Kombination von AFP mit 3D-Druck für die Produktion flexibler Teile
Electroimpact (Mukilteo, Washington, USA) wurde 1986 gegründet und ist ein globaler Anbieter von Werkzeugen und Produktionsautomatisierung, der behauptet, der weltweit größte Integrator von Flugzeugmontagelinien zu sein. Im Bereich Verbundwerkstoffe ist das Unternehmen für seine fortschrittliche Technologie in automatisierten Hochgeschwindigkeits-Tapelaying- (ATL) und Fiber Placement-(AFP)-Systemen bekannt. Electroimpact betont, dass es ingenieursgetrieben ist – 400 seiner 600 Mitarbeiter haben Ingenieurabschlüsse – und Entwicklungen, die vom gleichen Ingenieurteam konzipiert und abgeschlossen werden, vom Konzept über das Design, die Herstellung, die Installation und die Übernahme durch den Kunden.
Im Juli 2020, CW berichtete über das neue Scalable Composite Robotic Additive Manufacturing (SCRAM)-System des Unternehmens. Hier teilen wir unser Interview mit einem Teil des Engineering-Teams von SCRAM:Projektmanager Cody Brown, Verfahrensentwicklungs- und Steuerungsingenieur Ryan Bischoff und leitender Maschinenbauingenieur Reese Allen. Ihre Erklärung des Ursprungs, der Implementierung und der Zukunft dieser additiven Fertigung mit Endlosfasern gibt Einblicke, wie die nächste Generation der Verbundwerkstoffproduktion aussehen könnte.
Anstreben eines groß angelegten FDM
Braun :„Wir haben vier Jahre daran gearbeitet, wollten aber warten, bis wir zeigen konnten, dass es echte Teile in Luft- und Raumfahrtqualität produzieren würde. Unser ursprüngliches Ziel war es, einen großformatigen 3D-Drucker für die Fused Filament Fabrication (FFF) herzustellen, der komplexe Teile mit Endlosfasern herstellen kann. Wir hatten nicht die Absicht, einen AFP-Prozess zu entwickeln, aber als wir versuchten, das Faservolumen zu erhöhen und eine höhere physikalische Festigkeit der gedruckten Teile zu erreichen, stießen wir mit FFF an eine Wand. Es ist einfach kein geeignetes Verfahren für die in-situ-Konsolidierung mit hohem Fasergehalt und geringen Hohlräumen. Am Ende haben wir also einen Prozess erhalten, der thermoplastisches Verbundmaterial AFP mit FFF kombiniert, wobei unverstärktes und/oder mit geschnittenen Fasern gefülltes Filament verwendet wird.“
