Paris Air Show 2019:Höhepunkte
Static Display des kunststoffintensiven Militärflugzeugs Airbus A400M auf der Paris Air Show 2019. Quelle | CW
Die Erwartungen an die Paris Air Show 2019 (17. bis 23. Juni) waren gemischt. Es wurde gehofft, Boeing würde mehr Grundlagen für das New Midsize Aircraft (NMA) schaffen, aber die 737-MAX-Krise hat einen Großteil der Energie und Aufmerksamkeit des Unternehmens verbraucht. Tatsächlich gab Boeing am ersten Tag der Flugschau eine sehr allgemeine Ankündigung zu den Geschäftsbedingungen und veröffentlichte seine 20-Jahres-Prognose für Verkehrsflugzeuge. Nichts auf NMA. Die größte Aufmerksamkeit, die Boeing während der Messe hervorrief, war die Nachricht, dass es 200 737 MAX-Flugzeuge an die International Airline Group (IAG) verkauft hatte.
Airbus hingegen kündigte mit der A321XLR (LR =Long Range) die neueste Version der A320neo an. Die A321XLR, die 2023 in Dienst gestellt werden soll, wird eine Reichweite von 4.700 Seemeilen haben, die durch zusätzliche Kraftstoffspeicherkapazität erreicht werden kann. Airbus sagte, dass die Reichweite des Flugzeugs den Fluggesellschaften günstigere Single-Aisle-Optionen auf Strecken bieten wird, die jetzt hauptsächlich von teureren Double-Aisle-Flugzeugen bedient werden. Zu diesen Strecken gehören New York-Rio, Shanghai-Sydney und Madrid-Dubai.
Trotz des Fehlens von NMA-Neuigkeiten gibt es unter den Verbundwerkstoffunternehmen, die auf der Paris Air Show ausstellen, nach wie vor ein entschiedenes Bemühen, Materialien und Prozesstechnologien zu entwickeln und auszurichten, um die Anforderungen von Boeing und Airbus an die Lieferkette im kommenden Jahrzehnt zu erfüllen. Dazu gehören traditionelle duroplastische Prepregs mit Autoklav-Aushärtung, Flüssigharzinfusion von trockenen Fasern mit Aushärtung außerhalb des Autoklaven, thermoplastische Verbundwerkstoffe und additive Fertigung. Die Erwartungshaltung in der gesamten Lieferkette ist spürbar.
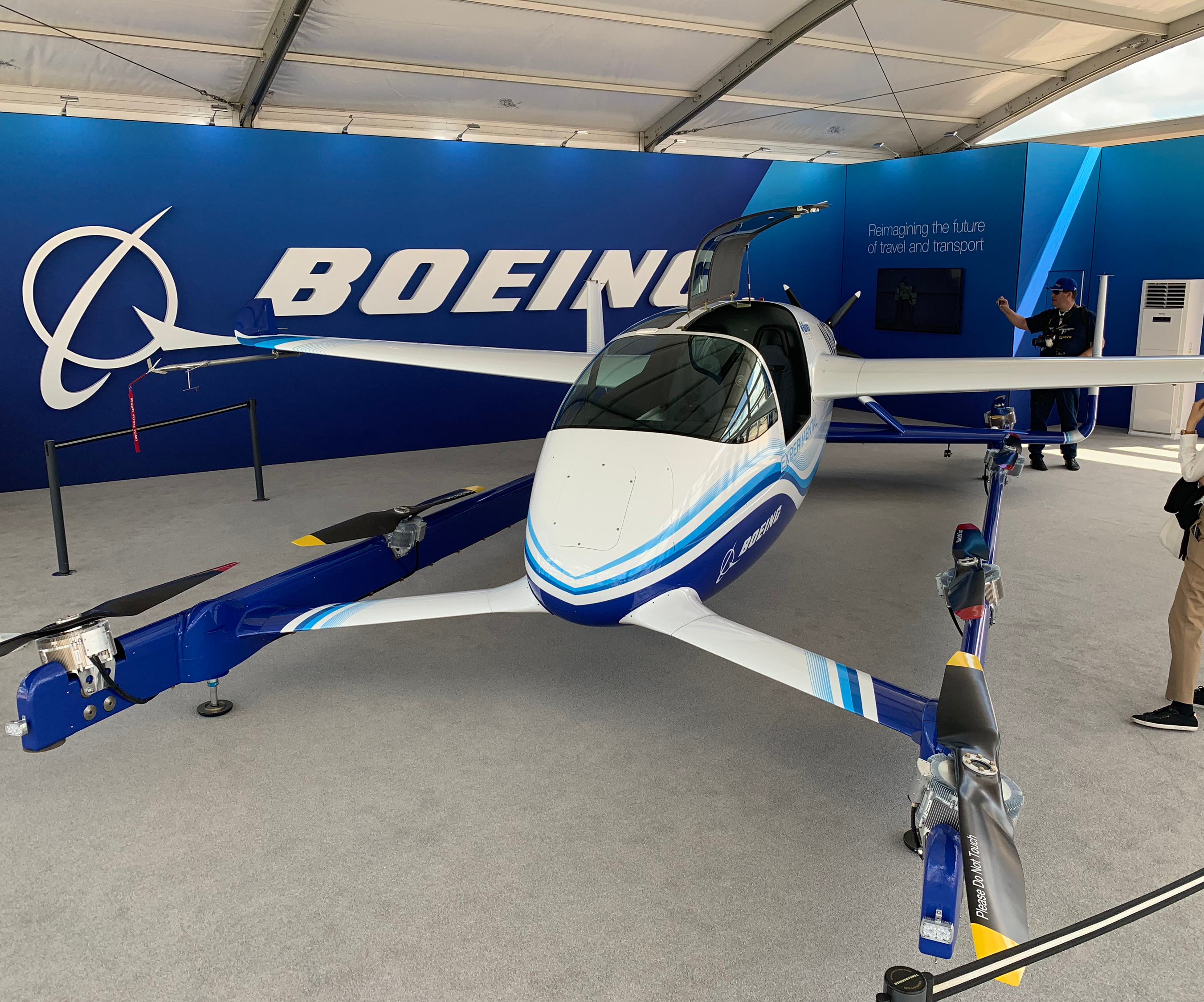
Auf der Fluglinie gab es das übliche Aufgebot an kommerziellen, militärischen und zivilen Flugzeugen mit täglichen Flugvorführungen. Bemerkenswert in der Luft waren Demonstrationen von elektrisch angetriebenen Flugzeugen, die einen starken und leisen Kontrast zu dem ohrenbetäubenden Gebrüll bildeten, das mit den Kampf- und Verkehrsflugzeugen verbunden war. In den statischen Displays gab es eine Reihe von EVTOL-Booten (elektrischer vertikaler Start und Landung), die auf den städtischen Mobilitätsmarkt ausgerichtet waren. Insbesondere dieser Flugzeugtyp erweist sich als bedeutendes Ziel von Verbundmaterialien, die für den elektrisch angetriebenen Flug notwendig sind. Das Produktionsvolumen einiger dieser Plattformen wird jedoch wahrscheinlich in die Tausende gehen pro Jahr, was Material- und Prozesstechnologien mehr in Richtung eines automobilähnlichen Produktionsmodells treibt. Allerdings stecken EVTOLs noch in den Kinderschuhen, insbesondere angesichts der noch zu überwindenden regulatorischen, Qualifikations- und Luftraummanagementhürden.
