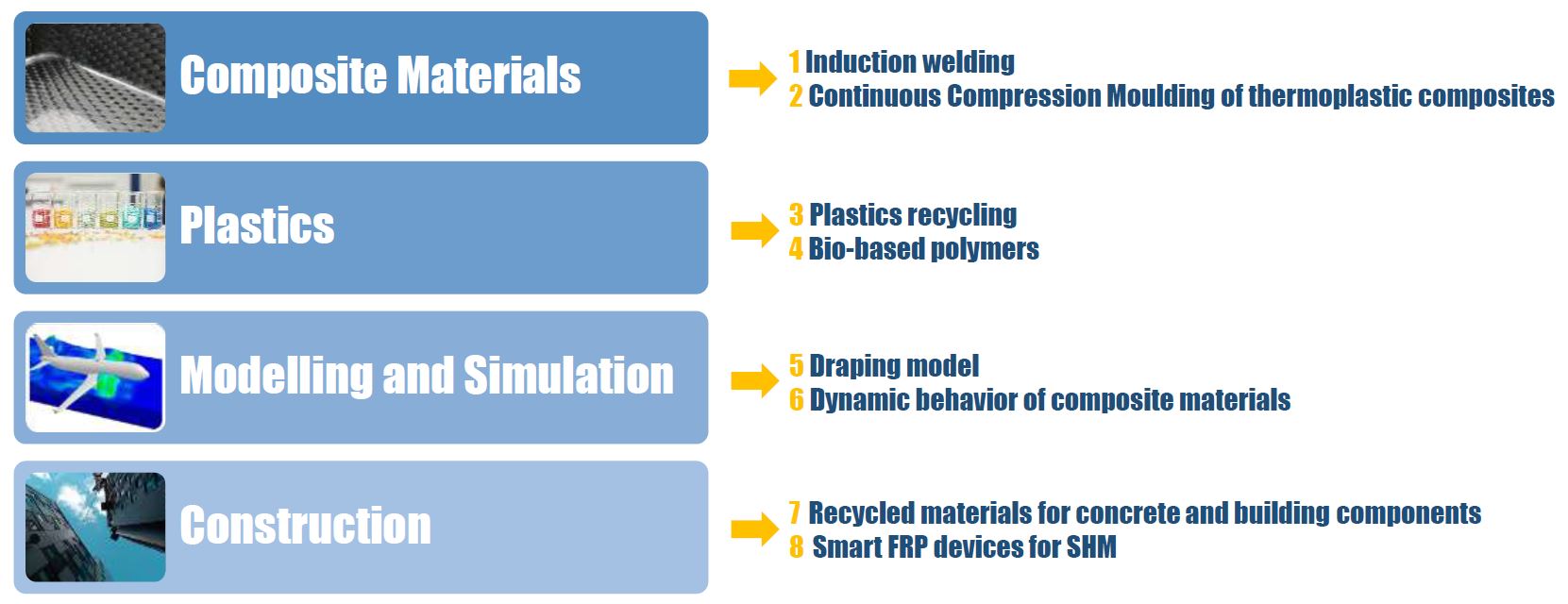
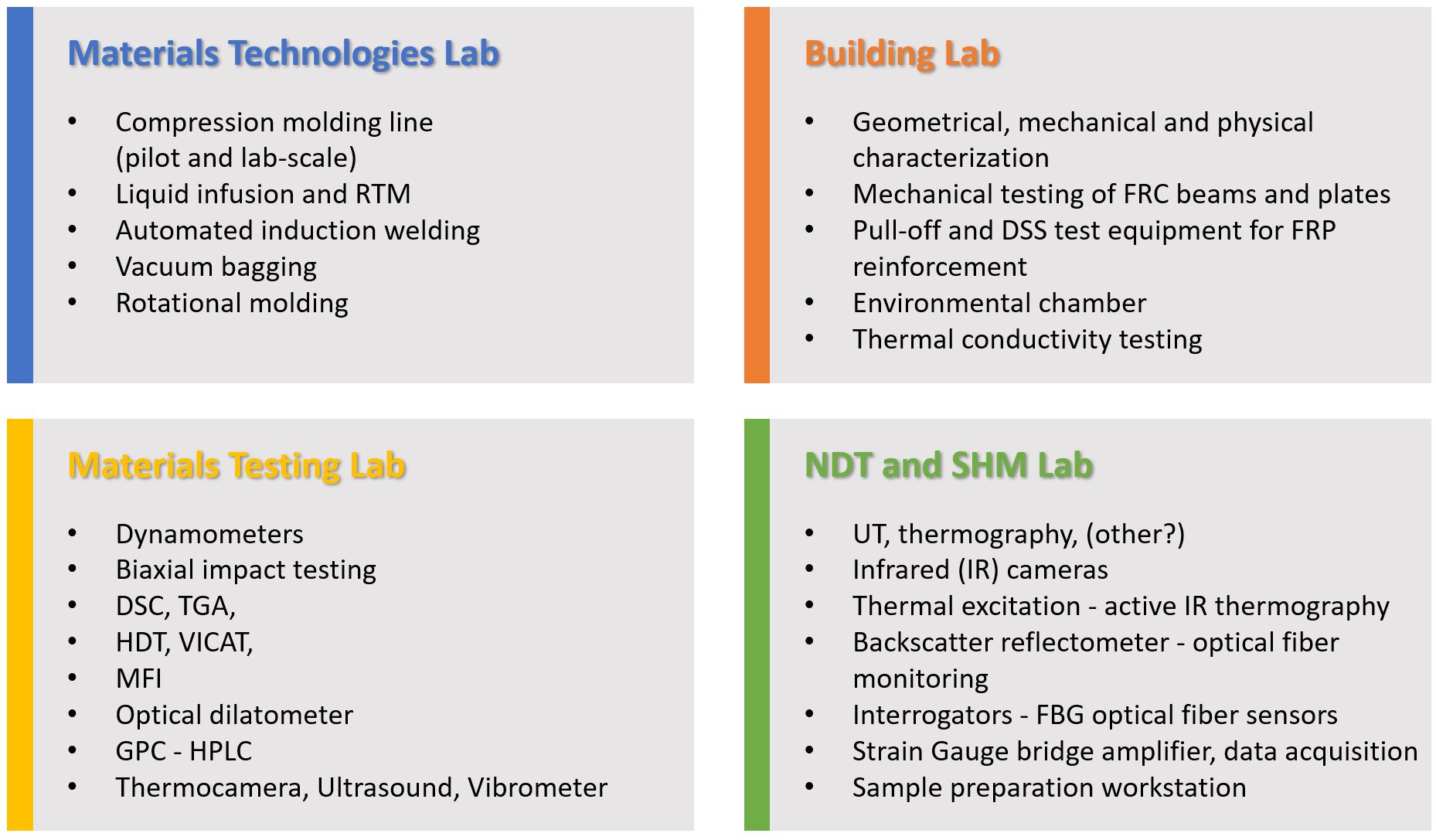
Das Hauptziel von CETMA ist die Unterstützung von Unternehmen und Innovationen. Die Verbundwerkstoffaktivitäten von CETMA werden von vier Hauptlabors betreut und sind in der Abteilung Advanced Materials and Processes (AMP) organisiert, die auch vier Bereiche umfasst:
- Materialien und Charakterisierung
- Technologien und Prozesse
- Modellierung und Simulation
- Diagnose und strukturelle Zustandsüberwachung
AMP beschäftigt 30 Mitarbeiter, darunter Material-, Luftfahrt-, Bau- und Chemieingenieure sowie einen Chemiker, Materialwissenschaftler, Architekten und mehrere Techniker – entsprechend seinem Glauben an multidisziplinäre Teams.
