Kombinieren von Kunststoffen und Verbundwerkstoffen für Klasse-A-Teile ohne Werkzeug
Die Herstellung von Verbundteilen mit einem Klasse-A-Finish ist nicht der Heilige Gral – es gibt viele Unternehmen, die dies routinemäßig tun. Allerdings mit Harzinfusion ohne teure Werkzeuge oder Gelcoats und mit einer Rate von einem Teil pro Stunde? Nun, das ist etwas Einzigartiges.
Von Kunststoffen zu Verbundwerkstoffen
Plastics Unlimited wurde vor 25 Jahren von Terry und Nancy Kieffer gegründet, erklärt ihr Sohn Dakota Kieffer, Vertriebs- und Marketingleiter des Unternehmens. „Sie waren Landwirte in Iowa und suchten nach einer neuen und wachsenden Industrie“, erklärt er. „Sie dachten, Kunststoff wäre besser als Schweißen oder Holzbearbeitung und wollten nicht mit ihren Nachbarn konkurrieren. Sie haben sich Spritzguss, Rotationsguss und Recycling von Kunststoffen angeschaut, sind dann aber auf Thermoformen gestoßen und haben es wirklich verstanden.“ (Thermoformen verwendet Hitze und Vakuum/Druck, um thermoplastische Platten zu Formteilen zu formen.)
Dann kamen Kieffers Eltern in Kontakt mit einem Unternehmen, das glasfaserverstärkte Kunststoffteile (GFK) herstellt. „Sie sahen, wie stark FRP war, aber auch, dass es einen langen, mehrstufigen Prozess erforderte, ungefähr vier Stunden pro Teil – also wurden nur zwei Teile pro Tag hergestellt“, fährt er fort. „Im Vergleich zu unserer Produktion in Kunststoff fanden sie das zu langsam. Wir haben alle 2-6 Minuten Teile gedreht – vielleicht sogar 5-6 Teile auf einmal produziert – also Tausende von Teilen pro Tag.“ Um die Lücke zu schließen, hatte Kieffers Vater die Idee, eine thermogeformte Kunststoffschale als Werkzeug zu verwenden .
Das Ergebnis ist ein werkzeugloser Herstellungsprozess für Verbundteile, den Plastics Unlimited als Toolless Engineered Composite (TEC) bezeichnet. „Es entfernt den Gelcoat und Werkzeugfreigabeschritte“, sagt Kieffer. „Außerdem können Sie beim Thermoformen die Klasse-A-Oberfläche inspizieren und sich vergewissern, dass sie perfekt ist.“ Mit anderen Worten, die Oberfläche der Klasse A ist nicht unter einem Verbundlaminat verborgen. „Wir brauchten nur ein einziges Thermoformwerkzeug, und für unsere Kunden aus Kunststoffteilen war der Prozess dennoch sinnvoll.“
Patentierter Verbundprozess
