Sie können es mitnehmen:Hybride Arbeitsmethoden verlagern einige Aufgaben an einen beliebigen Ort
Die zunehmende Nutzung digitaler Produktions- und Kommunikationstools während der COVID-19-Pandemie hat die Zukunft des hybriden Arbeitsplatzes beschleunigt, bei dem einige Mitarbeiter und Aufgaben außerhalb der Produktionsstätte umgeleitet werden können.
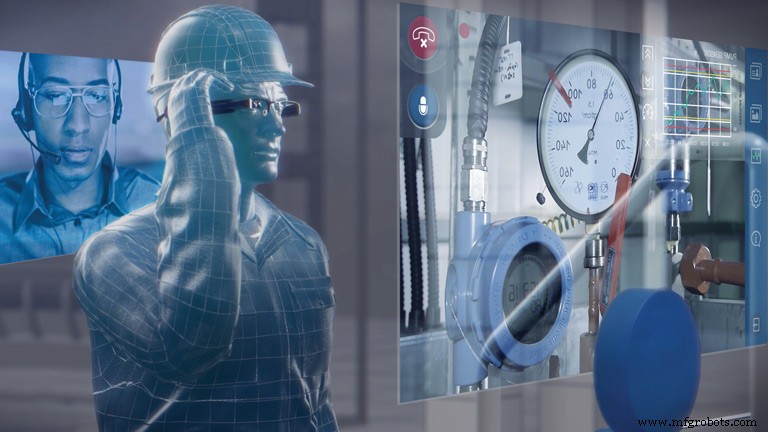
Während Personal wie Designer und Ingenieure problemlos aus der Ferne arbeiten können – und dies je nach Unternehmen bereits vor der Pandemie getan haben – benötigen Maschinen dennoch Bediener vor Ort. Allerdings veranlassen Lösungen wie Virtual oder Mixed Reality und Cloud-basierte Konnektivität Unternehmen dazu, ihre Planung und Durchführung bestimmter Fertigungsaufgaben zu überdenken.
Die Vorteile von Hybrid
Angesichts nicht nur des Fachkräftemangels, sondern auch der Notwendigkeit, ihre Arbeitsplätze an die Pandemieprotokolle anzupassen, haben Hersteller ihre Suche intensiviert, um digitale Tools für ihre einzigartigen Umgebungen zu finden und zu optimieren.
„Obwohl die Vorteile aus Gesundheits- und Sicherheitssicht während einer globalen Pandemie klar sind, sahen Hersteller insbesondere Produktivitäts- und Mitarbeiterbindungsvorteile“ bei der Verfolgung hybrider Arbeitsvereinbarungen, sagte Reid Paquin, Forschungsdirektor für IDC Manufacturing Insights in Needham, Mass. „Beendet ein Drittel erlebte auch eine höhere Mitarbeitererfahrung/-zufriedenheit, was unserer Meinung nach eine Rolle bei den Bemühungen der Branche spielen wird, mit Talent-/Arbeitsproblemen umzugehen.“
Neben der Fertigung „haben die meisten großen OEMs Außendienstelemente, und ein Problem, das derzeit fast überall auftritt, ist der Verlust von Mitarbeitern und Probleme beim Wissenstransfer“, sagte Charlie Neagoy, Senior Vice President of Customer Success bei Librestream. „Wir sind derzeit etwa drei Millionen Menschen in Bezug auf den Ruhestand dem Zeitplan voraus, und das hat diese Wissenslücke beschleunigt. Die hybride Belegschaft – die Fähigkeit, Dinge von verschiedenen Orten aus zu erledigen – trägt dazu bei, den Wissensverlust auszugleichen, der durch die Frühverrentung entsteht. Hybride Belegschaften können Arbeitsplätze auf der ganzen Welt und verschiedene Arten von Flexibilität für ihre Mitarbeiter bieten.“
