Einsatz mobiler Suszeptoren für innovatives thermoplastisches Induktionsschweißen
Die Institut de Soudure Group (IS Groupe, Villepinte, Frankreich) – wörtlich „das Schweißinstitut“ Frankreichs – verfügt über mehr als 100 Jahre Erfahrung im Schweißen von Metallen und etabliert sich heute als führend beim Schweißen thermoplastischer Verbundwerkstoffe. Wie in CW berichtet 2018 Feature "Welding thermoplastischer Verbundwerkstoffe", IS Groupe und ihre Verbundwerkstoffmarke Composite Integrity entwickelte im Demonstrationsprojekt „Arches TP“ mit dem Airbus Tier-1-Zulieferer STELIA Aerospace (Toulouse, Frankreich) das Verfahren „Dynamisches Induktionsschweißen“ zum Verbinden von Carbonfaser (CF)/Polyetherketonketon (PEKK) unidirektionalen (UD) Tape-Stringern und Rumpfschalen , das auf der Paris Air Show 2017 vorgestellt wurde.
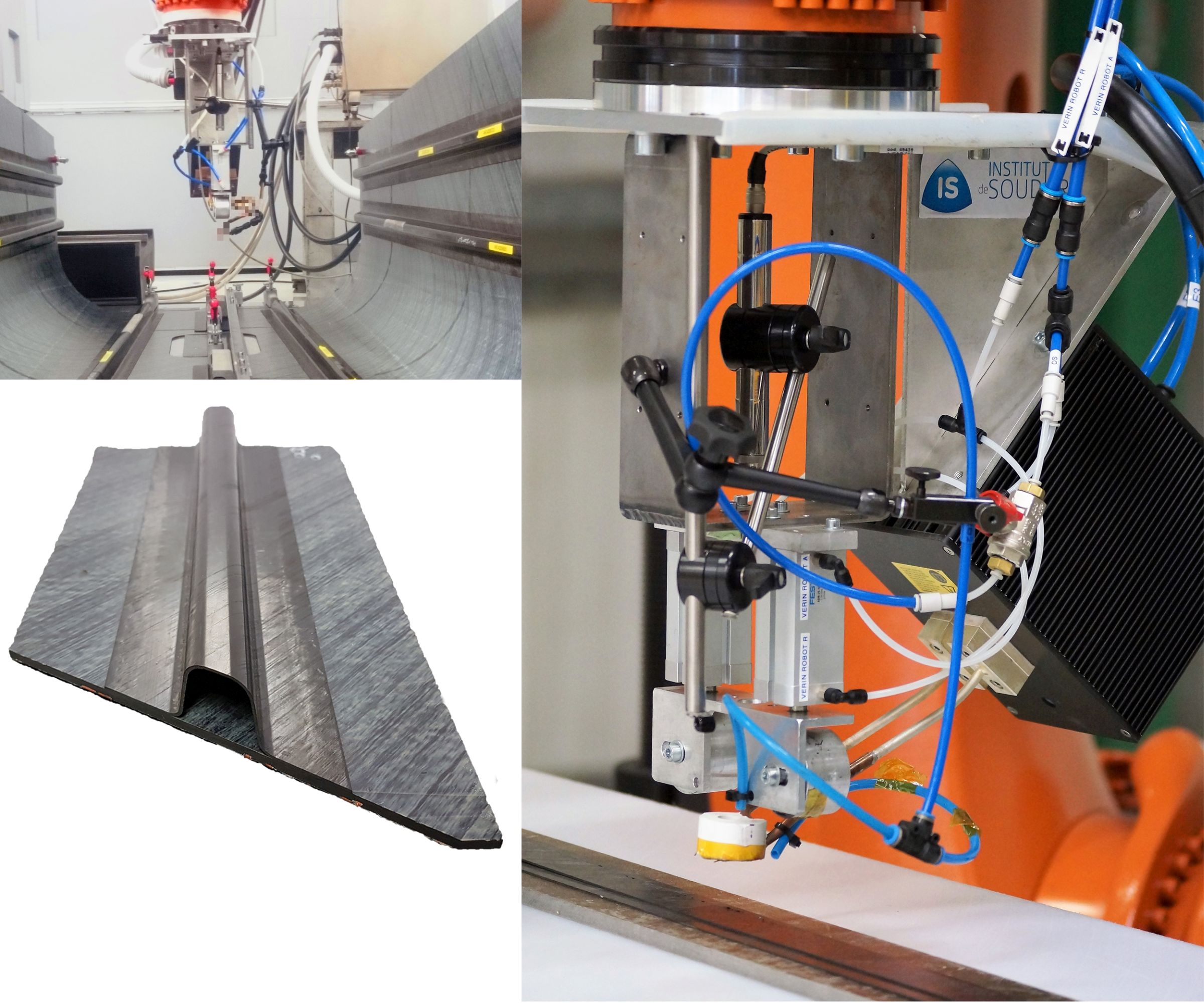
„Dies war der Beginn unserer Entwicklung mit dem Induktionsschweißen für Flugzeugstrukturteile“, erklärt Jérôme Raynal, Aeronautics &Composites Director bei IS Groupe. „Der von uns entwickelte dynamische Induktionsschweißprozess war zwar erfolgreich, hatte jedoch einige Einschränkungen in Bezug auf die Leistung im Radius des geklebten Stringers und die globale Erwärmung der Platte, da an der Schnittstelle kein Suszeptor vorhanden ist.“