Allen :„AFP ist eigentlich ein additiver Fertigungsprozess. Bei SCRAM verwenden wir es jedoch nicht konventionell mit einem festen, harten Werkzeug, sondern drucken ein Werkzeug, das wir anschließend auswaschen können, um sehr komplexe Geometrien zu erstellen, die wirklich strukturell sind.“
Braun :„Wir können dieses lösliche Werkzeug an Stellen anbringen, die nicht festgefahren sind, damit Sie innere Hohlräume schaffen können. Das Ziel ist nicht, mit unseren großen AFP-Systemen zu konkurrieren, sondern ein sehr geschicktes System so nah wie möglich an einem 3D-Drucker zu machen. Dies mit echten sechs Freiheitsgraden und Genauigkeit zu tun, ist tatsächlich sehr kompliziert. Die resultierende Zelle macht Befestigungselemente und Klebstoffe überflüssig und stellt integrierte, komplexe Teile her, die sehr schnell wiederholt werden können.“
Hochleistung für die Luft- und Raumfahrt
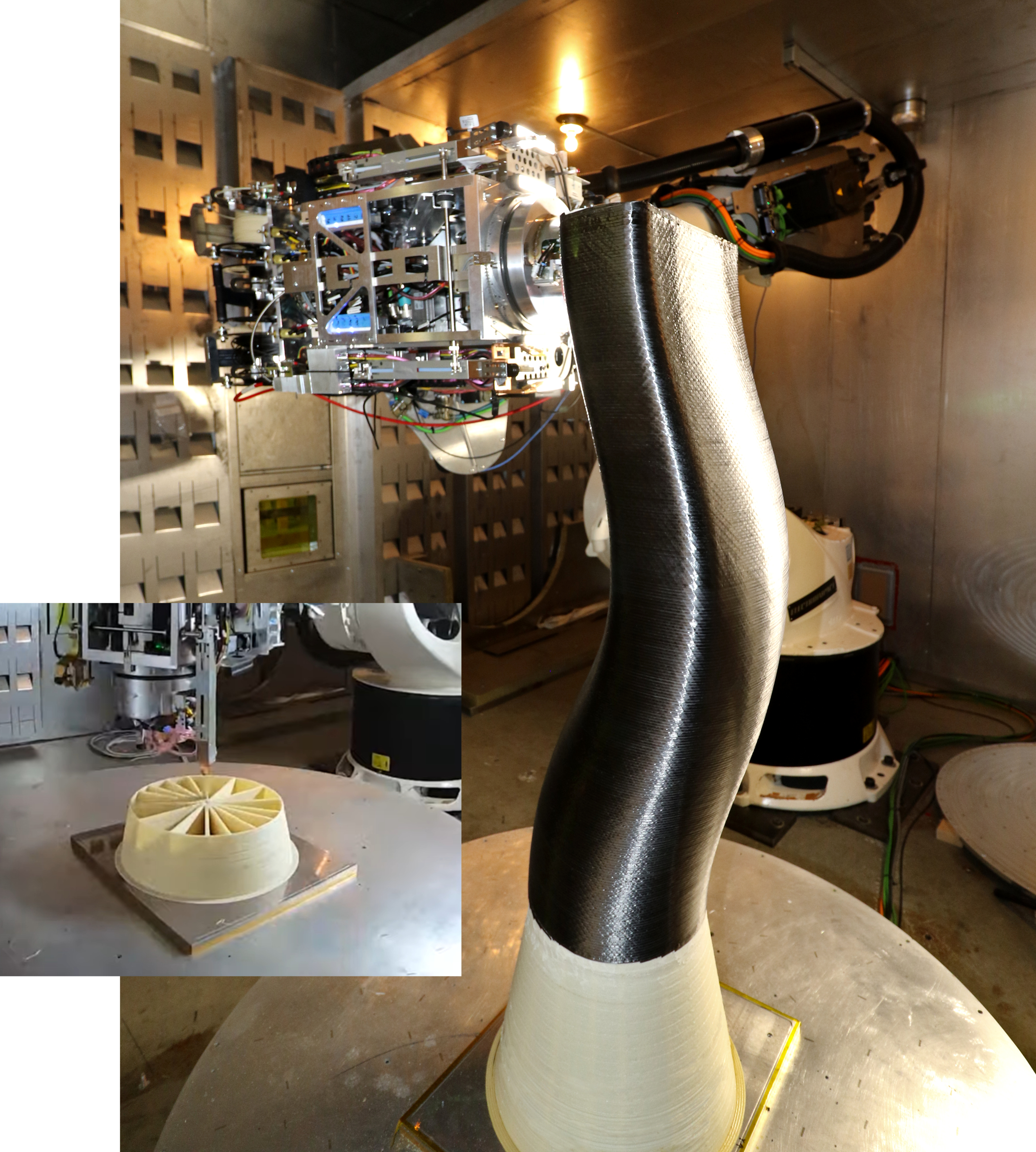
Braun :„Die ersten Anwendungen, die wir in der Luft- und Raumfahrt und Verteidigung anstreben, beginnen wir mit PEEK [Polyetheretherketon]. Wir haben dann mit PEKK [Polyetherketonketon] und niedrig schmelzendem PAEK [Polyaryletherketon] mit dramatischem Erfolg gearbeitet.“
Bischoff :„Der Wärmeausdehnungskoeffizient [CTE] ist Ihr größter Feind. Dies ist der Grund, warum die Verwendung von PEEK so herausfordernd ist – es liebt es zu kristallisieren und zu schrumpfen. Obwohl der WAK für PEKK und andere PAEK-Harze nicht Null ist, ist ihre kristalline Struktur viel besser kontrollierbar und daher einfacher zu verarbeiten. Alternative PAEKs bieten auch eine viel bessere Verarbeitbarkeit und höhere Layup-Geschwindigkeit.“
Allen :„Thermische Gradienten müssen aufgrund des CTE-Problems vermieden werden, daher versucht man, den Prozess und das Teil so isotherm wie möglich zu halten. Andernfalls kommt es zu Verwerfungen. Die Verwendung der beheizten Kammer ist ein Muss – auch wenn Sie sie nicht auf einer hohen Temperatur halten – nur um sicherzustellen, dass keine Zugluft entsteht und ein Teil des Drucks keine andere Temperatur hat als der Rest.“
Laserbasierte Zelle
