16 wichtige Punkte zum Stempelprozess [praktische Erfahrung]
Das Stanzverfahren ist ein Umformverfahren, bei dem Blechen eine gewünschte Form gegeben wird. Der Stanzprozess kann verschiedene andere Blechoperationen wie Stanzen, Biegen, Stanzen, Scheren, Lochen usw. umfassen.
In diesem Artikel lernen wir verschiedene Aspekte des Blechstanzprozesses aus Shanes praktischer Erfahrung kennen.
1. Informationen aus Abfall
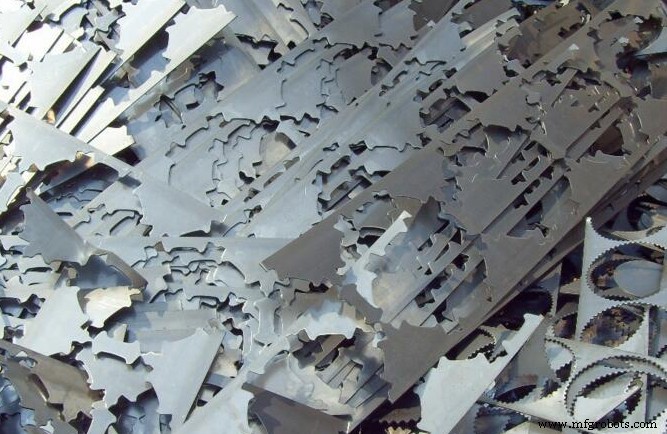
Schrott ist im Wesentlichen die Reflexion des gebildeten Lochs. Das ist das gleiche Teil in der entgegengesetzten Position. Anhand des Ausschusses können Sie beurteilen, ob der Spalt zwischen Ober- und Unterwerkzeug korrekt ist.
Wenn der Spalt zu groß ist, hat der Abfall raue und wellige Bruchflächen und eine schmale helle Zone. Je größer der Spalt, desto größer der Winkel zwischen der Bruchfläche und dem Bereich der hellen Zone.
Wenn der Spalt zu klein ist, zeigt der Abfall eine Bruchfläche mit kleinem Winkel und einen breiten hellen Bandbereich. Übermäßige Lücken bilden Löcher mit großen Locken und Kantenrissen, was zu einer leichten dünnen Kante führt, die aus dem Abschnitt herausragt.
Ein zu kleiner Spalt bildet ein Band mit leichter Kräuselung und großem Winkelriss, was zu einem Schnitt führt, der mehr oder weniger senkrecht zur Materialoberfläche verläuft.
Ein idealer Abfall sollte einen vernünftigen Kollapswinkel und ein gleichförmiges helles Band haben. Dadurch wird der Stanzdruck gering gehalten und ein sauberes rundes Loch mit wenig Grat entsteht.
Aus dieser Sicht steht die Vergrößerung des Spalts zur Verlängerung der Lebensdauer der Matrize im Austausch für die Qualität des fertigen Lochs.
2. Auswahl des Schneidspalts
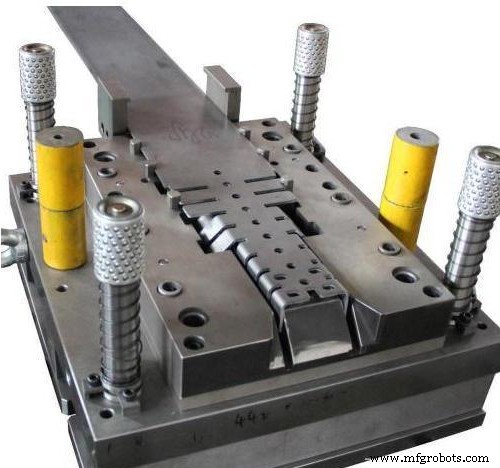
Das Spiel der Matrize hängt von der Art und Dicke des zu stanzenden Materials ab. Eine unangemessene Freigabe kann die folgenden Probleme verursachen:
(1) Wenn der Spalt zu groß ist, ist der Grat des gestanzten Werkstücks relativ groß und die Stanzqualität ist schlecht.
