Nanomaterialien:Produkte, Lieferkette ausgereift für Verbundwerkstoffe der nächsten Generation
Das Versprechen von Nanomaterialien, beispiellose mechanische Eigenschaften zusammen mit einer maßgeschneiderten elektrischen und thermischen Leitfähigkeit für Verbundwerkstoffe zu liefern, wird seit Jahrzehnten angekündigt. Aufgrund ihrer einzigartigen Eigenschaften und ihrer enormen Oberfläche haben Nanomaterialien das Potenzial, die Produktleistung über die aktuelle Makroskala hinaus zu steigern Verbundstoffe. Obwohl Nanomaterialien wie Graphen und Kohlenstoff-Nanoröhrchen (CNTs) von einer Reihe von Unternehmen und Websites kommerziell erhältlich sind, ist die weit verbreitete Anwendung in Verbundwerkstoffen nicht so offensichtlich.
Unterdessen entwickeln sich Materialien und Terminologie schnell weiter; CW bietet eine Einführung in aktuelle Nanomaterialien sowie wichtige Entwicklungen bei neuen Materialien und der Lieferkette.
Nanolandschaft für Verbundwerkstoffe
Nanomaterialien können Metall, Keramik, Polymer, Kohlenstoff oder aus natürlichen Quellen wie Cellulose sein. Nanomaterialien bilden einen Verbundstoff, wenn sie zur Verstärkung einer Polymer-, Keramik- oder Metallmatrix verwendet werden, und werden typischerweise nach ihrer Form (Morphologie) als Partikel, Fasern oder Plättchen klassifiziert (siehe „Nanomaterialtypen und -definitionen“ unten). Wenn das Material von Mikrometern abnimmt (10 -6 Meter) in Nanometer (10 -9 Meter) vergrößert sich die Oberfläche, so dass die Nanomaterial-Matrix-Grenzfläche mehr Volumen des Komposits ausmacht. Aus diesem Grund können mit ein bis zwei Größenordnungen weniger Belastung im Vergleich zu Mikromaterialien wie Ruß und gemahlenen Fasern Verbesserungen der Endprodukteigenschaften von 20-50% erreicht werden. Genauso wie die Eigenschaften eines Makroverbundwerkstoffs von der Mechanik an der Faser-Harz-Grenzfläche abhängen, sind das Verständnis und die Kontrolle der Grenzflächen eines Nanoverbundwerkstoffs für die Verwaltung von Materialeigenschaften und Leistung noch wichtiger.
Das Versprechen von Nanomaterialien wurde jedoch durch Schwierigkeiten bei der Skalierung kostengünstiger Herstellungsverfahren hochwertiger Materialien mit minimalen Fehlern behindert. Darüber hinaus war die Erzielung einer homogenen Dispersion von Nanomaterialien in Matrices aufgrund der Tendenz von Nanomaterialien zur Agglomeration eine Herausforderung. Letzteres kann durch Funktionalisierung der Nanomaterialoberfläche überwunden werden. Gängige Techniken, die oft kombiniert werden, umfassen das Modifizieren der elektrischen Ladung des Nanomaterials oder der Matrix, das Modifizieren des pH-Werts oder das Hinzufügen eines Tensids.
Die Verbundwerkstoffindustrie stellt sich einen Nanoverbundstoff typischerweise als eine beliebige Matrix mit einem darin dispergierten Nanomaterial vor. Mikroverbundwerkstoffe können jedoch aufgrund des Primärmaßstabs der Grenzflächen von Nanoverbundwerkstoffen unterschieden werden. Abb. 1 zeigt Beispiele für verschiedene Mikro-/Nano-Komposit-Kombinationen und Schnittstellen. Eine mikroskalige (mikronische) Matrix wird mit Nanopartikeln, Nanofasern oder Nanoplättchen verstärkt, wie in A, B bzw. C zu sehen, während ein Nanokomposit wird als Matrixphase unterschieden, die auf der gleichen Skala gemischt ist als Nanomaterial, wie in E und F gezeigt.