Unten sind die Highlights der Show.
Spirit AeroSystems. Die weltweit größte Flugzeugzelle, Spirit AeroSystems (Wichita, Kan. US), startete die Show am frühen Montagmorgen mit einer Pressekonferenz, in der die Einführung ihrer ASTRA-Rumpfplatte (Advanced Structures Technology and Revolutionary Architecture) angekündigt wurde, die zeigen soll, wie ein vollständig zusammengesetzter Der Rumpf könnte so ausgelegt werden, dass er die Leistungs-, Geschwindigkeits- und Kostenanforderungen eines Single-Aisle-Flugzeugs der nächsten Generation erfüllt. Das Design und die Herstellung dieses Panels werden hier in einer eigenständigen Geschichte behandelt.
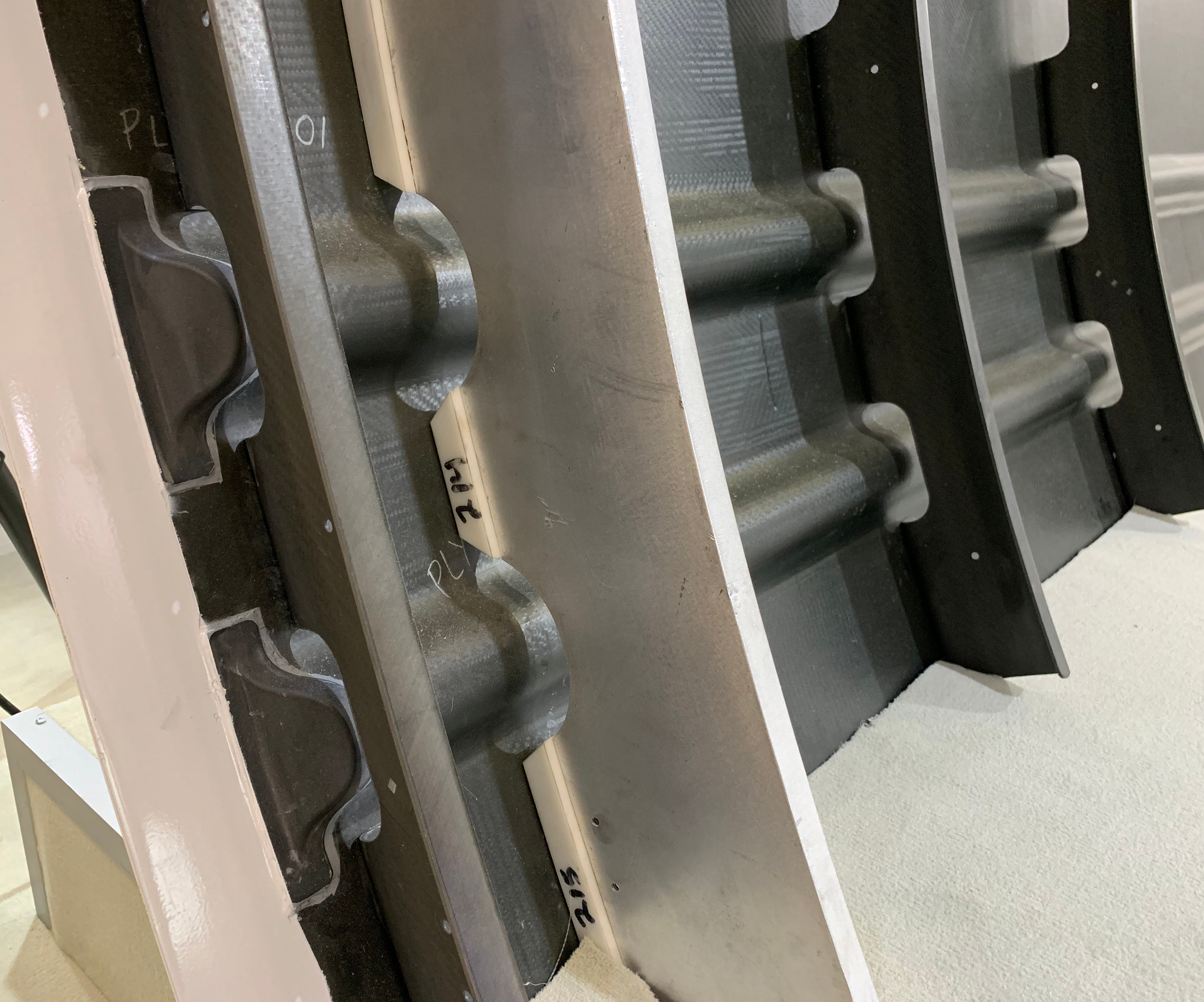
MTorres. Am Stand von MTorres (Torres de Elorz, Navarra, Spanien) wurde eine weitere bemerkenswerte Verbundtafel auf der Messe gefunden. Diese rippenversteifte „Gitter/Haut-Struktur“, die durch Harzinfusion trockener Kohlefasern hergestellt wird, ist eigentlich die Idee von Stephen Tsai, Veteran der Verbundwerkstoffe und emeritierter Professor für Luft- und Raumfahrt an der Stanford University, der am MTorres-Stand war erkläre es. Tsai sagte, er habe dieses Design vor einigen Jahren entworfen und es auf der Gitter-/Haut-Struktur basiert, die bei der Herstellung der Vickers Wellington verwendet wurde , ein britischer Bomber aus dem Zweiten Weltkrieg, hergestellt von Vickers-Armstrongs und berühmt für die Aufrechterhaltung der strukturellen Integrität bei Abstürzen. Um dieses Design in einer Verbundanwendung zum Leben zu erwecken, hat Tsai die Rippen in einer Gitterstruktur entworfen, wobei jede Rippe eine feste Breite und Höhe hat und der Abstand zwischen den Rippen ebenfalls festgelegt ist.