Wenn der Abstand zu klein ist, obwohl die Stanzqualität gut ist, ist der Verschleiß der Matrize stark, was die Lebensdauer der Matrize stark verringert und leicht zum Brechen des Stempels führen kann.
(2) Wenn der Spalt zu groß oder zu klein ist, kann leicht eine Haftung auf dem Stanzmaterial erzeugt werden, was zu einer Biegung des Materials während des Stanzens führt.
Bei einem zu kleinen Spalt kann leicht ein Vakuum zwischen der Unterseite des Stempels und dem Blech entstehen, was zu einem Rückprall des Abfalls führt.
(3) Angemessener Abstand kann die Lebensdauer der Matrize verlängern, einen guten Entlastungseffekt haben, Grat und Bördeln reduzieren, die Platte sauber halten, der Lochdurchmesser ist konstant und wird die Platte nicht zerkratzen, die Schleifzeiten verkürzen, halten Platte gerade und genaue Stanzpositionierung.
Bitte beachten Sie die folgende Tabelle, um das Formspiel auszuwählen (die Daten in der Tabelle sind in Prozent)
Auswahl des Abstands (Gesamtabstand) | |||
Materialwissenschaft | Minimum | Am besten | Maximal |
Rotes Kupfer | 8 % | 12 % | 16 % |
Messing | 6 % | 11 % | 16 % |
Baustahl | 10 % | 15 % | 20 % |
Aluminium (weich) | 5 % | 10 % | 15 % |
Edelstahl | 15 % | 20 % | 25 % |
% × Materialstärke =Stanzabstand |
3. So verbessern Sie die Standzeit der Matrize
Für Benutzer kann die Verbesserung der Lebensdauer der Matrize die Stanzkosten erheblich reduzieren.
Die Faktoren, die die Lebensdauer der Matrize beeinflussen, sind wie folgt:
- Art und Dicke des Materials;
- Ob ein angemessener unterer Werkzeugabstand ausgewählt ist
- Strukturform von Schimmelpilzen
- Ob es beim Materialstanzen eine gute Schmierung gibt
- Ob die Form einer speziellen Oberflächenbehandlung unterzogen wurde
- Wie Titanplattierung, Kohlenstofftitannitrid
- Ausrichtung der oberen und unteren Türme
- Angemessene Verwendung der Einstelldichtung
- Ob die Schrägkantenmatrize richtig verwendet wird
- Ob die Werkzeugbasis der Werkzeugmaschine abgenutzt ist
4. Probleme, die beim Stanzen von Löchern in Sondergröße beachtet werden müssen
- Wenn der minimale Lochdurchmesser im Bereich von φ0,8–φ1,6 liegt, verwenden Sie einen speziellen Stempel.
- Wenn Sie eine dicke Platte stanzen, verwenden Sie bitte eine größere Matrize im Verhältnis zum Bearbeitungslochdurchmesser.
Beispiel 1. Gemäß den Verarbeitungsbedingungen in der folgenden Tabelle, obwohl die Verarbeitungsöffnung der Matrize in Station A entspricht, verwenden Sie bitte die Matrize in Station B.
Textur des Materials | Plattendicke (mm) | Öffnung (mm) |
Baustahl (40kg/mm 2 ) | 6.0 | 8.2-12.7 |
Edelstahl (60kg/mm 2 ) | 4.0 | 8.2-12.7 |
Beispiel 2. Verwenden Sie gemäß den Verarbeitungsbedingungen in der folgenden Tabelle, obwohl die Verarbeitungsöffnung der Matrize der B-Station entspricht, bitte die Matrize der C-Station.
Textur des Materials | Plattendicke (mm) | Öffnung (mm) |
Baustahl (40kg/mm 2 ) | 6.0 | 22.9-31.7 |
Edelstahl (60kg/mm 2 ) | 4.0 | 22.9-31.7 |
(3) Generell darf das Verhältnis der Mindestbreite zur Länge der Stempelkante 1:10 nicht unterschreiten.
