Zukünftige Verbundstoffherstellung – AFP und additive Fertigung
„Überdrucken“ auf vorgefertigte CFK-Oberflächen und Halterungen (oben links) , hybridisierende Prozesse wie 3D-Druck und Filament Winding (oben rechts) , 3D-Druckkerne auf AFP-Laminaten und AFP-Skins auf 3D-gedruckte Kerne (rechts unten) und CEAD AM Flexbot 3D-Druck bei 45 Grad (unten links) . Bildnachweis:TU München, Lehrstuhl für Carbon Composites
Im September besuchte ich das virtuelle Symposium „FUTURE COMPOSITE MANUFACTURING – AFP &AM“ zum Thema Automated Fiber Placement (AFP) und Additive Manufacturing (AM). Gastgeber dieses Symposiums war der Lehrstuhl für Carbon Composites (LCC) am Technische Universität München (TUM, München, Deutschland). An der Veranstaltung war auch der Forschungspartner der TUM, die Australian National University (ANU, Canberra) beteiligt. Das Symposium begutachtete die F&E-Fähigkeiten von Verbundwerkstoffen sowohl an der TUM als auch an der ANU sowie abgeschlossene und laufende Projekte mit Industriepartnern wie AFPT, Airbus, BMW, CEAD, DLR, Fraunhofer, GKN Aerospace, INOMETA, SGL Carbon und Victrex.
Die Zusammenarbeit der TUM mit ANU begann 2010 mit dem AutoCRC-Projekt zur Entwicklung von komprimierten Erdgasspeichern (CNG) aus thermoplastischen Verbundwerkstoffen. Seitdem wurde die gemeinsame Forschung und Entwicklung fortgesetzt, einschließlich der Bildung des Zentrums für die automatisierte Herstellung von Advanced Composites (AMAC) des Australian Research Council und dreier Hauptschwerpunkte an der ANU:
- Materialverbesserung
- Nanoskalige Materialien und Beschichtungen zur Verbesserung der funktionellen Eigenschaften von Kohlenstoffverbundwerkstoffen