Braun :„Viele Dinge, die dieses System ermöglichen, gab es zu Beginn noch nicht, einschließlich des PAEK-Bands und des kompakten Hochleistungslasers, den wir verwenden, sowie der echten sechsachsigen CAM-Software für die additive Fertigung.“
„Der SCRAM-Kopf verwendet zwei 3D-Druckdüsen auf beiden Seiten des AFP-Systems [Eröffnungsbild]. Eine wird verwendet, um die löslichen Werkzeuge zu drucken, und die andere druckt unverstärktes oder gehacktes Faserfilament. Man sieht, dass man mit einem Gerüst ausgestattet ist. Dieser hält eine Reihe von Spiegeln, um das Laserlicht um die Düsenspitze herum umzuleiten und das Substrat zu erhitzen. Dies ermöglicht es uns, im Vergleich zu herkömmlichem FFF eine außergewöhnliche Haftfestigkeit zwischen den Schichten zu erreichen. Die Lichter am System sollen das Teil für die Kameras beleuchten [Abb. 2]. Wir verwenden diese überall, damit der Bediener sicher und ohne Gefahr durch den Laser sehen kann, was vor sich geht.“
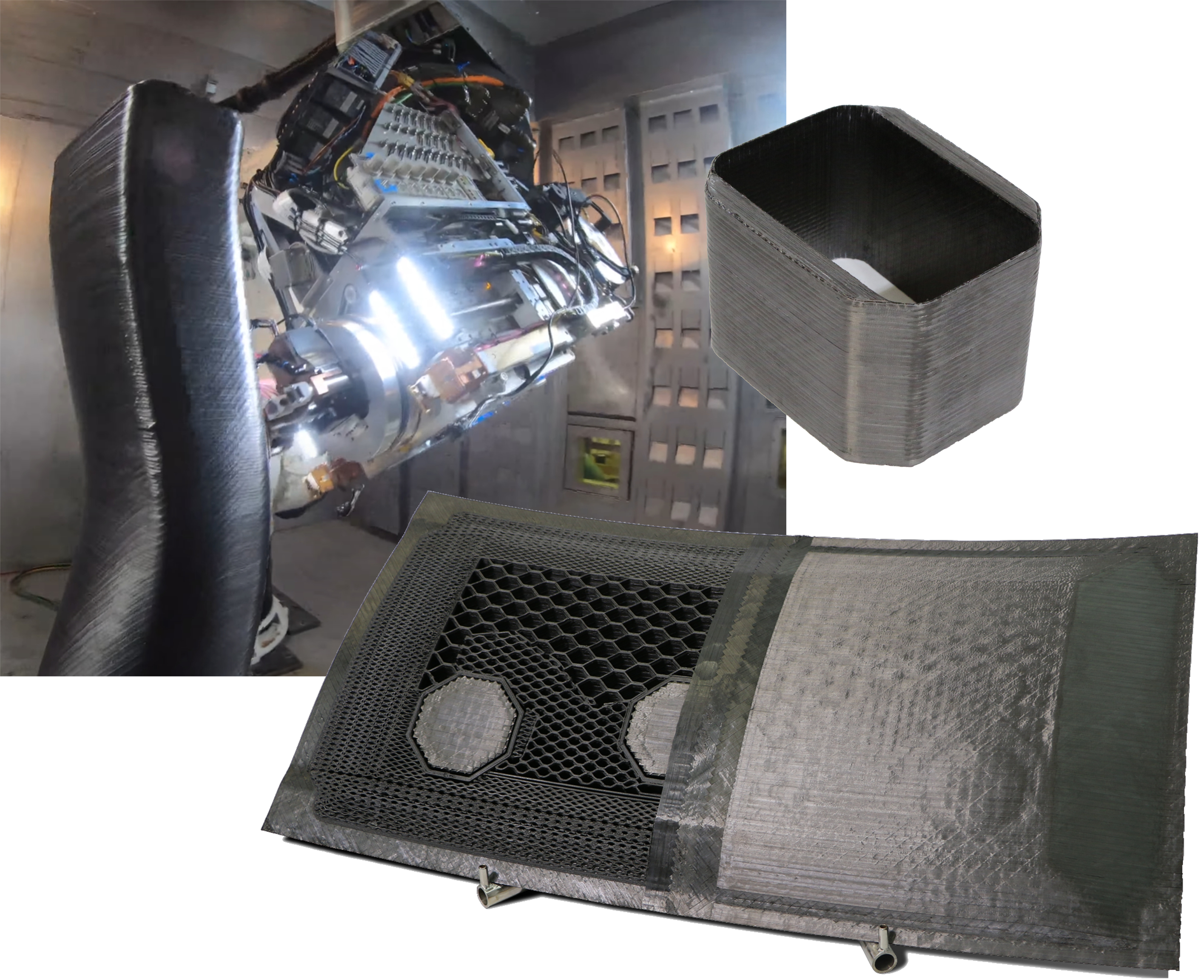
Materialformate und Porosität
Braun :„Wir haben viele verschiedene Materialien verarbeitet, die meisten von ihnen wurden nach unseren Spezifikationen in Bezug auf Fasern, Harz, Faservolumen und Abmessungen hergestellt. Wir haben vor kurzem mit kommerziell erhältlichen Slit Tows experimentiert. Die FFF-Filamente aus geschnittenen Fasern werden ebenfalls nach unseren Spezifikationen unter Verwendung des gleichen Harzes und der gleichen Fasern hergestellt, die wir für die Endlosfaserbänder auswählen. Wir haben Filamente mit 1-, 3,5- und 6,35-Millimeter-Durchmesser verwendet. Wir können größer werden, mussten es aber noch nicht.“
„Wir erreichen beim AFP 50-60% Faservolumen, bei den FFF-Anteilen jedoch deutlich weniger, da diese extrudiert werden. Die Porosität liegt in der Größenordnung traditioneller Verfahren außerhalb des Autoklaven, hat jedoch mit der Verfeinerung des Verfahrens dramatisch abgenommen. Unter Verwendung von extrem hochwertigen Materialien und im Labor haben wir eine Porosität von unter 0,5% erreicht, gemessen mit CT [Computertomographie]-Scans. Wie immer gibt es eine Vielzahl von Variablen, die diese Zahl beeinflussen, und wenn wir sehr komplexe Teile herstellen, ist es eine Herausforderung, eine geringe Porosität beizubehalten. Wir haben viele zerstörende und zerstörungsfreie Prüfungen von Teilen und Coupons durchgeführt, die mit dem System hergestellt wurden.“