Librestream mit Sitz in Winnipeg, Manitoba, Kanada, bietet eine Remote-Lösungsplattform für Augmented Reality (AR) an. „Ein damit verbundener Vorteil von Hybridarbeitsplätzen besteht darin, dass sie Plattformen für die gemeinsame Zusammenarbeit mehrerer Parteien ermöglichen“, fügte Neagoy hinzu. „Sicherheit ist auch ein wichtiger Grund für den Einsatz von Hybrid-Arbeitskräften. Viele der Standorte und Geräte in der Fertigung sind gefährlich, sodass der Zugriff auf einen Standort aus der Ferne das Unfallrisiko verringert.“
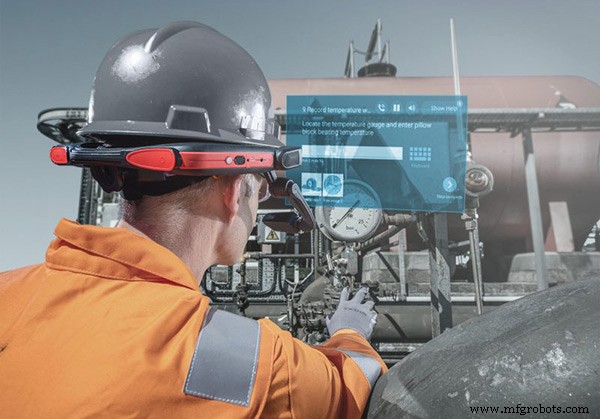
Darüber hinaus können erforderliche Inspektionen und Zertifizierungen aus der Ferne durchgeführt werden, so Neagoy weiter. „Mit unserer Onsight-Plattform können wir nachverfolgen, wie viele Inspektionen unsere Kunden jede Woche durchführen. Unsere Kunden führen jede Woche zwischen 7.000 und 8.000 Inspektionen aus der Ferne durch. Vor COVID verzeichneten wir etwa 2.000 Inspektionen pro Woche.“
Laut Federico Sciammarella, Präsident und CTO von MxD, Chicago, das sich auf die digitale Fertigung konzentriert und Teil von Manufacturing USA ist, einem Netzwerk von 14 fortschrittlichen Fertigungsinstituten, hat die Pandemie gezeigt, dass eine hybride Belegschaft die Widerstandsfähigkeit der Organisation und die Effizienz der Mitarbeiter erhöht /P>
„Wenn eine Organisation über die richtige Netzwerkinfrastruktur verfügt und diese sicher ist, ist es möglich, den Betrieb aus der Ferne auszuführen“, sagte Sciammarella. „Eine ordnungsgemäße Netzwerkinfrastruktur macht ein Unternehmen widerstandsfähiger, da Einzelpersonen immer noch auf die notwendigen Daten zugreifen können, um den Betrieb aufrechtzuerhalten, selbst wenn sie aus der Ferne arbeiten.“
Wie und wo anfangen
Wie bei jeder organisatorischen oder branchenspezifischen Transformation wird Technologie allein aufkommende Probleme nicht lösen. Fernüberwachungs- und Kollaborationstools sind alltäglich geworden, aber wie immer ist eine ordnungsgemäße Planung entscheidend für die Einführung eines Hybridmodells.
