Traktion gewinnen mit Markforged:3D-gedruckte Räder umspritzen und gießen
Anmerkung des Herausgebers:Dieser Gastbeitrag wurde von Charles Guan verfasst, einem Absolventen des MIT Maschinenbau und ehemaliger Lehrer für Maschinenwerkstatt und Design am MIT. Er ist auch der Erbauer der Roboterüberholung auf ABCs BattleBots. Er arbeitet als technischer Berater für Robotik und Transportwesen und wird von Markforged gesponsert, um an BattleBots und anderen Robotik-Wettbewerben teilzunehmen. Weitere Informationen finden Sie auf seiner Website und auf Equals Zero Robotics!
Raddesign
Räder. Mit über 6.000 Jahren Geschichte im Rücken könnten Sie sich vorstellen, dass wir sie inzwischen perfekt gemacht haben. Wie ich in BattleBots Season 2 auf die harte Tour herausgefunden habe, ist dies in vielerlei Hinsicht alles andere als wahr. Sie können das Rad tatsächlich neu erfinden und es falsch machen. Ich habe Overhaul 2.0 mit einer leistungsstarken und stabilen quadratischen 6-Rad-Antriebsplattform entwickelt, um die Geschwindigkeit zu meinem Vorteil zu nutzen, um Gegner in seinem Grappling-Lifter zu fangen. Ich wählte die Räder basierend auf meinem Wissen aus:Industrierollen mit mittlerer Härte und Laufflächen aus thermoplastischem Elastomer (TPE), die von Anfang an im Roboterkampf verwendet wurden. 16-PS-Motoren durch diese Räder in einen Roboter zu stecken, der in 1 Sekunde 30 km/h erreichen sollte, war Neuland.
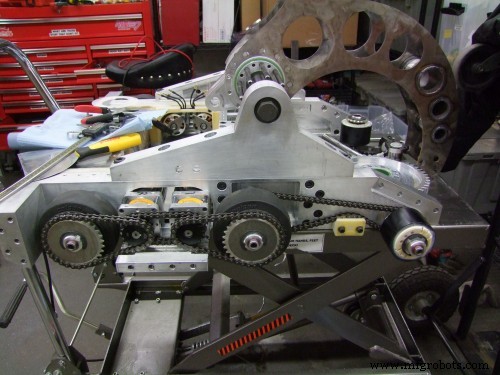
Das hat in der Arena überhaupt nicht zu meinen Gunsten geklappt. Die TPE-Räder begannen sich zu lösen und schmolzen buchstäblich von der Kraft, die durch sie geleitet wurde. Ihr glattes Profil glitt über die losen Trümmer und Partikel in der Kiste, als würde der Bot auf Eis fahren. Meine 16 PS bürstenlosen Antriebsmotoren waren daher so ziemlich eine totale Verschwendung. Wenn Sie sich mein Match gegen die Beta in der vergangenen Saison ansehen, werden Sie feststellen, dass ich BattleBots für einen Großteil des Matches mit dem D1 Grand Prix verwechselt habe.
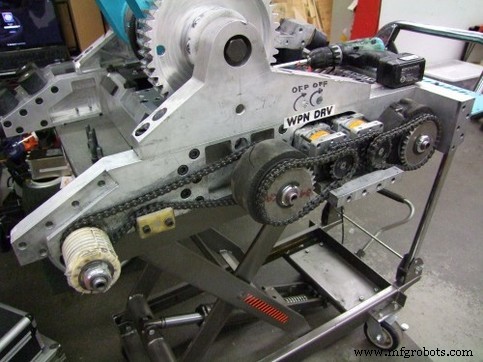
Nach dem BattleBots Season 2-Turnier habe ich mich über die nächsten Schritte Gedanken gemacht. Die Räder müssten geändert werden, um die Kraft des Bots auf den Boden zu bringen. Hier begann ich mit der Erforschung gießbarer Gummimischungen. Es machte mir nichts aus, einige Formen herzustellen, das Material zu gießen und dann in der Zeit, die zum Aushärten benötigt wird, an etwas anderem zu arbeiten. Während der zweiten Staffel von BattleBots hatte ich einige Konkurrenten – einschließlich der Beta – vor Ort beobachtet, wie sie ihre eigenen Urethanräder gossen.
