Mit Paletten und Robotern neue Maßstäbe setzen
Das Angebot und die Anforderungen an flexible Bearbeitungszellen steigen
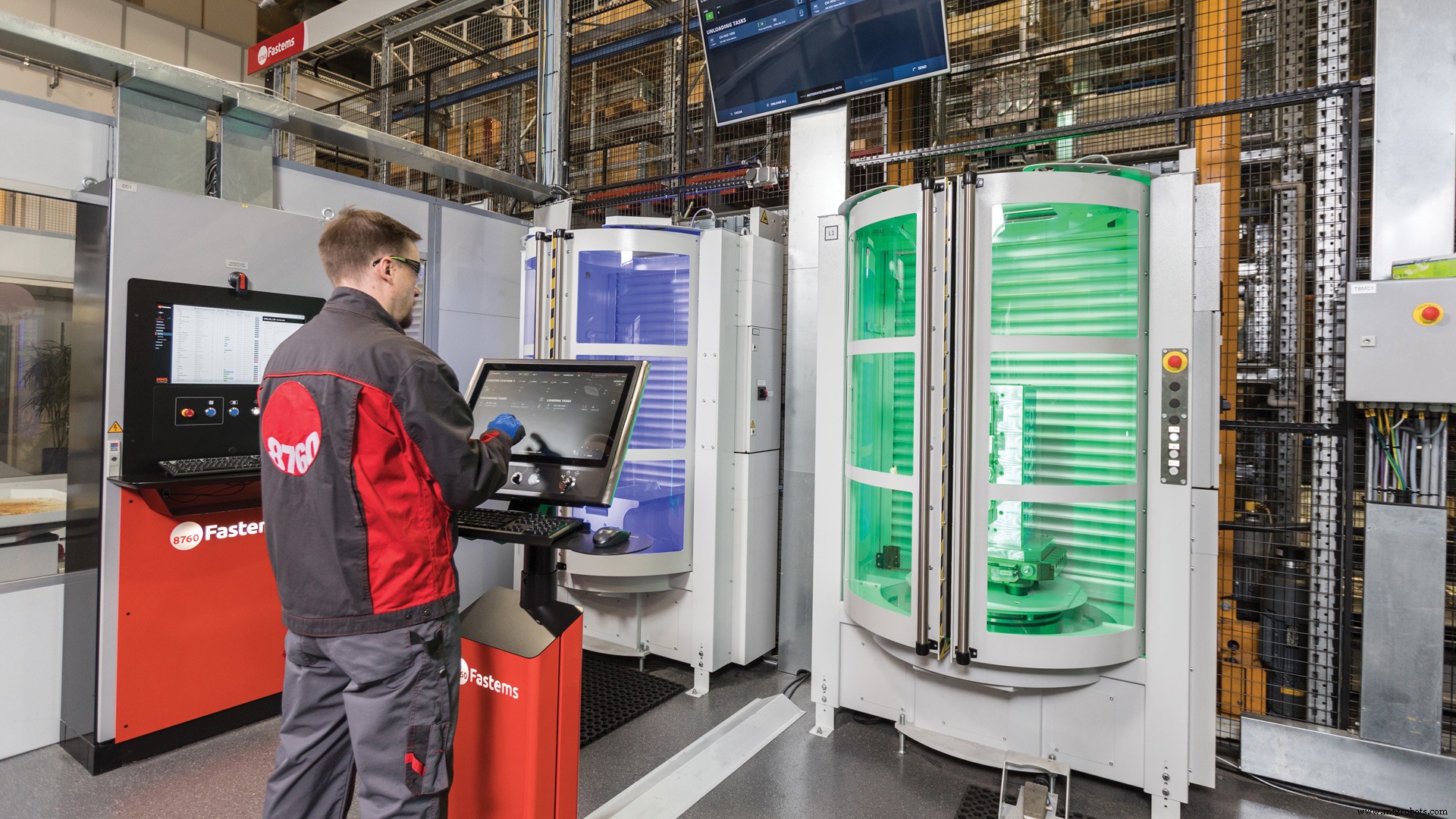
Da sich automatisierte Fertigungsprozesse aufgrund von Problemen wie dem Fachkräftemangel weiter von „nice to have“ zu „must have“ entwickeln, entstehen flexible Fertigungssystemkonfigurationen in neuen und aufregenden Formen.
