Vollständige Chip-Kontrolle
OIL-S-XPF Formgewindebohrer ermöglicht stabiles und spanfreies Gewindebohren in der Zylinderkolbenfertigung
Mark Coryea | OSG USA
Das Einsparen von ein paar Sekunden mag zunächst nicht nach viel klingen, aber wenn Sie über 1 Million Teile pro Jahr herstellen, zählt jede Sekunde. Überlegen Sie, was eine Einsparung von 10 Sekunden pro Teil, eine Reduzierung der Ausschussrate, eine Verkürzung der Endmontagezeit und eine dreifache Werkzeuglebensdauer bewirken könnten! Dies ist eine Realität für Flickinger Industries, ein Vertragsbearbeitungs- und Fertigungsunternehmen in Fort Wayne, Indiana, USA.
Flickinger Industries wurde 1960 in Fort Wayne gegründet und belieferte hauptsächlich die Pumpen- und Pneumatik-/Hydraulikzylinderindustrie. Heute ist Flickinger Industries mit 45 Vollzeitmitarbeitern immer noch führend in diesen Branchen und bedient gleichzeitig Kunden in den Bereichen Landwirtschaft, Automobil und Medizin. Im Laufe der Jahre hat sich das Personal von Flickinger Industries mit schnellen Umstellungen vertraut gemacht. Die Bearbeitung von Kleinserienteilen hat sich zu einer der Spezialitäten des Unternehmens entwickelt. Durch die Nutzung seiner hochmodernen 75.000 Quadratfuß großen Anlage zusammen mit 23 modernen CNC-Drehmaschinen und vertikalen CAT40-Bearbeitungszentren kann Flickinger Industries mühelos Auflagen von zwei bis 200.000 Stück bewältigen.
Einer der größeren Kunden von Flickinger Industries ist ein bekannter, weltweit führender Anbieter von Bewegungs- und Steuerungstechnologien. Das Unternehmen produziert Aluminium-Luftzylinderkolben in Größen von ½″ Durchmesser bis 3″ Durchmesser und in Losgrößen von typischerweise 2.000 bis 5.000 Stück – insgesamt über 1 Million Kolben pro Jahr. Die Teile sind aus T356-Aluminiumstangenmaterial gefertigt und jeder Kolben hat ein Mittelloch mit Gewinde. Die Gewindeoberfläche muss frei von Schlieren und Graten sein, die die Montage behindern würden. Das Gewindeschneiden des Mittellochs ist eine Herausforderung, da das Werkzeug stationär ist, während sich das Teil dreht. Flickinger Industries verwendete viele Jahre lang einen geschnittenen Gewindebohrer eines Mitbewerbers und gewöhnte sich an den periodischen katastrophalen Bruch des Gewindebohrers, der bei lang absplitternden Materialien wie Aluminium auftritt.
Anfang 2019 beschädigte ein Bruch einen Revolver einer Drehmaschine, was zu übermäßigen Ausfallzeiten und kostspieligen Reparaturen führte. Zu dieser Zeit besuchte ich Flickinger Industries mit einem Händler und diskutierte die Probleme, die durch die fehlende Chipkontrolle verursacht wurden. Das damals verwendete Werkzeug war ein 5/16″-24-Schnitt-Gewindebohrer eines Wettbewerbers in blanker Oberfläche, spiralgenutet mit modifizierter Bodenfase in der Passungsklasse 2B. Ich zeigte die Formgewindebohrerserie XPF von Flickinger Industries OSG und erklärte, wie Probleme mit der Spankontrolle durch die Verwendung von Formgewindebohrern der Vergangenheit angehören würden, etwas, von dem das Unternehmen wusste, aber nie gedacht hatte, dass es dieses Problem lösen würde.
Da ein Gewindebohrer durch plastische Verformung des Arbeitsmaterials Gewinde formt, entstehen keine Schneidspäne. Ohne Schneidspäne können Probleme bei der Spanabfuhr vollständig vermieden werden. Der XPF ist der Hochleistungs-Formgewindebohrer von OSG, der keine Späne produziert und für die Bearbeitung von Materialien bis zu 35 HRC optimiert ist. Es ist einzigartig mit einem Design mit niedrigem Drehmoment konstruiert, um eine längere Lebensdauer bei höheren Geschwindigkeiten zu ermöglichen. Seine V-Beschichtung ermöglicht zudem eine extreme Verschleißfestigkeit. Der XPF ist mit oder ohne Kühlmittelbohrungen und in Standard- oder Langschaftausführung erhältlich.