- Graphenverstärkte Prepreg-Bänder für thermische und elektrische Leitfähigkeit
- Laser-AFP
- Projekt mit Ford zur Entwicklung von Verbundstahl
- Digitale Steuerung des Heiz-Bias, z.B. Prozessstabilität für Ecken/3D-Geometrien
- Erweiterte Diagnostik mit Röntgen-CT
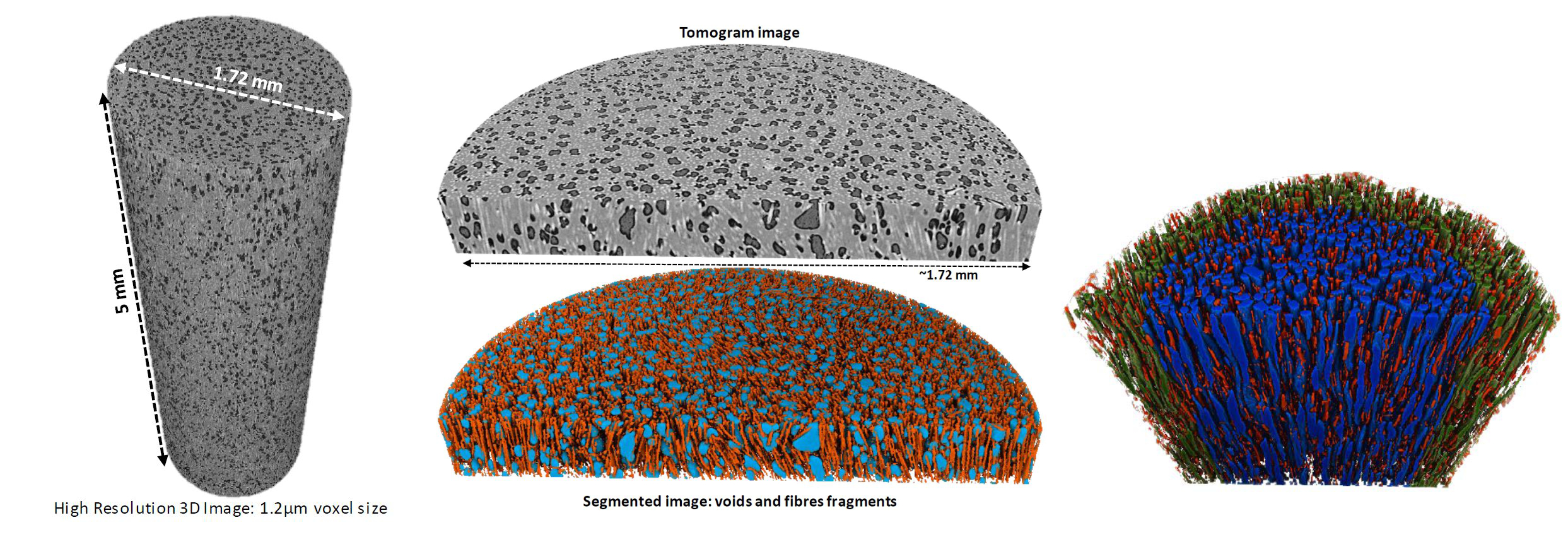
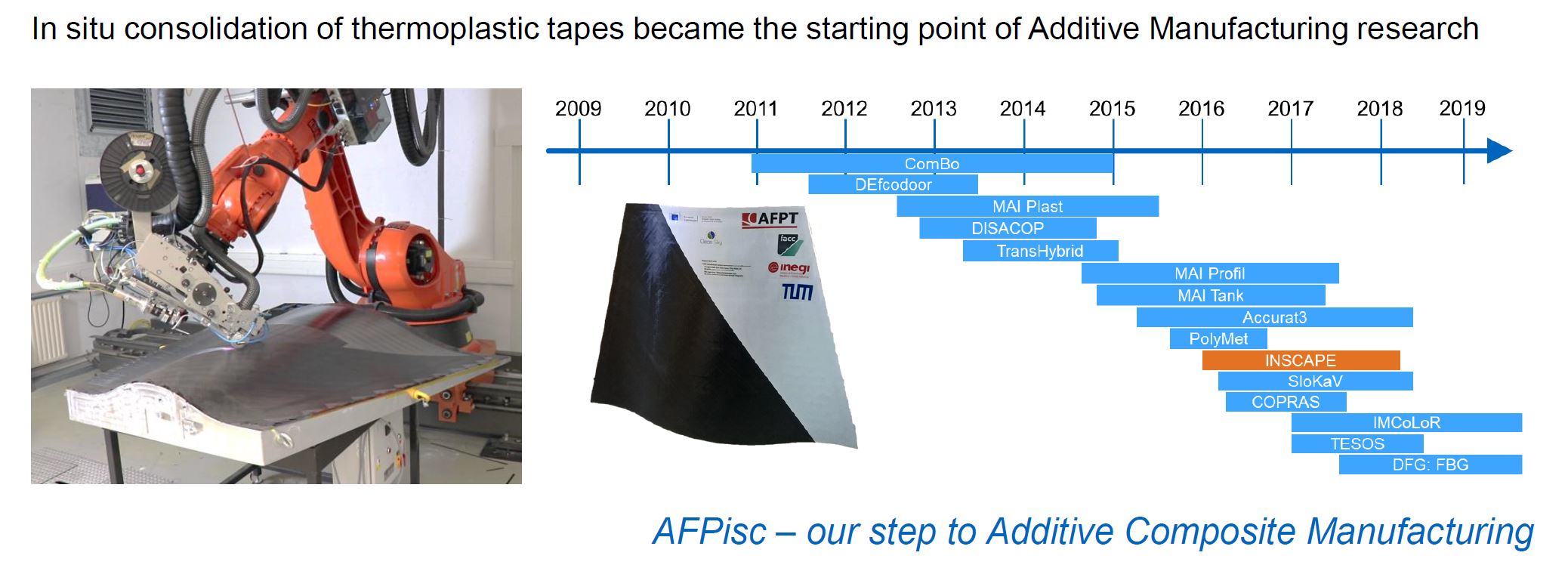
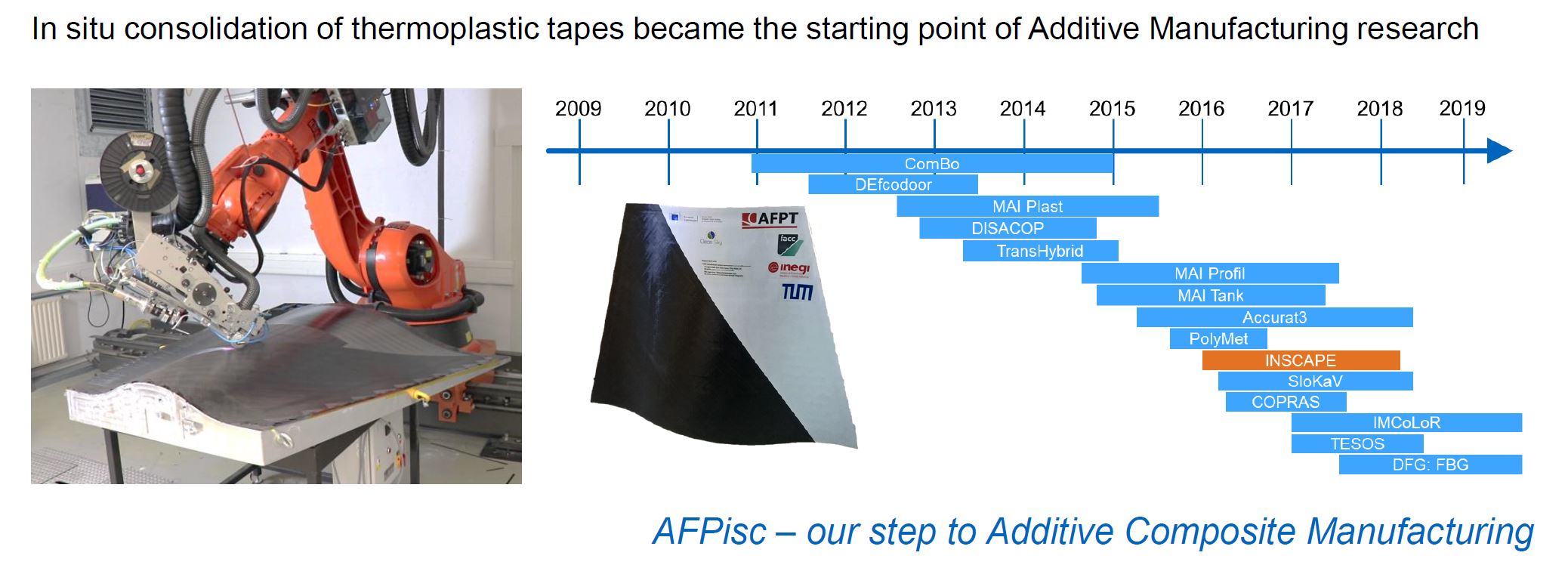
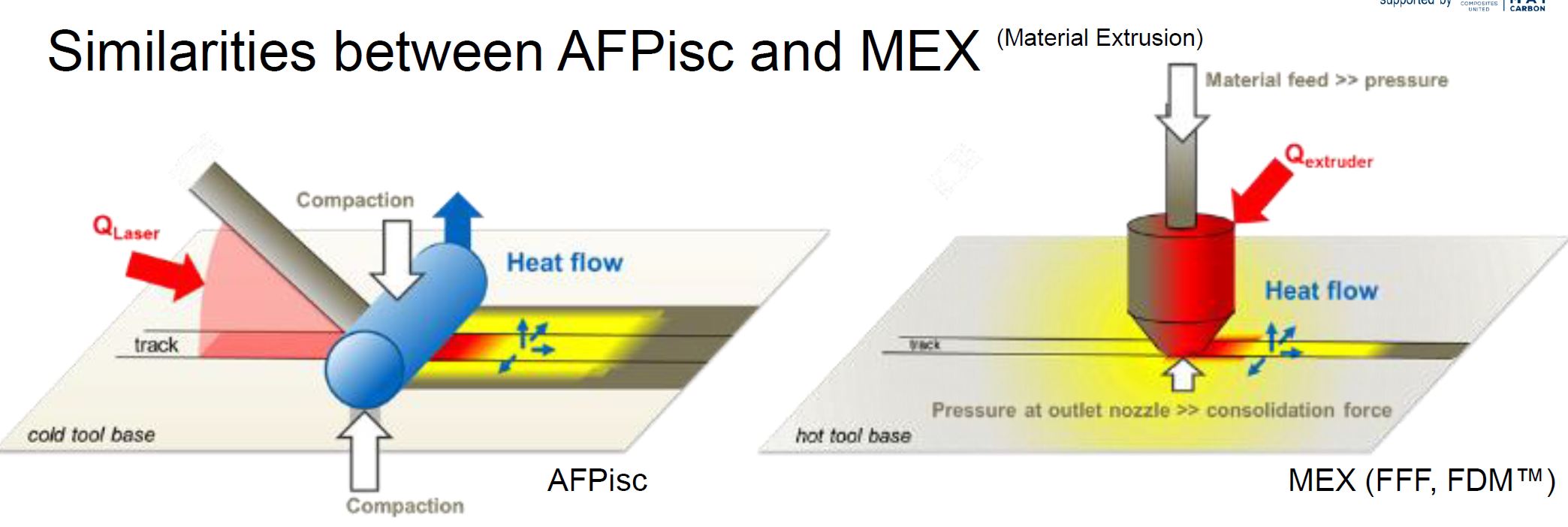
Er diskutierte die Ähnlichkeiten zwischen der Materialextrusion (MEX), dem am häufigsten verwendeten Verfahren für den 3D-Druck von faserverstärkten Verbundwerkstoffen, und AFP ISC:
- Lokale, wiederkehrende Wärmebehandlung
- Schichtbasiertes Design und orthotrope Materialeigenschaften
- Materialplatzierung entlang programmierter 2D- und 3D-Pfade und thermische Aktivierung zwischen den Schichten.
Drechsler diskutierte dann den zukünftigen Bedarf an Verbundwerkstoffen und wie die Kombination von AFP und MEX Lösungen bieten könnte, einschließlich kurzfristiger Werkzeuge und längerfristiger Hochleistungs-Leichtbaustrukturen, die sowohl kosteneffizient als auch ökologisch nachhaltig sind.
Um die Fähigkeiten von LCC zu skizzieren, gab Drechsler einen Überblick über seine MEX-Ausrüstung sowie vergangene und laufende F&E-Projekte in der additiven Fertigung.
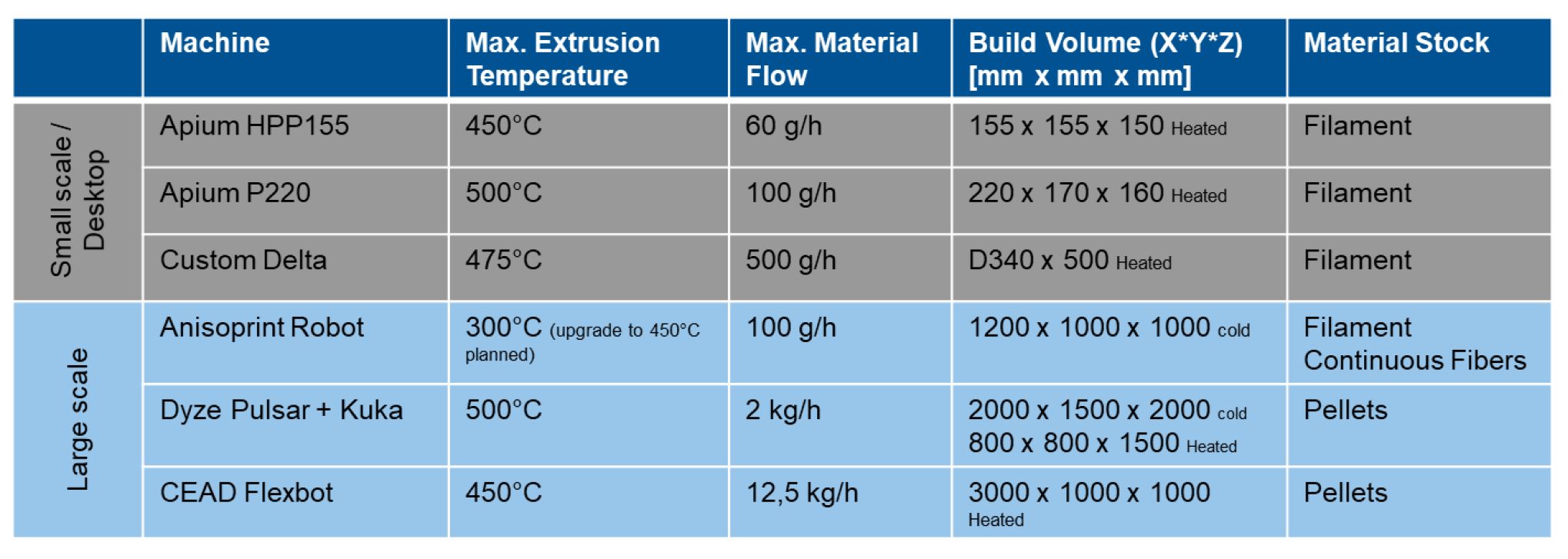
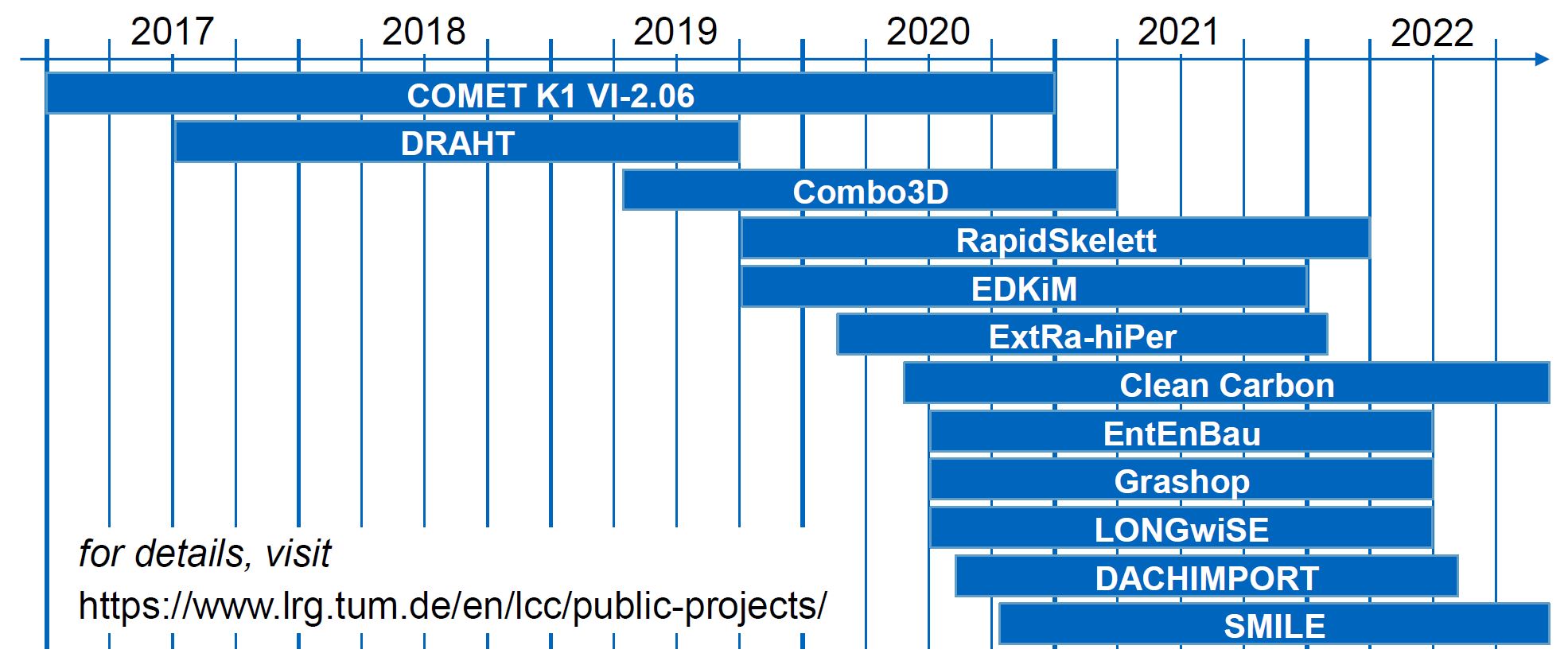
In Bezug auf ISC AFP umfassen die jüngsten und laufenden Entwicklungen bei LCC:
- Ein Behälterwickelkopf zur Unterstützung der Industrialisierung von Strukturen wie Druckbehältern, einschließlich Wasserstoffspeichertanks
- Regelung der Laserstrahlerwärmung
- Verwendung einer flüssigkeitsgekühlten Walze zur Konsolidierung
