Lösung des Rätsels der Datenanalyse in der Fertigung
Neue Tools zur Datenerfassung und -analyse in der Fertigung können die Belastung durch die Digitalisierung des Fabrikbetriebs im IoT-Zeitalter verringern
Da der Übergang zu einer stärker vernetzten Fertigungsindustrie an Dynamik gewinnt und Hersteller damit beginnen, Fabrikdaten zu sammeln, wird die Notwendigkeit einer schnellen und effizienten Datenanalyse immer wichtiger. Datenerfassungs- und Analysetools sind im Zeitalter der digitalen Fertigung/Industrie 4.0 von größter Bedeutung, und Hersteller rüsten sich mit neuen Lösungen, die ihnen dabei helfen, Fabrikdaten effektiver zu erfassen, zu verwalten und zu analysieren, indem sie Key Performance Indicators (KPI) wie z Gesamtanlageneffektivität (OEE), Maschinenbetriebszeit, Maschinen-/Spindelauslastung und andere Metriken.
Es stehen viele Fertigungsdatenerfassungs- und Maschinenüberwachungsoptionen zur Verfügung, von denen die meisten zumindest einige grundlegende Analysen von Fertigungsmetriken in Paketen zur Betriebsüberwachung oder in MES-Systemen (Manufacturing Execution Software) anbieten. In einigen Fällen arbeiten Automatisierungsunternehmen mit etablierten IT-Anbietern zusammen, wie die kürzlich angekündigte Partnerschaft des Automatisierungsanbieters ABB Inc. (Cary, NC, und Zürich) und Hewlett Packard Enterprise Co. (HPE; Palo Alto, CA). Kombinieren Sie das Know-how von ABB in den Bereichen Industrieautomation und Betriebstechnologie (OT) mit der Erfahrung und dem Softwareportfolio von HPE im Bereich Hybrid-IT.
Zusammenarbeit von OT mit IT
In der im November 2017 angekündigten Partnerschaft zwischen ABB und HPE wird das digitale Angebot Ability von ABB mit den hybriden IT-Lösungen von HPE kombiniert. Ability-Lösungen werden auf hybriden Plattformen wie HPE ProLiant für Microsoft Azure Stack ausgeführt, mit Bereitstellungen an den bevorzugten Standorten der Kunden in Industrieanlagen und Rechenzentren oder in der Microsoft Public Cloud, je nach Bedarf, um die Anforderungen an Leistung, Sicherheit oder standortübergreifend zu erfüllen Zusammenarbeit.
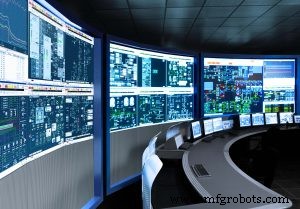
Die Partnerschaft verschiebt Rechenressourcen mithilfe von „Edge Computing“ näher an den Ort, an dem sie benötigt werden. ABB und HP werden die Rechenzentrumsautomatisierung von Ability, die die Infrastruktur steuert und überwacht, mit OneView, der IT-Infrastrukturautomatisierungssoftware von HPE, integrieren. „Ehrlich gesagt können wir das nicht alleine schaffen; wir brauchen einen Partner für diesen Hybrid, und OT/IT wird benötigt“, sagte der in Dublin ansässige Ciaran Flanagan, Group Vice President und Head of Global Datacenter Solutions bei ABB. Durch die Kombination von IT und OT, die heute weitgehend isoliert sind, „glauben wir, dass es enorme Chancen gibt und sich schnell entwickelt“, fügte er hinzu.
Die ABB/HPE-Partnerschaft bietet Benutzern sichere Edge-Rechenzentren für abgelegene Industrieumgebungen und nutzt auch die Rack-Infrastruktur von Rittal mit den industriellen Stromverteilungssystemen von ABB und der softwaredefinierten Infrastruktur und den Services von HPE. „Die Protokollebene ist in der OT ganz anders als in der IT“, bemerkte Volkhard Bregulla, HPE Vice President, Global Manufacturing Industries. „Die IT-Seite ist ganz vorne.“ Die ABB-HPE-Lösung wird im ersten Halbjahr 2018 verfügbar sein.