Beispiel 3. Für einen rechteckigen Stempel ist bei einer Schneidkantenlänge von 80 mm eine Schneidkantenbreite von ≥ 8 mm am besten geeignet.
(4) Das Verhältnis zwischen der Mindestabmessung der Stempelkante und der Blechdicke.
Es wird empfohlen, dass die Mindestabmessung der Stempelkante das Zweifache der Blechdicke betragen sollte.
5. Gesenkschleifen
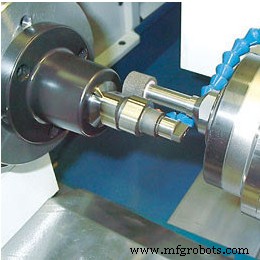
1. Bedeutung des Werkzeugschleifens
Regelmäßiges Schleifen der Matrize ist die Garantie für eine gleichbleibende Stanzqualität.
Regelmäßiges Schleifen der Matrize kann nicht nur die Lebensdauer der Matrize, sondern auch die Lebensdauer der Maschine verbessern. Es ist notwendig, die richtige Mahldauer zu erfassen.
2. Die spezifischen Eigenschaften der Matrize müssen geschärft werden
Beim Werkzeugschleifen gibt es keine strenge Anzahl von Schlägen, um festzustellen, ob Schleifen erforderlich ist.
Es hängt hauptsächlich von der Schärfe der Kante ab.
Es wird hauptsächlich durch die folgenden drei Faktoren bestimmt:
(1) Überprüfen Sie die Verrundung der Schneidkante. Wenn der Verrundungsradius R0,1 mm erreicht (der maximale R-Wert darf 0,25 mm nicht überschreiten), ist Schleifen erforderlich.
(2) Überprüfen Sie die Stanzqualität und ob große Grate vorhanden sind?
(3) Bestimmen Sie, ob Schleifen aufgrund des Maschinengeräusches erforderlich ist.
Wenn das Geräusch derselben Matrize während des Stanzens ungewöhnlich ist, weist dies darauf hin, dass der Stempel stumpf geworden ist und geschliffen werden muss.
Hinweis:Das Schleifen sollte auch in Betracht gezogen werden, wenn die Schneidkante rund oder die Rückseite der Schneidkante rau ist.
3. Schleifverfahren
Es gibt viele Möglichkeiten, die Matrize zu schleifen, was durch eine spezielle Schleifmaschine oder Hobelschleifmaschine realisiert werden kann.
Die Schleiffrequenz von Stempel und Untergesenk beträgt generell 4:1; Bitte passen Sie die Matrizenhöhe nach dem Schleifen an.
(1) Gefahren falscher Mahlmethoden:
Falsches Schleifen verschlimmert die schnelle Beschädigung der Matrizenkante, was zu einer erheblichen Verringerung der Anzahl der Schläge pro Schleifen führt.
(2) Vorteile der richtigen Schleifmethode:
Die Qualität und Genauigkeit des Stanzens kann durch regelmäßiges Schleifen der Matrize stabil gehalten werden.
Die Schneide der Matrize wird langsam beschädigt und hat eine längere Lebensdauer.
4. Schleifregeln
Beim Werkzeugschleifen sind folgende Faktoren zu berücksichtigen:
(1) Wenn die Kantenverrundung R0,1–0,25 mm beträgt, hängt dies von der Schärfe der Kante ab.
(2) Die Oberfläche der Schleifscheibe ist zu reinigen.
(3) Eine lockere, grobe und weiche Schleifscheibe wird empfohlen. Wie WA46KV.
(4) Der Schleifbetrag (Schnittbetrag) darf jedes Mal 0,013 mm nicht überschreiten.
Die übermäßige Schleifmenge führt zu einer Überhitzung der Werkzeugoberfläche, was einer Glühbehandlung entspricht, wodurch das Werkzeug weicher wird und die Lebensdauer des Werkzeugs stark verkürzt wird.
