Thermoplastische Primäraerostrukturen machen einen weiteren Schritt nach vorn
Vorteilhafte Eigenschaften thermoplastischer Verbundwerkstoffe, wie z. B. Zähigkeit, vergleichsweise hohe Festigkeit außerhalb der Ebene und Nachhaltigkeit/Recyclingfähigkeit, haben das Design von Flugzeugen angezogen Ingenieure haben sich seit Jahrzehnten mit dem Begriff der Primärstrukturen aus thermoplastischen Verbundwerkstoffen vertraut gemacht. Aber Flugzeug Fertigung Ingenieure waren unsicher, einen kostengünstigen Weg zu finden, um sie von der CAD-Simulation in die Produktion zu bringen. Sie lassen sich jedoch nicht abschrecken:Die Bemühungen um die Entwicklung der notwendigen Fertigungstechnologien wurden weltweit fortgesetzt – vielleicht nirgendwo so hartnäckig wie in den Niederlanden.
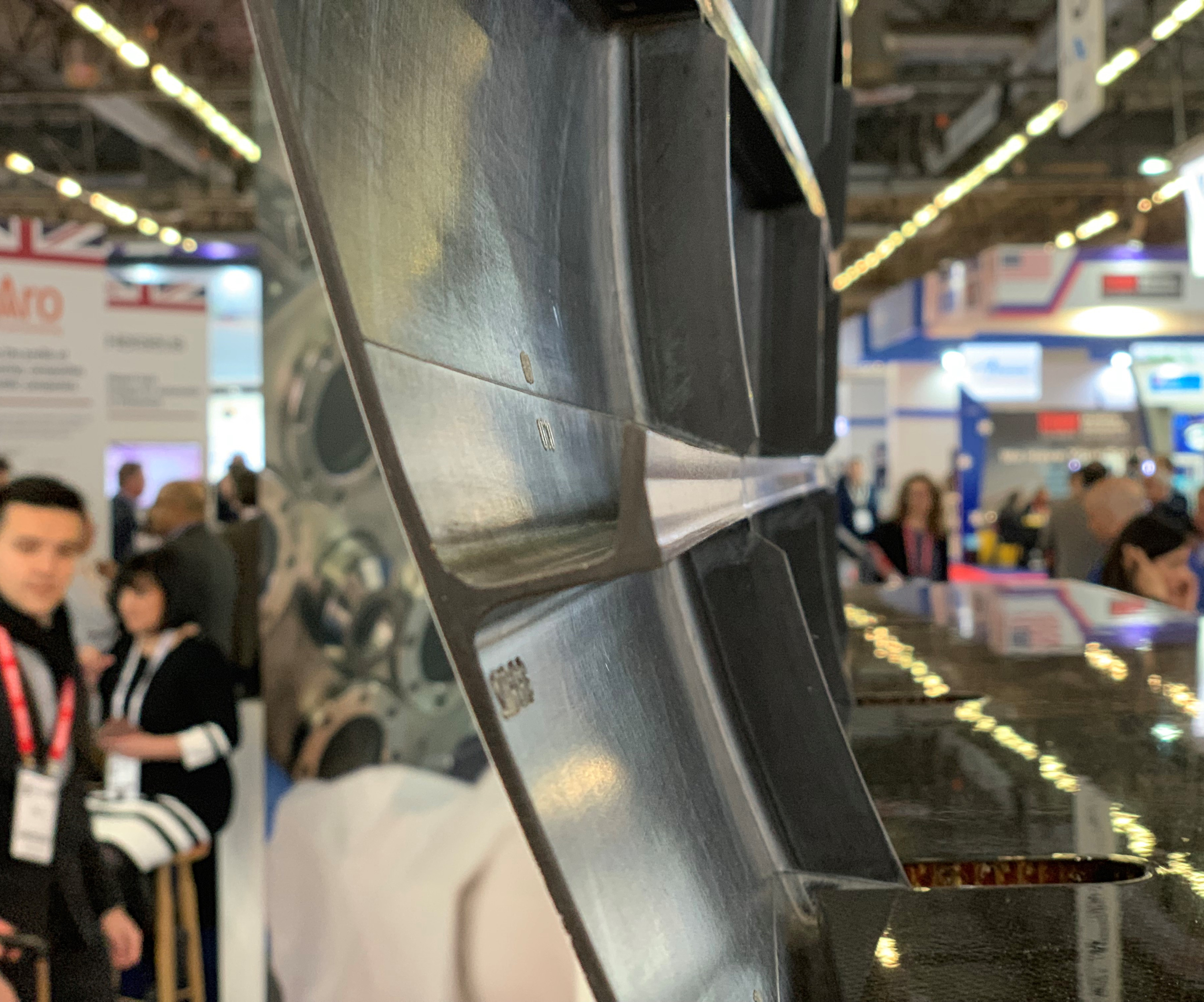
Integrale L-Stringer. Der für Gulfstream entwickelte und gebaute GKN Fokker-Kohlefaser/PEKK-Rumpf verfügt über gebogene Längs-L-Stringer mit einem leicht stumpfen Winkel, um die Werkzeugfreigabe zu ermöglichen. CW Foto | Jeff Sloan
2009 gründeten neun niederländische Industrieunternehmen und Forschungsinstitute zusammen mit Airbus (Toulouse, Frankreich) das Konsortium Thermoplastic Affordable Primary Aircraft Structure (TAPAS). Die Initiative wurde 2014 auf 12 Partner ausgeweitet und als TAPAS2 fortgeführt. GKN Fokker (Hoogeveen, Niederlande) zielt auf von Airbus entwickelte Anwendungen im Rahmen von TAPAS2 ab und hat kürzlich einen Rumpfdemonstrator entwickelt, der eine so genannte „Butt-Jointed Orthogrid-Technologie“ verwendet, die eine kostengünstige Produktion eines thermoplastischen Verbundrumpfdesigns ermöglicht.