„Zusammenarbeit, Videokonferenzen und Plattformen/Anwendungen zum Teilen von Inhalten sind einige der Bereiche, in die Hersteller investiert haben oder investieren wollen, um hybride Arbeitsmodelle besser zu ermöglichen“, bemerkte Paquin von IDC Manufacturing Insights. „Die meisten Hersteller müssen fast immer einige Mitarbeiter vor Ort haben. Instandhaltung/Asset Management ist einer der Bereiche, in denen dies der Fall sein wird; es muss jemand da sein, der an einem Schraubenschlüssel dreht. In Zukunft können Hersteller dies möglicherweise stärker auf Roboter verlagern, aber im Moment ist dies aufgrund der ausgereiften Technologie und der Investitionskosten für die meisten Hersteller nicht möglich.“
Hersteller, die bereits große Investitionen in Automatisierung, Datenerfassung und Remote-Konnektivität getätigt hatten, verfügten bereits vor der Pandemie über die Infrastruktur, um diesen Wandel zu unterstützen, räumte Paquin ein. „Wir haben festgestellt, dass Hersteller mit Cloud-Systemen wie ERP am besten für hybrides Arbeiten geeignet sind. Der beste Ansatz besteht darin, eine Strategie/Roadmap im gesamten Unternehmen zu erstellen, diese jedoch in kleineren Schritten umzusetzen. Beginnen Sie mit Backoffice-Funktionen, da weniger Investitionen erforderlich wären, um diesen Gruppen Remote-Arbeit zu ermöglichen. Achten Sie auf die geltenden Richtlinien für Remote-Arbeit und die Verwaltung von Remote-Mitarbeitern und integrieren Sie Best Practices und gewonnene Erkenntnisse, wenn Sie weitere Funktionen erweitern.“
In Anbetracht dessen, dass der durchschnittliche Arbeitnehmer 240 Stunden im Jahr – 10 Tage – damit verbringt, auf Informationen zu warten, riet Neagoy von Librestream:„Wenn Sie ein Operator vor Ort sind, ist es eine gute Strategie, das Wissen eines Fachexperten in die digitale Welt einzubetten Arbeitsanweisung, also warten Sie nicht mehr auf diesen Experten.“
Neue Technologie in die Hände der richtigen Mitarbeiter zu geben, sei von entscheidender Bedeutung, so Neagoy weiter. „Wenn Sie eine neue Technologie einführen, beginnen Sie mit dem Technologieexperten. Unsere Kunden sehen in der Regel eine bimodale Verteilung der Benutzerakzeptanz:Sie unterscheidet sich radikal zwischen Personen, die 10 Jahre vor dem Ruhestand stehen, und Personen, die weniger als 10 Jahre in ihrer Karriere sind.“
Seien Sie versichert, sagte er, dass „dies etwas ist, das in drei Monaten umgesetzt werden kann. Es wird nicht in drei Monaten vollständig realisiert sein, aber in drei Monaten sollten Sie in der Lage sein, die Nadel zu bewegen.“
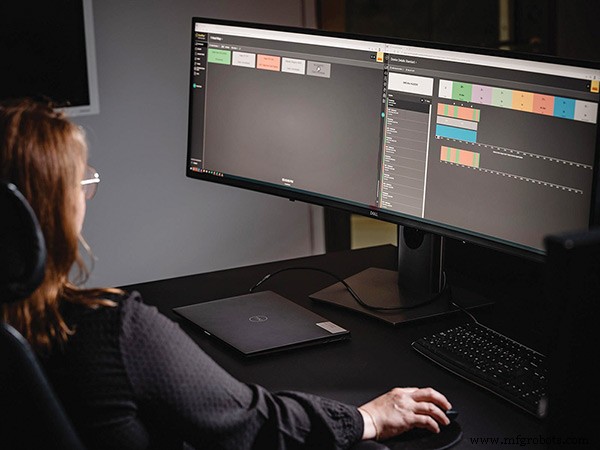
Wie bei der Herangehensweise an andere Fertigungsbetriebe, so Sciammarella von MxD, „müssen Maßnahmen sorgfältig und ganzheitlich geplant werden, wobei die grundlegenden Werkzeuge der kontinuierlichen Verbesserung im Auge zu behalten sind. Es ist wichtig, zuerst zu überprüfen, was Sie derzeit haben und warum. Das „Warum“ ist entscheidend und mag offensichtlich erscheinen, aber das ist nicht immer der Fall, insbesondere wenn Sie eine lange Geschichte von Workflows haben. Ein Unternehmen möchte an einen Punkt gelangen, an dem das Team weiß, welche Daten und Informationen digitalisiert werden können – falls dies noch nicht geschehen ist – und wie diese genutzt werden können, um nicht nur flexible Arbeitszeiten zu unterstützen, sondern auch einen kontinuierlichen Verbesserungsprozess, der genutzt werden kann aus der Ferne, damit die Produktion weiterhin Produkte herstellen und die Arbeit nach Bedarf optimieren kann.“
Wenn ein Unternehmen mit der Implementierung von Cloud-Technologien für Geschäftsdaten begonnen hat, fügte er hinzu, „könnte es diese Cloud-Technologien für die Erfassung von Betriebsdaten nutzen und Dateien und Informationen für diese Belegschaft leicht verfügbar machen.“
Jüngste Erfolge
Für Fives Lund aus Seattle, einem Hersteller hochgradig kundenspezifischer Maschinen, sind Flexibilität am Arbeitsplatz und die richtigen Tools zur Ausführung kritischer Aufgaben aus der Ferne seit Jahren Teil der Kultur.