Ladendaten sammeln und dann analysieren
In der Werkstatt gibt es viele Möglichkeiten zur Überwachung und Erfassung von Daten, die meisten bieten zumindest grundlegende Maschinenanalysen und einige anspruchsvolle Analysen der Werkstatt.
Bei der Überwachung von Maschinen müssen Shop-Manager zunächst wissen, wann bestimmte Maschinen laufen, ob sie ausgefallen oder offline sind. Laut David McPhail, President und CEO, Memex Inc. (Burlington, ON), ist es wichtig zu wissen, wann die Maschine unter Programmsteuerung steht. "Wir sind agnostisch, wenn es darum geht, wie Sie sich verbinden", sagte er.
Mit der Tempus-Plattform MERLIN (Manufacturing Execution Real-Time Lean Information Network) von Memex können Prozess- und diskrete Hersteller ihre Maschinen entweder in lokalen oder Cloud-Umgebungen verbinden. MERLIN Tempus ist eine MES-Software, die Dashboards enthält und sich mit FANUC FOCAS, MTConnect, OPC und anderen Protokollen verbinden kann, um Werkzeugmaschinen über das Internet zu verbinden.
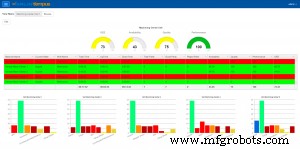
Für ältere, nicht intelligente Geräte hat Memex eine MTConnect-Schnittstelle entwickelt. „Es gibt 16 digitale Eingangssignale von der Maschine“, sagte McPhail. „Es gibt drei Datenströme:von der Ausrüstung; vom Humankapital, etwas, worüber ein Mensch die Kontrolle hat [und] das uns eine Maschine nicht sagen kann; und von externen Lösungen wie ERP.“
Benutzer können das Tempus MES, das ein Manufacturing Operations Management (MOM)-Portfolio ist, in der Werkstatt ausführen, um den Maschinenstatus zu überprüfen, sagte McPhail. „Normalerweise führen unsere Mitarbeiter unsere Software auf einem Tablet aus und laufen in der Werkstatt herum. Nehmen wir an, ein Bediener hat Probleme mit einem Teil; Sie erhalten eine Nachricht:„Unterstützen Sie den internen Kunden.“ Dadurch wechselt der Operator von einem reaktiven in einen aktiven Modus.
„Es gibt keine benutzerdefinierte Programmierung“, fuhr McPhail fort, und das System enthält Analysetools. „Das Stück Datensammlung ist grundlegend. Der von uns gewählte Business Case ist OEE, aber Sie könnten TPM [Total Predictive Maintenance] und viele andere einfügen. Es berechnet im Wesentlichen die finanziellen Auswirkungen einer schlechten Leistung.“
Memex entwickelt ein FOEE (Financial OEE)-Modul, das später in diesem Jahr veröffentlicht werden soll und das den Geschäften die Kosten für den Betrieb von Geräten mit nicht optimalen Einstellungen berechnen wird. Das Modul zeigt Shop-Managern, „dass Sie derzeit mit weniger als der Spitzenleistung laufen, um ein Delta von so viel, und jede Stunde, die Sie [auf diesem Niveau] laufen, kostet Sie so viel“, sagte McPhail.
Überwachung ein Muss, aber Analyselähmung vermeiden
Eine große Frage für Geschäfte, die Datenüberwachung/-analyse einrichten, ist, wie viele Daten gesammelt werden sollen. Während die Branche die Notwendigkeit von „Big Data“-Analysen hochjubelt, ist für den durchschnittlichen Shop weniger möglicherweise mehr.
„Wir arbeiten mit unseren Kunden zusammen, um die Gleichung zu verstehen. Das Wie ist eine bekannte Entität. Das Warum, der Business Case, der es untermauert“, ist das, woran Memex arbeitet, sagte McPhail.