Hochpräzise Robotersteuerung
Bischoff :„SCRAM bietet hochpräzise Robotertechnologie. Standard-Roboter von der Stange sind eine erschwingliche Lösung, um Bewegungen mit 6 Freiheitsgraden zum Platzieren und Drucken zu erreichen, aber sie sind bei weitem nicht genau genug für AFP in Luft- und Raumfahrtqualität. Wir haben vor Jahren damit begonnen, herauszufinden, wie diese Roboter in AFP-Systemen in der Luft- und Raumfahrt eingesetzt werden können. Sie müssen die Grundlagen des Systems und die Probleme beim Erreichen der Genauigkeit wirklich verstehen. Wir haben eine ganze Robotergruppe von 60-70 Ingenieuren, und das ist alles, was sie tun.“
„Es ist ein unglaublich komplexes Thema, eine hohe Positions- und Bahngenauigkeit zu erreichen. Sie haben Ungenauigkeiten im Roboter (CTE des Roboters, Spiel, Vibrationen usw.) und in der externen Achse, Werkzeugpunktkalibrierungen, einen sich drehenden Teilrahmen und mehrere andere Ursachen. Wenn Sie keines davon berücksichtigen oder adressieren, kann dies katastrophal sein, wenn Sie mit dem Drucken in einem echten 3D-Raum beginnen. Um dies zu erreichen, werfen wir die mit dem Roboter gelieferte Steuerung weg und führen alles mit einer Siemens-CNC aus. Anschließend fügen wir allen Roboterachsen das patentierte sekundäre Feedback von Electroimpact hinzu, das uns von einer Toleranz von 30-40 mil [0,030-0,040 Zoll] auf ±15 mil [0,015 Zoll] bringt. Dann wenden wir eine kinematische Kompensation höherer Ordnung an, um ±10 mil [0,010 Zoll] zu erreichen.“
Geschwindigkeit, Endeffektoren und rotierender Drucktisch
Braun :„Wir verwenden in-situ-Konsolidierung, daher wird die Auftragsgeschwindigkeit nicht annähernd die von duroplastischen Prepreg-Bändern erreichen. Außerdem ist dies ein Roboter, keine große, versteifte Portalplattform (wie AFP), die für höhere Geschwindigkeiten ausgelegt ist. Und Geschwindigkeit ist nicht nur das Verlegen und Drucken, sondern beinhaltet auch die Vorlaufzeit für die Werkzeugbestückung. Die eigentliche Kennzahl ist, wie schnell Sie ein digital gefertigtes Teil zur Hand haben können?“