Ein Suszeptor ist ein Material, das zwischen den beiden Fügeflächen einer geschweißten thermoplastischen Verbundverbindung platziert wird und durch die Induktionsspule im Schweißkopf erhitzt wird. Der Suszeptor kann elektrisch leitend zum Widerstandsheizen oder magnetisch zum Hystereseheizen sein, wodurch die Matrix an der Schweißgrenzfläche geschmolzen wird, die gleichzeitig zusammengepresst wird, um eine schmelzverbundene Verbindung mit sehr hoher Festigkeit zu erzeugen. Wie in der Veröffentlichung vom Januar 2000 „Design of a Resistive Susceptor for Uniform Heating While Induction Bonding of Composites“ von Bruce Fink, Shridhar Yarlagadda und John W. (Jack) Gillespie erläutert, waren Suszeptoren, die in induktionsgeschweißten thermoplastischen Verbundwerkstoffen verwendet wurden, ursprünglich ein Metall Sieb oder Netz, manchmal mit Polymer imprägniert.
IS Groupe glaubte, dass die anfänglichen Probleme, auf die es stieß, durch weitere Entwicklung gelöst werden könnten. „Wir haben eine neue Runde der internen Reflexion begonnen“, sagt Raynal. Dazu gehörten Gespräche mit dem thermoplastischen (TP) Materiallieferanten Arkema (Colombes, Frankreich), die eine Entwicklungspartnerschaft eingegangen sind. „Wir haben jetzt gemeinsam mit Arkema eine neue Technologie namens Innovative Solution for Welding (ISW) entwickelt und patentiert“, fügt Raynal hinzu.