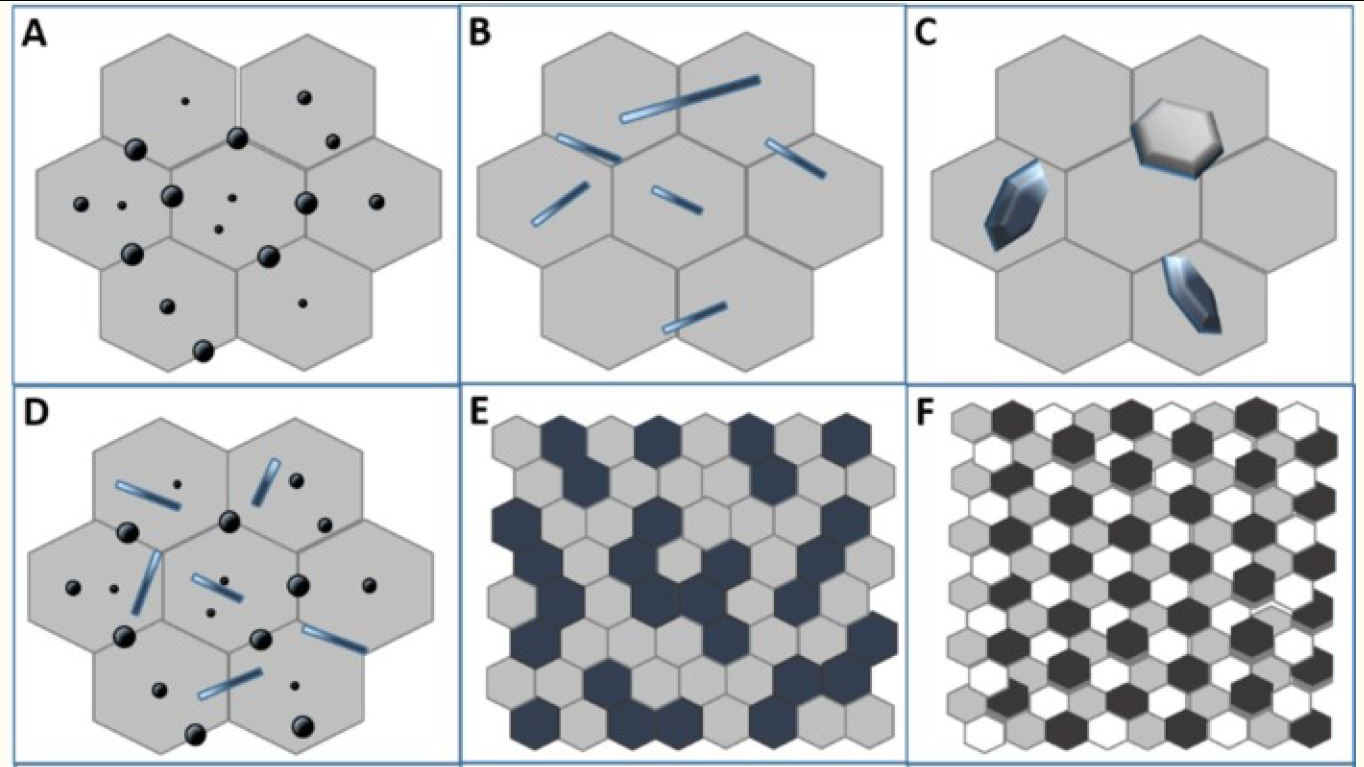
Abb. 1 Gängige Mikro-/Nano-Verbundstrukturen für keramische Materialien. Mikro/Nano-Komposit, umfassend eine Mikronmatrix mit (A) abgerundeten Nanopartikeln, (B) Nanoverstärkungen mit hohem Aspektverhältnis, (C) plättchenartigen Nanoverstärkungen und (D) sowohl abgerundeten als auch länglichen Nanoverstärkungen; (E) zweiphasiger Verbundstoff, hergestellt aus zwei nicht mischbaren ultrafeinen Phasen; (F) mehrphasiger Verbundstoff aus drei (oder mehr) nicht mischbaren Nanophasen. Quelle | „Structural Ceramic Nanocomposites:A Review of Properties and Powders‘ Synthesis Methods“ von Paola Palmero, Nanomaterials (Basel). Juni 2015
2D-Nano- zu 3D-Multifunktionsverbundwerkstoffen
Innerhalb der Nanolandschaft ist die vielleicht aktivste Region die, die 2D-Nanomaterialien umfasst. Das beliebteste davon ist Graphen, das dank seiner außergewöhnlichen Eigenschaften große Popularität erlangt hat. Graphen ist das leichteste Gewicht (0,77 mg/m 2 .) ) und stärkstes bekanntes Material (100-300 mal Stahl), härter als Diamant, aber elastischer als Gummi, mit 100 mal schnellerer Elektronenbeweglichkeit als Silizium, 13 mal besserer elektrischer Leitfähigkeit als Kupfer und einer sehr großen Oberfläche. Graphen scheint in der Lage zu sein, gewisse Lücken in herkömmlichen Eigenschaftsbeschränkungen zu schließen. Zum Beispiel kann Graphen, wenn es Gummi hinzugefügt wird, gleichzeitig die Reifenhaftung erhöhen und den Verschleiß reduzieren. Formel-1-Fans wissen aus dem Wechsel von Rennwagen zwischen weichen Reifen (hoher Grip, weniger Verschleißfestigkeit) und harten Reifen (weniger Grip, mehr Verschleißfestigkeit), dass diese beiden Eigenschaften normalerweise nicht nebeneinander existieren. „Carbon Black war der normale Füllstoff für Gummi in Reifen, aber Graphen bietet eine viel höhere Leistung bei einem viel geringeren Lastfaktor und ersetzt 1-2% Ruß durch nur 0,01% Graphen“, erklärt Terrance Barkan, Executive Director von The Graphene Council (New Bern, NC, USA), eine Ressourcen- und Unterstützungsorganisation der Branche.
Forscher waren bestrebt, diese Materialien weiterzuentwickeln und im letzten Jahrzehnt Hunderte von 2D-geschichteten Nanomaterialien aus Polymeren, Metallen und Kohlenstoffallotropen wie Graphen zu synthetisieren (siehe „Nanomaterialtypen und Definitionen“). Diese 2D-Nanomaterialien können dann kombiniert, zusammengefügt, gestapelt und/oder angeordnet werden, um eine fast unendliche Vielfalt von 3D-Architekturen zu bilden, um neuartige, multifunktionale Materialien zu schaffen. Graphen und andere 2D-Nanomaterialien wurden zu 3D-Architekturen mit großen Porenvolumina, geringer Dichte, verbesserten mechanischen Eigenschaften, hohen spezifischen Oberflächen, schnellem Elektronen- und Massentransport (verwendet beim Kühlen sehr heißer Oberflächen) sowie einzigartigen optischen Eigenschaften und photonischen Fähigkeiten kombiniert .
