Hochgeschwindigkeits-Hochgeschwindigkeitsfertigung thermoplastischer Verbundwerkstoffe
Um das Auflegen zu beschleunigen und dennoch eine gute Designflexibilität zu bieten, haben SABIC und Airborne bei der Entwicklung des Lagenauflegeprozesses für thermoplastische Verbundbänder eine Idee aus dem Postwesen übernommen. Mehrere preiswerte Trays, die sich auf einem Fördersystem (hier gezeigt) bewegen, halten kurz unter Zuführeinheiten an. Jeder Zuführer schneidet eine Bandlage mit den richtigen Abmessungen und der richtigen Ausrichtung und legt sie in das Fach ab, das dann zur nächsten Zuführeinheit weiterläuft. Die Fächer zirkulieren weiter durch die Zuführeinheiten, bis die richtige Anzahl und Ausrichtung der Lagen in jedem Stapel erreicht ist, um die Designanforderungen eines bestimmten Laminats zu erfüllen. Quelle | SABIC
Bis zu vier Laminate (mit jeweils bis zu 15 Lagen) pro Minute und 1,5 Millionen Laminate pro Jahr herstellen zu können, verspricht die Digital Composites Manufacturing Line (DCML), eine neue Hochgeschwindigkeitsanlage zur Herstellung von konsolidierten Laminaten aus thermoplastischen Verbundbändern von einer einzigen Produktionslinie aus – einschließlich vollständiger Inspektion, die zu 100 % digital ist, einschließlich Messungen und Datenverfolgung – des eingehenden Materials und der ausgehenden Laminate. Diese Produktionsrate ist anscheinend signifikant schneller als jedes andere handelsübliche Klebeband-Handlingsystem – für Thermoplaste oder Duroplaste – und dieses System wurde speziell entwickelt, um die hohe Leistung und die effektiven Umwandlungskosten zu erfüllen, die von der Unterhaltungselektronikindustrie gefordert werden (siehe „Unterhaltungselektronik:Hybrid-Verbundabdeckungen“). Glücklicherweise sind die Teile für diesen Markt nicht riesig – nicht in der Größenordnung der Luft- und Raumfahrt oder der Automobilindustrie –, aber OEMs benötigen viele davon, in der Größenordnung von mehreren zehn Millionen pro Jahr.
„Ein Hochgeschwindigkeitsprozess zur Verarbeitung von thermoplastischen Bändern war wirklich erforderlich, da die derzeitige Technologie relativ arbeitsintensiv, teuer und langsam ist“, erklärt Gino Francato, SABIC Global Composites Leader. „Das macht es schwierig, die vielen Vorteile dieser Materialien wirtschaftlich zu rechtfertigen und zu nutzen – um dünne, leichte Teile mit hoher Ästhetik, Schlagzähigkeit und mechanischer Leistung sowie Recyclingfähigkeit herzustellen – in Branchen mit hohem bis sehr hohem Produktionsvolumen. Ohne die Möglichkeit, die Produktionsgeschwindigkeit erheblich zu erhöhen und eine vollautomatische Handhabung und Inspektion zu verwenden, werden thermoplastische Klebebänder teure Nischenprodukte bleiben, die hauptsächlich auf den Einsatz in der Luft- und Raumfahrt und in der Automobilindustrie beschränkt sind.“
Die DCML ist eine Idee von SABIC (Bergen op Zoom, Niederlande) und Airborne (Den Haag, Niederlande) mit Technologie von Siemens AG (München, Deutschland) und KUKA AG (Augsburg, Deutschland). SABIC steuerte Werkzeuge zur Materialtechnologie und Modellierung von Verbundwerkstoffen bei, um die Entwicklung kundenspezifischer Materialien und das virtuelle Prototyping von Teilen zu beschleunigen. Airborne baute die Linie und steuerte auch Know-how in den Bereichen Automatisierung, Digitalisierung und Industrialisierung des Composites-Produktionsprozesses bei. Siemens steuerte integriertes Product Lifecycle Management (PLM) und speicherprogrammierbare Steuerung (PLC) bei, um die Automatisierung zu verbessern und maschinelles Lernen zu erleichtern. KUKA steuerte Industrieroboter und Lösungen für die Fabrikautomation bei. Obwohl das neue Hochgeschwindigkeitsverfahren seit 2018 auf mehreren Presseveranstaltungen allgemein beschrieben wurde, gibt es viele Details, die noch nicht preisgegeben wurden. Folgendes wissen wir derzeit.