Chancen zu ergreifen, um sicherzustellen, dass ihre Mitarbeiter überall so effektiv wie möglich sein können, „ist seit unserem Beitritt zur Fives-Gruppe im Jahr 2015 ein fortlaufender Prozess“, sagte CEO Casey McGarity. „Schon vor COVID war das ein fortlaufender Prozess und eine Reise – kein Ziel.“
Vor der Pandemie „war unsere Belegschaft ziemlich stark auf unser Werk in Seattle konzentriert – aber wir hatten immer Ingenieure und Techniker, die vor Ort waren und die Ausrüstung unterstützten“, fügte Jonathan Schwedhelm, leitender Maschinenbauingenieur und technischer Leiter, hinzu. „Wir entwickeln auch einige unserer komplexen Automatisierungsgeräte gemeinsam mit unseren Schwesterunternehmen auf der ganzen Welt.“
Dann kam die Pandemie. Und während Fives Lund mit anderen großen Arbeitgebern in seiner Region in Bezug auf die Heimarbeit auf Augenhöhe war, „haben wir ein ziemlich praktisches Umfeld“, erklärte Schwedhelm. „Unsere Ingenieure und Techniker arbeiten sehr eng zusammen, um unsere Geräte zu bauen, zu testen und zu unterstützen.“ Das bedeutete, kreativ zu werden, um die Entwicklung und Lieferung von Geräten fortzusetzen und Kunden zu unterstützen.
„Das bedeutete schon früh, dass einige Ingenieure kleinere Projekte und Baugruppen mit nach Hause nahmen, um daran zu arbeiten. Einige unserer Steuerungsingenieure bauten Hardware in ihren Häusern auf, damit sie die Maschinen programmieren konnten – aber das lässt sich wirklich nicht skalieren.“
Hier kam Run MyVirtual Machine von Siemens ins Spiel. Die Simulationssoftware für den Maschinenbetrieb „eröffnet Steuerungsingenieuren die Möglichkeit, mit dem Bau der Steuerungen der Maschine zu beginnen und Kinematik und Betrieb zu testen sowie die Maschinen maßstabsgetreu zu simulieren Stellen Sie sicher, dass sie die Dinge so schnell erledigen, wie Sie denken“, sagte Schwedhelm.
Run MyVirtual Machine hat Wunder bei einem Projekt gewirkt, das im Jahr vor der Pandemie begann, fuhr er fort.
