Airbaggehäuse-Prototyp testet 3D-gedruckte Verbundwerkstoffe
Joyson Safety Systems (Auburn Hills, Michigan, USA) ist seit mehr als einem Jahrhundert an der Entwicklung, Herstellung und dem Verkauf von Sicherheitskomponenten für eine Vielzahl von Märkten beteiligt, darunter Airbags, Sicherheitsgurte, Lenkräder und Sicherheitselektronik für die Automobilindustrie Industrie.
Das Unternehmen hat kürzlich eine Machbarkeitsstudie durchgeführt, um das Potenzial anderer bestehender Materialien und Prozesse zur Verbesserung von Produkten wie dem Gehäusecontainer des Fahrerairbags (DAB) zu untersuchen
Ein komplettes Airbagsystem besteht aus einem Gasgenerator, einem Airbagkissen, einer Abdeckung und einem Gehäuse mit Befestigungspunkten am Lenkrad. Das Airbagkissen selbst befindet sich im Raum des Gehäuses und der Abdeckung.
Die Leistung des DAB-Gehäuseteils ist entscheidend. Neben der Fixierung des gesamten Airbagsystems während der Fahrt muss das Teil auch den Kräften standhalten, die beim Entfalten des Airbags auf das Airbagsystem einwirken. Für die Prüfung musste das für das Teil verwendete Material eine ausreichende Festigkeit, Schlagzähigkeit und Hitzebeständigkeit in einem Temperaturbereich von -35 °C und +85 °C aufweisen.
Der Originalbehälter wurde im konventionellen Spritzgussverfahren hergestellt und bestand aus mit 40% Glasfasern verstärktem Polyamid (PA). Für die Machbarkeitsstudie hatte sich das Team von Joyson Safety Systems zum Ziel gesetzt, innerhalb weniger Tage ein funktionsfähiges Prototypenteil herzustellen, und es wollte ein Material finden, das ähnliche mechanische, thermische und Leistungseigenschaften wie die Originalmaterialien aufweist.
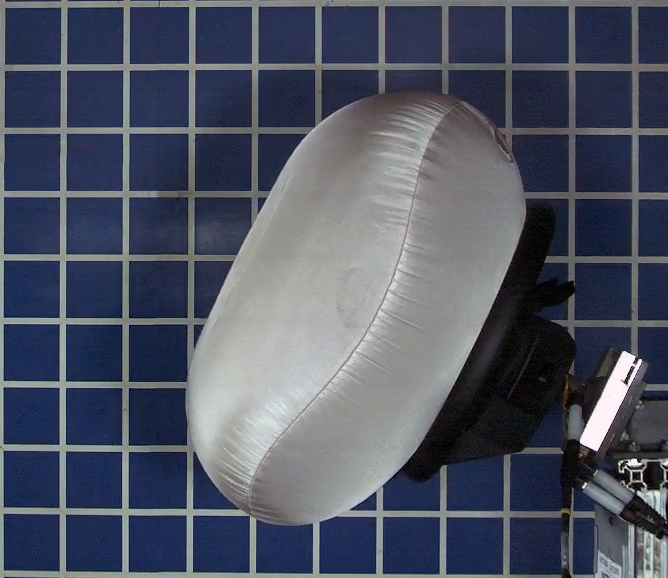
Das Innovationsteam von Joyson führte eine Marktanalyse durch, um geeignete Materialien zu finden, und wandte sich schließlich an CRP Technology (Modena, Italien) für seine Windform TOP-LINE-Reihe von Hochleistungsverbundwerkstoffen und den hauseigenen 3D-Druckservice.
Konkret entschied sich das Team für das Windform SP Kohlefaser/PA-Material von CRP, das noch bessere Eigenschaften aufweist als die vorherigen Materialien, die es für das Teil verwendet hat. Die Teile würden mit einem ausgewählten additiven Fertigungsverfahren des Lasersinterns (SLS) hergestellt.
Das Team war in der Lage, schnell ein Prototypenteil herzustellen und es in einem kompletten Airbagmodul zu testen, was die hohe Festigkeit und Schlagzähigkeit des neu gestalteten Teils sowie die thermische Stabilität in einem Temperaturbereich demonstrierte. Im Vergleich zum ursprünglichen Spritzgussverfahren konnte das neue Teil auch schneller mit SLS hergestellt werden und machte teure Werkzeuge überflüssig.
„Diese Gelegenheit hat eine Vielzahl von Möglichkeiten und Überlegungen für eine weitere Zusammenarbeit mit CRP Technology eröffnet“, sagt Samer Ziadeh, Entwicklungsingenieur im Team Core Engineering Materials bei Joyson Safety Systems.
Faser
- Ode an den Prototyp
- Die Frage zur Vertragspflege – Teil I
- Die Entwicklung leichter Verbundwerkstoffe in der Medizinindustrie
- Ein Leitfaden zum Verständnis des Herstellungsprozesses von Verbundwerkstoffen
- Wie sieht die Zukunft von Verbundwerkstoffen in der Sportartikelindustrie aus?
- Ein tiefer Einblick in die Anwendungen von Verbundwerkstoffen in der Luft- und Raumfahrt
- 3 Gründe, warum die Schifffahrtsindustrie Verbundwerkstoffe nutzt
- 5 Tipps zum Finden des besten Herstellers von Kohlefaserteilen
- Nèos International gründet neues Hauptquartier für Verbundwerkstoffe in Großbritannien
- Der Wert des Feingusses (Teil 2)