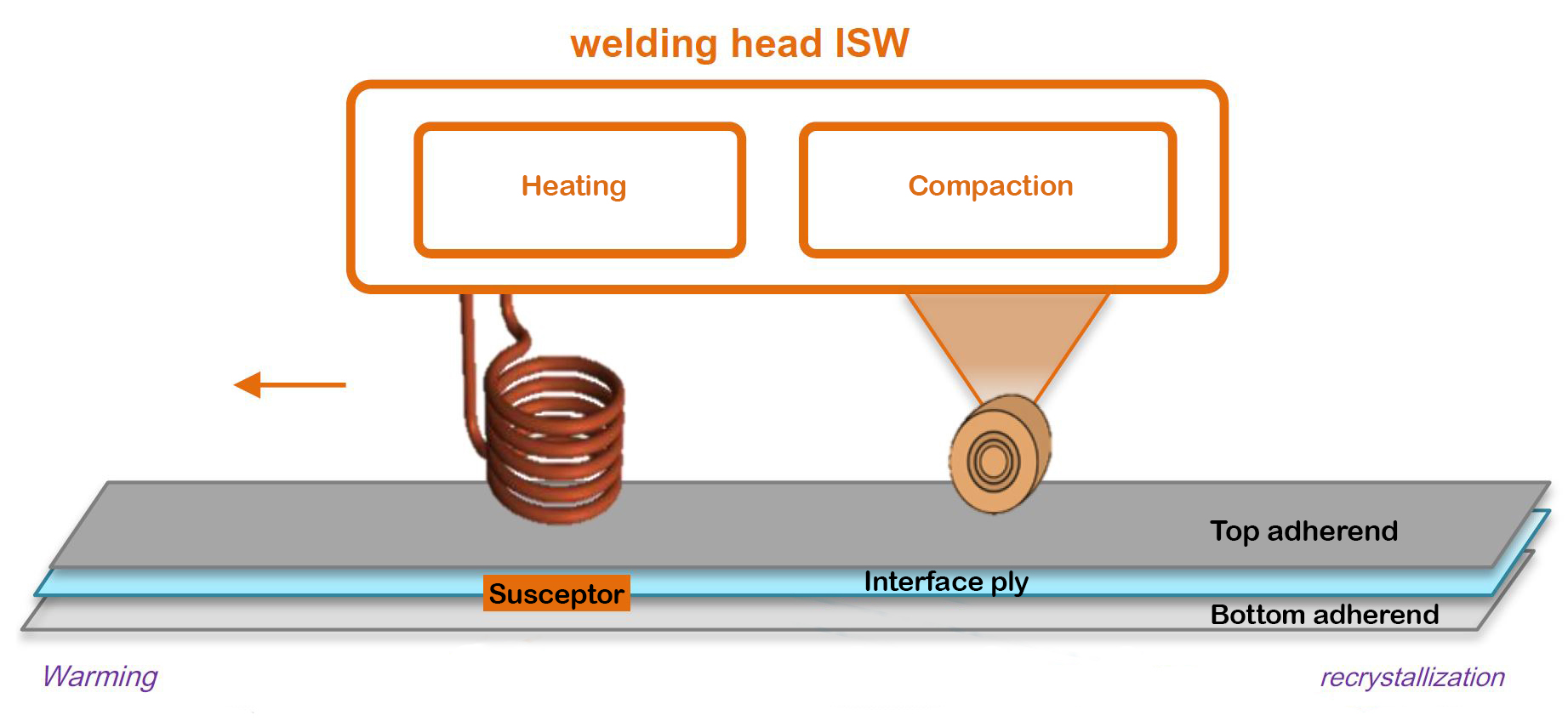
ISW-Grundlagen
„Die Basis von ISW besteht darin, einen Suszeptor zum Erwärmen der Schweißschnittstelle zu verwenden, aber dies ist ein mobiler Suszeptor, der mit dem Schweißkopf verbunden ist“, erklärt Raynal. „Der Suszeptor ermöglicht es uns, die Heizzone perfekt an der Schweißnaht zu lokalisieren, aber der Schweißkopf mit Suszeptor bewegt sich, sodass nichts in der Grenzfläche zurückbleibt, was die Eigenschaften der Schweißstruktur stört.“ In frühen Iterationen des Induktionsschweißens wurden Metallgitter-Suszeptoren in der Schweißnaht belassen, dies wurde jedoch als unerwünscht angesehen. Neuere Techniken sind in der Lage, Suszeptoren zu eliminieren, da die Kohlefaser in üblichen Laminaten für die Luft- und Raumfahrt elektrisch leitfähig ist. Dies hat auch die Verwendung von Kohlefasermaterialien als Suszeptoren ermöglicht.
Ein weiterer Teil der ISW-Lösung besteht darin, eine reine TP-Matrix oder eine Lage mit geringem Faservolumen an der Schweißgrenzfläche zu verwenden, um den Harzfluss zu verbessern. Die Schmelztemperatur und Viskosität dieser Grenzschicht kann eingestellt werden und kann auch funktionalisiert werden, um eine elektrische Leitfähigkeit oder Isolierung bereitzustellen, um galvanische Korrosion zu verhindern, beispielsweise zwischen Kohlefaser und Aluminium oder Stahl.