„Das Teil im Video war 36 Zoll groß (mit der bedruckten Basis überstieg es 4 Fuß) und sein Durchmesser betrug 16 Zoll. Wenn wir ununterbrochen im Schichtbetrieb liefen, könnten wir dies in wenigen Tagen produzieren, was eine unglaublich kurze Zeit ist, um ein Teil in der Hand zu haben. Teile werden auch direkt aus der CAD-Datei produziert. Wenn Sie also iterieren müssen, ändern Sie das CAD, posten die Werkzeugwege neu und drucken das neue Teil.“
Allen :„Im Moment haben wir zum Drucken des Support-Tools einen hochskalierten, filamentbasierten Prozess. Der Durchsatz ist etwas langsam, was sich auf die Druckzeit auswirkt. Im Juli haben wir unseren ersten Endeffektor mit einem Pelletschneckenextruder in Betrieb genommen. Dadurch wird die Leistung erhöht, jedoch werden dicke Perlen erzeugt. Daher werden wir auch einen Fräs-Endeffektor für die Bearbeitung der bedruckten Oberfläche hinzufügen.“
Braun :„Wir werden eine Familie kompatibler Endeffektoren haben, die der Roboter aufnehmen und absetzen kann, und die je nach Bedarf eine Vielzahl von additiven und subtraktiven Funktionen ausführen. Das Pick-up- und Drop-off-Verfahren des Endeffektors ist vollautomatisch, was bei allen unseren AFP-Systemen sowie bei SCRAM Standard ist. Der gesamte Endeffektor wird über ein Schnittstellenmodul für den automatischen Werkzeugwechsel am Roboter befestigt und es gibt Ständer für die Endeffektorlagerung.“
„Das System druckt auf eine externe Rotationsachse und wird von der CNC gesteuert. Wir haben dies, weil der Roboter allein nicht jeden Punkt der Teile erreichen kann, die wir herstellen möchten. Im weiteren Verlauf beabsichtigen wir, das System auf Schienen zu bringen, um größere Teile herzustellen, aber wir wollen das System zuerst in diesem Maßstab verfeinern. Wir haben über den Einsatz von zwei Robotern gesprochen und wissen philosophisch, wie wir vorgehen würden. (Wir haben andere integrierte Multi-Roboter-Fertigungssysteme entwickelt.) Aber wenn zwei Roboter in überlappenden Arbeitsbereichen arbeiten, wird die Steuerung extrem kompliziert.“
Zukünftige flexible Produktion möglich
