3D-Filament-Wicklung ermöglicht Fahrzeugsitzkonzept
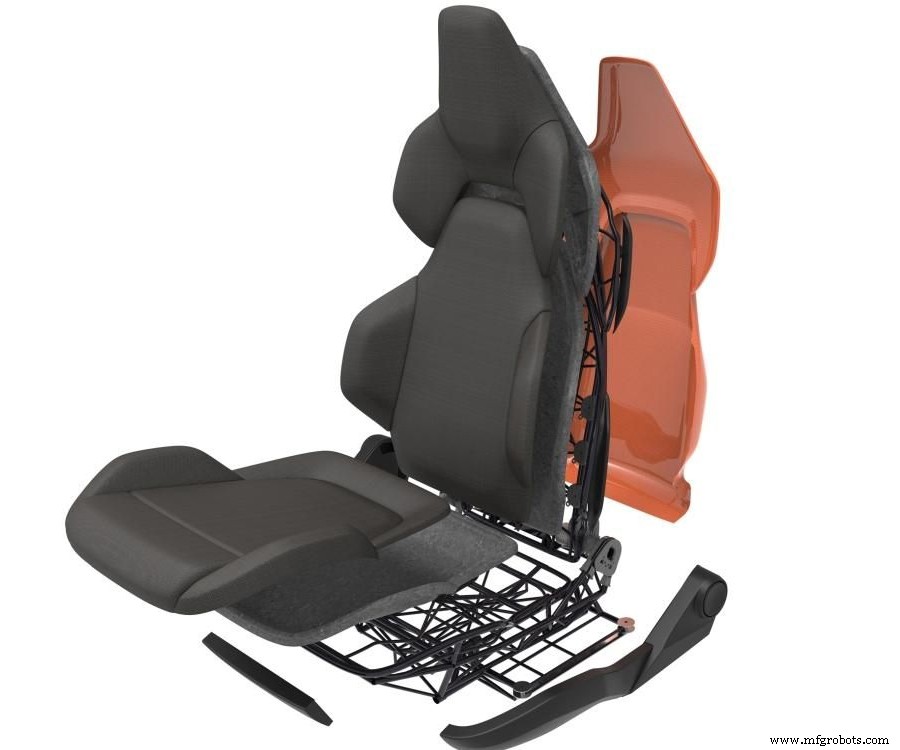
Nachhaltigkeit und Umweltverantwortung werden immer häufiger zu Treibern von Technologietrends in der Automobilindustrie. Energie- und emissionsarme Fahrzeuge sind für die internationale Automobilbranche zu einer Priorität geworden, und Trends zu alternativen Transporttechnologien wie Elektromobilität und Urban Air Mobility (UAM) nehmen an Fahrt auf. OEMs suchen nach neuen Materialien und Prozessen als Wegbereiter für diese zukünftigen Fortbewegungsarten, aber der Wandel im Automobilsektor geht oft nur langsam voran. Damit sich neue Materialien und Verfahren vollständig durchsetzen können, müssen sie nicht nur qualifiziert, sondern auch wirtschaftlich sein und eine Serienfertigung ermöglichen.
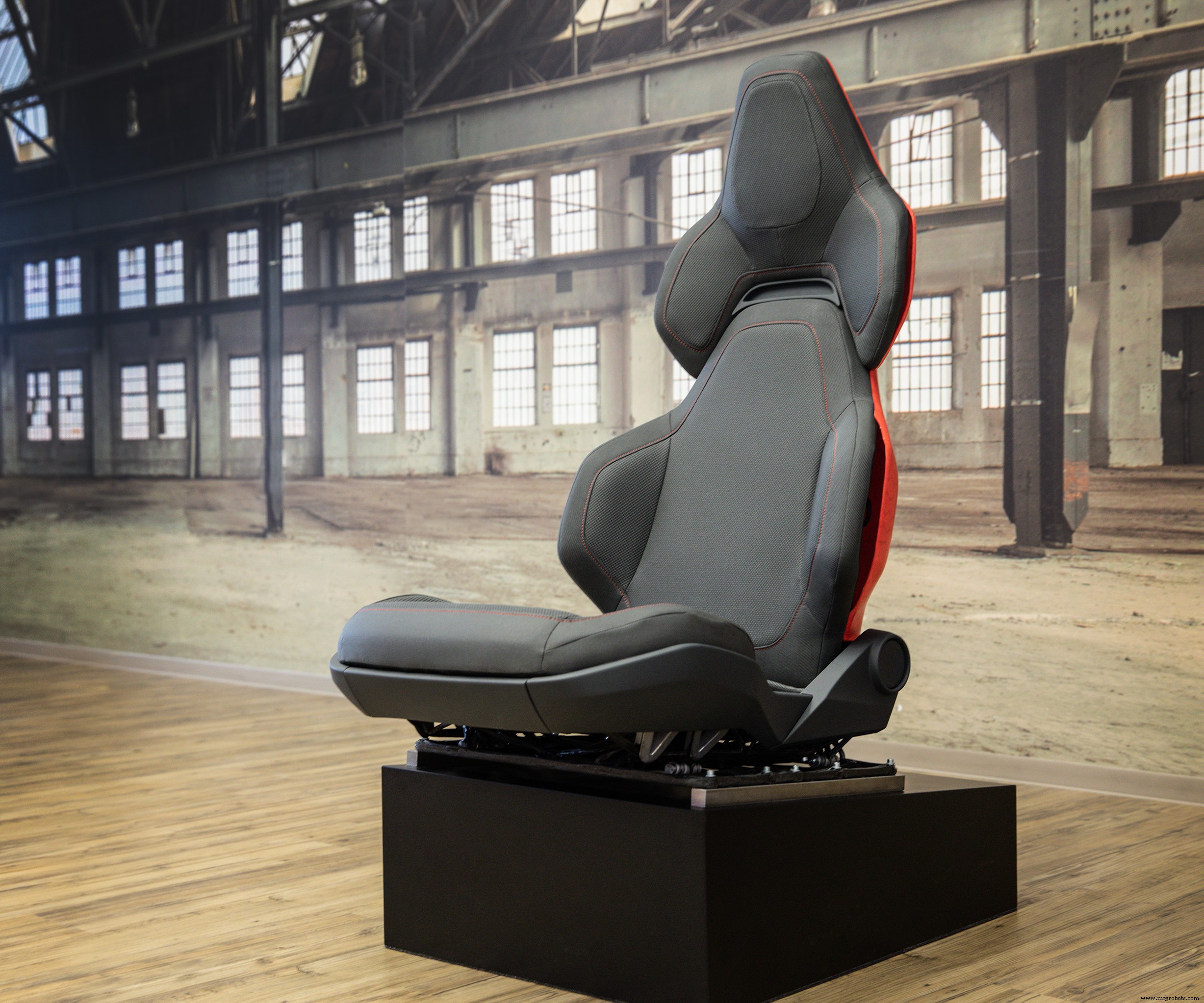
Ultraleichter Sitz. Das Sitzkonzept Ultra Leichtbausitz (ULBS) wurde in Zusammenarbeit mehrerer Unternehmen mit einer Kombination von Technologien entwickelt. Quelle | csi entwicklungstechnik
Kürzlich hat ein innovatives Projekt mit Potenzial für den Automobilsektor – sowie aufstrebende Märkte wie Hypercars und Flugtaxis – gezeigt, wie neue Materialien, Prozesse und Technologien sowie eine enge Zusammenarbeit zwischen Unternehmen Transportmittel der nächsten Generation ermöglichen könnten. Ziel des Projekts war es, einen Autositz mit modernsten generativen Technologien komplett neu zu denken und dies mit nur so viel richtigem Material wie nötig am richtigen Ort – und um schnell Ergebnisse zu erzielen. Der resultierende ultraleichte Metall-Verbund-Hybrid-Fahrzeugsitz-Prototyp wurde in nur sieben Monaten durch einen simulationsgetriebenen Designansatz, agile Projektmanagementmethoden und eine enge Zusammenarbeit und Systemintegration zwischen den beteiligten Unternehmen entwickelt.
