Innovative Verbundwerkstoffe zur Erschließung neuer Märkte
Obwohl die Basis des Unternehmens mit Sicherheit auf dem Filament Winding liegt, hat CompoTech diesen Prozess durch stiftbasiertes Wickeln, Überspulen und innovative Werkzeug- und Materialkonzepte in neue Anwendungen getrieben. Das Ergebnis ist ein fließender Prozess, der oft durch Hybridisierung neue Leistungsniveaus erreicht, beispielsweise mit Metallen und Herstellungsmethoden wie 3D-Druck und einer eigenen Version des automatisierten Faserlegens (AFL).
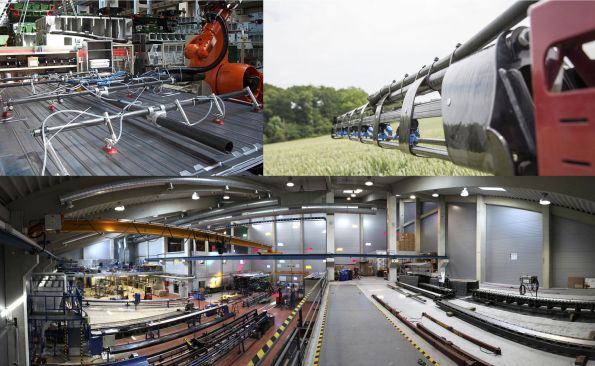
CompoTech produziert Teile für ein breites Anwendungsspektrum, darunter Industrieanlagen (Vakuumgreifermontage, oben links) und landwirtschaftliche Geräte (Sprühgestänge, oben rechts) aus dem Werk in Sušice, Tschechien (unten). QUELLE:Bilsing Automation (Greifer, oben links), Hardi International (Spritzgestänge, oben rechts) und CompoTech.
CompoTech (Sušice, Tschechische Republik) wurde 1995 von Ondrej Uher und Vitek Sprdlik, dem heutigen R&D-Direktor bzw. technischen Direktor des Unternehmens, gegründet. „Sie haben ursprünglich eine Filamentwickelmaschine zur Herstellung von Kajak- und Kanupaddelwellen gebaut, die ihre eigene Technologie zum axialen Wickeln von 0°-Fasern integriert hat“, erklärt Humphrey Carter, Business Development Director von CompoTech. „Das ist heute eine Kernkompetenz. Wir haben gezeigt, dass diese Konstruktion stärkere und steifere Strukturen mit einem höheren Widerstand gegen das Knicken der Fasern erzeugt.“
Das Unternehmen hat auch die Möglichkeit entwickelt, integrale Verbundreifen für Verbindungen zu wickeln. Diese werden in Teilen von Hängegleiterholmen über Antriebswellen bis hin zu Industriekomponenten verwendet. „CompoTech konstruiert die Maschinen und die Steuerungssoftware“, sagt Carter. „Da wir die volle Kontrolle über den Prozess haben, können wir das Design besser optimieren. Wir entwickeln die Verfahrenstechnik maßgeschneidert nach den Designkriterien und können diese unseren Technologiepartnern sowie Composite-Konstrukteuren und -Herstellern zur Verfügung stellen. Wir haben die Technologie beispielsweise an Southern Spars/North Marine Group lizenziert.“
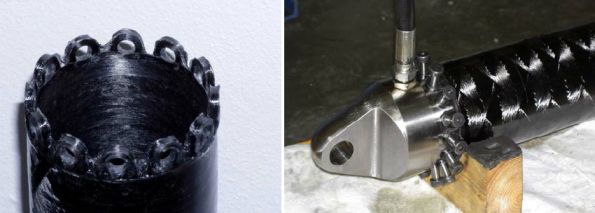
CompoTech wickelt Fasern um Stifte (links) um Strukturen zu erzeugen
mit integrierten Anschlüssen (rechts). QUELLE:CompoTech
Werkzeugmaschinen konstruieren
Derzeit beschäftigt das Unternehmen etwa 50 Mitarbeiter, davon fast die Hälfte in Design und Engineering. Es hat auch enge Verbindungen zur Tschechischen Technischen Universität (CTU) in Prag und auch zur Westböhmischen Universität (Pilsen, Tschechische Republik). CompoTech hat Verbundlösungen für eine Vielzahl von Anwendungen entwickelt, darunter Ausleger für landwirtschaftliche Spritzgeräte, Wellen für Windblattspitzen, Fahrradrahmen und -räder, Rohre und Rahmen für Automobilmontagegreifer und leichte Portalkomponenten für Laserschneider und CNC-Maschinen.