Die vollständige Amortisation einer primären Flugzeugstruktur aus thermoplastischem Verbundwerkstoff – wenn auch noch in Jahren – könnte jetzt in Sicht sein, da Gulfstream Aerospace (Savannah, Georgia, USA) mit GKN Fokker zusammengearbeitet hat, um seine TAPAS2-Rumpftechnologie weiterzuentwickeln und den Weg für eine mögliche Anwendung zu weisen die Materialien und den Prozess zu einem vollen Rumpf. Die Geschichte hinter dem neu entwickelten Rumpfpaneel (das Anfang dieses Jahres auf der JEC World gezeigt wurde) ist eine der Weiterentwicklungen in den Design- und Herstellungsmethoden und darüber hinaus in einem stärker integrierten Design-Manufacturing-Engineering-Ansatz.
„Traditionell“, erklärt Andries Buitenhuis, Chefingenieur von GKN Fokker, „ob sie Stoffe oder unidirektionale Bänder verwendeten, die Designer hielten sich meistens an konventionelle Schichten mit 0-, 90- und 45-Grad-Ausrichtung. Sie arbeiteten von ihren Ply-Layup-Tischen aus, unabhängig von anderen Disziplinen.“ Der neue Ansatz ist eine integrierte, digitalisierte Design-Fertigungs-Softwareplattform (entwickelt von TAPAS), in der Ingenieure verschiedener Disziplinen alle auf dasselbe digitale Modell schauen und die Möglichkeit haben, komplexere Teilekonstruktionen zu konzipieren. „Dies eröffnet eine ganz neue Welt beispielloser Optimierungsmöglichkeiten“, fährt Buitenhuis fort. „Bei komplexen Formen können die Faserrichtungen überall sein. Wir können unkonventionelle Laminate bauen und einen neuen Blick auf Designzulässigkeiten, Fertigungslücken und -überlappungen, Radien usw. werfen. Und Sie können die Festigkeit der Struktur vor Ort optimieren.“ Diese erweiterten Designoptionen nutzen die Faserlenkungsfähigkeit von Maschinen zur automatischen Faserplatzierung (AFP) und die Fortschritte bei anderen Fertigungsmöglichkeiten, die unten diskutiert werden, vollständiger.
Die Gestaltungsfreiheit, die dieses integrierte digitale System bietet, hat sich bei der Entwicklung und Herstellung von Business-Jet-Panels als unverzichtbar erwiesen. Bei den TAPAS2-Rumpfkonstruktionen weist die Kohlefaser/Polyetherketonketon (PEKK)-Platte (hergestellt mit APC PEKK-FC von Solvay) eine geschweißte, befestigungsfreie Rahmen-Haut-Verbindung auf, die einen wesentlichen Beitrag zur Kosteneffizienz des Designs leistet. „Wir gehen davon aus, dass wir mit Aluminium-Rumpfschalen eine Kostenparität erreichen“, erklärt Arnt Offringa, Leiter Thermoplastische Verbundwerkstoffe bei GKN Fokker, „und das liegt daran, dass Aluminiumschalen genietet werden.“ Es wird erwartet, dass der Wegfall mechanischer Befestigungselemente eine Kostenreduzierung von 20 % und eine Gewichtsreduzierung von 10 % bei den Primärstrukturen von Flugzeugen im Vergleich zu herkömmlichen Verbundlösungen mit sich bringt. Natürlich kommt ein Großteil der Kosten- und Gewichtseinsparungen aus dem Wegfall der Befestigungselemente selbst sowie der Arbeitskosten für deren Installation. Von großer Bedeutung ist auch die Beseitigung von Löchern in den Verbundkomponenten, um die Befestigungselemente aufzunehmen – Löcher, die eine zusätzliche Verstärkung und damit ein zusätzliches Gewicht erfordern.
