Verbundwerkstoffe als Karosserieverstärkungen
Obwohl Verbundwerkstoffe in der Karosserie von Automobilen (BIW) einen gewissen Einzug gehalten haben, wurde der Materialeinsatz in diesem Bereich des Fahrzeugs lange Zeit von Stahl und in jüngerer Zeit von Aluminium dominiert. Aus diesem Grund verlassen sich Autohersteller stark auf Schweißen und mechanische Befestigungselemente wie Bolzen und Schrauben, um Metallstrukturen zu verbinden. Obwohl im Allgemeinen robust, können Schweißverbindungen und Befestigungselemente versagen. Sie tragen auch wenig dazu bei, die Steifigkeit zu verbessern (ohne die Masse unangemessen zu erhöhen) oder das Geräusch/Vibration/Härte (NVH) oder die durch ein Fahrzeug strömende Aufprallenergie abzuschwächen. Eine Möglichkeit, diese Herausforderungen zu meistern, besteht darin, BIW-Verbindungen und -Hohlräume mit Verbundwerkstoffen in Verbindung mit Strukturklebstoffen zu verstärken.
Ein Beispiel für eine solche Lösung ist eine Klasse von Materialien/Technologien, die als Verbundkörperlösungen (CBS) bezeichnet werden. Dazu zählen 3D-Struktureinlagen zur Verstärkung primärer Fahrzeugstrukturen, die Elemente des BIW oder anderer Fahrzeugunterbauten kombinieren, thermoplastische Träger (mit durchgehender oder diskontinuierlicher Faserverstärkung) und wärmeaktivierte, schäumende Strukturklebstoffe. CBS-Elemente werden im Karosseriebau früh im Fahrzeugbau installiert, bevor eine elektrophoretische Rostschutzbeschichtung (E-Coat) aufgebracht wird.
CBS-Komponenten werden typischerweise in einem 2K-/Spritzguss-Umspritzungsverfahren hergestellt, bei dem der Träger – mit Schweißlaschen oder Schnappverschlüssen, um das CBS vorübergehend mit metallischen BIW-Komponenten zu verbinden – selektiv mit expandierbarem Klebstoff und möglicherweise einem zusätzlichen Dichtmittel (in einem 3K-Verfahren) umspritzt wird. für zusätzliche Funktionalität. Der sich trocken anfühlende, ungehärtete Klebstoff (basierend auf kundenspezifischer Epoxidchemie) kann in komplexe Formen gegossen werden, ermöglicht jedoch eine E-Coating-Bedeckung von metallischen Elementen, indem er einen Spalt zwischen Verbund- und Metalloberflächen vor der wärmeinduzierten Ausdehnung während der Nachbearbeitung aufrechterhält -E-Coat Ofenhärtung. Während sich der Schaum ausdehnt, werden Lücken zwischen Träger und umgebenden Komponenten abgedichtet und sie in einer kastenartigen „Makrostruktur“ miteinander verbunden, die die mechanischen Eigenschaften verbessert, insbesondere bei hohen und dynamischen Belastungen.
Bei frühzeitiger Einbeziehung in das Fahrzeugdesign sind CBS-Module massen- und kosteneffiziente Optionen zur Erhöhung der lokalen und globalen BIW-Steifigkeit und zur Verbesserung der Fahrgastsicherheit und des Komforts bei geringerer Masse. Sie ermöglichen auch neutrale oder kostengünstigere gegenüber schwereren Ganzmetalllösungen. Ursprünglich nur in der Automobilindustrie verwendet, hat ein wachsendes Portfolio an Träger- und Klebematerialien die Anwendung von CBS erweitert, von denen einige Highlights folgen.
Für Leistungsherausforderungen entwickelt
Die CBS-Technologie wurde von L&L Products Inc. (Romeo, Michigan, USA) entwickelt und kommerzialisiert. Mit einer langjährigen Erfahrung als Automobilzulieferer von Dichtmitteln, akustischen Gegenmaßnahmen und Verstärkungen zur Verbesserung der BIW-Leistung hat L&L die Technologie entwickelt, um Kunden dabei zu helfen, die Sicherheit der Insassen zu verbessern und strengere Crash-Anforderungen bei geringeren Kosten und Gewicht zu erfüllen und gleichzeitig die Verarbeitung und Montage während des Fahrzeugbaus zu verbessern .
