Durch Verbundwerkstoffe angetriebene Wasserturbinenschaufelkonstruktion
Der Begriff „Wasserkraft“ erinnert oft an immense Operationen, die von speziell gebauten Infrastrukturen wie Dammsystemen und großen Turbinen mit traditionell metallischen, auf Propellern basierenden Turbinenschaufeln angetrieben werden. In vielen Gebieten gehen jedoch die neuen Kapazitäten für große, leistungsstarke Wasserkraftwerke aus. Gleichzeitig wächst die Nachfrage nach mehr und kostengünstigerer erneuerbarer Energieerzeugung weiter.
Das US-Energieministerium (DOE) prognostizierte in seinem Bericht „Hydropower Vision“ aus dem Jahr 2018, der den aktuellen Stand der Wasserkraft in den Vereinigten Staaten und seine Ziele für die Zukunft skizziert, dass der US-Wasserkraftmarkt wächst – von 101 Gigawatt (GW) der Energiekapazität im Jahr 2018 auf eine potenzielle Kapazität von fast 150 GW im Jahr 2050 – würde neue fortschrittliche Technologien erfordern, die mehr Energie zu niedrigeren Kosten bereitstellen können.
Eine mögliche Lösung könnten kleinere Wasserkraftgeneratoren sein, die ungenutzte Energie aus Wassersystemen mit geringem Durchfluss wie Bewässerungskanälen und Bächen gewinnen, so Darren Wren, General Manager bei Kinetic NRG (Gold Coast, Australien). Kinetic NRG wurde 2016 vom verstorbenen Gründer Paul Camilleri gegründet und ist ein privat finanziertes Unternehmen für erneuerbare Energien, das sich auf die Entwicklung neuer Technologien zur Erzeugung von Wasserkraft konzentriert, um kostengünstigen und zuverlässigen Strom zu liefern.