Die COVID-19-Pandemie hat die Hersteller eindeutig dazu veranlasst, den Einsatz von Robotern in Palettensystemen zu beschleunigen. Aber das ist nicht die einzige faszinierende Wendung, die das FMS in letzter Zeit genommen hat.
„Flexible Fertigungssysteme können heute ganz andere Dinge bedeuten als früher“, erklärt Automation Manager Zach Spencer von Methods Machine Tools mit Sitz in Sudbury, Massachusetts. „Früher war jeder an Palettenwechselsysteme gewöhnt, um maximale Flexibilität zu erreichen ihre Maschinen. Diese Palettenpools ermöglichten es den Kunden, verschiedene Spannvorrichtungen auf verschiedenen Paletten zu montieren und ihre Maschinen unbeaufsichtigt zu betreiben.
„Flexible Automatisierung kann heute viele Formen annehmen. Dies kann alles sein, von palettierten Maschinen, Robotern, die Paletten bewegen – wie unsere Automatisierungssysteme Plus-K und Plus-K60 – bis hin zu komplexeren, aber dennoch einfach zu bedienenden Systemen wie flexiblen Bildverarbeitungssystemen zum Einrichten von Teilen.“
Für diejenigen, die neu im Automatisierungsspiel sind, sagte Spencer, dass sie einfach anfangen sollen.
„Wir empfehlen normalerweise, mit einem kleineren und weniger komplizierten System zu beginnen, um sich mit der Automatisierung vertraut zu machen – machen Sie sich damit vertraut, bevor Sie einen großen Sprung machen. Für uns kann diese kleinere oder intelligentere Art von System bedeuten, dass wir eine Maschine statt vieler bedienen und einen Chargenlauf durchführen müssen, anstatt viele verschiedene Arten von Werkstücken gleichzeitig zu bearbeiten.“
Lösungen, groß und klein
Da das Palettenautomatisierungsgeschäft „das Herzstück“ von Fastems ist, steht das finnische Unternehmen an der Spitze aufkommender Automatisierungstrends. Die Pandemie hat die Hinzufügung von Robotern zum Be- und Entladen von Teilen in FMS-Anlagen beschleunigt, sagte Mika Laitinen, Solution Sales Director bei Fastems.
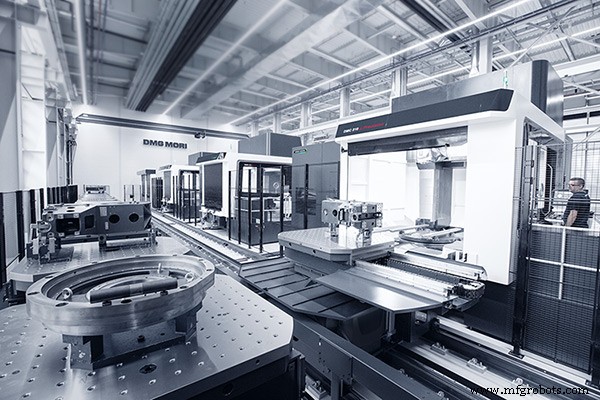
Andere Hilfsoperationen werden zunehmend innerhalb derselben Systeme hinzugefügt, fügte Christopher Rezny, Regionalleiter für die Zentral-U.S. bei Fastems, hinzu. Egal, ob ein Teil gedreht oder bearbeitet wird, es muss gewaschen werden. Darüber hinaus müssen Teile geprüft werden – entweder einzeln oder nach einem Durchlauf von vielleicht 100. Entgratungs- und automatische Vorrichtungsladevorgänge können ebenfalls durchgeführt werden, und die Anbindung an automatisch geführte Fahrzeugsysteme (AGV) hält den Materialfluss in den Betrieb aufrecht.
Ursprünglich für horizontale Bearbeitungszentren konzipiert. das FPC-System (für flexible Palettenbehälter) von Fastems kann auf bis zu vier Werkzeugmaschinen erweitert werden.