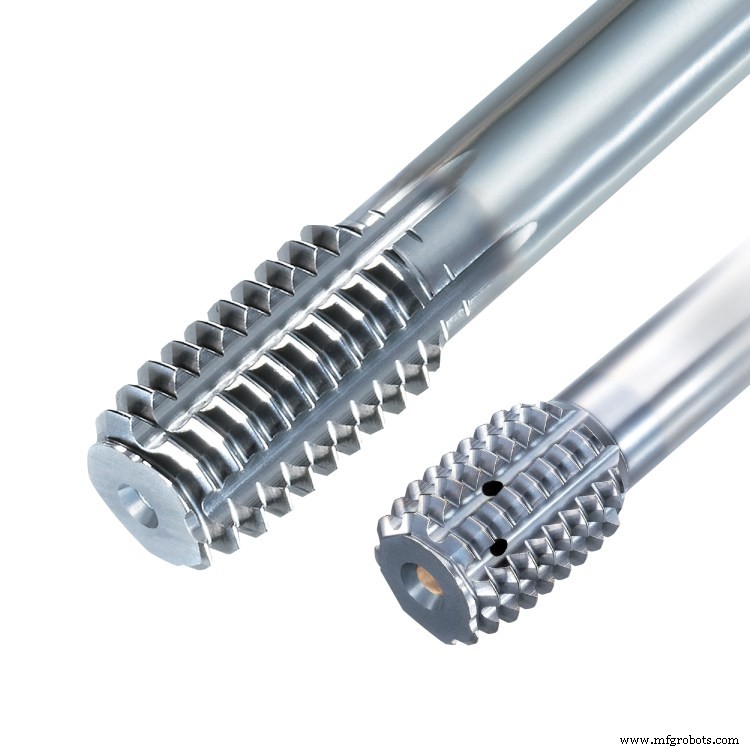
Nach einer ausführlichen Bewertung der Anwendung bot ich an, ein Testwerkzeug des Ölhahns OIL-S-XPF im Rahmen der garantierten Probebestellung von OSG USA mitzubringen. Der XPF-Tap war eine meiner stärksten Waffen gegen die Konkurrenz. Es hat bei mehreren Materialien den Sieg errungen und sich gegen jeden namhaften Hersteller auf dem Markt durchgesetzt. Für die Bearbeitung verwendet Flickinger Industries eine Mori Seiki SL-Drehmaschine und WSO-Emulsionskühlmittel mit 12 Prozent. Wie erwartet war der Prozess ein großer Erfolg. Innerhalb der ersten 10 Minuten kommentierte der Bediener „Das ist doppelt so schnell wie der alte Wasserhahn!“
Der geschnittene Gewindebohrer des Wettbewerbers benötigte ungefähr 20 Sekunden pro Teil, während der XPF-Formgewindebohrer nur 10 Sekunden benötigte. Während regelmäßiger Stichprobenkontrollen für Flankendurchmesser und Gewindeoberfläche lagen alle gut innerhalb der optimalen Spezifikationen. Die normale Standzeit für den vorherigen Gewindebohrer des Wettbewerbers betrug 3.000 Stück, was der XPF mit Leichtigkeit erreichte und übertraf. Tom Schroeder, Werksleiter von Flickinger Industries, sagte, er sei „von XPF begeistert, da wir so viel Zeit pro Teil sparen.“
Der erste Test-Gewindebohrer fertigte über 14.000 Stück, bevor ein leichtes Festfressen des Gewindes beobachtet wurde, aber das Werkzeug konnte weiterhin verwendet werden. Der zweite Test verlief genauso gut wie der erste, und die nächste Frage von Flickinger Industries lautete:„Stellt OSG den XPF in ½″-20 und 7/16″-20 Gewindegrößen her?“ Und die Antwort lautet „Ja, das tun wir!“
Die Standzeit für das OIL-S-XPF ist jetzt standardmäßig auf 10.000 Stück festgelegt, obwohl Tests gezeigt haben, dass sie weiter gehen könnten. Dennoch sanken die Kosten pro Einheit von 0,017 $ auf 0,006 $ pro Teil, was geschätzte jährliche Kosteneinsparungen von 37.775 $ ermöglichte. Ich bin stolz sagen zu können, dass heute jeder bei Flickinger Industries hergestellte Aluminiumkolben Gewindebohrer aus der XPF-Serie von OSG verwendet. Durch den Einsatz der XPF-Formgewindebohrer von OSG ist Flickinger Industries in der Lage, Probleme bei der Spankontrolle zu lösen, Brüche zu reduzieren und zukünftige Maschinenschäden zu vermeiden, um die Leistung zu maximieren.
Zuvor im OSG-Blog vorgestellt.
Industrietechnik
- Motorsteuerkreise
- Steuerkreise
- Vollständige Terahertz-Polarisationskontrolle mit erweiterter Bandbreite über dielektrische Metaoberflächen
- Optimierung des Bedienfelds für Industriemaschinen
- Eine vollständige Anleitung zum Schweißen von Edelstahl
- So löten Sie Aluminium – Eine vollständige Anleitung
- 8 wichtige Tipps zur Verbesserung der Spankontrolle beim Bohren
- Cloud-Überwachung, ein Fernsteuerungssystem
- 5 Vorteile der Fernsteuerung der Produktion
- Java-Anwendung auf PLCnext Control