GKN Fokker erreichte im Dezember 2017 mit Airbus den Technology Readiness Level (TRL) 3 (Proof of Concept) für einen druckbeaufschlagten Rumpf und demonstrierte damit Kostenparität mit Aluminium-Rumpfpaneelen unter TAPAS2. Auf dem Weg dorthin erweiterte das Team von GKN Fokker seine Vision für diesen Thermoplast Rumpftechnologie von Verkehrsflugzeugen bis hin zu Business-Jet-Anwendungen.
Interesse von Gulfstream
Die erfolgreiche Arbeit von GKN Fokker für Gulfstream an thermoplastischen Verbundbauteilen machte eine Partnerschaft mit dem Business-Jet-Hersteller zu einem logischen nächsten Schritt. „Es ist allgemein bekannt, dass Gulfstream seit Jahren thermoplastische Verbundteile fliegt“, sagt Mark Chapman, Manager der Advanced Structures and Materials Initiative (ASMI) von Gulfstream. Er fügt hinzu, dass das Rumpfpaneel-Projekt „eine natürliche Weiterentwicklung von dem ist, was wir bisher gemacht haben, angefangen mit einfacheren Teilen bis hin zu primären Strukturteilen“. GKN Fokker hat mit Gulfstream bei der Entwicklung zahlreicher Sekundärkomponenten aus thermoplastischen Verbundwerkstoffen zusammengearbeitet, darunter Ladebordwände und Seitenruder sowie Bodenplatten der G650.
Im Jahr 2015 stellten Offringa und Buitenhuis Gulfstream TAPAS2-Projektentwicklungen vor, und Chapman und sein Team erkannten das Potenzial, die Vorteile der TAPAS2-Ergebnisse zu nutzen. „Wir sahen die potenziellen Vorteile der Gewichtsreduzierung, der besseren Schlagfestigkeit und Zähigkeit sowie der verbesserten Leistung“, erinnert sich Chapman. Auch das befestigungsfreie Design ist ansprechend. „Die Schweißtechnologie würde es uns ermöglichen, den Rumpf effizienter zu montieren“ als eine mechanisch befestigte Baugruppe, sagt Chapman.
Die Partnerschaft mit GKN Fokker unterstützt Gulfstreams Forschung und Entwicklung komplexerer Rumpfformen, deren Herstellung mit Metallstrukturen möglicherweise nicht wirtschaftlich ist. „Bisher kann man Metall nur strecken“, bemerkt Chapman. „Die für komplexe Formen notwendigen Spleiße und Stützstrukturen sind nicht sehr effizient.“ Offringa stimmt zu:„Solch komplexe Geometrien sind mit herkömmlichen Technologien nur schwer herzustellen.“
Konstruktion und Fertigung verbinden
Um ein verbindungsloses, produzierbares Design zu erreichen, konzentriert sich der Ansatz von GKN Fokker darauf, den beiden Hauptkräften standzuhalten, denen die Rumpfgelenke ausgesetzt sind:Kabinendruck und Stöße wie Werkzeugstürze. Der Kabinendruck übt eine radiale Kraft auf den Rumpf aus, wodurch hohe Belastungen in der Spant-zu-Haut-Verbindung erzeugt werden. Bei herkömmlichen Konstruktionen enthalten Rumpfspanten "Mauslöcher", durch die die Längsstringer verlaufen. Unter der Kraft des Kabinendrucks dienen diese Mauslöcher als Diskontinuitäten, die hohen Schälkräften ausgesetzt sind – ein Hauptproblem für ein Design ohne Befestigungselemente, da Verbundwerkstoffe im Vergleich zu Metallen eine geringe Festigkeit außerhalb der Ebene haben. Stöße erzeugen auch hohe Belastungen in der Rahmen-Haut-Verbindung, da sich der Rahmen beim Aufprall nicht biegt.