Zwischen 1995 und 2004 war CORE Products, ein Joint Venture von L&L und Gurit Essex (Wattwil, Schweiz), für die frühe Anwendungsentwicklung und die CBS-Fertigung verantwortlich. L&L erwarb schließlich alle Vermögenswerte von CORE, das jetzt als L&L Products Europe firmiert.
L&L arbeitete während der ersten Entwicklung und der anschließenden Erweiterung der CBS-Technologie eng mit seinen Materiallieferanten zusammen. Ein solches Unternehmen, die Lanxess AG (Köln, Deutschland), bietet L&L in Europa seit langem Unterstützung bei der Charakterisierung und Simulation von Verbundträgermaterialien und -materialien.
CBS in Bewerbung
Neben den bereits erwähnten Vorteilen bietet die CBS-Technologie einen besseren Lastpfadübergang, mehrachsiges Lastmanagement und Energieabsorption; größere Profilstabilität (Widerstand gegen Einsturz oder Eindringen); niedrigeres NVH; und verbesserte Fahrdynamik und Crash-Performance bei höheren Lasten. Darüber hinaus bietet es einen schnelleren Implementierungszeitpunkt während der Fahrzeugkonstruktion/-neukonstruktion und erfordert keine Änderungen der Montagereihenfolge im Karosseriebau. Da die CBS-Technologie die Kontrolle der Energieübertragung durch Karosseriestrukturen erleichtert und gleichzeitig Deformationen und/oder Eindringen minimiert, ist sie ideal geeignet für Anwendungen, die einem Frontal-, Seiten- oder Heckaufprall oder Dacheindrücken widerstehen, um Insassen, Fahrgasträume und Batterien besser zu schützen. Es ist auch für Strukturen nützlich, die anspruchsvolle Protokolle wie das Insurance Institute for Highway Safety (IIHS, Arlington, Virginia, U.S.) bestehen müssen Crashtests mit kleiner Überlappung.