Ich wusste nichts über Reifen- und Raddesign, noch über Formen und Gießen. Sprechen Sie über einen Schuss im Dunkeln! Zum Glück hatte ich im Sommer auf der Detroit Maker Faire einige Firmenvertreter von Smooth-On in die Enge getrieben und mit ihnen ausführlich über ihre Gedanken darüber gesprochen, welches ihrer Produkte sich für die Herstellung von Traktionsrädern eignet. Smooth-On ist ein Unternehmen, das sich hauptsächlich auf den Formenbau und das Gießen für Spezialeffekte, Kostüme und Requisiten spezialisiert hat – nicht für industrielle Zwecke. Ihre Vertriebspartner sind jedoch landesweit, sodass ihre Materialien sehr leicht zum Experimentieren verfügbar sind – nur 15 Autominuten von Boston entfernt. Die Mission:Lernen Sie den Harzguss-Workflow kennen, indem Sie maßgeschneiderte Räder für ein maßstabsgetreues 30-Pfund-Modell von Overhaul herstellen, das ich damals für einen Wettbewerb im Herbst 2016 entwarf.
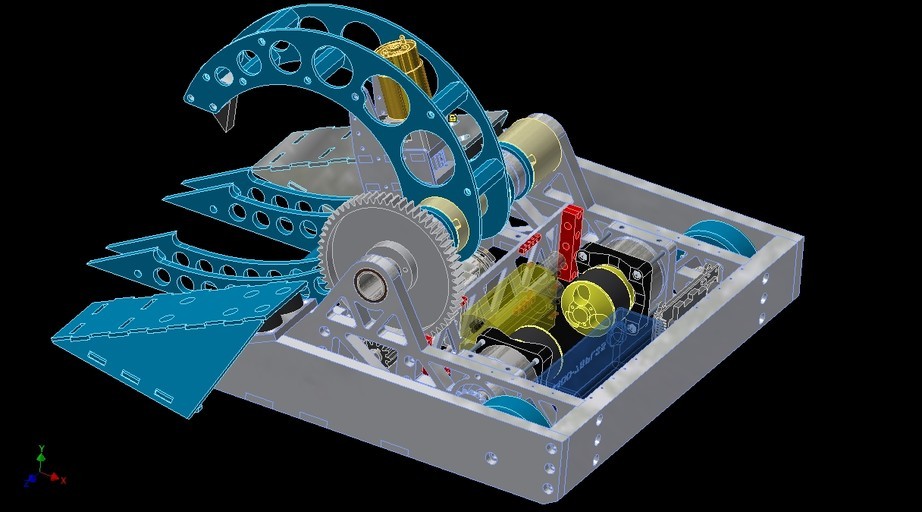
Die Form entwerfen
Die Vertreter wiesen mich auf zwei Materialien hin, die eine vorteilhaft hohe Reißfestigkeit und Zugfestigkeit aufwiesen, die Reoflex- und die Simpact-Serie. Diese beiden Eigenschaften sind bei einer Radmischung wünschenswert, bei der der Gummi ständig durch seine Laufflächendicke geschert und über den Boden geschleift wird. Ich habe eine Probe von ReoFlex 50 (für eine Härte von 50 A, die einigermaßen weich wie eine Schuhsohle ist) in die Hände bekommen und mich daran gemacht, die Form und die Nabe zu entwerfen.