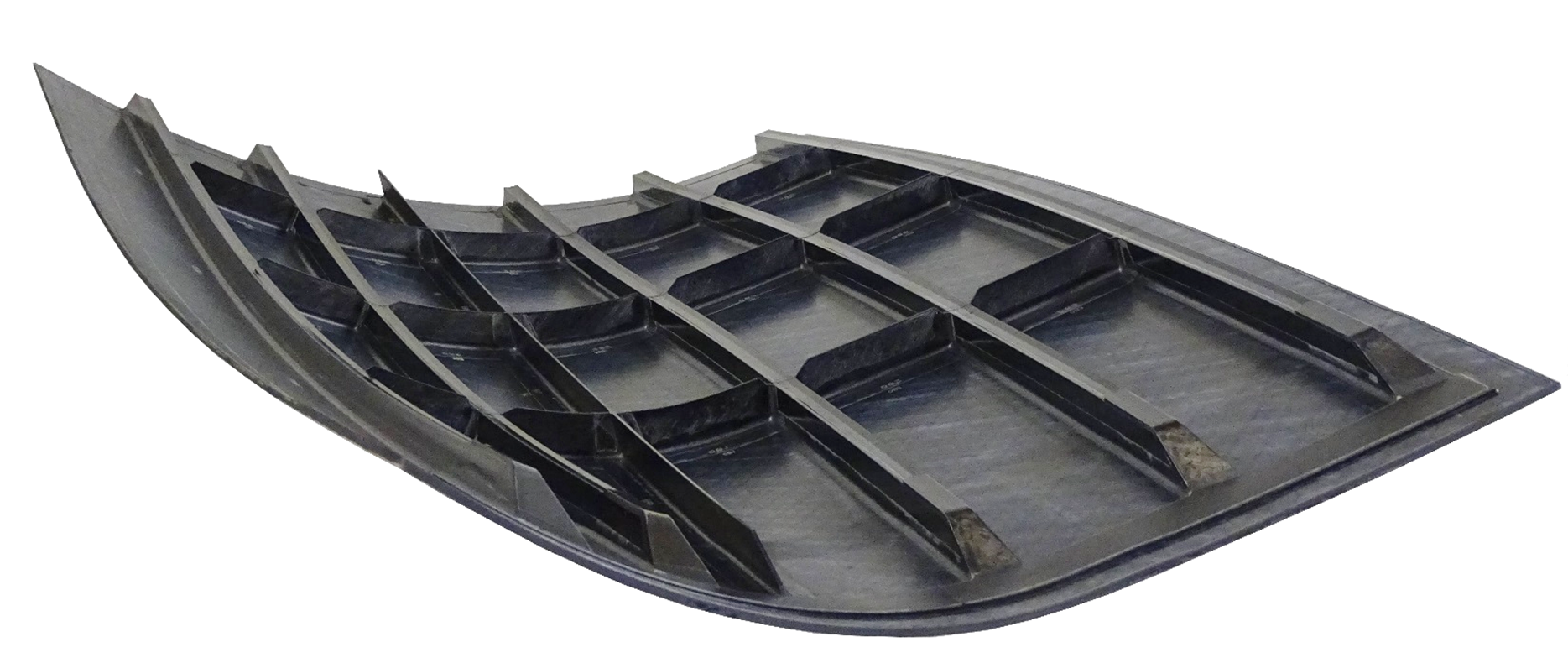
Doppelte Krümmung. Die Rumpfplatte aus thermoplastischem Verbundmaterial nimmt die komplexe Geometrie eines Achterrumpfs eines Gulfstream-Geschäftsjets mit fasergesteuerter AFP-Schichtung der Haut und einer gemeinsamen Verfestigung des Orthogrids auf. Beachten Sie die umlaufenden Messerwangen, die später mit dem Rahmen verschweißt werden. Quelle | GKN Fokker
Das Team von GKN Fokker/Gulfstream wusste, dass es unmöglich war, die Herausforderungen einer komplexen Krümmung entweder mit Metall oder mit konventionellen Konstruktions- und Herstellungsansätzen aus Verbundwerkstoffen zu meistern. Buitenhuis betont insbesondere:„Ohne Fiber Steering wäre ein komplexes Rumpfdesign nicht möglich.“ Diese Fähigkeit von AFP-Maschinen hat es den Konstrukteuren ermöglicht, die Faserorientierung lokal basierend auf der komplexen Form der Schale zu optimieren und von den standardmäßigen 0/45/90-Faserorientierungsoptionen abzuweichen. „Faserlenkung zur Form- und Gewichtsoptimierung ist eine der wichtigsten Weiterentwicklungen dieses Projekts“, glaubt Chapman.
GKN Fokker fertigte die Außenhaut des Rumpfpaneels auf einer Ultraschall-AFP-Maschine, die das Unternehmen für das schnelle Auflegen von thermoplastischen Klebebändern entwickelt hatte. Das Band ist unidirektional, was auch die Laminatleistung im Vergleich zu Gewebebändern verbessert.
Das neue Konzept, das unter TAPAS und TAPAS2 entwickelt wurde und jetzt in der Gulfstream-Platte zum Einsatz kommt, wird als "Stoßverbindung orthogonal versteift" beschrieben, um die hohen Belastungen durch Kabinendruck und Aufprallkräfte sowie andere Leistungsanforderungen erfolgreich zu bewältigen Haut mit geschweißten Rahmen.“ Beim Auspacken dieser Beschreibung werden drei wichtige Konstruktionsmerkmale und die zu ihrer Umsetzung erforderlichen Fertigungsentwicklungen hervorgehoben:(1) das Orthogitter, (2) die Stoßverbindung und (3) die Schweißtechnologie.
