Vorantreiben der digitalen Fabrik mit Echtzeit-MES-Daten
Mit dem Vorstoß in Richtung einer vollständig digitalen Fabrik war die Software für Manufacturing Execution Systems (MES) für Hersteller aller Art wichtiger denn je. Durch den Einsatz der neuesten reaktionsschnellen Manufacturing Execution System-Lösungen im Fertigungsbetrieb können Bauherren schnelle Updates zu zeitkritischen Betriebsdaten erhalten, die dazu beitragen können, Fabrikprozesse zu verbessern und die digitale Fabrik näher an die Realität heranzuführen.
Da die Konvergenz von Fertigungs- und Unternehmenssoftwaresystemen voranschreitet, erkennen immer mehr Hersteller die Vorteile, die eine digitale Fabrik bietet, da die Datenleistung in Echtzeit oder nahezu in Echtzeit viel mehr Einblick in die Fertigung bietet, als ihnen bisher zur Verfügung stand vorbei an. Hersteller nehmen die Implementierung der Infrastruktur, die für intelligente Fertigungslösungen und das industrielle Internet der Dinge (IIoT) erforderlich ist, immer ernster, und meistens bilden Cloud-basierte MES-Systeme den Kern dieser Technologien.
„Der Trend geht zur Konvergenz von Geschäftssystemen, um eine gründliche Analyse des Geräte- und Systembetriebs zu erhalten. Wir sehen, dass Datenanbieter ihre Kräfte bündeln“, sagte Pete Tecos, Executive Vice President, 5ME (Cincinnati), und verwies auf die jüngste Partnerschaft von 5ME mit SmartWare, die Freedom Smart Manufacturing-Lösungen und Bigfoot CMMS-Plattformen (Computerized Maintenance Management System) von Smartware vereint. „Je schneller wir Daten sammeln und zwischen verschiedenen Systemen austauschen, desto besser sehen wir den Gesamtbetrieb.“
Der Einfluss der Cloud
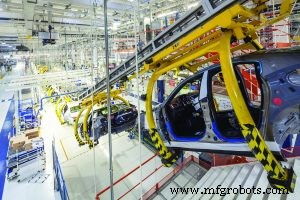
Da immer mehr Unternehmen Cloud-basierte Fertigungstechnologie einführen, verschmelzen die Fähigkeiten von MES-Lösungen, Enterprise Resource Management (ERP) und Betriebsdatenerfassungssystemen nahtloser und arbeiten zusammen, um die Bemühungen von IIoT und Industrie 4.0 in der Werkstatt effektiver zu machen Etage.
„Es ermöglicht das Streben nach dem ‚Heiligen Gral der Fertigung‘:umfassende Systemanalysen in Echtzeit durch Datenaustausch“, erklärte Tecos. „Anpassungen und/oder Korrekturen erfolgen schneller und mit weniger Unterbrechungen der Fertigungsabläufe.“
Heutige Softwarelösungen für die Fertigung bieten dem Fertigungsunternehmen eine Fülle von Tools zur Verfolgung wichtiger Fabrikmetriken, einschließlich der Gesamtanlageneffektivität (OEE) und vieler anderer, und diese angereicherten Systeme greifen gut ineinander, wenn Entwickler dieser Lösungen zusammenarbeiten, um die Anforderungen zu erfüllen des IoT/IIoT.