(5) Beim Schleifen muss ausreichend Kühlmittel zugeführt werden.
(6) Während des Schleifens müssen der Stempel und die untere Matrize stabil befestigt und spezielle Werkzeugvorrichtungen verwendet werden.
(7) Die Schleifmenge der Matrize ist sicher. Wenn dieser Wert erreicht wird, wird der Stempel verschrottet.
Wenn Sie es weiterhin verwenden, können Form und Maschine leicht beschädigt werden, und der Gewinn ist den Verlust nicht wert.
(8) Nach dem Schleifen muss die Kante mit Ölstein behandelt werden, um übermäßig scharfe Kanten und Linien zu entfernen.
(9) Nach dem Schleifen ist die Klinge zu reinigen, zu entmagnetisieren und zu ölen.
Hinweis:Die Schleifmenge der Matrize hängt hauptsächlich von der Dicke der gestanzten Platte ab.
6. Achten Sie vor Gebrauch auf den Stempel
1. Speichern
(1) Wischen Sie die Innen- und Außenseite der oberen Formhülse mit einem sauberen Tuch ab.
(2) Achten Sie bei der Lagerung darauf, die Oberfläche nicht zu zerkratzen oder zu verbeulen.
(3) Öl zum Schutz vor Rost.
2. Vorbereitung vor Gebrauch
(1) Obere Matrizenhülse vor Gebrauch gründlich reinigen.
(2) Überprüfen Sie die Oberfläche auf Kratzer und Dellen. Entfernen Sie sie gegebenenfalls mit einem Ölstein.
(3) Innen und außen ölen.
3. Vorsichtsmaßnahmen beim Installieren des Stempels an der oberen Matrizenhülse
(1) Reinigen Sie den Stempel und ölen Sie seinen langen Griff.
(2) Setzen Sie den Stempel ohne Kraftaufwand unten in die obere Matrizenhülse der großen Stationsmatrize ein.
Ein Nylonhammer kann nicht verwendet werden.
Beim Einbau kann der Stempel nicht durch Anziehen der Schrauben an der oberen Matrizenhülse fixiert werden. Die Schrauben können erst angezogen werden, nachdem der Stempel richtig positioniert ist.
4. Bauen Sie die obere Formbaugruppe in den Revolver ein
Wenn Sie die Lebensdauer der Matrize verlängern möchten, sollte der Spalt zwischen dem Außendurchmesser der oberen Matrizenhülse und der Revolverbohrung so gering wie möglich sein.
Führen Sie daher die folgenden Verfahren sorgfältig durch.
(1) Keilnut und Innendurchmesser der Revolverbohrung reinigen und ölen.
(2) Passen Sie die Keilnut der oberen Werkzeugführungshülse an, damit sie mit der Keilnut der Revolverkopfbohrung übereinstimmt.
(3) Führen Sie die obere Formhülse gerade in das Turmloch ein und achten Sie darauf, dass sie nicht kippt.
Die obere Matrizenführungshülse sollte durch ihr Eigengewicht in die Revolverbohrung gleiten.
(4) Wenn die obere Matrizenhülse zu einer Seite kippt, kann sie mit weichen Materialwerkzeugen, wie z. B. einem Nylonhammer, leicht nach rechts geklopft werden.
Wiederholen Sie das Klopfen, bis die obere Matrizenführungshülse durch ihr Eigengewicht in die richtige Position gleitet.
Hinweis:Kraft nicht auf den Außendurchmesser der Führungshülse des Oberwerkzeugs, sondern nur auf die Oberkante des Stempels aufbringen.
Schlagen Sie nicht auf die Oberseite der oberen Matrizenhülse, um eine Beschädigung der Revolverkopfbohrung und eine Verkürzung der Lebensdauer einzelner Stationen zu vermeiden.
6. Schimmelpflege
Wenn der Stempel durch das Material gebissen ist und nicht herausgenommen werden kann, überprüfen Sie bitte gemäß den folgenden Punkten.