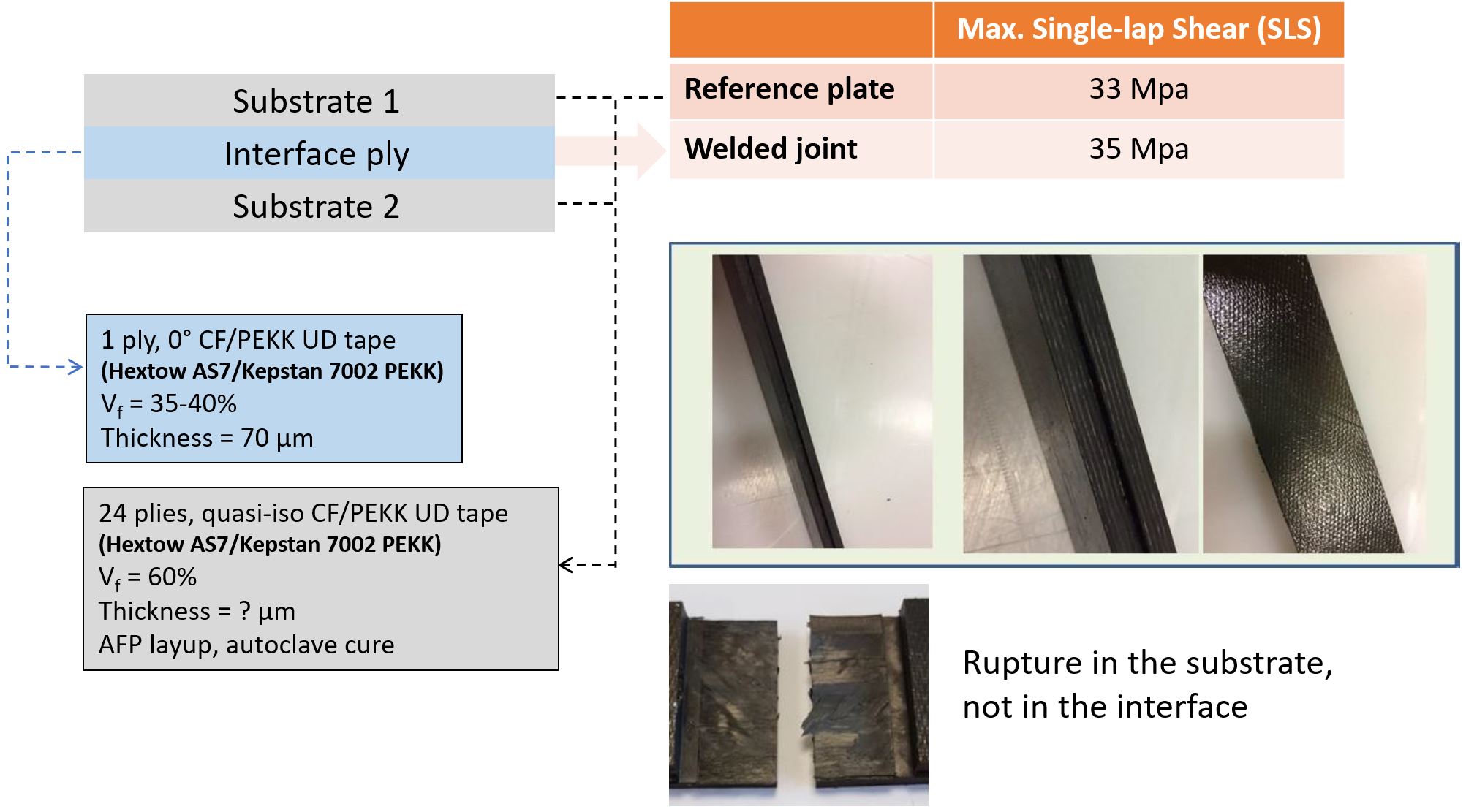
ISW-Ergebnisse
„Am Ende haben wir einen gemeinsamen Koeffizienten von 80-90%“, sagt Raynal. Der Fugenkoeffizient entspricht der Festigkeit der Schweißnaht und wird bei Metall, Kunststoffen und Verbundwerkstoffen verwendet. „Wir haben beim Einzel-Überlappungs-Scherversuch zweier vorverfestigter Platten, die mit ISW zusammengeschweißt wurden, 80-90% der Eigenschaften der ungeschweißten, autoklavverfestigten Referenzplatten erreicht.“ Bei diesen Versuchen wurde UD-Band aus Hextow AS7-Kohlefaser (Hexcel, Stamford, Connecticut, USA) und Arkema Kepstan 7002 PEKK verwendet.
