Warum die optische Messtechnik in Bewegung ist
Vor kurzem wurde die Leistungsfähigkeit optischer Messtechnik in Kombination mit Automatisierung erkannt. Was macht die Automatisierung von Messvorgängen so wichtig?
Die Verlagerung der Messtechnik in den Prozess, anstatt sie nur im Qualitätslabor zu belassen, wird die Gesamtqualität verbessern und die Automatisierung der Fertigung selbst effizienter machen“, sagte Robert Wasilesky von Carl Zeiss Industrial Metrology LLC (Brighton, MI). „Metrology Optimized Manufacturing [MOM] ist definitiv ein Trend, den wir sehen.“ Er achtete darauf, dass die Messtechnik die Fertigung nicht ermöglicht – sie funktioniert jetzt gut –, sondern sie optimiert, um noch besser zu funktionieren.
Die optische Messtechnik in ihren verschiedenen Formen ist seiner Meinung nach oft die beste Methode, um die Automatisierung zu verbessern, da sie im Vergleich zu anderen Methoden schnell ist. Zu den weiteren Vorteilen optischer Verfahren gehört ihre Fähigkeit, empfindliche Oberflächen wie Karosseriebleche, Verbundteile oder empfindliche chirurgische Implantate zu messen, ohne sie zu markieren oder zu verformen. Ein weiteres Beispiel ist die Verwendung von Messgeräten zum präzisen Bewegen von Robotern, wodurch ihre Standortgenauigkeit von wenigen Millimetern auf 100 μm oder besser erhöht wird.
MOM zu erweitern, sagte Wasilesky, bedeute, die Kundenschulung zu erweitern. Fertigungsingenieure sind sich heute möglicherweise nicht bewusst, wie viel optimierter ihr Geschäft sein könnte.
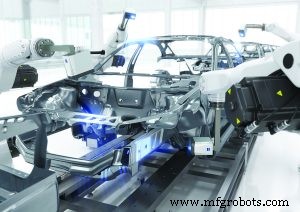
„Ich denke, es gibt ein Potenzial zur Steigerung der Fertigungseffizienz, insbesondere in der Automobilindustrie, durch vergleichbare Sprünge und Grenzen durch Metrology Optimized Manufacturing“, sagte er. Das Konzept muss die Hersteller erreichen, und Wasilesky stellte fest, dass die Automatisierungsseite des Messtechnikmarkts jährlich um fast 20 % wächst, während der Rest des qualitätsbezogenen Markts um etwa 6 % wächst. Er sagte, dies sei zum großen Teil auf die größere Kundenakzeptanz optischer Messmethoden gegenüber Kontaktsonden zurückzuführen, eine Ansicht, die von anderen in einer Reihe von Gesprächen geteilt wurde. Die Technologie ist besser geworden, es gibt eine größere Auswahl an optischen Methoden, und die Verarbeitungssoftware, die auf immer schnelleren Computerplattformen gehostet wird, hat sich dramatisch verbessert. „Während die Prinzipien die gleichen sind, ist es einfach viel leistungsfähiger geworden“, sagte er.
Ein gutes Beispiel für diese Konvergenz aus schnellerer Optik, besseren Algorithmen und leistungsstarker Rechenleistung ist der optische 3D-Sensor AIMax Cloud von Zeiss. Als strukturiertes Lichtsystem klassifiziert, benötigt es nur einen Projektor und einen Sensor. Dies führt zu einem kompakteren Messkopf, aber vielleicht noch wichtiger ist, dass das System so programmiert ist, dass Merkmale schnell gemessen werden, typischerweise in weniger als 0,5 Sekunden – denken Sie an Löcher, Schlitze, Nieten oder T-Stifte – aus einer Punktwolke und nicht Bereitstellen der Punktwolke als Endergebnis. Dies macht es zu einem System, das sich ideal für die Inline-Inspektion eignet, insbesondere für Automobil-Blech- und BIW-Komponenten (Body in White). Wasilesky erklärte, dass das System, einschließlich Sensor- und Roboterbewegung, eine Messgenauigkeit von 300 μm oder mehr nach Six Sigma bieten könnte.
