Roboterunternehmen erstellt Industrie 4.0-freundliche Software
FANUC hat mit seiner IoT-Lösung „Zero Down Time“ eines der Versprechen von Industrie 4.0 wahr werden lassen, nämlich die vorausschauende Wartung von Fabrikanlagen. ZDT kann auf jeden Roboterarm von FANUC und seine Peripheriegeräte angewendet werden.
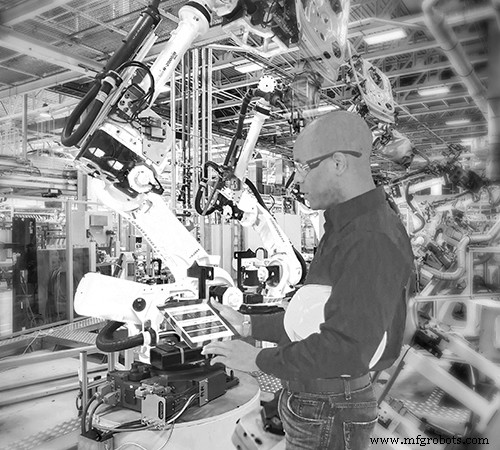
Um den Rest der Automatisierung in einer Fabrik zu unterstützen, wird das Robotikunternehmen später in diesem Jahr das Intelligent Edge Link and Drive (FIELD)-System von FANUC zur Verfügung stellen, eine kostenlose Open-Source-Plattform für Drittentwickler, die diese zum Schreiben von Anwendungen verwenden können sammelt und analysiert Daten von anderen automatisierten Geräten.
Intelligente Fertigung setzte sich mit Joe Gazzarato, Engineering Director von ZDT bei FANUC America, zusammen, um mehr zu erfahren.
Joe, worum geht es bei ZDT?
„ZDT“ steht für „Zero Down Time“. Da die Hersteller jetzt rund um die Uhr arbeiten und versuchen, die Nachfrage zu befriedigen, kann jede unerwartete Ausfallzeit sie die Produktion kosten. Mit ZDT überwachen wir den mechanischen, System- und Prozesszustand unserer Roboter, um unerwartete Ausfallzeiten zu vermeiden.
Wir haben über 21.000 Roboter an mehr als 100 Kundenstandorten in 16 verschiedenen Ländern mit ZDT verbunden.
Wir überwachen diese Roboter und wenn unsere Analysen ein Problem vorhersagen, benachrichtigt unser ZDT-System den Kunden und unser Serviceteam, damit wir das Problem beheben können, bevor es zu unerwarteten Ausfallzeiten kommt. Wir haben Kunden bereits mehr als 85 Millionen US-Dollar eingespart, indem wir Probleme identifiziert haben, von denen wir glauben, dass sie zu unerwarteten Ausfallzeiten geführt hätten.
Wie haben Sie das erreicht?
Wir arbeiten jetzt seit etwas mehr als vier Jahren an ZDT. Wir haben mit nur 500 Robotern angefangen, mit 50 Robotern an jedem der 10 Standorte.
Wir haben Software für unsere Roboter entwickelt, die Nachrichten mit wichtigen Daten produziert. Diese Roboter senden ihre Nachrichten an einen Datensammler in der Fabrik des Kunden. Die ZDT-Daten
Die Aufgabe von Collector besteht darin, die Nachrichten zu verschlüsseln und an unser Rechenzentrum in der Cloud zu senden, wo sie gespeichert und mithilfe von Programmen, die von unseren Ingenieuren geschrieben wurden, automatisch analysiert werden.
Wenn eine der Analysen feststellt, dass ein Problem vorliegt, werden E-Mails an den Kunden und unser Serviceteam gesendet, und einer unserer Servicetechniker ruft den Kunden an, um sicherzustellen, dass er versteht, was die Warnung bedeutet, wie sie bestätigt und wie sie behoben werden kann. Wenn der Kunde Hilfe benötigt, kann der Techniker auch veranlassen, dass Teile oder Support an den Standort gesendet werden, damit wir das Problem beheben können, bevor es zu Ausfallzeiten kommt.
Welche spezifischen Technologien machen ZDT möglich?
Der ZDT Data Collector hat sehr geringe Bandbreitenanforderungen. Einige andere Implementierungen rund um Big Data streamen Daten ständig mit einer Rate von Millisekunden. ZDT ist nicht so konzipiert. Wir sammeln in einem Jahr weniger als 500 Megabyte an Daten von dem Roboter. Der Datensammler kann auch auf einem kleinen Computer laufen. Es erfordert nicht viel Rechenleistung.