1. Nachschleifen von Stempel und Unterteil.
Die Matrize mit scharfer Kante kann schöne Schneidabschnitte bearbeiten. Bei stumpfer Kante ist zusätzlicher Stanzdruck erforderlich. Darüber hinaus ist der Werkstückabschnitt rau, was zu einem großen Widerstand führt, wodurch der Stempel vom Material gebissen wird.
2. Werkzeugabstand.
Wenn das Spiel der Matrize im Verhältnis zur Plattendicke nicht richtig gewählt ist, benötigt der Stempel eine große Entformungskraft, wenn er vom Material getrennt wird.
Wenn der Stempel aus diesem Grund vom Material erfasst wird, ersetzen Sie bitte das untere Gesenk mit angemessenem Abstand.
3. Status verarbeiteter Materialien.
Wenn das Material verschmutzt oder verschmutzt ist, haftet der Schmutz an der Matrize, so dass der Stempel vom Material gebissen wird und nicht bearbeitet werden kann.
4. Verformtes Material.
Nach dem Stanzen des Lochs klemmt das verzogene Material den Stempel und lässt den Stempel beißen.
Materialien mit Verzug sind vor der Verarbeitung zu richten.
5. Übermäßiger Einsatz von Federn.
Verursacht Frühjahrsmüdigkeit. Bitte überprüfen Sie immer die Leistung der Feder.
7. Ölen
Die Ölmenge und die Anzahl der Öleinspritzungen hängen von den Bedingungen der Verarbeitungsmaterialien ab.
Bei rost- und zunderfreien Materialien wie kaltgewalzten Stahlplatten und korrosionsbeständigen Stahlplatten muss das Öl in die Form eingespritzt werden.
Die Öleinspritzpunkte sind die Führungsbuchse, die Öleinspritzöffnung, die Kontaktfläche zwischen dem Messerkörper und der Führungsbuchse, das untere Werkzeug usw. Verwenden Sie leichtes Motoröl als Öl.
Bei Materialien mit Rost und Zunder wird das Rostpulver während der Bearbeitung zwischen Stempel und Führungshülse gesaugt, wodurch der Schmutz entsteht, sodass der Stempel nicht frei in der Führungshülse gleiten kann.
Wenn Sie in diesem Fall Öl auftragen, haftet der Rost leichter daran.
Wischen Sie daher beim Spülen dieses Materials im Gegenteil das Öl ab, zersetzen Sie es einmal im Monat und entfernen Sie den Schmutz des Stempels und der unteren Matrize mit Dampföl (Brennholz).
Dadurch kann sichergestellt werden, dass die Form eine gute Schmierleistung aufweist.
8. Häufige Probleme und Lösungen im Prozess der Schimmelpilznutzung
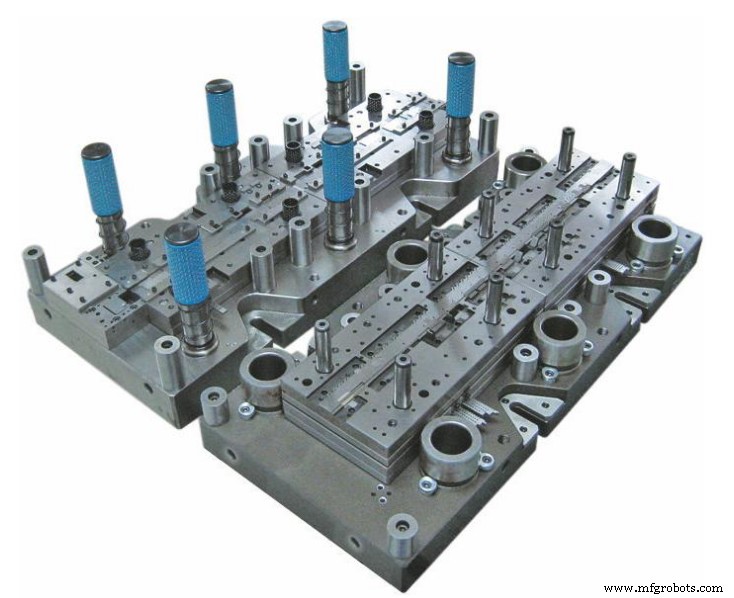
Problem 1:Die Platte löst sich aus dem Kiefer
Grund | Auflösend |
Unvollständiges Entladen der Form | 1. Verwenden Sie einen Schlag mit einer Neigung |
2. Gleitmittel auf die Platte auftragen | |
3. Hochleistungsmatrize wird angenommen |
Problem 2:Starker Matrizenverschleiß
Grund | Auflösend |