Die erste Technologie des Unternehmens heißt Hydro-kinetic Energy Generator (HEG) mit einem Durchmesser von 1,5 Metern und einer Leistung von bis zu 30 Kilowatt (kW) aus Wasserströmen von 2,0 Metern pro Sekunde. Diese Leistung macht es zu einem „Mikro“-Wasserkraftsystem nach Klassifizierungsbehörden wie dem US-amerikanischen DOE, das Mikrosysteme als solche mit einer Leistung von bis zu 100 kW definiert. Der HEG ist für den direkten Einsatz in Flüssen, Bewässerungskanälen oder Tail Races gedacht, die Wasser aus bestehenden Dämmen leiten, und ist für Wasserkraft mit geringer Fallhöhe ausgelegt – was bedeutet, dass die „Fallhöhe“ oder der Abstand zwischen der Wasserlinie und der Turbine weniger als 20 Meter beträgt.
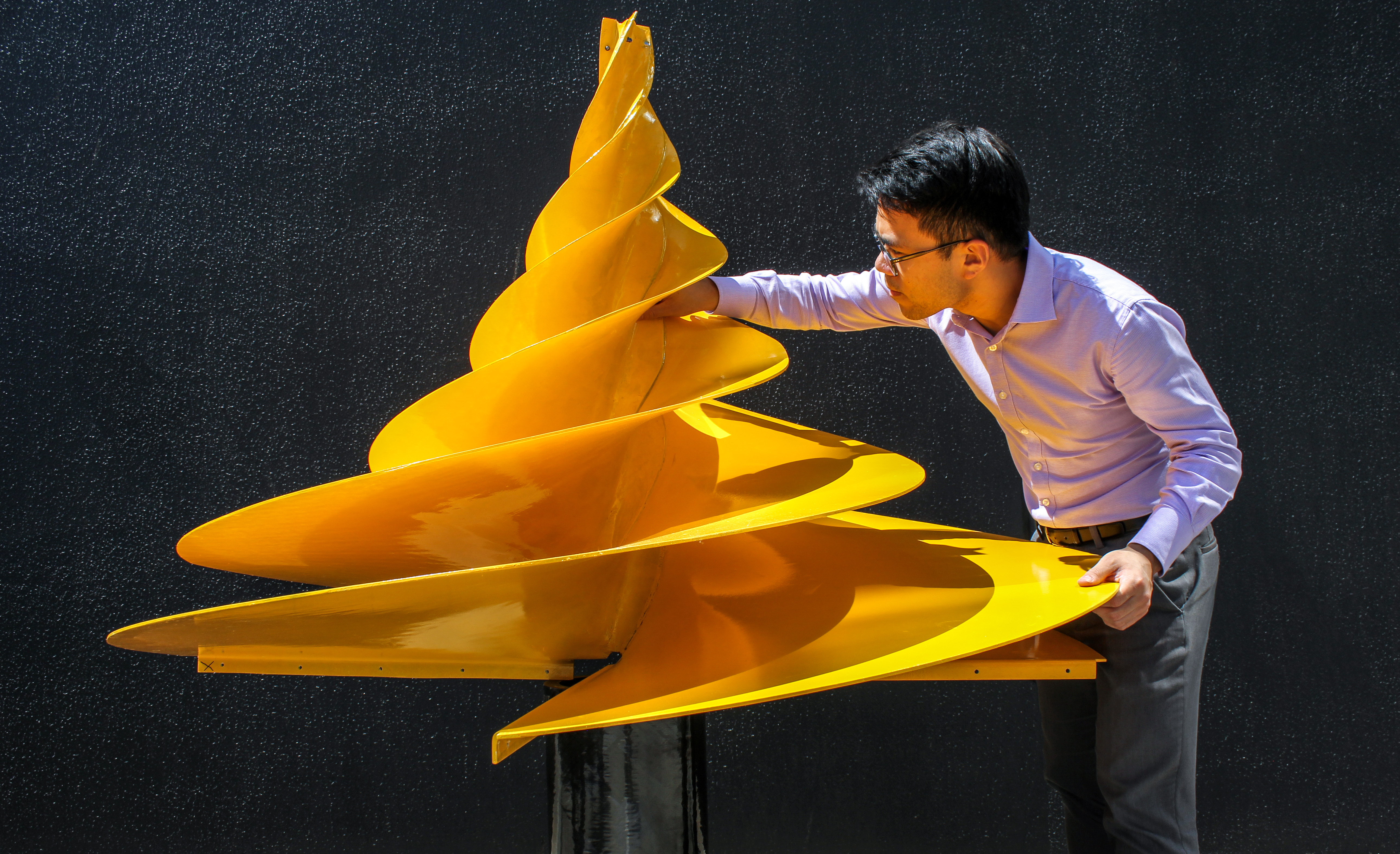
Die Entwicklung des HEG und seiner spiralförmigen Turbinenschaufel sei seit etwa fünf Jahren in Arbeit, sagt Wren. „Es war eine ziemliche Reise. Das Design ist jetzt buchstäblich durch Versuch und Irrtum entstanden.“
Entwicklung einer modularen, herstellbaren Klinge
Die ersten kleinen Spiralschaufelmodelle von Kinetic NRG wurden aus Metall geformt, aber als es an der Zeit war, den Prototypen im Originalmaßstab mit einem Durchmesser von 1,5 Metern herzustellen, „stellten wir tatsächlich fest, dass wir es nicht schaffen konnten“, sagt Wren. Das Konzept bestand darin, mit einem flachen Metallstück zu beginnen und dann eine Reihe von Spiralen zu formen oder zu schmieden, die von der Mitte aus strahlen. „Wir konnten einfach keine Möglichkeit finden, auf bestimmte Punkte des Teils zuzugreifen, um die erforderliche Festigkeit zu erzeugen“, erklärt er.
