Kohlenstofffasern werden Lufttaxi-eVTOLs ermöglichen
Dieser Blog ist eine Reaktion auf einen Artikel vom Januar 2019 in WIRED Magazin, das behauptet, dass die Produktion von Kohlefaserverbundwerkstoffen die Entwicklung von Elektrofahrzeugen (EV)/vertikalen Start- und Landeflugzeugen (VTOL) für den urbanen Mobilitäts- und Lufttaximarkt zurückhält. Ich werde darüber diskutieren, aber auch einige potenziell disruptive neue Technologien anbieten, also lesen Sie es bis zum Ende durch.
Obwohl ich dem Autor applaudiere, dass er über diese sich schnell entwickelnde Branche berichtet und auf die Notwendigkeit hingewiesen hat, bei der Konstruktion mit Blick auf die Herstellbarkeit zu sein, ist er manchmal irreführend, wahrscheinlich weil er nicht sehr gut in der Verbundwerkstoffindustrie ausgebildet ist. Zum Beispiel:
Obwohl dies technisch wahr ist, wird Airbus bis Mitte 2019 auf 60 A320-Flugzeuge pro Monat hochfahren und Boeing ist auch 2019 auf dem Weg zu 57 Flugzeugen/Monat für die B737. Für die A320 bedeutet dies die Produktion von drei 6,3 m großen Seitenleitwerksbaugruppen aus kohlenstofffaserverstärktem Kunststoff (CFK) pro Tag und auch drei 12,45-m-Spannweite CFK-Leitwerksbaugruppen pro Tag .
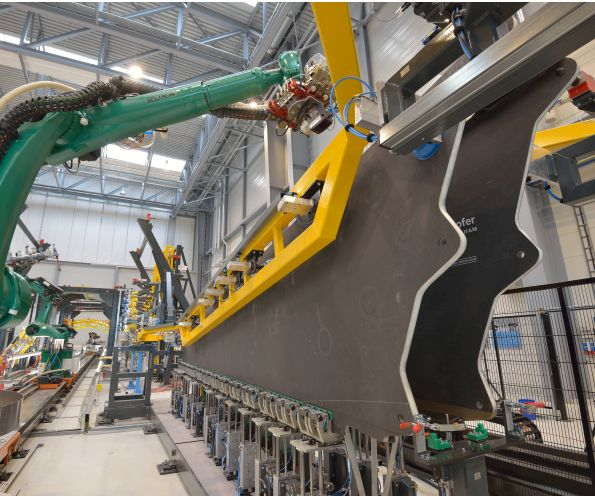
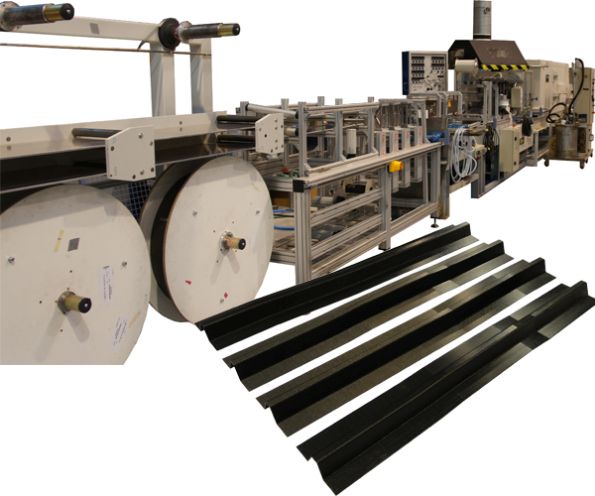
Außerdem hat Airbus eine Technologie nach der anderen für die nächste Iteration der A320, die als A320 Neo Plus bezeichnet wird, qualifiziert – viele verwenden Verbundwerkstoffe und alle zielen auf 60-70 Flugzeuge pro Monat ab. Diese Verbundwerkstofftechnologien umfassen ein Portfolio, das Resin Transfer Moulding (RTM), Formpressen von Sheet Moulding Compound (SMC) und thermoplastische Verbundwerkstoffe (TPCs) umfasst, die Zykluszeiten von problemlos 700+ Flugzeugen pro Jahr aufweisen. Einige der neuesten Technologien in der Entwicklung reduzieren die Zykluszeiten von CFK-Teilen von 4 Stunden auf 15 Minuten oder weniger. Die meisten der neuen Technologien, die Airbus qualifiziert hat, sind stark automatisiert, ebenso wie die neuen Montagemethoden.