„2019 begannen wir mit der Arbeit an einer großen Automatisierungsanlage, und unser Kunde verlangte von uns den Einsatz von CNC-Steuerungen von Siemens. Wir sind mit einer Reihe verschiedener NC-Steuerungssysteme vertraut, aber die Maschine, die wir bauten, hatte eine wirklich einzigartige Kinematik, und wir wussten, dass sie einige große technische Hürden hatte, die wir beseitigen mussten, bevor Hardware verfügbar war – und sicherstellen mussten wir könnten es tun, ohne hier in unserer Einrichtung vor den Steuerpulten sitzen zu müssen.“
Obwohl er Erfahrung mit anderer Modellierungssoftware hatte, fuhr er fort:„Da es sich um ein Siemens-Projekt handelte, konnten wir dieses Tool zum ersten Mal nutzen – es bei der Planung verwenden, Risiken reduzieren und sicherstellen, dass wir es sind gute Entscheidungen zu treffen, während wir den Designprozess durchliefen. Und jetzt, wo die Lieferkette zu einem größeren Problem wird und die Lieferzeiten für unsere Steuerungskomponenten herausfordernd sein können, können wir weitermachen, ohne vollständig ins Stocken zu geraten.“
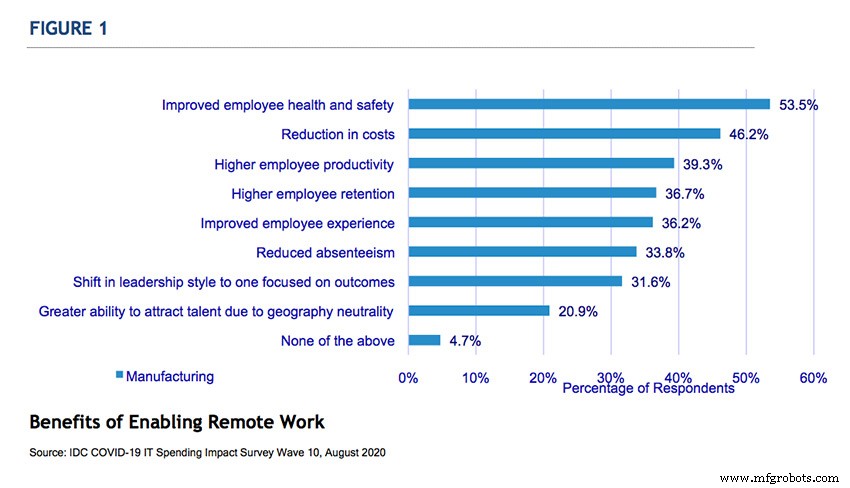
Der Kern der Kultur von Fives Lund ist die Tatsache, dass „unsere Ingenieure – Mechanik, Elektrik und Software – oft Schulter an Schulter vor Ort arbeiten und tatsächlich Maschinen bauen und Fehler beheben“, bemerkte McGarity. „Zumindest stehen die Ingenieure zur Verfügung, um die Werkstatt zu besuchen, wenn sie auf Probleme stoßen“ oder um bei der Planung, Montage oder Prüfung zu helfen. In dem Maße, in dem Ingenieure nicht „da draußen aktiv an Aufgaben in der Fertigung teilnehmen“, „sind sie tief in die Planung dieser Dinge involviert.“
In Bezug auf das Kernproblem der Implementierung hybrider Arbeitsabläufe in der Fertigung bemerkte McGarity, dass das Fertigungspersonal zwar vor Ort bleiben musste, „es aber sehr schwierig und ganz anders für Fives Lund war, die Ingenieure nicht direkt vor Ort zu haben, um bei diesem Prozess zu helfen. Wie viele Unternehmen haben wir die Risiken von COVID gegen das Risiko der Kultur und Effizienz abgewogen, die ein starkes, geschlossenes Team mit sich bringt. Die Tools, die wir haben, tragen dazu bei, diese Kultur aufrechtzuerhalten. Wir haben mit einer besonders gesunden und starken Gruppe begonnen, aber diese kollektiven Muskeln schrumpfen ein wenig, selbst mit guten Werkzeugen. Je effektiver die Werkzeuge sind, desto besser können wir unsere Kräfte länger aufrechterhalten. Aber wir müssen auch zurückkommen und uns daran erinnern:‚Wir sind stärker, wenn wir uns körperlich nahe sind‘.“
Anpassung mit angepassten Arbeitsabläufen
Hybridlösungen sind auch für Sandvik Coromant selbstverständlich, das nicht nur Werkzeuge bereitstellt, die seinen Kunden Möglichkeiten zur Fernarbeit bieten, sondern auch die Arbeitsabläufe in seinen eigenen Schneidwerkzeugfabriken angepasst hat.