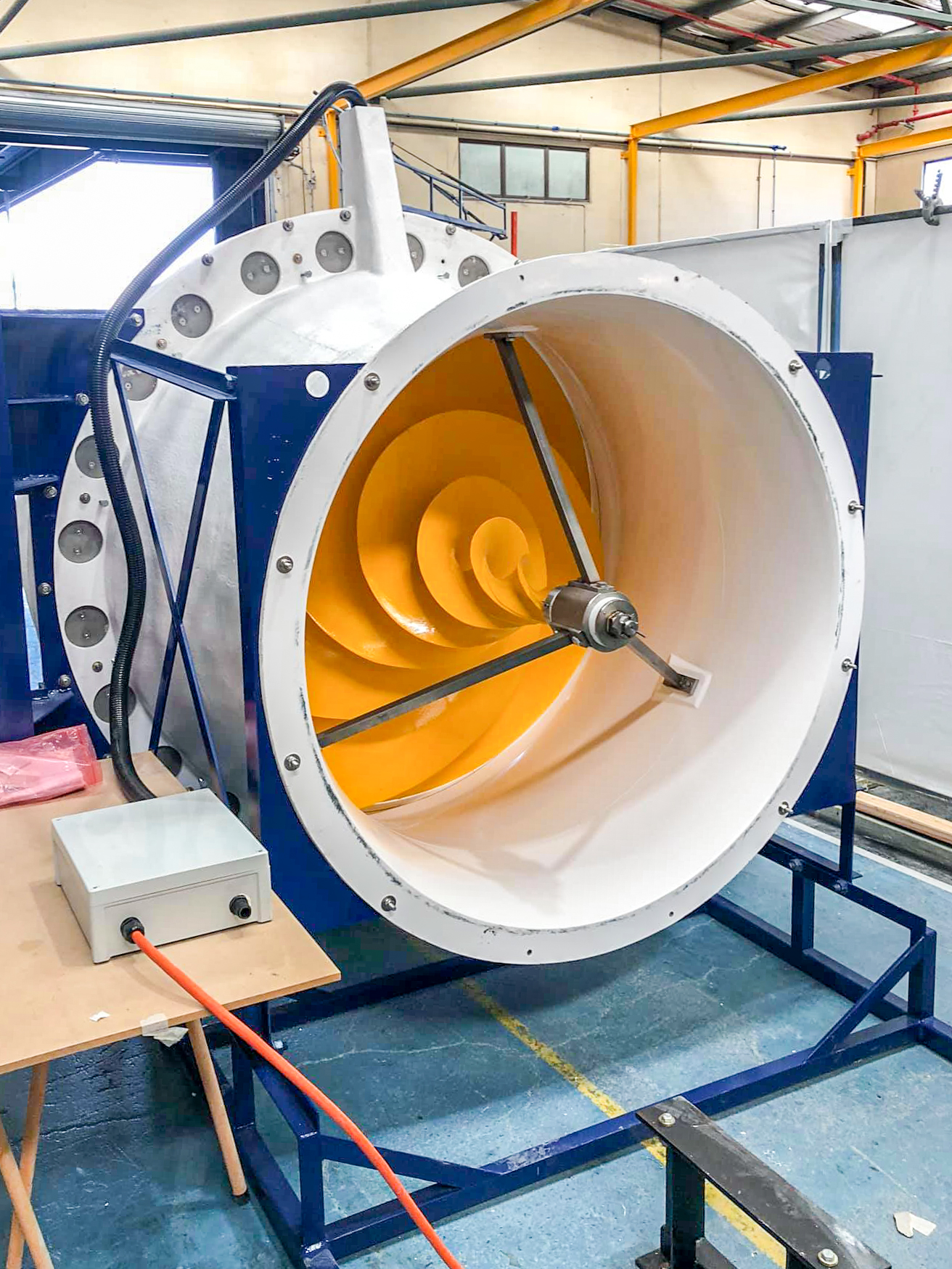
Das Unternehmen gab schließlich seine metallischen Bemühungen auf, aber nicht das Design selbst. Laut Wren hat sich Kinetic NRG mit einer lokalen Universität zusammengetan, um alternative Fertigungstechniken und Materialien wie Nylon oder Keramik zu untersuchen, und begann mit 3D-Druckunternehmen zu sprechen, um zu sehen, ob die additive Fertigung eine praktikable Option sein könnte. Dennoch bot sich keine Lösung an, die die richtige Kombination aus Herstellbarkeit und mechanischen Eigenschaften bietet. Nach einer dreijährigen Reise wurde Kinetic NRG schließlich über eine Versorgungsnetzwerkverbindung mit dem Team des Ingenieurbüros Advanced Composite Structures Australia (ACS-A, Melbourne) eingeführt, das sich auf die Entwicklung und Herstellung von hochwertigen Kleinserien spezialisiert hat -Verbundwerkstoffkomponenten für eine Vielzahl von Endmärkten hinzugefügt.