Zeiss bietet auch Lösungen für Near-Line-Messungen sowie schnelleren, optischen Ersatz für CMMs auf dem Shopfloor für Off-Line-Messungen, die ebenfalls nahe am Produktionsort sind. Die AIBox ist ein solches Komplettsystem, das darauf abzielt, KMG-Genauigkeitsniveaus zu erreichen, ohne in einen Qualitätsraum zu gehen. Die AIBox ist in der Lage, einen sphärischen Fehler von weniger als 40 μm gemäß dem VDI 2634-Standard zu messen, wobei sowohl ein digitales Streifenprojektionssystem als auch ein Standard-Photogrammetriegerät verwendet werden. Es ist für Großteile bis 2000 mm Größe und 1000 kg Gewicht Standard.
Automatisierung und Teile
Eines der nützlicheren optischen Messgeräte zum Einbetten in ein automatisiertes System sind Videosysteme auf Präzisionsbewegungstischen, wie z. B. die Nikon iNEXIV-Serie. Da das Messsystem eine Kamera enthält, lässt es sich leicht an Vision-Aufgaben anpassen und eröffnet neue Möglichkeiten, wie das Lesen von Barcodes oder QR-Codes, die heute bei Teilen üblich sind, so Nate Frost, Produktmanager für Nikon Metrology (Brighton, MI). . „Wir können auch Textdaten lesen, entweder eine Teilenummer auf einem Teil oder auf einem gedruckten Papier, das dem Teil beiliegen könnte.“ Damit wird die Automatisierung auf die nächste Stufe gehoben, denn durch Lesen eines Barcodes und Identifizieren des Teils kann das Gerät das richtige Messprogramm aufrufen und die Ergebnisse automatisch in einem Bericht für das einzelne Teil festhalten.
Dies könnte besonders nützlich sein, da sich die Smart Factory und das industrielle Internet der Dinge weiterentwickeln. „Das sind keine klassischen Automatisierungsaufgaben“, sagt Frost. „Das automatische Laden von Teilen in ein Messsystem sollte etwas sein, das jeder Anbieter von Messtechnik anbieten kann. [Das Lesen von Strichcodes ist] stattdessen mit dem Treffen von Entscheidungen verbunden“, sagte er. Es beseitigt den menschlichen Faktor und verbessert gleichzeitig die Qualität.
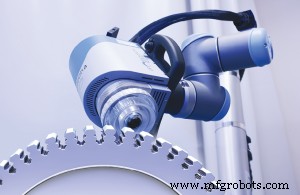
Ebenso wichtig ist eine effiziente Teileprogrammerstellung. Einem allgemeinen Trend in der Branche folgend, ist das Erstellen von Programmen aus dem Offline-Lesen eines CAD-Modells jetzt in CMM-Manager 3.6 von Nikon verfügbar. Dies ist die neueste Version der Support-Software für die Bildverarbeitungssysteme von Nikon. „Die vorherige Software verwendete nur einen Joystick, um ein Programm einzulernen“, sagte Frost. „Das ist ziemlich neu für Videomessprogramme.“ Wieso den? Denn im Gegensatz zur Offline-Programmierung einer Kontaktsonde oder sogar eines Laserliniensensors muss ein Videoprogramm Beleuchtung, Kanteneffekte, Glitzern von reflektierenden Oberflächen und andere für Videos einzigartige Effekte berücksichtigen. „Simulationen können durchgeführt und Inspektionsergebnisse in Echtzeit verifiziert werden. Je vollständiger das CAD-Modell ist, desto effizienter wird der Inspektionsprozess“, sagte Frost. „Mit Bildverarbeitung, Autofokus-Laser, Drehindexer und taktiler Eingabe können wir sogar Merkmale und Geometrien messen, die Sie mit einem herkömmlichen Bildverarbeitungssystem nicht sehen können.“
Warum glaubt er, dass es einen Push zur Automatisierung gibt? „Der gemeinsame Nenner ist, dass Unternehmen ihre Mitarbeiter und ihren Betrieb zurücklehnen“, sagte Frost. „Sie erwarten von ihren Mitarbeitern mehr Flexibilität. Sie möchten, dass sie in der Lage sind, eine CNC-Fräse und ein Messsystem zu betreiben. Wir sehen das überall, aber besonders in Job Shops, wo Mitarbeiter ein Tausendsassa sein müssen.“ Die Automatisierung der Messtechnik wird dies viel einfacher machen.