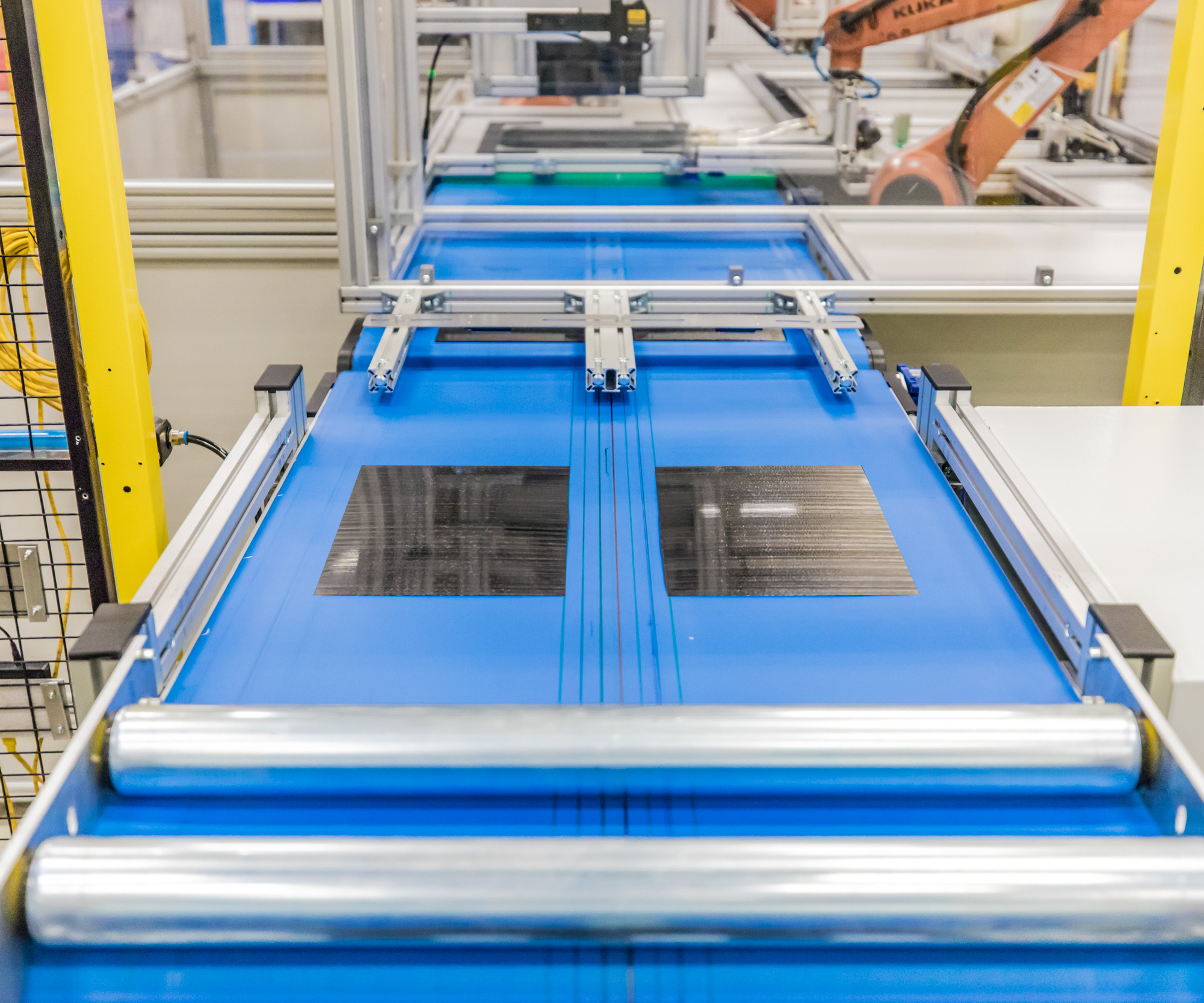
Sobald das Tablett die Förderschleife verlässt, geht es zur Schweißstation, wo jeder Stapel an zwei Stellen heftgeschweißt wird, um die Roboterhandhabung an der Konsolidierungsstation zu erleichtern. Nach der Konsolidierung geht das Laminat zum Beschneiden und zur Inspektion (hier gezeigt). Quelle | SABIC
Die Linie wurde entwickelt, um anpassbare, endkonturnahe Flachlaminate aus unidirektionalen (UD) thermoplastischen Bändern herzustellen und bietet Layup, Konsolidierung, Beschnitt, digitale und visuelle Inspektion, automatische Freigabe und Verpackung für den Versand an die Kunden. Bis zu vier Laminate können pro Minute hergestellt werden, und jedes Laminat kann einen anderen Auflegeplan, eine andere Ausrichtung und Anzahl von Lagen haben und theoretisch sogar unterschiedliche Materialien verwenden (mit unterschiedlichen Verstärkungen und Harzmatrizen, obwohl dies zusätzliche Zuführeinheiten erfordert).
Das gleichzeitige Erzielen verschiedener Lagen hängt nur davon ab, wie oft ein bestimmtes Tablett (mit einem bestimmten Laminatdesign) unter jedem Zuführer durchläuft, um die richtige Anzahl von Lagen und Ausrichtungen zu erreichen, um seinen Legeplan zu