Wren bezeichnet das, was als nächstes geschah, als „Meeting of Minds“. aus Erfahrung in der Lage wäre, die erforderlichen Anforderungen an Form, Gewicht und Steifigkeit von Kinetic NRG zu erfüllen.
Die innovative Klingenform war die wichtigste Designherausforderung für das Projekt, wobei die mechanischen Anforderungen an die Klinge laut Wren auf den Standards des US-amerikanischen DOE und der International Electrotechnical Commission basieren. Die restlichen Komponenten des Systems – Übertragung, Energieverwaltung, Kommunikation usw. – sind Standardprodukte, die bekanntermaßen alle erforderlichen Vorschriften erfüllen.
Laut Falzon bewertete ACS-A zunächst die metallischen Versuche beim Klingendesign und ermittelte dann, wie die erforderliche Form, Maßtoleranzen und das Gewicht der Klinge erreicht werden. Das Blatt musste auch in der Lage sein, aquatischen Umgebungen standzuhalten und steif genug zu sein, um die Stahlwelle der Turbine zu tragen, auf der es befestigt ist. Das ACS-A-Team begann mit dem ursprünglichen Metalldesign und „reverse-engineered“ ein Glasfaser-Verbundblatt, um die ursprüngliche Steifigkeit zu erreichen, sagt Falzon. Beim Wechsel von einer geschweißten, metallgeformten Struktur zu einem Verbundlaminat mussten jedoch einige konstruktive Änderungen vorgenommen werden. Falzon erklärt:„Wir traten einen Schritt zurück und fragten:‚Okay, wenn wir die Vorteile von Verbundwerkstoffen voll ausschöpfen wollen, wie sieht das dann aus?‘“
