Experteninterview:Pat Warner, Spezialist für additive Fertigung des Renault Formel-1-Teams
Pat Warner ist ADM Manager beim Renault Sport Formula One Team – einem internen Spezialisten für additive Fertigung, der daran arbeitet, erstklassige gedruckte Komponenten sowohl für Prototypen- als auch für Produktionszwecke zu liefern. Pat ist seit mehr als 19 Jahren intensiv an der additiven Fertigung in der Formel 1 beteiligt und hat eine Reihe wichtiger Entwicklungen in der Technologie und ihren Anwendungen miterlebt, die er freundlicherweise im folgenden Interview mit AMFG besprechen wollte:
AMFG:Wie kamen Sie ursprünglich zur additiven Fertigung?
Pat:Ich war ursprünglich CNC-Maschinist beim damaligen Benetton Formula Team und wechselte 1997 in die CAM-Abteilung. Wir kauften unsere erste SLA-Maschine '98, wussten aber nicht so recht, was wir damit anfangen sollten. Die Maschine wurde in einem Raum neben der Maschinenhalle aufgestellt und die Programmieraufgabe an die CAM-Gruppe übertragen. Bis zum Jahr 2000 hatten wir genügend Anwendungen gefunden, um die SLA-Maschine für zwei neuere, schnellere Modelle zu PX zu bringen. Bis 2002 kauften wir zwei weitere. Im Jahr 2003 haben wir die Abteilung um das Lasersintern erweitert und seitdem sukzessive auf die bestehende Abteilung mit neun Maschinen erweitert.
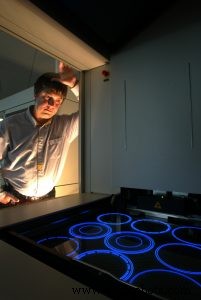
AMFG:Was waren einige der größten AM-Erfolgsgeschichten, die Sie während Ihrer Zeit bei Renault erlebt haben?
Pat:Im Laufe der Jahre waren es so viele.
Wir prototypieren jede neue Komponente des Autos und bauen sie auf Funktion/Passform zusammen. Das ist in der Welt der Additiven nichts Neues, aber wir finden unsere Fehler sehr schnell. Die Verpackung eines modernen Formel-1-Autos stellt eine Herausforderung für das Designteam dar, da es schwierig ist, den Mechanikern Platz zu geben, um auf Teile des Autos zuzugreifen, wenn man auf einen Bildschirm schaut.
Für unsere Strukturbauteile aus Titan, wie beispielsweise das Getriebegehäuse, fertigen wir eigene Feingussmodelle. Wir haben viel Zeit und Mühe in die Verfeinerung dieses Prozesses gesteckt und landen normalerweise bei der Gießerei, die wir benutzen, um Muster von uns zu kaufen (zu diesem Zeitpunkt stellen wir nur Komponenten für das Team her).
Die additive Fertigung hat zweifellos die Entwicklungsgeschwindigkeit in den Windkanälen der Formel 1 erhöht. Als wir im Windkanal uneingeschränkte Betriebszeiten hatten, produzierten wir mehr als 600 Teile pro Woche, nur um den Tunnel zu speisen. Die Menge an konventionellen Fertigungsressourcen, die erforderlich ist, um das gleiche Ziel zu erreichen, wäre immens.
Schnelle Vorrichtungen und Vorrichtungen haben bei der Produktion des Autos und bei kurzfristigen Modifikationen auf der Strecke geholfen. Am Freitag ein Problem zu finden, Ersatzartikel herzustellen und sie rechtzeitig für das Qualifying an die Strecke zu liefern, ist schon oft vorgekommen.
Natürlich hatten wir auch unsere kleinen Katastrophen, aber sie alle helfen beim Lernprozess.
AMFG:Was sind die wichtigsten Herausforderungen, die Sie in Bezug auf AM als Werkzeug für Prototypen und Produktion erlebt haben?
Pat:Wieder waren es so viele.
Als wir damit anfingen, war die Langlebigkeit des Teils ein großes Problem, SLA-Materialien waren sehr zerbrechlich und vertragen Feuchtigkeit nicht gut. Wenn Sie ein Teil eine Woche lang auf Ihrem Schreibtisch aufbewahren könnten, ohne dass es von jemandem zerbrochen wird, würde es sich verformen, da es Feuchtigkeit aus der Luft aufnimmt. Die Materialentwicklung hat sich um diese Probleme gekümmert und dabei einige erhebliche Verbesserungen vorgenommen.