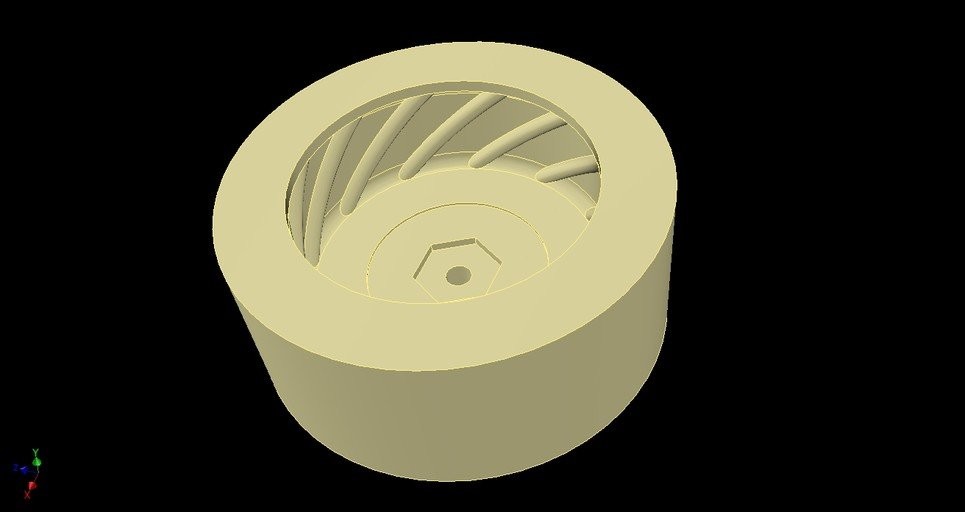
Nach der Leistung von Overhaul in der Box war ich ziemlich überzeugt, dass auf der Oberfläche des Rads eine Art Schmutzbeseitigungsfunktion benötigt wird. Wir versuchen zwar nicht, wie bei Autoreifen Wasser zu kanalisieren oder durch Schlamm zu krallen, aber es gab immer noch losen Schutt und Farbflocken aus der Arena selbst, mit denen wir fertig werden mussten. Zu Beginn habe ich ein einfaches spiralförmiges Laufflächenmuster erstellt. Das war in keiner Weise optimiert – ich wollte vorerst nur schnell in die Formgebungsphase kommen. Ich dachte, die spiralförmigen Rillen würden dazu neigen, Schmutz zur Seite weg von der Kontaktfläche zu drücken. Die genaue Ausrichtung und Anzahl der Rillen ist offensichtlich immer noch eine ungeklärte Wissenschaft, wenn Sie jemals Reifen einkaufen gegangen sind.
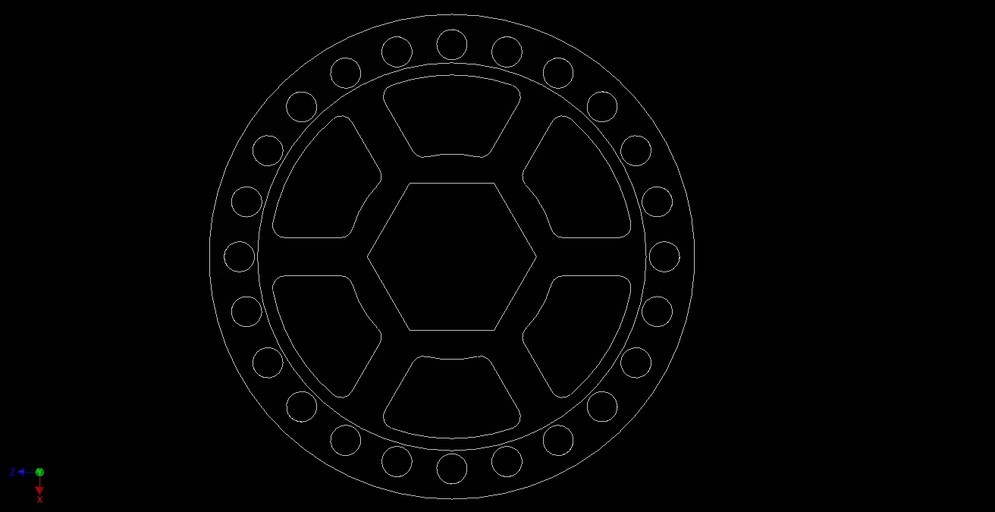
Als nächstes stand ich vor der Aufgabe, die Radnabe zu konstruieren. Ich warf einen Blick in meine Schachtel mit Roller- und Skateboard-Rädern, um mich inspirieren zu lassen. Sie alle hatten ein gemeinsames Merkmal:Durchgangslöcher oder Schlitze, um die und in die das Urethan floss. Mir war sehr wichtig, dass das Laufflächenmaterial auch bei Haftungsversagen auf der Nabe bleiben kann. Ich habe eine ziemlich einfache zylindrische Nabe modelliert, aber mit vielen Durchgangslochmerkmalen in einer sich verjüngenden Mittelrippe, um eine maximale Fläche und einen maximalen Querschnitt für die Haftung des Urethans zu bieten. Ich habe Onyx gegenüber normalem Nylon für die Nabe aufgrund seiner höheren Steifigkeit und Festigkeit gewählt. mit Hafteigenschaften versehen. Die erhöhte Steifigkeit würde es mir ermöglichen, die Radnabe leicht zu machen, während das Harz besser an der mikroskopisch rauen Textur von Onyx über glänzendem Nylon haftet.
