Maschinenzustandsüberwachung hält eine Fabrik am Laufen
1901 erhielt Ransom E. Olds ein Patent für die Idee eines sich kontinuierlich bewegenden Fließbands, mit dem er die ersten Oldsmobile-Fahrzeuge baute. 1913 verbesserte Henry Ford das Konzept, indem er bewegliche Förderbänder hinzufügte, und mit diesen beiden Innovationen sank die Zeit, die zum Zusammenbau eines Autos benötigt wurde, von 1½ Tagen auf 1½ Stunden. Die moderne Montagefabrik war geboren.
In den nächsten vier Jahrzehnten wurde die Idee einer sich bewegenden Produktionslinie von zahlreichen Branchen übernommen, von Radios bis Rasierern, Uhren bis Krippen, Nägeln bis Zeitungen. Während des Zweiten Weltkriegs bauten die USA 300.000 Flugzeuge mit fahrenden Produktionslinien. Die Idee wurde zum Rückgrat der Fertigung auf der ganzen Welt und bleibt der wichtigste Weg, um Produkte für Massenmärkte bereitzustellen.
Die Werkzeuge und Maschinen, die für die Montagearbeiten verwendet werden, sind der kritischste Teil jeder Linie. In den 1950er Jahren wurde die Zuverlässigkeit von Fabrikanlagen zu einem wichtigen Bestandteil des Betriebs. Wenn eine einzelne Maschine nicht mehr funktionierte, wurde die gesamte Linie stillgelegt, bis Reparaturen durchgeführt werden konnten. Ungenutzte Maschinen und Monteure verringerten die Effizienz und wirkten sich auf die Kosten aus. Wartung wurde wichtig.
In der letzten Hälfte des 20. Jahrhunderts bestanden die meisten Werkswartungen aus planmäßigen regelmäßigen Wartungsarbeiten. Dies verbesserte die Zuverlässigkeit und Lebensdauer der Maschinen, half den Fabrikbetreibern jedoch nicht dabei, Gerätestörungen oder ungeplante Ausfallzeiten vorherzusagen und zu vermeiden. In den letzten zwanzig Jahren ist die Maschinenzustandsüberwachung zu einem wichtigen Bestandteil des Fabrikbetriebs geworden. Manchmal auch als Smart Factory, Industrial IoT (IIoT) oder Industrie 4.0 bezeichnet, fügen Fabriken Sensoren und Analysesysteme hinzu, die den Zustand der Fertigungsanlagen im Auge behalten.
Die Zustandsüberwachung ist der Prozess der Ausstattung von Geräten mit Sensoren, die signifikante Parameteränderungen erkennen können, die auf einen bevorstehenden Fehler oder Ausfall hinweisen. Diese Systeme suchen nach zwei Dingen. Erstens:Arbeitet die Maschine außerhalb ihrer Konstruktionsparameter und erfordert eine schnelle Reaktion? Zweitens:Was sind die langfristigen Trends kritischer Parameter für die Vorhersage, wann die Maschine gewartet, repariert oder ersetzt werden muss.
Werkselektromotoren
Eine der allgegenwärtigsten Maschinen in Fabriken ist der Elektromotor. Es wird geschätzt, dass heute 300 Millionen Motoren in Produktionsstätten auf der ganzen Welt laufen. Sie liefern die Energie, um Produkte in einer Fabrik herzustellen, zu montieren und zu bewegen. Der Ausfall eines einzelnen Motors kann eine Produktionslinie zum Erliegen bringen und 10.000 US-Dollar pro Stunde kosten. Zustandsüberwachungssensoren und -analysen warnen frühzeitig vor Problemen. Die schnelle Behandlung dieser Probleme führt zu niedrigeren Wartungskosten, weniger Unterbrechungen im Prozessablauf und verbesserter Sicherheit für die Anlagenbediener.
Der Zustand eines jeden Motors kann durch die Überwachung von drei Betriebsparametern bestimmt werden:
-
Vibration – gemessen mit einem Beschleunigungsmesser.
-
Temperatur – gemessen mit einem Kontakttemperatursensor.