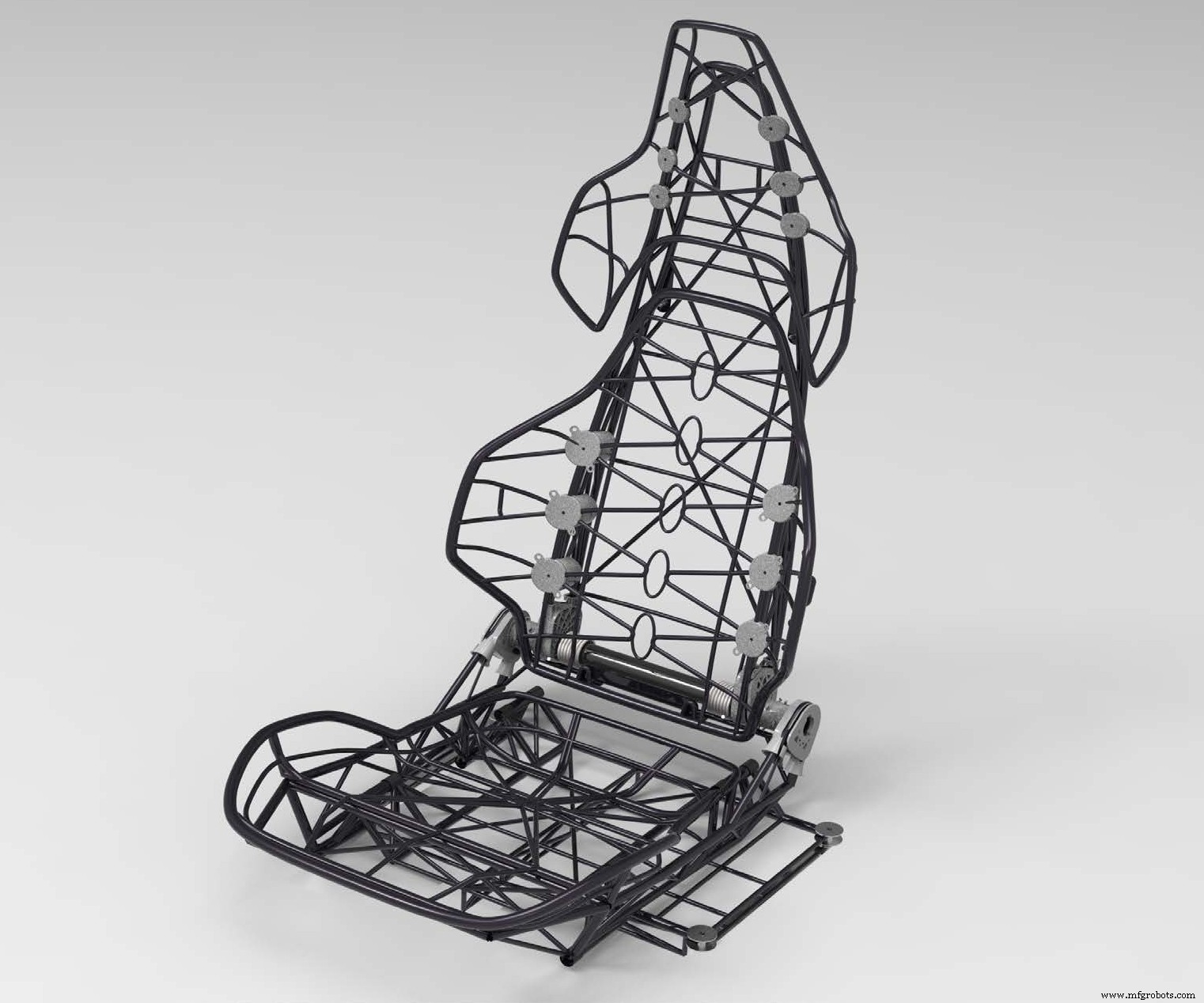
Einen besseren Sitz bauen
Die Machbarkeitsstudie Ultraleichtbausitz (ULBS) wurde in Zusammenarbeit mehrerer Unternehmen mit einer Kombination von Technologien entwickelt. Die Vision des Projekts war, so der Konzern, „ein ultraleichtes Sitzkonzept zu schaffen, das in seiner Gewichtsoptimierung im Markt herausragend ist.“ Die initiierenden Unternehmen csi entwicklungstechnik GmbH (csi, Neckarsulm, Deutschland), Alba Tooling &Engineering (Forstau, Österreich) und Automotive Management Consulting (AMC, Penzberg, Deutschland) entwickelten das prototypische Sitzkonzept in Zusammenarbeit mit Covestro (Leverkusen, Deutschland), LBK Fertigung (Friedberg, Deutschland), Robert Hofmann (Lichtenfels, Deutschland) und 3D|CORE (Herford, Deutschland).
Aus dem Verbundprojekt entstand ein Sitzprototyp mit einem Gewicht von etwas mehr als 10 Kilogramm, der Polster, Strukturrahmen, Funktionseinlagen und die Sitzkonsole für die Fahrzeugmontage beinhaltet. Der Sitz ist 20 % leichter als vergleichbare Leichtbausitze auf dem Markt, von denen viele Aftermarket-Sitze sind. Laut ULBS-Projektleiter Stefan Herrmann, verantwortlich für Leichtbau bei CSI, gibt es derzeit keine konkurrierenden Sitze auf dem Markt, die weniger als 12 Kilogramm wiegen.