Unangemessener Würfelabstand (zu klein) | Matrizenabstand erhöhen |
Fehlausrichtung der oberen und unteren Matrizensitze | 1. Stationseinstellung und Ausrichtung von Ober- und Unterwerkzeug2. Revolverhöheneinstellung |
Die verschlissenen Matrizenführungskomponenten und Revolvereinsätze wurden nicht rechtzeitig ausgetauscht | Ersetzen |
Überhitzung des Stempels | 1. Gleitmittel auf die Platte auftragen2. Für Schmierung zwischen Stempel und Unterwerkzeug sorgen3. Im selben Programm werden mehrere Formensätze mit derselben Spezifikation und Größe verwendet |
Die unsachgemäße Schleifmethode führt zum Ausglühen der Matrize, was den Verschleiß verschlimmert | 1. Weiche Schleifscheibe2. Reinigen Sie die Schleifscheibe regelmäßig3. Kleiner Biss4. Ausreichend Kühlmittel |
Stufenstanzen | 1. Erhöhen Sie die Schrittweite2. Bridge-Stepping wird übernommen |
Problem 3:Stempelband und Stempelhaftung
Grund | Auflösend |
Unangemessener Würfelabstand (zu klein) | Matrizenabstand erhöhen |
Stanzkantenpassivierung | Zeitgerechtes Schleifen |
Schlechte Schmierung | Schmierbedingungen verbessern |
Problem 4:Rückprall von Abfall
Grund | Auflösend |
Unteres Modulproblem | Verwenden Sie kugelsicheres Material, um die Form abzusenken |
Bei Bohrungen mit kleinem Durchmesser verringert sich das Spiel um 10 % | |
Durchmesser größer als 50,00 mm, Spalt vergrößert | |
Kratzer werden auf der Kantenseite des Würfels hinzugefügt | |
Punsch | Die Tiefe erhöhen |
Installieren Sie die Auswurfleiste aus Polyurethan | |
Schräge Schnittkante annehmen |
Problem 5:Schwieriges Entladen
Grund | Auflösend |
Unangemessener Würfelabstand (zu klein) | Matrizenabstand erhöhen |
Lochverschleiß | Zeitgerechtes Schleifen |
Frühlingsmüdigkeit | Ersetzen Sie die Feder |
Stanzhaftung | Haftung entfernen |
Frage 6:Stampfgeräusch
Grund | Auflösend |
Schwierigkeiten beim Entladen | Erhöhen Sie das Spiel der unteren Matrize und sorgen Sie für eine gute Schmierung |
Ausstoßkraft erhöhen | |
Auslaufplatte mit weicher Oberfläche | |
Es gibt ein Problem mit der Auflage des Blechs auf der Werkbank und im Revolver | Kugelförmige Stützmatrize |
Arbeitsgröße reduzieren | |
Arbeitsdicke erhöhen | |
Blechdicke | Stanze für schräge Kanten verwenden |
9. Vorsichtsmaßnahmen für die Verwendung von speziellen Umformwerkzeugen
1. Der Hub des Gleitblocks verschiedener Maschinenmodelle ist unterschiedlich, achten Sie daher auf die Einstellung der Schließhöhe des Formwerkzeugs.
2. Es muss sichergestellt sein, dass die Leiste ausreichend ist, also muss sie sorgfältig angepasst werden. Es ist am besten, jedes Mal 0,15 mm nicht zu überschreiten.
