Experteninterview:Sintavia-Präsident Doug Hedges über die Serienproduktion mit 3D-Metalldruck
Sintavia ist ein unabhängiger Hersteller, der Dienstleistungen zur Herstellung von Metalladditiven für kritische Industrien wie Luft- und Raumfahrt und Verteidigung sowie Öl und Gas anbietet .
Mit Fokus auf die Serienfertigung von Metallteilen mittels additiver Fertigung bietet das Unternehmen einen einzigartigen End-to-End-Service, der neben der Fertigung und Nachbearbeitung auch die Prüfung umfasst , Metallurgie und Pulvercharakterisierung im hauseigenen Labor.
Kürzlich hat Sintavia seine Expansionspläne bekannt gegeben und eine brandneue 55.000 Quadratmeter große Anlage mit einem klaren Schwerpunkt auf Produktion bezogen.
Diese Woche freuen wir uns über ein Gespräch mit Sintavias Präsident Doug Hedges, um zu besprechen, wie das Unternehmen hochwertige, zertifizierte Metallteile herstellt, warum AM perfekt für die Luft- und Raumfahrtindustrie ist und was die AM-Branche tun kann, um die Einführung der Technologie zu beschleunigen.
Können Sie uns etwas über Sintavia erzählen?
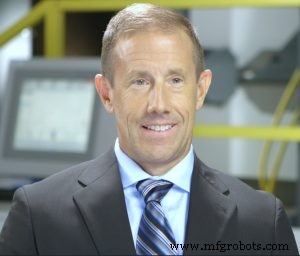
Sintavia wurde 2012 von Brian Neff, dem CEO und Chairman des Unternehmens, gegründet. Das Unternehmen wurde als interne additive Fertigung mit einem Unternehmen namens CTS Engines gegründet, einem unabhängigen MRO für Düsentriebwerke mit Sitz in Fort Lauderdale, Florida.
Sintavia wurde 2015 ein separates Unternehmen und wir zogen nach Davie, Florida, wo wir noch heute sind.
Als Unternehmen haben wir einen umfassenden Hintergrund in der Luftfahrt. Wir sahen, dass sich die Möglichkeit bot, diesen Hintergrund zu nutzen, um ein vertikal integriertes Unternehmen mit vielen verschiedenen Angeboten zu gründen. Um gut in der additiven Fertigung zu sein, müssen Sie auch in Messtechnik, Metallurgie, Zerspanung, Wärmebehandlung, Prüfung usw die MRO- und OEM-Fertigungsbereiche, um ein neues, eigenständiges Unternehmen zu schaffen, das sich auf Luft- und Raumfahrt und Verteidigung sowie Öl und Gas konzentriert.
Das Einzigartige an Sintavia ist, dass die vertikale Integration alles, was wir tun, untermauert:von der Nachbearbeitung, Qualität, Metallurgie, Scannen usw. Alle diese Elemente befinden sich unter einem Dach in unserer Produktionsstätte hier in Davie, Florida.
Die Luft- und Raumfahrt ist ein zentraler Schwerpunkt für Sintavia. Könnten Sie uns einige Vorteile der additiven Fertigung für die Luft- und Raumfahrtindustrie erläutern?
Die additive Fertigung funktioniert aus verschiedenen Gründen gut für die Luft- und Raumfahrt.
Zunächst ist es wichtig zu beachten, dass die Technologie als Prototypenentwicklungswerkzeug für OEMs in der Luft- und Raumfahrt- und Verteidigungsindustrie begann, um Designs und Tests schnell zu wiederholen. die Motoren. Es hat sich jetzt so entwickelt, dass Unternehmen Motoren mit additiven Teilen bauen.
Das ist also immer noch ein großer Treiber. Aber dann sind da noch all die anderen typischen Vorteile, die AM zu einer großartigen Technologie machen. Hier meine ich die Konsolidierung von Schweißkonstruktionen, komplexe Gussteile, Leichtbau, werkzeuglose Konstruktion. Natürlich ist die Komplexität nicht kostenlos – aber sie wird durch die Verwendung von Additiven stark erweitert.
Zum Beispiel liegt für uns ein Hauptaugenmerk bei der Teileauswahl auf externen Ventilkörpern an der Außenseite von Düsentriebwerken und Kanälen. Einen aufstrebenden Markt für Chassis und Wärmetauscher sehen wir auch in der Luft- und Raumfahrtindustrie.