„Wir sind seit Anfang der 2000er Jahre im Industrie- und Werkzeugmaschinensektor aufgrund seiner Verbreitung in der Tschechischen Republik tätig“, erklärt Carter. „Dies ist eine sehr konservative Branche, die Verbundwerkstoffe nicht kennt. Daher gehen wir auf Werkzeugmaschinenausstellungen und bilden sie aus.“ Diese Industrie weiß bereits, dass Schwingungen von beschleunigenden Teilen und von Schnittflächen, wie zum Beispiel Fräszähnen, eine Verringerung der Bearbeitungsgenauigkeit und der Werkzeugstandzeit verursachen. CompoTech erklärt, dass die Oberwellen eines Schneidwerkzeugs – seine Schwingung basierend auf Masse, Steifigkeit und aufgebrachten Lasten/Kräften – oft der limitierende Faktor für Leistung und Produktivität sind. Weniger bekannt ist, dass kohlenstofffaserverstärkter Kunststoff (CFK) in der Struktur von Maschinen und Werkzeughaltern verwendet werden kann, um die Masse zu reduzieren und die Steifigkeit gegenüber Stahl zu erhöhen. Bei der Verwendung von Pechfasern berichtet CompoTech von einer Gewichtsreduzierung von 25 % bzw. einer Steifigkeitssteigerung von 200 % (400 GPa mit unidirektionaler Faser erreicht). Dies sind die beiden wichtigsten Möglichkeiten, die Eigenfrequenz einer Struktur zu erhöhen und Resonanzen zu vermeiden. Dies ist, wenn die Struktur von selbst vibriert, was die Probleme für bereits vibrationsanfällige rotierende Teile und Maschinen mit variabler Drehzahl verschärft.
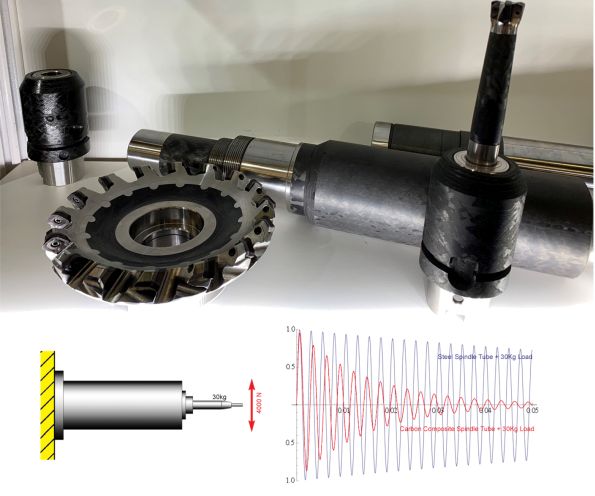
CompoTech verwendet CFK und zusätzliche Dämpfungsmaterialien, um das Gewicht zu reduzieren und die Steifigkeit und Dämpfung gegenüber Stahl zu erhöhen, um Vibrationen zu vermeiden. Ihre Technologie reduziert auch die Werkzeugmaschinendrift, was die Bearbeitungsleistung und Produktivität verbessert. QUELLE:CompoTech
„Der Einsatz unseres Verfahrens für CFK reduziert auch die Drift von Werkzeugmaschinen gegenüber autoklavierten Verbundwerkstoffen, da wir weniger thermischen Stress verursachen“, fügt Carter hinzu. „Werkzeughalter sind oft lange, schlanke Balken, die sich je nach Konstruktion und Materialzusammensetzung im Laufe der Zeit verändern können. Dies beeinflusst dann die relationale Position des Werkzeugs und verringert seine Genauigkeit.“