„Allerdings ist ein direkter Vergleich oft nicht Apfel-zu-Äpfel, weil Aftermarket-Sitze die Sitzkonsole oft nicht in die Gewichtsdefinition einbeziehen“, sagt Herrmann, „Außerdem ist der Sitzkomfort des ULBS im Vergleich zu Sitzen mit ähnliches Gewicht. Vorhandene Sitze sind oft Schalensitze, die noch leichter, aber nicht so komfortabel sind, oder traditionelle Supersportsitze, die ein viel höheres Gewicht haben.“
Die ULBS verfügt über mehrere innovative Technologien, von denen die Faserroving-Skelettstruktur basierend auf der Prozesstechnologie xFK in 3D die wichtigste Rolle spielt. (Weitere Informationen zu xFK in 3D und anderen Filamentwinding-Technologien finden Sie unter „Filament Winding, Reinvented“.) Die grundlegende Bedeutung der preisgekrönten Technologie zur Endlosfaser-Roving-Ablage liegt in ihrer Gestaltungsfreiheit, in der simulationsgetriebenen und material- optimierte Faserplatzierung exakt in Lastrichtung sowie beim einfachen, kostengünstigen und abfallfreien Aufbringen von Fasermaterial. Für die Lastübertragung in dieser Rahmenstruktur wurden 3D-gedruckte Teile verwendet. In Bereichen mit höchsten Belastungen, wie den Lehnenbeschlägen, verwendet der Sitz 3D-gedruckte Strukturen aus Edelstahl mit hoher Festigkeit und hohem Modul. In weniger belasteten Bereichen wird Aluminium-3D-Druck verwendet.
csi entwicklungstechnik, ein auf Karosseriestrukturen (BIW) sowie Automotive Interior und Exterieur spezialisiertes Engineering-Unternehmen mit den Geschäftsfeldern carbonfaserverstärkte Polymere (CFK) und additive Fertigung, betreute und koordinierte das Projekt auf Basis der Idee initiiert von AMC. csi lieferte das Styling, die Oberflächengestaltung, das Konzept, die Simulation, die Konstruktionstechnik und das Projektmanagement für das Projekt.