Früheinsteiger kommen voran
Vertikal ausgerichtete CNT-Folienprodukte von NanoStitch wurden 2015 von N12 Technologies (Somerville, MA, USA) eingeführt. Bei der Verschachtelung in Verbundlaminaten erhöht NanoStitch die interlaminare Scherfestigkeit (ILSS) um>30 % und die Kompression nach dem Aufprall (CAI) um 15 % . CW berichtete im Jahr 2018, dass N12 Technologies zugestimmt hat, die 60 Zoll breite, kontinuierliche CNT-Filmproduktionslinie des University of Dayton Research Institute (UDRI, Dayton, Ohio, USA) als zweite Produktionsstätte zu integrieren. „Wir haben jetzt den Produktionsbetrieb in Kettering, Ohio, vollständig validiert“, sagt Christopher Gouldstone, N12 Director of Production Development. Er sagt, dass eines der größten Anwendungshighlights für NanoStitch im Jahr 2019 darin besteht, offizieller Technologiepartner für Verbundwerkstoffe für das Santa Cruz Syndicate World Cup Mountain Bike Team zu werden. „Nach einem kollaborativen Entwicklungsprozess zur Implementierung von NanoStitch in Santa Cruz Bicycle-Designs fährt das Syndicate diese Saison auf schlagfesten NanoStitch-verstärkten Rädern“, sagt Gouldstone. „N12 wendet NanoStitch weiterhin an, um die Schlag-, Kompressions-, Scher- und Ermüdungseigenschaften von Verbundwerkstoffen für mehrere Märkte, einschließlich Luft- und Raumfahrt und Konsumgüter, zu verbessern. Wir haben auch die Entwicklung für Multifunktionalität vorangetrieben, indem wir die hohe Leitfähigkeit vertikal ausgerichteter CNTs für elektrostatische Erdung, Dehnungsempfindlichkeit und Oberflächenerwärmung nutzen.“
Thermoplastisches Nanokomposit ersetzt Aluminium
Inzwischen einer der ersten kommerziellen Thermoplaste nanocomposites wurde Anfang 2019 von Alpine Advanced Materials LLC (Dallas, Texas, USA) auf den Markt gebracht. HX5 ist ein Hochleistungsmaterial, das entwickelt wurde, um 6061 T6 Aluminium in Luft- und Raumfahrtqualität zu ersetzen und die Leistung zu verbessern und gleichzeitig das Gewicht um bis zu 50 % zu reduzieren. HX5 wird durch eine exklusive Lizenz von Lockheed Martin Corp. (Bethesda, Maryland, USA) vermarktet, wo das Produkt als APEX (Advanced Polymers Engineered for the Extreme) entwickelt und in Teilen für Flugzeuge, Hubschrauber und Amphibientransporter getestet und erprobt wurde Fahrzeuge, Raketen, Raketen und Satelliten.