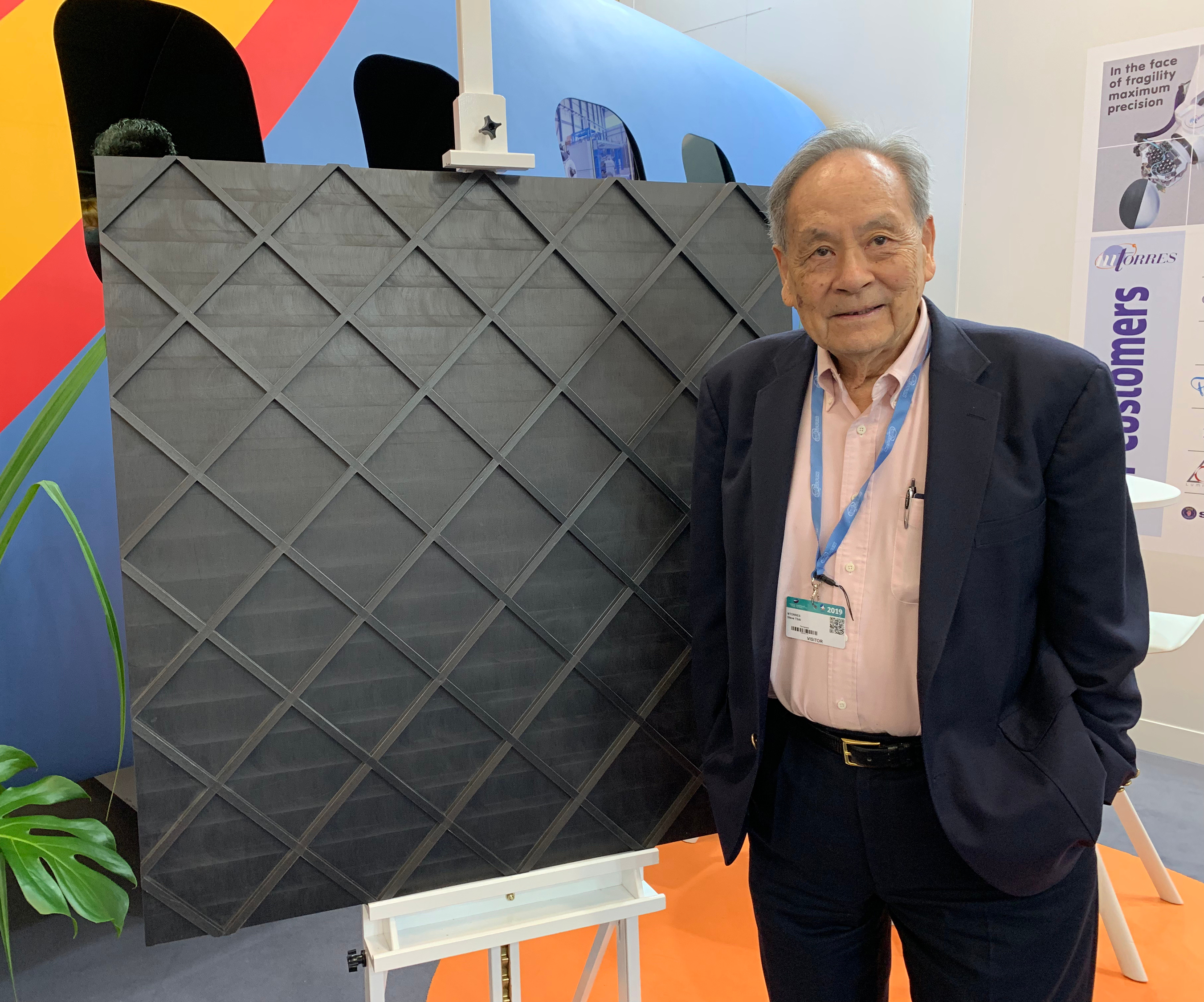
Steve Tsai steht mit der rippenverstärkten Platte, die er entworfen hat und MTorres half ihm bei der Herstellung. Der entscheidende Faktor ist die genaue Faserplatzierung zum Aufbau der Rippen. Quelle | CW
Die Herausforderung seines Entwurfs, sagte Tsai, bestand darin, Rippenkreuzungen zu entwickeln, die großen mechanischen Belastungen standhalten konnten. Was er entwickelte, war eine Rippenarchitektur, die Kohlefaserbänder verwendet, die kontinuierlich in eine Richtung (benennen Sie es A) und diskontinuierlich in die sich kreuzende Richtung (benennen Sie es B) gelegt werden. Dann würden für die nächste Schicht Bänder diskontinuierlich in A-Richtung und kontinuierlich in B-Richtung platziert. Dieses Muster würde fortgesetzt, bis die gewünschte Dicke der Rippe erreicht ist. Auf diese Weise würde jeder Rippenstoß immer von einem durchgehenden Band gekreuzt. Sobald die Rippen in das Werkzeug eingebaut sind, wird eine Haut über eine automatisierte Faserplatzierung (AFP) oder eine automatisierte Tapelegung (ATL) darüber gelegt und die gesamte Struktur wird mitgehärtet.
Die Vorteile dieses Designs, so Tsai, sind vielfältig, aber der wichtigste ist, dass es "schwer ist, dass ein Schaden über den lokalisierten Bereich hinausgeht", was bedeutet, dass ein Riss, der sich in der Haut ausbreitet, nicht leicht über eine der Rippen hinaus wandern kann, die das betroffenen Regionen. Tsai sagte auch, dass die Gitter-/Haut-Struktur sehr gewichts- und materialeffizient ist. Dennoch stellte er fest:"Dies ist einfach zu entwerfen, aber schwer herzustellen." Hier kommt MTorres ins Spiel.