- Charakterisierung von Bändern zur Optimierung des ISC.
Die Entwicklungen von LCC im Bereich MEX und 3D-Druck wurden in den nächsten 2 Tagen in mehreren Präsentationen weiter untersucht.
CEAD und großflächiger 3D-Druck
Die nächste Präsentation nach Drechslers Keynote hielt Maarten Logtenberg, Executive Director von CEAD (Delft, Niederlande). CEAD wurde 2014 gegründet und hat kommerzielle Systeme basierend auf seiner Continuous Fiber Additive Manufacturing (CFAM)-Technologie sowohl als Gantry-basierte geschlossene Zelle (CFAM Prime) als auch als roboterbasiertes System (AM Flexbot) verkauft. LCC besitzt letzteres (siehe Tabelle oben) und arbeitet mit LCC an mehreren Projekten zusammen (siehe CW Artikel über CEAD und seine Arbeit mit TUM LCC).
Zu den Highlights der Präsentation von Logtenberg gehörten die Entwicklung von Hybridlösungen von CEAD, die CNC-Fräsen, große beheizte Druckbetten (1,2 m x 3 m und 1,2 m x 2 m) und beheizte Rotationsdruckbetten integrieren. Es verfolgt auch noch größere Zellen und den 45-Grad-Druck sowie den Druck von faserverstärkten Werkzeugen für die Serienautoklavenfertigung von Verkehrsflugzeugteilen.
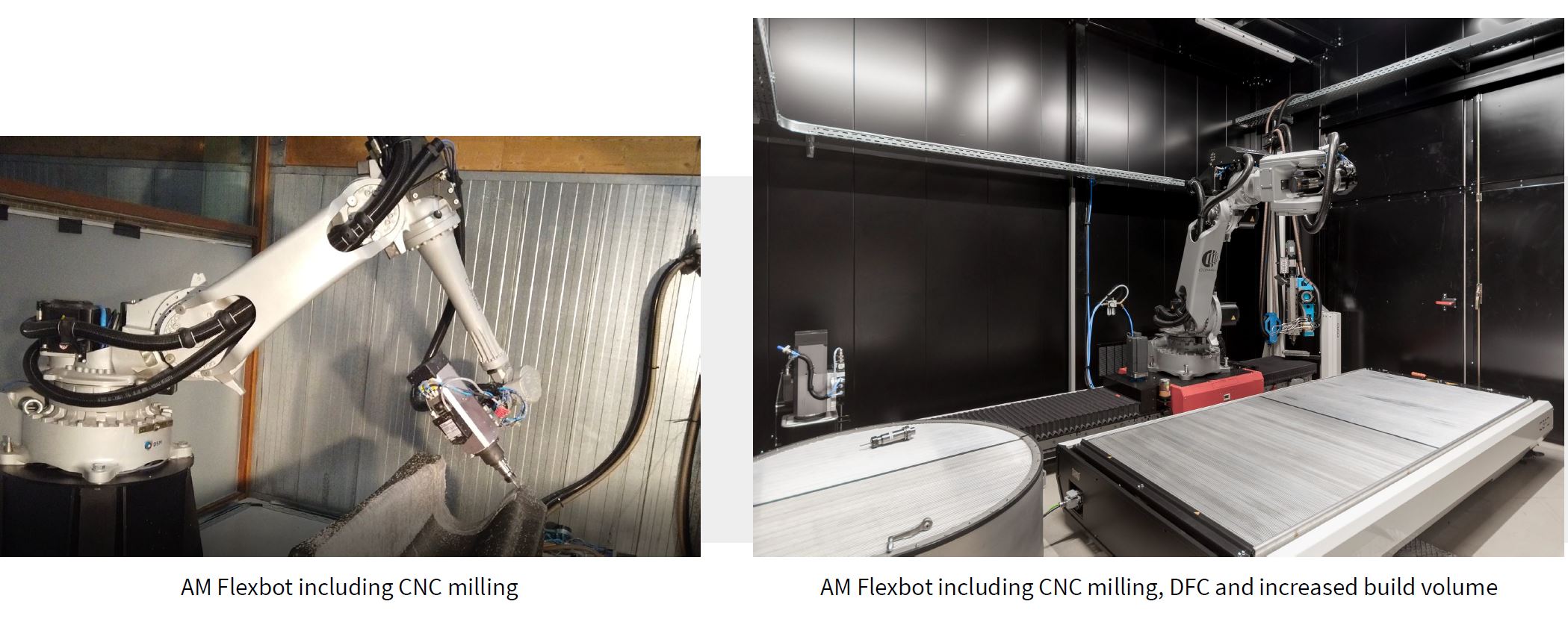
Logtenberg stellte fest, dass eine der größten Herausforderungen für 3D-gedruckte Autoklavenwerkzeuge die thermische Ausdehnung ist und Werkzeuge, die viel größer als 4 Meter sind, dazu neigen, sich zu stark auszudehnen (siehe „Hybrid, großformatige additive Werkzeuge“), was es schwierig macht, durch die Werkzeugkonstruktion ausreichend zu kompensieren . Die von ihm vorgeschlagene Lösung besteht darin, die bisher meist verwendete Schnittfaserverstärkung durch Endlosfasern zu ersetzen, die von Systemen wie AM Flexbot aufgebracht werden.