„Alpine Advanced Materials hat vollen Zugriff und globale Rechte an der APEX-Technologie sowohl für militärische als auch kommerzielle Anwendungen“, sagt Jon Bennett, Vice President of Corporate Development bei Alpine Advanced Materials. „HX5 lässt sich wie Metall bearbeiten, beschichten, lackieren, schweißen und kleben, lässt sich aber im Spritzguss verarbeiten.“ Da Alpine derzeit viele Details nicht teilen darf, CW hat eine Geschichte der Entwicklung des Materials aus öffentlich zugänglichen Informationen zusammengestellt.
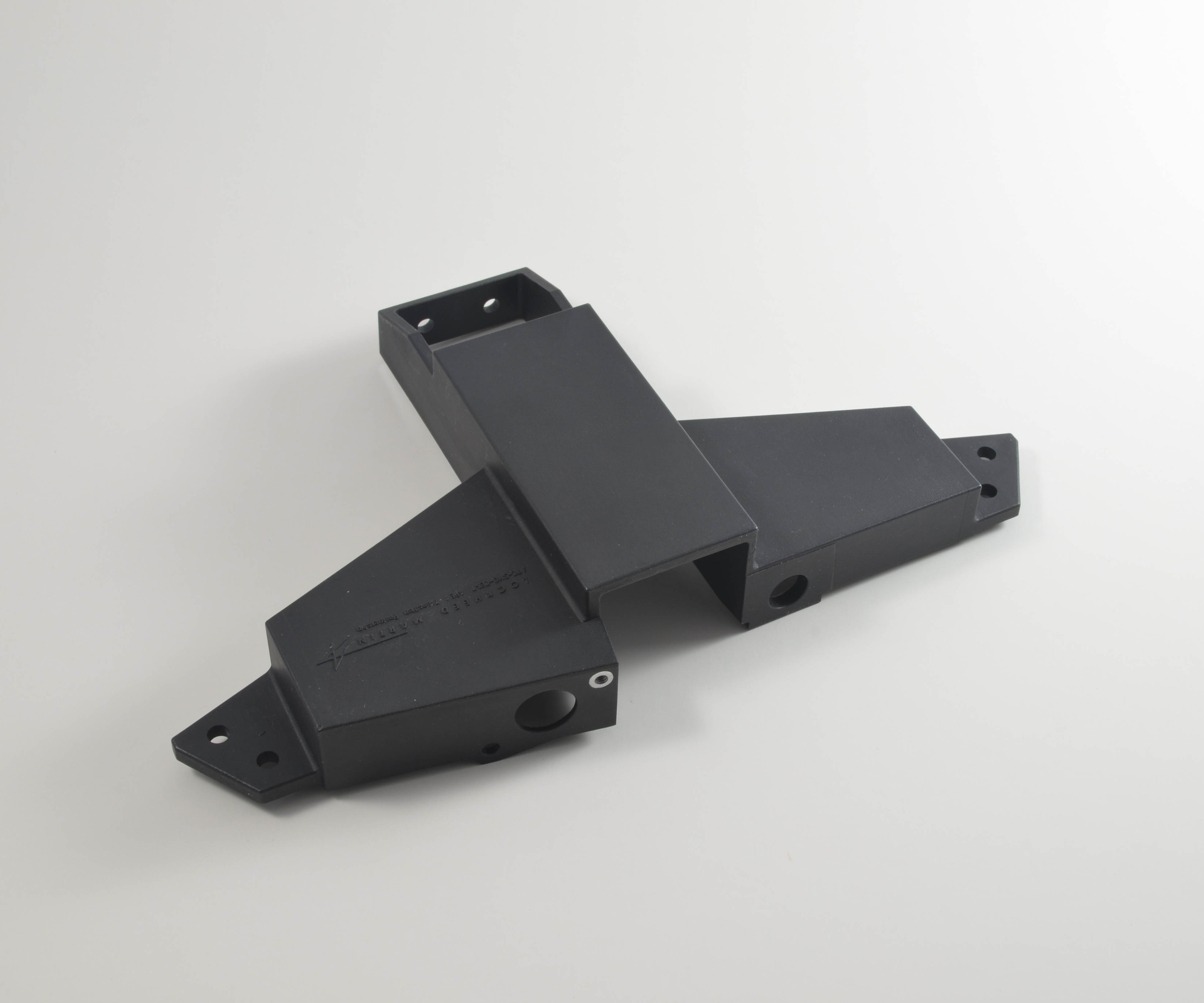
Abb. 2 Brackets aus thermoplastischem Nanokomposit. Diese Vorderansicht einer Raketen-Vorder-Zerstörungshalterung zeigt die Vorteile des Spritzgießens mit thermoplastischem HX5-Nanokomposit, das die Kosten um 93 % und das Gewicht um 15 % im Vergleich zur Aluminiumbasis reduziert. Quelle | Alpine Advanced Materials LLC
Laut Lockheed Martins APEX-Broschüre 2013 ist HX5 mit der gesamten Palette thermoplastischer Verbundwerkstoffprozesse kompatibel, einschließlich Formpressen, Extrusion, Thermoformen, automatisierter Faserplatzierung, Filamentwickeln und 3D-Druck. Es ermöglicht auch Fügeverfahren wie Schweißen und Umspritzen. Laut Artikeln, die von 2011 bis 2016 veröffentlicht wurden, wurde die Entwicklung des thermoplastischen Nanokomposits von Dr. Slade Gardner beaufsichtigt, jetzt Chief Technology Advisor von Alpine Advanced Materials und zuvor Lockheed Martin Fellow in Advanced Manufacturing and Materials für Lockheeds Space Systems Co. Gardner stellte ein Team zusammen der Forscher, die bis 2008 die Formulierung für APEX entwickelten und bis 2009 Prototypen von Teilen für Kunden herstellten. Das Team begann 2010 mit der Herstellung von Prototyp-Hardware für Raumfahrzeuge, einschließlich einer vorderen Zerstörungshalterung für Raketen, die 93 % billiger und 15 % leichter war als die Aluminiumbasis ( Abb. 2). „Das Aluminiumteil hatte eine Produktionsvorlaufzeit von 28 Tagen; Umgekehrt haben wir 300 APEX-Teile an einem einzigen Arbeitstag geformt“, sagte Gardner in einem Lockheed-Nachrichtenartikel aus dem Jahr 2014.