Eine der von Ihnen verwendeten Metall-3D-Drucktechnologien ist Powder Bed Fusion. Welche Vorteile bietet diese Technologie für Luft- und Raumfahrtanwendungen?
Nun, Metall-3D-Druck im Allgemeinen eignet sich wirklich für einzigartige Designs.
In der Frühphase unserer Arbeit setzen wir Pulverbettschmelzen mit Lasern und Elektronenstrahlen ein, um schichtweise Hochdruckkanäle und Komponenten aufzubauen. Der Einsatz der Technologie als Ersatzwerkzeug für Schweiß- und Gussteile, die bereits in der Industrie verwendet werden, hat offensichtlich den Vorteil.
Aber die Kraft von Additiven geht weit darüber hinaus:Sie können Teile besser, leichter und stärker herstellen – was im Wesentlichen eine verbesserte Leistung ermöglicht. Um die Leistungsfähigkeit von AM wirklich nutzen zu können, müssen die Komponenten letztendlich für die additive Fertigung ausgelegt sein.
Mit der additiven Fertigung – ich spreche hier in erster Linie von Lasern – kann man Bauteile wie Wärmetauscher und Fahrwerke nutzen, um Geometrien herzustellen, die bisher nicht herstellbar waren.
Sie haben beispielsweise auch Strömungskörper oder Ventilbaugruppen, die Sie mit AM schneller herstellen und konsolidieren können. Dadurch können unsere Kunden nicht nur ihre bestehenden Lieferketten optimieren, sondern auch bessere Produkte herstellen und die Stärken des OEM-Marktes für Luft- und Raumfahrt sowie Verteidigung ausspielen.
Nehmen Sie Wärmetauscher als Beispiel:Additive Manufacturing ermöglicht Ihnen um sehr feine Wände und kleine, komplizierte Geometrien im Inneren des Bauteils herzustellen. Sie können also eine Wand von 200 Mikrometer oder weniger haben. Darüber hinaus haben Sie mit der additiven Fertigung jetzt eine bessere Möglichkeit, die Wärme aus dem Bauteil abzuleiten. Das ist großartig, denn das Ziel des Endspiels bei Wärmetauschern besteht darin, die Wärme aus dem Bauteil zu entfernen, damit Sie mehr Elektronik darin packen können.
Wir verwenden additive Metallfertigung, um ihre Produkte zu verbessern. Alles von Ventilkörpern, externen Düsentriebwerkskomponenten, Kanälen und Wärmetauschern bis hin zu Chassis und verschiedenen Arten von Rohrstrukturen, die durch Schweißnähte mit vielen komplexen Vorrichtungen und Vorrichtungen hergestellt wurden, um sie zusammenzuschweißen.
Das heißt , wir machen noch viel mehr. Wir arbeiten beispielsweise an dem, was sich im Inneren von Turbomaschinenausrüstungen befindet, von einem kleineren Laufrad, das sich in einem Kompressor befinden könnte, bis hin zu einem größeren Laufrad, das sich in einer Rakete befinden könnte.
Wir haben einen Schwerpunkt in der kommerziellen Luft- und Raumfahrt – im Wesentlichen Düsentriebwerke – und einen weiteren Schwerpunkt auf Antriebe, bei denen es sich um Raketenteile handelt.
Wir haben dann das „Dazwischen“ innerhalb der Luft- und Raumfahrt- und Verteidigungsindustrie, womit ich mich auf die obskuren Komponenten beziehe, die früher aus 10 bis 100 Stück gefertigt wurden, aber jetzt können wir in ein Einzelstück mit additiver Fertigung.
Könnten Sie auf einige der Designherausforderungen eingehen, die mit diesen Anwendungen verbunden sind?
AM ist ein relativ neues Verfahren in der Fertigung. Wir verwenden Laser oder Elektronenstrahlen, um das Pulver schichtweise aufzuschmelzen. Im Wesentlichen machen wir kleine bis mittelgroße Schweißkonstruktionen, das „Mikroschweißen“.
Bei diesem Mikroschweißverfahren gibt es eine schnelle Abkühlung, bei der der Laser das Metallpulver freilegt. Sie haben einen Fall von zwei Extremen:einen sehr heißen Druckprozess, bei dem gleichzeitig eine schnelle Abkühlung stattfindet.