Als wir anfingen, Komponenten von externen Lieferanten einzukaufen, stellten wir fest, dass Sie das gleiche Teil selten zweimal erhalten, selbst wenn es in einigen Fällen aus der gleichen Konstruktion stammt. Dies ermutigte uns, mehr intern zu arbeiten, mehr Zeit damit zu verbringen, die Geräte und Materialien zu verstehen und unsere Prozesse zu verfeinern. 2004 haben wir uns mit Boeing zusammengetan. Diese Partnerschaft hat uns beiden auf diesem Weg geholfen und dazu geführt, dass wir mehr Komponenten in unsere Fahrzeuge einbauen können. Wir haben Materialien speziell für unsere Bedürfnisse entwickelt, die im Handel erhältlich sind (die FIA-Bestimmungen schreiben dies vor) und woanders verwendet werden.
Bildung war auch eine Herausforderung, obwohl die Technologie schon seit geraumer Zeit auf dem Markt ist, ihre Einführung in die Mainstream-Produktion erfolgte jedoch schrittweise, ebenso wie die Bildung. Infolgedessen bekommen wir immer noch neue Designer, die noch nie mit additiver Fertigung in Berührung gekommen sind.
AMFG:Welche neuen Innovationen würden Sie sich in Bezug auf Druckplattformen und Materialien am meisten wünschen?
Pat:Beide Bereiche haben sich in den 19 Jahren, in denen ich involviert bin, weit entwickelt, aber die Technologie kann noch weiter reifen. Wir müssen unseren Prozessen immer noch viel Aufmerksamkeit schenken, um die gewünschten Ergebnisse zu erzielen, und wir sehen immer noch Inkonsistenzen bei einigen der Komponenten, die wir kaufen. Einige dieser Inkonsistenzen könnten in der von uns verwendeten Ausrüstung liegen, aber in letzter Zeit wurden gute Schritte unternommen In diesem Bereich sind einige davon betroffen, wie die Lieferanten diese Geräte verwenden und die Materialien recyceln. Es geht jedoch nicht nur um die Plattformen und Materialien; wir brauchen auch bessere Designtools für AM.
Wir alle kennen die leichten Hohlstrukturen mit Gitterwerk im Inneren. Dies sollte perfekt für den Motorsport und die Luft- und Raumfahrt sein, aber in Wirklichkeit sind wir nicht in der Lage, Festigkeit, Steifigkeit und Versagensmechanismen solcher Komponenten gut genug vorherzusagen, um ihr volles Potenzial auszuschöpfen.
AMFG:Wie sehen Sie die Entwicklung von AM in der Formel 1 in den nächsten Jahren?
Pat:Wir finden ständig neue Anwendungen. Mit der Größe der Toolbox steigt auch die Anzahl der Anwendungen.
Metalle machen jedes Jahr große Fortschritte, ebenso wie Hochtemperaturpolymere. Wenn sie sich weiterentwickeln und wir besser verstehen, wie man sie verwendet, können wir viel mehr aus AM-Teilen herausholen.
Es ist eine ziemlich aufregende Zeit für AM, es gewinnt viel Aufmerksamkeit und Geld. Dies kann nur gut für die gesamte Branche sein, denn es ist noch ein weiter Weg, bis wir die konventionelle Fertigung vollständig herausfordern können.
www.renaultsport.com
3d Drucken
- Überdenken des Softwareintegrationsprozesses für additive Fertigungsverfahren
- Experteninterview:Felix Ewald, CEO von DyeMansion
- Interview mit einem Experten:Ibraheem Khadar von Markforged
- Interview:Dominic Parsonson von Fuji Xerox Australia
- Experteninterview:James Hinebaugh von Expanse Microtechnologies
- Experteninterview:CEO von PostProcess Technologies zur Lösung des Post-Processing-Engpasses für die additive Fertigung
- Experteninterview:Sintavia-Präsident Doug Hedges über die Serienproduktion mit 3D-Metalldruck
- Experteninterview:Brian Alexander von Solvay zur Entwicklung von Hochleistungspolymeren für den 3D-Druck
- Experteninterview:Jabils Rush LaSelle zur Zukunft der additiven Fertigung
- Additive Fertigung in der Luft- und Raumfahrt