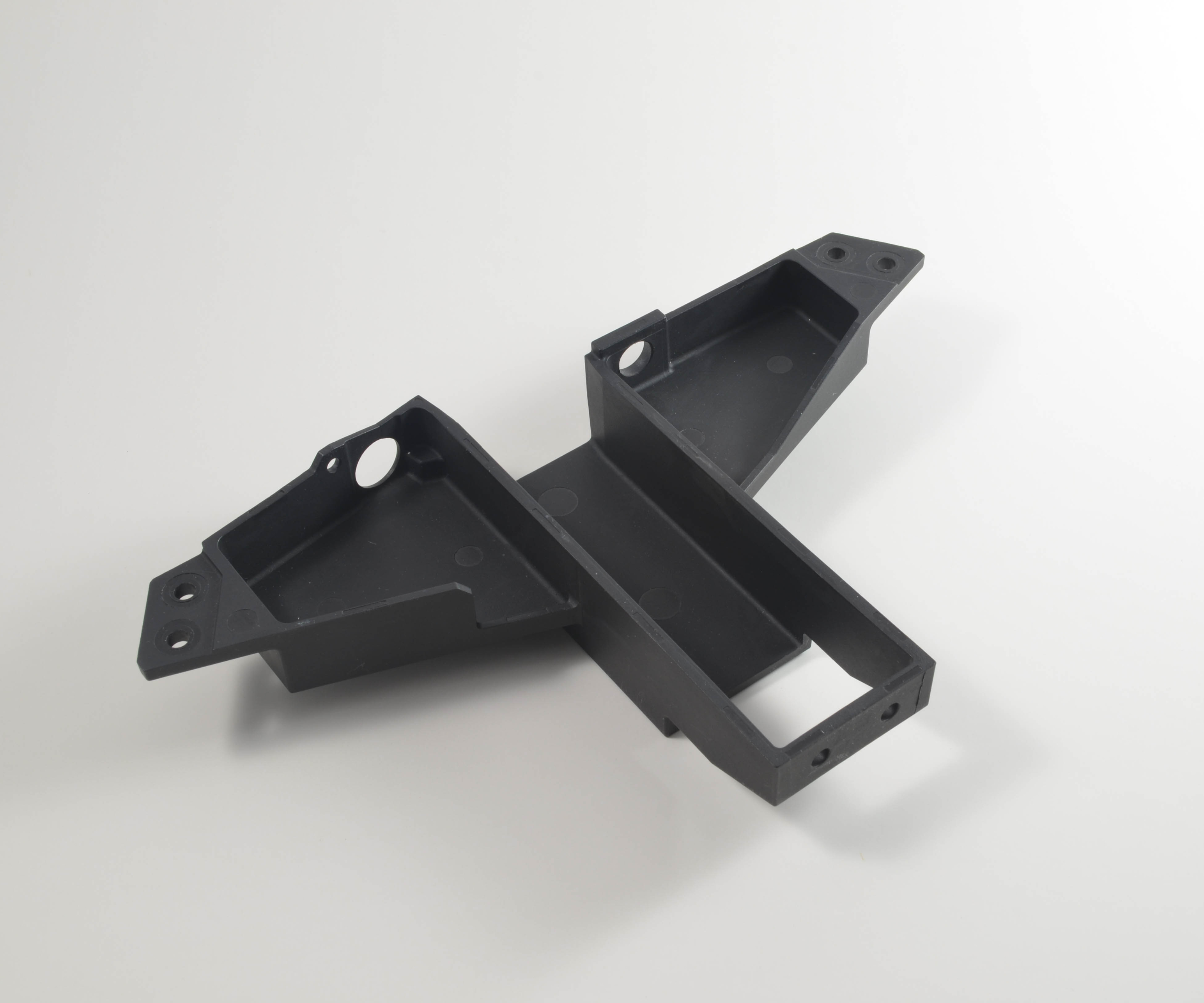
Rückansicht des thermoplastischen Nanokomposit-Brackets. Quelle | Alpine Advanced Materials LLC
Das Team begann damit, spritzgegossenes APEX mit Langfaserverbundwerkstoffen zu kombinieren, um Hybridstrukturen herzustellen, die maximale Erschwinglichkeit und hohe Leistung bieten. In einer Anwendung – einem kostengünstigen Feststoff-Raketenmotorgehäuse der nächsten Generation – wurden 40 Raketennasenkonen in zwei Arbeitsschichten spritzgegossen, um die Fähigkeit zu großflächigen Teilen zu demonstrieren. „Unsere Nasenkonen bedeuten eine Kosteneinsparung von 98 % und eine Verbesserung der Durchlaufzeit von 99 %“, sagte Gardner. Im Jahr 2011 wurde APEX zugelassen, um einen teureren endlosfaserverstärkten Verbundstoff in den Flügelspitzenverkleidungen des F-35-Kampfjets zu ersetzen. Das Material wurde auch in mehr als 1.000 Clips verwendet, die die Hauptstruktur des A2100-Satelliten stabilisieren, sowie für Clips, Halterungen und Kabelkanäle in anderen Lockheed-Raketenabwehrprodukten.
Gardner beschrieb das APEX-Material als eine kurzfaser- und nanofaserverstärkte Mischung aus „Ultrapolymer“. Es wird auch als eine Plattform erklärt, die nicht auf ein einzelnes Polymer beschränkt ist und so maßgeschneiderte, herstellbare Formulierungen ermöglicht, einschließlich der Verwendung mit Endlosgewebe- und unidirektionalen Faserverstärkungen. HX5 hat Feuer-, Rauch- und Toxizitätstests (FST) für Flugzeuginnenräume und Hochtemperatur-Leistungstests bei 520 °F/270 °C bestanden.
„Alpine plant, eine Vielzahl von Spezialmaterialien zu kommerzialisieren, aber HX5 ist auf absehbare Zeit unser Flaggschiffprodukt“, sagt Bennett. Das Unternehmen verkauft nicht das HX5-Material, sondern entwickelt und fertigt kundenspezifische Teile. „Wir bauen Prototypen von HX5-Teilen, die in vielen Branchen eingesetzt werden“, fügt er hinzu und weist darauf hin, dass Aluminium in Verkehrsflugzeugen und Drehflüglern ersetzt wird, mit besonderem Fokus auf Innenausstattungen und Einzelteilen für den Leichtbau, was wiederum die CO2-Emissionen reduziert. HX5 eignet sich gut für die Neukonstruktion von Aluminium- oder konventionellen Verbundbaugruppen, um die Teileanzahl zu reduzieren.