vervollständigen. Angesichts des schnellen Modellwechsels in der Unterhaltungselektronik steht Flexibilität im Mittelpunkt des Systems, das durch zusätzliche Feeder am Frontend oder Funktionalität (z. B. Bohren, Preforming usw.) am Backend erweitert werden kann. Ursprünglich war die Linie für den Betrieb der unidirektionalen kohlenstofffaserverstärkten Polycarbonatbänder von SABIC ausgelegt, aber Berichten zufolge ist das System flexibel genug, um thermoplastische Bänder von Polyethylen (PE) und Polypropylen (PP) bis hin zu Polyetheretherketon (PEEK) mit unidirektionaler Kohlefaserverstärkung zu verarbeiten oder Glasfaser – oder beides – oder sogar Gewebegewebe.
Das System ist Industrie 4.0-kompatibel und ermöglicht eine durchgängige Digitalisierung – von der Produktentwicklung aus Verbundwerkstoffen bis hin zur physischen Produktion in der Fabrikhalle – mit vollständiger Qualitätskontrolle basierend auf maschinellem Lernen, um im Laufe der Zeit automatisch kontinuierliche Qualitätsverbesserungen zu erzielen. Die Linie kann aus der Ferne überwacht und gesteuert werden, sodass Hersteller Einstellungen (z
Funktionell besteht die DCML aus drei Hauptabschnitten:Lagenaufbau, Konsolidierung und Beschneiden/Inspektion.