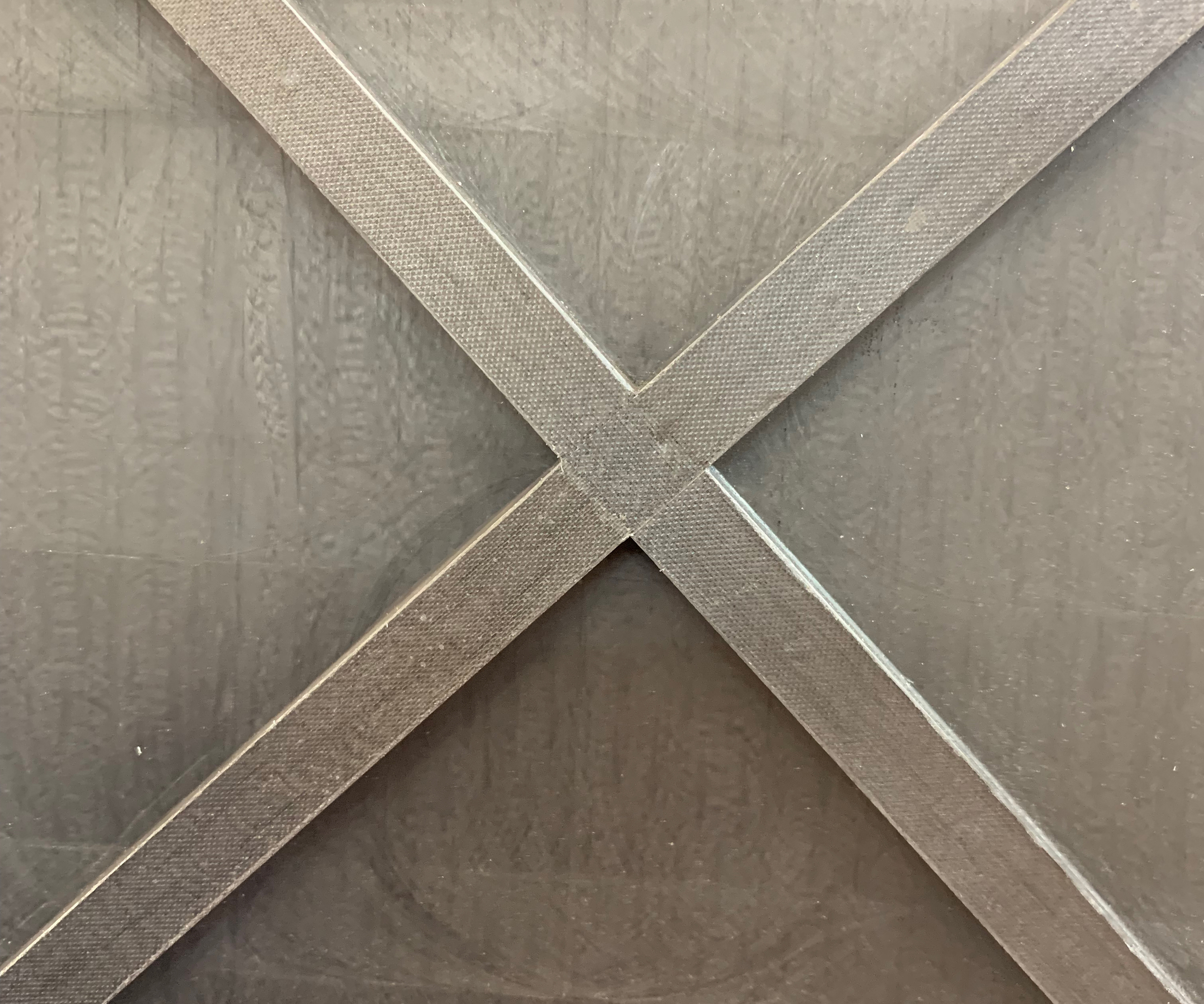
Tsai sagte, der limitierende Faktor bei der Herstellung seines Plattendesigns sei die Platzierung der Rippenbänder gewesen. Um vollständig industrialisiert zu werden, war eine Schnittgeschwindigkeit und -genauigkeit bei der Bandplatzierung erforderlich, die bis vor kurzem nicht möglich war. Tsai wandte sich jedoch mit seinem Entwurf an MTorres und fragte, ob der ATL/AFP-Spezialist die Aufgabe übernehmen könne. Iñigo Idareta, Abteilungsleiter Sonderprojekte im Unternehmen, und das Composites-Team von MTorres wurden mit der Aufgabe beauftragt und arbeiteten mit Tsai zusammen, um die Technologien von MTorres an die Anwendung anzupassen. Es gebe zwei Herausforderungen, sagte Idareta auf der Flugschau:die Feinabstimmung der Schnittgeschwindigkeit und -genauigkeit bei der Bandplatzierung, wobei die AFP-Cut-on-the-Fly-Fähigkeit von MTorres entscheidend war, um eine konstant hohe Auflegegeschwindigkeit aufrechtzuerhalten; und Entwicklung von Werkzeuglösungen, die den Aufbau jeder Rippe ermöglichten, ohne dass die Rippe die Stapelintegrität verliert. Darüber hinaus war die Verwendung des MTorres-eigenen Trockenkohlefaserformats für AFP-Anwendungen erforderlich, um diese anspruchsvolle Infusion zu ermöglichen. Alle seien erreicht worden, sagte Idareta. Basierend auf dem Design von Tsai wurde auch die Verwendung einer schrägen Faseranordnung der vierlagigen und etwa 1,2 mm dicken Verkleidung der Verkleidung erreicht.
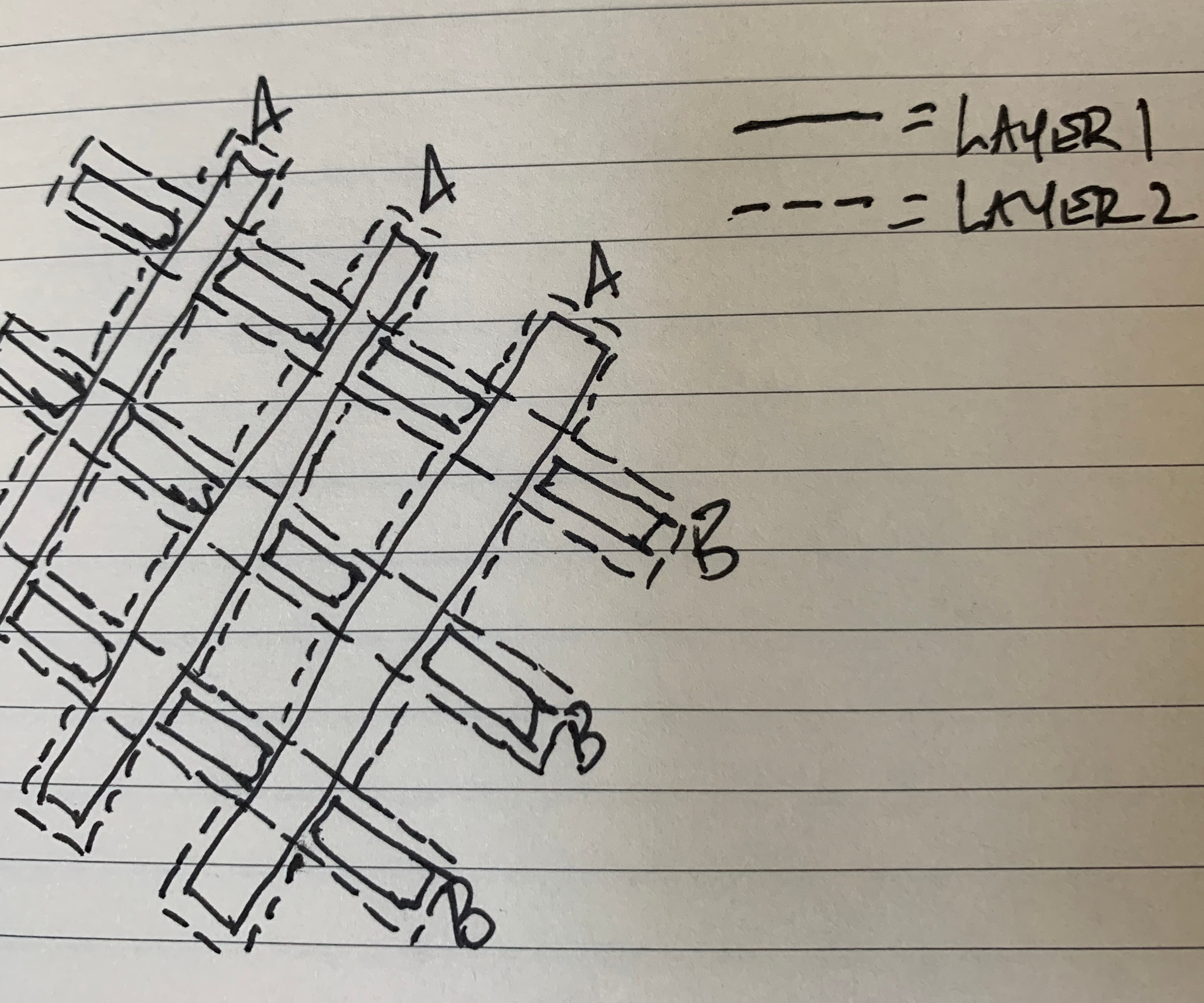
Die verwendete Kohlefaser war ein trockenes 50K-Material von Mitsubishi Chemical Carbon Fiber &Composites Inc. (Sacramento, Kalifornien, USA), das hauptsächlich ausgewählt wurde, weil es zufällig das Material war, das MTorres zur Verfügung hatte. Das Harz war ein „Standard“-Epoxidharz in Industriequalität. Idareta sagt, dass das Panel von Alan Nettles bei der NASA getestet wurde und gut funktionierte. Insbesondere die Rippen-Haut-Verklebung sei ausgezeichnet. Tsai räumte ein, dass die Schwachstelle der Platte die Rippenverbindung ist, bei der es sich um ein Kreuzlagenlaminat [0/90] handelt. Die Rippen waren alle [0]. Die Verbindungen hatten also etwa die Hälfte der einachsigen Zugfestigkeit und etwas mehr als die Hälfte der einachsigen Druckfestigkeit. Trotz dieser Schwäche ist die Gitter-/Hautstärke mehr als doppelt so hoch wie die aktuelle Aluminiumtechnologie des gleichen Designs, das zusätzliche geringere Gewicht der Verbundwerkstoffe nicht mitgerechnet. Tsai sagte auch, dass Aluminium dreimal so viel wiegen würde, um die gleichen Festigkeitseigenschaften wie durch sein Design zu erreichen.
Was kommt als nächstes für diese Technologie? Tsai sagte, es sei „einsatzbereit“ und listete mehrere mögliche Teiletypen auf:Rumpfstrukturen, Trägerraketen, Autopaneele, Batteriegehäuse. Idareta sagte, MTorres arbeite an der Iteration des Designs, einschließlich der Entwicklung eines gebogenen Panels und eines Full Barrel Panels. Beide, sagte er, sind in Reichweite.