Während einige Unternehmen an massiven Big Data-Problemen mit Simulationsumgebungen wie CAE-Daten arbeiten, ist dies in den meisten Geschäften nicht der Fall. „Big Data nennen wir das digitale Abgase“, fügte McPhail hinzu. „Wenn Sie eine Mazak-Maschine nehmen und jedes Tag abonnieren, wird Sie diese [Datenmenge] überwältigen. Müssen Sie wirklich jeden Datenpunkt kennen?“
Ein anderer Entwickler, Predator Software (Portland, OR), zielt mit seiner Predator-Suite von Anwendungen zur Betriebsüberwachung auf alles ab, von Zwei-Mann-Werkstätten bis hin zu großen Fertigungsunternehmen, so Mike Rogers, Predator Software Director, Automation and OEM Relations. „Predator MDC [Maschinendatenerfassung] ist unser Kernprodukt für die Überwachung, und mit über 20 verschiedenen Protokollen, von Mori, OPC und OPC/UA, können wir alles in der Fertigung überwachen“, sagte Rogers.
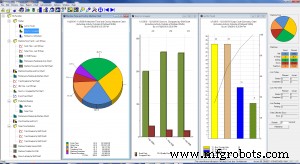
Das Sammeln und Analysieren von Daten wird heute von den Geschäften eher akzeptiert. „Das wird das heißeste Thema“, sagte Rogers. „Jeder will es und nicht jeder hat es. … Große Konzerne wollen Big Data. Der kleine Kerl [muss] laufen lernen, bevor er rennt. Sie werden sonst überwältigt.“
Ein Schlüssel ist, Kunden davon zu überzeugen, sich auf einfache Dinge zu konzentrieren, wie er bemerkte, wie „wird die Maschine laufen? Sitzt es? Läuft es? … Es kann ein überwältigender Prozess sein “, sagte Rogers. "Eines der Probleme, auf die ich stoße, ist, den Champion in der Organisation zu finden, der es durchführt."
Die MDC-Lösung von Predator verfügt über eine intuitive Benutzeroberfläche, die den Benutzern den Einstieg erleichtert, sagte Rogers. „MDC hat [eine eingebaute] Charting- und Reporting-Engine. Wenn Sie die Permutationen ausführen, haben wir zwischen 20.000 und 30.000 Berichte.“ MDC ist eines der acht Kernprodukte von Predator, das auf die Erfassung und Überwachung, Steuerung und Kommunikation von Betriebsdaten abzielt. Die Produkte arbeiten alle auf einer Datenbank, und wenn Kunden MDC kaufen, erhalten sie auch das DNC-Kommunikationsmodul. Die Software von Predator unterstützt Microsofts Access-Datenbank, die von vielen kleineren Geschäften verwendet wird, sagte Rogers, und sie unterstützt auch Microsoft SQL Express, SQL Server und Oracle-Datenbanken. Die Predator-Software kann entweder vor Ort oder in der Cloud betrieben werden.
Befolgen Sie die OEE
Sowohl kleine als auch große Betriebe müssen der OEE-Metrik große Aufmerksamkeit schenken, die es Maschinenbedienern und -managern ermöglichen kann, die Effizienz zu optimieren. Es ist von entscheidender Bedeutung, den Prozess zu visualisieren, um es dem Verkaufspersonal zu erleichtern, sich ändernde Bedingungen schnell zu erkennen, zu verstehen und darauf zu reagieren.
„Wir bieten sowohl die Datenerfassung als auch die Datenanalyse an, und wir können dies entweder à la carte oder als Komplettlösung anbieten“, sagte Jeff Price, Executive Vice President und General Manager, 5ME LLC (Cincinnati). Mit der Freedom-Suite von 5ME erhalten Benutzer Software plus verfügbare Hardware, um eine Vielzahl von Maschinen zu verbinden und zu steuern.