Obwohl die ersten HX5-Teile spritzgegossen werden, plant Alpine, andere fortschrittliche Fertigungsverfahren wie das Umspritzen zu nutzen. „Alpine setzt sich auch weiterhin dafür ein, die Wettbewerbsposition der Vereinigten Staaten durch die Teilnahme an zahlreichen Verteidigungsentwicklungsprogrammen zu verbessern“, sagt Bennett.
Nano-CMCs für Hyperschall
Weiter weg vom Boden und bei viel höheren Geschwindigkeiten ist ein weiteres aufstrebendes Anwendungsgebiet für Nanomaterialien:Nano-Keramik-Matrix-Verbundwerkstoffe (CMCs) für Hyperschall. Hyperschall ist ein aerodynamischer Begriff für Geschwindigkeiten, die viel höher als die Schallgeschwindigkeit sind, typischerweise weniger als Mach 5. Im Allgemeinen ist Hyperschall eine Kategorie von Militärwaffen und -fahrzeugen, die für die Reise mit Hyperschallgeschwindigkeit ausgelegt sind. Diese Technologie wird weltweit entwickelt, auch in den USA.
Geschwindigkeiten über Mach 5 erfordern leichte Strukturmaterialien, die Temperaturen von 2480°C standhalten, ohne zu schmelzen oder sich zu verformen, und gleichzeitig Erosion und Projektilen widerstehen. Das heißt, sie müssen hart, mechanisch zäh und bruchfest sein. Diese Fahrzeuge erfordern auch spezielle elektrische und thermische Eigenschaften, um Elektrizität zu leiten und/oder umschlossene Komponenten abzuschirmen. Selbst die neuesten Metalltechnologien haben Mühe, all diese Anforderungen zu erfüllen.
Feuerfeste Keramiken – einschließlich Metallkarbide, Metallnitride und Metallboride – haben die leichte Haltbarkeit, um solch extremen Umgebungen standzuhalten, aber ihre Synthese und Verdichtung erfordert hohe Drücke und Temperaturen über 1980°C, was sie energieintensiv und teuer macht. Reine Feuerfestkeramiken sind auch zu spröde.
Das US Naval Research Lab (NRL, Washington, D.C., USA) nutzt seine Expertise bei der Entwicklung neuartiger, hochtemperaturbeständiger und feuerbeständiger Phthalonitril-Harze, um ein potenziell kostengünstiges Verfahren zur direkten Herstellung von nanokristallinen feuerfesten Keramiken voranzutreiben. Die Technologie verwendet neuartige Polymerverbindungen, um diese Keramiken in-situ in einem Schritt zu synthetisieren und zu verdichten, ohne dass Keramikpulver bei hohen Drücken und Temperaturen gesintert werden muss. Diese Entwicklung wird von Dr. Matthew Laskoski, NRL-Forschungschemiker und stellvertretender Leiter der Abteilung für fortschrittliche Materialien, geleitet und in seinem 2018 erschienenen Artikel „Naval Research Lab entwirft Verbundwerkstoffe für neue Plattformen“ beschrieben. 5, Nr. 2 Zukunftsstreitkräfte für Marinewissenschaft und -technologie Zeitschrift.
Bei diesem Verfahren wird ein neues kohlenstoffreiches Harz mit einer Polyphenol-ähnlichen Chemie mit Metallpulvern durch Kugelmahlen vermischt, eine gängige Technik, die bei der Verarbeitung von Nanomaterialien verwendet wird. Der resultierende Keramikvorläufer kann zu Scheiben, Kegeln, Kugeln oder anderen anwendungsspezifischen Formen kompaktiert werden. Ein reaktives Schmelzinfiltrationsverfahren – solche Verfahren werden üblicherweise zur Herstellung von (CMCs) verwendet – produziert verdichtete Karbide in einem drucklosen, argongefüllten Ofen mit 1370°C. Die dichten Karbide werden somit in einer einstufigen Reaktion bei niedrigerer Temperatur als und ohne den Druck herkömmlicher Sinter- und Heißpresstechniken gebildet. Da die Kristallgröße der Karbide weniger als 40 Nanometer beträgt, sind die resultierenden Nanokeramiken nicht so spröde wie grobkörnige Materialien.
Ein weiterer Vorteil besteht darin, dass das duroplastische Polymer als schmelzbare Kohlenstoffquelle wirkt, die mit den Metallpulverpartikeln reagiert. Es erleichtert auch die Verstärkung der Keramik mit Metallen, Kohlefasern und Sekundärkeramik. (Ein Beispiel für Sekundärkeramiken ist in Abb. 1 (E) zu sehen, wo das zweiphasige Komposit eine primäre Keramikmatrix und eine sekundäre Keramikverstärkung umfasst.) Die resultierenden CMCs bieten einen Weg zur weiteren Kontrolle von mechanischen, thermischen, elektrischen und ablativen Eigenschaften.
Laut Laskoski werden feuerfeste Karbide wie Zirkoniumkarbid und Titankarbid von extrem hohen Temperaturen nicht beeinflusst und sind unempfindlich gegenüber Feuer, Plasma oder atmosphärischer Erwärmung während der Hypergeschwindigkeitsfahrt. Die aus Polymeren gewonnenen nanokristallinen Keramiken von NRL gehen jedoch über Carbide hinaus und umfassen stickstoffreiche Harze, die mit Metallen reagieren können, um Metallnitride zu bilden. NRL hat Siliziumnitrid-, Zirkoniumnitrid- und Titandiborid-Verbundwerkstoffe sowie Verfahren zur Verstärkung der resultierenden CMCs mit zähen Fasern entwickelt. Diese feuerfeste Keramik weist eine hohe Festigkeit, thermische Stabilität und variable elektrische und thermische Leitfähigkeiten auf, die es ihnen ermöglichen, die Anforderungen von Hyperschall-Fahrzeugkomponenten zu erfüllen.