Was CBS bemerkenswert machte, war, dass es zu den ersten modularen Mischmaterialansätzen gehörte, einfach zu installieren war, thermische und chemische Stabilität für die E-Beschichtung bot und die Reihenfolge der Fahrzeugmontage nicht veränderte, aber eine verbesserte Leistung bei geringerer Masse und neutraler/ niedrigere Kosten – der heilige Gral der Autoindustrie.
„Die Designvielfalt der CBS-Technologie hilft, die Montage in Bereichen mit komplexen oder schwer zugänglichen Bedingungen zu vereinfachen“, erklärt Núria Ignés, Engineering Manager Structural Products, L&L Products Reinforce bei L&L Products EMEA (Altorf, Frankreich). „Der Einsatz der CBS-Technologie bei Türen und anderen Verschlüssen beispielsweise reduziert nicht nur das Gewicht und erhöht die Steifigkeit, sondern kann auch die Türfertigung vereinfachen, wenn sie frühzeitig in den Konstruktionsprozess integriert wird. Dank CAE-Tools und jahrzehntelanger Erfahrung sowie der Kombination aus Träger und Schaumstoff, die nach dem Aushärten eine robuste Verbindung zum BIW bietet, können wir die richtige Menge des richtigen Materials an der richtigen Stelle verwenden, um Steifigkeit mit Masse und Kosten in Einklang zu bringen oder Energieabsorption mit Akustik und Kosten.“