Kieffer stellt fest, dass ein Verbundstoff zwei Materialien kombiniert, um ein besseres Material zu ergeben als jeder einzelne Bestandteil. „Wir kombinieren zwei verschiedene Arten von Materialien und zwei verschiedene Verfahren, um ein besseres Produkt herzustellen.“ Insbesondere ein Produkt, das aus Kunststoff, Harz und Glasfaser besteht und eine einzigartige Kombination von Vorteilen bietet. „Kunststoffe haben eine viel bessere Schlagzähigkeit als Gelcoats“, erklärt er. „Außerdem ist es möglich, beliebige Texturen oder Designs auf den Kunststoff zu drucken, zum Beispiel ein Camouflage-Muster. Die Kunststoffe bieten auch eine große Bildtiefe ohne anschließendes Polieren, wodurch sekundäre Nachbearbeitungsvorgänge entfallen.“
Im Vergleich zum Spritzen von Schnittfasern in einem offenen Formverfahren ermöglicht diese patentierte Technologie einen höheren Fasergehalt, eine höhere Qualität und keine/wenig flüchtigen organischen Verbindungen (VOCs). Er weist darauf hin, dass das Aufsprühen von gehackten Fasern auf Kunststoffe für Wannen und Spas nicht patentiert ist. „Wir verwenden immer Vakuuminfusion, um das FRP zum Teil des Produkts zu machen“, sagt Kieffer und fügt hinzu:„Unsere Teile haben eine glatte Oberfläche, also sind wir eher ein leichtes RTM mit Dichtungsplatten. Wir bringen es immer auf das nächste Level. Kunden kommen mit einem Problem zu uns und wir versuchen eine Lösung zu finden, die ihren Bedürfnissen entspricht. Wir sind sehr innovativ und patentieren unsere Neuentwicklungen.“
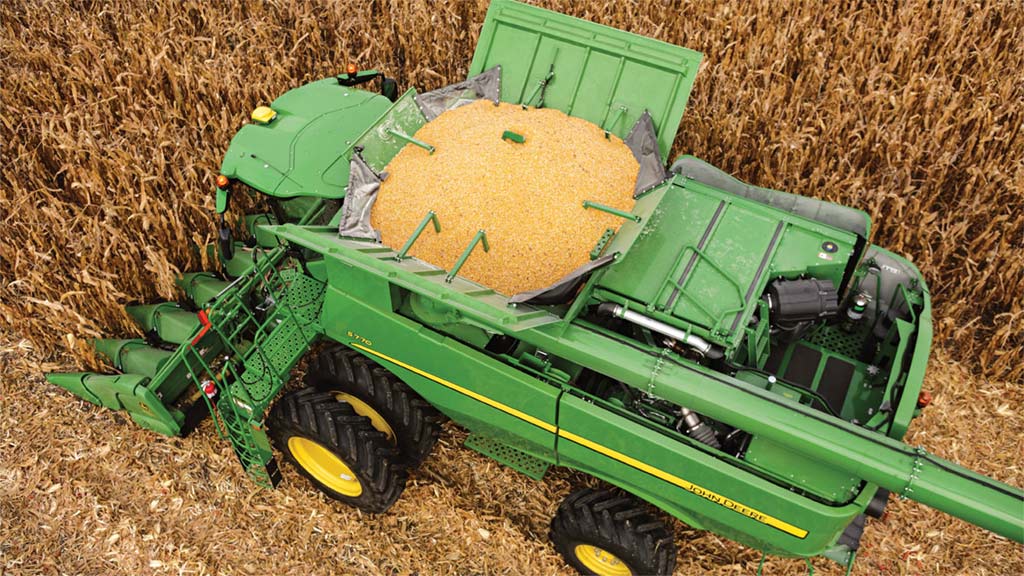
Beispielteile
Eines der Teile, die Plastics Unlimited mit diesem Verfahren herstellt, ist eine Korntankerweiterung für John Deere-Mähdrescher von Deere &Company (Moline, Illinois, USA). „Das ist der oberste Teil des Mähdreschers, also offen, wo das Getreide sitzt“, erklärt Kieffer. „Im Vergleich zum Original-Stahltank ist unser haltbarer. Wir machen es innen glatt und außen John Deere Grün mit schwarzen Einsätzen an den Ecken. Es ist die größte verfügbare Korntankerweiterung und kann flach zusammengeklappt werden. Es ist im Vergleich zu unseren Mitbewerbern ein technisch ausgereifteres Produkt, bei dem Schaumstoff und Rippen hinzugefügt wurden, um die Steifigkeit zu erhöhen.“ Dazu bedarf es einer teilweisen Stahlarmierung, die tatsächlich eingegossen wird, sagt Kieffer, „nicht sekundär verklebt“.
Diese Kombination von Materialien und Verfahren verleiht dem fertigen Teil eine hohe Zähigkeit. „Wir haben Videos, in denen Betonblöcke auf diese Teile fallen“, sagt Kieffer. Er sagt, dass durch das Formen von Stahlbefestigungen die Auszugsfestigkeit 4-5 mal höher ist als die, die mit einer sekundären Verklebung mit Methylmethacrylat-Klebstoffen nach Industriestandard erreicht wird.