Motoren für solche Fahrzeuge nehmen große Wärmemengen auf und müssen diese effektiv abführen, was selbst die fortschrittlichsten Metalllegierungen ohne Verlust an Festigkeit und struktureller Integrität nicht leisten können. Laskoski behauptet, dass Metallnitrid- und -boridkomponenten diese Herausforderung eher lösen können, während Siliziumnitrid-Verbundwerkstoffe Potenzial für hochfeste, oxidationsbeständige Kommunikationsradome bieten. Das NRL entwickelt eine additive Fertigungstechnologie, die Nanostrukturen in diese Materialien einbaut und die dielektrischen, thermischen und elektromagnetischen Abschirmeigenschaften mit einer höheren Auflösung weiter abstimmt, als dies mit derzeit verfügbaren Materialien möglich ist.
Nanokomposit-Toxizität und sichere Handhabung
Da Nanomaterialien kleiner sind als menschliche Körperzellen und Blutzellen, gibt es Bedenken hinsichtlich ihrer Toxizität, nicht nur durch die Exposition der Arbeiter bei der Materialherstellung und -verarbeitung, sondern auch bei der maschinellen Bearbeitung, dem Schleifen und dem Recycling von Teilen. Der Graphene Council hat kürzlich ein Webinar veröffentlicht, in dem das National Institute for Occupational Safety and Health (NIOSH, Washington, DC, USA) diese Themen diskutiert und seine Ressourcen aufgelistet hat, darunter drei Veröffentlichungen aus dem Jahr 2018:„Protecting Workers during Nanomaterial Reactor Operations“, „Protecting Workers beim Umgang mit Nanomaterialien“ und „Schutz der Arbeitnehmer bei der Zwischen- und Nachbearbeitung von Nanomaterialien“.
NIOSH gibt an, umfangreiche toxikologische Studien nur an wenigen Nanomaterialien, einschließlich Kohlenstoffnanoröhren (CNTs), durchgeführt zu haben. Da Ratten und Mäuse, die CNTs und Kohlenstoffnanofasern (CNFs) ausgesetzt waren, anhaltende Lungenentzündungen, Tumore und Fibrose (progressive Lungennarben, die das Atmen erschweren) zeigten, betont NIOSH, dass es wichtig ist, die Exposition der Arbeiter während der gesamten Nanomaterialproduktion zu kontrollieren. Die Gewinnung von Nanomaterialien aus Reaktoren und die Reinigung von Reaktoren führt zu potenziell hohen Expositionen. Arbeiter können auch beim Sprühen und Bearbeiten (z. B. Kugelmahlen) sowie beim Umgang mit Nanomaterialien zum Wiegen, Verpacken und Mischen/Zusammensetzen ausgesetzt sein. NIOSH gibt an, dass die Kontrolle der Arbeitnehmerexposition mit Standardtechniken möglich erscheint, einschließlich Quelleneinhausung, lokaler Absaugung, persönlicher Schutzausrüstung (PSA) und bewährten Verfahren bei der Reinigung und Reinigung von Feinstaub.
Der von NIOSH empfohlene Expositionsgrenzwert (REL) für CNT/CNF liegt unter 1 μg/m 3 als zeitgewichteter 8-Stunden-Durchschnitt (TWA). Analytische Techniken wie Raster- und Transmissionselektronenmikroskopie (REM, TEM) können verwendet werden, um sicherzustellen, dass dieser Schwellenwert eingehalten wird. NIOSH weist ausdrücklich darauf hin, dass es unsicher ist, den zulässigen Expositionsgrenzwert (PEL) der OSHA für Graphit (5.000 μg/m 3 . zu verwenden ) oder Ruß (3.500 μg/m 3 .) ) und dass mehr Forschung erforderlich ist, um die Gesundheitsrisiken von CNTs und CNFs umfassend zu charakterisieren, einschließlich Langzeittierstudien und epidemiologischen Studien an Arbeitnehmern.