„Zum ersten Mal, zumindest in Finnland, wird dieser Motorblock in dieser Art von Werkzeugmaschinen mit AGVs automatisch be- und entladen“, da die Anlage ohne Regalbediengerät gebaut wurde. Das AGV bewegt die Bearbeitungspalette zum Waschen, Prüfen, Entgraten und Endbearbeiten von Ort zu Ort. „Wir haben auch Vormontageaufgaben, um bestimmte Endbearbeitungsvorgänge durchzuführen. Und wir haben Speicher. Wir haben also die gleichen Elemente wie beim herkömmlichen Regalbediengerät auf Regalbediengerät-Basis, aber jetzt ist alles auf einer Ebene“ aufgrund des Komponentengewichts.
Der Einsatz von AGVs anstelle eines Krans ist in einer solchen Situation ideal, fuhr Laitinen fort, da die Bearbeitungszeit ziemlich lang ist – mehrere Stunden –, sodass es kein Problem darstellt, das langsamere Be- und Entladefahrzeug für den Palettenwechsel zu verwenden.
Laufzeit und Roboter
Ob Palettensysteme linear oder rotierend sind, mit Einzel- oder Mehrmaschineneinrichtung, die Geschmacksrichtungen von FFS sind vielfältig.
Bei DMG Mori finden sein LPP oder linearer Palettenpool und sein einfacheres RPS oder Rotationspalettensystem in mehreren Konfigurationen ein Zuhause.
„Der typische Sweetspot für einen LPP ist 24 bis 36 Paletten und zwei oder drei Maschinen und zwei Ladestationen“, sagt John McDonald, General Manager für Entwicklung am Produktionsstandort von DMG MORI in Davis, Kalifornien. Wir haben Materialfluss in und aus den Ladestationen, Arbeit steht im Palettenpoolsystem an und die Maschinen arbeiten Tag und Nacht.“
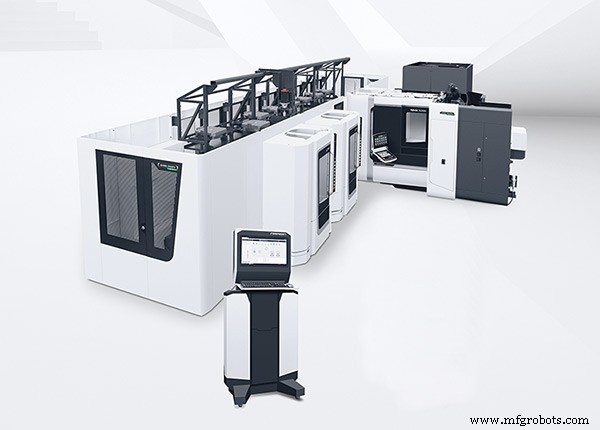
Inzwischen ist das RPS „ein System mit einer Maschine und einer Palette“, fuhr McDonald fort. „In der Regel sind fünf Paletten darin, und wir gehen bis zu 21 Paletten. Diese eignen sich wiederum hervorragend für Warteschlangenarbeiten. Sie haben nicht so viel Teilemix oder kombinieren es mit einer Art Schnellwechselvorrichtung, sodass Sie Ihre Arbeitsumgebung ändern können.“
Letztendlich das richtige FFS für eine bestimmte Werkstatt ist derjenige, der die unbeaufsichtigte Laufzeit optimiert. Es geht darum, mehr Spindelstunden am Tag zu haben und mehr „Walkaway“-Zeit, um die Mitarbeiter andere Aufgaben erledigen zu lassen, sagte er.