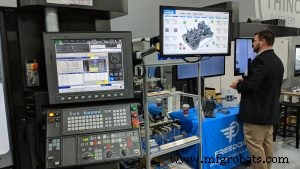
„Unser Team hat eine lange Geschichte mit OT-Geräten, und wir haben Schnittstellen oder Adapter zu fast jedem Asset in der Anlage, oft auf der CNC-Steuerung“, fügte Price hinzu. „Wenn wir Legacy-Controller haben, haben wir auch eine Hardware-Appliance“, um eine Verbindung zum Netzwerk herzustellen. Zusammen mit der Freedom eLog-Software bietet 5ME Datenvisualisierung mit anpassbaren Smartboards, die auf Flachbildfernsehern angezeigt werden, sagte Price.
„Mit der Smartboard-Technologie haben wir Dashlets oder Assistenten – eine Sammlung von Daten mit Torten- und Balkendiagrammen – die Sie in Smartboards speichern können“, sagte er. Die Smartboards verwenden eingebettete Raspberry Pi-Systeme, um die Verarbeitungsgeschwindigkeit dort zu erhöhen, wo die Daten am dringendsten benötigt werden. „Wir verwenden Raspberry Pi mit Smartboards, um die Visualisierung in die Werkstatt zu bringen“, sagte Price. „Jahrelang hatten wir in Automobilwerken Andon-Platinen, aber die sind ziemlich starr.“
Auf Freedom-Servern, die sich in der Cloud oder vor Ort befinden, findet die Datenverarbeitung statt. Mit der angebotenen Konnektivität können Kunden auf Errungenschaften aufbauen, die die Branche bereits erzielt hat, so Price, wie z. B. Lean Manufacturing und Six Sigma. „Wir schließen diesen ganzen Prozess kurz“, fügte er hinzu. „Die meisten unserer Kunden werden mit OEE, das sich aus Verfügbarkeit, Leistung und Qualität zusammensetzt, eine Produktivitätssteigerung von mindestens 20 % feststellen. Verfügbarkeit ist, ob Sie [auf optimalem Niveau] laufen, Leistung ist, ob Sie auf dem Niveau produzieren, das Sie sein sollten, und Qualität ist eine reine Ertragssituation.“
Allein mit der OEE-Metrik können Geschäfte große Leistungssteigerungen erzielen, sagte er. „Verfügbarkeit ist der große Gewinn. Die anfänglichen Verbesserungen betragen 10–20 % in 30 Tagen.“ Die Freedom Suite ist eine Softwareinstallation über das Internet. „Es ist ein geringer IT-Fußabdruck, der die Leistungsfähigkeit der Verarbeitung auf Controllern nutzt. Wir können 100 Maschinen in vier Wochen bauen.“
Der Preis fügte hinzu, dass die Geschäfte die Daten auf das Wichtigste herunterfiltern müssen. „Das hängt von den Analysetools ab; wir nennen es Tropf – reich an Daten, arm an Informationen“, sagte er. „Wenn Ihre Systeme die richtigen Metriken präsentieren, gibt es eine Menge Verbesserungen zu erzielen.“
Den ersten Datenschritt machen
Nicht alle Geschäfte, insbesondere kleinere ohne große OT/IT-Budgets, sind leicht vom Wert der Betriebsdatenüberwachung zu überzeugen. „Die Leute versuchen, ihre Grundlinie zu verstehen“, sagte Price. „Die Dinge wie wie oft laufen Ihre Geräte? Es gibt immer noch eine Lücke – unsere Rolle besteht darin, diese Lücke zu schließen. Sie verstehen es nicht.“ 5ME-Kunden wie Textron, Bell Helicopter, Caterpillar, Schlumberger und Cummins interessieren sich für Big Data, aber sie haben nicht alle einen Anwendungsfall dafür, sagte Price, obwohl er einen solchen Nutzen in der vorausschauenden Wartung sieht.
„Die Datenerfassung und -analyse ist für jeden modernen Hersteller unerlässlich – von kleinen Geschäften bis hin zu Großunternehmen“, sagte Jody Romanowski, CEO von Cimco Americas Inc. (Streamwood, IL). „Genaue Echtzeitdaten helfen dabei, Bereiche zu identifizieren, die verbessert werden können, egal ob es sich um Ausrüstung, Prozesse oder Personal handelt. Diese Daten sind erforderlich, um signifikante Verbesserungen zu erzielen.“ Das Werkstattangebot von Cimco, MDC-Max, ist eine Datenerfassungslösung, die eine strukturierte und automatisierte Produktionsüberwachung ermöglicht. Vom skalierbaren MDC-Max können sowohl kleine Geschäfte als auch große Hersteller profitieren, sagte Romanowski.