Orthogrid
Die Festigkeitsanforderungen des Paneels werden teilweise durch vollständig verbundene orthogonale Gitteraussteifungen erfüllt. Dieses Orthogitter eliminiert die Spitzenbelastungen, die mit den Mauslöchern verbunden sind, und befreit das Design von Punkten, an denen die Schälkräfte verstärkt werden. Das Orthogrid besteht aus durchgehenden Längsstringern und Spanten, die aus zwei unterschiedlichen Komponenten bestehen:diskontinuierliche, aber verbundene Umfangsschaufelstringer und darüber geschweißte Spanten.
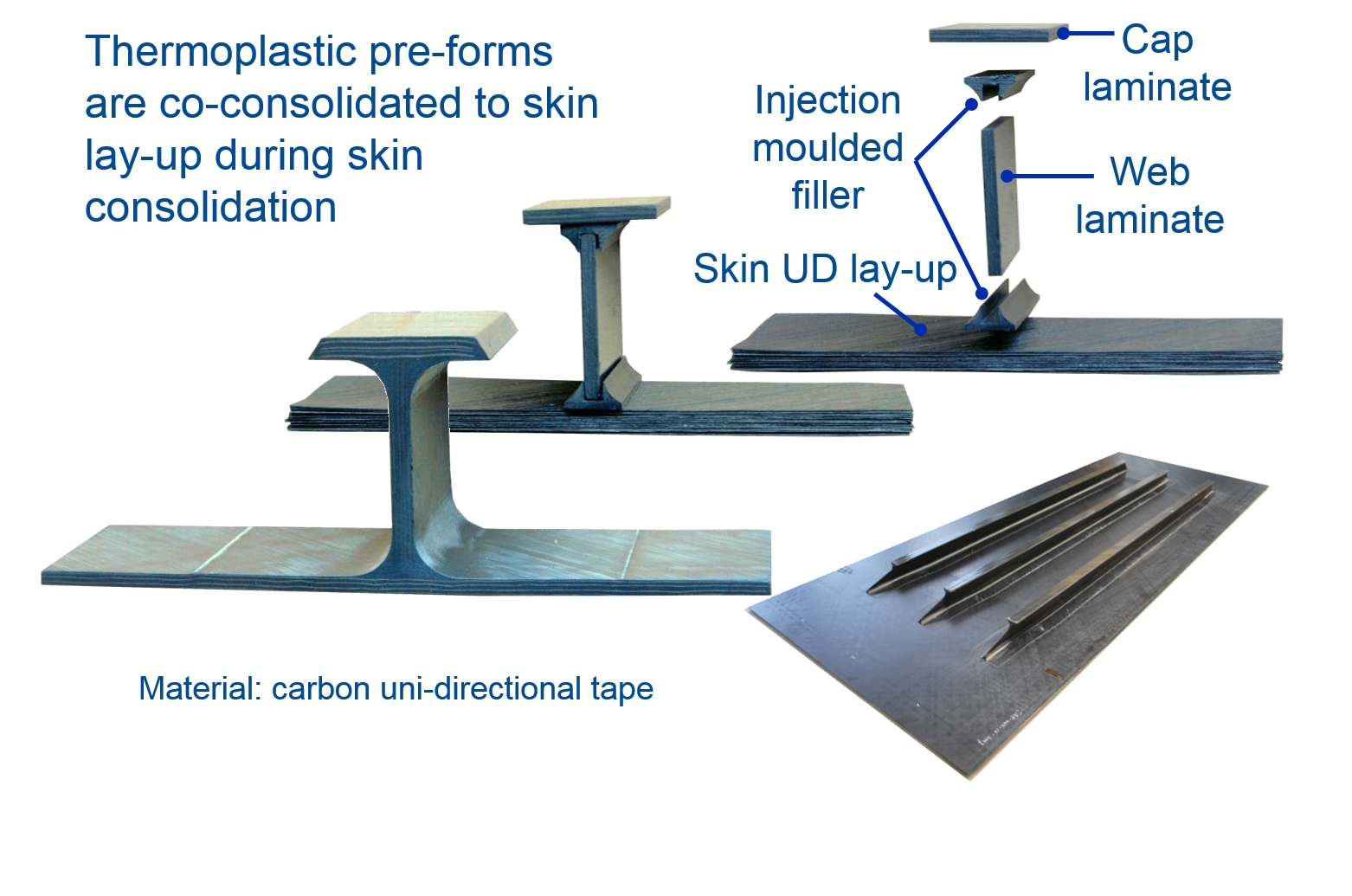
Kostengünstige Stoßverbindung. GKN Fokker hat eine Stoßverbindung entwickelt und patentiert, die eine Orthogitter- und Orthogitter-zu-Haut-Verbindung mit kostengünstigen Kurzfaser-Spritzgusselementen und Endlosfaser-Flachlaminaten für den Stringersteg und die Kappe ermöglicht (hier ein T-Stringer; die Gulfstream-Platte integriert L-Stringer mit der gleichen Technik). Quelle | GKN Fokker
Somit stellt dies eine neue Generation im Rumpfversteifungsdesign dar, die sich während der jahrelangen Entwicklung von Orthogrids entwickelt hat. Anfangs verwendete GKN Fokker T-Stringer, bei denen die Kappen sowohl der Längs- als auch der Umfangsträger durchgehend waren und sich an den Ecken überlappten. Das Verbinden mit dem Rahmen erforderte jedoch das Entfernen der umlaufenden Kappe. So wurden T-Stringer zu L-Stringern und Rahmen zu umlaufenden Klingen-Stringern, an die dann Rahmen angeschweißt wurden.