Außerdem können verschiedene Aspekte des Designs von Tsai modifiziert werden, um eine Vielzahl von Lastfällen zu erfüllen. Dazu gehören Rippenbreite, Rippenhöhe, Schnittwinkel und Abstand zwischen Rippen. Obwohl MTorres Infusion verwendete, um die auf der Flugschau ausgestellte Platte herzustellen, könnte sie auch mit traditionellem Duroplast-Prepreg hergestellt werden.
GKN Aerospace. Der Spezialist für kommerzielle Tragflächen, GKN Aerospace (Redditch, UK), gab auf der Airshow bekannt, dass er die ersten Teile für seinen Teil der Arbeit am Airbus Wing of Tomorrow-Programm, ein fünfjähriges (2018-2022), firmenübergreifendes, britisches Programm hergestellt hat Katapultanstrengungen zur Entwicklung von Materialien und Prozesstechnologien für die Hochgeschwindigkeits-Fertigung (100 pro Monat) von harzverstärkten Kohlefaser-Verbundstoffflügeln, die in einem Single-Aisle-Flugzeug der nächsten Generation eingesetzt werden sollen.
Paul Perera, VP Technology bei GKN Aerospace, war auf der Airshow und informierte über das Programm. Er sagte, GKN beschäftigt derzeit 60 Mitarbeiter, die an den Holmen und Rippen für den Flügel arbeiten, wobei der Großteil der Arbeit vom Global Technology Center von GKN aus erledigt wird, das später in diesem Jahr in neue Einrichtungen in Filton, Großbritannien, umzieht.
Der Holm wird von GKN trocken gelegt und dann infundiert. Die Rippen werden sowohl aus thermoplastischen Verbundwerkstoffen als auch aus Aluminium hergestellt. Das National Composites Centre (Bristol, Großbritannien) arbeitet für Wing of Tomorrow an mehreren Technologien, darunter iCAP (Digital Capability Acquisition Program), um datenbasierte Automatisierungslösungen zu entwickeln, sowie automatisierte Faserschneide- und -platzierungssysteme von Loop Technology (Poundberry , Dorchester, UK), die in der Flügelfertigung eingesetzt werden. Northrop Grumman (ehemals Orbital ATK, Clearfield, Utah, USA) entwickelt Stringer für das Programm. Die unteren Flügelverkleidungen werden von Spirit AeroSystems in seinem Werk in Prestwick, Schottland, hergestellt; Die oberen Flügelhäute werden von Airbus hergestellt. Ziel ist die Lieferung von drei Shipsets an das Airbus-Flügelwerk in Broughton, Großbritannien, zur Montage in den nächsten 18 Monaten, der erste im Juni 2020, der zweite Ende 2020 und der dritte Anfang 2021. Letztendlich, wenn das Programm voranschreitet Wie geplant wird sich die Harzinfusion als praktikables Verfahren für die Hochgeschwindigkeitsproduktion eines Verbundflügels für einen Single-Aisle der nächsten Generation erweisen. Laut Perera zeigen 1-Meter-Holmprofile, die im GKN-Werk auf der Isle of Wight, Großbritannien, hergestellt und bewertet wurden, dass die Materialien und das Verfahren für die Anwendung gut geeignet sind.