Stärke in thermoplastischen Verbundwerkstoffen
„Wir bieten ein umfassendes Leistungsspektrum im Bereich Verbundwerkstoffe“, sagt Alessandra Passaro, Leiterin der AMP-Abteilung bei CETMA, „aber unsere Aktivitäten im Bereich thermoplastischer Materialien sind derzeit einer unserer Schwerpunkte. In unserem Labor wurden alle Arten von thermoplastischen Matrixpolymeren verarbeitet. Wir begannen 2004 mit TWINTEX Mischfasern zu arbeiten und vor etwa 15 Jahren mit dem Formpressen mit einer einfachen Presse. Jetzt haben wir patentierte Continuous Compression Moulding (CCM) und Induktionsschweißtechnologien entwickelt. Wir haben alle thermoplastischen Verbundwerkstoffe analysiert, die in diesen Prozessen eingesetzt werden können.“
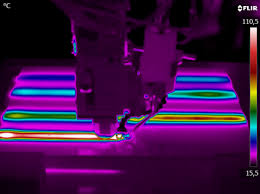
Die CCM-Linie kann Teile mit konstantem Querschnitt aus PPS, PEEK, PEKK oder PAEK herstellen. Aber inwiefern unterscheidet sich der CETMA-Prozess von dem, der von Unternehmen wie XELIS (Markdorf, Deutschland) und ATC Manufacturing (Post Falls, Idaho, USA) verwendet wird? (Siehe CW-Artikel:„Kompressionsformen in Luft- und Raumfahrtqualität“ und „Beschleunigung von thermoplastischen Verbundwerkstoffen in der Luft- und Raumfahrt“.) Passaro erklärt:„Es gibt einige spezifische Details bei der Konstruktion des von uns verwendeten Werkzeugs. Unsere Technologie ist flexibler hinsichtlich der verwendbaren Geometrien und Matrixmaterialien. Es befindet sich noch in der Entwicklung.“ Obwohl patentiert, wird die Technologie noch weiterentwickelt und einige Aspekte sind proprietär. Der Grund, warum CETMA CCM verfolgt hat, ist nicht. „Wir haben den zunehmenden Einsatz und Bedarf an kontinuierlichen thermoplastischen Verbundprozessen gesehen“, sagt Passaro. „XELIS ist ein Produktunternehmen, kein Maschinenlieferant. Wir sind eine unabhängige F&E-Organisation und investieren daher in die Technologie und entwickeln sie aus einem anderen Blickwinkel.“
Ein Beispiel dafür ist die umfangreiche Prozesssimulation zur Analyse der Temperaturverteilung im Werkzeug. „Die Simulationsergebnisse geben uns ein vollständiges Bild der Temperaturentwicklung im Material über die Zeit“, erklärt sie, „die inline von einer Seite nur sehr schwer zu überwachen ist und dennoch entscheidend für die Minimierung von Defekten im Verbund ist.“
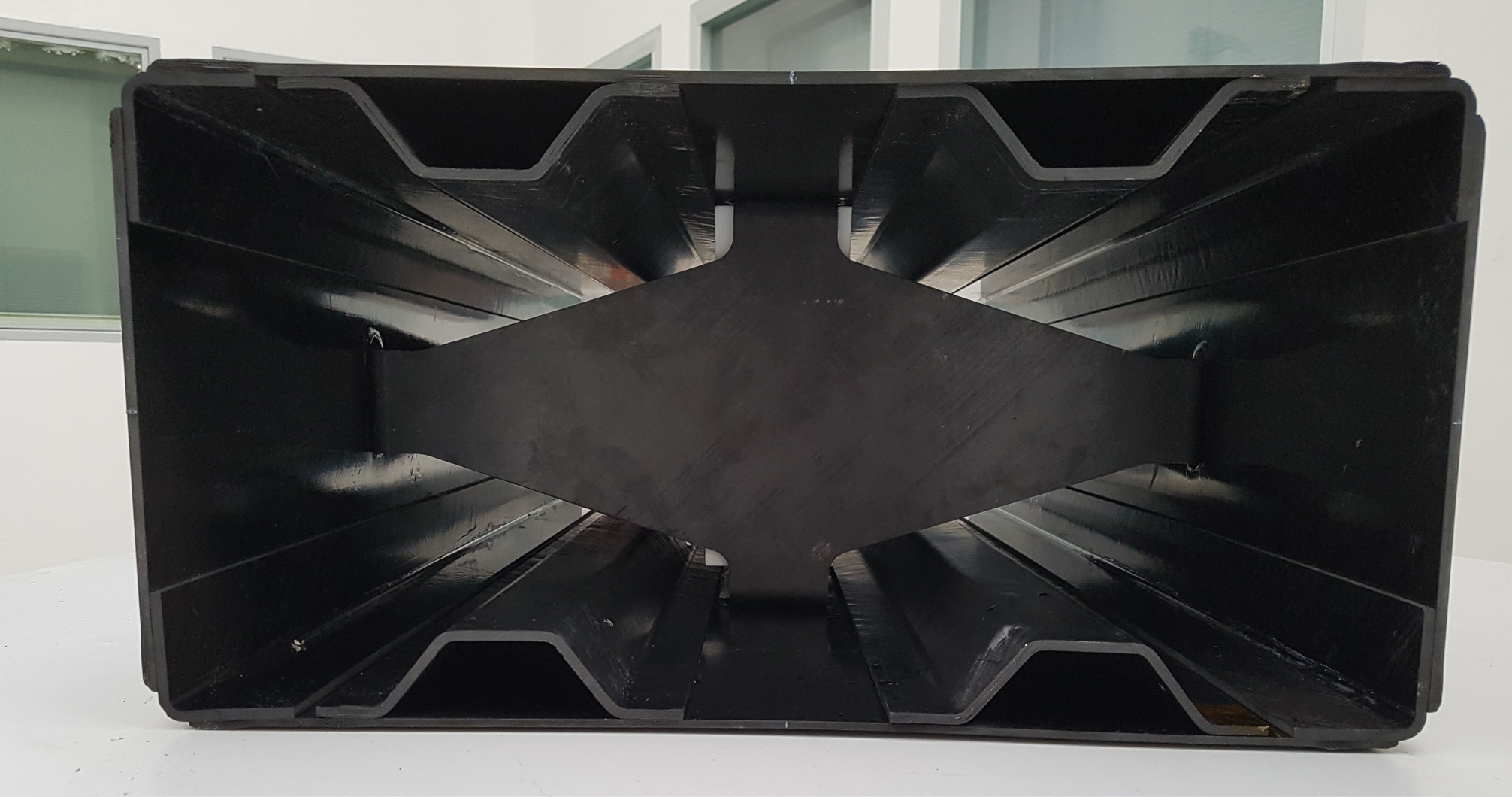
Induktionsschweißen für Montage
Ein weiterer wichtiger Bestandteil des Know-hows von CETMA bei thermoplastischen Verbundwerkstoffen ist die patentierte Induktionsschweißtechnologie, die ein Steuerungssystem und eine Kühlung umfasst, um die Wärme in der Schweißlinie zu halten. CETMA nutzte die Technologie zusammen mit dem Partner EURECAT (Barcelona, Spanien), um CCM-Profile und -Platten zu einem Kielträger aus thermoplastischem Verbundwerkstoff für ein Flugzeug des Typs Airbus A320 im Clean Sky 2 KEELBEMAN-Projekt zu montieren. Mein Blog vom Januar 2020, „Advancing Thermoplast Composites and RTM for Clean Sky 2 …“, enthält weitere Details zu diesem Projekt sowie zu den Details des Schweißens von CETMA.
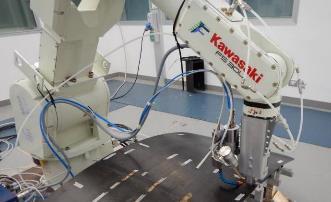
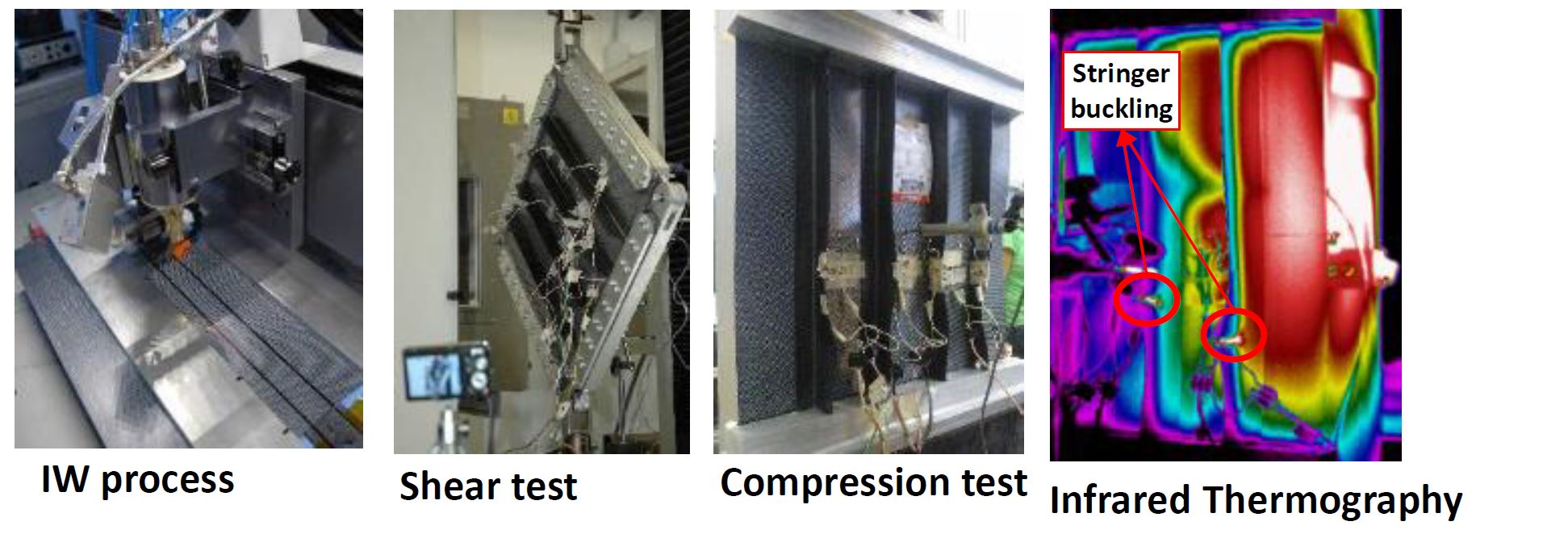
„Wir haben zwei Arten von Induktionsschweißsystemen entwickelt“, sagt Passaro. „Eine ist eine stationäre Maschine für ebene Flächen und eine roboterbasierte für komplexe 3D-Geometrien. Beide ermöglichen kontinuierliche Schweißnähte im industriellen Maßstab, ohne dass zusätzliche Materialien in der Schweißnaht erforderlich sind, und liefern gleichzeitig eine sehr hohe Haftungsleistung in Baugruppen.“
CETMA hat das Induktionsschweißen von Verbundlaminaten aus Kohlefasergewebe und unidirektionalem (UD)-Band sowie einer Reihe von Matrixmaterialien demonstriert:PPS, PEEK, PEI, PEKK, PP, PA6, PA12 und einem hybriden duroplastischen Epoxid/PVB ( Polyvinylbutyral) thermoplastisches System.
Es hat seine Expertise in Computermodellierung und Simulation auch auf den Induktionsschweißprozess übertragen. „Damit können wir den Temperaturverlauf im Fügebereich beim Schweißen vorhersagen und helfen so grundlegend bei der Optimierung der Prozessparameter“, sagt Passaro.

Clean Sky 2 und F&E-Projekte im Bereich Verbundwerkstoffe
Neben KEELBEMAN ist die AMP-Abteilung von CETMA derzeit an vier weiteren Clean Sky 2-Projekten beteiligt.