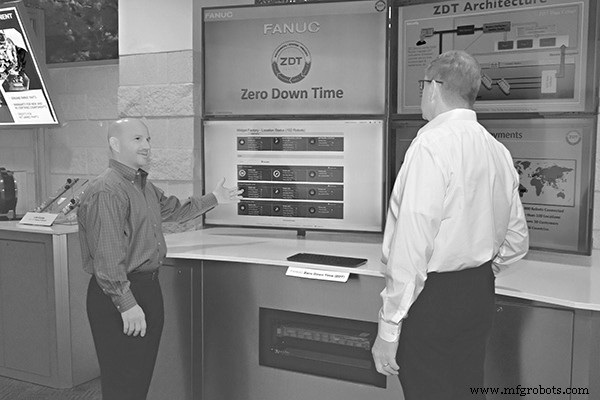
Ein weiterer Schlüssel ist unsere Cloud-Infrastruktur. Die Tools, die wir verwenden, um die Daten für die Analyse aufzunehmen und zu speichern, sind wirklich wichtig. Wir stellen sicher, dass die Daten so organisiert sind, dass sie bei der Speicherung sicher und effizient für die Verwendung durch unsere Analyseprogramme bleiben.
Unsere Analytik ist wahrscheinlich einer der wichtigsten Bestandteile von ZDT und der Schlüssel zu unserem bisherigen Erfolg. Sie werden von denselben Ingenieuren geschrieben, die unsere Robotersteuerungssoftware entwickeln. FANUC-Ingenieure mit jahrelanger Robotererfahrung haben die Analyseprogramme geschrieben, die sich mit den von uns gesammelten Daten befassen. Ihre Expertise beim Schreiben von Robotersoftware hat ihnen geholfen, sehr gut darin zu werden, Analysen aus den von unseren Robotern erzeugten Daten zu schreiben.
Gibt es andere Verwendungen für die Daten, die Sie im ZDT-Prozess sammeln?
ZDT macht auch viele andere Dinge. Wir haben viele Funktionen entwickelt, um Kunden dabei zu helfen, ihre Produktivität zu steigern, ihre Wartungsressourcen zu optimieren, ihren Supportaufwand zu reduzieren und die Lebensdauer ihrer Roboter zu verlängern.
Ein gutes Beispiel ist unsere Prozessänderungsanalyse. Eine häufige Erfahrung für viele von uns, die mit Automatisierungsgeräten gearbeitet haben, ist es, auf der Baustelle aufzutauchen und festzustellen, dass Ihr System nicht richtig arbeitet oder etwas anders macht als am Tag zuvor. Und man fragt herum und bekommt die gleiche Antwort. „Ich habe es nicht angerührt“ oder „Niemand hat etwas geändert.“ Ohne ZDT müssen die Menschen dann ihre eigene Analyse durchführen, um herauszufinden, was sich geändert hat.
Mit ZDT wissen unsere Kunden genau, ob einer ihrer Roboter geändert wurde, da wir jeden Tag alle Arten von Daten von den Robotern protokollieren. Wenn ein Roboter geändert wird, weiß er genau, welches Programm oder welche Einstellung geändert wurde, zusammen mit Datum und Uhrzeit, sodass er wahrscheinlich feststellen kann, wer die Änderung vorgenommen hat, und er kennt auch den ursprünglichen Wert. All dies macht es dem Kunden wirklich einfach, Dinge sehr schnell zurückzugeben.
Sind meine Daten sicher?
Der ZDT-Datensammler, der von der Firewall des Kunden blockiert werden kann, verschlüsselt die Daten, wenn sie an unser Rechenzentrum gesendet werden, und ist nur ein ausgehender Dienst.
Stellen Sie sich ZDT auch als schreibgeschützt vor. Wir können nur Informationen sehen, die von den Robotern gesammelt wurden. Wir können nichts ändern.
Wenn FANUC sagt, dass ZDT-Benutzer im gesamten Unternehmen auf Diagnoseinformationen zugreifen können, bezieht sich das auf Roboter und nicht auf andere Geräte in der Fabrik?
Typischerweise, aber wir haben ZDT tatsächlich so konzipiert, dass Kunden einige ihrer Peripheriegeräte verfolgen können.
Nehmen wir an, das Bekleidungspaket eines Roboters umfasst externe Luftleitungen und elektrische Kabel, die Strom zum Ende des Armwerkzeugs führen. Sie können die Abnutzung des Schlauchpakets den Daten des Roboters zuordnen. Nachdem sich der Roboter zum Beispiel so viele tausend Grad bewegt oder sein Handgelenk so viele tausend Mal verdreht hat, kann ZDT den Kunden benachrichtigen, dass die Bedingung erfüllt ist, und er kann jemanden losschicken, um das Kleiderpaket zu inspizieren.