„Das Vorhandensein der Technologie, was CAD/CAM angeht, hat uns geholfen, aber wir brauchen hier natürlich immer noch Leute, die die Ausrüstung bedienen“, sagte Production Unit Manager Richard Boyle. „Wir sind noch nicht an dem Punkt angelangt, an dem unsere Ausrüstung das Licht ausmacht – wir brauchen immer noch unsere Mitarbeiter hier –, aber es gab uns eine gute Gelegenheit, mit den technischen Aspekten unserer Fertigungshalle fortzufahren, wobei die Fertigungsingenieure im Büro sind in der Produktion und auch die Möglichkeit, einen Teil der Zeit von zu Hause aus zu arbeiten.“
Als die Pandemie ausbrach, arbeiteten Sandvik-Designer auch die meiste Zeit aus der Ferne, sagte Boyle, und fuhr jede Woche nach einem rotierenden Zeitplan einen in die Werkstatt, um die Produktion zu unterstützen und gleichzeitig die Exposition einer Person zu begrenzen. In der Zwischenzeit beschäftigt das Unternehmen eine sogenannte unbemannte Produktion, bei der Maschinenbediener wechseln, „wenn wir ein Gerät haben, das automatisiert ist und ohne Anwesenheit eines Bedieners läuft.“
Boyle erklärte, dass zwischen zwei achtstündigen Maschinenbedienerschichten ein vierstündiges Intervall eingeplant sei. Mit zwei einander gegenüberliegenden Zellen können diese Zeitpläne gestaffelt werden, sodass nur ein Bediener vor Ort sein muss, um eine Unterbrechung in jeder Zelle zu betreuen. „Wir haben Leute, die fast rund um die Uhr mit der Arbeit beginnen, um sicherzustellen, dass wir eine vollständige Abdeckung haben.“
Er schreibt auch Sandviks Partnerschaft mit Microsoft und seiner Mixed-Reality-Technologie HoloLens für die Erleichterung der hybriden Arbeit zu. „Der größte Teil der Technologie, die wir in der Produktion von unserem MES und unseren Dashboards nutzen – alle verfügbaren Daten – kommt aus ihren Lösungen. Wir hatten hier und da einen Ausfall, vielleicht für ein paar Stunden, wo wir uns nicht bei einem Dienst anmelden können, aber sie sind selten.“
Während der Pandemie hat Sandvik ein neues Gerät in Auftrag gegeben, das aus Schweden eingeflogen wurde, als alle Passagierreisen storniert wurden, erinnerte sich Boyle. „Anstatt zu warten, bis die Reise wieder erlaubt war und der Techniker aus Schweden vorbeikommen und die Installation abschließen konnte, konnten wir durch den Einsatz von Technologien wie HoloLens unser lokales Wartungspersonal direkt mit dieser Person zusammenarbeiten lassen, die direkt durch sie hindurchsehen konnte beobachten, was sie tun, und sicherstellen, dass wir uns auf die richtigen Dinge konzentrieren, um diese Maschine in Betrieb zu nehmen und in Betrieb zu nehmen.“
Letztendlich, so Boyle, ist die Balance zwischen hybriden und traditionellen Arbeitsabläufen „immer ein Kampf. Daran muss man arbeiten. Bei Hybrid sagen wir nicht, dass jemand zu 100 Prozent remote ist. Wenn Sie versuchen können, einen Prozess für Remote zu öffnen, der dafür noch nicht ganz bereit ist, ist es manchmal schwierig, ihn wieder hineinzuziehen. Wir waren sehr langsam und akribisch, einen Prozess für Hybrid zu öffnen, um sicherzustellen, dass wir es sind in der Lage, es schnell aufrechtzuerhalten und zu modifizieren, damit es nicht ausfällt.“
Für Kunden bietet Sandvik Remote-Ready-Produkte, darunter CoroPlus Machining Insights und CoroPlus Process Control, sagte Jeff Rizzie, Director of Digital Machining Sales for the Americas.