Die andere Aufgabe des FMS besteht natürlich darin, mehr Arbeit in die Tür zu bekommen. „Ich habe Kunden, die an meine Tür klopfen und sagen:‚Hier ist ein Job zum Bieten, da ist ein Job zum Bieten.‘ Ich sehe, dass die meisten Leute denken:‚Kann ich dieses Ding wirklich implementieren?‘ Unsere private Technologie Touren und bildungsbasierte Veranstaltungen zeigen diesen Kunden, wie diese Tools tatsächlich zusammenarbeiten, um diese unbeaufsichtigte Laufzeit zu erreichen.“
Die 2021 eingeführte Software LPS 4 von DMG Mori ist die vierte Generation der Automatisierungssystem-Management-Software des Unternehmens. Damit können Hersteller einige der Materialverwaltungsschritte eliminieren, indem sie sich direkt mit einem ERP verbinden. Wenn ein Kunde beispielsweise 500 Blöcke aus 6061er Aluminium zur Herstellung von Wasserpumpen bestellt, erklärt McDonald:„Sobald Sie diesen Wasserpumpenauftrag erstellt haben, kann Ihr ERP-System die Nachfrage nach dem, was es als nächstes produzieren wird, an das Palettenpoolsystem leiten . Wir haben diesen manuellen Link entfernt, bei dem jemand Daten aus dem ERP in die LPS 4-Software eingibt; Wir haben diese Schleife geschlossen, indem wir diese beiden miteinander verbunden haben. Nicht alle Kunden sind heute bereit, dieses Niveau zu nutzen – aber einige der produktiveren Geschäfte tun dies.“
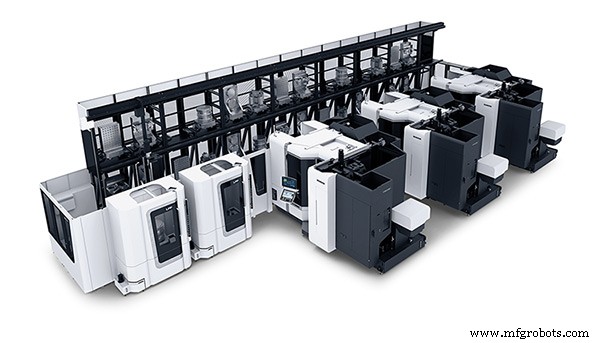
Um zu veranschaulichen, was sein FMS leisten kann, betreibt DMG Mori ein Ein-Meter-LPP mit drei Maschinen in seiner eigenen Maschinenhalle, stellte McDonald fest. „Sie verfügt über eine Teilewaschstation, eine Roboterbeladung, hydraulische Vorrichtungen und Materialpaletten. Wir bearbeiten die Gussteile, aus denen wir unsere Maschinen bauen, hier in unserem Werk in Davis. Ein Bediener lädt das Gussteil auf die Materialpalette. Fast alle diese Gussstücke müssen gekrant werden; Sie sind viel zu schwer, als dass sie jemand heben könnte. Sie werden auf eine Palette gekrant, die wie eine Gabelstaplerpalette aussieht. Dort wird das Teil abgelegt und wandert dann in die Palettenregale. Die Materialpalette geht in die Roboterladung selbst, ebenso wie die Vorrichtungspalette. Der Roboter nimmt also das Teil auf und lädt es auf die Vorrichtung, dann wird das Teil mit einer hydraulischen Werkstückhalterung befestigt. Und dann geht das Teil ins Bearbeitungszentrum.
„Sobald dieser Vorgang abgeschlossen ist, geht es in die Teilereinigung; Das Teil wird gereinigt, um Späne oder Splitt aus den mit Klebeband versehenen Löchern zu entfernen. Wir haben Kunden, die das noch weiter vorangetrieben haben, wo wir Messmaschinen und Lasermarkierzellen integriert haben. Einige Kunden nutzen das LPP auch in Kombination mit unserer zentralen Werkzeugverwaltung – so werden nicht nur die Werkstücke, sondern auch die Werkzeuge im Maschinenmagazin automatisch gewechselt. Typischerweise sehen wir OEMs, die diese Art von Zellen implementieren.“
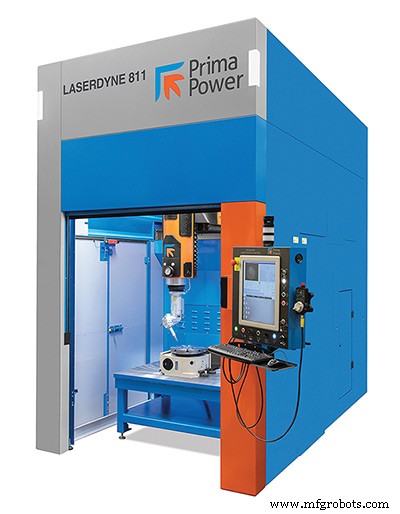
Auch Methods dient der Entwicklung von einfachen Palettenwechselsystemen zu robotergeführten Lösungen mit Palettenmanagementsteuerung, sagte Spencer.