Ohne ZDT können Sie die Wartung regelmäßig durchführen, aber mit ZDT würden Sie sie basierend auf der Verwendung des Roboters inspizieren. Kunden optimieren also die Nutzung ihrer Wartungsressourcen und führen Wartungsarbeiten durch, wenn sie erforderlich sind, und nicht nur aufgrund der verstrichenen Kalenderzeit.
Auch wenn ZDT keine Daten von anderen Geräten sammelt, bereitet sich FANUC darauf vor, später in diesem Jahr eine Technologie herauszubringen, die genau dafür entwickelt wurde.
Wie würden Sie das FIELD-System beschreiben?
FIELD ist eine Plattform, die wir dieses Jahr in den USA einführen. Es wurde entwickelt, um Daten von allen netzwerkfähigen Komponenten zu sammeln, einschließlich Robotern, Schweißsteuerungen, SPS und Sensoren und nicht unbedingt FANUC-Geräten. Jedes netzwerkfähige Gerät in einer Einrichtung kann seine Daten mit dem FIELD-System teilen, das intern in der Anlage betrieben wird.
FANUC stellt Softwareentwickler-Kits zur Verfügung, damit Dritte Anwendungen schreiben können, die auf diese Daten zugreifen und Dinge tun, die dem Kunden einen Mehrwert bieten. ZDT ist ein Beispiel für den Wert, den FANUC durch die Verwendung dieser Art von Daten bietet, aber wir glauben, dass es Millionen von Möglichkeiten gibt, was Menschen mit Daten von Fertigungsanlagen tun können. Das FIELD-System soll es anderen Unternehmen ermöglichen, eigene Anwendungen zu entwickeln und an Hersteller zu verkaufen.
Für das FIELD-System stehen zwei verschiedene Server zur Verfügung. Eine, die FIELD Base Pro, kann bis zu 30 Geräte verbinden. Wir unterstützen auch einen Unified Computing Server von Cisco, der bis zu 150 Geräteverbindungen unterstützen kann. Sie können zusammengelegt werden, sodass Informationen zwischen den Servern ausgetauscht werden können.
Es gibt viele verschiedene IoT-Plattformen, aber das FIELD-System von FANUC ist aufgrund mehrerer Vorteile, die es bietet, einzigartig.
- Es läuft innerhalb der Fabrik. Andere laufen in der Cloud, wie es ZDT tut. Da FIELD-Anwendungen innerhalb der Fabrik ausgeführt werden, können die Anwendungen viel reaktionsschneller sein. Sie erhalten ihre Daten nahezu in Echtzeit und können sie analysieren und sehr schnell Entscheidungen treffen. Sie sind auch nicht auf eine Internetverbindung angewiesen.
- FANUC hat die FIELD-Plattform vollständig offen gestaltet. Es wird eine FIELD-System-Partnervereinigung geben, in der Personen, die Anwendungen schreiben oder das FIELD-System in ihre Systeme oder mit ihren Geräten integrieren möchten, dies tun können. Die Mitgliedschaft ist kostenlos.
- Das System kann sich mit jedem netzwerkfähigen Gerät verbinden. Viele der anderen existierenden Plattformen unterstützen nur sehr wenige Protokolle oder ein paar Standardprotokolle, aber FANUC bietet Geräteherstellern auch die Möglichkeit, ihr eigenes Protokoll zu schreiben. Wenn also kein vorhandener Treiber vorhanden ist, um Ihr Gerät mit dem FIELD-System zu verbinden, können Sie einen erstellen. Und dieses Entwickler-Kit ist für Gerätehersteller kostenlos verfügbar.
Die Idee ist, diese Gemeinschaft von Geräte- und Anwendungsentwicklern zu schaffen, um die Fertigungsmöglichkeiten zu erweitern.
Automatisierungssteuerung System
- Industrie 4.0-Softwarelösungen:Wer weiß es besser als die Anwender?
- GE gründet ein 1,2-Milliarden-Dollar-IIoT-Unternehmen
- Sepro führt Apps zur Verbesserung der Robotersoftware ein
- Collaborative Robot Marketplace fügt Überwachungssoftware hinzu
- Der Aufstieg des Roboters:Investition in disruptive Automatisierung
- B&R Software nutzt das Potenzial von Robotern besser aus
- Mitsubishi Electric erwirbt das US-Softwareunternehmen Iconics
- Moderne HMI-Software treibt Industrie 4.0 voran
- Epson entwickelt autonomen zweiarmigen Roboter für die Hightech-Fertigung
- Der Wissensaustausch im Unternehmen, in der Branche