Raynal sagt, dass ISW verwendet werden kann, um jede Art von Matrix zu schweißen:PE, PA, PEKK, PEEK sowie kohlenstoff-, glas- oder aramidfaserverstärkte thermoplastische Verbundwerkstoffe. „Wir haben auch gezeigt, dass es kein Problem ist, Komponenten mit Kupfergewebe für den Blitzeinschlagschutz (LSP) zu schweißen, was für die Produktion von Flugzeugstrukturen wichtig ist“, fügt er hinzu. ISW ist so konzipiert, dass es vollständig automatisiert wird, wobei der Schweißkopf an einem 6-Achsen-Roboterarm befestigt ist.
Temperaturkontrolle
Wie in der obigen Veröffentlichung von Kirk/Yarlagadda/Gillespie erläutert, ist ein häufiges Problem bei Metallgitter-Suszeptoren, die einem Magnetfeld ausgesetzt sind, die resultierende ungleichmäßige Temperaturverteilung in dem zu schweißenden Teil. „Wir kontrollieren dies, indem wir einen Suszeptor verwenden, um nur die Schweißgrenzfläche zu schmelzen“, erklärt Raynal. „Wir messen die Temperatur mit einem Laserpyrometer, das die Kante des Suszeptors tatsächlich von der Seite misst. Wir kennen also genau die Temperatur an der Grenzfläche. Wir verwenden auch Kühlung, um die Temperatur zu kontrollieren und eine ausreichende Kristallisation des thermoplastischen Materials während der gesamten Schweißnaht sicherzustellen.“
STELIA Stringer-Skin-Schweißversuche
Der Tier-1-Lieferant von Airbus, STELIA (Toulouse, Frankreich), ist einer der ersten Kunden für diese Induktionsschweißentwicklung. IS Groupe und Arkema führten für STELIA eine spezielle Studie durch, um einen 7-lagigen CF/PEKK-Stringer auf eine 14-lagige Außenhaut mit Kupfergewebe für den Blitzschlagschutz (LSP) zu schweißen. Das Endziel besteht darin, 30 Meter lange Konstruktionen mit geraden und doppelt gekrümmten Abschnitten zu schweißen. Die Komponenten wurden unter Verwendung von 194 g/m² UD-Band hergestellt, das Tenax HST45-Kohlenstofffasern (Teijin, Osaka, Japan) und Kepstan 7002 PEKK umfasste. STELIA spezifizierte eine homogene Schweißnaht mit einer mechanischen Leistung von>85% des autoklavverfestigten Referenzmaterials und ohne Verschlechterung der thermischen oder mechanischen Eigenschaften der Fügeteile. Außerdem wurde ein Verfahren gefordert, das robust gegenüber Änderungen der Klebeschichtdicke ist. Chemische und Eigenschaftsprüfungen an den geschweißten Komponenten wurden von IS Groupe durchgeführt.