Eine weitere Modifikation ist erforderlich, da die sowohl in Längsrichtung als auch in Umfangsrichtung verwendeten gebogenen Stringer das Lösen des Werkzeugs viel schwieriger machen. So sind die L-Stringer mit einem Kappen-Steg-Winkel von mehr als 90 Grad ausgelegt, sodass Werkzeugteile immer seitlich aus dem Stringer-Raster gleiten können.
Stoßverbindungen
GKN Fokker hat nicht nur das Orthogrid-Design, sondern auch einen neuen Fertigungsansatz für das Gitter sowie den Gitter-zu-Haut-Verbindungsmechanismus entwickelt. „Die Herstellung des Gitters kann unerschwinglich teuer sein“, bemerkt Offringa, „aber unser Gitter besteht aus flachen Laminaten und einfachen spritzgegossenen ‚Füllstoffen‘.“
Genauer gesagt hat GKN Fokker seine patentierte Stumpfverbindungstechnologie auf die Gulfstream-Platte (auch auf die vorherigen TAPAS-Platten) angewendet. Der Steg und die Kappe der T- oder L-Stringer-Komponenten sowie die Blade-Stringer-Komponenten werden aus Vorformlingen hergestellt, die aus einem flachen Kohlefaser/PEKK-Laminat wasserstrahlgeschnitten werden. Die Verbindungselemente (Skin to Steg und Steg to Cap) sind spritzgegossene, pi-förmige Füllstoffe aus einem kurzfaserigen Carbon/PEKK-Material. Sowohl der Harz- als auch der Kohlefasertyp stimmen mit denen in den Gitterelementen überein.