Braun :„Diese multifunktionale Zelle wird dem Endkunden einen Mehrwert bieten. Es müssen nicht immer endlosfaserverstärkte Thermoplastteile hergestellt werden. Durch das Hinzufügen von Extrusion und Fräsen zur Endlosfaserablage erweitern wir deren Spektrum und Flexibilität. Einige der von uns demonstrierten Strukturen haben beispielsweise subtraktive Funktionen innerhalb des Teileaufbaus. Der Roboter überprüft dann die Oberfläche und schließt diese Kavität. Dies ist derzeit ohne mehrere Schritte, spezielle Werkzeuge und/oder Endmontage in irgendeiner Form nicht möglich.“
„Allerdings gibt es ein noch größeres Thema, als nur Teile zu produzieren. Langfristig hat dieser Ansatz die Chance, die Art und Weise, wie Luft- und Raumfahrt- und Verteidigungssysteme entwickelt und hergestellt werden, dramatisch zu verändern. Eine einzige Produktionslinie wird nicht mehr einem einzigen Produkt gewidmet sein. Stattdessen wird die Produktion flexibel. Wenn Sie die Werkzeugausstattung reduzieren können, können Sie auch die im Regal sitzenden Ersatzteile reduzieren. Diese Flexibilität hat Auswirkungen auf die gesamte Lieferkette, einschließlich der Reduzierung von Abfall aufgrund des Verfalls von Materialien.“
Bischoff :„Mit einer kleinen Handvoll SCRAM-Zellen und digitalem Design müssen Sie nur das Rohmaterial zur Hand haben, im Gegensatz zu Dutzenden von festen Werkzeugen und Duroplasten mit begrenzter Haltbarkeit.“
Braun :„Wir haben noch einen Weg vor uns, bevor die Produktion wirklich auf diese Weise abgewickelt wird, aber jetzt können Sie deutlich sehen, wie dies möglich ist.“
Harz
- ACEO® stellt neue Technologie für den 3D-Druck mit Silikon vor
- Emirate übernehmen 3D-Drucktechnologie für Flugzeugteile
- Eine Einführung in den 3D-Druck mit selektivem Lasersintern
- TPU-3D-Druck:Ein Leitfaden zum 3D-Druck flexibler Teile
- Drucken der Sicherung 1 mit der Sicherung 1
- Impossible Objects arbeitet mit BASF für den 3D-Verbunddruck zusammen
- Broetje-Automation erweitert AFP-Portfolio für die Serienfertigung von Verbundwerkstoffen
- Victrex- und Bond-Partner für den 3D-Druck von PAEK-Teilen
- VDMA entwickelt Roadmap für 3D-Druck mit Manufacturing Roadmap
- Rückverfolgbarkeitspraktiken für die Fertigung von Präzisionsteilen