„Im Grunde beginnt man auf Werksebene mit Schnittstellen zu Anlagen und einer Vielzahl von Fertigungssystemen und stellt dann eine Visualisierungsebene [OEE-Cockpit] bereit, um Leistung und KPIs anzuzeigen“, sagte Tecos. „Zu guter Letzt schieben Sie Echtzeitinformationen nach oben in den Bereich der Geschäftssysteme [ERP, MES, CMMS, Qualitätssysteme]. Wenn all diese Systeme symbiotisch statt in Silos arbeiten, können Sie den Betrieb durch den Austausch von betrieblicher Echtzeit-Intelligenz in Richtung einer hocheffizienten adaptiven Fertigung lenken – das ist der Heilige Gral.“
Kompatibilität mit anderen Plattformen ist der Schlüssel, fügte Tecos hinzu. „Benutzerfreundlichkeit, Datenerfassungsfunktionen und Vielseitigkeit bei Maschinentypen sind ebenfalls wichtig. Unsere Software präsentiert Daten aus mehreren Perspektiven und ordnet sie drei Kategorien zu:Häufigkeit, Dauer und Monetarisierung. Wir untersuchen die Korrelationen zwischen diesen und nehmen im Wesentlichen die Häufigkeits- und Dauerdaten, um eine monetarisierte Ansicht
der Vorgänge zu erstellen.“
Die Ergebnisse einiger 5ME-Kunden sind beeindruckend. Nach der Installation der eLog-Systeme von 5ME halbierte das Werk des Schwermaschinenbauers Caterpillar in East Peoria, IL, die durchschnittliche Länge der Verzögerungen und verbesserte die In-Cycle-Zeiten der Maschinen um 30 % bei allen Maschinen, auf denen Freedom eLog installiert war, was 1,2 Millionen US-Dollar ausmachte Steigerung der Wertschöpfung. Das Unternehmen berichtete, dass es fand, dass die elektronischen „faktenbasierten“ Daten weitaus besser, genauer und weniger emotional waren als das Papiersystem/der manuelle Prozess, der zuvor verwendet wurde.
Unternehmensansicht einnehmen
MES-Systeme sind keine eigenständigen Systeme mehr, bemerkte Stephen Brown, Vice President, Manufacturing Practice, Americas, Siemens PLM Software (Plano, TX). „MES ist Teil einer vernetzten Unternehmens-IT-Infrastruktur. Der Wert von MES wird jetzt dadurch definiert, wie gut sich das MES-System in die gesamte Wertschöpfungskette integriert, sowohl vorgelagert zur Produktentwicklung und Produktionstechnik als auch nachgelagert zur Automatisierung“, sagte er.
„Kunden möchten die gesamte Wertschöpfungskette digitalisieren, vom Produktdesign über die Produktionsplanung, das Produktionsengineering, die Produktionsausführung bis hin zum Service. Wir nennen das das digitale Unternehmen“, sagte Brown. „Genauer gesagt verwenden wir den Begriff Digital Twin. Wir helfen unseren Kunden, einen digitalen Zwilling nicht nur des Produkts, sondern auch des Produktionsprozesses sowie der Anlagen und Produktionsanlagen zu erstellen. Unsere Kunden verwenden dann den digitalen Zwilling, um das Produkt und seinen Herstellungsprozess vollständig zu simulieren, bevor sie harte Dollars für Prototypen, Werkzeuge und Sachanlagen investieren.“
Diese Faktoren ermöglichen eine schnelle Innovation, bemerkte er. „Es geht nicht nur darum, Fertigungsabläufe zu verwalten. Es geht darum, einen flexiblen, reaktionsschnellen und vorhersehbaren Herstellungsprozess zu schaffen, der in der Lage ist, auf neue Produktanforderungen zu reagieren.“