Die Automobilindustrie hat auch den Weg zu einer höheren Massenproduktion geebnet, als eVTOLs erfordern (VERKABELT zitierte prognostizierte Nachfrage von 23.000 Fahrzeugen bis 2035). BMW erhöht die Produktion seines i3 und i8 Modelle – beide mit Voll-CFK-Fahrgastzellen – von 130 bis 200 Einheiten/Tag und Audi-Zulieferer Voith Composites produziert die CFK-Rückwand für den A8 mit einer Leistung von 150-300 Einheiten/Tag . Beachten Sie, dass der BMW i3 und i8 Module sind der unten gezeigten Flugzeugzelle für den Airbus Helicopters EC 135 sehr ähnlich — beide Hersteller befestigen dann Außen- und Innenkomponenten an diesem Rahmen.
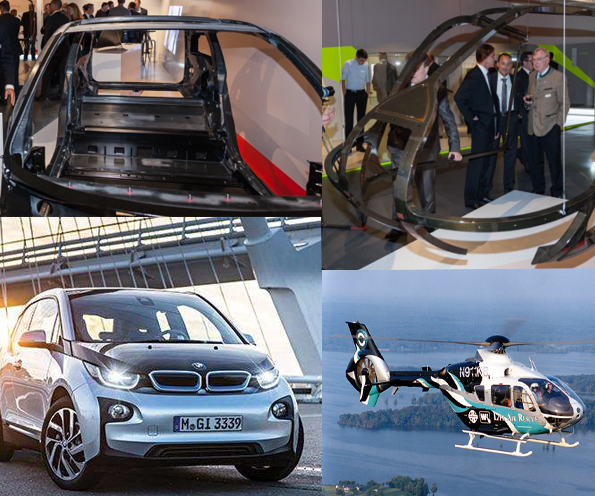
Die Karosserierahmen des BMW i3 und i8 sind dem des Airbus Helicopters EC135 sehr ähnlich.
QUELLE: Meilensteine des Spitzenclusters – Rückblick und Zukunftsaussichten, MAI Carbon, S. 36-7 (oben), BMW und Airbus Helicopter (unten).
Inzwischen ist der Audi A8 Rückwand wird im 5-Minuten-Takt mit RTM und automatisierter Platzierung von trockenem Kohlefaserband hergestellt, in Länge und Faserorientierung auf spezifische Belastungen abgestimmt und variiert von einer Basis von 6 Lagen (1,5 mm dick) bis zu 19 Lagen (3,7 mm dick) mit lokaler Verstärkung, um hohen Punktbelastungen gerecht zu werden. Dieses einzelne Teil bietet 33 % der Torsionssteifigkeit der Antriebszelle bei 50 % des Gewichts im Vergleich zu einer Baugruppe aus drei bis fünf geschweißten Aluminiumteilen.
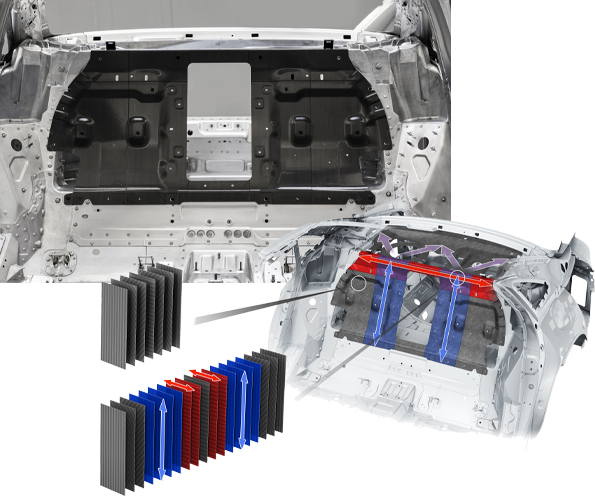
Der Audi 2019 A8 verfügt über eine in 5 Minuten aus Kohlefaserband gefertigte CFK-Rückwand. QUELLE:Audi und Voith Composites.
Thermoplaste
Aber diese Beispiele nutzen nicht einmal die thermoplastische Technologie, die als bevorzugte Wahl für Boeings neue mittelgroße Flugzeuge (NMA) bevorzugt wird, die vor dem zweiten Quartal 2019 angekündigt werden sollen. Thermoplastische Teile werden seit den 1990er Jahren in Flugzeugen eingesetzt, während die Entwicklung fortgesetzt wurde , mit Airbus und europäischen Tier-1-Zulieferern, die immer größere Flügel- und Rumpfsektionen (mit integrierten Versteifungen) prototypisieren und dieses Jahr auf Rumpfdemonstratoren in Originalgröße skalieren. Beachten Sie, dass thermoplastische Verbundwerkstoffe auch Schweißen ermöglichen, was weitere Möglichkeiten bietet, Befestigungselemente und Montagen zu eliminieren.