TRINITI - Thermoplastische Hochdruck-Stickstofftanks aus mehreren Materialien für Flugzeuge (JTI-CS2-CFP09-2018-02). Das auf zwei Jahre angelegte Projekt, das 2019 begann, zielt darauf ab, einen Prototypen eines Flugzeugtanks zur Langzeitspeicherung von Stickstoff für Brandbekämpfungszwecke zu bauen. Diehl Aviation (Gilching und Dresden, Deutschland) ist Themenmanager für das Projekt. Zu den Partnern gehört auch das Forschungs- und Entwicklungslabor für Luft- und Raumfahrt Novotech s.r.l. (Neapel, Italien), Composites Testing Laboratory (Inverin, Co. Galway, Irland). Im Rahmen des Projekts werden Tanks aus thermoplastischen Verbundwerkstoffen aus mehreren Materialien durch eine Kombination von Prozessen hergestellt, wie z ). (Weitere Informationen zu ISC AFP finden Sie unter „Konsolidieren thermoplastischer Verbund-Flugzeugstrukturen, Teil 1 und Teil 2“.) Ein Ziel von TRINITI ist es, Mikrorisse in kryogenen Umgebungen zu reduzieren oder sogar zu eliminieren. Derzeit arbeitet CETMA daran, alle thermoplastischen Materialien zu identifizieren, die die Anforderungen von Luft- und Raumfahrtdruckbehältern erfüllen können.
ERSATZ – Innovative Verbund-Pax- und Ladebodengitter in Originalgröße für regionale Demonstratoren am Boden des Flugzeugrumpfes – (JTI-CS2-2017-CfP07-REG-01-14). Dieses 18-monatige Projekt, das im Oktober 2018 gestartet wurde, zielt darauf ab, vollflächige Fahrgast- und Ladebodengitter aus kohlenstofffaserverstärkten thermoplastischen (TP) Verbundwerkstoffen herzustellen. Die hochautomatisierte Fertigung umfasst das Folgewalzprofilieren und das Induktionsschweißen für die Montage. Ziel ist es, Gewicht und wiederkehrende Kosten im Vergleich zu herkömmlichen Metall- und Duroplast-Verbundlösungen zu reduzieren. Die Bodengitter aus Verbundwerkstoff werden für Bodentests in die Clean Sky 2-Regionalflugzeugrumpf-Demonstratoren eingebaut und auf ihre technischen und wirtschaftlichen Auswirkungen sowie auf ihre Flammwidrigkeit gemäß FAR 25.583-Vorschriften bewertet. Themenführer ist Leonardo, während CETMA das Projekt in Zusammenarbeit mit dem Maschinenhersteller OMI S.r.l. koordiniert. (Fogliano Redipuglia, Italien).
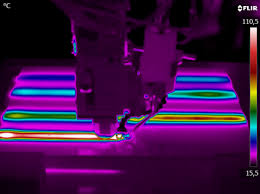
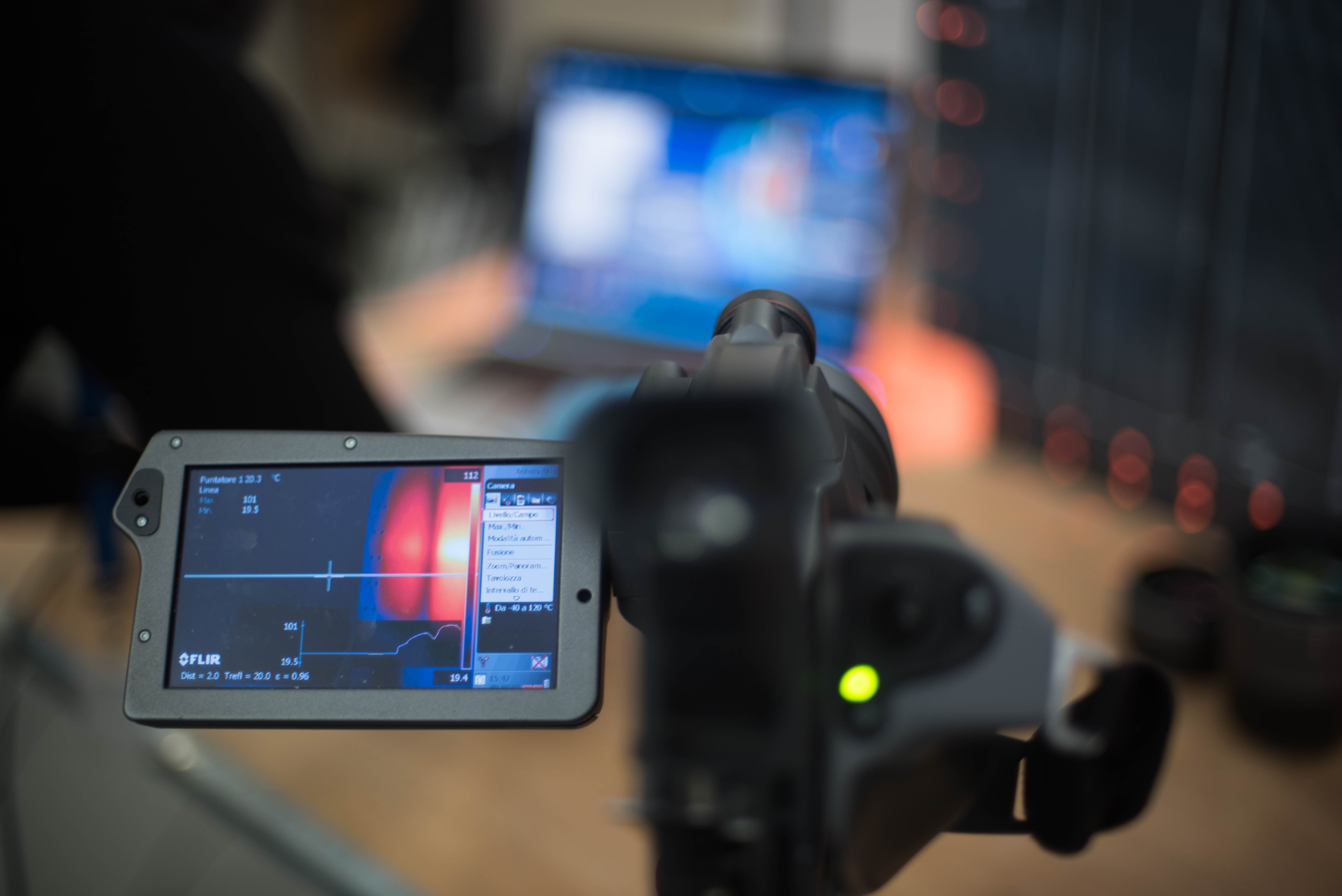
Einer der Hauptbeiträge von CETMA zu SPARE ist die Entwicklung der Infrarot-Thermografie (IRT) zur Inline-Überwachung des progressiven Profilierens. Bei diesem Verfahren werden Rollen aus TP-Verbundlaminat einer Verdichtung und Erwärmung unterzogen, bis die Materialprozesstemperatur, die komplexe Form und die Designdicke erreicht sind. „Allerdings ist darauf zu achten, dass die innersten Lagen ein vollständiges Aufschmelzen der Matrix und eine Verfestigung erfahren“, erklärt Passaro. „Außerdem gibt es ein schmales Temperaturfenster, das das Schmelzen sicherstellt, das Polymer jedoch nicht abbaut. IRT ist eine berührungslose Methode, die die abgestrahlte Wärmeenergie über die Teileoberfläche mit hoher Genauigkeit misst.“
CETMA verwendete Fenster aus Zink-Selenur (ZnSe), um in das geschlossene Gerät zu schauen. Sie sind transparent für IR-Wellen und funktionieren bei Temperaturen bis zu 500°C. Zwei solcher Fenster wurden in der progressiven Rollformanlage des SPARE-Projekts mit darüber aufgehängten IRT-Kameras konstruiert, um einen nahezu senkrechten Blick auf das verarbeitete Material zu ermöglichen. Editierbare Steuerungssoftware ermöglichte die Überwachung, Aufzeichnung und Alarmierung, wenn Werte außerhalb des definierten Zielbereichs lagen.