Bei der Dämpfung hat CompoTech über die inhärenten Eigenschaften von Faser- und Polymerverbundstoffen hinausgegangen und bahnbrechend andere Materialien aufgenommen, die eine 12- bis 20-fache Dämpfung von Stahl bieten, Schwingungen direkt entgegenwirken und deren Abklingen beschleunigen (siehe Grafik oben). „Wir haben über ein Jahrzehnt Erfahrung in der Entwicklung von gedämpften Verbundwerkstoffen, um die gewünschten Eigenschaften und Leistung zu erzielen“, sagt Carter. Ein Beispiel ist ein neues Design des Werkstückfutters, so dass im Vergleich zu einem Stahlfutter viel weniger Spannkraft benötigt wird. Eine andere ist die modifizierte Vorrichtung zum Drehen eines Niederdruckturbinen-(LPT)-Gehäuses von Flugzeugtriebwerken aus der schwer zerspanbaren Inconel-718-Legierung. CompoTech wurde im Rahmen des EU-finanzierten INTEFIX-Projekts entwickelt und CFK-Ringe als Ersatz für Metallringe entwickelt, die als Positionierer in der Halterung verwendet werden. Das Ergebnis war kein Steifigkeits- oder Funktionsverlust bei gleichzeitig verbessertem Werkstückverhalten und besserer Bearbeitungsleistung. Tatsächlich wurde die Vorrichtung intelligent gemacht, um die Werkstückspannung während des Prozesses bedarfsgerecht anzupassen.
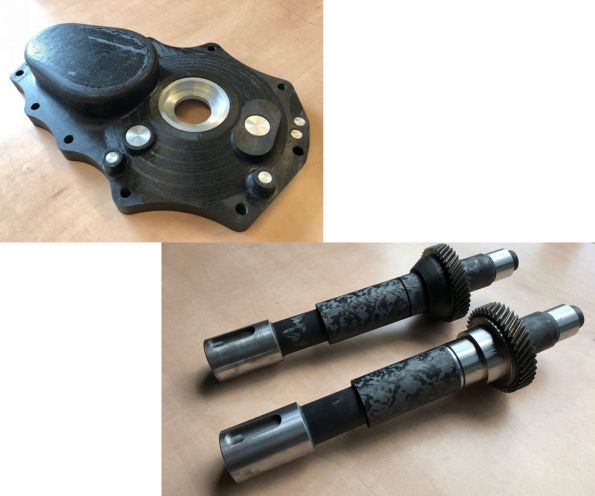
CompoTech hat entwickelt , in Zusammenarbeit mit CTU, KIMM und Samyang Reduction Gear, ein Elektrofahrzeug-Hybrid-Metall-/Verbundgetriebe und -Getriebewellen mit reduziertem Gewicht und geringerem Geräuschpegel. QUELLE:CompoTech
CompoTech arbeitet auch laufend an einem Hybrid-Metall-Verbundgetriebe für Elektrofahrzeuge mit dem Ziel, die Masse um 25 Prozent zu reduzieren und auch Geräusche durch Erhöhung der Eigenfrequenz und Dämpfung zu reduzieren. Dieses Projekt (2016 bis Okt 2019) findet in Zusammenarbeit mit der Tschechischen Technischen Universität (CTU) in Prag, dem Korea Institute of Machinery and Materials (KIMM, Daejeon, Südkorea) und der Samyang Reduction Gear Co. Ltd. (Inchon, Südkorea) statt. Der Hauptkörper des Getriebes wird mit Metalleinsätzen für die Lagerflächen zusammengesetzt. CompoTech entwarf und produzierte das obere und untere Getriebegehäuse sowie die Getriebewellen. Alle bestehen aus mehreren Teilen, die verklebt werden. CTU hat Tests und FE-Analysen bereitgestellt, während die koreanischen Partner des Projekts die technischen Spezifikationen bereitstellen und die Getriebe fertigstellen, montieren und testen.