Dieser Weg nach vorn wurde in der Präsentation „Einführung von 3D-gedruckten Spurverstärkern für die Produktion von Verbundklappen . unterstützt “ von Thomas Herkner bei GKN Aerospace in München, Deutschland. Diese 3D-gedruckten CFK-Verstärker werden als Werkzeug bei der Herstellung von CFK-Landeklappen für die Airbus A350 und A330 verwendet. Obwohl in diesem erfolgreichen Programm bei GKN geschnittene Faserverstärkungen verwendet wurden, zeigte Herkner eine Roadmap für die weitere Entwicklung, die die Verwendung von Endlosfasern in 3D-gedruckten Werkzeugen sowie schließlich in den Flugzeugteilen selbst umfasste.
Dieser Weg nach vorn wurde von LCC-Forschung Patrick Consul in einem kürzlich erschienenen CW-Blog gut erklärt:
Consul präsentierte auch auf dem TUM-Symposium das Prozessdesign für großmaßstäbliche, extrusionsbasierte AM. Er diskutierte, wie die unten gezeigten Glas- und Phasenübergänge die größte Änderung der Materialeigenschaften von geschnittenen faserverstärkten Pellets darstellen, die in 3D-Drucksystemen wie CFAM und AM Flexbot geschmolzen und extrudiert werden.
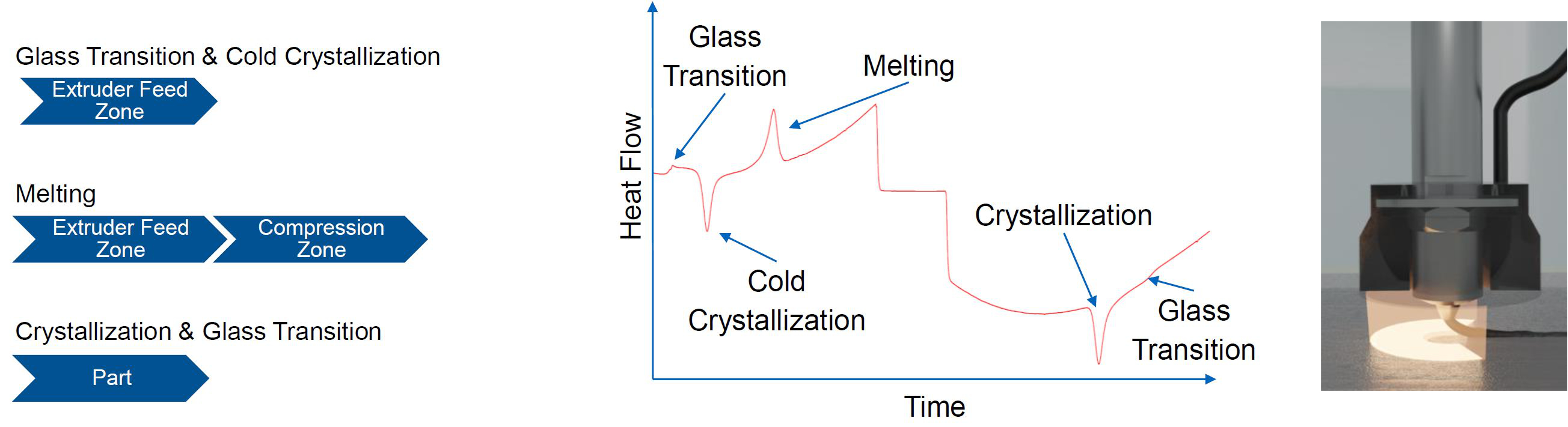
Die Arbeit von Consul hat analysiert, wie MEX-Parameter wie Polymerviskosität und Extrusionstemperatur und Drehmoment die Kristallinität im gedruckten Verbundmaterial beeinflussen, was wiederum die Fähigkeit beeinflusst, Schichten während des 3D-Drucks miteinander zu verschweißen. Neben dieser Schicht-zu-Schicht-Verbindung hat Consul auch die Faserausrichtung und Eigenspannung in den gedruckten Schichten untersucht. Eine vorgestellte Lösung war die Verwendung eines Lasers zum Vorwärmen des Substrats während des Druckens – heute weit verbreitet in der ISC-AFP von thermoplastischen Verbundwerkstoffen –, wodurch das Wissen von AFP auf AM übertragen wurde. Erste Experimente verwendeten einen Ring steuerbarer Laserdioden.
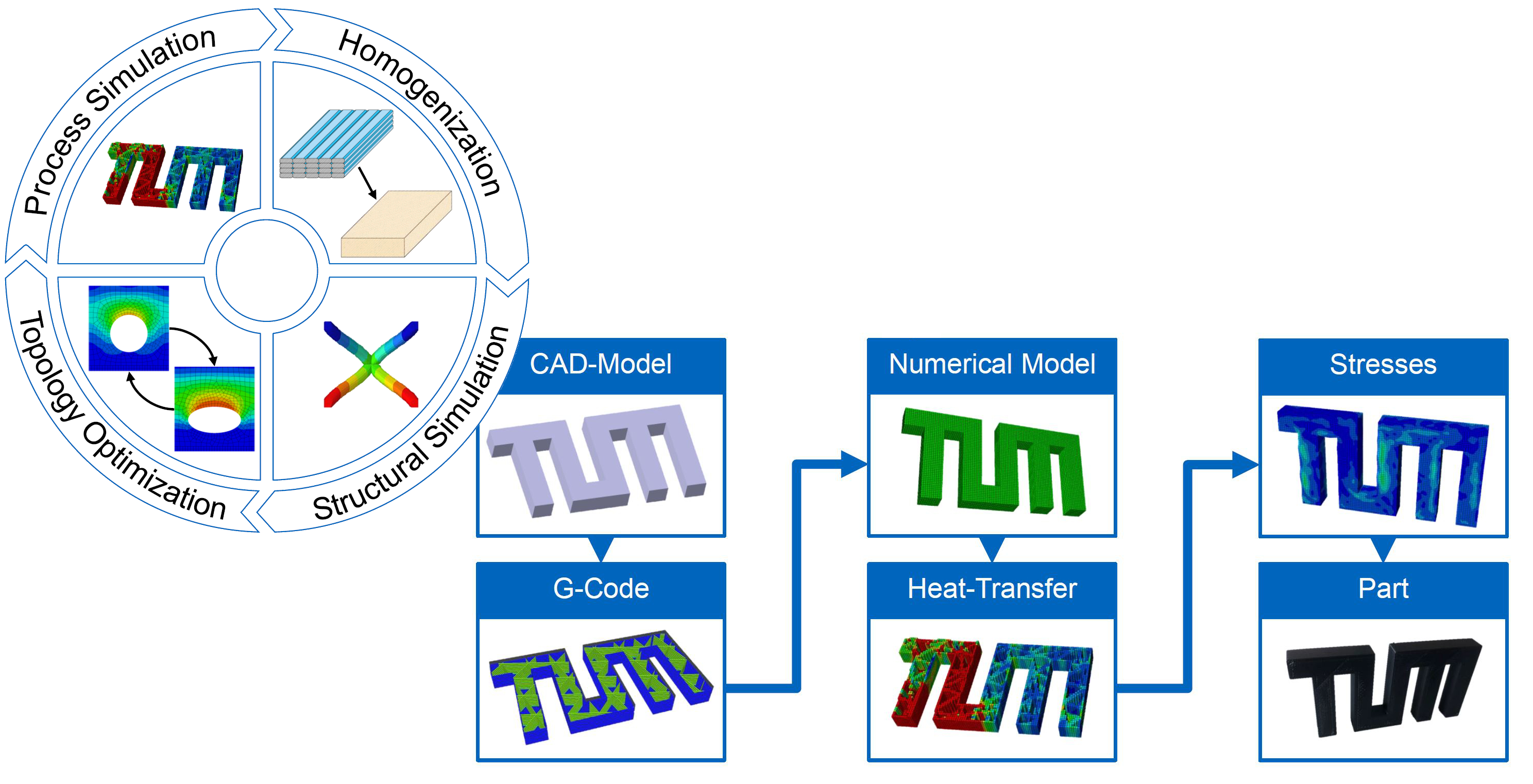
Der Kollege von Konsul, Matthias Feuchtgruber, präsentierte später am Tag, wie er vom Prozessdesign und der Materialcharakterisierung zur Entwicklung einer virtuellen Prozesskette für Composites AM übergeht.