IS Groupe und Arkema konnten die Anforderungen von STELIA erfüllen und erreichten im Vergleich zu autoklavverfestigten Referenzlaminaten>85 % der Leistung bei Einzellappenscherung (SLS) und interlaminarer Scherfestigkeit (ILSS). Es gab kein Auspacken oder eine Verschlechterung der Komponentenlaminate oder des LSP-Netzes. Der einzige Bereich, in dem sie zu kurz kamen, ist die Geschwindigkeit. STELIA forderte eine Schweißgeschwindigkeit ≥ 1 Meter/Minute. „Derzeit sind wir bei 0,3 Metern (10 Zoll) pro Minute“, räumt Raynal ein, „aber wir arbeiten weiter auf diese Zielgeschwindigkeit hin.“ Gibt es eine Grenze der Substratdicke, die geschweißt werden kann? „Wir können luft- und raumfahrttypische Dicken schweißen und haben 5-Millimeter-dicke Komponenten auf ein 5-Millimeter-Substrat geschweißt.“
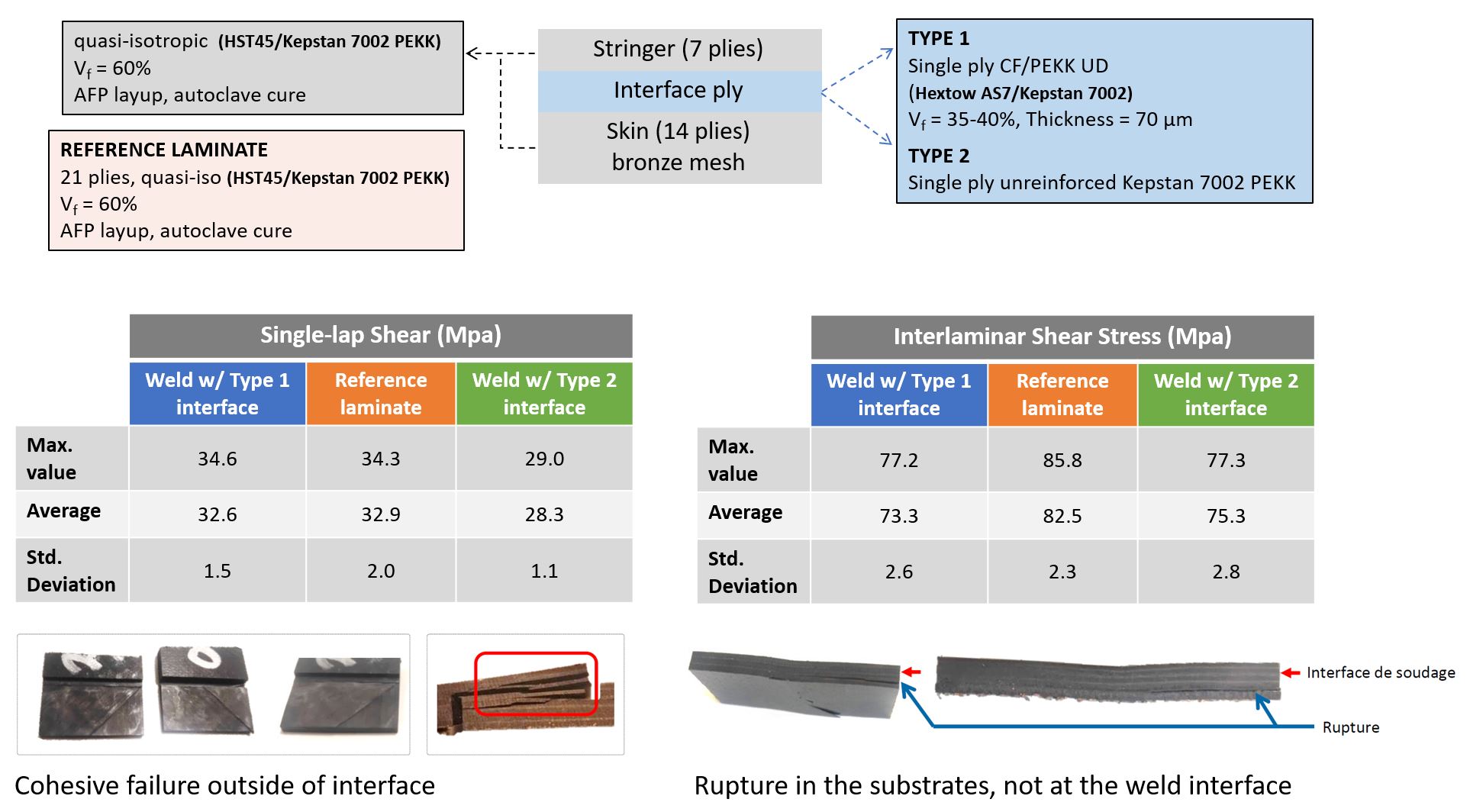
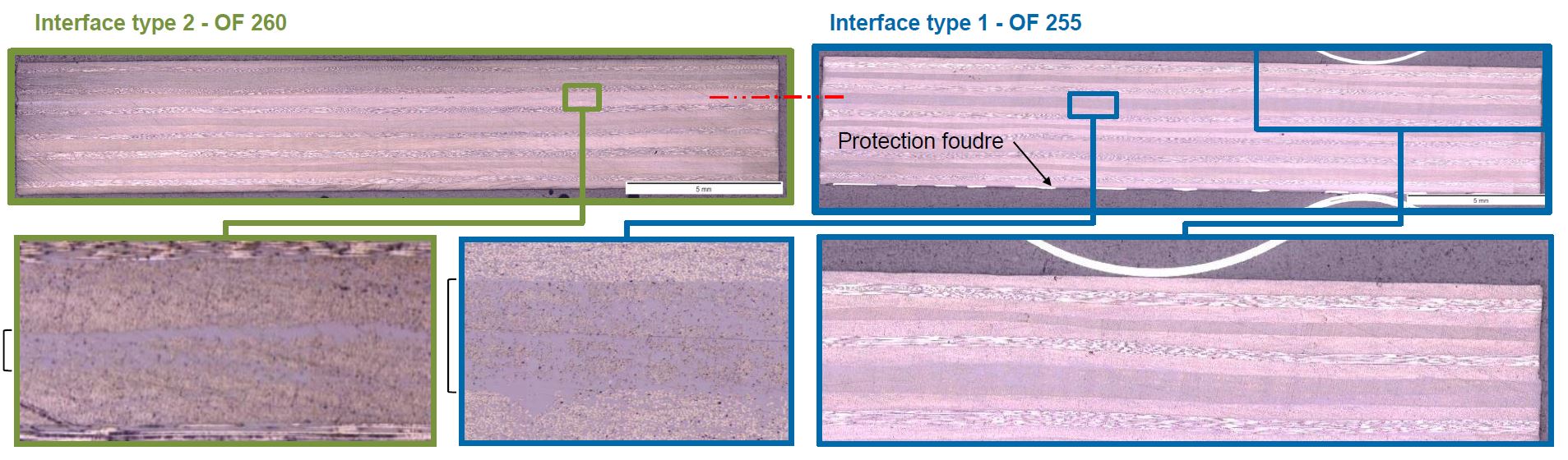
Arkema-Partnerschaft, Chancen und Herausforderungen
Warum mit Arkema arbeiten? „Weil es eine Beziehung zwischen der Technologie und den Materialien gibt“, erklärt Raynal. „Zum Beispiel machen die Materialien an der Grenzfläche und ihr