Plastics Unlimited kann bis zu 2.500 dieser Teile pro Monat herstellen, wobei einige der Platten 1,5 mal 2,70 Meter groß sind. „Dies würde teure Werkzeuge erfordern, wenn sie nicht mit unserer Methode hergestellt würden“, sagt Kieffer und stellt fest, dass TEC für ziemlich große Teile verwendet werden kann – bis zu 2,40 x 2,70 m. „Unsere Teile können mehr Form und Geometrie haben als Stahl. Das ist unseren Kunden wichtig, weil sie sich dadurch über das Styling differenzieren können. Unsere UV-Beständigkeit ist auch besser als die der meisten Gelcoats.“
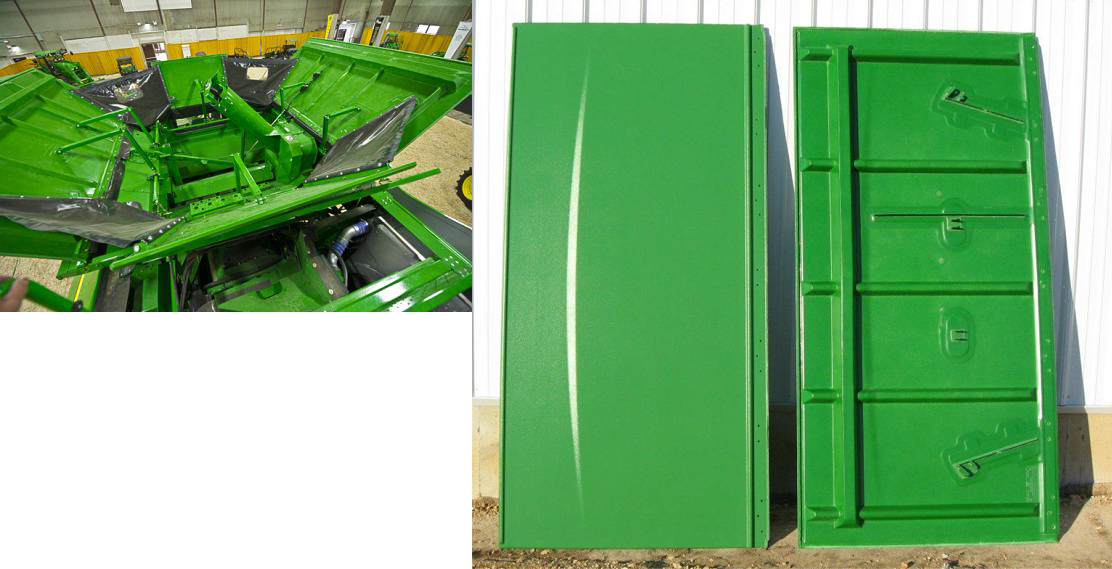
Plastics Unlimited liefert Teile für eine Reihe von Unternehmen, darunter Harley-Davidson und Gehl Teleskop-Hebebühnen. „Wir fertigen auch Soft-Touch-Teile, die wie Leder aussehen und sich anfühlen“, sagt Kieffer. Das Unternehmen hat auch LKW-Komponenten für Navistar und Teile für Wohnmobile (RV) für Winnebago hergestellt. „Wir bevorzugen die Massenproduktion, von 100.000 Teilen pro Jahr bis zu einigen Hundert.“
Kieffer erkennt an, dass Long Fiber Injection (LFI) und Resin Injection Moulding (RIM) wettbewerbsfähige Verfahren sind, „aber die Teile sind nicht so strukturell wie das, was wir tun. Ein Korntank eines Mähdreschers fasst beispielsweise 400 Scheffel, was 10 Tonnen Kraft ausübt. RIM-Teile, die nicht stark verstärkt sind, können diese Art von Lastanforderung einfach nicht erfüllen und RIM-Werkzeuge sind sehr teuer.“
Weiterführende Entwicklung
„Wir machen viel F&E-Arbeit mit unseren Kunden“, sagt Kieffer. „Wir erforschen verschiedene Harze, Schäume, Laminate, Verstärkungsschichten und Oberflächen und zeigen ihnen dann Prototypen, damit sie sehr schnell Tests durchführen können. Wir werden versuchen, die Herstellbarkeit des Teils zu verbessern, um Kosten zu senken und die Leistung zu verbessern sowie die verschiedenen Betriebsanforderungen wie extreme heiße und kalte Temperaturen und Stöße zu erfüllen.“
Plastics Unlimited hat eine Produktionsfläche von 100.000 Quadratfuß und 75 Mitarbeiter, darunter ein Team von drei Ingenieuren. Seine 5-Achsen-Thermwood-CNC-Maschine ermöglicht die interne Werkzeugherstellung und auch schnelle Prototypenerstellung, letzteres ist für Kunden wichtig, um die Entwicklungszeiten zu verkürzen.