Alexander Matschinski präsentierte dann die Integration von Endlosfasern in Verbundwerkstoffe AM und präsentierte die folgende Tabelle, die die Grundlage für die geänderte Tabelle wurde, die ich in CW verwendet habe 's Next-Gen Supplement-Artikel zum Endlosfaser-3D-Druck. Matschinski sprach auch über die Arbeit im Design von Endlosfaser-AM-Strukturen und die zukünftige Entwicklung des „Überdruckens“ auf vorgefertigte CFK-Teile und -Oberflächen.
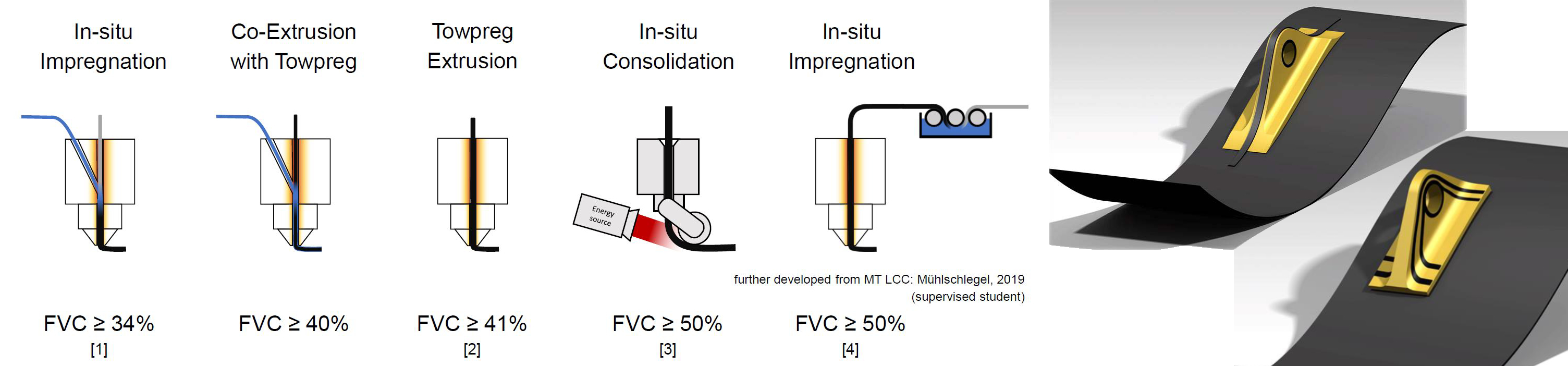
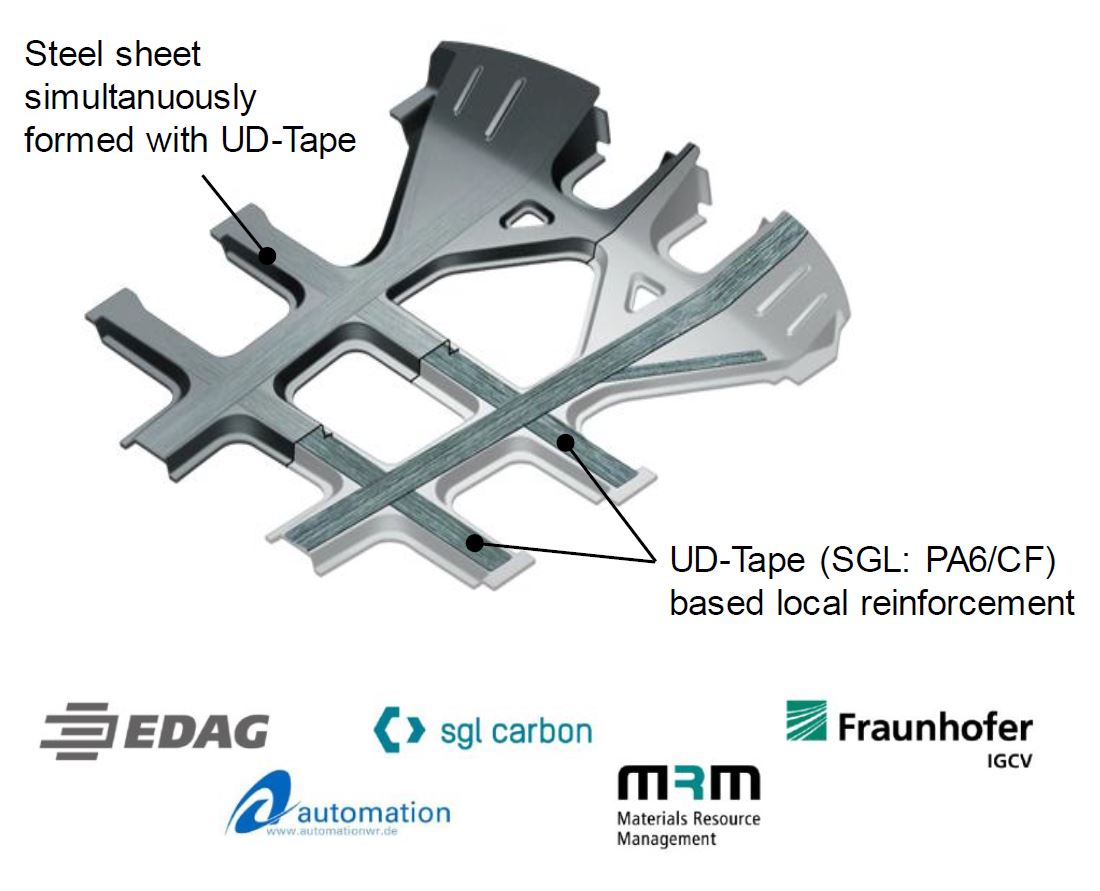
Weitere interessante Anwendungen von Endlosfasern zeigte Dr.Christopher Ebel von der SGL Carbon, unter anderem zur Verstärkung von Stahlunterbodenstrukturen für Automobile, zur Reduzierung der Teileanzahl von 37 auf 9 und zur Gewichtseinsparung um 41 %. Ein weiteres Konzept war das 3D-Wicking mit Towpreg imprägniert mit Snap-Cure-Epoxidharz für belastungsoptimierte Strukturen. Dieser digital gesteuerte Ansatz beginnt mit der Vereinfachung komplexer Lasten und der Topologieoptimierung, gefolgt von der automatisierten Fertigung. Die resultierenden Teile können den Formschluss von Einsätzen in Strukturen ausnutzen, was eine Lasteinleitung ohne Steifigkeitsverlust ermöglicht. Für solche Einsätze können die neuesten 3D-Metalldruckverfahren verwendet werden, was die Effizienz des Lasthandlings und die Kostensenkung weiter optimiert.
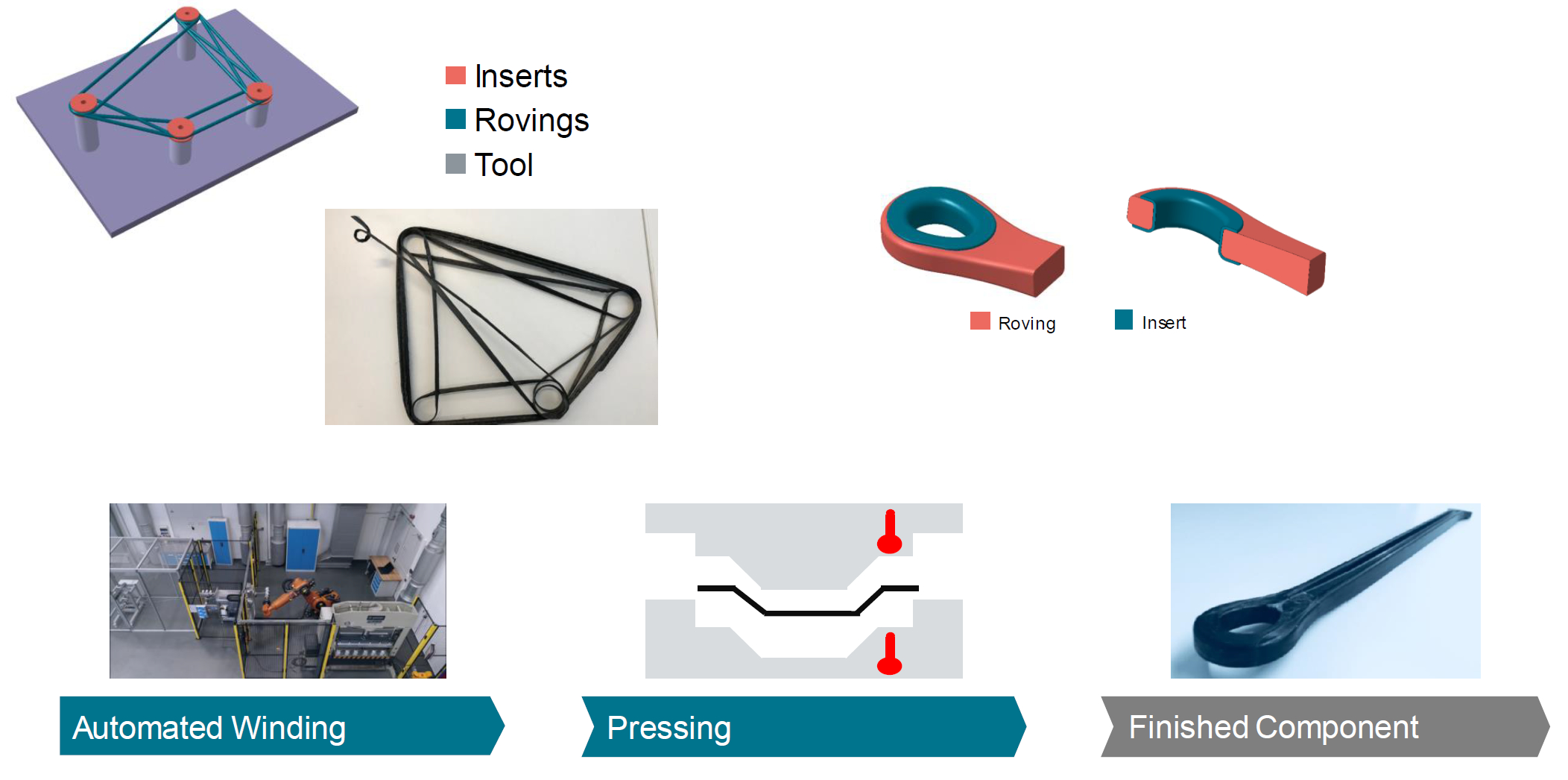
Sebastian Nowotny vom DLR diskutierte die Kombination von 3D-Druck mit ISC AFP von thermoplastischen Verbundwerkstoffen, einschließlich des 3D-Drucks auf AFP-Laminaten und AFP auf teilweise offenen 3D-gedruckten Strukturen. Erste Experimente umfassen den 3D-Druck eines Kerns auf eine vorgefertigte CFK-Haut und das anschließende Auflegen von AFP/Band auf den 3D-gedruckten Kern. Es wurden Proben hergestellt und dann einem Zugschertest unterzogen, um die Haut-Kern-Verbindung zu bewerten.