-
Strom – gemessen mit einem induktiven oder Shunt-Stromsensor.

Beschleunigungsmesser liefern Daten zum mechanischen Zustand des Motors. Temperatursensoren liefern Daten sowohl zum mechanischen als auch zum elektrischen Zustand, und Stromsensoren untersuchen den elektrischen Zustand. Sensoren können auch Daten über den Zustand von Geräten und Werkzeugen liefern, die am Motor angebracht sind.
Beschleunigungsmesser
Alle rotierenden Motoren haben einen Anker, der an Lagern aufgehängt ist und sich mit unterschiedlichen Geschwindigkeiten dreht. Die Anker sind ausgewuchtet, damit sie beim Rotieren nicht vibrieren. Ein unwuchtiger oder beschädigter Anker erzeugt jedoch Vibrationen, die die Lager beeinträchtigen können. Wenn die Vibrationen bei Resonanzfrequenzen anderer am Motor angebrachter Geräte liegen, kann es zu schweren und schnellen Schäden kommen. Die Vibrationsfrequenz eines Motors stimmt mit der Motordrehzahl überein und liegt typischerweise im Bereich von wenigen Hz bis 4 kHz. Beschleunigungssensoren eignen sich zur Messung dieser Schwingungen.
Beschleunigungsmesser werden auch als Kontaktmikrofone verwendet, die auf hochfrequente Geräusche (Quietschen) von Lagern hören, bei denen die Schmierung erschöpft ist. Diese Frequenzen reichen von 5 kHz bis 15 kHz. Piezoelektrische Beschleunigungsmesser funktionieren gut, weil sie einen breiten Frequenzgang haben, der beide Frequenzbereiche mit einem einzigen Gerät abdeckt.
Typischerweise wird eine schnelle Fourier-Transformation (FFT) verwendet, um das Signal zu analysieren. Die FFT-Daten zeigen jedes Frequenzband der Vibration und ihre Intensität. Abbildung 2 zeigt die Eigenschwingungsfrequenzen und -amplituden eines typischen Motors.
Neue Motoren haben Eigenschwingungsfrequenzen, die aufgezeichnet und als Grundlage für den Vergleich mit Daten verwendet werden, die später im Leben des Motors aufgenommen wurden. Wenn diese Messungen im gleichen Bereich wie die ursprünglichen Daten bleiben, ist der Motor in gutem Zustand. Wenn sich Frequenzen oder Intensitäten mit der Zeit zu verschieben beginnen, ist dies ein Hinweis auf Verschleiß von Teilen des Motors und ein Ausfall kann unmittelbar bevorstehen. Reparaturen können daher geplant werden, bevor ein Ausfall auftritt. Dadurch werden katastrophale Produktionsstillstände vermieden und die Produktionseffizienz verbessert.

Abbildung 3 zeigt den Vibrationssensor Modell 8911 von TE Connectivity Sensors Business Unit. Es enthält einen piezoelektrischen Beschleunigungsmesser und einen Mikrocontroller, der eine FFT-Konvertierung in ein vom Kunden benötigtes Format durchführt. Außerdem ist dieser Sensor batteriebetrieben und überträgt die Daten drahtlos über LoRa-Frequenzen. Dadurch entfällt die Festverdrahtung. Der Sensor kann einfach mit einem Klebstoff, einem Montagebolzen oder einem Magnetfuß an einem Motor montiert werden. Ohne Verkabelung und einfache Montage kann der Sensor in sehr kurzer Zeit und zu sehr geringen Kosten von der Auslieferung in den vollen Betrieb übergehen.
Temperatursensoren
Die beiden Teile eines Motors, die am stärksten von hohen Temperaturen betroffen sind, sind Lager und Statorwicklungen. Um effektiv zu sein, müssen Sensoren, die diese Parameter messen, in engem physischen Kontakt mit den interessierenden Motorteilen stehen, daher sind für Motoranwendungen normalerweise einzigartige Designs erforderlich.