„Wir arbeiten auch mit Nahverkehrs- und Luft- und Raumfahrtunternehmen zusammen“, fährt er fort. „Viele U-Bahn-Innenräume sind derzeit aus GFK mit Gelcoat plus dahinterliegender Aluminiumstruktur. Sie brauchen ein leichtes, aber auch ein kosmetisches Oberflächenfinish. Wir betrachten ein breites Anwendungsspektrum, darunter Medizin, Elektrotechnik und Bauwesen.“
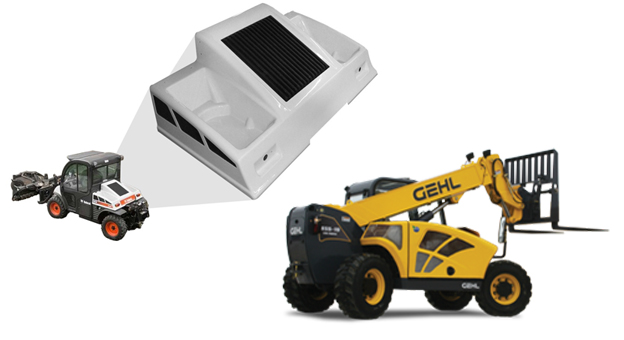
Darüber hinaus beschäftigt sich das Unternehmen mit dem Thermoformen von kohlenstofffaserverstärkten Kunststoffen (CFK). „Wir haben Tepex- und Polystrand-Materialien geformt und arbeiten an verschiedenen Entwicklungen mit einem medizinischen Kunden“, sagt Kieffer. „Wir können High-End-Kunststoffmaterialien wie Kydex verwenden und für die Luft- und Raumfahrt mit CF/Epoxy versehen oder Materialien wie Polyurethan, Polycarbonat und ABS, die eine schöne äußere Oberfläche bieten und kostengünstig sind. Hinter diesen letzteren Kunststoffen können wir glasfaserverstärkte Polyester-, Vinylester- oder Epoxidlaminate verwenden.“
Plastics Unlimited operiert an der Schnittstelle von Kunststoffen, Metallen und Verbundwerkstoffen, sagt Kieffer. „Unsere Teile sind in der Regel 30 bis 40 Prozent leichter als Stahl. Aber wir stellen fest, dass der Markt noch einiges an Aufklärung darüber braucht, was Verbundwerkstoffe sind und was sie können.“ Dennoch sieht das Unternehmen viel Potenzial für zukünftiges Wachstum. „Nicht alle Materialien funktionieren zusammen und vor allem nicht alle Harze funktionieren mit allen Kunststoffen“, bemerkt er. „Wir haben im Laufe der Jahre so viele Tests und Entwicklungen durchgeführt, dass wir die Landschaft und die Möglichkeiten sehr gut verstehen. Wir verfügen über ein einzigartiges Know-how und bieten ein einzigartiges Spektrum möglicher Lösungen.“
Harz
- Kubernetes in Azure:Tools und Tipps für den Erfolg
- Programmiermuster und Tools für Cloud Computing
- „Smooth-Touch“-TPEs für neue Verpackungs- und Teiledesignanforderungen
- Roboterarmteile für die Pick-and-Place-Automatisierung
- Anpassung von Ultraschallsensoren für die Optimierung und Steuerung von Verbundwerkstoffprozessen
- Wiederaufbereitbare, reparierbare und recycelbare Epoxidharze für Verbundwerkstoffe
- Victrex- und Bond-Partner für den 3D-Druck von PAEK-Teilen
- 20 grundlegende Schweißwerkzeuge und -ausrüstung für Anfänger
- Veredelungsverfahren für Teile und Komponenten
- TÄGLICHE UND REGELMÄSSIGE WARTUNG FÜR FÖRDERER UND TEILE