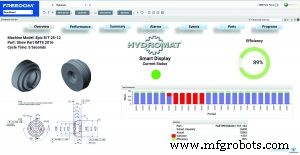
Einmal in der Produktion und wenn sie mit der Automatisierung verbunden sind, können die Kunden von Siemens Entscheidungen anhand von Echtzeitdaten aus der Fertigung treffen, sagte Brown. „Beispiele sind Maschinenverfügbarkeit oder Betriebszeit in Echtzeit, die von der Produktionsplanungssoftware zur Optimierung von Zeitplänen verwendet werden können, und Qualitätsprobleme, die während der Produktion erkannt werden und nahezu in Echtzeit an die Konstruktion für die Teiledisposition übermittelt werden können, was besonders wichtig ist Luft- und Raumfahrt“, sagte Brown. „Schließlich fügen Sie IoT und Datenanalysen mit Mindsphere hinzu, und wir schließen den Kreislauf im gesamten digitalen Unternehmen.“
Siemens verwaltet den Innovations- und Veränderungsprozess mit seinem Teamcenter PLM und erstellt einen digitalen Zwilling des Produkts und des Herstellungsprozesses, sagte Brown. „Wir integrieren uns dann in unser MOM-Portfolio [Manufacturing Operations Management], senden die erforderlichen Produkt-, Fertigungs- und Qualitätsdaten an die Werkstatt und verwenden dann Mindsphere für IoT und Big-Data-Analysen, um As-Built-Daten zu erfassen und Erkenntnisse in das Produkt einzuspeisen und Prozessdesign für kontinuierliche Verbesserung.“
Hochfahren für IIoT
Hersteller versuchen mehr, Big Data und den IoT/IIoT-Boom zusammen mit Cloud-Mobilität zu nutzen, sagte Eric Green, Vice President von Dassault Systèmes-Delmia. „Das betrifft heute alle Hersteller, aber bis es einen endgültigen Business Case gibt, befinden sie sich noch in der Sondierungsphase“, sagte er.
„Bei einigen der Technologien speziell rund um IIoT und IoT entdecken und verstehen sie immer noch, welche Möglichkeiten es gibt. Wenn Sie an das IIoT denken, machen die Hersteller seit vielen Jahren den Vorläufer“, bemerkte Green. „Das IIoT bietet eine neue Generation, eine neue Evolution. Aber wir haben Kunden, die Geräte haben, die über 20 Jahre alt sind, und diese neuen Technologien müssen in der Lage sein, vorhandene Geräteinvestitionen zu unterstützen.“
Entscheidend für die Hersteller wird es sein, herauszufinden, wo und wie sie Innovationen anwenden können, fügte er hinzu. „Als Verbraucher schafft jeder von uns ein Erlebnis, mit den Autos, die wir fahren, und den Smartphones und intelligenten Geräten, die wir haben. Das wirkt sich darauf aus, wie Unternehmen auf den Markt gehen. Es zwingt diese Hersteller, effizienter oder innovativer zu sein.“
Das Ziel von Entwicklern wie Dassault sei es, aufregende neue Produkte schnell und effizient auf den Markt zu bringen, bemerkte er. „Wenn Sie neue Produkte auf den Markt bringen wollen, vom Produktdesign über die Herstellung bis hin zum Verbraucher, erfordert die Innovationsplattform eine schnelle Zusammenarbeit, um das Design auf den Markt zu bringen.“ Dies gehe über ERP hinaus, fügte er hinzu, und sei eher eine Geschäftsinnovationsplattform. Anwendungen wie MOM, Manufacturing Operation Management, die das Produkt vom Design bis zur Fertigung durch einen kollaborativen, modellbasierten Ansatz führen, können die Bereitstellung von Produkteinführungen beschleunigen.