Perera stellte fest, dass sich ein Großteil des Wing of Tomorrow-Programms um die Automatisierungsentwicklung drehen wird. Tatsächlich, sagte er, wird die Automatisierung ein entscheidender Faktor für die Harzinfusion für die Luft- und Raumfahrtfertigung der nächsten Generation sein.
Solvay-Verbundwerkstoffe. Wenn Sie nach Beweisen suchen, wie sich der Fokus auf die Industrialisierung und Produktionseffizienz der Luft- und Raumfahrtfertigung auf die Materiallieferanten auswirkt, sind Sie bei Solvay Composite Materials (Alpharetta, Georgia, USA) genau richtig, das sich in der Mitte eines mehrjährigen Jahres befindet Bemühungen um eine Neubewertung, wo und wie es Kunstharze, Bänder und Prepregs in Luft- und Raumfahrtqualität herstellt. Der Schwerpunkt von Solvay liegt auf der Entwicklung einer Betriebsstrategie, die sich auf Einrichtungen konzentriert, die weniger Produktnummern auf hochspezialisierten Geräten produzieren, die die Geschwindigkeits- und Qualitätsanforderungen von Flugzeugen der nächsten Generation erfüllen. Marc Doyle, Executive VP Aerospace von Solvay, sagt, dass die neue Anlage des Unternehmens in Wrexham, Wales, Großbritannien, ein Symbol für diese Bemühungen ist. Das im September 2018 eröffnete Werk produziert nur zwei Produktnummern (Klebstoffe), aber in einem hochstrukturierten, hochoptimierten, automatisierungsdominierten Umfeld, das auf die Just-in-Time-Anforderungen seiner Kunden ausgerichtet ist. Das Unternehmen erwartet, diesem Modell bei allen neuen Einrichtungen zu folgen und wird versuchen, auch bestehende Anlagen umzurüsten.
Im Bereich der Materialinnovationen hob Solvay zwei bemerkenswerte Bemühungen hervor – eine konzentrierte sich auf Thermoplaste und die andere auf Kohlefasern. Mike Blair, Executive Vice President für Forschung und Innovation, sagte, eine der größten Herausforderungen/Chancen von Thermoplasten sei ihr Hochtemperatur-Delta; das heißt, die hohen Prozesstemperaturen von Thermoplasten können in Teilen beim Abkühlen, insbesondere bei großen Teilen, Probleme mit dem Wärmeausdehnungskoeffizienten (CTE) verursachen. Das Ziel? Ändern Sie die Polyketonchemie, um die Prozesstemperaturen zu senken, ohne den Glasübergang zu beeinträchtigen (Tg ) Temperatur. Darüber hinaus sucht das Unternehmen nach Möglichkeiten, die Verarbeitbarkeit und Handhabung seiner thermoplastischen Kunststoffe in automatisierten Anlagen zu verbessern. „Unsere standardmäßigen PEEK- und PEKK-Materialien funktionieren tatsächlich gut“, sagte Blair. „Wir müssen sie nur modifizieren, um sie anpassungsfähiger zu machen.“
Ebenso faszinierend ist die Innovation rund um Carbonfasern. Im Jahr 2017 erwarb Solvay den Hersteller von Large-Tow-Polyacrylnitril (PAN) European Carbon Fiber GbmH (Kelheim, Deutschland), wodurch Solvay eine neue und gesunde Lieferung von PAN für 50.000 Tow-Carbonfasern erhielt. Vor diesem Hintergrund stellte sich die Herausforderung:Kann eine Large-Tow-Carbonfaser so formatiert werden, dass sie die Leistungsmerkmale einer Small-Tow-Carbonfaser mit mittlerem Modul (IM) bietet? Blair sagte, dass die Idee zum Nachdenken anregt, aber nicht trivial. Er stellte fest, dass die bloße Handhabung von 50.000-Tow-Fasern an und für sich die Faser beschädigen kann. Ohne zu viel darüber zu verraten, was Solvay im Sinn hat, sagte Blair, dass das Unternehmen an einer Handhabungstechnologie arbeite, die Faserschäden vermeiden soll. „Ein aggressiver Zeitplan dafür“, sagte er, „wäre 18 Monate.“
Toray Advanced Composites. Das ehemalige TenCate Advanced Composites wurde nun vollständig von Toray übernommen und geht seit März an Toray Advanced Composites (Morgan Hill, Kalifornien, USA). Steve Mead, Geschäftsführer, sagt, dass EVOTL derzeit für das Unternehmen besonders aktiv ist (Duroplaste und Thermoplaste). Er stellte fest, dass „wir Material für aufkommende EVOTL-Programme liefern“ und fügte hinzu, dass „Verbundwerkstoffe aufgrund des parasitären Batteriegewichts dieser Flugzeuge ein echter Wegbereiter sind. Nichtverbundwerkstoffe sind keine Option.“ Die Kombination aus Fertigung in Luft- und Raumfahrtqualität zu Automobilpreisen ist faszinierend, sagte er.
Eviation. Zu den hochkarätigen Vorstellungen auf der Paris Air Show gehörte Alice , ein vollelektrisches Vollkompositflugzeug, das von Eviation (Kadima-Tzoran, Israel) eingeführt wurde. Alice ist ein neunsitziges Regionalverkehrsflugzeug mit einer Reichweite von 1.000 Kilometern bei einer Reisegeschwindigkeit von 240 Knoten. Das Flugzeug verfügt über einen primären Schubpropeller am Heck und zwei zusätzliche Schubpropeller an den Flügelspitzen, um den Luftwiderstand zu reduzieren und Redundanz zu schaffen. Omar Bar-Yohay, CEO von Eviation, stellte das Flugzeug vor und sagte, dass Flugtests in Moses Lake, Washington, USA, durchgeführt würden, gefolgt von der US-amerikanischen Federal Aviation Administration (FAA)-Zertifizierung Ende 2020 oder Anfang 2021. Das Flugzeug wird eine Listenpreis von 4 Millionen US-Dollar und Bar-Yohay sagte, dass das Unternehmen durch Zertifizierung und frühe Produktion vollständig finanziert ist.