Volumenanteil einen Unterschied. Wir sind Spezialisten für Prozesse, aber wir mussten eng mit einem Partner für Materialien zusammenarbeiten. Diese gemeinsame Entwicklung war notwendig, um die Schweißtechnik komplett zu optimieren.“
IS Groupe und Arkema sind Miteigentümer der ISW-Technologie und haben diese Technologie durch ein solides Patentportfolio geschützt, das bereits fünf französische und internationale Patentanmeldungen umfasst. ISW kann mit jeder thermoplastischen Verbundmatrix verwendet werden, und IS Groupe demonstriert die Technologie durch Programme, die sie mit Unternehmen in Europa und den USA hat, darunter Latécoère (Toulouse, Frankreich) und Collins Aerospace Aerostructures (Chula Vista, Kalifornien, USA).
Für Arkema liegt der Fokus auf PEKK, sagt Raynal und verweist auf seine strategische Allianz im Jahr 2018 mit Hexcel zur Entwicklung von CF-/Thermoplast-Bändern für zukünftige Flugzeuge, die sich darauf konzentrieren, ihren Kunden niedrigere Kosten und schnellere Produktionsgeschwindigkeiten zu bieten. Im Rahmen dieser Partnerschaft wird in Frankreich ein gemeinsames F&E-Labor eingerichtet.