Nach mehreren Iterationen und Diskussionen besteht das aktuelle Design aus vier identischen Verbundklingen, die ineinandergreifen, um die endgültige Spiralform zu bilden. „Die Verbundklinge ist tatsächlich dicker als die Stahlkonstruktion, aber aufgrund der geringeren Dichte der Materialien, mit denen wir arbeiten, leichter“, sagt Falzon. „Durch die Dicke erhalten wir auch eine viel höhere Biegesteifigkeit im Vergleich zur Stahlkonstruktion, sodass Sie insgesamt ein viel steiferes Produkt erhalten.“
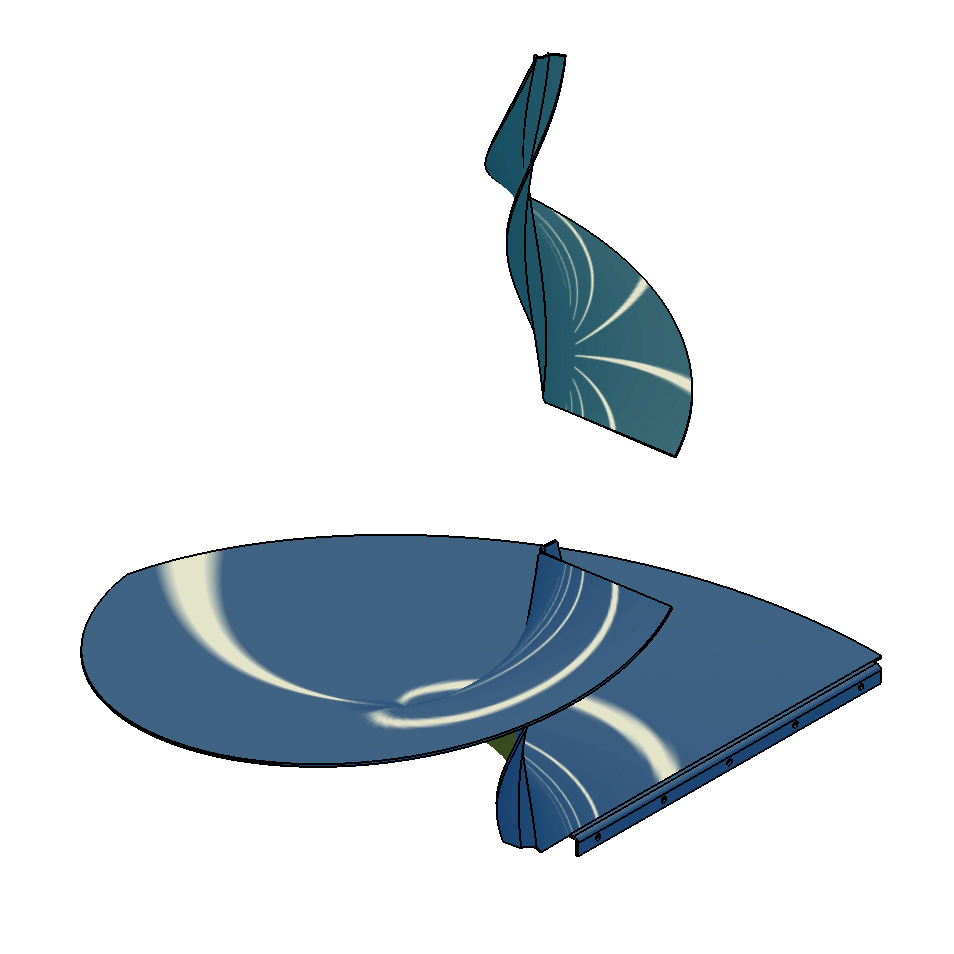
Umgedrehtes Werkzeug
Die Entwicklung der Werkzeugform war laut Falzon der schwierigste Teil des Prozesses. Das ACS-A-Team bewertete die Form der ursprünglichen Rotorblattbaugruppe mit der CATIA-Software von Dassault Systèmes (Waltham, Massachusetts, USA). Dies führte zur Entwicklung der Schaufeloberflächen und der Gestaltung von Werkzeugkonzepten. „Wenn man sich die Teile heute ansieht, werden sie tatsächlich verkehrt herum hergestellt. Das Klingenmodell musste invertiert werden, um das Werkzeug zu erstellen, und es ist bizarr, bis Sie das eigentliche Werkzeug sehen, wenn es ankommt. Es ist ziemlich komplex“, sagt Falzon. Er erklärt, dass die Werkzeuge umgedreht werden mussten, „um sicherzustellen, dass wir die erforderliche Oberflächengüte auf der dem Wasserstrom ausgesetzten Seite der Klinge erreichen“ und um sicherzustellen, dass jede der hergestellten Klingenkomponenten in einem Stück entformt werden konnte. Auch das Werkzeug musste präzise sein:Die ineinandergreifenden Schaufelkomponenten mussten sich im montierten Zustand exakt zueinander und zur Zentralwelle der Turbine ausrichten. Für den Prototyp wurden die von Sykes Australia (Sydney) gelieferten Werkzeuge aus kostengünstiger Werkzeugpaste hergestellt, die auf eine Schaumstoffunterlage aufgetragen und dann in die endgültige Form CNC-gefräst wurde.