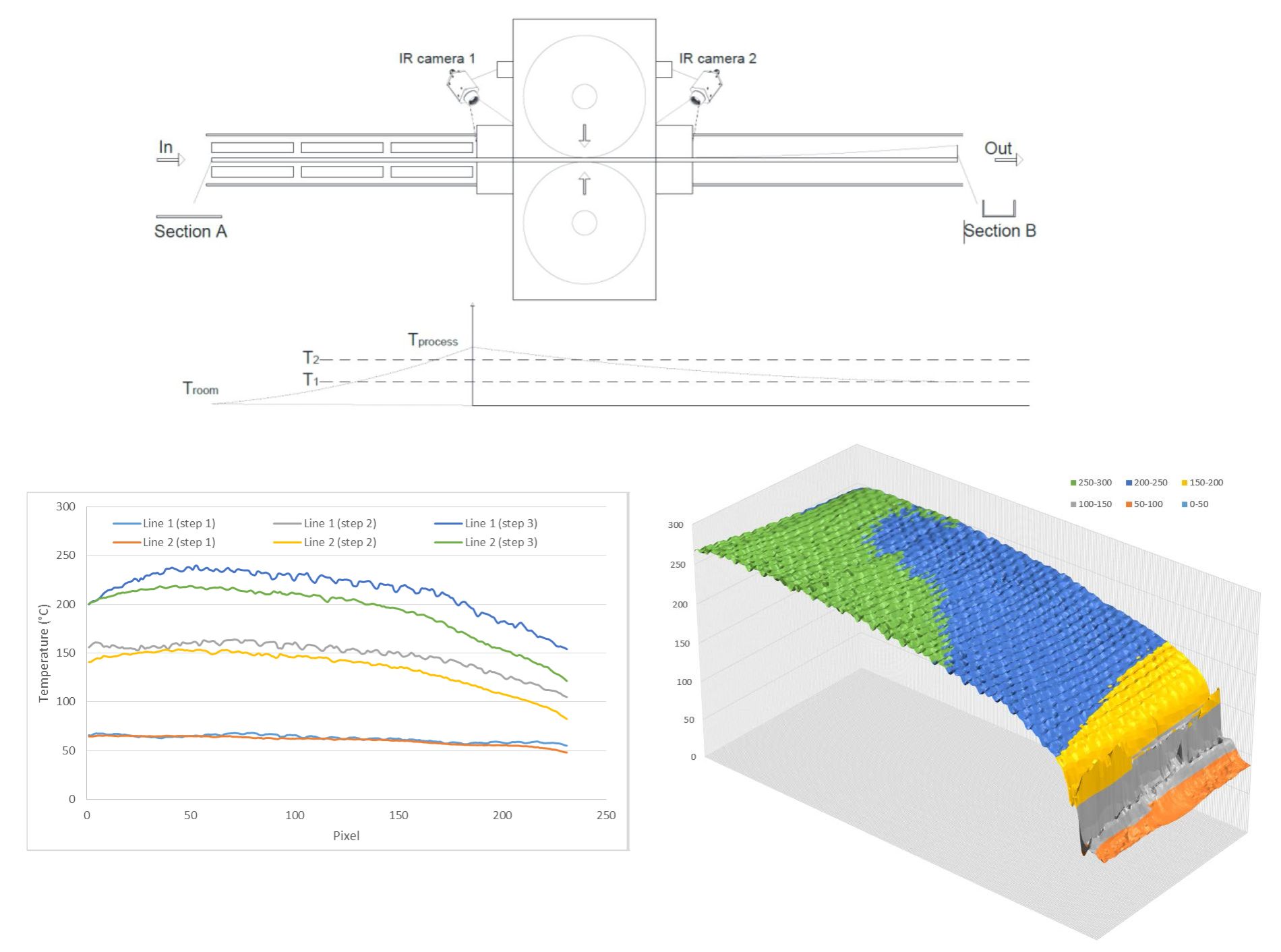
Die Gleichmäßigkeit der Materialtemperatur über den Profilquerschnitt wurde an den beiden Grenzpunkten bewertet – Linie 1 befindet sich in der Nähe des Erwärmungsschritts und Linie 2 befindet sich weiter entlang des Umformprozesses. Jeder wurde in 3 aufeinanderfolgende Schritte unterteilt (Abb. 19):Anfangsphase (Schritt 1), Umformprozess gestartet (Schritt 2) und Umformung mit reduzierter Geschwindigkeit (Schritt 3). IRT zeigte, dass die Temperatur an den Außenkanten des Laminats niedriger war als im mittleren Bereich, was zu einer ungleichmäßigen Erwärmung und mechanischen Eigenschaften führte. Eine 3D-Darstellung der IRT-aufgezeichneten Oberflächentemperaturen (Abb. 20) bot eine visuelle Hilfestellung, um die Temperaturverteilung besser zu verstehen.
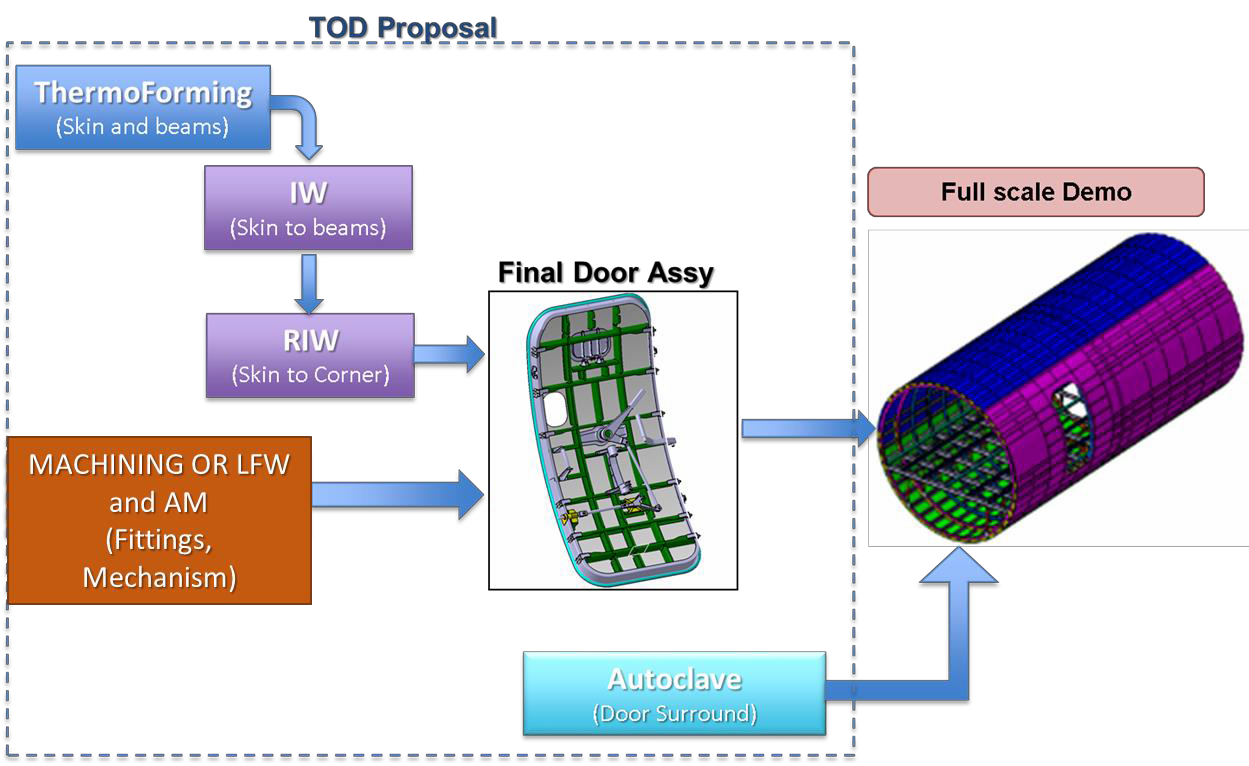
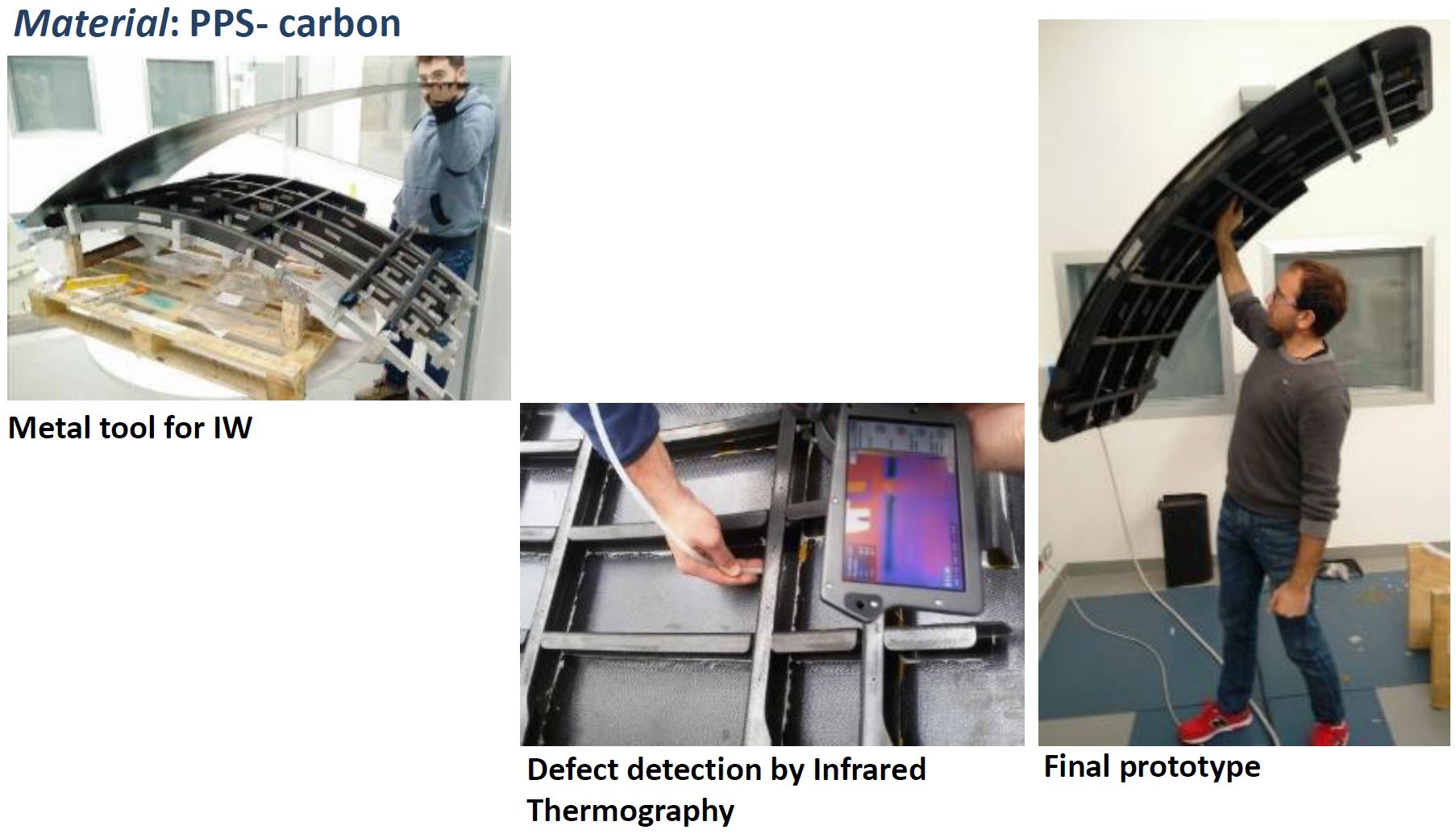
TOD – Thermoplast an Türen (JTI-CS2-2017-CfP07-REG-01-12). TOD zielt darauf ab, eine schnelle Produktion und Montage einer vollwertigen thermoplastischen Verbundtür (einschließlich Rumpfunterkonstruktionen) für ein Regionalflugzeug zu entwickeln und zu validieren. TOD ist Teil der Clean Sky 2 Regional Aircraft IADP (Innovative Aircraft Demonstrator Platform), die die Integration von Technologien, die in der Clean Sky Phase eins entwickelt wurden Green Regional Aircraft ITD (Innovative Technology Demonstrator) zu einem höheren Komplexitäts- und Reifegrad durch zwei fliegende Teststände und drei große integrierte Bodendemonstratoren. Unter der Leitung von Leonardo wird CETMA mit den Projektpartnern The Welding Institute (TWI, Cambridge, Großbritannien) und der Luft- und Raumfahrt Tier 1 und dem Engineering-/Industrialisierungsunternehmen DEMA (Design Manufacturing SpA, Somma Vesuviana, Italien) zusammenarbeiten.