Herrmann erklärt:„csi verantwortete die Arbeitspakete im Bereich der digitalen Prozesskette – Styling, Engineering Design, Surface Design, CAE-Simulation, Topologiesimulation, Validierungssimulation und virtuelle Projektbestätigung.“
Er betont, dass das ULBS-Projekt nicht nur durch den Einsatz innovativer Materialien und Fertigungsverfahren bemerkenswert ist, sondern die Entwicklung eines komplexen Bauteils, das innerhalb von nur sieben Monaten neue Komponentendesigns umfasst, in enger Zusammenarbeit zwischen den Partnern.
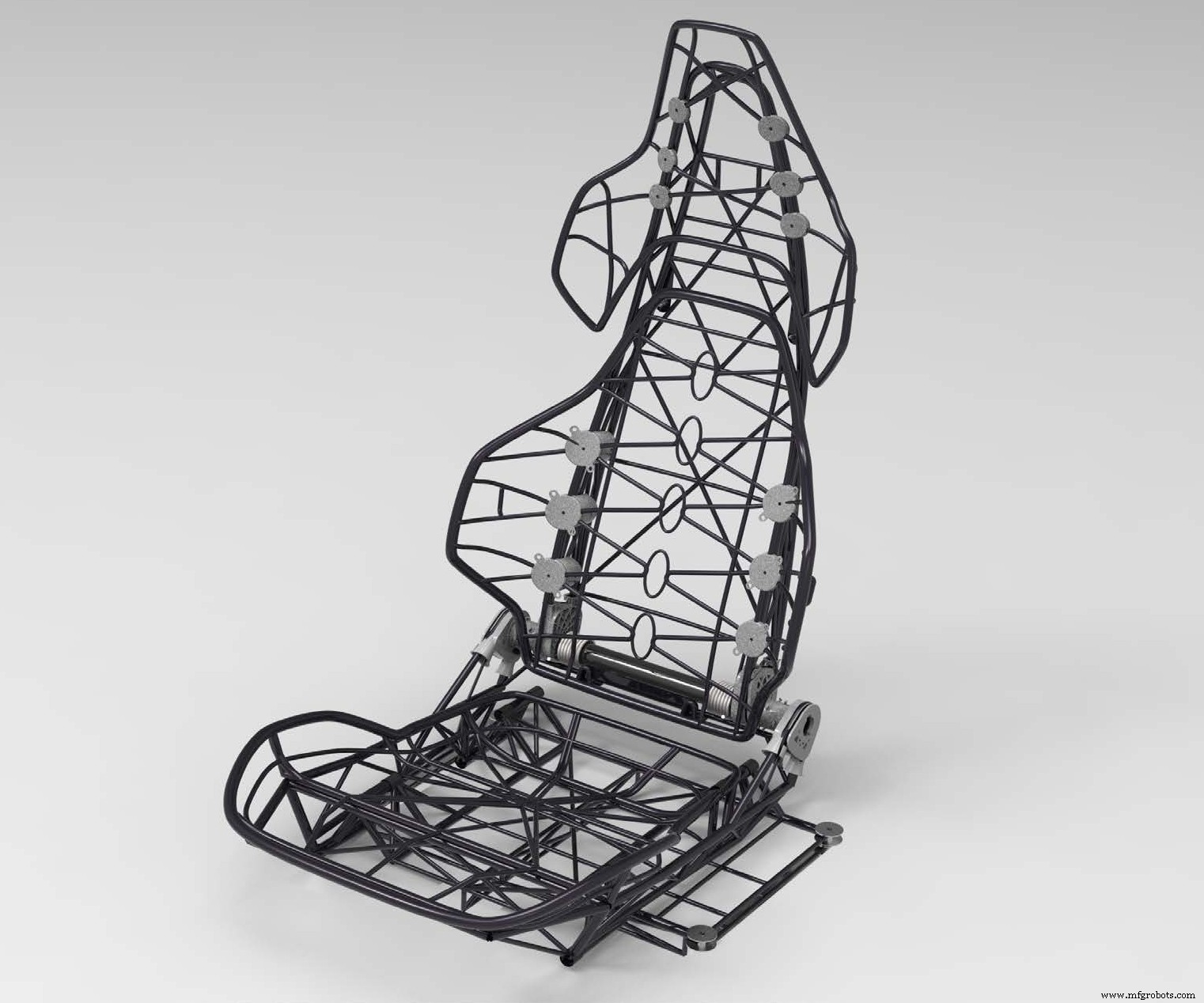
Filamentumwickeltes Sitzgestell. Ein Großteil der Gewichtsreduzierung im ULBS-Projekt resultiert aus der Faserwickelprozesstechnologie xFK von AMC in 3D. Quelle | csi entwicklungstechnik
Einen Rahmen aufwickeln
Ein Großteil der Gewichtsreduzierung im ULBS-Projekt resultiert aus xFK in 3D von AMC, einer hochflexiblen, konfigurierbaren, kostengünstigen und nachhaltigen Faserverbundtechnologie zum Wickeln von Bauteilen.
xFK in 3D wurde bereits für eine Vielzahl von Produkten und Anwendungen für verschiedene Branchen und Marktsegmente eingesetzt. SGL Group Wiesbaden, Deutschland) zeigte auf der internationalen Composites-Messe JEC World 2018 mehrere mit dieser Technologie hergestellte Automobil- und Fahrradteile. Eines der ausgestellten Teile, ein von AMC entwickeltes Fahrradkettenblatt aus Kohlefaser, soll bis zu 70 % Gewicht einsparen. im Vergleich zu einer Aluminiumversion.
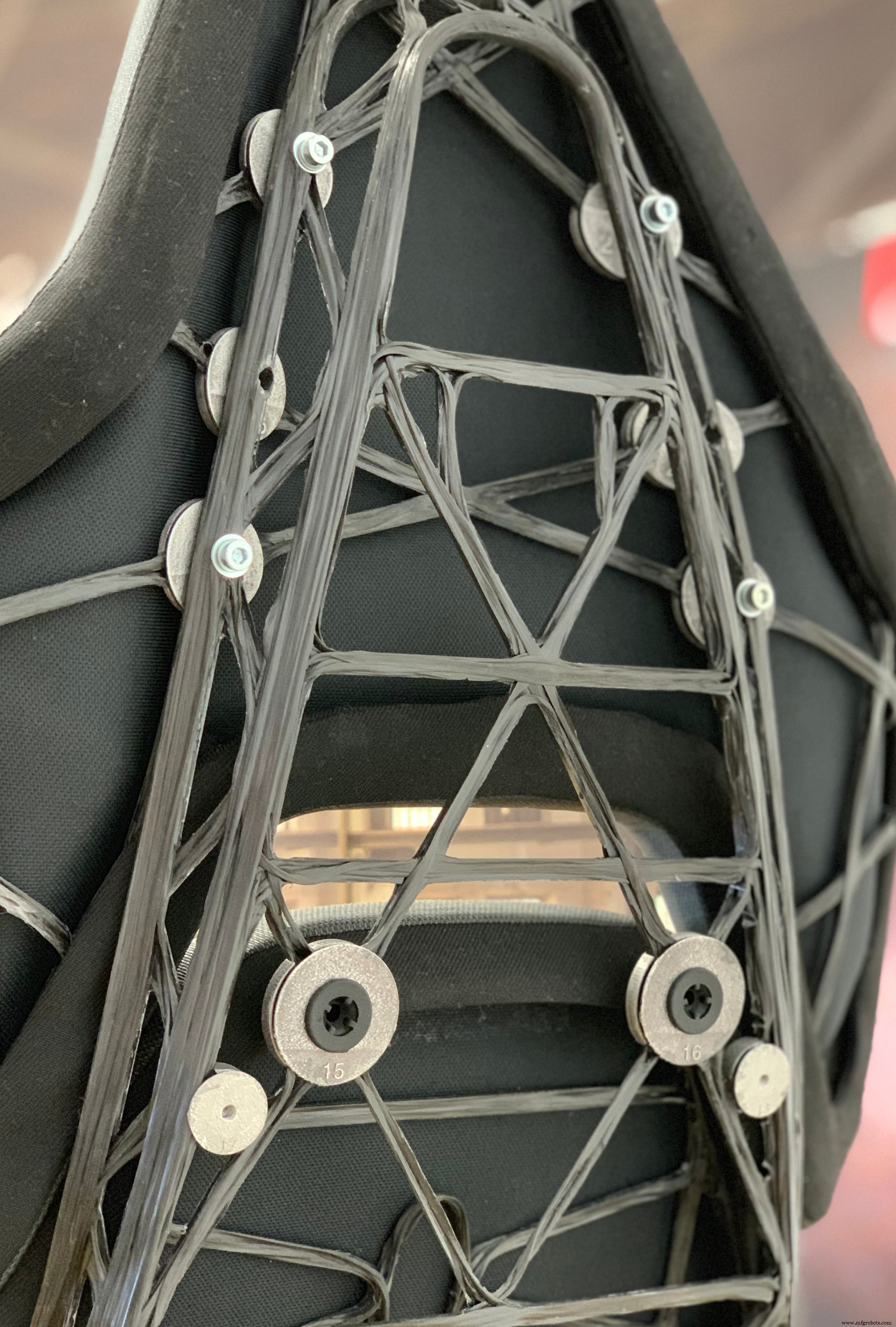
Wickelbuchsen. Ein mit Duroplast imprägnierter Faserroving wird um eine Positionierungsvorrichtung gewickelt, sodass die Fasern so angeordnet werden können, dass sie den Lasten und gewünschten Funktionen jedes Teils entsprechen. Quelle | csi entwicklungstechnik