Diashow-Titel
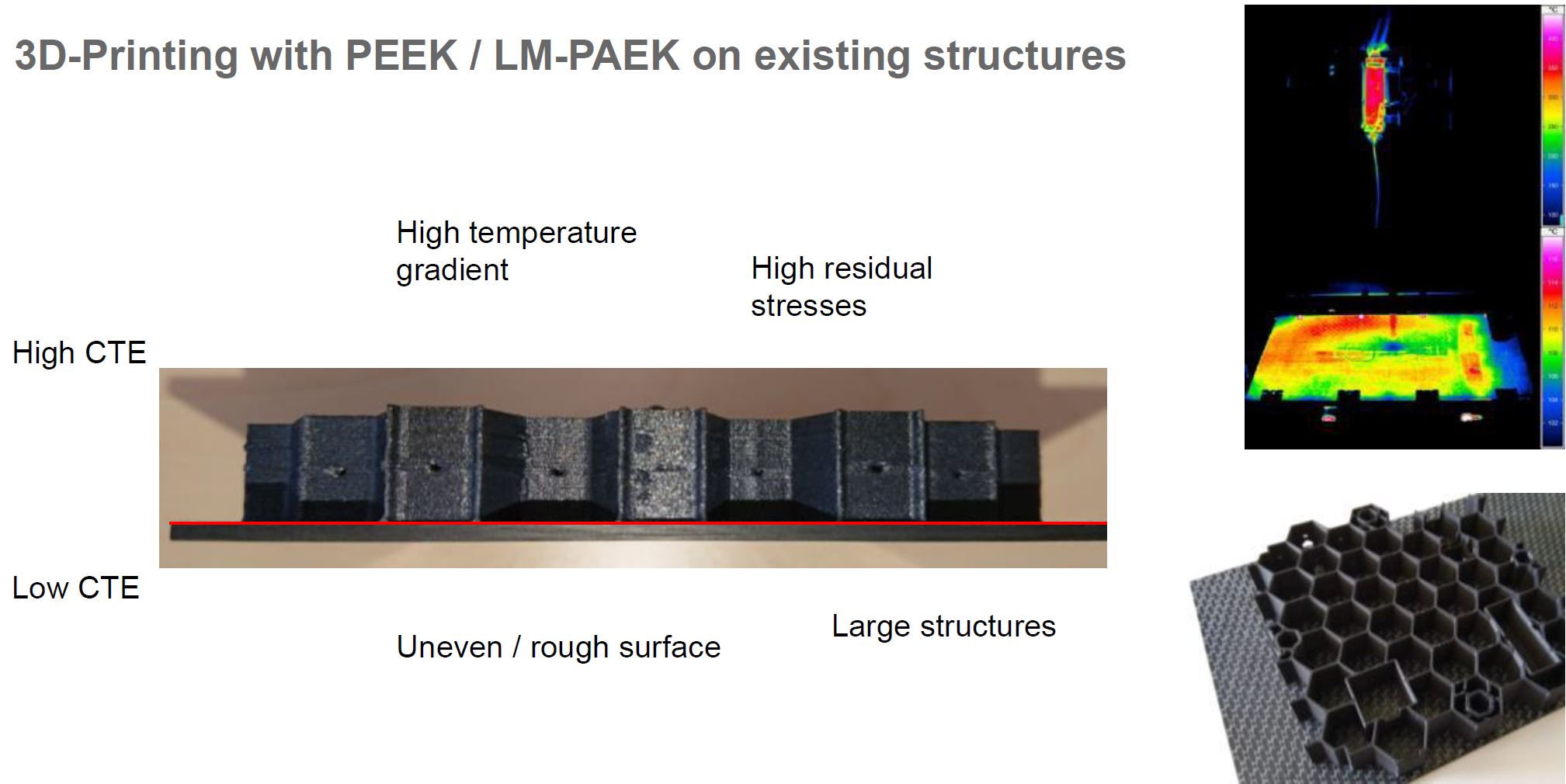
Bildnachweis:Sebastian Nowotny, DLR, TUM Symposium Sept. 2020
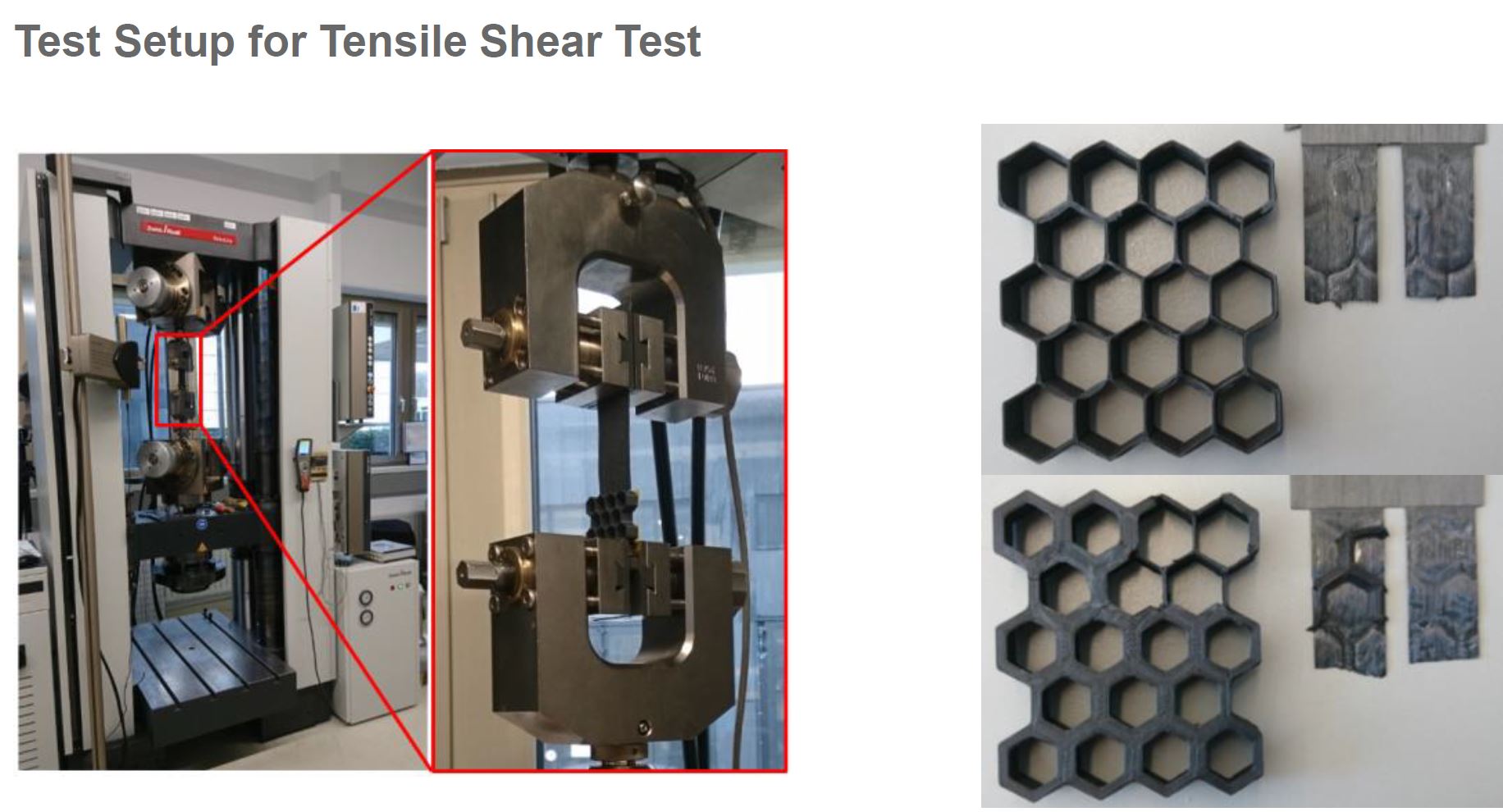
Zugscherprüfung von Coupons, die mit Hybrid-3D-Druck und AFP hergestellt wurden. Bildnachweis:Sebastian Nowotny, DLR, TUM Symposium Sept. 2020
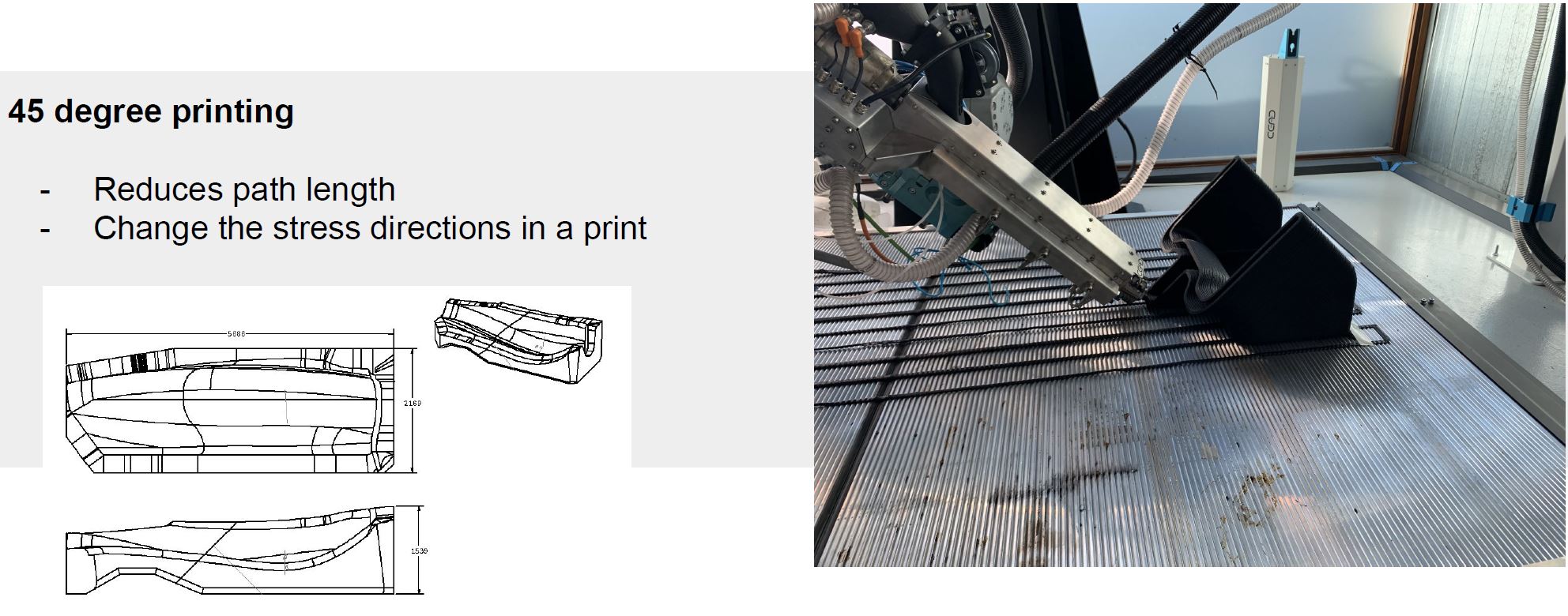
Bildnachweis:CEAD, TUM Symposium Sept. 2020
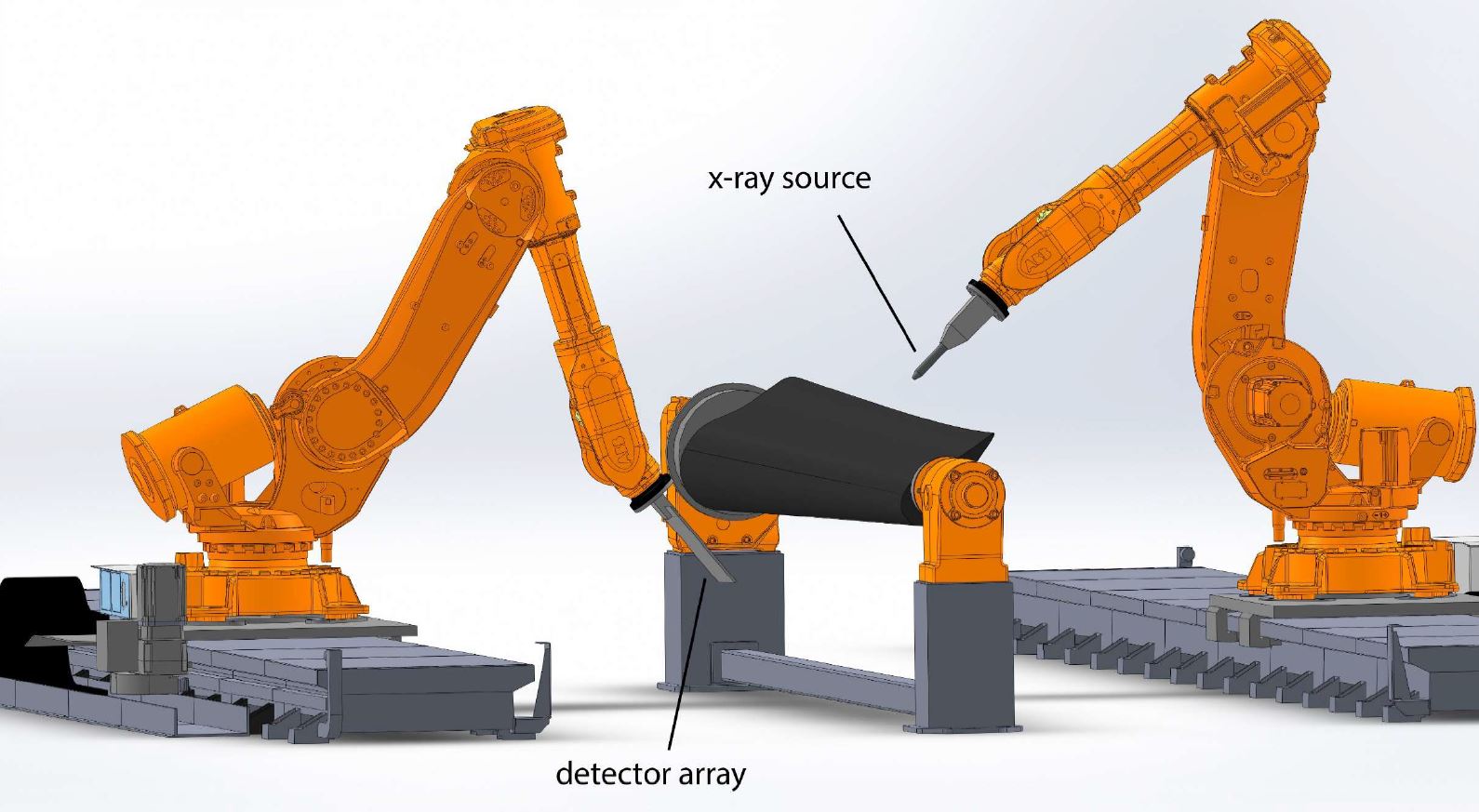
Zukünftige Anwendung der Computertomographie bei der Herstellung von Verbundwerkstoffen. Bildnachweis:Australian National University, TUM Symposium Sept. 2020
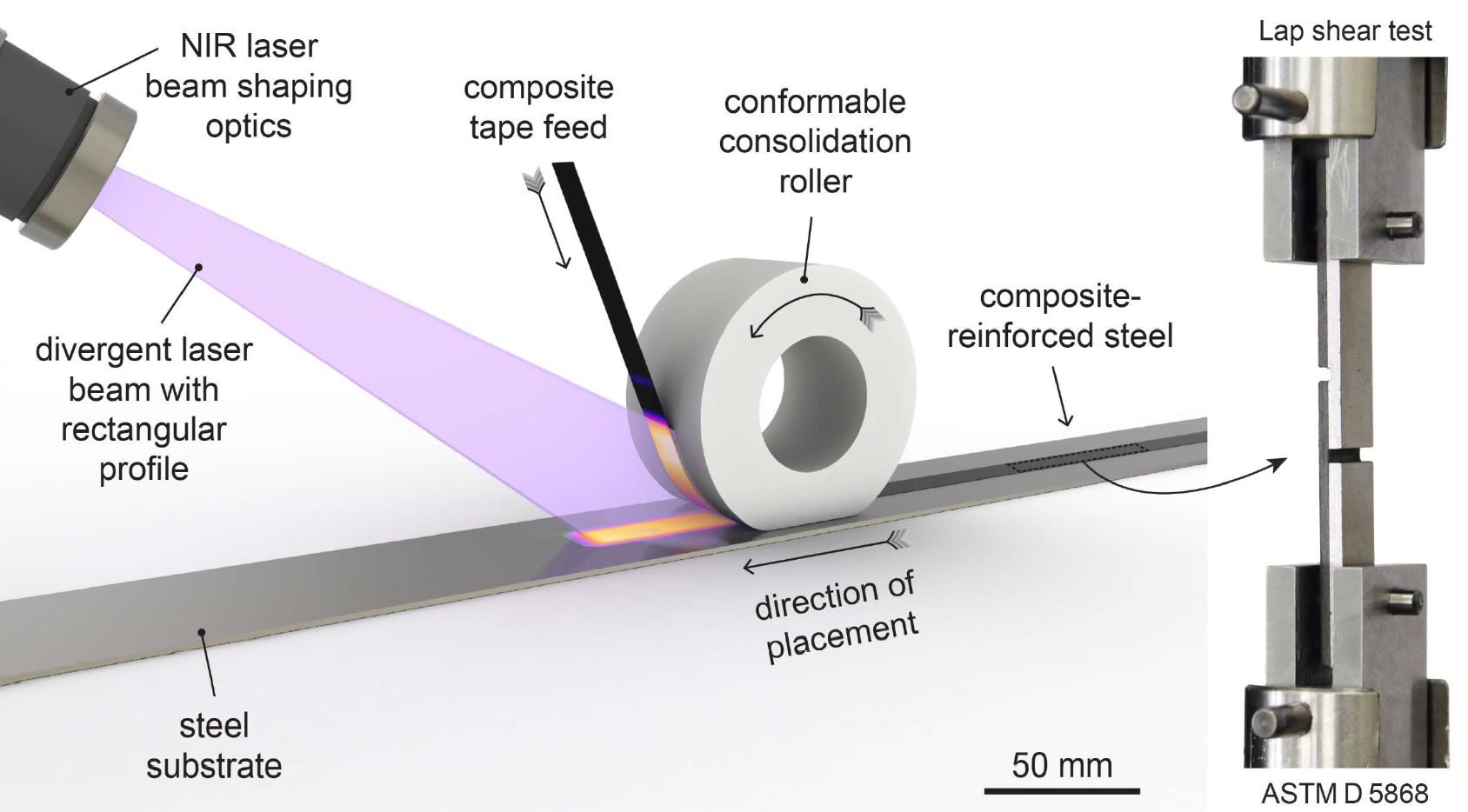
Entwicklungsarbeit mit Laser-AFP zur Erzeugung hybrider CFK-Metall-Strukturen. Bildnachweis:Australian National University, TUM Symposium Sept. 2020
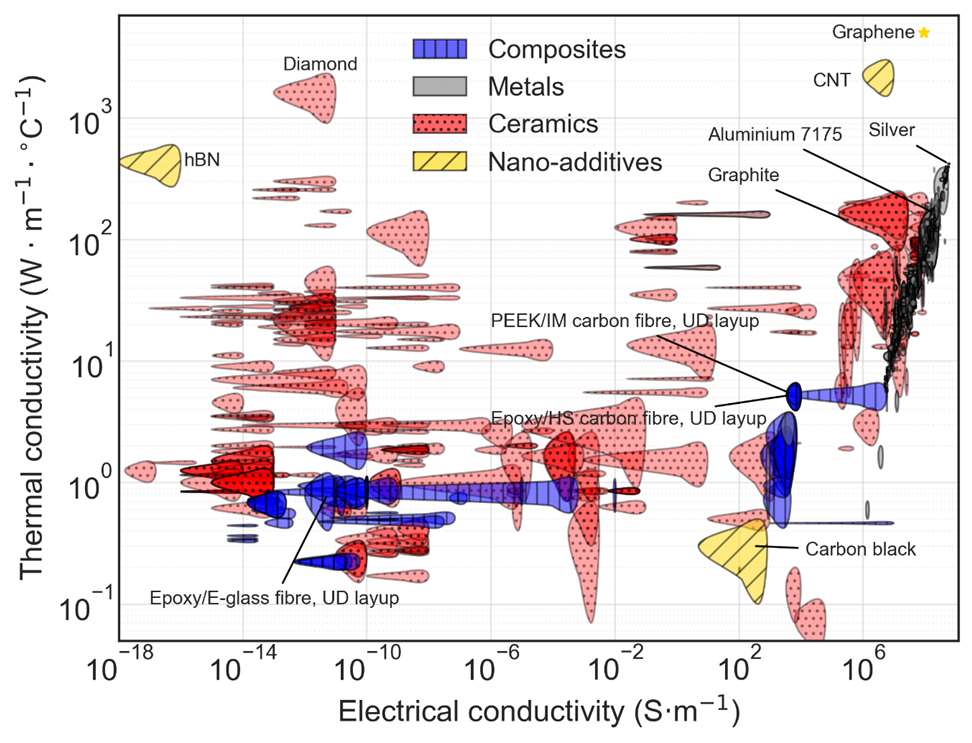
Graphenverstärkte Prepreg-Bänder für thermische und elektrische Leitfähigkeit. Bildnachweis:Australian National University, TUM Symposium Sept. 2020