Der vorgeschlagene Ansatz umfasst die Optimierung und Validierung des Thermoformens für Komponentenherstellungs- und Fügeprozesse wie das Induktionsschweißen (IW) und das Widerstandsimplantatschweißen (RIW), die eine Gewichtsreduzierung durch den Wegfall mechanischer Befestigungselemente ermöglichen. TOD wird auch die Industrie 4.0-Automatisierung und Inline-Überwachung vorantreiben, um die Hochgeschwindigkeitsproduktion hochwertiger Teile (Null Fehler) mit robuster Prozesssteuerung zu unterstützen. Zu den erwarteten Vorteilen gehören:
- Mindestens 15 % Gewichtsreduktion
- Reduzierung von Abfall und Ausschuss um 10 % durch Sensoren und Inline-Überwachung
- Bis zu 75 % Energieeinsparung im Vergleich zur Standard-Autoklavenverarbeitung
- Reduzierte wiederkehrende Kosten durch adaptive intelligente Fertigung (erhöhte Flexibilität, geringere Gesamtkosten für Werkzeuge)
- Verbesserte CO2-Emissionen während der Herstellung und leichterer Flugzeugbetrieb.
CETMA ist an zahlreichen weiteren Entwicklungsprojekten beteiligt. Ein Beispiel ist NHYTE (New Hybrid Thermoplastic Composite Aerostructures, hergestellt von Out of Autoclave Continuous Automated Technologies), das darauf abzielt, innovative integrierte Aerostrukturen aus hybriden thermoplastischen Matrixmaterialien mit multifunktionalen Fähigkeiten zu demonstrieren.
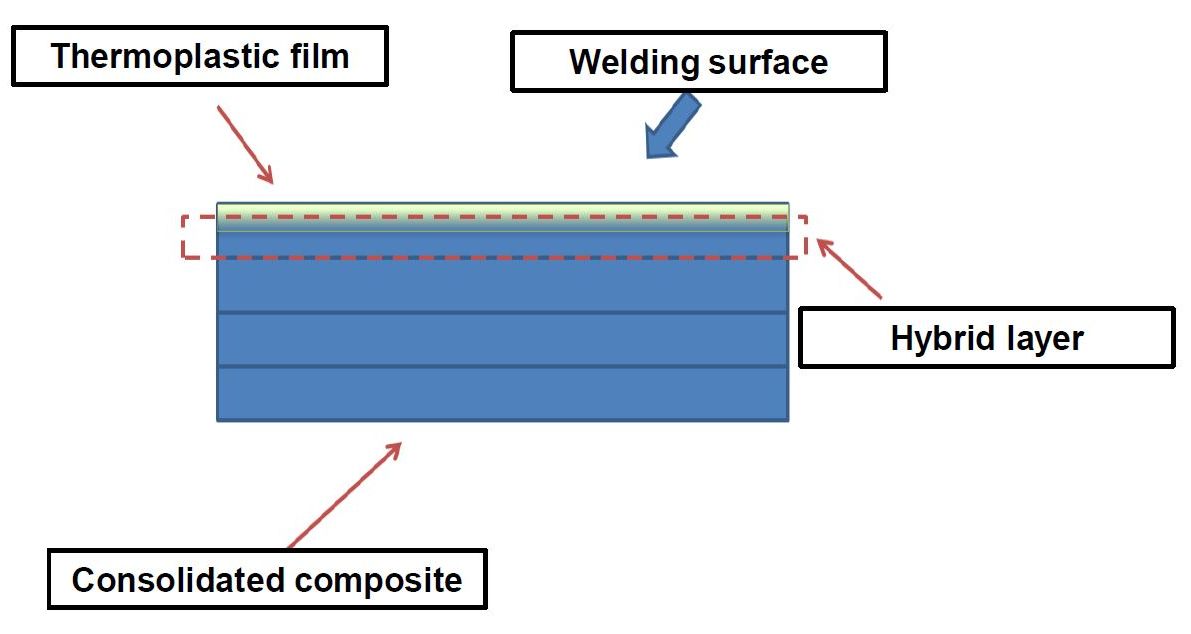
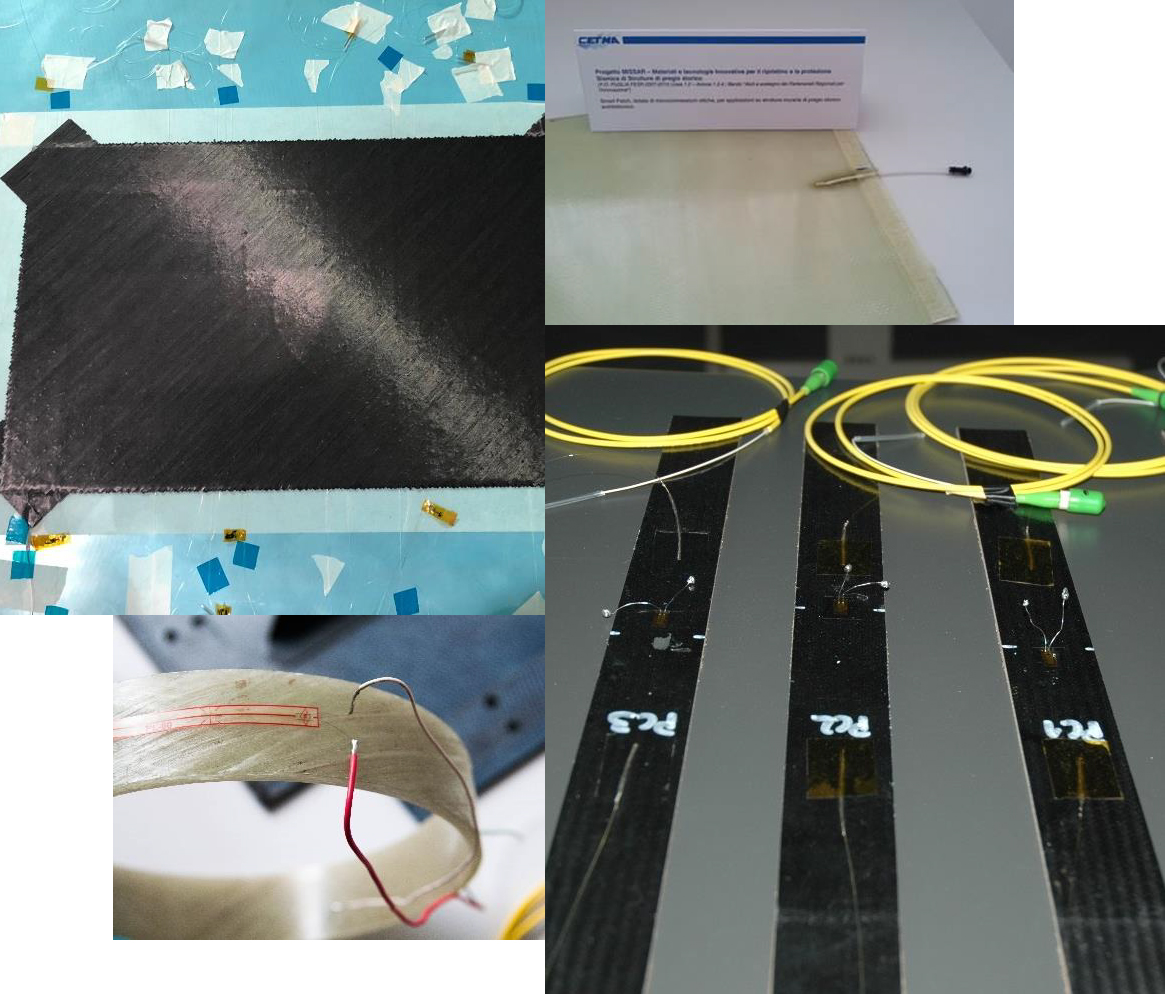
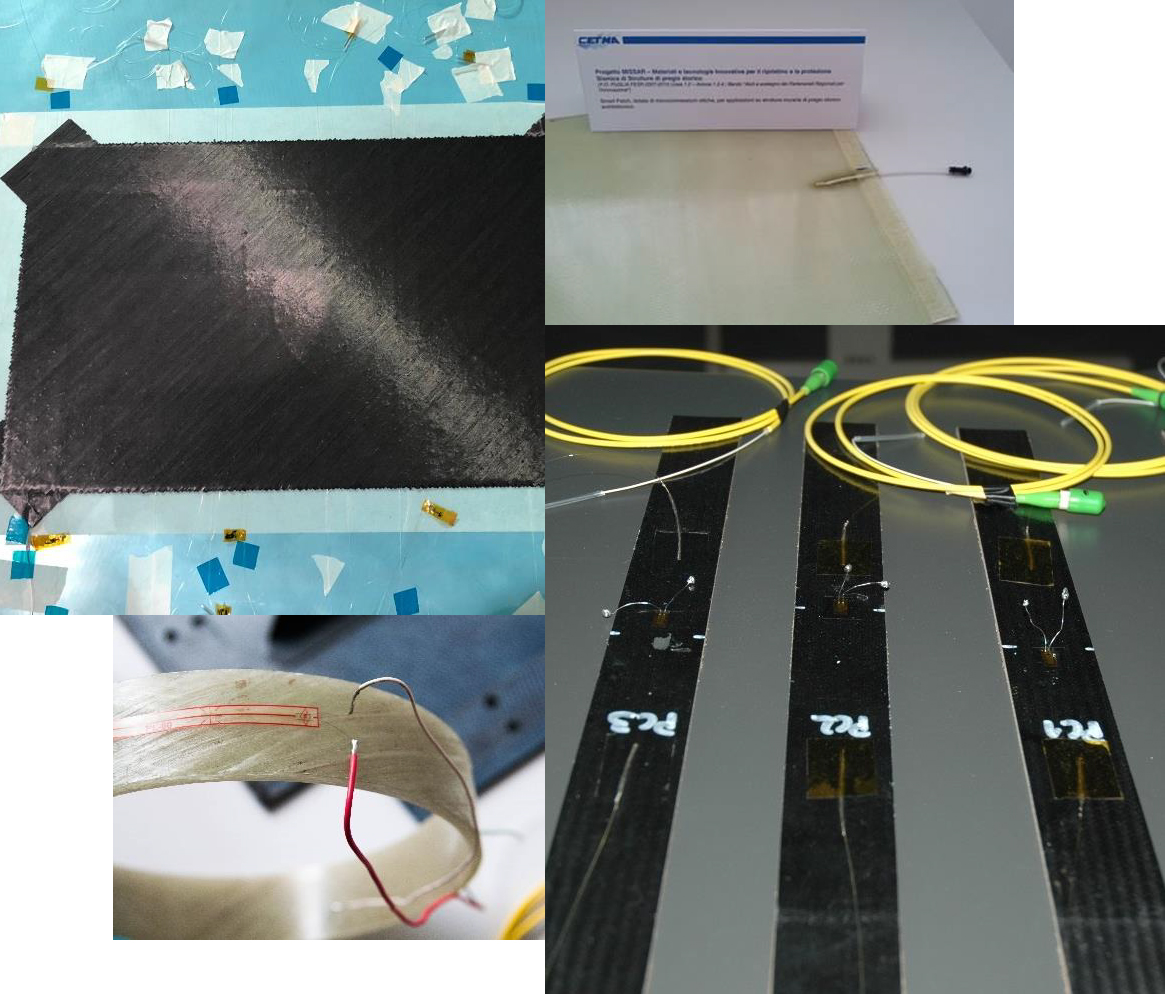
Das im Rahmen des Horizon 2020-Programms finanzierte und von NOVOTECH (Neapel, Italien) geleitete NHYTE begann im September 2018 und sollte im Januar 2020 enden. Das Hochleistungs-Hybridmaterial basiert auf einem kommerziellen Kohlefaser/PEEK-Prepreg mit amorphem PEI Folien, um eine in-situ-Konsolidierung mit automatisierter Faserplatzierung (ISC AFP) und anschließende Montage mit der patentierten Induktionsschweißtechnologie von CETMA zu ermöglichen. CETMA hat eine umfassende Charakterisierungskampagne abgeschlossen, die physikalisch-mechanische und virtuelle Tests des Hybridverbundwerkstoffs und des Induktionsschweißverfahrensaufbaus umfasst.