„Ein wirklich interessanter Aspekt der CBS-Technologie ist ihre ‚biomimetische‘ Natur“, fügt Peter Cate, Global Strategic Marketing Manager bei L&L, hinzu. „So wie die zellverstärkenden Streben im Zentrum von Knochen die masseeffizienteste Methode der Natur sind, um Steifigkeit zu erhöhen und Lasten in Hohlstrukturen zu bewältigen, verstärken CBS-Einheiten, sobald sich der Klebstoff ausdehnt, die Hohlräume der Fahrzeugkarosserie auf dieselbe Weise und helfen den Ingenieuren, die Struktur zu optimieren Steifigkeit bei geringster Masse.“
„Durch die Erhöhung der lokalen und Gesamtsteifigkeit und die effektivere Verteilung der Lasten über eine Struktur sind CBS-Verstärkungen maßgeschneiderte Lösungen, um lokale Steifigkeits- und Metallermüdungsprobleme zu lösen, ohne Masse hinzuzufügen“, fährt Pal Swaminathan, Business Development Manager, Tepex Automotive, Lanxess Corp . fort (Pittsburgh, Pennsylvania, USA). „NVH-Verbesserungen sind auch üblich, wenn die CBS-Technologie in Karosseriestrukturen integriert wird. Auch hier ermöglicht eine sorgfältige technische Analyse die Entwicklung und Standortoptimierung von Lösungen, um Fahr- und Fahreigenschaften in Einklang zu bringen.“
Frühe Bewerbungen
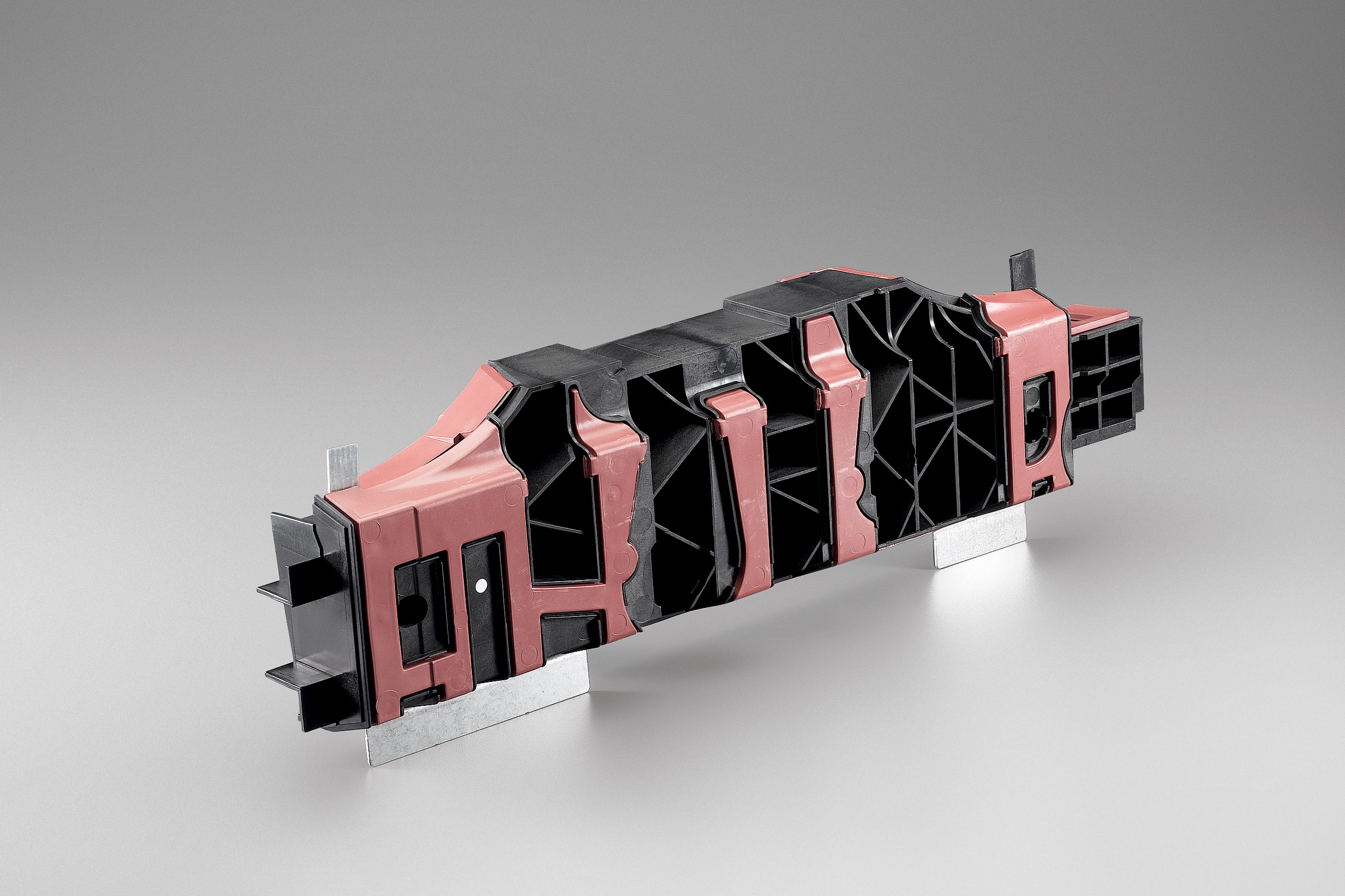
Die erste kommerzielle Automobilanwendung von L&L von CBS war 1998; bis 2002 gewann die technologie marktakzeptanz. Ein gutes frühes Beispiel wurde beim Citroën C4 Picasso von 2006 implementiert Limousinen der PSA Group (Paris, Frankreich – jetzt Stellantis