Die xFK im 3D-Verfahren wickelt Tragstrukturen abfallfrei mit duroplastisch harzgetränkten Endlosfasern. Ein mit Epoxidharz getränkter Faserroving wird um eine Positionierungsvorrichtung oder Wickelbuchsen gewickelt, sodass die Fasern spezifisch angeordnet werden können, um den Belastungen jedes Teils und den gewünschten Funktionen gerecht zu werden.
„Ein großer Vorteil von xFK in 3D ist die Beseitigung von Schwachstellen bei der Lastabtragung und -einleitung in Bauwerke“, sagt Herrmann. Er erklärt, dass Schwachstellen oft nicht im Kontinuum des Tragwerks liegen, sondern in den Bereichen, in denen Lasten in das Tragwerk eingeleitet werden, insbesondere dort, wo benachbarte Bauteile mit dem Tragwerk verbunden sind. Die xFK in 3D-Technologie ermöglicht Lastübertragungen über Verbindungen hinweg und ermöglicht es, Fasern entsprechend der gewünschten Bauteilfunktionen und Lastfälle auszurichten und in drei Dimensionen zu fertigen.
Das Filament Winding Verfahren bietet auch zusätzliche Vorteile. Der Prozess trägt dazu bei, Materialverschwendung zu minimieren – weniger als 1 % des Faserrovings wird verschwendet.
csi erkannte die Stärken von xFK in 3D und entwarf den ULBS-Sitzrahmen, der unter der Beratung von Dr. Clause Georg Bayreuther, Technologieleiter von AMC, konstruiert wurde.
„In Zusammenarbeit mit csi-Ingenieuren haben die AMC-Berater und die Werkzeugexperten von Alba dieses Konzept und die Struktur für den im xFK im 3D-Verfahren herzustellenden Sitzrahmen entwickelt“, sagt Peter Fassbaender, Technologieberater und Initiator von xFK in 3D-Technologie.
Alba fertigte die Werkzeuge für den CFK-Sitzrahmen und leistete technische Unterstützung. Auch wenn der Sitzrahmen aus Kohlefaser gewickelt wurde, sind auch Naturfasern oder Basaltfasern gute Kandidaten.