Im Betrieb laufen Motorlager typischerweise zwischen 60° – 70°C (140° – 160°F). Bei richtiger Belastung und Schmierung können Lager eine extrem lange Lebensdauer haben. Das häufigste Problem tritt auf, wenn Schmiermittel aufgrund von Leckagen verschwinden oder aufgrund von Überhitzung der Umgebung ausfallen. Diese Fehlermodi können über ziemlich lange Betriebszeiten auftreten – Tausende von Stunden. Wenn das Schmiermittel aufgebraucht ist, beginnt die Lagertemperatur zu steigen und kann mit einem Temperatursensor und einer Analysesoftware leicht verfolgt werden.
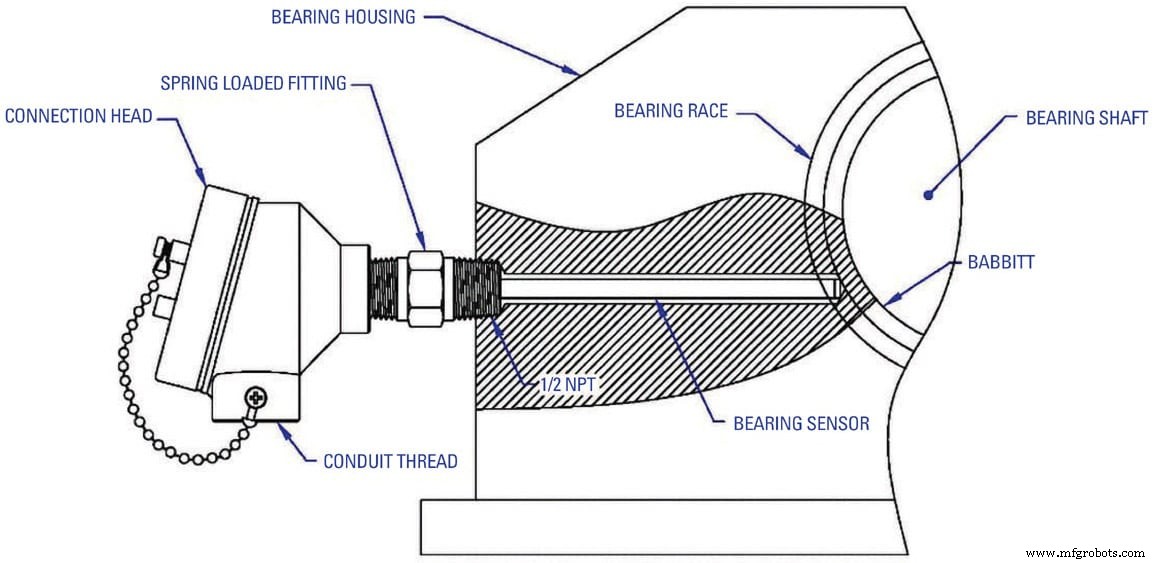
Abbildung 4 zeigt einen federbelasteten NTC- oder RTD-Temperatursensor, der für direkten Kontakt mit einem äußeren Lagerlaufring ausgelegt ist. Diese Montage bietet die genauesten Temperaturmessungen. Das Lagergehäuse muss über Merkmale verfügen, die den Temperatursensor aufnehmen und einen engen Zugang zum Lager ermöglichen.
Temperatursensoren werden auch verwendet, um die Temperatur von elektrischen Statorwicklungen zu messen. Dies sind die Spulen, die die Magnetfelder erzeugen, um die Drehung des Ankers voranzutreiben. Werden diese Wicklungen durch Schlag oder Korrosion beschädigt, erhöht sich der Widerstand des Drahtes und seine Fähigkeit, Strom zu leiten, lässt nach. Dadurch erhitzen sich die betroffenen Drähte. Sie können Temperaturen erreichen, die die Isolierung schmelzen lassen und sogar einen Brand verursachen.

Die Abbildungen 5a und 5b zeigen Temperatursensoren (TE Connectivity Sensors Business Unit), die in die Statorwicklungen eines Motors eingebaut sind. Die Sensoren werden zu einem festen Bestandteil des Geräts.