„Ein sehr erfolgreiches System, das wir entwickelt und eingesetzt haben, ist unser RoboDrill Plus-K-System“, erklärte Spencer. „Dieses System verwendet einen FANUC RoboDrill mit einem FANUC Roboter, um es zu pflegen. Auf der Roboterseite besteht die Möglichkeit, bis zu 60 Werkstücke gleichzeitig im System zu speichern. Dieses System verfügt über eine in die Maschinensteuerung eingebettete Palettenverwaltungsfunktion, die es dem Bediener ermöglicht, spezifische Programmnummern für die verschiedenen 60 Stationen festzulegen, an denen Teile gelagert werden können. Dieses flexible System ermöglicht auch eine erweiterte Werkzeugausstattung auf der Maschine, was bei der Arbeit an verschiedenen Arten von Teilen in den 60 verschiedenen Arbeitsstationen enorm hilfreich sein kann.“
Und die High-Mix-, Low-Volume-Produktion ist nicht vom Tisch, fügte Spencer hinzu. In diesen Fällen „empfehlen wir in der Regel eine starrere Lösung. Bei jedem Automatisierungs- oder Werkzeugmaschinenverkauf versuchen wir, dem Kunden die ROI-Berechnungen für sein Geschäft zu zeigen, um den Verkauf der Ausrüstung zu genehmigen. Wir tun, was wir können, um einen ROI von 18 bis 20 Monaten für den Kunden zu übertreffen.“ Das Plus-K-System des Unternehmens ist maßgeschneidert für Arbeiten mit hohem Mix und geringem Volumen, fügte er hinzu.
„Wir haben mit flexiblen Systemen große Erfolge in der Medizinbranche erzielt. Ich denke, ein Hauptgrund dafür ist der Bedarf in der medizinischen Industrie an einer High-Mix-Anwendungsart. Damit meine ich, dass sie in der Regel kleine Chargen – bis zu vielleicht 10 Teile gleichzeitig – verarbeiten können, bevor sie eine andere Art von Teil herstellen müssen. Dies eignet sich perfekt für eine flexiblere Lösung, die extrem einfach von einer Teilenummer zur nächsten geändert werden kann.“
Für Track-and-Trace-Anforderungen, fuhr er fort, „bieten wir Zellcontroller an, die Kunden bei der Rückverfolgbarkeit von Teilen durch Systeme unterstützen können. Zellcontroller können die Betriebszeit von Geräten, Alarmstatus und -historie sowie die Maschinennutzung überwachen. Diese Systeme verfügen in der Regel über QR-Code-, Barcode- oder RFID-Scanfunktionen, mit denen der Bediener während der laufenden Produktion Teile in und aus den Zellen scannen kann. Diese Informationen werden normalerweise in einer lokalen Datenbank der Zelle gespeichert, wo sie auf den Server eines Kunden kopiert werden können.“
Der Laserwinkel
Wenn Laserschneiden und -schweißen in die Gleichung eintreten, nimmt ein FMS eine etwas andere Definition an, sagte Dominic Rickard, Vertriebsleiter für Nordamerika bei Prima Power Laserdyne mit Sitz in Brooklyn Park, Minnesota.
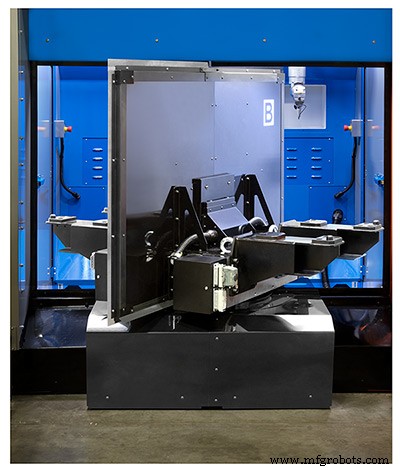
„Ein flexibles Fertigungssystem für die 3D-Laserbearbeitung bedeutet, ein System bereitzustellen, das eine Vielzahl von Laserprozessen unterstützen kann, d. h. Laserschweißen, Laserbohren und 3D-Laserschneiden“, erklärte Rickard. „Das System muss die Fertigungsanforderungen unterstützen und an die zukünftigen Anforderungen des Unternehmens anpassbar sein.“
Diese Anpassungsfähigkeit würde die Unterstützung umfassen für:
--Geringes Volumen heute und höheres Volumen in der Zukunft.