Hochvolumige Automobilindustrie
„Die Präzision und Geschwindigkeit optischer Messtechniken macht sie so gut für die Automatisierung“, stimmte Andreas Blind, Vice President of Sales, Marketing and Services bei Jenoptik (Rochester Hills, MI) zu. Jenoptik bietet ein breites Spektrum an Messtechnik-Sensoren, hauptsächlich, aber nicht ausschließlich, für die In-Prozess-Kontrolle. Diese reichen von Luftmessgeräten und Kontaktmessgeräten bis hin zu fortschrittlichen optischen Hochgeschwindigkeitssensoren. „Jeder hat seinen Platz. Optische Techniken funktionieren in der Regel nicht gut in schmutzigen oder öligen Umgebungen, optische Techniken sind jedoch viel flexibler und besonders nützlich, wenn die Teile nicht berührt werden können oder wenn es auf Geschwindigkeit ankommt“, sagte er.
Die Opticline-Geräteserie von Jenoptik ist ein gutes Beispiel für eine Technik – ein Schattenbild – verpackt in einem automatisierten Hochgeschwindigkeitsschrank zum Messen von Wellen. Shadowgraph-Systeme sind ideal zum Messen von rotierenden Teilen, auch von nicht achsensymmetrischen, wie Nocken- und Kurbelwellen. Das Unternehmen stellt fest, dass weltweit über 2500 Opticline-Systeme in einer Vielzahl von Größen und Fähigkeiten zum Messen großer oder kleiner Teile installiert sind. Beispielsweise gibt es eine Reihe von Opticline-Stationen mit Schnittstellen zur statistischen Prozesskontrolle (SPC) für eine schnelle Überwachung unter Verwendung des SPC-Systems der Wahl für diese Fabrik. Die Genauigkeiten werden in MPe angegeben und betragen bis zu (1,5 +L/200) μm für die Messung von Durchmessern mit einer Messgeschwindigkeit von bis zu 80 mm/s.
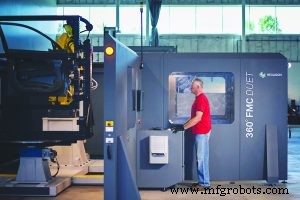
Eine weitere wichtige Funktion der optischen In-Prozess-Kontrolle ist laut Blind die Erkennung von Oberflächenfehlern. „Unsere Optisense-Technologie verwendet eine Kombination aus einzigartigen Sensoren, Beleuchtung, Automatisierung und Software, die uns hilft, selbst kleinste Defekte auf Oberflächen und Teilen zu erkennen“, sagte er. Die Erkennung von Oberflächenfehlern in den Bohrungen von Motorzylindern ist angesichts des heutigen Fokus auf Kraftstoffverbrauch und Emissionen besonders wichtig. Das Aufkommen plasmagespritzter Bohrungen, die dickere und schwerere Stahlhülsen in Aluminiumblöcken ersetzen, macht die Erkennung von Oberflächenfehlern besonders wichtig. „Unsere IPS-Line-Bore-Sensoren sind in verschiedenen Bohrungsgrößen von 4 bis 150 mm erhältlich, je nach Art des verwendeten Sensors“, sagte Blind. „Sie können Fehler bis zu einer Größe von 30 μm erkennen und sind normalerweise automatisiert, obwohl sie auch in halbautomatischen Versionen erhältlich sind“, sagte er. Er wies darauf hin, dass die Automatisierung für den Automobilsektor besonders wichtig ist. „Achtzig Prozent unserer Ausrüstung gehen derzeit in die Automobilindustrie“, sagte er.