N.V., Amsterdam, Niederlande). Neun CBS-Komponenten – im unteren Bereich der A-Säule, im unteren und oberen Bereich der B-Säule sowie am Querträger über der Hinterachse – reduzierten die Fahrzeugmasse um 12 Kilogramm gegenüber Metallic-Optionen. Einige CBS-Einsätze erhöhen selektiv die Tragfähigkeit und minimieren das Eindringen in den Fahrgastraum beim Aufprall, wodurch die Insassensicherheit verbessert wird. Andere verbesserten die NVH-Leistung des BIW. Alle Träger wurden aus 35 Gew.-% Kurzglas/Polyamid 6 (PA6) spritzgegossen. Ähnliche CBS-Einheiten wurden im Ford Transit von 2012 verwendet Lieferwagen von Ford Motor Co. (Dearborn, Michigan, USA).
Neuer Träger, Schaumstoffoptionen
Im Laufe der Jahre haben L&L und seine Lieferanten die CBS-Technologie um neue Schaumformulierungen, eine breitere Palette von Trägerharzen und Verstärkungen und durch die Anwendung des Konzepts auf verschiedene Strukturen erweitert.
Beispielsweise werden die meisten CBS-Träger für Crashanwendungen aus hitzestabilisiertem, 30 Gew.-% glasfaserverstärktem PA6 hergestellt, da ein Gleichgewicht zwischen Steifigkeit und Duktilität innerhalb einer komplexen 3D-Form erforderlich ist. Zwei solcher Träger wurden an vorderen Längsträgern für eine große Elektrofahrzeug-(EV)-Plattform verwendet, wo sie angeblich nicht nur die Montage vereinfachten (die Anzahl der Teile reduzierten), sondern auch das Eindringen von Crash in die Firewall um 20 % reduzierten.
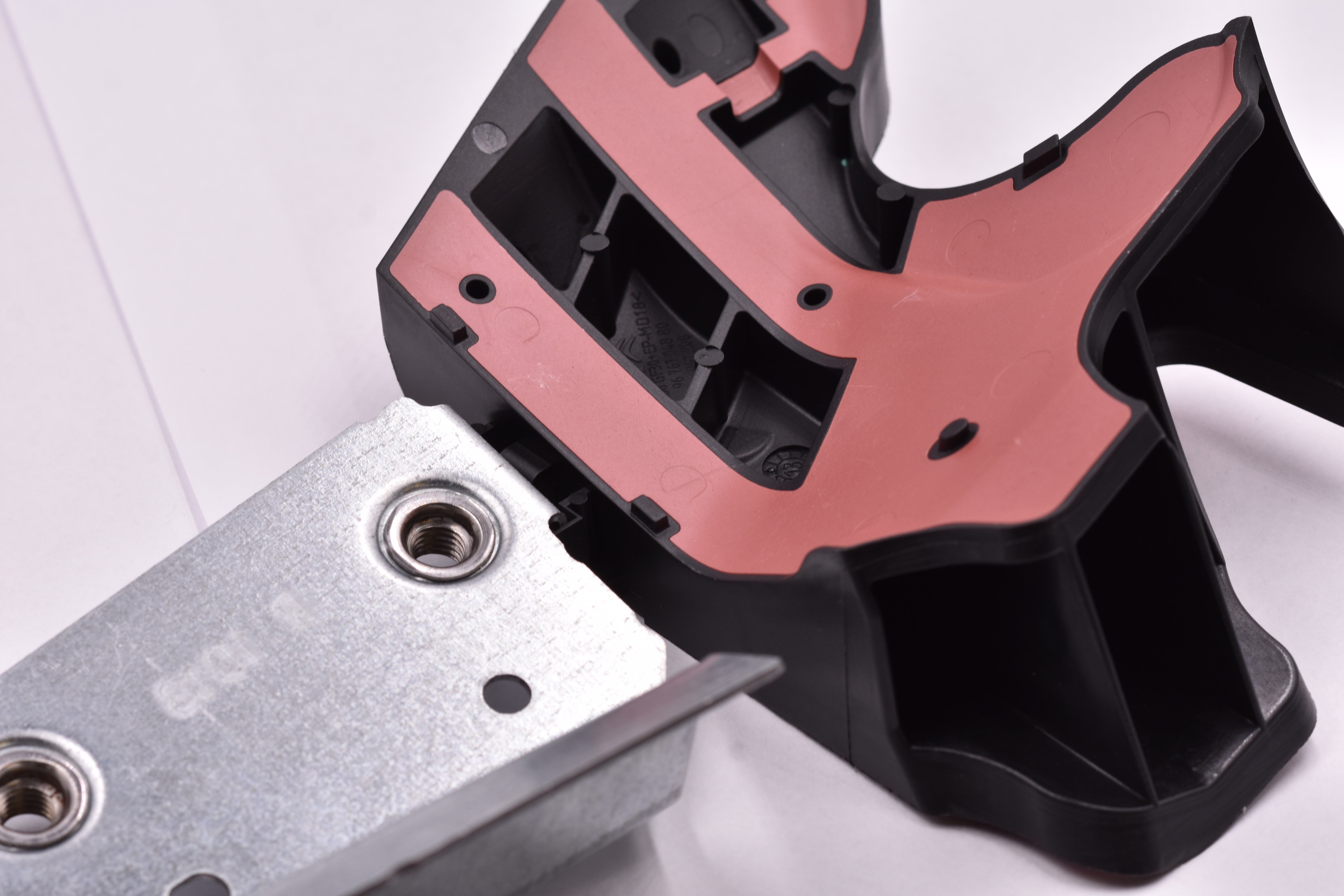