--Eine Reihe von Materialien, von Baustahl, Edelstahl und Aluminium bis hin zu Spezialmaterialien. Das Umschalten von einem Unterstützungsgas auf ein anderes über elektronische und programmgesteuerte Steuerung ist wichtig.
--Schneller Wechsel von einem Fertigungsprozess zum anderen – vom Schweißen zum Schneiden zum Bohren und umgekehrt. Er sagte beispielsweise:„LASERDYNE-Systeme können in ein bis zwei Minuten vom 3D-Laserschneiden zum 3D-Schweißen wechseln.“
Darüber hinaus, so riet er, muss ein laserbasiertes FMS Parameter- und Prozessinformationen in Echtzeit an Fertigungs-/Betriebsüberwachungssysteme liefern – und diese Informationen müssen auch aufgezeichnet und für zukünftige Referenzen und Analysen gespeichert werden.
„Aus unserer Sicht ist die Größe des Systems oder der Maschine unabhängig von der Flexibilität“, sagte Rickard. „Die Größe der Anlage wird durch die Teile bestimmt, die der Kunde laserbearbeiten wird. LASERDYNE-Systeme wurden entwickelt, um die Fertigungsflexibilität zu unterstützen, unabhängig davon, ob ein kleines oder großes System gekauft wird.“
Die neueste Ergänzung von Prima Power Laserdyne ist das LASERDYNE 811-System, das die flexible Fertigungsphilosophie auf verschiedene Weise unterstützt, erklärte Rickard.
„Erstens unterstützt dasselbe System einen Hersteller, der einen hohen Teilemix und ein geringes Volumen hat, oder einen Hersteller, der das System bestellt, um ein einzelnes Teil für mehrere Jahre zu bauen. Zweitens kann der Kunde die Automatisierung zum Zeitpunkt der Installation des Systems oder jederzeit in der Zukunft integrieren. Das System ist modular und anpassbar. Drittens kann das System ein eigenständiges Gerät oder ein integraler Bestandteil der Fertigungszelle sein.“
Das System war ein Segen für einen Kunden, einen Subunternehmer für die Automobil-, Lebensmittelverarbeitungs- und Haushaltswarenmärkte, sagte er. Dieser Kunde wollte seine Verarbeitungskapazität erweitern und die Teil-zu-Teil-Zeit für eine Vielzahl von 3D-Metallteilen und mehrere zylindrische Teile verkürzen. Außerdem wollte der Kunde die Umschaltzeit für die Teilehalterung reduzieren.
„Wir haben dem Kunden die LASERDYNE 811 mit einem Zwei-Positionen-Rundtisch [Drehtisch] zum Laserschneiden von 3D-Teilen zur Verfügung gestellt. Darüber hinaus haben wir eine gemeinsame Vorrichtungsschnittstelle bereitgestellt, damit der Bediener die Teilevorrichtungen auf dem Drehtisch einfach wechseln kann. Zur Unterstützung des zylindrischen Teils stellten wir einen Drehtisch bereit, der die gleiche Teilebefestigungsschnittstelle verwendete, sodass der Kunde den Drehtisch einfach hinzufügen und entfernen konnte. Das Hinzufügen des Drehtisches ist dasselbe wie das Hinzufügen und Entfernen der Teilehalterung.
„Das Ergebnis ist, dass der Kunde einen hohen SKU-Mix laserbearbeiten und die Teil-zu-Teil-Zykluszeiten verkürzen kann, was die Gesamtkosten senkte, den Werksdurchsatz erhöhte, die Teilevorlaufzeiten für Endverbraucher verkürzte und es dem Kunden ermöglichte, zu bleiben ohne Qualitätsverlust konkurrenzfähig.“
Rickard erklärte, wie entscheidend die Entwicklung des FMS für den Erfolg seines Unternehmens war.