Skin und Orthogrid werden in einem Invar Inner Mold Line (IML)-Tool zusammengeführt. Das Werkzeug verfügt über Nuten, in die die orthogonalen Komponenten und Werkzeugblöcke geladen werden. Die AFP-geformte Haut wird dann auf dem IML platziert und die gesamte Baugruppe wird verpackt und im Autoklaven konsolidiert.
Schweißen
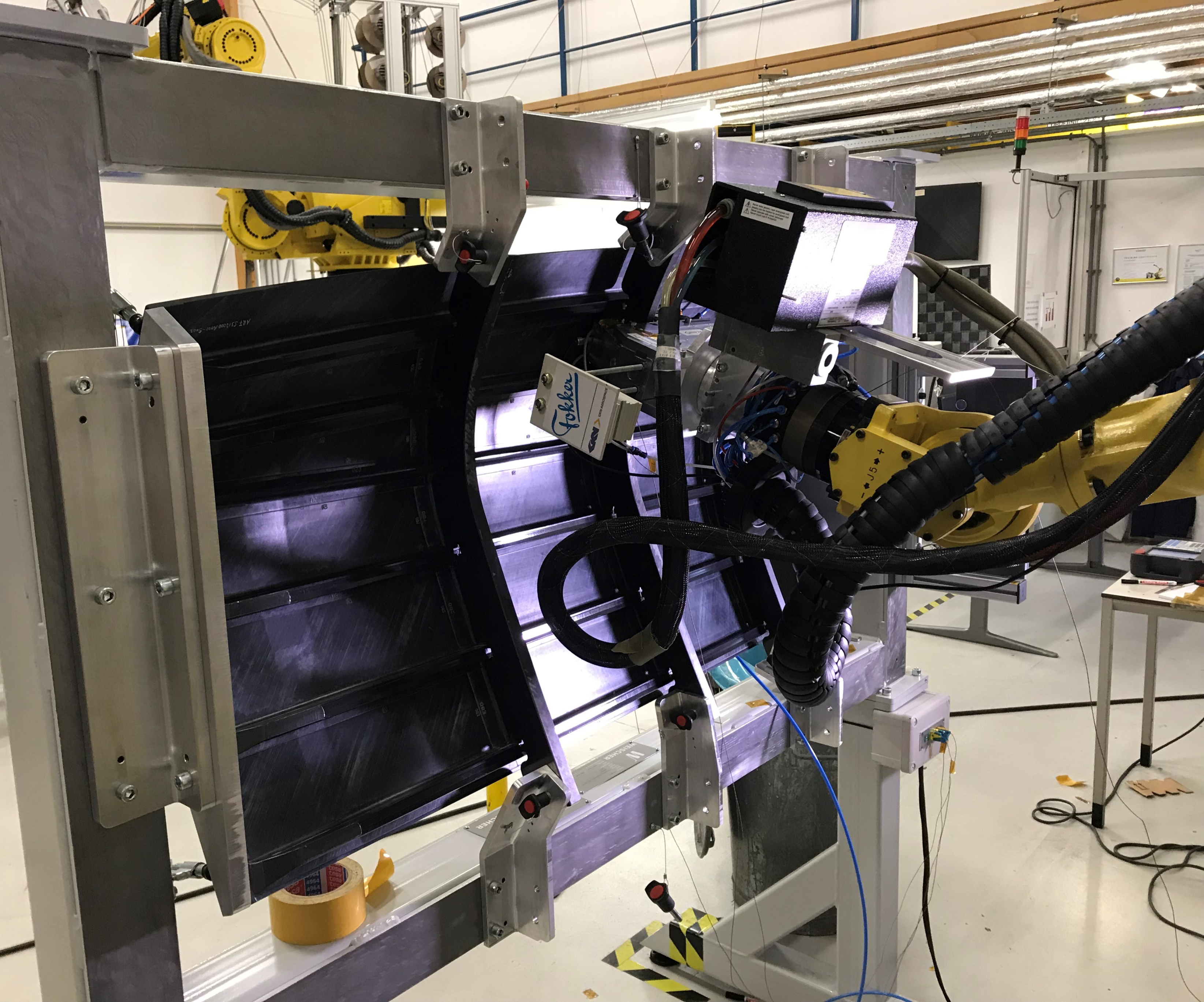
Automatisiertes Schweißen. Als Beitrag zur Wirtschaftlichkeit der thermoplastischen Verbundwerkstoff-Rumpfplatte hat GKN Fokker ein Roboterschweißverfahren entwickelt und eingesetzt. Quelle | GKN Fokker
Die Kombination aus Orthogitter- und Stoßfugen-Konstruktion ermöglicht eine befestigungsfreie Verbindung von Orthogitter und Rahmen durch Schweißen. Während der TAPAS2-Phase wurden mehrere Schweißtechnologien von TAPAS-Teammitgliedern entwickelt, darunter Induktions-, Leitungs- und Ultraschallschweißtechnologien. Bei der Gulfstream-Platte wurde Konduktionsschweißen verwendet, um den Rahmensteg mit dem umlaufenden Schaufelstringer zu verbinden. Diese Aufgabe wird mit dem an einem Roboter montierten Schweißkopf ausgeführt – eine weitere Entwicklung, die zu einer kostengünstigen Herstellbarkeit beiträgt.
Ein Schritt von mehreren
GKN Fokker begann seine Zusammenarbeit mit Gulfstream im Jahr 2017 und erstellte Designkonzepte für das Rumpfpaneel. In den Jahren 2018 und 2019 folgten Design und Herstellung mehrerer gebogener Platten, wobei der erste Meilenstein-Demonstrator auf der diesjährigen JEC World präsentiert wurde.