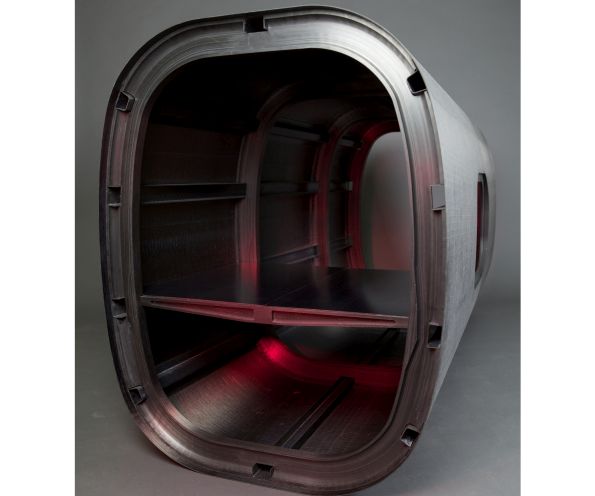
Automated Dynamics, jetzt Teil der Trelleborg Group , produzierte diesen integral versteiften CF/PEEK-Helikopter-Heckausleger in Originalgröße im Jahr 2012 unter Verwendung von in-situ-Konsolidierung während der automatisierten Faserplatzierung, wodurch langwierige Autoklavenzyklen sowie Befestigungselemente und Klebstoffe überflüssig wurden.
QUELLE:Automatisierte Dynamik, Trelleborg
Die Lieferkette für TPC-Materialien und -Verarbeitung ist in den letzten drei Jahren schnell zusammengewachsen, wobei alle großen Kohlefaserlieferanten jetzt thermoplastische Bänder und umspritzte Teile mit geringer Zykluszeit herstellen, die von mehreren Unternehmen sowohl für Luft- und Raumfahrtanwendungen als auch für Automobilanwendungen demonstriert wurden. Thermoplastisches Schweißen wurde auch von mehreren Unternehmen demonstriert.
Auszug aus „Overmolding as Enabler for Composites, Aerospace to Automotive“, Interview mit Scott King beim Verbundwerkstoffhersteller CCP Gransden:
CCP Gransden hat seine einstufige Thermoform- und thermoplastische Verbund-Overmolding-Technologie verfeinert, um leichte, komplexe Komponenten mit typischerweise <2 Minuten Zykluszeiten unter Verwendung einer breiten Palette von Polymeren und Fasern herzustellen. QUELLE:CCP Gransden
Neueste Technologie
Aber die Technologie hat sich seit 2014 weiterentwickelt und umfasst nun mehrere interessante Entwicklungen:
Thermoplastumspritzte Duroplaste
Das OPTO-Light-Projekt im AZL Aachen demonstrierte umspritzte Rippen und Clips aus thermoplastischem Verbundwerkstoff (TPC) auf einer Kohlefaser/Epoxid Verbundteil.
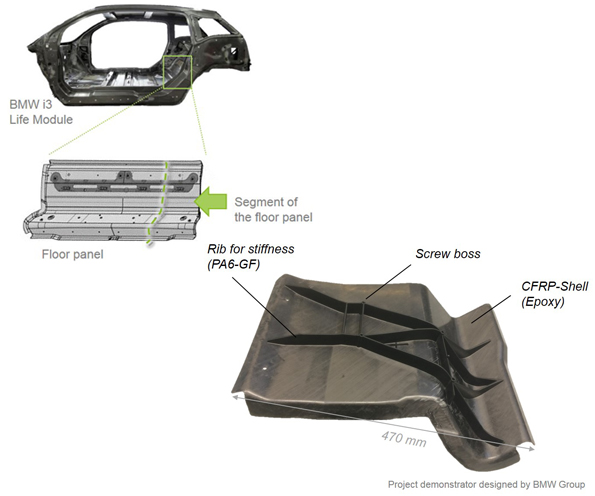
Umspritzen + UD lasttragende Pultrusionen
Das Projekt MAI Skelett hat umspritzte TPC-Pultrusionen in einem zweistufigen 75-Sekunden-Prozess demonstriert, um einen strukturellen Dachträger/Windschutzscheibenrahmen herzustellen, der alle BMW i3 . übertrifft Teileanforderungen bei gleichzeitiger Integration von Anbauteilen und Clips sowie Änderung des Crashverhaltens von sprödem zu duktilem Versagensmodus für erhöhte BIW-Restfestigkeit.