Aufgrund dieser extremen Temperaturunterschiede unterliegt Ihr Teil einem Verzug. Diese Teile sind also nicht wie herkömmliche Schweißkonstruktionen aus Gussteilen; sie sind an und für sich einzigartige Gegenstände.
Eine der größten Herausforderungen besteht darin, vorherzusagen, wie sich diese Teile im additiven Fertigungsprozess bewegen werden. Ein wesentlicher Teil dieser Herausforderung besteht darin, diese hochmoderne Technologie und High-Tech-Tools zu verwenden, um die Vorhersage zu Beginn zu machen, um bei der gesamten Koordination des Prozesses zu helfen.
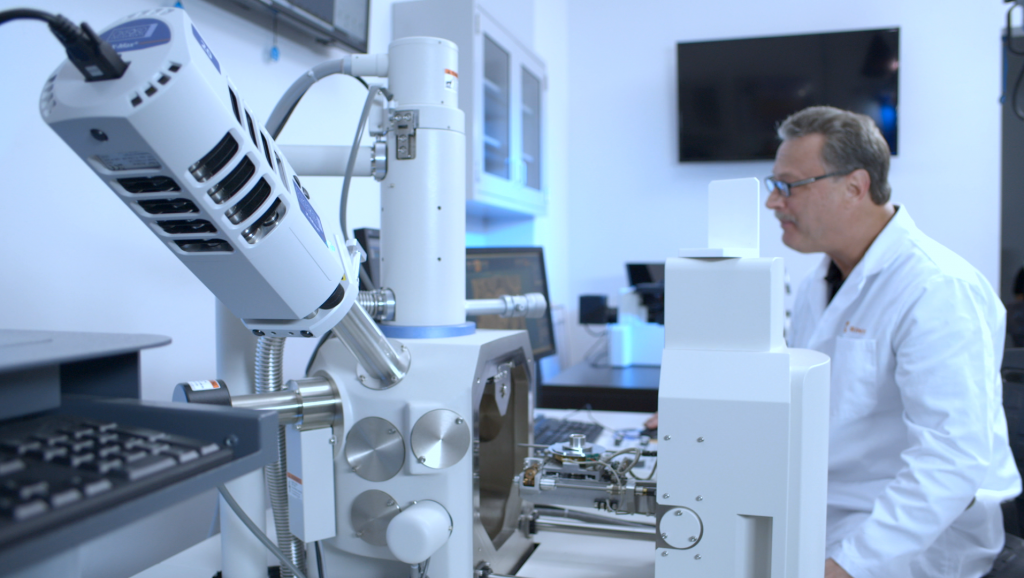
Wir bei Sintavia verwenden die Finite-Elemente-Analyse (FEA) zu Beginn des Konstruktionszyklus. Die Ingenieure von Sintavia erhalten von unseren Kunden die ersten Daten in Form von CAD-Modellen, Zeichnungen und Spezifikationen. Unsere Ingenieure arbeiten mit unseren Kunden zusammen, um wichtige Parameter zu erarbeiten, z Teil.
Wir verwenden Mathematik, um vorherzusagen, wie das Teil verzerrt wird, und minimieren diese Verzerrung, um ein Teil mit sehr hoher Wiedergabetreue zu erhalten. Wir müssen wissen, wie sich dieses Teil auf uns bewegen und verschieben wird, damit wir Flansche, Bohrungen, Löcher usw. Mit diesem Ansatz können wir auch die Nachbearbeitung dieses Teils zu einem späteren Zeitpunkt berücksichtigen.
Bedenken Sie, dass die additive Fertigung ein enorm leistungsfähiger Prozess zur Herstellung komplexer Teile ist, der jedoch in Abstimmung mit herkömmlichen Verfahren eingesetzt werden muss. Die Abstimmung des additiven Verfahrens mit dem subtraktiven Verfahren ist entscheidend.
Wir hören viel über die Herausforderungen bei der Nachbearbeitung von Metallteilen und das ist eine der Dienstleistungen von Sintavia. Könnten Sie uns durch einige der größten Herausforderungen in der Nachbearbeitung und Ihrem Ansatz führen?