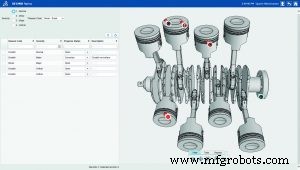
„Für uns als Organisation sehen wir das als eine Schlüsselpriorität an“, sagte Green. „MOM bietet ein breiteres Spektrum an Funktionen als MES – mit mehreren Standorten, einem breiteren Spektrum und Umfang sowie einer umfassenderen Bestandskontrolle. Was Sie sehen, ist, dass verschiedene Organisationen ihren Anwendungsbereich um MOM erweitert haben, und dies hängt mit der Innovation zusammen, die wir anbieten.“
Dem Benutzer nahezu Echtzeitfähigkeit zu geben, ist ein entscheidender Vorteil. „Der Wert besteht darin, dass wir globale Sichtbarkeit haben, wenn es Änderungen gibt, können diese Änderungen weitergegeben und Fehler beseitigt werden.“
Die Delmia-Apriso-Software ermöglicht digitale Kontinuität, vom Engineering bis zu allen Aspekten der Fertigung, sagte Green. „Es ist die Fähigkeit, eine virtuelle Welt zu nutzen, um verschiedene Szenarien zu optimieren, wie zum Beispiel den Modellmix“, sagte er. „Durch die Kombination des realen Ausführungsmodells und der Daten mit der virtuellen Welt des Engineerings verwenden wir Simulation oder Optimierung, um die Auswirkungen von Änderungen auf der Grundlage realer Fabrikdaten zu bewerten, bevor wir Änderungen in der Fabrik implementieren. Die Delmia Apriso-Software hilft Benutzern, Transparenz und Kontrolle über globale Vorgänge bereitzustellen, um die Ausführung über Produktion, Bestände und Qualität hinweg zu optimieren.“
Das MOM-Portfolio von Siemens umfasst MES, Quality, Advanced Scheduling und Manufacturing Intelligence. „Mit diesen Anwendungen sind Lösungen für die Konstruktion und Simulation von Fertigungsanlagen, unser Tecnomatix-Portfolio und dann natürlich IoT und Datenanalyse mit Mindsphere verbunden“, fügte Brown hinzu. „Wir nehmen die technische Stückliste und wandeln sie in die Fertigungsstückliste und dann in eine Prozessliste um. Hier übernimmt MES.
„Wir erstellen Arbeitsanweisungen für jeden Schritt, einschließlich Qualitäts- und Inspektionsschritte, und können diese Anweisungen dann an den Bediener senden, wenn ihm ein bestimmtes Teil an der Arbeitsstation präsentiert wird“, sagte Brown. Oder wir können einen spezifischen Code an eine Roboter-Arbeitszelle senden, basierend auf dem Teil, das dieser Arbeitszelle präsentiert wird. In der Welt der kundenindividuellen Massenproduktion, in der Losgrößen gegen eins gehen, sind wir in der Lage, Durchlaufzeiten und Kosten zu erreichen, die in der Vergangenheit nur mit harter Automatisierung und sehr großen Auflagen erreicht wurden.“
Siemens hat außerdem eine neue Automation Gateway-App für Simatic IT MES UAF 2.1 hinzugefügt, die OPC-Konnektivität und direkte Konnektivität zu Siemens S7-Steuerungen bietet, sagte Brown. Die App konfiguriert Automatisierungsknotenobjekte, die aus Eigenschaften bestehen, die mit Automatisierungssystem-Tags verbunden sind. „Automation Gateway umfasst einen Dienst, der die Verbindung mit Automatisierungssystemen aufrechterhält und Automatisierungsdaten synchronisiert“, sagte er. „Automatisierungsdaten werden dem UA-App-Befehl zum Lesen und Schreiben ausgesetzt, und die App kann über die Signalverwaltung Automatisierungsdaten-Änderungsereignisse abonnieren.“
Mehr maschinelle Analysen
Da die Nachfrage nach Analytik wächst, gibt es immer mehr Auswahlmöglichkeiten, wie die neuen Maschinenanalyselösungen, die Rockwell Automation (Milwaukee) letzten Herbst auf seiner Rockwell Automation Fair angekündigt hat. Zu diesen Systemen gehörten Rockwells FactoryTalk Analytics for Devices und eine cloudbasierte FactoryTalk for Machines-Anwendung für Gerätehersteller sowie System- und Unternehmensanalysen.