Projektpartner SGL Carbon liefert nun Carbonfasern mit entsprechender Schlichte für Single-Matrix-Lösungen aus der PP- oder PA6-Familie, inklusive Pultrusionen, Organoblech und Overmolding Compound sowie Design- und Prozess-Know-how für die Bauteilentwicklung, letztere über ihr Lightweight Applications Center (LAC, Meitingen, Deutschland).
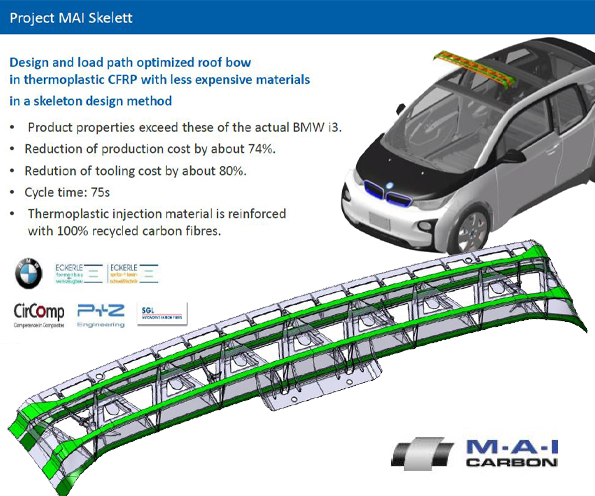
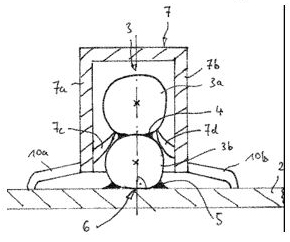
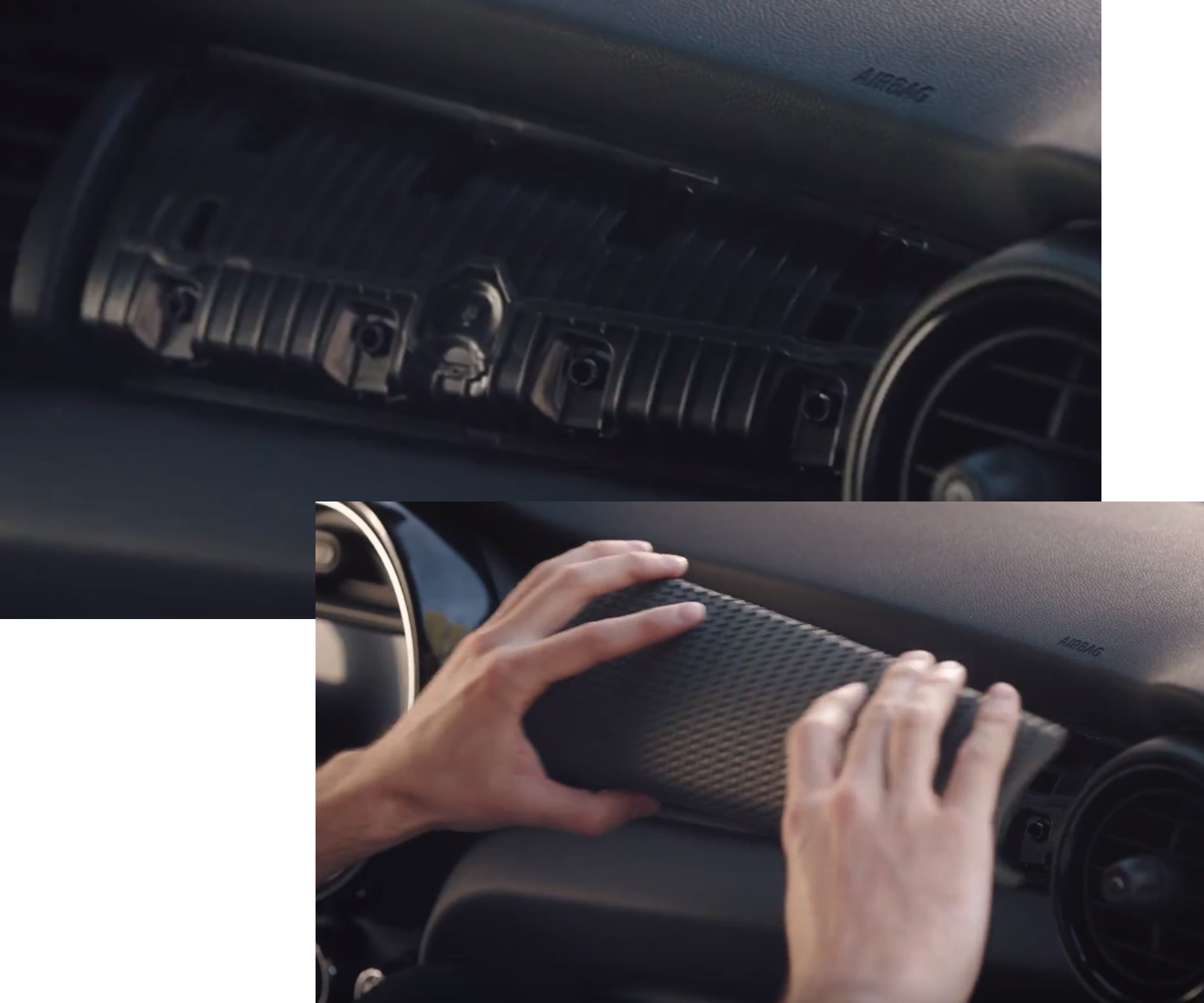
BMWs neues patentiertes Das hochpräzise Befestigungssystem verwendet spritzgegossene oder umspritzte Clips (unten) und 3D-gedruckte Kugeln (oben) ohne Befestigungselemente, Bohrlöcher oder Klebstoff. Die unteren Bilder zeigen, wie dieses System es ermöglicht, im Rahmen des MINI Yours Customized-Programms 2019 individuelle 3D-gedruckte Innenverkleidungen „aufzuschnappen“.
QUELLE:Patent DE 10 2013 214 269 B3 (oben)
https://www.youtube.com/watch?v=1pyxNKw-nf8 (unten)
Zurück zum VERKABELTEN Artikel und seine uninformierten Behauptungen:
Zwar wird diese Methode der CFK-Herstellung seit vielen Jahren eingesetzt, aber es stimmt auch, dass sowohl Flugzeug- als auch Automobilhersteller bereits auf stärker automatisierte, nahezu abfallfreie Materialien und Prozesse sowie auf Thermoplaste mit nachgewiesenen Vorteilen in Eliminieren von Befestigungselementen, wodurch Recyclingfähigkeit/Recyclinginhalt und Reparierbarkeit ermöglicht werden.