Die Nachbearbeitung muss eine koordinierte Anstrengung zwischen dem Druckprozess selbst und der Nachbearbeitung sein, die mit diesem Teil nach der Produktion einhergeht.
Eine häufige Herausforderung, die die meisten Leute nicht sehen, ist die Pulverentfernung nach dem Prozess. Nach dem Druckvorgang muss das gesamte Pulver vom Teil entfernt werden. Da einige dieser Teile sehr komplexe Geometrien aufweisen, stellen wir kundenspezifische Maschinen – entweder Ultraschall- oder herkömmliche Vibrationssysteme – zum Entfernen des Pulvers her.
Es ist typisch, das Pulver vor dem nächsten Schritt vom Teil zu entfernen, der fast immer zum Spannungsabbau dient. Wir entlasten intern entweder mit einem Vakuumofen oder einem Kastenofen, um die Restspannungen aus dem additiven Bauprozess zu entfernen.
Von dort aus gehen Sie zu einem Drahterodiergerät oder einer Bandsäge, um das Teil von der Platte zu entfernen. Dann müssen Sie natürlich die Stützen entfernen. Diese Stützen können alles sein, von einfachen Gitterstützen bis hin zu etwas sehr Massivem, das verwendet wird, um das Teil zu halten und sehr große und Nickel-Superlegierungsteile herzustellen. Diese unterliegen großen thermischen Belastungen.
Aus diesem Grund benötigen Sie möglicherweise einen sehr robusten maschinellen Prozess, um die Stützen von diesen Teilen zu entfernen. Das kann mit erheblichem Aufwand verbunden sein. Und wenn ich „maschineller Prozess“ sage, kann das viele verschiedene Dinge bedeuten. Es könnte so einfach sein, sie einfach mit einer Zange an einer sehr steifen fünfachsigen Werkzeugmaschine abzubrechen, um diese Stützen vom Teil zu entfernen.
Ab diesem Punkt haben Sie mehrere Möglichkeiten. Sie können zum Beispiel zu HIP gehen, das wir vor Ort anbieten, oder wir verwenden die maschinelle Bearbeitung. Wenn ich in diesem Fall von maschineller Bearbeitung sage, meine ich maschinelle Bearbeitung zum Drucken. Dies ist also wirklich nicht anders als das, was Sie in einer Maschinenwerkstatt sehen würden.
Zum größten Teil haben wir eine 2D-Zeichnung mit vielen Kontrollen und wir bearbeiten dieses Teil, um es mit den Spezifikationen in Einklang zu bringen.
Um zu den Metallpulvern selbst zu kommen, wie läuft die Entwicklung von Metallpulvern bei Sintavia ab?
Um es klar zu sagen, wir entwickeln nicht wirklich Pulver an sich. Aber wir waren daran beteiligt, Unternehmen bei der Entwicklung von Legierungen zu unterstützen, die in der Vergangenheit nicht kommerziell erhältlich waren.
Wir haben Firmen, mit denen wir zusammenarbeiten, die beispielsweise eine Variante eines Werkzeugstahls oder eine Variante aus Edelstahl anbieten. Dies sind in der Regel Speziallegierungen, die sie entwickelt haben, um in Zukunft einen Leistungsvorteil zu erzielen.
Wir haben fluggeprüfte Pulverlösungen für die Luft- und Raumfahrtindustrie. Wir beschaffen das Pulver, bringen es in unser Labor und führen es durch eine Vielzahl von Tests, bevor der Bau beginnt.
Eine unserer Stärken bei Sintavia ist die vollständige Charakterisierung unseres Pulvers vor Ort in unserem Labor. Dies ermöglicht es uns, Proben zu nehmen und zu verstehen, was mit dem Pulver passiert. Normalerweise lagern andere Unternehmen diesen Prozess aus. Während wir also Materialien von unserem Pulverlieferanten beziehen, führen wir Durchflusstests, Morphologie, Partikelgrößenverteilung, Gasanalyse, ICP für Chemie usw. durch.
Wir führen etwa acht oder neun Tests durch, um sicherzustellen, dass die Pulver die Herstellungsanforderungen unserer Kunden erfüllen. Dann, während das Pulver verwendet wird, beproben und archivieren wir diese Pulverproben, um zu verstehen, was mit dem Pulver während des weiteren Baus passiert. Dies bedeutet, dass wir genau verstehen können, was mit dem Pulver passiert, wenn es nach und nach verwendet wird.