„Prima Power Laserdyne war aus der Not heraus ein früher Pionier in der 3D-Laserbearbeitung. Um erfolgreich zu sein, mussten wir flexible Fertigungssysteme anbieten. In den Anfängen des Geschäfts war es sehr schwierig, eine Einwegmaschine zu verkaufen. Die Kunden bestanden darauf, dass die Systeme flexibel sein mussten. FMS ist sozusagen ein Kernstück unserer DNA.
„Im Laufe der Jahre begannen die Laserquellen des Systems bei CO2-Lasern und migrierten zu Nd:YAG-Systemen zu jetzt Faserlasersystemen. Mit jedem Wechsel der Laserquelle konnte eine höhere Anzahl an Materialien laserbearbeitet werden. Im Laufe der Zeit haben wir unsere Systeme entwickelt und verbessert, um das Schweißen, Bohren und Schneiden zu unterstützen, indem wir die Düse am Ende der optischen Laserkette wechseln.“
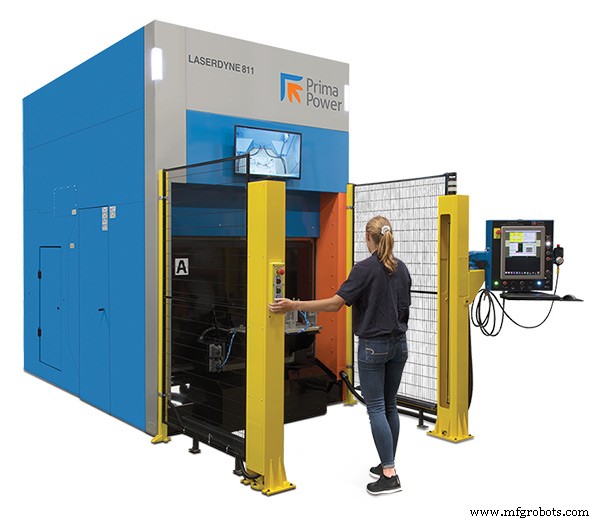
Eine weitere Änderung war die Einführung von SPC und MTConnect in die Systeme des Unternehmens. „Mit SPC kann der Hersteller alle Prozess- und Maschinenparameter zur Analyse oder Dokumentation aufzeichnen. Mit MTConnect kann der Hersteller die Parameter in Echtzeit streamen und so eine Echtzeit-Prozessüberwachung bereitstellen. Schließlich hat das System Echtzeitkontrolle über alle Aspekte der Maschine, einschließlich Puls-für-Puls-Steuerung des Lasers. Die Echtzeitsteuerung ermöglicht der Steuerung sieben oder mehr Achsen zu unterstützen und vereinfacht die Automatisierungsintegration mit LASERDYNE-Systemen.“
Letztendlich schloss er:„Der allgemeine Fertigungssektor und Auftragsfertiger sind führend, wenn es um die Definition und den Bedarf von FMS geht. Diese Kundengruppe benötigt die Möglichkeit, ihre Herstellungsprozesse anzupassen.
In der Regel unterstützt diese Gruppe eine Vielzahl von Produkten und Kunden. Der Lebensunterhalt und der Erfolg hängen davon ab, wie schnell und effizient sie sich an die Arbeit anpassen können, die der Markt bietet. Jeder Marktsektor hat einen Auf- und Ab-Zyklus. Wenn ein Marktsektor ausfällt, kann die Geschwindigkeit, mit der sich der Hersteller an den wachsenden Marktsektor anpassen kann, den Unterschied zwischen dem Wachstum des Unternehmens und der Aufgabe des Geschäfts ausmachen.“
Automatisierungssteuerung System
- Roboter bauen mit Raspberry Pi und Python
- Die 13 besten Smart-Home-Geräte und -Systeme des Jahres 2019
- Roboter, verträumte Unternehmen und die Zukunft der Arbeit
- Die 6G-Reise beginnt mit einem Knall (und einem Launch)
- Bewältigung der Fertigungsherausforderung mit Daten und KI
- Delaware:die perfekte Mischung aus Mensch und KI
- Die Zukunft des Testens:Automatisierung und kollaborative Roboter
- Werden Automatisierung und Roboter die Welt verändern?
- Kopplung von KI und Robotik mit mehreren Inspektionssystemen
- Beseitigung der Plackerei des Palettenrecyclings