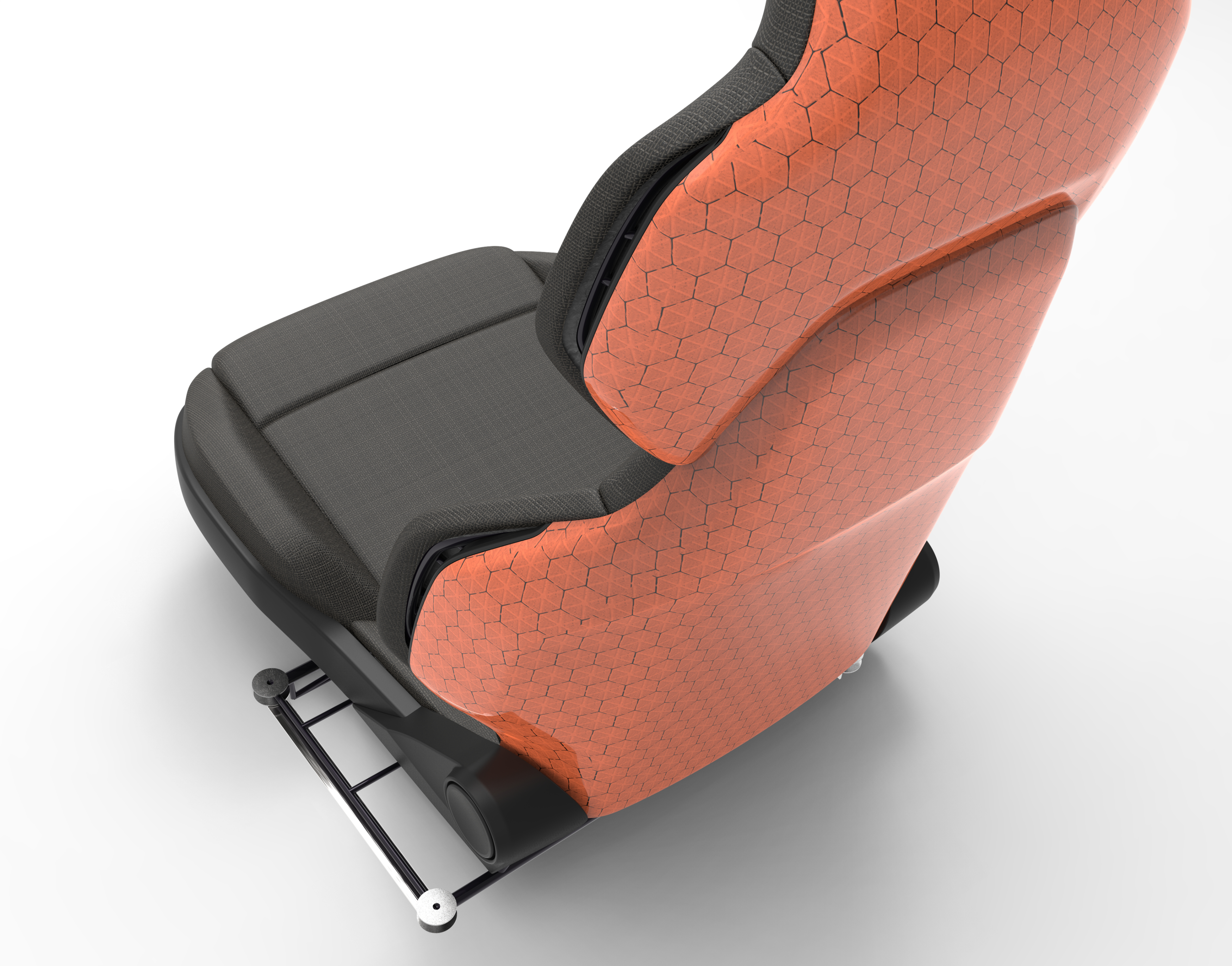
Neue Technologien. Der ULBS-Prototyp verwendet eine Kombination neuer Technologien, darunter eine Rückwandschale aus intralaminarem Verstärkungskern (IRC)-Material und 3D-gedruckte Sitzlehnenpolster aus thermoplastischem Polyurethan (TPU). Quelle | csi entwicklungstechnik
Eine hybride Materialstruktur
Neben dem Rahmen enthält der ULBS-Prototyp mehrere weitere Neuheiten. Alba, die die Werkzeuge lieferte, lieferte auch die Werkzeuge, die Konstruktion und die Fertigung für den Schaumstoffkörper des Sitzes und führte die Montage des Sitzes durch. Eine Faservliesmatte bedeckt den CFK-Rahmen des Sitzes, der dann mit einem 3D-gedruckten PUR-Schaumstoff überzogen wird. Der Sitzpolsterbereich besteht aus traditionellem Schaumstoff.