Sintavia hat angekündigt, diesen Monat ein brandneues Werk mit einer Aufstockung der Maschinen zu eröffnen. Könnten Sie die Vision hinter dieser neuen Einrichtung teilen?
Wir freuen uns sehr, diesen Monat unsere neue Einrichtung eröffnen zu können.
Die neue Einrichtung wird 55.000 Quadratfuß groß sein und wir werden diese Einrichtung auf unseren früheren Erfolgen aufbauen.
Ein wichtiger Punkt ist, dass es sich stark um die Produktion dreht. Wir werden neue Maschinen im Wert von über 30 Millionen US-Dollar, größere moderne AM-Ausrüstung, Pulverfördersysteme, Backup-Generatoren, Stromversorgungen und Inertgas beherbergen. Wir gehen davon aus, dass wir mehr als 135 neue Stellen für Sintavia und Südflorida schaffen werden.
Die neue Anlage ist wirklich die Vision, das, was wir in einem kleineren Maßstab gemacht haben, 12 Maschinen hier in unserer aktuellen Anlage zu betreiben und dies auf eine 55.000 Quadratfuß große Anlage mit bis zu 65 . zu skalieren Maschinen.
Bei der additiven Fertigung, bei der Wärmebehandlung, werden große Anstrengungen unternommen. Nachbearbeitung, Veredelung, Reinigung usw.
Im Wesentlichen möchten wir den additiven Prozess in einer einzigen Einrichtung steuern. Das ist wirklich das Geschäftsmodell:Wir wollen das, was wir getan haben, skalieren und dies in einen Fertigungsprozess einbringen, der unseren OEM-Kunden Qualität und Wiederholbarkeit garantiert.
Könnten Sie in Zukunft auf andere Branchen wie die Automobil- oder Medizinbranche ausweiten, wo auch eine große Nachfrage nach 3D-gedruckten Metallteilen besteht?
Ja, absolut. Wir haben einiges im Gange, sowohl in der Automobilindustrie als auch in der Medizin. Und es gibt noch andere Branchen, für die Additiv ebenfalls Sinn macht.
Wir beschäftigen uns beispielsweise mit Industriegasturbinen. Obwohl unser Hintergrund Fluggasturbinen sind, sind bodengebundene Gasturbinen für Energie im Grunde skaliert und leicht unterschiedliche Flugturbinentriebwerke.
Die Technologie lässt sich auch sehr gut im biomedizinischen Sektor anwenden.
Sintavia ist AS9100-akkreditiert — AS9100 ist ein Qualitätsmanagementsystem für die Luft- und Raumfahrtindustrie. Unser Labor ist für mechanische Messungen nach ISO 17025 akkreditiert, was alles von Pulvercharakterisierung und Chemie bis hin zu Zugtests und Ermüdungstests bedeuten kann.
Die biomedizinische Industrie hat eine andere Akkreditierungsagentur; Das meiste davon ist auf ISO 13485 zurückzuführen. Sobald Sie AS9100 haben, können Sie zu ISO 13485 wechseln. Es ist kein großer Sprung zwischen diesen verschiedenen Branchen. Denn:Qualität ist Qualität und Prozesse sind Prozesse. Wenn Sie in der Luft- und Raumfahrt tätig sind, können Sie diesen Übergang zu anderen Märkten vollziehen.
Außerdem ist die Qualitätskontrolle neben allem, was ich erwähnt habe, der wichtigste Aspekt.
Vom ersten Tag an haben wir uns auf die Entwicklung unseres Qualitätssystems mit AS9100 konzentriert, ISO- und Nadcap-Zertifizierungen. Dies ist alles sehr vorteilhaft für unsere OEM-Kunden und kann definitiv auch eine Ressource für andere Branchen sein.
Was sind Ihrer Meinung nach einige der Dinge, die erforderlich sind, um die Einführung des Metall-3D-Drucks zu beschleunigen?
Bei all unserer Technologie und unseren Fähigkeiten in der Analytik sollten wir uns wirklich auf das konzentrieren, was das Geschäft antreibt. Das Geschäft wird von Geld und Geschwindigkeit angetrieben. Das bedeutet, dass die Technologie schneller, billiger und etablierter werden muss.