Am Ende das VERKABELTE Der Autor widerspricht seiner ganzen These, denn der eVTOL-Pionier ICON will nicht nur seine CFK-Flugzeugzelle voranbringen, sondern auch Teile für größere Flugzeuge herstellen. Kohlefaser wird eVTOLS offensichtlich nicht erden, sondern spielt bereits heute eine wichtige Rolle darin, dass Unternehmen clevere Konstruktionen für eine Vielzahl von zukünftigen Fahrzeugen sowohl in der Luft als auch auf der Straße vorantreiben. Der Einsatz modernster Technik ist sinnvoll, denn all diese Neufahrzeuge müssen ohnehin zertifiziert werden.
Ein wichtiger Punkt war aus dem Artikel von BetaTechnologies CEO Kyle Clark:
Scott Bledsoe, CEO von Blue Force Technologies, betonte auch die Bedeutung von Aerodynamik, Antrieb, Styling, Strukturen und Herstellung Teams mit jeweils gleichem Sitz bei jedem Schritt des Designs und der Entwicklung am Tisch.
Aber vielleicht ist es am wichtigsten, auf dem Laufenden zu bleiben, wo sich die Herstellung von Verbundwerkstoffen bewegt, und mit den vielen Material-, Ausrüstungs- und Technologielieferanten in Kontakt zu treten, die ihr Know-how teilen und bei der Entwicklung zukünftiger Anwendungen helfen möchten. Kontaktieren Sie uns unter CompositesWorld denn das ist, was wir tun — technische, zuverlässige Verbindungen und Informationen bereitzustellen.
Harz
- Kohlenstofffasern
- 3 Gründe, warum Kohlefaserhersteller bald mehr tun werden
- Was ist Kohlefaser?
- Der Aufstieg kohlenstofffaserverstärkter Kunststoffe
- Kohlefaserverstärkter Kunststoff (CFK)
- Ist Kohlefaser leitfähig?
- Fords Last GT wird ein Kohlefaser-Supersportwagen in limitierter Auflage
- Neuerfundene Flugzeugkabine von Pagani und Airbus mit digitaler Decke
- Air Jordan 1 Kohlefaser-Sneaker ist ein Muss für Sammler
- Verbundstoffrecycling – keine Ausreden mehr