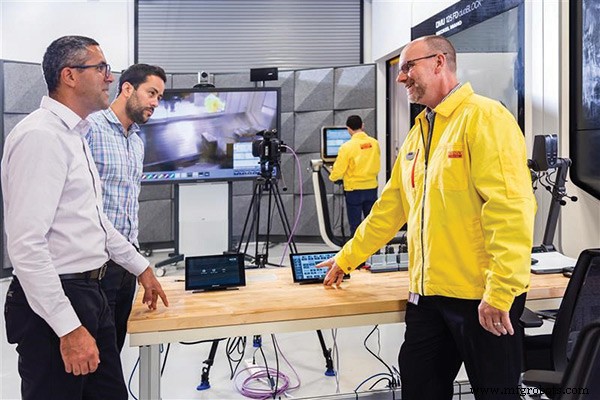
Machining Insights ist eine Software-as-a-Service-Plattform, die den Maschinenzustand überwacht, erklärte Rizzie. „Wir können feststellen, was mit einer bestimmten Werkzeugmaschine passiert, indem wir uns einfach bei einer Site anmelden. Ich kann Nutzungsdaten verstehen, wie viele Teile ich herstelle, und mir die Planung und mehrere Datenpunkte ansehen, die direkt von der Maschine kommen. Diese Art von Lösungen sind von enormem Wert, auch aus betrieblicher Sicht. Ich muss jetzt nicht mehr vor Ort sein, um zu verstehen, was in meinem Geschäft passiert, indem ich die Daten richtig verwende.“
CoroPlus Process Control geht noch einen Schritt weiter, indem es den Zustand eines gesamten Fertigungsprozesses misst, fuhr Rizzie fort. „Es kann eine adaptive Steuerung durchführen und die Maschine außer Kraft setzen. Erkennt er eine Kollision oder einen Werkzeugbruch, kann er die Maschine automatisch abschalten. Es kann einen Befehl ausgeben, ein Schwesterwerkzeug oder ein redundantes Werkzeug zu erwerben und die Fertigung wieder aufzunehmen. Und es kann bei der unbemannten Bearbeitung helfen – es fügt dem Prozess ein zusätzliches Maß an Sicherheit hinzu.“
Darüber hinaus ist Sandvik bestrebt, seine Mitarbeiter weiterzuentwickeln, um sie besser für die Fernunterstützung von Kunden auszurüsten, bemerkte Annika Langeen, Vizepräsidentin für Marketing in Amerika. „Wir haben unsere Sandvik Coromant Center mit der neuesten Technologie ausgestattet, um Remote-Support bei Kundenprojekten und virtuelle Live-Schulungen zu ermöglichen“, sagte sie. „Mit der neuesten Audio- und Videotechnologie können Kunden sehen, was innerhalb und außerhalb der Maschinen in unseren Sandvik Coromant Centern passiert, und von jedem beliebigen Ort aus in Echtzeit mit unseren Yellow Coat-Experten interagieren. Seit vielen Jahren bieten wir auch ein umfangreiches E-Learning-Programm an, um Kunden, Studenten und Mitarbeitern zerspanendes Wissen zu vermitteln. Die Teilnehmer können das Schulungsprogramm absolvieren und sich jederzeit und überall zertifizieren lassen.“
Hybride Arbeit in der Zukunft
Die digitale Fertigung wird oft als Instrument zur Rekrutierung und Bindung von Arbeitskräften angepriesen. Paquin von IDC stimmt zu.