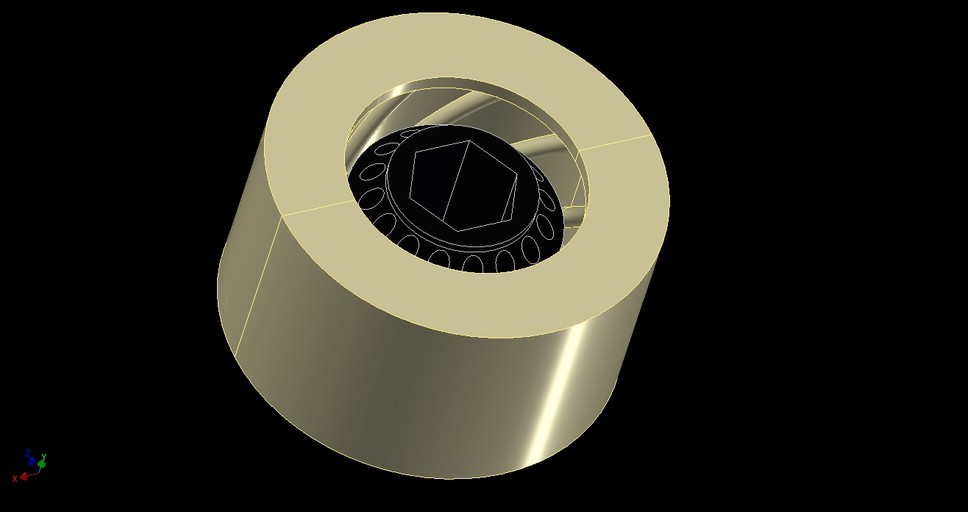
Da die Tiny Overhaul auch einige kleinere Vorderräder benötigen würde, habe ich die parametrischen Funktionen von Autodesk Inventor verwendet, um schnell ein 2-Zoll-Modell zu generieren. Diese Form hatte einen ziemlich beengten Bereich zum Gießen, daher interessierte ich mich dafür, wie sich das Material verhalten würde.
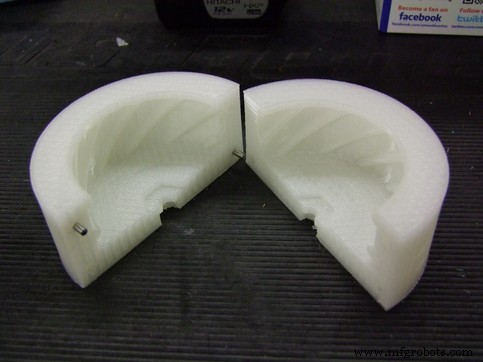
Ich habe eine Testform mit einfachem unverstärktem Nylon auf dem Mark Two gedruckt. Die Form war sehr spärlich – 4 Wände und 4 Dach- und Bodenschichten, aber nur 25 % Füllung, gedruckt auf der gröbsten Schichteinstellung von 0,2 mm. Ich modellierte Registrierungsstiftlöcher in die Hälften, um die Ausrichtung zu gewährleisten.