Wie bei den Vibrationssensoren wird die anfängliche Betriebstemperatur gemessen und aufgezeichnet. Im Laufe der Zeit werden die Temperaturen periodisch gemessen und mit der Basislinie verglichen. Wenn die Temperaturen beginnen, vom Normalwert abzuweichen, ist dies ein Hinweis auf mechanische Probleme für die Lager oder elektrische Probleme für die Statorwicklungen. Auch hier kann die Wartung geplant werden, bevor ein größerer Ausfall auftritt, wodurch eine unerwartete Abschaltung der Linie verhindert wird.
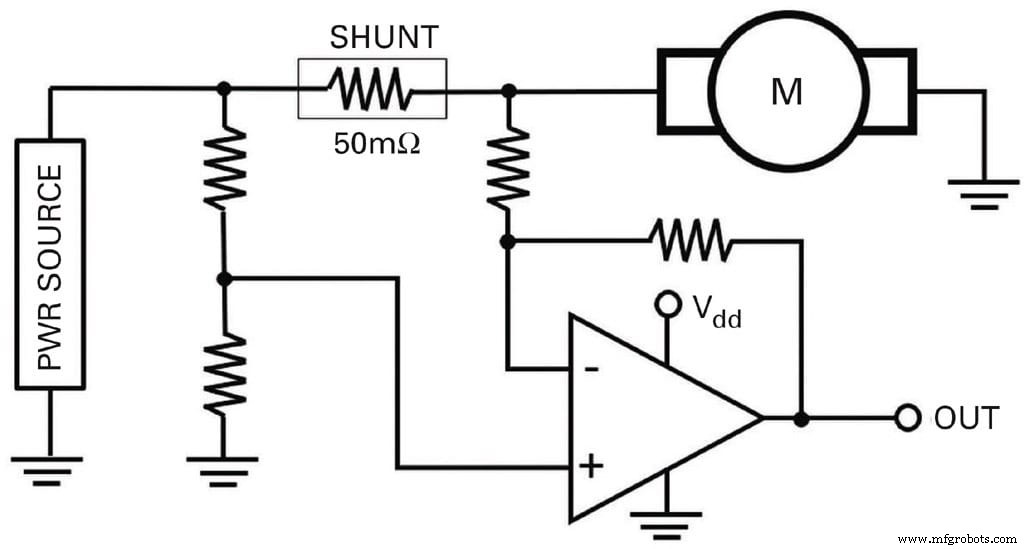
Stromsensoren
Während Vibrations- und Temperatursensoren den physischen Zustand eines Motors melden können, kann ein Stromsensor seinen elektrischen Zustand überprüfen. Stromsensoren gibt es in zwei Grundkonfigurationen:Shunt- oder induktive Ausführungen. Jeder hat Vor- und Nachteile. Die Stromaufnahme eines Motors wird von vielen Faktoren beeinflusst:der angelegten Spannung, der Motordrehzahl, der Belastung der Motorwelle und dem Zustand der Ankerbürsten. Ströme außerhalb des zulässigen Bereichs können auf Netzspannungsprobleme, Kurzschlüsse in den Stator- oder Ankerwicklungen, verschlissene Bürsten oder Probleme mit angeschlossenen Werkzeugen hinweisen.

Ein Shunt-Stromsensor ist ein Leistungswiderstand mit sehr geringem Wert, der in Reihe mit der elektrischen Stromleitung zum Motor geschaltet wird. Die über dem Widerstand entwickelte Spannung ist proportional zu dem durch ihn fließenden Strom. Unter Verwendung des Ohmschen Gesetzes (I =E/R) und Kenntnis der Spannungs- und Widerstandswerte kann der Strom berechnet werden. Shunts werden dort eingesetzt, wo eine sehr hohe Genauigkeit erforderlich ist oder für bürstenlose Hochfrequenzmotoren. Abbildung 6 zeigt den Schaltplan für einen Nebenschlusssensor.