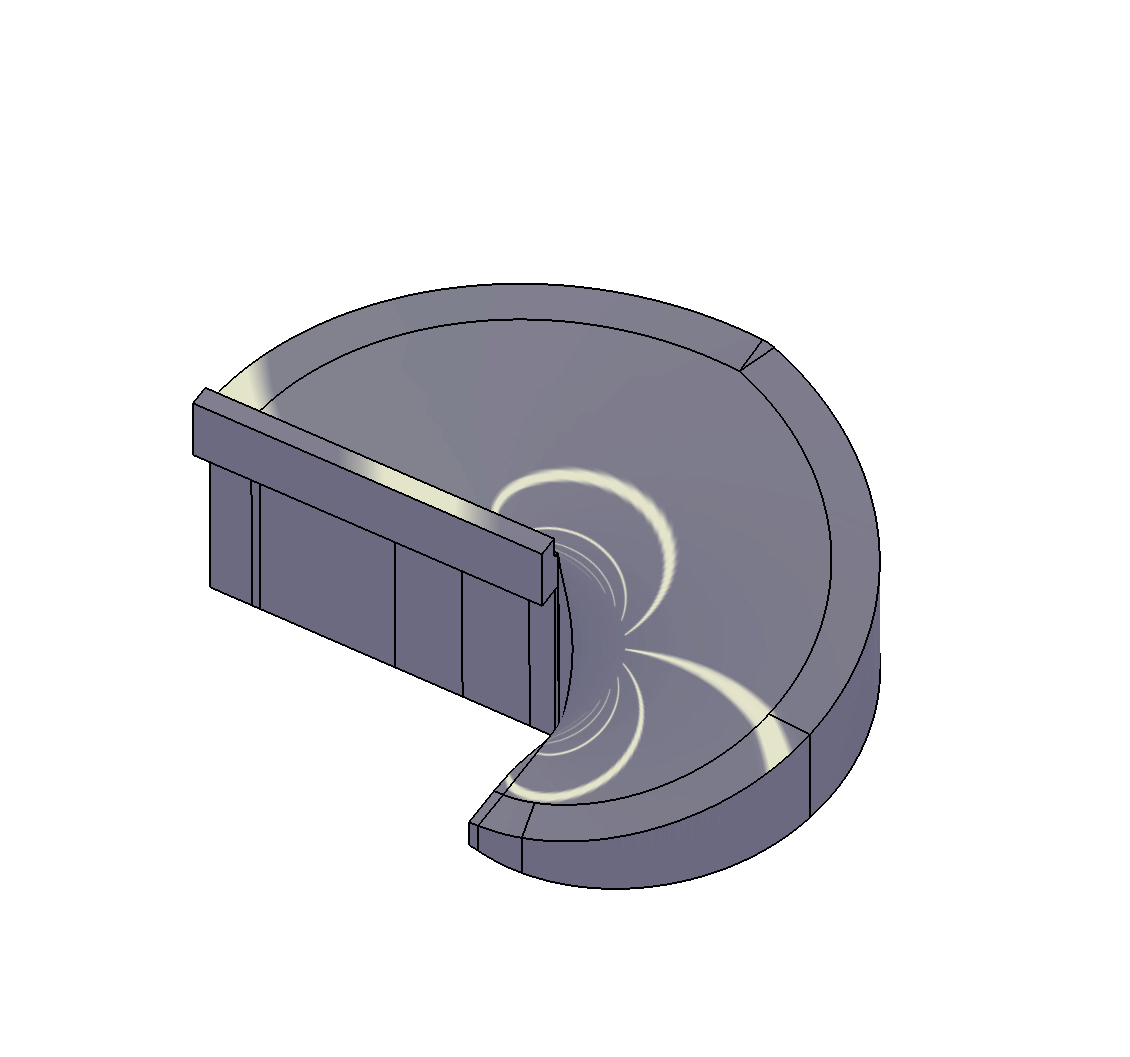
Nach der Entwicklung des Werkzeugs wurde die aktuelle Prototypenklinge in Originalgröße aus Glasfaser-Non-Crimp-Gewebe (NCF) und Epoxidharz hergestellt, per Handlaminierung hergestellt und bei Raumtemperatur ausgehärtet, gefolgt von einer Nachhärtung in einem Ofen bei erhöhter Temperatur und Anwendung einer Farbe in Marinequalität. Die Materialien wurden laut Falzon ausgewählt, um sowohl die strukturellen als auch die Kostenanforderungen für das Teil zu erfüllen. Die ineinandergreifenden Teilkomponenten sind verklebt – gewählt gegenüber mechanischer Befestigung für bessere Kontrolle und Maßhaltigkeit bei der Montage. „Der wahre Trick“, sagt er, „besteht darin, sicherzustellen, dass die Blätter ineinandergreifen können, aber sobald wir alles laminiert und miteinander verbunden haben, bildet es eine sehr steife Baugruppe, die die erforderliche strukturelle und hydrodynamische Formleistung erreicht.“
Die digitale Analyse der Steifigkeit und anderer mechanischer Eigenschaften der Struktur wurde mit Werkzeugen von MSC Software (Newport Beach, Kalifornien, USA) durchgeführt. „Dieses System ist viel effizienter, leichter und kann mehr Arbeit leisten als das ursprüngliche Design“, fügt Falzon hinzu.