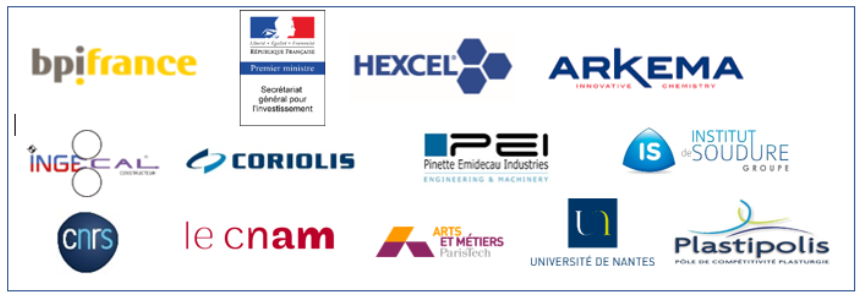
Die 13,5 Millionen Euro teuren, 48-monatigen Hochautomatisierten integrierten Verbundwerkstoffe für leistungsfähige anpassungsfähige Strukturen (HAICoPAS)-Projekt ist eine Fortsetzung der strategischen Allianz Arkema-Hexcel. Diese rein französische Zusammenarbeit umfasst die IS Groupe sowie die kundenspezifischen Maschinendesigner Ingecal (Chassieu), Coriolis Composites (Quéven), Pinette Emidecau Industries (Chalon Sur Saone) und ein Konsortium von Universitätslabors. HAICoPAS wird das Design und die Herstellung von Materialien für die Herstellung von Verbundteilen optimieren, um wettbewerbsfähige Kosten bei hoher Geschwindigkeit zu erzielen. Es zielt auch darauf ab, eine produktivere Technologie für die Platzierung/Layup von Verbundwerkstoffen und ein neues System zum Zusammenbau von Endteilen durch Schweißen mit Online-Qualitätskontrolle zu entwickeln.
Gezielte Anwendungen umfassen Flugzeugprimärstrukturen, Strukturteile für die Automobilindustrie und Pipelines für die Öl- und Gasindustrie. Recyclingfähigkeit und Nachhaltigkeitsvorteile thermoplastischer Materialien sind für diese Märkte ebenfalls wichtig und werden in HAICoPAS nachgewiesen und quantifiziert.
„Einer der Vorteile, die wir mit ISW bieten können, ist eine Einsparung des Stromverbrauchs um mehr als 50 % gegenüber unserem dynamischen Induktionsschweißverfahren aus dem Jahr 2017“, betont Raynal. „Bei konventioneller Induktion braucht man viel Leistung, um die Oberfläche zu erwärmen. Aber mit einem Suszeptor an der Grenzfläche ist die erhitzte Oberfläche viel kleiner und benötigt viel weniger Energie.“ Er merkt an, dass dies auch dazu beiträgt, eine Dekompaktierung im Radius von Stringern zu vermeiden. „Wenn man zu stark erhitzt, kann man das Material im Radius aufweichen und die Fasern hier bewegen lassen. Wir müssen also nur die Kontaktzone für die geschweißten Substrate perfekt erwärmen, ohne den Radius zu erwärmen. Mit ISW ist das kein Problem.“
Es gibt jedoch immer noch thermische Probleme. „Bei flachen Formen ist die Wärmekontrolle unkompliziert, aber mit zunehmender Komplexität der Formen wird es schwieriger“, sagt Raynal. „Für 2020 besteht das Hauptziel darin, die Entwicklung fortzusetzen und das Schweißen von Stringern auf der Haut in einem repräsentativen Maßstab zu erreichen. Unser Fokus liegt auch darauf, die Technologie in neue Flugzeugentwicklungsprogramme einzuführen.“
Weitere Informationen finden Sie unter Composite Integrity auf der JEC World 2020, Halle 5, Stand N89.
Harz
- Die 5 wichtigsten Vorteile des Induktionsschweißens
- C# verwenden
- Eine Einführung in das Ultraschallschweißen von Kunststoffen
- Covestro verstärkt Investitionen in thermoplastische Verbundwerkstoffe
- Graphenverstärkte thermoplastische Masterbatches auf den Markt gebracht
- Solvay erweitert die Kapazität von thermoplastischen Verbundwerkstoffen
- Thermoplastische Verbundwerkstoffe bei Oribi Composites:CW Trending, Episode 4
- Schweißen von thermoplastischen Verbundwerkstoffen
- Was Gemeinden fehlen, wenn sie keine mobilen Inspektionen verwenden
- Vermeidung von Schweißproblemen und -fehlern durch die Verwendung verifizierter Metalle