Analytik ergänzt MES- und ERP-Systeme und hilft Herstellern, die wachsenden Datenströme von Sensoren zu nutzen, die über das IIoT verbunden sind. „Die Leute sprechen weiterhin über Industrie 4.0 und Smart Manufacturing“, sagte Todd Montpas, Business Manager, Information Software, Rockwell Automation. „Was sie wirklich interessiert, ist, ob die Technologie Erweiterungen der Maschinenleistung bietet, und was sie wirklich verlangen, sind all diese Fähigkeiten auf der Ausführungsebene – wir müssen sicherstellen, dass sie Prozesse haben, die funktionieren.“
Viele Kunden seien an Cloud-basierten Systemen interessiert, fügte er hinzu und stellte fest, dass einige Großkunden Interesse an Microsofts Azure-Cloud zeigten. „Was wir versuchen, ist ein sehr skalierbarer Ansatz mit einer skalierbaren Ausführung, der jedoch in eine skalierbare Analysestrategie integriert ist. Durch das Anbringen eines Sensors können Sie Echtzeitanalysen auf Maschinenebene und maschinelles Lernen zur Vorhersage von Fehlern erhalten.“
Auf der Hannover Messe stellte GE Digital (Boston) im April seine neue Plant Applications MES-Lösung vor, die darauf abzielt, sein Angebot für hybride Fertigungsindustrien für hochautomatisierte Produktionsprozesse zu erweitern. Diese neue Version bietet Kunden eine neue Benutzeroberfläche, die das fortschrittliche UX-Design von GE verwendet, um es dem Betriebspersonal besser zu ermöglichen, die Geräteeffektivität zu analysieren und die Ursachen von Ausfallzeiten zu identifizieren.
„Eines der interessanten Dinge, die ich heute sehe, ist, dass viele Kunden versuchen, sich auf das industrielle IoT vorzubereiten“, sagte Matthew Wells, Vice President, Digital Product Management, GE Digital. „Es entwickelt sich, aber es etabliert sich ein Konzept einer Hybrid Cloud. Es ist MES mit einem großen E [Betonung der Ausführung]; Sie wollen das vor Ort am Laufen halten. Was das Industrial IoT und die Cloud bieten, ist eine Möglichkeit, dies zu ergänzen.“
Reaktionszeiten und die Notwendigkeit einer Zuverlässigkeit von über 99 % für den Fertigungsbetrieb haben Hersteller davon abgehalten, in Scharen in die Cloud zu strömen, bemerkte Wells. „Reicht 99 % Zuverlässigkeit aus? Viele Kunden werden dieses Risiko für ihre Produktionsanlagen nicht akzeptieren“, sagte er. „Was die Cloud wirklich bietet, ist eine Möglichkeit, tiefer in die Daten einzutauchen. In der Cloud können Sie den Verlauf speichern und maschinelles Lernen durchführen. Wenn Sie über die Cloud verfügen, können Sie auf große Datenmengen zugreifen und die Effektivität Ihrer Analysen steigern.“
Der jederzeitige Zugriff auf mehrere Terabyte an Daten in der Cloud ermöglicht es Herstellern, den digitalen Zwilling voll auszuschöpfen, fügte Wells hinzu, der die Hauptattraktion des IIoT ist. „Der Digital Twin ist eine Reihe von Analysen, die im Grunde das Verhalten von Maschinen modellieren, die ständig im Hintergrund laufen und die Daten optimieren“, sagte Wells. „Hier beginnt wirklich der Wert des Industrial IoT. Es ist ein aufstrebender Markt, der schnell wächst.“
Automatisierungssteuerung System
- Die digitale Fabrik:Smart Manufacturing treibt Industrie 4.0 voran
- Die Bedeutung von IIoT in einer Smart Factory
- 5 Minuten mit PwC zu KI und Big Data in der Fertigung
- Engpässe überwinden:Die Macht der Analytik in der Fertigung
- Censornet:Sicherung der Zukunft der Fertigungsindustrie
- GE Digital:Transformation der Fertigung mit Smart MES
- Bewältigung der Fertigungsherausforderung mit Daten und KI
- GE Digital:Operational Insights with Data &Analytics
- Der Aufstieg digitaler Plattformen in der Fertigung
- Starthilfe für die digitale Transformation in der Fertigung