Recycling von Kohlefaser
Ein weiterer wichtiger Bereich für CETMA ist das Recycling. Der KREIS Das Projekt zielt darauf ab, Prepreg-Abfälle, die bei der Herstellung von Verbundteilen anfallen, zu verwenden, indem es zu einer Formpressmasse recycelt wird, die dann verwendet wird, um Zeheneinsätze für Sicherheitsschuhe zu formen. CETMA wird diesen Sekundärrohstoff charakterisieren und ein numerisches Modell entwickeln, um die strukturelle Leistung der Schuheinlagen vorherzusagen. Dieses Modell hilft bei der Analyse und Überprüfung des Aufprallverhaltens, um die Sicherheitsvorschriften zu erfüllen, wobei die Ergebnisse verwendet werden, um das Design der Zeheneinsätze zu verfeinern und abzuschließen. Das italienische Projektteam umfasst Base Protection (Barletta), den Hersteller von Composite-Motorsport-/Automobilteilen HP Composites (Ascoli Piceno), den Maschinen- und Produktionslinienspezialisten Elks Group (Ascoli Piceno) und Petroceramics (Stezzano).
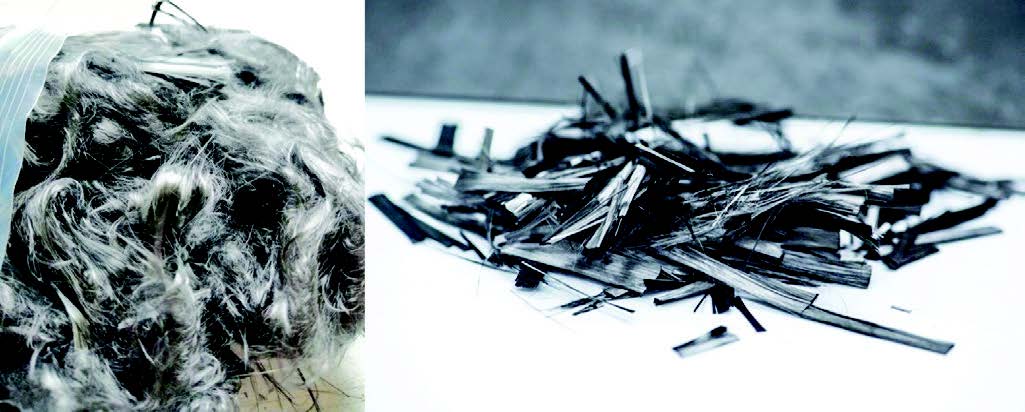
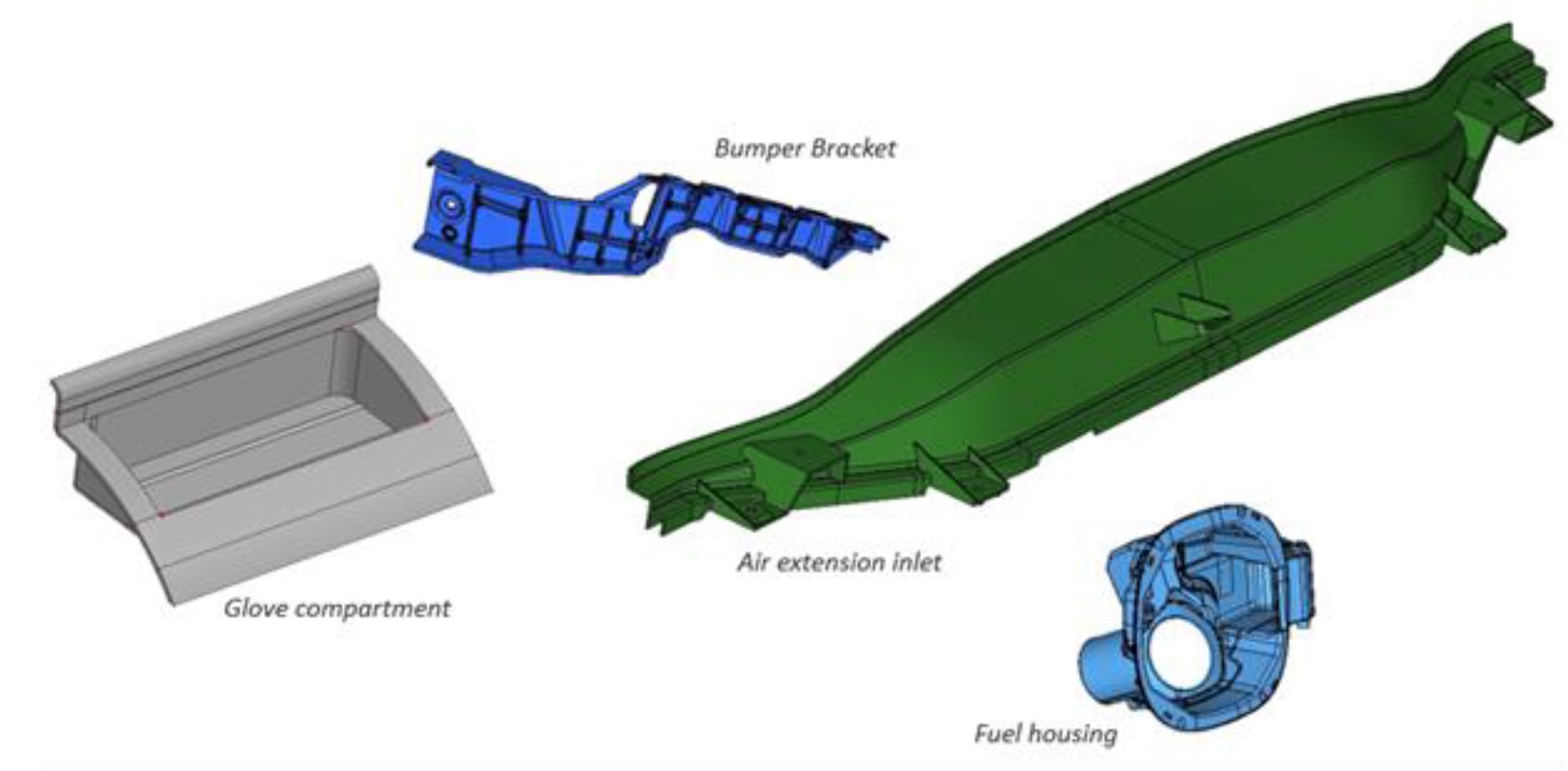
Die bisher vielleicht größte Investition von CETMA in das Recycling erfolgte über den REVALUE Projekt mit dem Ziel, recycelte Kohlenstofffasern für hochwertige Verbundwerkstoffe zu entwickeln. Das vom European Institute of Innovation &Technology (EIT, Budapest, Ungarn) geförderte Projekt REVALUE hat zum Ziel, recycelte Carbonfasern (RCF) des führenden Herstellers ELG Carbon Fiber (Coseley, UK) mittels Pyrolyse zu verwenden und mit neue und recycelte thermoplastische Polymere als Ersatz für die derzeitigen Materialien, die von Centro Ricerche Fiat (CRF, Turin, Italien) für die Herstellung ausgewählter Automobilkomponenten verwendet werden.