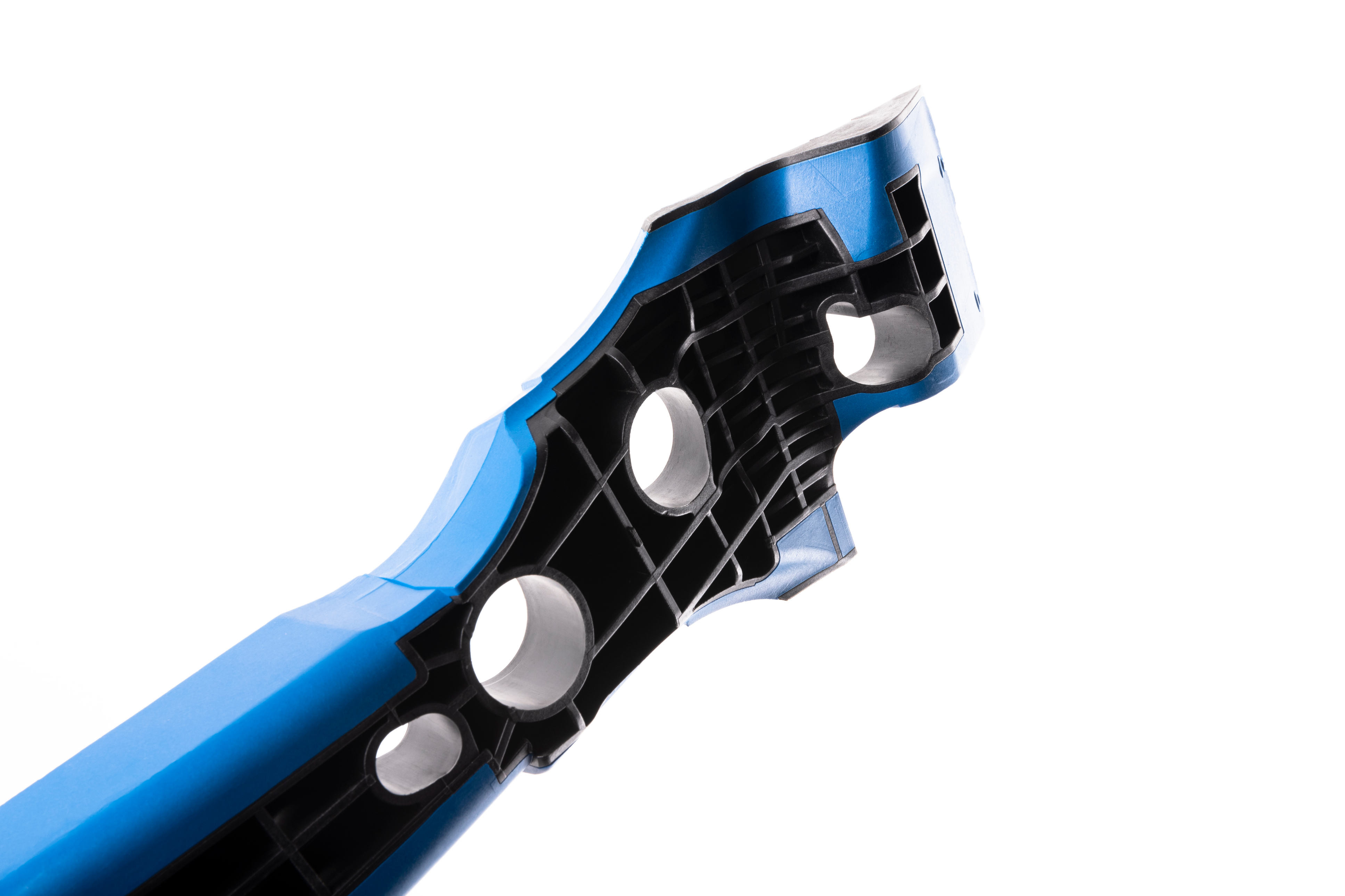
Für höhere Aufprallanforderungen sind jetzt Hybridträger erhältlich, wie zum Beispiel die verstärkenden A-Säulen des größtenteils aus Aluminium gefertigten Porsche 911 Carrera Cabriolet von 2019 Sportwagen der Porsche AG (Stuttgart, Deutschland). Da es sich um ein Cabriolet handelt, war die Versteifung des dachlosen Rahmens entscheidend, um die Passagiere im Falle eines Überschlags zu schützen. Um die Fahrzeuge leicht und wendig zu halten, ersetzte Porsche schwere Stahlrohr-Überrollbügel durch CBS-Einsätze in den A-Säulen. Säulenschalen wurden aus hochfestem Stahl gefertigt, die durch CBS-Einlagen im Inneren jeder Säule stabilisiert und versteift wurden. Der Hauptträgerkörper war formgepresstes Organoblech (47 Vol.% Glasgewebe Köperbindung/PA6), das vorgewärmt, vorgeformt und dann mit Rippen spritzumspritzt wurde (30 Gew.% Kurzglas/PA6/6). Die Organoblechseite trägt den expandierenden Klebstoff L-5235 von L&L. Diese Hybridtechnologie erfüllte nicht nur alle Leistungs- und Gewichtsziele (was die Stahlrohroption angeblich nicht erreichte), sondern reduzierte die Fahrzeugmasse um 5,4 Kilogramm, erleichterte die Montage und senkte den Fahrzeugschwerpunkt, was die Fahrdynamik verbesserte.
Für Anwendungen, bei denen kein Ofenprozess zur Aktivierung des expandierenden Klebstoffs zur Verfügung steht oder bei denen in der Lackiererei zusätzliche Unterstützung benötigt wird, arbeitet L&L an anderen Umgebungshärtungslösungen.