Neue Sensoren, mehr Automatisierung
Eine weitere unangenehme Realität für Messtechnikanbieter ist, dass Qualitätsprüfungen oft als Kosten angesehen werden können, einfach als verlorene Zeit in der Produktion. Das sagt Stefan Scherer, Präsident und CEO von Alicona (Graz, Österreich). Er sagte, Metrologie könne einen Mehrwert schaffen. „Wenn wir zeigen können, dass sie ihren Fertigungsprozess mithilfe von Messtechnik anpassen können, um die Fertigung proaktiv zu verbessern und flexibler zu gestalten, wird das unserer Meinung nach einen großen Unterschied machen.“ Er glaubt insbesondere, dass die Ergebnisse aus der Metrologie in der wachsenden Smart Manufacturing- oder Industrie 4.0-Bewegung von entscheidender Bedeutung sind. „Wir müssen Maschinen ein intelligentes Auge geben“, erklärte er.
Alicona ist ein innovatives Unternehmen, das auf einem relativ neuen Messprinzip namens Focus Variation basiert. Diese Technik liefert hochauflösende Oberflächendaten mit begrenzter Schärfentiefe, ähnlich aber fortschrittlicher als konfokale Bildgebung oder optische Schnitte, da sie auch Farbdaten liefert. Es misst sowohl die Oberflächenform als auch die Rauheit und ist nach Angaben des Unternehmens besonders nützlich in Produktionsumgebungen. „Unsere Technologie ist nützlich, um kleine Merkmale mit hoher Präzision oder relativ kleine Merkmale zu messen, wie z. B. bei der Mikro- oder Präzisionsfertigung, wenn die Toleranzen im Bereich von 20 μm oder weniger liegen“, sagte Scherer. Um optimal zu funktionieren, erfordert Focus Variation eine Ra-Oberflächenrauhigkeit von 9 Nanometer oder mehr. Die Datengeschwindigkeit beträgt bis zu 1,7 Millionen Punkte pro Sekunde.
Nach ersten Erfolgen bei der Messung von Kantenvorbereitungen für Schneidwerkzeuge erweiterte das Unternehmen sein Angebot und automatisierte seine Sensoren.
Automatisierung ist entscheidend für Scherers Vision eines intelligenten Auges, und das Unternehmen wandte sich dabei an kollaborative Roboter oder Cobots. Warum Cobots? „Wir sehen eine Verschiebung hin zu höherer Präzision und gleichzeitig weniger Volumen. Früher fertigte ein Hersteller vielleicht eine Million Teile. Heute stellen sie vielleicht 50.000 Teile einer Art her und stellen dann auf die Produktion von 75.000 eines anderen um“, sagte er. Er glaubt, dass Cobots Arbeiter in diesen flexiblen Fertigungsumgebungen unterstützen, sie nützlich machen und einen Mehrwert schaffen. „Wir haben einen Cobot auf einer mobilen Plattform montiert, um ihn einfacher zu einem Bearbeitungszentrum zu bringen“, sagte er. Der Benutzer überprüft einige Schlüsselparameter, um die Maschine für die Herstellung des nächsten Teilenummernsatzes einzurichten, und fährt dann mit der nächsten Aufgabe fort.
Die neuesten Angebote von Alicona sind zwei neue Cobot-Produkte für definierte Anwendungen, eines für lange Rundwerkzeuge und das andere für Turbinenscheiben. Die Werkzeuglösung erweitert Aliconas Know-how in der Kantenvorbereitungsmessung um Neun-Achsen-Messungen auf einer tragbaren Plattform mit Rädern.
Bei der Alicona Disk-Lösung wird der Roboterarm mit angebrachtem Messsensor von einem Bediener an die gewünschte Oberflächenposition manipuliert. Am Sensor sind zwei Handgriffe mit integriertem Joystick montiert. Mittels einer App zeigt ein Smartphone die Live-Ansicht zur manuellen oder automatischen präzisen Positionierung und Messung an.