Induktive Stromsensoren verwenden einen Ring mit hoher Dielektrizitätskonstante um das Stromkabel. Strom durch den Draht induziert ein Magnetfeld im Ring (Bin). Ein in den Ring eingebetteter Hall-Effekt-Sensor misst das Magnetfeld und induziert über einen Verstärker und eine Spule, die um den Ring gewickelt sind, ein umgekehrtes Magnetfeld (BF), um dem Bin entgegenzuwirken. Die zur Erzeugung des BF-Feldes erforderliche Spannung ist das Ausgangssignal. Die Nettowirkung der beiden Magnetfelder erscheint am Hallsensor als Nullfeld. Je höher der Stromfluss in der Leistungsleitung, desto höher muss die BF-Spannung sein. (Siehe Abbildung 7)
Jenseits des Motors

Oft können auch am Motor angebrachte Geräte auf Gesundheit überwacht werden. Abbildung 8 zeigt ein Beispiel einer Fräsmaschine, die einen mehrschneidigen Rotationsschneider verwendet, um eine flache Oberfläche in ein Werkstück zu bearbeiten. Der Zustand des rotierenden Schneidwerkzeugs ist sehr wichtig für die Qualität des Schneidvorgangs. Je schärfer die Spannuten am Fräser, desto präziser der Schnitt und desto besser die Oberfläche der fertigen Arbeit. Wenn jede Flöte einen Schnitt macht, erhöht sich der Motorstrom, um die benötigte Leistung bereitzustellen. Scharfe Flöten benötigen weniger Kraft, um das Metall zu schneiden. Stumpfe Flöten erfordern mehr Kraft.

Durch Überwachung des Motorstroms für diese Fräsmaschine ist es möglich festzustellen, welche der Spannuten am Schneidwerkzeug scharf und welche stumpf sind und geschärft werden müssen.
Die Beiträge der Zustandsüberwachung zum IIoT
Seit der Erfindung der Produktionslinie und der damit verbundenen industriellen Revolution gab es zahlreiche technische Innovationen, die den Fortschritt in der Fertigung vorangetrieben haben. Fabriken haben in den letzten 70 Jahren durchschnittliche Produktivitätssteigerungen von 2,8 % pro Jahr erlebt. Technologien wie Elektrowerkzeuge, Spritzguss, Bestückungsgeräte, automatische Tests und Robotik haben alle dazu beigetragen. Heute kommt die Maschinenzustandsüberwachung hinzu. Eine erfolgreiche Zustandsüberwachung beginnt mit Sensoren an Fabrikmaschinen, die ständig Daten über deren Zustand und Betrieb melden. Durch die Verwendung von Echtzeitanalysen können Fabrikbetreiber Problemstellen identifizieren und die erforderlichen Reparaturen und Wartungsarbeiten planen, ohne auf katastrophale Ausfälle warten zu müssen. Dies wird der Fertigung Produktivitätsgewinne bringen. Alles beginnt jedoch mit Sensoren.
Dieser Artikel wurde von Pete Smith, Senior Manager, Sales and Marketing Support, TE Connectivity Sensor Solutions – TES (Schaffhausen, Schweiz/Berwyn, PA) verfasst. Wenden Sie sich für weitere Informationen an Mr. Smith unter Diese E-Mail-Adresse ist vor Spambots geschützt! JavaScript muss aktiviert werden, damit sie angezeigt werden kann. oder besuchen Sie hier .
Sensor
- Markt zur Zustandsüberwachung soll bis 2025 3,9 Mrd. $ erreichen
- Wie Condition Monitoring ein PdM-Programm verbessert
- Das Produkt von SKF Machine Condition Advisor gewinnt Auszeichnung
- Honda Motorenwerk profitiert von Maschinenüberwachung
- SKF-Gerät ermöglicht Diagnose des Maschinenzustands
- B&R präsentiert Zustandsüberwachungslösung auf der Agritechnica
- Überwachung des Zustands von Anlagenmaschinen
- Fallstricke bei der Zustandsüberwachung und Potenzial für die Werkswartung
- Zustandsüberwachung Ihrer Ausrüstung
- Zustandsüberwachung:5 häufige Arten von Fehlern und ihre Bedeutung