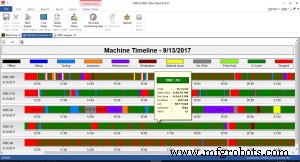
„Wenn Kunden eine Echtzeit-Datenanalyse in Betracht ziehen, sind sie oft etwas überfordert mit einer ganzen Reihe von Datenpunkten. Unser Ansatz besteht darin, das Projekt zunächst einfach zu halten und drei bis fünf Datenpunkte zu analysieren, um einen frühen Erfolg zu sichern“, sagte sie. „Hersteller können dann nach und nach mit der Analyse weiterer Datenpunkte beginnen. Im OEE-Kontext kämpfen alle Hersteller mit einer vollständigen und konsistenten Analyse des Qualitätsparameters.
„Wir empfehlen keinen Big-Data-Ansatz zur Erfassung von Maschinendaten“, so Romanowski weiter. „Wir raten, es einfach zu halten und zunächst die tief hängenden Früchte zu ernten und dann auf Erfahrungen und den gemeisterten Herausforderungen aufzubauen. Wenn Unternehmen, die weltweit Shopfloors betreiben, danach streben, global einen konsistenten Überblick zu bekommen, auch über Geschäftsbereiche hinweg, wird die Projektkomplexität dramatisch zunehmen, wenn auch nicht unbedingt aus Big-Data-Perspektive. Stattdessen wächst die Komplexität normalerweise durch den Umgang mit älteren Maschinen/Systemen und unterschiedlichen Verfahren und/oder Kulturen. Das legt einen weiteren Schwerpunkt darauf, die ersten Phasen so betriebsbereit und einfach wie möglich zu halten und sich gleichzeitig auf taktische Ziele wie die ERP-Integration in weiteren Phasen des Projekts zu konzentrieren.“
Für Shops, die die Daten sammeln, aber nicht ausreichend analysieren, können neue Analysetools einen Vorteil bieten. „Oft ist ihre aktuelle Software zu begrenzt, starr oder kompliziert“, sagte Romanowski. „MDC-Max ist flexibel genug, um die zukünftigen Anforderungen unserer Kunden zu skalieren und zu erfüllen. Die Daten müssen auf jedem Gerät leicht zugänglich sein und sinnvoll aggregiert werden – beispielsweise in Berichten und Echtzeit-Dashboards.“
Bei einem Cimco-Kunden außerhalb von Tianjin, China, sagte Romanowski, der Hersteller habe eine Schlüsselmaschine, die einen Produktivitätsengpass darstellte und andere Maschinen beeinträchtigte. „Nachdem der Hersteller ein einfaches MDC-Max-System mit einer begrenzten Anzahl von Datenpunkten in Betrieb genommen hatte, verzeichnete er eine um 30 % höhere Auslastungsrate auf dieser bestimmten Maschine“, bemerkte sie, „wodurch die Produktivität sowohl durch die Reduzierung dieses spezifischen Engpasses als auch durch die Steigerung gesteigert wurde Produktivität auch auf allen anderen Maschinen. Die geschätzte Amortisationszeit für die Investition betrug in diesem Fall weniger als vier Monate.“
Automatisierungssteuerung System
- Der nächste Schritt in der Industrie 4.0:regelbasierte Analyse von Produktionsdaten
- Die vierte industrielle Revolution
- Datenkonform im IoT bleiben
- Was mache ich mit den Daten?!
- Wartung in der digitalen Welt
- Demokratisierung des IoT
- Maximierung des Wertes von IoT-Daten
- Der Wert der analogen Messung
- Tableau, die Daten hinter den Informationen
- Die Zukunft der Rechenzentren