Das auf der Messe ausgestellte Fahrzeug war ein nicht fliegender Prototyp, der erst eine Woche zuvor zusammengebaut wurde. Wo und wie dieses Flugzeug letztendlich produziert wird, bleibt abzuwarten. Der Prototyp seinerseits wurde aus Verbundstrukturen verschiedener Lieferanten zusammengebaut. Einer davon ist Multiplast (Vannes, Frankreich), Teil der Carboman Group SA (Vannes), ein Zusammenschluss aus fünf Unternehmen, zu dem auch Decision (Ecublens, Schweiz), SNE SMM (Lanester, Frankreich), Plastinov (Samazan, Frankreich) und Plastéol (Samazan). Multiplast, das auf eine Geschichte in der Herstellung von Schiffsstrukturen zurückblickt, hat den Rumpf für die Alice hergestellt aus Autoklaven (OOA) unter Verwendung einer Sandwichstruktur mit Nomex-Wabenkern. Der Rumpf wurde in zwei Hälften gebaut, basierend auf einer Steuerbord/Backbord-Mittellinienkonfiguration, wobei die beiden Rumpfsektionen miteinander verbunden/befestigt wurden (siehe Zeitraffervideo unten). Multiplast weiß nicht, ob es den Auftrag für die Serienfertigung des Handwerks erhält, prüft jedoch, was aus Material- und Prozesssicht erforderlich wäre, um die Fertigung zu industrialisieren. Flügel und Bauchverkleidungen für die Alice wurden von Composite Cluster Singapore (CCS) geliefert.
Stratasys. Der Maschinenspezialist für additive Fertigung (AM) Stratasys (Eden Prairie, Minnesota, USA) betonte auf der Paris Air Show seine Fähigkeit, AM für die Teile- und Werkzeugproduktion einzusetzen. Bei der Herstellung von Verbundwerkstoffen lag der Schwerpunkt auf Werkzeugen. Das Unternehmen hatte auf seinem Stand zwei Formen, die mit Stratasys-Maschinen hergestellt wurden. Das Material ist ULTEM 1010 von SABIC, ein unverstärktes Polyetherimid (PEI), das für die Autoklavenverarbeitung geeignet ist. Die erste Form diente der Herstellung einer Flügelvorderkante aus Kohlefaser und verfügt über In-Mold-Elektroden, um die Heizkapazität des Prepregs zu erhöhen und die Aushärtezeit von 1,5 Stunden auf nur 10 Minuten zu verkürzen. Der andere Teil war ein Layup-Tool von Boom Aerospace (Centennial, Colorado, U.S.) zur Herstellung von Kleinteilen für die Overture Überschallverkehrsflugzeug, das das Unternehmen entwickelt. Laut Scott Sevcik, VP Manufacturing Solutions bei Stratasys, hat Boom bereits zwei Stratasys-Maschinen im Einsatz, eine dritte wird noch in diesem Jahr ausgeliefert. Sevcik sagte, dass Stratasys voraussichtlich noch in diesem Jahr zwei neue kohlenstofffaserverstärkte Schnittmaterialien für AM-Anwendungen einführen wird; Stratasys, sagte er, arbeite auch an der Endlosfaserverstärkung für AM.