Aber wir sehen, wie sich die Dinge ändern. Während unserer Zeit hier bei Sintavia haben wir gesehen, wie sich Metal AM entwickelt hat. Aluminium war beispielsweise einst ein relativ schwierig zu druckendes Material in der additiven Fertigung, aber heute ist es fast alltäglich. Da wir zusätzliche Laser sehen, wie wir das Know-how und die Konstruktion von Teilen für die additive Fertigung sehen, wird es unseren Kunden eine schnellere Geschwindigkeit und Kosteneinsparungen bieten.
All dies kam historisch aus der Prototyping-Industrie, und wir wollen das in die Serienproduktion überführen. Es gibt bestimmte Dinge, die wir tun müssen, um es schneller und billiger zu machen, Qualität zu bieten und die Vorteile zu bieten, die jedermann kennt, die Metalladditive bieten können.
Wie sehen Sie die Entwicklung der additiven Metallfertigung in den nächsten fünf Jahren, und wie passt Sintavia in diese Vision?
Was wir wirklich tun müssen, ist, Teile serientauglich herzustellen. Für kritische Industrien müssen wir sicherstellen, dass wir echte Metallteile produzieren, die voll funktionsfähig sind.
Wir wissen, dass diese Teile in Bezug auf die mechanischen Eigenschaften sehr gut mit Gussteilen konkurrieren. Mit den richtigen Prozessen und Kontrollen können sie auch mit Rohprodukten, teilweise sogar mit Schmiedeprodukten, konkurrieren.
Qualitätskontrolle, d. h. das Verständnis der Qualitätsanforderungen und die Möglichkeit, Ihr Teil zu validieren, wird in Zukunft wirklich einen Unterschied machen.
Wir dürfen aber auch nicht aus den Augen verlieren, dass die Technologie noch relativ neu ist. Als Branche machen wir viele Dinge zum ersten Mal.
Das bedeutet, dass das Front-End des Prozesses in erster Linie erlernt werden muss.
Zum Beispiel müssen Ingenieure zu Beginn des Prozesses Support-Strategien verstehen und verbringen Sie Zeit damit zu lernen, wie die Teilegeometrie und die Stützgeometrie am besten optimiert werden können, was wiederum dazu beiträgt, bessere Teile zu produzieren und sicherzustellen, dass sich die Stützen relativ leicht lösen.
Dank dieser Arbeit, die bei der beginnen, haben Sie den kostspieligen und zeitaufwändigen Schritt des Entfernens des Supports durchgeführt und ihn deutlich kostengünstiger gemacht. Der technische Aufwand bei der Herstellung der Teile ist wirklich entscheidend, um einen ausgereiften Punkt zu erreichen, um Produkte nacheinander herzustellen.
Wie sieht die Zukunft von Sintavia aus?
Es sieht sehr spannend aus! Natürlich sieht es auch ziemlich anspruchsvoll aus, als wir in unser neues Werk einziehen. Wir werden Lean Manufacturing implementieren. Wir haben die erste große, schlanke additive Fertigungsanlage, die speziell für unsere Ausrichtung auf OEMs und die Lieferkette entwickelt wurde.
2019 werden wir einen Großteil der Arbeit fortsetzen, die wir in den letzten Jahren geleistet haben, um Teile für unsere Kunden zu qualifizieren und zu entwickeln.
Ich werde keine Namen nennen, aber wenn man sich die führenden Luft- und Raumfahrtunternehmen weltweit ansieht, ist die Wahrscheinlichkeit sehr hoch, dass wir für sie Geschäfte machen.
In einigen Fälle, wie unsere Beziehung zu Honeywell, wo wir der erste AM-Lieferant sind, der zugelassen ist, flugfertige Teile für Honeywell Aerospace herzustellen. Wir haben uns mit Honeywell zusammengetan, um unsere aktuelle Anlage und unsere nächste Anlage zu nutzen, um dies herauszubringen und Produktionsteile für Honeywell herzustellen.
Honeywell nimmt die Technologie relativ schnell an und hat viele, viele Anwendungen. Aber wenn Sie Honeywell verlassen, besteht eine gute Chance, dass wir jetzt für sie arbeiten, egal ob es sich um eine Flugzeugzelle oder ein Triebwerkskraftwerk handelt, ob es sich um einen Luft- und Raumfahrt- und Verteidigungsanbieter handelt.