Einzigartig ist, dass der Lagenauflegeabschnitt keine automatischen Bandauflegemaschinen (ATL) verwendet, die normalerweise Bänder auf Länge schneiden und sie in der erforderlichen Ausrichtung und Position auf einem sich unter dem Schneidkopf bewegenden Schalttisch platzieren würden. Stattdessen hat das Team einen neuartigen Hochgeschwindigkeitsansatz gewählt, der angeblich auf der Art und Weise basiert, wie Post sortiert und verteilt wird, um Lagenstapel zu bauen. Mehrere preiswerte Trays, die sich auf einem Fördersystem bewegen, halten kurz unter Zuführeinheiten an. Jede Zuführeinheit schneidet und legt eine Bandlage mit den richtigen Abmessungen und Ausrichtungen (überprüft durch hochauflösende Kameras, die Bänder auf Fehler und Veränderungen prüfen und Breite und Dicke an mehreren Stellen messen) in das Fach ab, das dann zum nächsten weiterläuft Zubringereinheit. Um Ausschuss zu reduzieren und das Layup zu beschleunigen, werden Bänder auf die für ein bestimmtes Projekt erforderliche Breite produziert. Die Schalen zirkulieren zurück durch die Zuführungen, bis die richtige Anzahl von Lagen in jedem Stapel abgelegt ist, bevor an zwei Stellen mit dem Heftschweißen fortgefahren wird, um die Handhabung an der Konsolidierungsstation zu erleichtern. Dieser Ansatz ermöglicht ein schnelles Layup, aber mit Designflexibilität.
Bei der Konsolidierung hebt ein Roboter vier geschweißte Stapel (jeweils zwei Stapel) aus ihren Trays und platziert sie zwischen einem Satz Metallplatten auf einem separaten Fördersystem. Die Platten erhitzen sich und erhitzen und verfestigen somit die Laminate (über Kontaktheizung), anschließend werden die Laminate abgekühlt und robotergesteuert auf ein drittes Fördersystem entladen. Die im letzten Konsolidierungsvorgang verwendeten Metallplatten werden wieder in den Plattenrücklauf und wieder in das Konsolidierungssystem zurückgeführt. Jede Minute betreten und verlassen vier Stapel diesen Abschnitt.
Die letzte Station für die nun konsolidierten Laminate ist die Inspektion, Besäumung und Verpackung. An dieser Station wird jedes Laminat auf einer Seite inspiziert und besäumt, bevor es zu einem zweiten Roboter gelangt, der das Laminat umdreht und von der anderen Seite inspiziert. Es sind keine Details zur verwendeten Trimmtechnologie verfügbar.
Die DCML hat, wie jedes Fertigungssystem, ihre Grenzen. In erster Linie gibt es einige Abstriche in Bezug auf die verfügbaren Lagenorientierungen, die Lagengröße und -form, die endgültige Laminatgröße und die Möglichkeit, Löcher/Fenster zu verlegen. Dies macht das System jedoch in Bezug auf Geschwindigkeit, Leistung, Ausschussrate und Umrüstkosten mehr als wett.
Berichten zufolge wird die erste kommerzielle Linie von Airborne in den Niederlanden im nächsten Jahr die Produktion aufnehmen, wobei das Unternehmen kundenspezifische thermoplastische Laminate für Kunden aus der Unterhaltungselektronik herstellt. Eine zweite Linie in Laborgröße ist bereits im Polymer Processing Development Center von SABIC (PPDC, Pittsfield, Massachusetts, USA) für Kunden verfügbar, die die Technologie ausprobieren und die Laminatqualität bewerten möchten.
Neben der Unterhaltungselektronik zählen Luft- und Raumfahrt, Automobil, Nahverkehr, Sportartikel und das Gesundheitswesen zu anderen Branchen, die als potenzielle Ziele für die Technologie gelten.
Harz
- Covestro verstärkt Investitionen in thermoplastische Verbundwerkstoffe
- Thermoplastische Verbundwerkstoffe bei Oribi Composites:CW Trending, Episode 4
- Fehlerbehebung beim Thermoformen von thermoplastischen Verbundwerkstoffen
- Thermoplastische Verbundwerkstoffe:Strukturelle Stoßstangenhalterung
- Toray Advanced Composites erweitert seine Fähigkeiten im Bereich thermoplastischer Verbundwerkstoffe
- Teledyne CML Composites investiert in thermoplastische Verarbeitungsmöglichkeiten
- Cato Composites erweitert Produktionskapazität für thermoplastische Verbundwerkstoffe
- Vorschau der JEC World 2019:SABIC
- Thermoplastische Verbundwerkstoffe:Malerische Aussicht
- Schweißen von thermoplastischen Verbundwerkstoffen