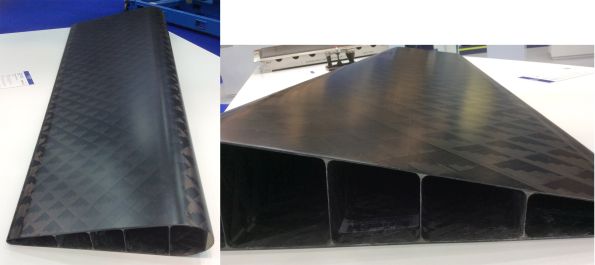
CompoTech hat entwickelt ein einteiliges Querruder mit Filament-Wicklung und Längsrippen – anstelle herkömmlicher Schottrippen, Prepreg und Kleben – was zu einer leichten, delaminationsbeständigen Struktur, insbesondere an der Hinterkante, führt.
QUELLE:Ginger Gardiner, CW auf der JEC 2019
Delaminationsbeständiges Querruder
Carter erklärt, dass ein Großteil der Forschungs- und Entwicklungsarbeit von CompoTech für Werkzeugmaschinen dann auf neue Anwendungen angewendet wird, wie das Querruder für den Jettrainer L-39NG von Aero Vodochody AEROSPACE (Odolena Voda, Tschechische Republik). „Dies ist eine anspruchsvolle Anwendung mit sehr hohen Drücken an der Hinterkante“, sagt er. Zusätzlich zu den Fluglasten erfährt die bewaffnete Version des Flugzeugs Druckwellen, wenn flügelmontierte Raketen abgefeuert werden. „Bei konventioneller Verbundbauweise kam es an der Querruderhinterkante zu Delaminationen“, bemerkt Carter. „Wir haben alle Klebeverbindungen eliminiert und stattdessen eine integrale Struktur durch nasses Filamentwickeln und Co-Härten geschaffen. Wir haben Monate damit verbracht, die Design- und Prozessschritte zu entwickeln. Zuerst wird unser robotergestützter Wickler verwendet, um die vier Kastenträger, die die Querruderholme bilden, mit Filament zu wickeln. Das sind Trapeze und dann D-Formen an den Vorder- und Hinterkanten.“ Die Hinterkante hat auch ein separates Stück darauf, um eine aerodynamischere Oberfläche zu schaffen.
„Wir fügen dann alle diese Teile auf ihren Dornen zusammen und überwinden sie, um die Außenflächen auf den Längsrippen zu erzeugen“, fährt Carter fort. Die gesamte Struktur wird vakuumverpackt und bei Raumtemperatur mit einer Nachhärtung bei 90 °C ausgehärtet.
Dieses Projekt ist ein gutes Beispiel dafür, wie wir gemeinsam mit einem Kunden die Prozesstechnologie und das Design entwickeln. Unsere Idee ist keine Massenproduktion von Querrudern oder anderen Teilen. Wir würden die Maschinen produzieren und unsere Kunden werden die Teile wickeln.“ Das Querruder fliegt jetzt und Aero Vodochody hat einen 4-Jahres-Auftrag für Bestellungen von L-39NG-Jettrainern.
Im Allgemeinen basiert der Nasswickelprozess von CompoTech auf Präzision, bei dem im Wesentlichen Towpreg im Handumdrehen hergestellt wird. „Wir verwenden meist Epoxidharze und härten bei 100 °C aus“, sagt Carter. „Für Anwendungen, die eine höhere Tg erfordern, wie beispielsweise einige Bohrlochwerkzeuge, die wir für den Einsatz in der Öl- und Gasindustrie hergestellt haben, können wir bei 140 °C aushärten.“
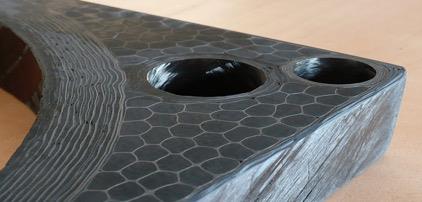
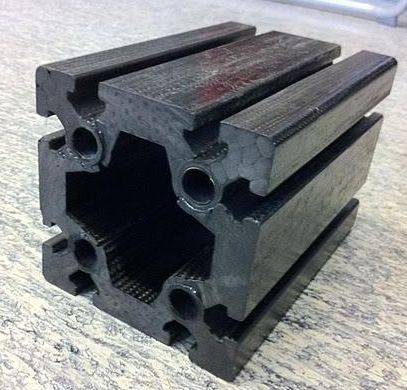
Beispiele für 3D Zellverbundwerkstoffe für hohe axiale Steifigkeit, dicke und komplex geschnittene Teile. QUELLE:CompoTech
Neuartige Prozesse
3D Cellular Composite (3Dc) ist der Name von CompoTech für eine Reihe von Verfahren, die einen Verbund mit dreidimensionaler Verstärkung herstellen. Durch einen zellularen Querschnitt erzielt diese Konstruktion einen hohen axialen Faseranteil in x-Richtung verbunden mit Fasern in y- und z-Richtung, die die Zellwände bilden. Wir haben dieses Verfahren für dicke Teile entwickelt, die eine sehr hohe axiale Steifigkeit erfordern“, sagt Carter. Diese Steifigkeit wird durch den sehr hohen 0° (axialen) Faseranteil erzeugt. Die Zellwände tragen über die Zellwände auch Querlasten über den Abschnitt und ermöglichen die Realisierung interessanterer Abschnitte, wie der oben gezeigten T-Nut.