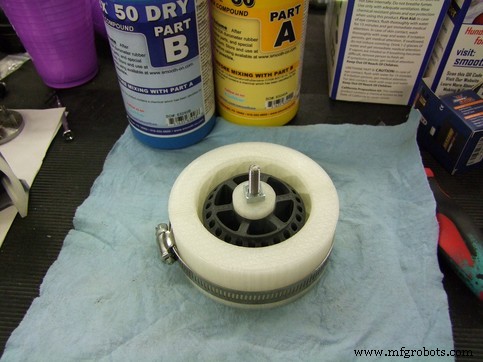
Gießen der Form
Die Formhälften sind so konzipiert, dass sie mit einer einzigen normalen Schlauchklemme zusammengehalten werden. Im Inneren sitzt die Radnabe auf einer Adapterbuchse, um sie in der Form zentriert zu halten, und diese Adapterbuchse hat ein Durchgangsloch zur Unterseite der Formhälften, damit ich eine Haltemutter und eine Schraube vertikal laufen lassen kann, um die Unterseite von . abzudichten die Radnabe gegen die Form. Vor dem Zusammenbau habe ich die Formhälften mit Spritztrennmittel beschichtet.

Auf Anraten von Freunden, die mehr Erfahrung mit Formen und Gießen hatten, habe ich mir einen Vakuumtopf ausgeliehen, um alle Luftblasen aus dem gemischten Harz zu ziehen. Smooth-on wirbt für seine Harze als „Minimierung von Lufteinschlüssen“, aber das Überkochen der Mischung zeigte mir, dass dies weniger als effektiv war. Eingeschlossene Luftblasen würden die Integrität der Radlauffläche verringern, da sie viele Unterbrechungen im Material aufweisen würden. Ich habe den Becher mit gemischtem Material entgast, anstatt die gesamte Form mit flüssigem Harz in die Kammer zu legen, da die gesamte Luft in den Formhälften durch das Drucken von Hohlräumen diese wahrscheinlich verformen oder sogar auslaufen und langsam ausblasen würde.
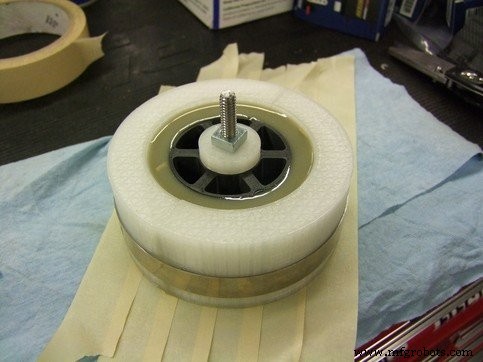
Es dauerte ungefähr 2 Minuten, um die 3-Zoll-Radform zu gießen – ich kippte den Mischbecher gerade genug, um einen kontinuierlichen Flüssigkeitsfluss aufrechtzuerhalten, ließ das Harz sich im Boden absetzen und staute sich nicht über der Form. Lassen Sie das Harz „seine Wasserlinie finden“, um zu vermeiden, dass große Luftblasen im Teil eingeschlossen werden.
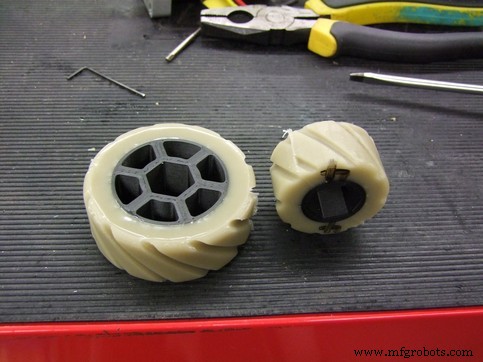
Ich habe als Startcharge sowohl ein 3″-Rad als auch ein 2″-Rad gegossen. Nachdem sich zumindest die ersten beiden Räder solide entwickelt hatten, war es an der Zeit, etwas zu produzieren. Ich habe zusätzliche Formen gedruckt, sodass ich 4 oder mehr Räder auf einmal gießen konnte – einer meiner Mischbecher war perfekt für zwei 3″-Räder und zwei 2″-Räder, also wurde das zum Standard.
Der Aushärtungsprozess
Die meisten Harzhersteller empfehlen eine anfängliche langsame Aushärtung bei Raumtemperatur und anschließendes Erhitzen des Materials, um die Polymervernetzungen weiter zu verstärken. Im Datenblatt von Reoflex 50 steht beispielsweise, das Material 4 bis 8 Stunden auf 65 Grad Celsius zu erhitzen. Ich habe eine beheizte Kammer bei ungefähr 70 Grad Celsius verwendet:Die neuen Räder, die aus dieser hitzebeschleunigten Kur hervorgegangen sind, waren definitiv zäher und widerstandsfähiger bei Berührung.