Auf dem Weg zur kommerziellen Produktion
Laut Wren wird das anfängliche Produktionsziel von Kinetic NRG 950 Einheiten über einen Zeitraum von drei Jahren sein und dann von dort auf mehrere Tausend pro Jahr hochskaliert werden. Potenzielle Kunden, so Wren, können Privatpersonen und Unternehmen, Energieversorger und Kommunen sein – ein breites Spektrum, das die Vielseitigkeit des HEG-Konzepts unterstreicht. Die Systeme können als „Mini-Wasserkraftwerke“ in Bewässerungskanälen installiert oder stromabwärts von bestehenden Wasserkraftgeneratoren platziert werden, um Strom aus unzureichend genutztem Abfluss zu erzeugen, oder als ergänzende Energie für abgelegene Gemeinden oder Unternehmen, sagt er.
Derzeit wird der HEG-Prototyp im Originalmaßstab mechanischen Tests im Wasser unterzogen; Inzwischen werden großtechnische Herstellungsverfahren für die kommerzielle Produktion evaluiert.
ACS-A erwartet, das Schaufeldesign je nach den mechanischen Testergebnissen und den Anforderungen für eine möglichst kostengünstige Herstellung nach Bedarf weiter zu verfeinern. Laut Falzon untersucht ACS-A insbesondere automatisierte Preforming-Prozesse, „damit wir mit minimaler Handarbeit die richtige Form erhalten“, gefolgt von Light Resin Transfer Moulding (L-RTM) oder einem anderen schnelleren Prozess.
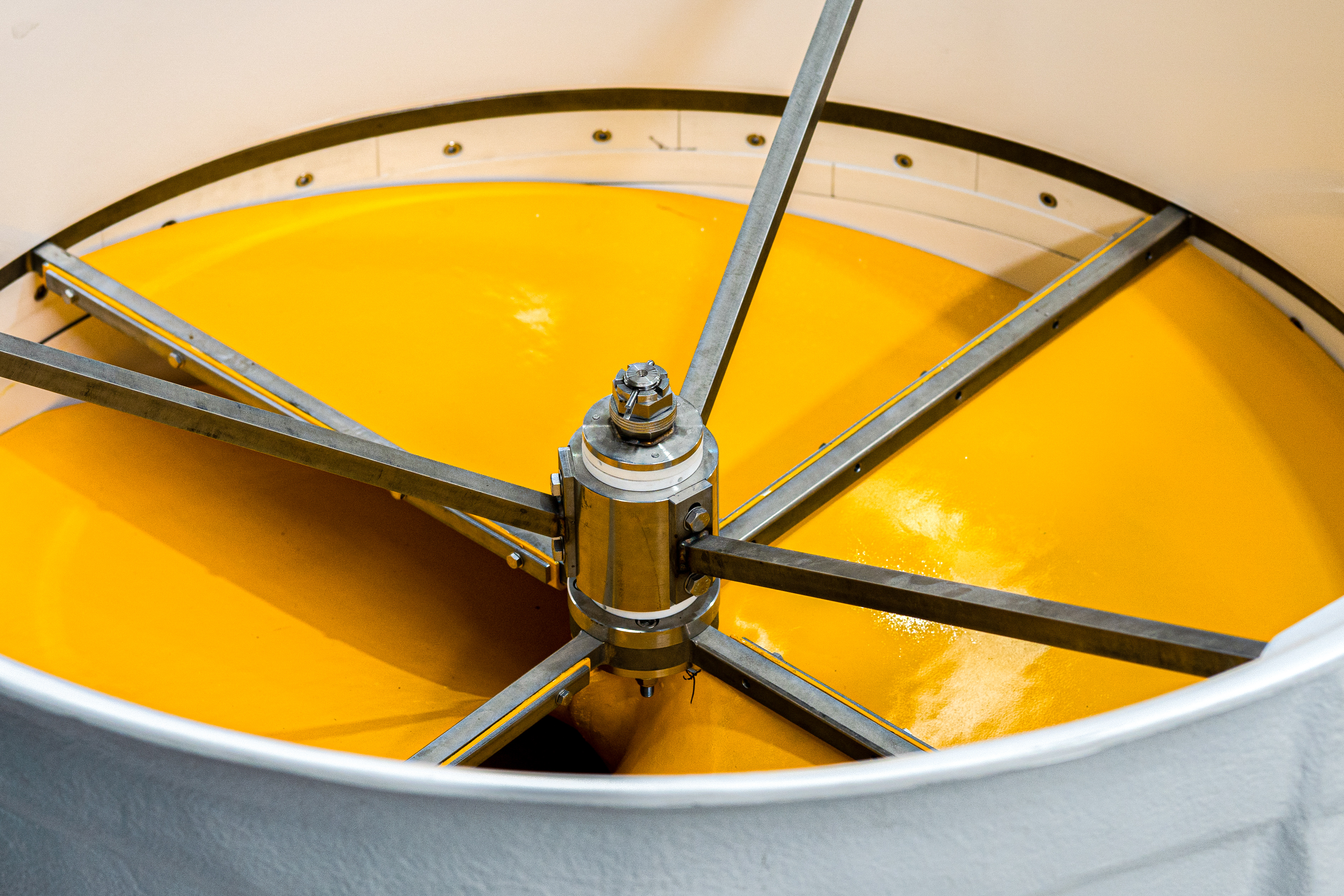
Methoden für die Turbinenmontage werden ebenfalls evaluiert, mit dem Ziel, sagt Wren, dass die Teilkomponenten der Schaufeln modular hergestellt und vor Ort montiert werden, um die Kosten und Herausforderungen beim Versand ganzer Einheiten im Originalmaßstab zu vermeiden und gleichzeitig lokale Beschäftigungsmöglichkeiten zu schaffen und die Installationskosten zu senken . Um dies