Standardlösungen, flexible Automatisierung
Ein weiterer allgemeiner Trend ist die Entwicklung einer Standard-Automatisierungslösung rund um vorhandene Messgeräte. Metrologieunternehmen bieten jetzt Standardlösungen an, die Roboter, Gehäuse und Vorrichtungen integrieren. Normalerweise zielen sie auf eine Klasse von Problemen ab, sie können jedoch auf die Durchsatz- und Toleranzanforderungen eines Herstellers zugeschnitten werden.
Im Jahr 2014 führte Hexagon Manufacturing Intelligence (North Kingston, RI) das 360 Smart Inline Measurement System oder 360 SIMS ein, das seine WLS-Geräte (Weißlichtscanner) mit strukturiertem Licht verwendet. Laut Hexagon ist ein um ein WLS herum aufgebautes Inline-System ideal für die Rohkarosserie-Produktion von Automobilen, da das WLS relativ unempfindlich gegenüber Vibrationen in der Nähe ist – es erfasst Daten in Millisekunden. Um es noch schneller zu machen, erfasst das 360 SIMS laut Amir Grinboim, Hexagon-Produktmanager, nur ausgewählte Merkmale wie Lücken und Bündigkeit oder Löcher.
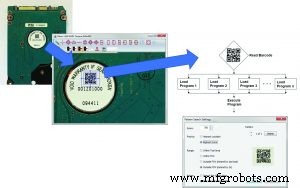
Hexagon hat dieses Inline-Angebot jetzt mit der 360 Flexible Measurement Cell oder 360 FMC erweitert, die erstmals im September 2016 eingeführt wurde. „Eine Standardlösung ist leistungsstark und kostengünstig, wenn es um Installation, Integration und Integration von Sicherheitsprotokollen geht “, sagte Grinboim. „Es reduziert die Gesamtkosten für Engineering und Design, wenn man das einmal macht.“ Die Sicherheitsprotokolle des 360 FMC erfüllen die Norm ANSI RIA 15.06-2012. Die Teile können bis zu 2,2 m lang und bis zu 1500 kg schwer sein.
Die grundlegende 360-FMC-Konfiguration ist ein Gehäuse, das mit einem einzelnen FANUC M-710iC/50-Roboter ausgestattet ist, der einen Hexagon WLS400A-Sensor montiert und vom CoreView-Softwarepaket gesteuert wird. Je nach gewählter Konfiguration misst es Teile, die an einem, zwei oder drei separaten Drehtellern befestigt sind. „Eine modulare, flexible Lösung wird es unseren Kunden ermöglichen, die Zelle nicht nur für die Messtechnik, sondern auch für den Durchsatz zu nutzen“, erklärte Grinboim. „Wir wollten, dass es sich während des gesamten Herstellungslebenszyklus an sich ändernde Bedingungen anpasst.“ Laut Grinboim können Kunden die Anzahl der Plattenspieler ohne großen Umbau oder Neuintegrationsaufwand hinzufügen oder reduzieren. „Das Hinzufügen – oder Entfernen – von Plattenspielern ist Plug-and-Play.“
Der 360 FMC benötigt keine Referenzziele auf dem Teil, da er sich auf die Roboterbewegung mit Kompensationsprogrammen verlässt. „Es misst mit einer Genauigkeit von 100–150 μm, basierend auf dem Merkmalstyp, was für typische Blechanwendungen in der Automobilindustrie geeignet ist“, sagte Grinboim.
Automatisierungssteuerung System
- Die Bedeutung des Stromkreisschutzes beim Design elektrischer Verteilungssysteme
- Warum die Zeit reif ist, zu proaktiven Operationen überzugehen
- Robotermesssystem automatisiert Messprozess
- 5 Ws der tragbaren Braillezeile
- Warum die US-Fertigungsindustrie eine Rezession erlebt
- Die 5 Werkzeuge, die Lean Manufacturing zum Erfolg führen
- WEF:Warum Cobots die Zukunft der Fertigung sind
- Das menschliche Element der Automatisierung
- Was ist das amerikanische Fertigungssystem?
- Die nächste Dimension von Hand-Auge-Anwendungen – Bewegung