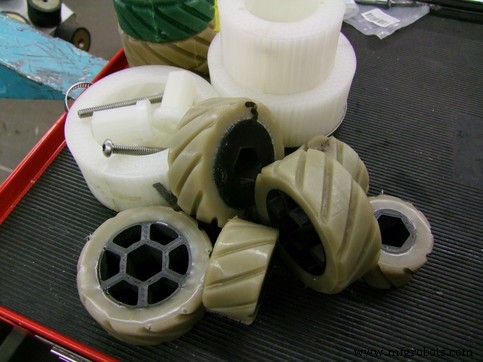
Das Ergebnis nach einer Woche des Experimentierens war ungefähr ein halbes Dutzend jeder Radgröße. Ich hatte meinen Vorrat an ReoFlex 50 aufgebraucht, also entschied ich, dass dies ein guter Ort war, um zu stoppen und sicherzustellen, dass die Räder tatsächlich im Wettbewerb funktionierten, bevor ich mehr Geld für Material ausgab. Ich war die letzten Tage zuvor in einen schönen Kreislauf gekommen – ich habe die Formen als letztes, was ich nachts vor der Abreise getan habe, gegossen, morgens entformt und dann im Laufe des Tages gebacken.
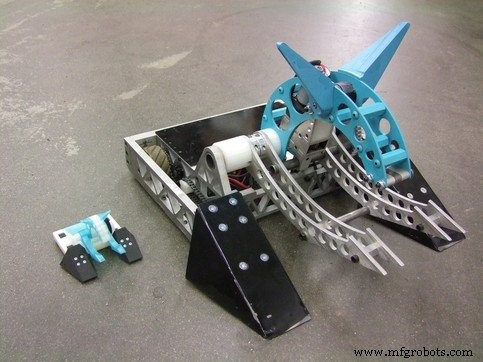
Und so sehen sie im Bot installiert aus. Wenn Sie an der Entwicklung von „30-Haul“, wie wir es nennen, interessiert sind, können Sie sich den Build-Thread auf meiner Website ansehen.
Was kommt als nächstes? Jetzt, da ich den Produktionsprozess erforscht und ein grundlegendes Design vor mir habe, ist es an der Zeit, dass die eigentliche Wissenschaft beginnt. Bleiben Sie dran für Teil II dieser Serie, in dem ich versuche, Räder aus verschiedenen Mischungen herzustellen und ihre Traktion auf einem lackierten Stahlboden zu testen. Im Moment sehen diese Räder nach ein paar harten Fahrten so aus!
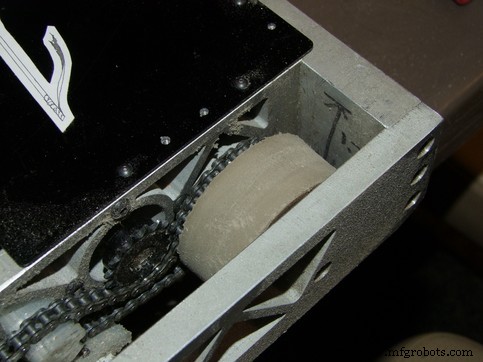
Erfahren Sie mehr über Markforged-Drucker und wie sie für Ihre Anwendungen geeignet sind!
3d Drucken
- Interview mit einem Experten:Spencer Wright von pencerw.com und nTopology
- Endbearbeitung von 3D-gedruckten Teilen mit… Buntstiften?
- Interview mit einem Experten:Ibraheem Khadar von Markforged
- Stratasys geht eine Partnerschaft mit GrabCAD und e-Xstream ein
- Stratasys belebt MakerBot mit der Methode wieder
- Sandguss mit FDM-Technologie
- Bessere Qualitätskontrolle mit 3D-gedruckten Teilen
- Schnallen Sie sich an mit funktionalen 3D-gedruckten Teilen!
- Neue Vorstellung des Go-Karts mit 3D-gedruckten Teilen
- Prototyping und Kleinserienfertigung mit Druckguss