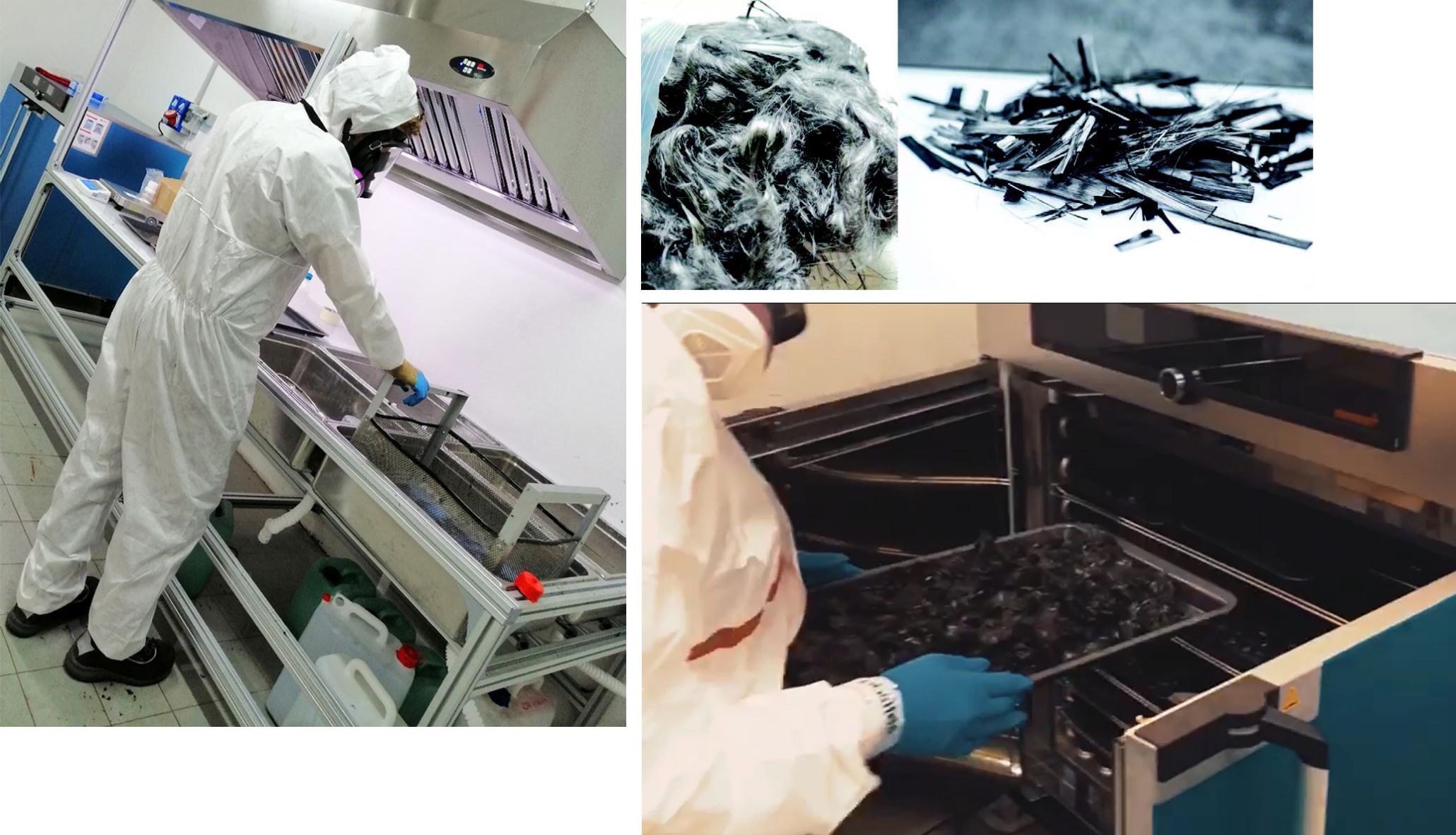
Wie jedoch im JEC Composites-Magazin vom Januar bis Februar 2020 festgestellt wurde Artikel „Neue Schlichteformulierung für recycelte Kohlefasern“ von Alessandra Passaro et. al., durch Pyrolyse hergestelltes RCF hat keine Schlichte, wodurch die spröden Fasern anfällig für häufiges Reißen während der Handhabung sowie für die Trennung der Faserkabel in Filamente sind, was zu einer verschlungenen, "flaumigen" Form mit geringer Schüttdichte führt. Im Rahmen von REVALUE hat CETMA eine spezielle Schlichteformulierung für RCF entwickelt, die mit neuem oder recyceltem Polypropylen (PP) und PA6 kompatibel ist. Anschließend wurde die Schlichtefähigkeit bewertet, um die RCF-Verarbeitbarkeit zu verbessern und die Grenzfläche mit den ausgewählten thermoplastischen Matrizen zu erhöhen.
Dazu hat CETMA eine Pilotanlage zur Klassierung von RCF entwickelt, die in der Lage ist, die Klassierung in Kilogramm-Mengen aufzubringen und gleichzeitig den Einfluss der Hauptparameter auf den Abscheidungsprozess zu bewerten. Die Anlage besteht aus drei Hauptstationen:Behandlung der Schlichte und Waschen der Fasern; Handhabung der trockenen Fasern vor und nach der Behandlung; und Ofentrocknung der Fasern. Vier Kilogramm RCF können pro Tag in einem kontinuierlichen Zyklus behandelt werden.
Die geschlichteten RCF von CETMA wurden dann vom französischen Forschungszentrum CEA und dem französischen Compounder SUEZ verwendet, um eine Formmasse aus neuen und recycelten thermoplastischen Polymeren herzustellen. Die physikalisch-chemische Charakterisierung der Verbindungen wurde abgeschlossen und die Fähigkeit der CETMA-Schlichte zur Verbesserung der mechanischen Leistung des endgültigen Verbundwerkstoffs wurde überprüft.
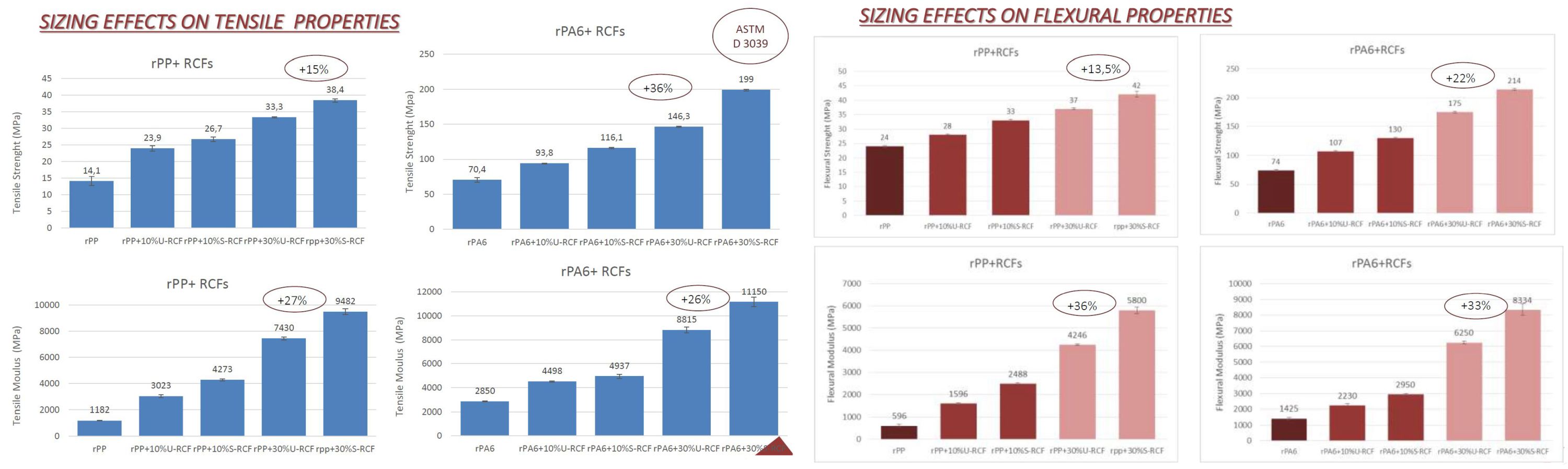
Mit den innovativen RCF-Formmassen wurden anschließend halbstrukturierte Automobilbauteile spritzgegossen, die derzeit aus glasfaserverstärktem PP oder PA6 bestehen. Neben dem offensichtlichen Vorteil beim Recycling und der Wiederverwendung von Materialien wurden auch die Reduzierung des Fahrzeuggewichts, des Kraftstoffverbrauchs und der CO2-Emissionen nachgewiesen.