Wir sehen 2019 und 2020 als relativ große Jahre für uns an, was die Einführung von Metalladditiven betrifft. Es ist wirklich aufregend, dass Honeywell heute hier ist, aber wir werden sehen, dass wir in den kommenden Jahren mehr Kunden haben werden, die Serien produzieren.
Wir richten unser Unternehmen aus, um diese Ressource für die OEMs der Welt bereitzustellen, damit sie einen vertikal integrierten Partner aus einer Hand für die Herstellung dieser Teile mit additiver Fertigung haben.
Irgendwelche letzten Gedanken?
Ich möchte wiederholen, dass Qualität unser Fokus ist.
Unsere Kunden sind ohne Zweifel die risikoscheuesten Kunden der Welt. Damit sie sich beim Fliegen dieser kritischen Komponenten aus der additiven Fertigung wohl fühlen, steht Qualität an erster Stelle.
Letztendlich möchten wir Produkte an technische Zeichnungen und Spezifikationen anpassen, um sie in realen Anwendungen zu verwenden. Um dies zu erreichen, muss man sich auf Konformität konzentrieren.
Außerdem ist AM heute der Ort, an dem die gesamte Medienaufmerksamkeit liegt und wo viel Zeit und Geld ausgegeben werden. Aber letztendlich sollte es darum gehen, den Teil, den Sie durch die additive Fertigung geschaffen haben, zu übernehmen und an die technischen Anforderungen Ihrer Kunden anzupassen.
Ja, wir sprechen gerne über additive Fertigung. Aber ich betrachte es auch gerne als fortgeschritten Herstellung. Ich möchte mich von den Schlagworten der additiven Fertigung entfernen und sagen, dass wir ein fortschrittlicher Hersteller von Präzisionsteilen für die Luft- und Raumfahrt sind. Wir möchten fortschrittliche Teile herstellen, um sicherzustellen, dass unsere Kunden ihre aktuellen Designs erheblich verbessern können.
Um mehr über Sintavia zu erfahren, besuchen Sie: https://sintavia.com/
Über Doug Hedges
Doug Hedges verfügt über mehr als 20 Jahre Erfahrung in der Luft- und Raumfahrtindustrie, vom experimentellen OEM-Komponentendesign bis hin zu FAA-zugelassenen Reparaturen, Änderungen und Komponentenentwicklung basierend auf Industriestandardspezifikationen und -kontrollen.
Vor seiner Tätigkeit bei Sintavia war er als Senior Engineer bei CTS Engines, Entwicklung von Reparaturen und Prozessen für die General Electric Triebwerksüberholung, Lead Project Engineer bei HEICO Aerospace, Senior PMA Engineer bei Kapco Global und Design Engineer bei Rolls-Royce. Doug hat einen BSME-Abschluss in Maschinenbau von der University of Minnesota.
Experteninterviews
In der Reihe Experteninterviews der AMFG werden innovative Unternehmen und Einzelpersonen vorgestellt, die die Zukunft der additiven Fertigung mitgestalten. Weitere Informationen zur Teilnahme an der Serie erhalten Sie unter [email protected].
3d Drucken
- Wie können Sie mit additivem MES auf die additive Serienproduktion skalieren?
- Interview mit einem Experten:Professor Neil Hopkinson, Direktor für 3D-Druck bei Xaar
- Interview mit einem Experten:Philip Cotton, Gründer von 3Dfilemarket.com
- Interview mit einem Experten:Dr. Alvaro Goyanes von FabRx
- Experteninterview:Ultimaker-Präsident John Kawola über die Zukunft des 3D-Drucks
- Experteninterview:Sintavia-Präsident Doug Hedges über die Serienproduktion mit 3D-Metalldruck
- Experteninterview:Brian Alexander von Solvay zur Entwicklung von Hochleistungspolymeren für den 3D-Druck
- Experteninterview:Carbons Mitbegründer Philip DeSimone über den Übergang zur Großserienproduktion mit 3D-Druck
- 4 Herausforderungen der additiven Fertigung, die mit Software gelöst werden können
- Experteninterview:Jabils Rush LaSelle zur Zukunft der additiven Fertigung