„CNTs wurden recht gut untersucht“, sagt Jo Anne Shatkin, Präsidentin von Vireo Advisors LLC (Boston, Massachusetts, USA), einem Beratungsunternehmen für Gesundheit und Sicherheit am Arbeitsplatz. „Vor zehn Jahren wussten wir es nicht, aber jetzt zeigen Studien, dass die drastischere Toxizität, von der wir befürchtet hatten, nicht wirklich eingetreten ist.“ Sie stellt fest, dass die Besorgnis über Nanomaterialien mit hohem Aspektverhältnis wie CNTs darin besteht, dass sie sich wie krebserregende Kieselsäure und Asbestfasern verhalten. „Aber nur sehr wenige der CNT-Materialstudien erfüllen derzeit dieses Faserparadigma“, erklärt sie. „Aber es gibt noch viele Herausforderungen. Wir haben hauptsächlich unberührte Nanomaterialien getestet, nicht funktionalisiert, wie sie verwendet werden. Es bleibt Unsicherheit, weil Nanomaterialien in Zusammensetzung, Form und Funktionalisierung so unterschiedlich sind.“ Alle diese Faktoren können die Toxizität beeinflussen, einschließlich der verwendeten Funktionalisierungsmethode und Chemie. „Sie schaffen Eigenschaften, die das CNT besser mit einem Polymer reagieren lassen, aber wir wissen nicht, wie sich das auf die Wechselwirkungen des Materials mit Blut oder Körperzellen auswirkt“, sagt sie. Wir befinden uns noch nicht in einem prädiktiven Stadium. Das ist es, was wir jetzt erforschen. können wir ein standardisiertes Modell zur Bewertung von Exposition und Toxizität entwickeln, das all diese Variablen berücksichtigt?“
Shatkin beschreibt die Arbeit und eine Reihe von Standardtestmethoden, die bei der American Society for Testing and Materials (ASTM, Conshohocken, PA, USA) und dem American National Standards Institute (ANSI, Washington, D.C., USA) entwickelt werden. „Die ISO/ANSI TC 229 Nanotechnology Standards Development Group hat Dutzende von Standards zum Testen von Nanomaterialien“, sagt sie, „sowie Arbeitsschutzmethoden, wie z. B. die Durchführung von SEM und TEM für Partikelverteilungsmessungen in Bezug auf PELs und RELs .“ Shatkin stellt fest, dass sowohl ISO als auch ASTM einen Standard in der Entwicklung haben, der das Risiko der Freisetzung von Nanomaterialien aus Verbundwerkstoffen durch maschinelle Bearbeitung, Schleifen und andere sekundäre Vorgänge untersucht. Hier ist zumindest vorläufig grünes Licht gegeben. Shatkin sagt, dass die Arbeit des Industriekonsortiens NanoRelease zeigt, dass das Schleifen und Bearbeiten von Teilen, die Nanomaterialien enthalten, keine neuen Gesundheits- und Sicherheitsrisiken darstellt. „Es werden zwar Nanomaterialien freigesetzt, aber diese sind an das Polymer gebunden, keine freien nanoskaligen Partikel“, erklärt sie. „Unsere aktuellen Richtlinien für Partikel aus der Bearbeitung von Verbundwerkstoffen sind also ausreichend.“ Unternehmen – insbesondere solche mit begrenzten Arbeitskräften und Ressourcen – betrachten jedoch Bearbeitungsstaub möglicherweise nicht als ernsthafte Gesundheitsgefahr. Daher befolgen sie möglicherweise nicht immer Richtlinien und bewährte Verfahren für PSA und Atemschutzgeräte, ganz zu schweigen von Gehäusen und Belüftungsgeräten. But because there is still uncertainty, such complacency isn’t an option when working with nanomaterials.
Nanocomposites are indeed enabling higher performance, greater multifunctional capabilities and potentially lower-cost and lighter-weight structures for numerous applications and markets. “There is a huge opportunity for benefit with nanomaterials, and we’ve learned a lot,” says Shatkin, “but there’s still a lot of uncertainty. Our best path forward is to be cautious, minimize exposure and make sure, as much as possible, that we make manufacture, handling and use as safe as possible.”
Verifying producers and supporting developers
One of the challenges facing a dynamic, fast-maturing technology is to build trust in the supply chain. To that end, the Graphene Council is working to mature the global supply chain through its Verified Graphene Producer program. Versarien plc (Cheltenham, U.K.) is the first graphene supplier to successfully complete this independent, third-party verification system that involves a physical inspection of the production facilities and review of the entire production process and safety procedures. “We also take random samples of their products and submit them for blind testing to be rigorously characterized at the National Physical Laboratory (NPL, Teddington, U.K.), a world-class institution that follows ISO/TR 19733:2019 for Nanotechnologies,” says the Graphene Council’s Barkan. NADCAP is an analogous audit program long used by the aerospace industry for the same purpose. “Without this type of program, customers have no clue what they are getting when they buy and receive graphene products,” says Barkan. “Our Verified Graphene Producer program is an important step to provide a level of confidence in the both products and producers worldwide.”
The Graphene Council also works to improve development of graphene applications. “We connect companies with resources to help them quickly navigate products, producers, materials science and testing for faster, more successful development,” says Barkan. “We also provide independent, third-party advisory services to help companies that want to use graphene, but don’t know where to start. We not only have reach into our formal members, but also track more than 200 companies involved with graphene worldwide. We monitor what is being developed and the latest scientific and research results, helping to understand what type of graphene to use, how to functionalize and disperse it and how to test for performance.” He notes a close relationship with the Graphene Engineering &Innovation Center (GEIC) at the University of Manchester (Manchester, UK), where graphene was first discovered. “This is a rapid prototyping center,” says Barkan, “and helps us to leverage what graphene can do.”
Harz
- waren kurz vor einem entscheidenden Durchbruch für die Transparenz der Lieferkette
- Drei gute Argumente für eine flexible Lieferkette
- Passt Blockchain perfekt in die Lieferkette?
- Wann wird Blockchain für die Lieferkette bereit sein?
- Umgestaltung der Lieferkette und Logistik für Resilienz
- Zukunftssichere Lieferkette für die neue Normalität
- Modernisierung der Lieferkette für ein verbessertes Kundenerlebnis
- Wie man sich auf die nächste Unterbrechung der Lieferkette vorbereitet
- Ist Ihr Unternehmen bereit für eine Warnung zur Einhaltung der Lieferkette?
- Vier Überlegungen für Lieferketten nach Covid