Außerhalb von REVALUE hat CETMA auch die Schlichte für RCF in mehreren Verbundwerkstoffprozessen, einschließlich Formpressen, Vakuuminfusion und RTM, weiterentwickelt und bewertet und in allen Fällen verbesserte Eigenschaften gezeigt.
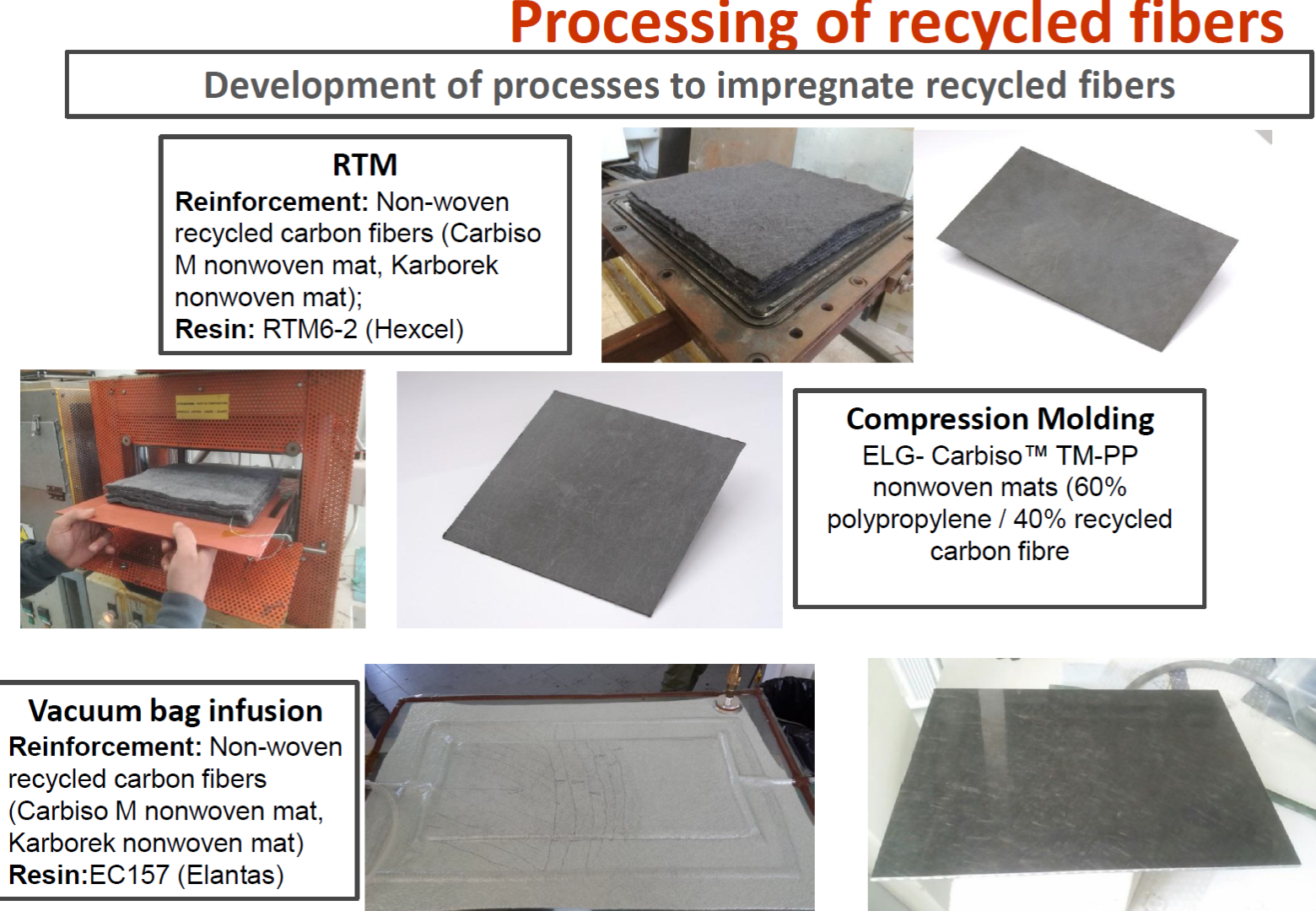
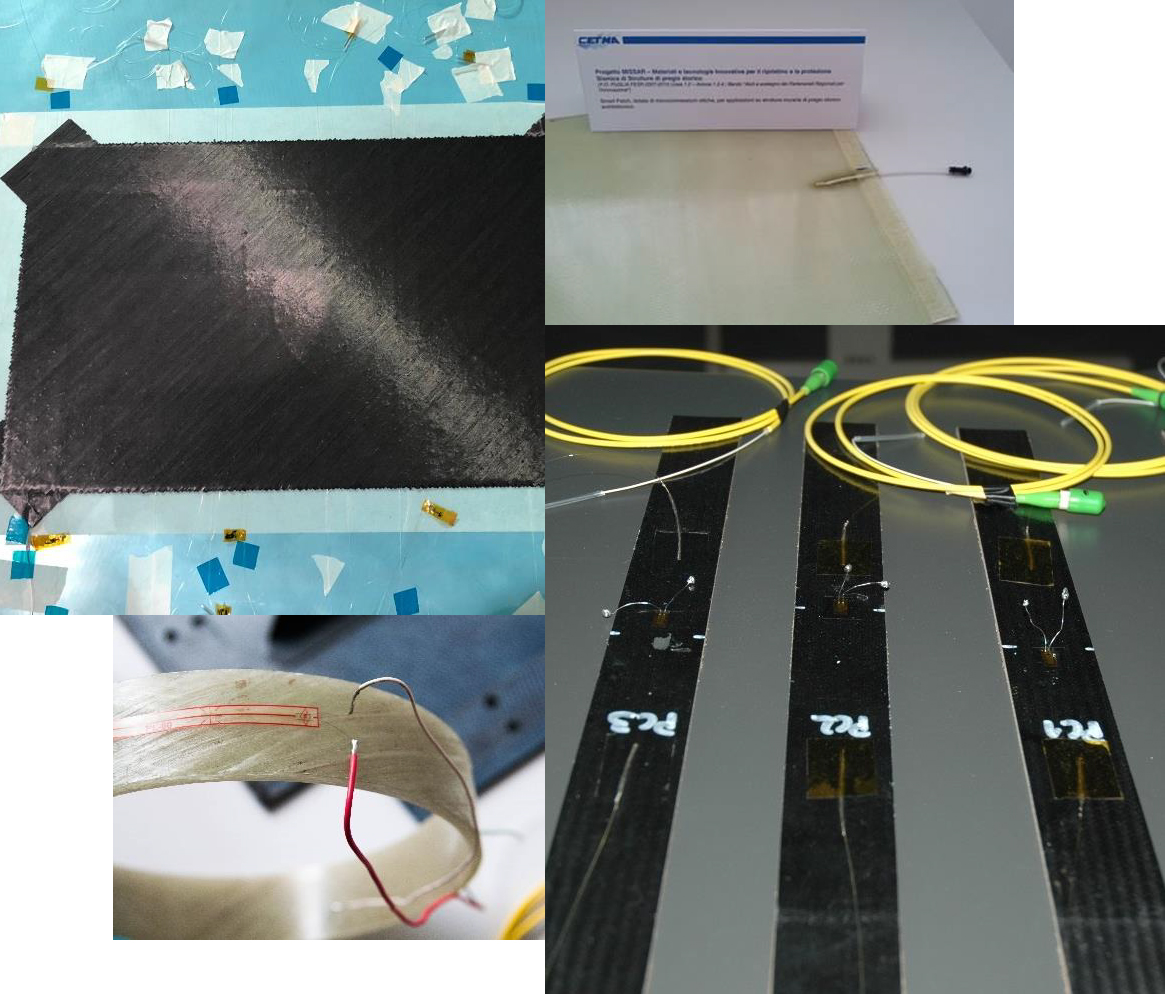
Structural Health Monitoring (SHM)
Dieser letzte Schlüsselbereich der Verbundwerkstoffaktivitäten für CETMA wird auch in der Industrie immer stärker betont. „Wir haben langjährige Erfahrung mit der Anwendung von SHM für Bau- und Bauanwendungen“, bemerkt Passaro. „Und wir haben auch viel mit SHM im Bereich Composites gearbeitet. Wir wissen, dass dies für zukünftige Anwendungen wichtig sein wird und sind daran interessiert, weiterhin mit Verbundwerkstoffherstellern und der Industrie zusammenzuarbeiten, um diese Technologie voranzutreiben.“
Harz
- Anpassung von Ultraschallsensoren für die Optimierung und Steuerung von Verbundwerkstoffprozessen
- Wiederaufbereitbare, reparierbare und recycelbare Epoxidharze für Verbundwerkstoffe
- Composites One und IACMI veranstalten zweitägigen Workshop
- Messung der Temperatur in Verbundwerkstoffen und Bondlines
- TPAC und TPRC entwickeln Recyclingprozess für thermoplastische Verbundwerkstoffe
- PES-Additiv erhöht die Bruch- und Mikrorissbeständigkeit in Epoxidverbundwerkstoffen
- SABIC und Nottingham Spirk arbeiten zusammen, um die Innovationsentwicklung zu beschleunigen
- Im Dienste der Composites-Welt in Israel und den USA
- Herausforderungen beim Schneiden:Composites mit gemischter Matrix und faserverstärkte Verbundwerkstoffe
- ABB Robotics:Technologieinnovation und Robotik-F&E