Wenn die Einstellung zu groß ist, können Maschine und Form leicht beschädigt werden.
3. Beim Streckziehen wählen Sie bitte eine leichte Federanordnung, um ein Reißen des Blechs oder ein schwieriges Entladen durch ungleichmäßige Verformung zu verhindern.
4. Installieren Sie eine Kugelstützform um die Formform herum, um ein Kippen der Platte zu verhindern.
5. Die Umformposition sollte so weit wie möglich von der Klammer entfernt sein.
6. Die Formgebung erfolgt am besten am Ende des Verarbeitungsprogramms.
7. Achten Sie auf eine gute Schmierung der Platte.
8. Achten Sie bei der Bestellung auf die Ausbringung von Sonderumformwerkzeugen. Wenn der Abstand zwischen den beiden Formationen gering ist, wenden Sie sich bitte unbedingt an den Verkäufer unseres Unternehmens.
9. Da das Umformwerkzeug eine lange Entladezeit benötigt, muss die niedrige Geschwindigkeit während des Umformvorgangs angenommen werden, und es ist am besten, eine Verzögerung zu haben.
10. Vorsichtsmaßnahmen für die Verwendung eines Rechteckschneiders
1. Der Schrittabstand soll so groß wie möglich sein und größer als 80 % der gesamten Werkzeuglänge sein.
2. Den Sprungschritt am besten durch Programmierung realisieren.
3. Es wird empfohlen, eine schräge Schneide zu verwenden.
12. Wie kann man stanzen, ohne die Nennkraft der Maschine zu überschreiten?
Runde Löcher mit einem Durchmesser von mehr als 114,3 mm müssen im Produktionsprozess gestanzt werden.
Ein solch großes Loch wird die Obergrenze der Nennkraft der Maschine überschreiten, insbesondere bei Materialien mit hoher Scherfestigkeit.
Dieses Problem kann gelöst werden, indem große Löcher durch mehrere Stanzmethoden gestanzt werden.
Das Schneiden entlang des Umfangs eines großen Kreises mit einer kleinen Matrize kann die Stanzkraft um die Hälfte oder mehr reduzieren. Die meisten Matrizen, die Sie bereits haben, können dies tun.
11. Eine einfache Methode zum Stanzen großer runder Löcher
Die Form dieser konvexen Linse kann in der gewünschten Radiusgröße hergestellt werden.
Übersteigt der Lochdurchmesser die Nennkraft des Stempels, empfehlen wir Schema (A).
Verwenden Sie diese Matrize, um den Umfang des Kreises auszustanzen.
Wenn der Lochdurchmesser innerhalb des Nennkraftbereichs des Stempels gestanzt werden kann, kann eine radiale Matrize und eine konvexe Linsenmatrize das erforderliche Loch viermal stanzen, ohne die Matrize zu drehen (B).
12. Schließlich wird es nach unten geformt
Bei der Auswahl des Umformwerkzeugs sollte die Abwärtsumformung vermieden werden, da sie zu viel vertikalen Platz beansprucht und zu zusätzlichen Blechricht- oder Biegevorgängen führt.
Abwärtsformteile können auch in das Unterwerkzeug fallen und dann aus dem Revolver herausgezogen werden.
Wenn jedoch die Abwärtsumformung die einzige Prozessoption ist, sollte sie als letzter Schritt in der Blechbearbeitung betrachtet werden.
13. Materialverzug verhindern
Wenn Sie eine große Anzahl von Löchern in die Platte stanzen müssen und die Platte nicht flach bleiben kann, kann die Ursache die Ansammlung von Stanzspannungen sein.
Beim Stanzen eines Lochs wird das Material um das Loch herum nach unten gedehnt, wodurch die Zugspannung auf der oberen Oberfläche der Platte erhöht wird.
Die Abwärtsbewegung führt auch zu einer Erhöhung der Druckspannung auf der unteren Oberfläche der Platte.