Vorherige NächsteChristian Weimer, Leiter der Materialabteilung bei Airbus Central Research &Technology, diskutierte den Endlosfaserdruck als Teil der sich entwickelnden Technologielandschaft mit dem Ziel, Gewicht bei reduzierten Kosten und erhöhter Nachhaltigkeit zu reduzieren, die erreicht werden müssen, damit Verbundwerkstoffe einen Platz in zukünftigen Flugzeugen sichern. Er betonte, dass wirklich effiziente 3D-Verbundwerkstoffe Folgendes verwenden müssen:
- Die richtigen Rohstoffe und Zwischenprodukte – Fasern, Halbzeug
- Effiziente Prozesse und Schnittstellen – AM-Thermoplaste, Spritzguss
- Angepasstes Design und Dimensionierung – integral, vollständig 3D-lastoptimiert)
- Oberfläche und Funktionalität – ESN (elektronische Seriennummer), SHM (Structural Health Monitoring)
Er erörterte auch den Bedarf an biologisch gewonnenen Fasern und Harzen, um dringende Klima- und ökologische Nachhaltigkeitsziele zu erreichen.
Auf dem TUM-Symposium gab es viele weitere Präsentationen, darunter auch Zusammenfassungen der Arbeit an der ANU, und alle waren sehr interessant, um zu zeigen, wie sich Verbundwerkstoffe weiterentwickeln und wie das LCC in Zusammenarbeit mit Partnern weltweit weiterhin vorstellt, was Verbundwerkstoffe leisten und unsere Branche voranbringen können.
Harz
- Einführung von AM Fridays und Additive Podcast
- Additive Fertigung mit Verbundwerkstoffen in der Luft- und Raumfahrt und Verteidigung
- Essentium und Lehvoss kooperieren bei der Entwicklung von Materialien für die additive Fertigung
- Robotik und die Zukunft von Produktion und Arbeit
- AMRC und Prodrive arbeiten zusammen, um die Herstellung recycelbarer Verbundkomponenten voranzutreiben
- PES-Additiv erhöht die Bruch- und Mikrorissbeständigkeit in Epoxidverbundwerkstoffen
- Nachhaltige Thermoplaste und additive Fertigung bilden in Colorado eine Allianz
- Was ist additive Fertigung? - Typen und Arbeitsweise
- Automatisierung und die Zukunft der digitalen Fertigung?
- Additive Fertigung in Medizin und Zahnmedizin