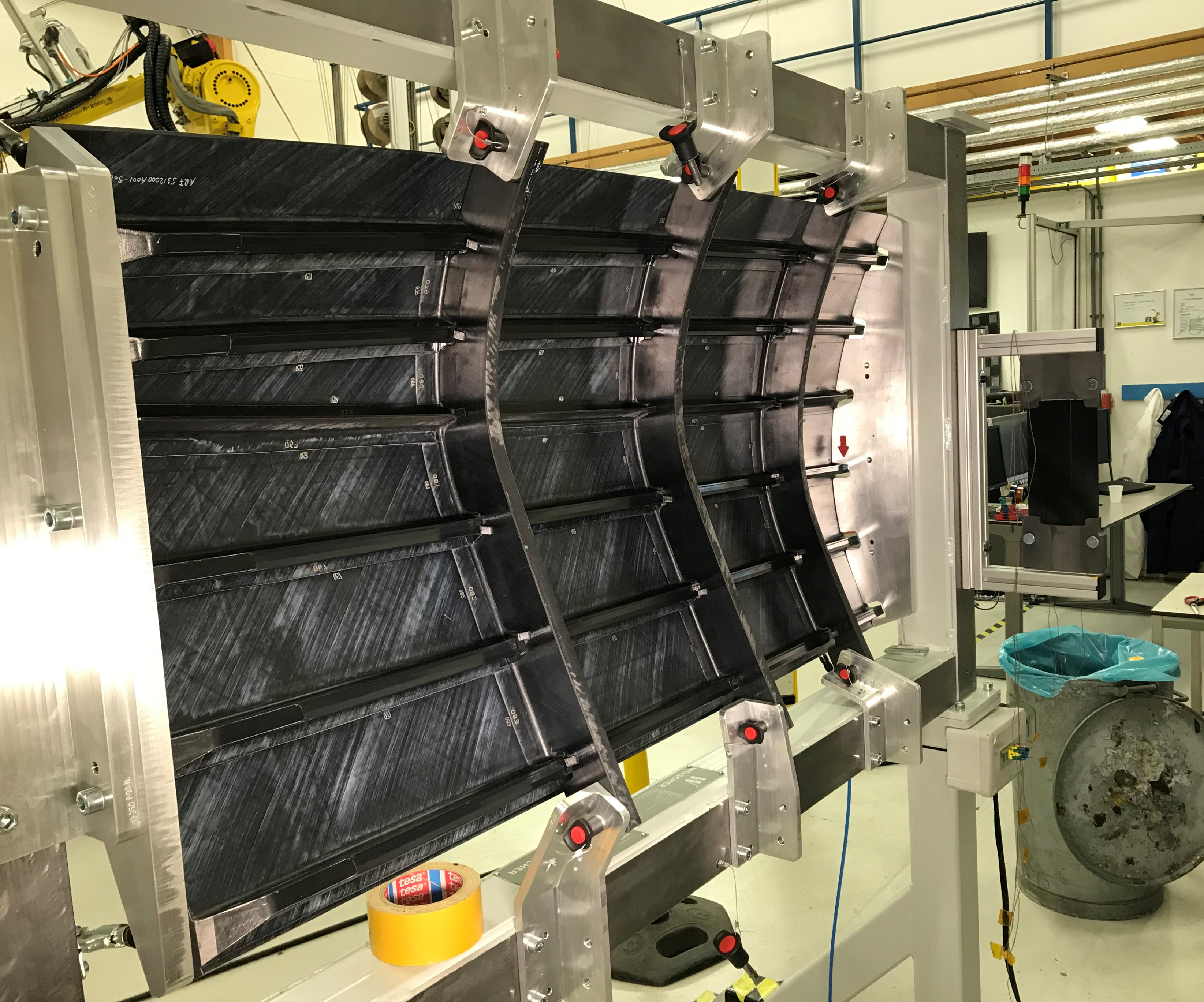
Abgeschlossene Komponente. Mit an die umlaufenden Blattstringer geschweißten Rahmenelementen ist die Gulfstream-Rumpfplatte bereit für Tests, Bewertungen und Weiterentwicklungen, während die Unternehmen auf die Produktion von thermoplastischen Verbundrümpfen hinarbeiten. Quelle | GKN Fokker
GKN Fokker baut weiterhin Panels und erwartet, noch in diesem Jahr TRL4 (Komponentenvalidierung) zu erreichen. „Wir diskutieren derzeit den Weg zur Vollreife“, berichtet Offringa. Chapman weist darauf hin, dass das Panel-Design nicht auf eine bestimmte Plattform abzielt, und berichtet, dass Panel-Tests dazu beitragen werden, Gulfstreams Verständnis der Materialeigenschaften und -leistung zu vertiefen. In Bezug auf den breiteren Geschäftsszenario für Primärstrukturen aus thermoplastischen Verbundwerkstoffen, einschließlich der Leistung des Jets, der Herstellungskosten, der Nutzungskosten und der Haltbarkeit, bemerkt Chapman:„Wir werden diese besser verstehen, wenn wir auf dem Weg der Forschung und Entwicklung weiter voranschreiten. Im Moment liegt unser Fokus darauf, diese komplexen Formen kostengünstig herzustellen.“
Harz
- Covestro verstärkt Investitionen in thermoplastische Verbundwerkstoffe
- Graphenverstärkte thermoplastische Masterbatches auf den Markt gebracht
- Solvay erweitert die Kapazität von thermoplastischen Verbundwerkstoffen
- Tarifgespräche nehmen eine neue Wendung
- Thermoplastische Verbundwerkstoffe bei Oribi Composites:CW Trending, Episode 4
- DLR-Institut für Konstruktion und Konstruktion steigert Reifegrad von thermoplastischen Rumpfstrukturen aus Verbundwerkstoff
- Suprem erweitert thermoplastische Fähigkeiten
- Schweißen von thermoplastischen Verbundwerkstoffen
- Designer müssen die Trends der Druckgussindustrie nutzen
- Designtipps für Spritzguss