Das Unternehmen bietet auch 3D-Druckdorne und -Stützen an, um Torsions- und Eigenfrequenzanforderungen ohne dickere Laminate zu erfüllen. „Dies ist ein weiteres Projekt, das mit CTU zusammenarbeitet“, sagt Carter, „wo wir eine automatisierte interne Konstruktion von Strukturen entwickeln.“ Er stellt fest, dass das Wickeln von thermoplastischen Verbundwerkstoffen massiv an Fahrt gewinnt. „Das ist unser nächster Schritt, unser Wickeln in Thermoplasten mit dem 3D-Druck zu kombinieren und durch Faltung innovative Formwerkzeuge für Verbundwerkstoffe sowie Werkzeugmaschinenstrukturen zu schaffen.“
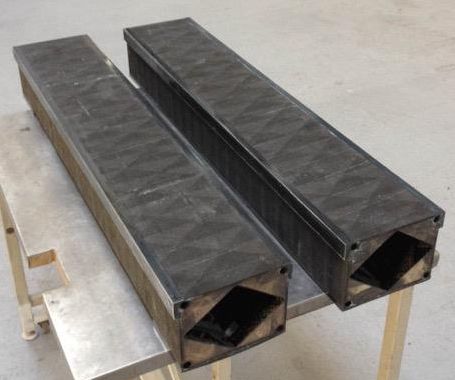
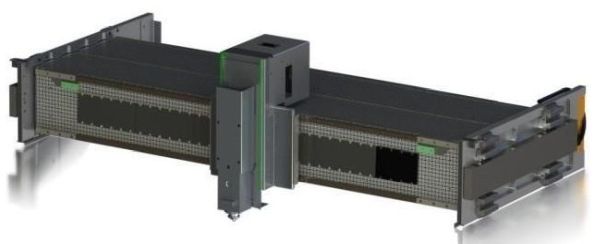
CompoTech verwendet hybridisierte Prozesse zur Herstellung steifer, leichter CFK-Portalstrukturen, die die Maschinengenauigkeit und -geschwindigkeit verbessern. QUELLE:CompoTech, Eagle Laser.
Harz
- AT&T, Tech Mahindra arbeiten an einer neuen Open-Source-KI-Plattform zusammen
- CompositesWorld SourceBook 2022
- Salewas neuer Wanderschuh mit thermoplastischen Verbundwerkstoffen
- CEAD bringt neuen E50-Roboter-Extruder für größere 3D-gedruckte Verbundwerkstoffe auf den Markt
- Verbundwerkstoffe als Karosserieverstärkungen
- Neue Technologien und Märkte bei World of Filament Winding Ereignis
- IRG CosiMo Konsortium für thermoplastische Verbundwerkstoffe enthüllt neue Anlagen
- Green Science Alliance Co. Ltd. stellt neue Nano-Zellulose-Verbundwerkstoffe her
- Hochleistungsverbundwerkstoffe in Israel
- Nèos International gründet neues Hauptquartier für Verbundwerkstoffe in Großbritannien