zu ermöglichen, muss ACS-A möglicherweise auch die Art und Weise ändern, wie die Klingen ineinandergreifen und die Anzahl der Unterkomponenten in jeder Baugruppe. „Wir werden immer noch die vollständigen Klingen in ihrer ursprünglichen Form haben, das wird immer noch ein wichtiger Teil davon sein“, sagt Wren, „aber wir können die Übergänge ändern, um die gleiche Form in weniger Komponenten einfacher zu machen Montage vor Ort.“
Die beiden Unternehmen prüfen auch die Umwandlung metallischer Komponenten der Turbine in Verbundwerkstoffe, um das Gewicht der Gesamtbaugruppe zu reduzieren. „Wir werden Glas verwenden, wo es angebracht ist, und Kohlefaser, wo es angebracht ist, aber letztendlich müssen wir einen Preis für die Technologie erzielen, um die Kosten der Energieerzeugung für das System kostendeckend zu machen“, sagt Falzon.
Da sich der Konstruktions- und Herstellungsprozess der Optimierung nähert, besteht die nächste Herausforderung laut Wren darin, die richtigen Investitions- und Fertigungspartnerschaften zu sichern, um auf kommerzielle Mengen zu skalieren.
Harz
- Smart-Badge-Referenzdesign mit Bluetooth-SoC
- Bewältigen von Designherausforderungen bei der Präzisions-DC-Energiemessung
- Megger spendet für das Windturbinen-Energieprogramm von Iowa Lakes
- Überlegungen und Beschränkungen des Energieübertragungssystems
- CompositesWorld SourceBook 2022
- CETEC-Initiative zur Kommerzialisierung der Technologie für die vollständige Recyclingfähigkeit von Verbundwerkstoff-Windturbinenblättern
- Continuous Composites, Siemens Energy verwendet Hochleistungsmaterialien für Stromgeneratoren
- Verbundwerkstoffe als Karosserieverstärkungen
- Hochleistungsverbundwerkstoffe in Israel
- Wasserkraft verstehen