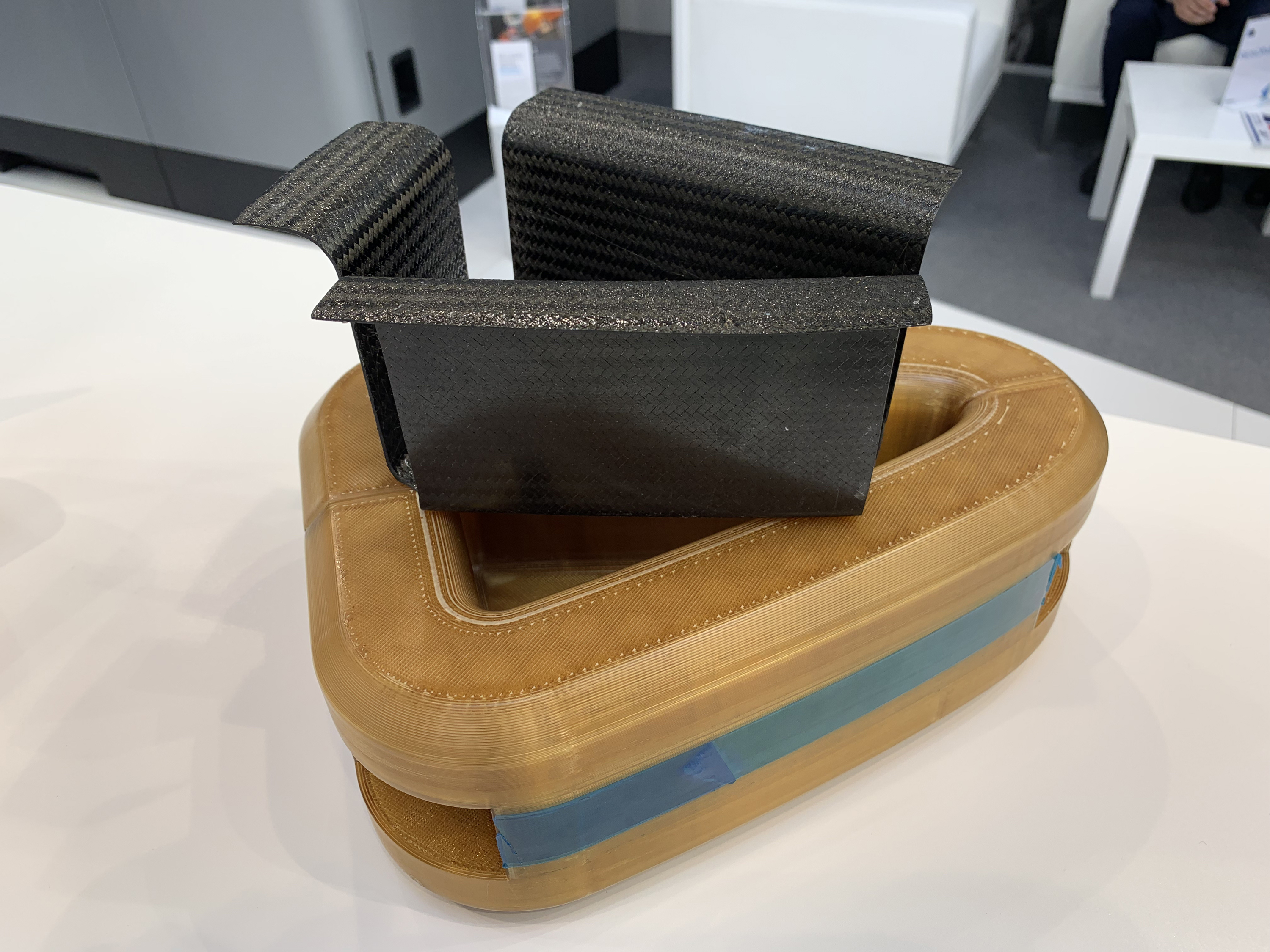
Boom Aerospace. Eine weitere spritzige Ankündigung auf der Paris Air Show kam von Boom Aerospace (Englewood, Colorado, USA), die, wie bereits erwähnt, Overture . entwickelt , ein völlig neues Überschall-Passagierflugzeug. Boom CEO und Gründer Blake Scholl sagte in einer Pressekonferenz, dass Boom kurz vor der Fertigstellung des Verbundwerkstoff-intensiven XB-1 steht , ein subskaliger Prototyp der Ouvertüre die voraussichtlich Ende 2019 eingeführt und irgendwann im Jahr 2020 getestet werden soll. Diese Testflüge, sagte Scholl, sollen Boom helfen, die Konstruktions- und Konstruktionsprinzipien des Flugzeugs zu bewerten und die gewonnenen Erkenntnisse auf die endgültige Konstruktion und Produktion anzuwenden Ouvertüre , die voraussichtlich Mitte der 2020er Jahre in Dienst gestellt wird. Dies ist ein längerer Zeitplan als zuerst von Boom erwartet. „Das ist ein ehrgeiziges Projekt“, sagte Scholl. „Anfangs ist man leicht zu optimistisch.“
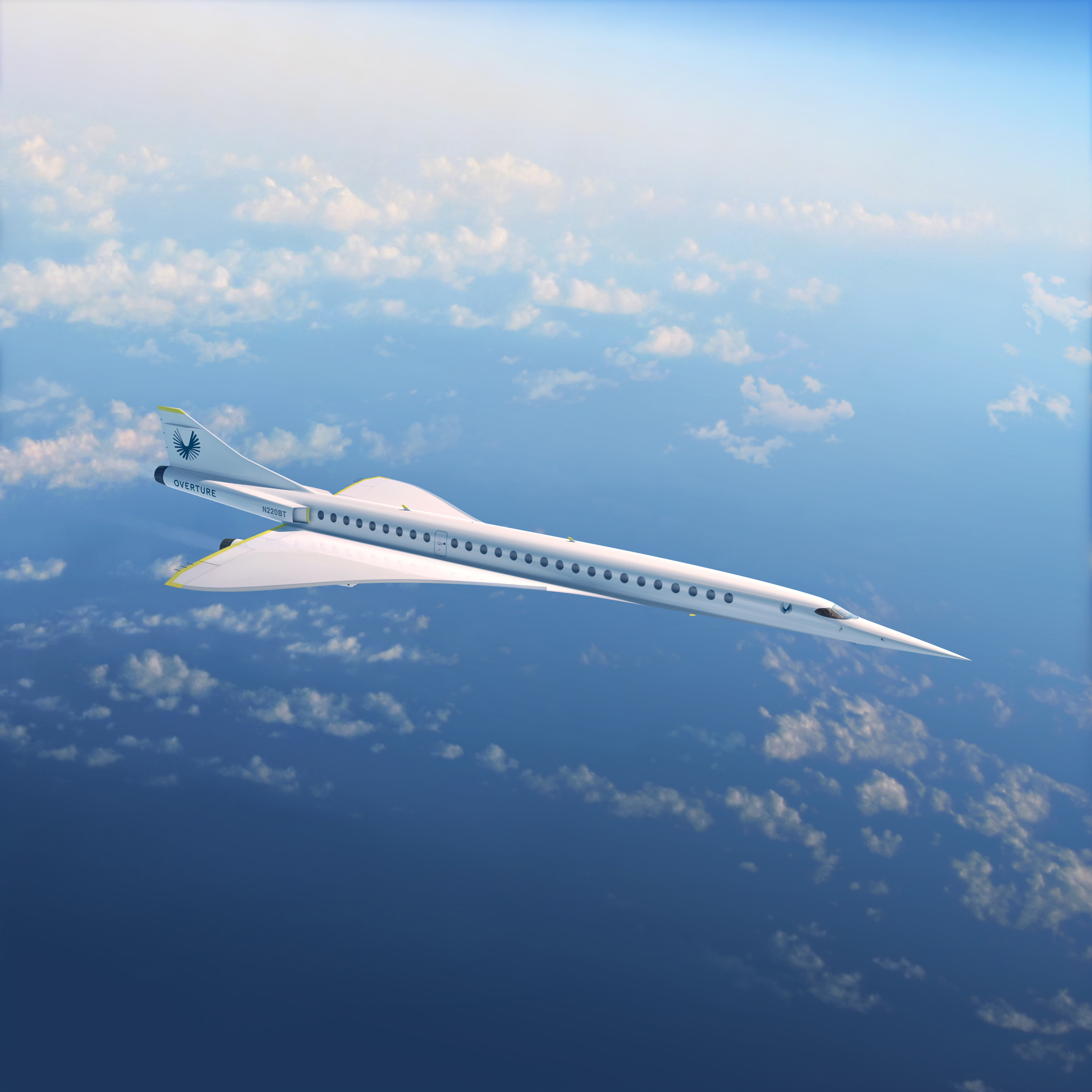
Ouvertüre wird voraussichtlich eine Höchstgeschwindigkeit von Mach 2,2, eine Reiseflughöhe von 60.000 Fuß (19.354 Meter) haben und Passagiere (55-75) in nur 7 Stunden von Sydney nach Los Angeles oder in nur 3,5 Stunden von Washington D.C. nach London bringen. Scholl gab an, dass die Ticketkosten bei Overture . gekostet haben Es wird erwartet, dass sie auf Sitzplatz-pro-Meile-Basis mit den aktuellen Preisen der Fluggesellschaften wettbewerbsfähig sein wird. Scholl sagte auch, dass Ouvertüre wird voraussichtlich eine Technologie namens Prometheus Fuels verwenden, die den Kohlenstoff der Atmosphäre in Benzin oder, im Fall von Boom, in Kerosin umwandelt, wobei Strom aus erneuerbaren Ressourcen verwendet wird. Auf diese Weise, sagte er, wird das Flugzeug einen Null-Kohlenstoff-Überschallflug ermöglichen.
Harz
- Renesas hebt Endpunktintelligenz auf der Embedded World 2019 hervor
- Bett Show 2019 - Besuchen Sie uns auf der Website
- Zerstörungsfreie Inspektion spielt eine Schlüsselrolle auf dem Luftwaffenstützpunkt
- JEC World 2019:Hexcel
- JEC World 2019:Hexion
- SAMPE-Gipfel 19 Paris
- 3 Möglichkeiten, Ihrem Druckluftsystem etwas Liebe zu zeigen
- Atlas Copco wird auf der SEMA Show 2017 ausstellen
- Druckluft hilft bei Urlaubsreisen
- Und das ist ein Abschluss für 2019!