„Hybrid-/Fernarbeit kann den Kandidatenpool für bestimmte Rollen erweitern, und wir hören immer wieder von Herstellern, dass es der jüngere Teil ihrer Belegschaft ist, der sich mehr Flexibilität und Optionen bei Arbeitsmodellen wünscht“, bemerkte er. „Für eine Branche, die darum kämpft, neue Talente anzuziehen, könnte die Nichteinführung hybrider Arbeitsmodelle dies zu einer noch größeren Herausforderung machen.“
Die große Herausforderung, bemerkte Neagoy von Librestream, „besteht einfach darin zu verstehen, wo ein hybrider Arbeitsplatz angewendet werden kann. 80 Prozent der Belegschaft sind im Außendienst tätig, sodass die Schaffung hybrider Belegschaften eine überwältigende Aussicht sein kann. Das Erfolgsrezept bei der Implementierung einer hybriden Belegschaft besteht darin, sehr klare Geschäftsziele zu identifizieren. Haben Sie etwas, das quantifizierbar und messbar ist, und fangen Sie klein an. Wenn Sie verschiedene Funktionsbereiche haben, die im Wesentlichen Duplikate voneinander sind, wählen Sie einen aus und kommen Sie damit zum Erfolg und wenden Sie das Gelernte dann auf die gesamte Organisation an.“
Beachten Sie auch, dass „es eine seltsame Dualität gibt, wie sich Menschen an hybride Belegschaften anpassen“, riet Neagoy. „Die Leute mit dem größten Wissen über das Geschäft können diejenigen sein, die technologisch am wenigsten versiert sind. Lassen Sie die erfahrenen Mitarbeiter wissen, dass neue Hybridtechnologien nicht da sind, um ihnen zu helfen – sie sind da, um anderen zu helfen.“
Während Plattformen und Technologien, die existieren, um Hybrid Realität werden zu lassen, während COVID umgestellt wurden, besteht das Problem jetzt darin, „wie man sie so integriert, dass sie für die Bedürfnisse jedes Unternehmens effektiv sind“, bemerkte Sciammarella. „Sind die richtigen Netzwerke und Konnektivität – also 5G – vorhanden und wie kann deren Sicherheit gewährleistet werden? Dies kann kostspielig sein und erfordert eine sorgfältige Überlegung, wie diese Tools und Plattformen so wirtschaftlich wie möglich integriert werden können.
„MxD hat immer gesehen, dass Unternehmen, die digital fähig sind, in Krisen besser abschneiden. Die Pandemie war nicht anders“, fuhr er fort. „Organisationen befinden sich auf unterschiedlichen Wegen, um die digitale Transformation zu vollbringen – und diejenigen, die weiter fortgeschritten sind, könnten im Allgemeinen leicht zu hybriden Praktiken übergehen.“
Nur weil die Werkzeuge zur Verfügung stehen, um eine hybride Belegschaft zu schaffen, liegt es letztendlich an der Kultur eines bestimmten Unternehmens und seiner Bereitschaft, „in sinnvolle Veränderungen zu investieren, damit sein Unternehmen nicht nur überleben, sondern gedeihen kann. Ehrlich gesagt ist die größte Herausforderung der Kulturwandel. In der Produktion ist der Mensch ein Gewohnheitstier, aus dem man nur schwer ausbrechen kann. Die andere große Herausforderung sind die finanziellen Kosten für die Digitalisierung, um eine hybride Belegschaft zu stärken“, bemerkte Sciammarella. „Für kleine Unternehmen ist es äußerst schwierig zu beurteilen, was die größte Rendite bringen könnte, wenn es so viele Möglichkeiten gibt.“
Automatisierungssteuerung System
- Wie können Luft- und Raumfahrtunternehmen die additive Fertigung mit MES auf die nächste Stufe heben?
- Was können Sie mit einer CNC-Fräsmaschine herstellen?
- Mit KI können Big-Box-Läden es mit E-Tail-Rivalen aufnehmen
- CNC-Fräser zu verkaufen:Was können Sie damit machen?
- 5 Möglichkeiten, wie Sie durch die Automatisierung des Herstellungsprozesses Geld sparen können
- Wie Software-Roboter Ihnen helfen können, die Kontrolle über die „neue Normalität“ zu übernehmen
- Was kann man mit einer CNC-Maschine machen?
- Konnektivität in der Fertigung:Wie kann sie verbessert werden?
- Kann KI Arbeitsplätze in der Fertigung schaffen?
- ABB sagt, dass beim Übergang zur Fahrzeugelektrifizierung Flexibilität erforderlich ist