Beim Stanzen einer kleinen Anzahl von Löchern ist das Ergebnis nicht offensichtlich, aber mit zunehmender Anzahl von Stanzlöchern steigen auch die Zugspannung und die Druckspannung exponentiell an, bis sich die Platte verformt.
Eine Möglichkeit, diese Verformung zu beseitigen, ist:
Stanzen Sie jedes zweite Loch und kehren Sie dann zurück, um die restlichen Löcher zu stanzen.
Dies erzeugt zwar die gleiche Spannung auf der Platte, löst aber die Anhäufung von Zug-/Druckspannungen auf, die durch aufeinander folgendes Stanzen in die gleiche Richtung verursacht werden.
Auf diese Weise teilt die erste Lochreihe den Verformungseffekt der zweiten Lochreihe.
14. Wenn Ihre Edelstahlbördelung verformt ist
Tragen Sie vor dem Bördeln hochwertiges Umformschmiermittel auf das Material auf, das das Material besser von der Matrize trennen und sich während des Umformens reibungslos auf der unteren Matrize bewegen kann.
Dadurch kann das Material die beim Biegen und Dehnen entstehende Spannung besser verteilen, um die Verformung am Rand des sich bildenden Bördellochs und den Verschleiß am Boden des Bördellochs zu verhindern.
15. Vorschläge zur Überwindung von Entladeschwierigkeiten
1. Verwenden Sie einen Stempel mit feinen Gummipartikeln.
2. Erhöhen Sie das Spiel der unteren Matrize.
3. Überprüfen Sie die Ermüdung der Feder.
4. Verwenden Sie eine Hochleistungsmatrize.
5. Geeignete Verwendung von schrägen Schneidwerkzeugen.
6. Schmieren Sie die Platte.
7. Für große Stationsdüsen muss ein Polyurethan-Auslasskopf installiert werden.
16. Hauptursachen für Abfallrebound
1. Die Schärfe der Schneide. Je größer die Verrundung der Schneidkante, desto einfacher ist es, Abfallrückprall zu verursachen.
2. Die Eintrittsmodul. Beim Prägen des Stempels an jeder Station sind die Anforderungen an den Eintrittsmodul sicher. Der Eintrittsmodul ist klein, was leicht zu Abfallrückprall führen kann.
3. Ob der Spielraum des Werkzeugs angemessen ist. Ein unangemessener Werkzeugabstand kann leicht zu einem Rückprall des Abfalls führen.
4. Ob sich auf der Oberfläche der verarbeiteten Platte ein Ölfleck befindet.
Sie müssen jedoch routinemäßige und regelmäßige Wartungsarbeiten durchführen, um sicherzustellen, dass die Kühlmittel und die Zufuhrsysteme den Erwartungen entsprechen.
Dies ist ein Gastbeitrag von Shane Vom MachineMfg-Team
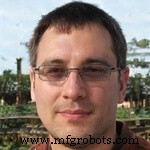
Shane ist seit mehr als 5 Jahren in der Maschinenbaubranche tätig. Er liebt das Schreiben und konzentriert sich darauf, technische Informationen, Anleitungen, detaillierte Lösungen und Gedanken zu Metallen und Metallbearbeitung auszutauschen. Durch seine Artikel können Benutzer verwandte Probleme immer leicht lösen und finden, was sie suchen.
Industrietechnik
- 5 lustige Fakten über Druckguss
- Prozessverbesserung:Der Schlüssel zu langfristigen Personalzuwächsen
- Präzisions-Metallstanzen:Alles darüber wissen
- Temperaturkontrolle und -beeinflussung während des Druckgussverfahrens
- Was ist der Unterschied zwischen Schmieden, Stanzen und Gießen?
- Folgeschnitt- vs. Transferstanzen
- Thyristor vs. Transistor:Wichtige Punkte zur Unterscheidung der beiden
- Was ist ein Folgeverbund-Stanzwerkzeug?
- Die Bedeutung des Stanzspiels beim Stanzen
- Informieren Sie sich über den BGA-Überarbeitungs- und Reparaturprozess