Mehrere verwandte Technologien auf der Grundlage von CBS wurden ebenfalls entwickelt. Das Continuous Composite System (CCS) von L&L, das bald seine erste kommerzielle Anwendung findet, kombiniert glas- oder kohlefaserverstärkte pultrudierte Träger — z. B. Polyurethan (PUR) mit oder ohne Gewebe sowie Rovings — mit maßgeschneiderten Dichtstoffen oder Strukturklebern. CCS-Elemente, die auch CBS-Teile und Metallkomponenten enthalten können, verbessern die Steifigkeit und Festigkeit von Strukturen mit konstantem Querschnitt bei geringerer Masse (typischerweise 75 % weniger als Stahl und 30 % weniger als Aluminium). Sie sind korrosionsbeständig, nicht leitend/elektrisch isolierend, bieten einen niedrigen linearen Wärmeausdehnungskoeffizienten (CLTE) und bieten ein hochgradig vorhersehbares Energiemanagement, wodurch sie ideal zur Verstärkung von Strukturbauteilen von Fahrzeugen mit einer Karosserie oder Rahmenabschnitten von Karosserien mit Karosserie geeignet sind. plus Batterierahmen für Elektrofahrzeuge.
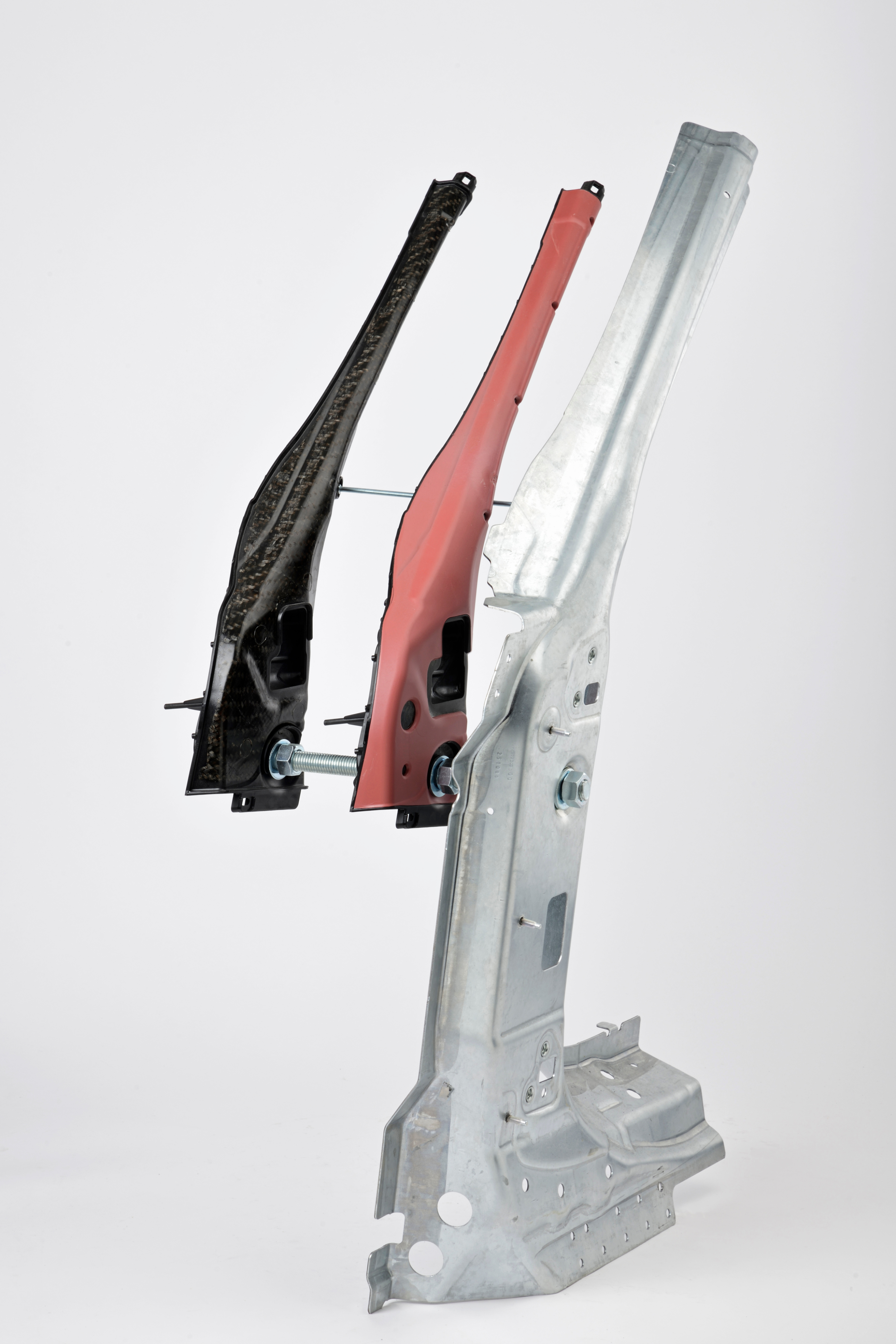
Verbundplattenverstärkungen bestehen aus selbsthaftenden, expandierenden Strukturklebstoffen, die mit Glasfaserverstärkungen coextrudiert werden und im Karosseriebau auf umgeformte Blechoberflächen aufgebracht werden. Das System verbessert nicht nur die Steifigkeit (Reduzierung von Welligkeit und Knicken) von großen/relativ ungestützten Platten, sondern verbessert auch das NVH aufgrund des erhöhten Trägheitsmoments. Darüber hinaus bietet es Möglichkeiten, Platten für geringere Masse und Kosten zu verkleinern. Kommerzielle Anwendungen umfassen Fahrzeugtüren, Dach- und Bodenbleche, Motorhauben, Kotflügel, Heckklappen und Heckklappen; mögliche Anwendungen sind Batteriegehäuse.