Eine weitere Gewichtsreduzierung wurde durch den Einsatz von 3D|CORE, einem intralaminaren Verstärkungskern (IRC)-Material, in der Rückwand-Schalenstruktur der Sitzlehne erreicht. Das Material ist ein intralaminarer Verstärkungskern (IRC) – ein struktureller Sandwichkern, der Kernkörper aus extrudiertem Polystyrol (XPS) und Polyethylenterephthalat (PET) in einem integrierten Wabenmuster umfasst. Bei der Herstellung von Verbundteilen wird die Wabenstruktur mit Harz gefüllt, was zu einer hohen intralaminaren Festigkeit führt. Der 3D|Core wird zwischen zwei Glasfaserschichten zu einem Vorformling zusammengesetzt, der mit thermoplastischem Epoxidharz mittels vakuumunterstütztem Resin Transfer Moulding (VA-RTM) infundiert wird.
Als Bindemittel für die Faservliesmatten lieferte Covestro seinen Dispercoll-Kleber sowie das 3D-gedruckte Rückenpolster. Die mechanischen Eigenschaften von Dispercoll sorgen laut Herrmann für eine gute Abriebfestigkeit, was wichtig ist, da der Oberflächenkontakt zwischen Kissen und Rahmen das Vlies mit der Zeit verschleißen kann.
„Wenn man ein Einzelfaser-Roving hat und dieses in ein Textil einbringt, entstehen Mikrobewegungen zwischen den harten CFK-Teilen und den Vliesmatten. Die Sitzgestellteile können am Textil reiben und es zerstören“, erklärt Herrmann.
Herkömmliche Sitze haben typischerweise eine größere Oberfläche, die die Polsterung unterstützt, und haben dieses Problem nicht. Bei xFK in 3D gibt es jedoch aufgrund der Rahmenstruktur eine kleinere Kontaktfläche.
„Wenn xFK in 3D-Strukturen gegen das Vliesgewebe drückt, braucht man ein spezielles und haltbares Bindemittel; das bietet Dispercoll in diesem Zusammenhang“, ergänzt Herrmann.
Covestro lieferte auch das angeblich weltweit erste 3D-gedruckte Kissen. Während bei Sitzlehnen üblicherweise konventioneller und werkzeugintensiver Schaumstoff verwendet wird, erhöht der Einsatz der 3D-gedruckten Sitzlehnenpolster aus TPU (thermoplastisches Polyurethan) die Flexibilität und Anpassungsfähigkeit des ULBS-Sitzes hinsichtlich seiner Ästhetik weiter. funktionale Integrationsmöglichkeiten und Komfort.
Ein Sitzplatz für die Zukunft
Das ULBS-Projekt erreicht mehrere Ziele. Das resultierende Konzept hat, obwohl es noch nicht auf dem Markt ist, das Potenzial, zahlreiche Nischenmärkte wie Hypercars, Air-Taxis, ultraleichte Fahrzeuge, Mikromobilität, Helikopter, Multicopter zu bedienen und Luftfahrt. Der ULBS ist zwar teurer als Serienautositze, demonstriert jedoch mehrere Technologien, die den Abfall minimieren und dadurch die Materialkosten senken. Im Vergleich zu anderen Kohlefasertechnologien erzeugt xFK in 3D einen sehr geringen Abfall. Tatsächlich ist das gesamte Projekt darauf ausgerichtet, minimale Ressourcen und nur das erforderliche Minimum an Material zu verwenden. Das ULBS bietet auch die Möglichkeit, nachwachsende und nachhaltige Ressourcen wie Naturfasern in der Rahmenstruktur, Kissen und Textilien zu verwenden.
Vor allem aber zeigt das Projekt, wie Unternehmen durch kurze und agile Abstimmungsverfahren gemeinsam die Time-to-Market minimieren können. Es ist auch ein gutes Beispiel für den Einsatz von Design Thinking, um ein Produkt erfolgreich von der Idee bis zum Hardware-Prototyp zu führen, indem man sich auf die funktionalen Anforderungen konzentriert und auf zukünftige Anwendungen und Nachhaltigkeitsziele blickt.
Faser
- Wicklungskonfigurationen
- Fahrradsitz
- Einrad
- Kindersitz
- Ultra-Breitband-Chip ermöglicht Smartphone-basierten Fahrzeugzugang
- Edge-Computing-Plattform ermöglicht tiefen Zugriff auf Automobildaten
- Leistungsmerkmale von Glasfasergarn
- Toilettensitzbezug aus Kohlefaser
- Neue Technologien und Märkte bei World of Filament Winding Ereignis
- Roth-Filamentwickler für größere Gewichts- und Kosteneinsparungen bei der Ariane 6