Wabenplattenverstärkungen bestehen aus leichtem Epoxid – in Pastenform zum manuellen Auftragen oder dünnflüssiger Flüssigkeit zum automatischen Pumpen – das nach dem Aushärten maschinell bearbeitet oder geschliffen werden kann. Diese sollen Wabenkerne vor allem an strategischen Stellen im Flugzeuginnenraum stabilisieren, ohne zusätzliche Masse hinzuzufügen. Andere Anwendungen umfassen Randverstärkung (Abdichten/Verstärken von Verbundplattenkanten), Einfügen von Einsätzen und lokale Verstärkung, wenn Metallscharniere/Einsätze in Verbundplatten installiert werden.
Was die Zukunft bringt
Seit seinem ersten Patent im Jahr 1999 hat L&L zahlreiche Erfindungen für die CBS-Technologie angemeldet. Angesichts der breiten Palette von Träger- und Klebstoffoptionen, die jetzt innerhalb dieser Produktfamilie verfügbar sind, überrascht es nicht, dass sich die Anwendungen über die Automobilindustrie hinaus auf Lkw und die Luft- und Raumfahrt ausgeweitet haben. Was kommt als nächstes?
„Im Laufe der Jahre haben sich CBS-Produkte weiterentwickelt, um neue Anwendungsanforderungen zu erfüllen, die Funktionen kombinieren“, fügt Ignés hinzu. „Was beispielsweise als strukturelle Verstärkung begann, hat sich weiterentwickelt, um nicht nur zu versteifen, sondern auch um akustische Funktionen zu verbessern oder die Energieabsorption zu erhöhen. Angesichts der überaus wünschenswerten Eigenschaften, die die CBS-Technologie bietet, erwarten wir nicht nur eine Zunahme der Automobilnutzung, sondern auch ein Wachstum in anderen Branchen.“
Harz
- CompositesWorld SourceBook 2022
- Fehlerbehebung beim Thermoformen von thermoplastischen Verbundwerkstoffen
- Die Entwicklung additiver Verbundwerkstoffe
- Thermoplastische Verbundwerkstoffe:Strukturelle Stoßstangenhalterung
- Menschen in Verbundwerkstoffen – Januar 2019
- CAMX 2018:Ausstellungsvorschau
- Schweißen von thermoplastischen Verbundwerkstoffen
- SPE ACCE 2018 Vorschau
- Hochleistungsverbundwerkstoffe in Israel
- 3D-Druckverbundwerkstoffe mit Endlosfasern