Automatisierte Herstellung von Aeroverbundwerkstoffen:Flüssigformung oder geschweißter Thermoplast?
Während OEMs und Zulieferer die Materialien und Prozesse erforschen, die die nächste Generation von Flugzeugen ermöglichen werden, werden zwei unterschiedliche Ansätze demonstriert. Die erste ist das Flüssigspritzen von Trockenfaser-Preforms, das beispielsweise in der High-Rate-Resin-Transfer-Moulding-(RTM-)Linie von Spirit AeroSystem (Prestwick, Schottland) für Airbus A320-Spoiler und auch im von Airbus geführten Wing of Tomorrow (WOT)-Programm verwendet wird die eine automatisierte Platzierung von Gelege (NCF) und Flüssigharzinfusion verwendet, gefolgt von einer Aushärtung außerhalb des Autoklaven (OOA) in einem Ofen (siehe „Hochgeschwindigkeits-automatisierte Luft- und Raumfahrt-RTM-Linie liefert Spoiler der nächsten Generation“ und „Update:Lower Wing Skin, Wing of Tomorrow“.)
Die zweite sind thermoplastische Verbundwerkstoffe (TPC), die beispielsweise im Clean Sky 2 Multifunctional Fuselage Demonstrator (MFFD) verwendet werden, bei denen durch automatisierte Faserplatzierung versteifte Häute erzeugt werden – in-situ-konsolidiert für die obere Hälfte und autoklavverfestigt für die untere Hälfte — gefolgt von der Montage durch Schweißen. Diese Programme verwenden Automatisierung, um die Produktionsrate und Qualität zu erhöhen und gleichzeitig die Kosten zu senken. Aber wie vergleichen sie sich?
Das Institut für Konstruktion und Konstruktion des Deutschen Zentrums für Luft- und Raumfahrt (DLR) betreibt das Zentrum für Leichtbau-Produktionstechnik (ZLP) in Augsburg. Unter seinen zahlreichen Verbundwerkstoff-Fertigungsprojekten bieten PROTEC NSR und Fast Lane RPB eine einzigartige Gelegenheit, jeweils ein flüssigkeitsgeformtes, duroplastisches hinteres Druckschott (RPB) für den Twin-Aisle-Airbus A350 mit einem thermoplastischen RPB für den Single-Aisle-Airbus zu vergleichen A320. Beide Projekte arbeiteten mit dem Tier-1-Lieferanten dieser Strukturen, der Premium Aerotec Group (PAG, Augsburg, Deutschland), zusammen und demonstrierten die Automatisierung bei der Bewertung von Zykluszeit und Kosten.
Flüssiggeformter TS-Schott
„Wir haben vor vielen Jahren mit PAG im Projekt AZIMUT begonnen, manuelle Prozesse für die Composite-Fertigung zu analysieren“, sagt Dr. Lars Larsen, Leiter Montage- und Fügetechnik beim ZLP Augsburg. „Unsere erste Automatisierungslösung diente dem Layup, und dann haben wir daran gearbeitet, weitere Vorgänge zu automatisieren.“ Das Hauptziel von PROTEC NSR war es, diese spezialisierten Lösungen für die RPB-Produktion in einen einzigen automatisierten Prozess zu bringen, erklärt Dr. Marcin Malecha, Projektleiter für PROTEC NSR beim DLR.
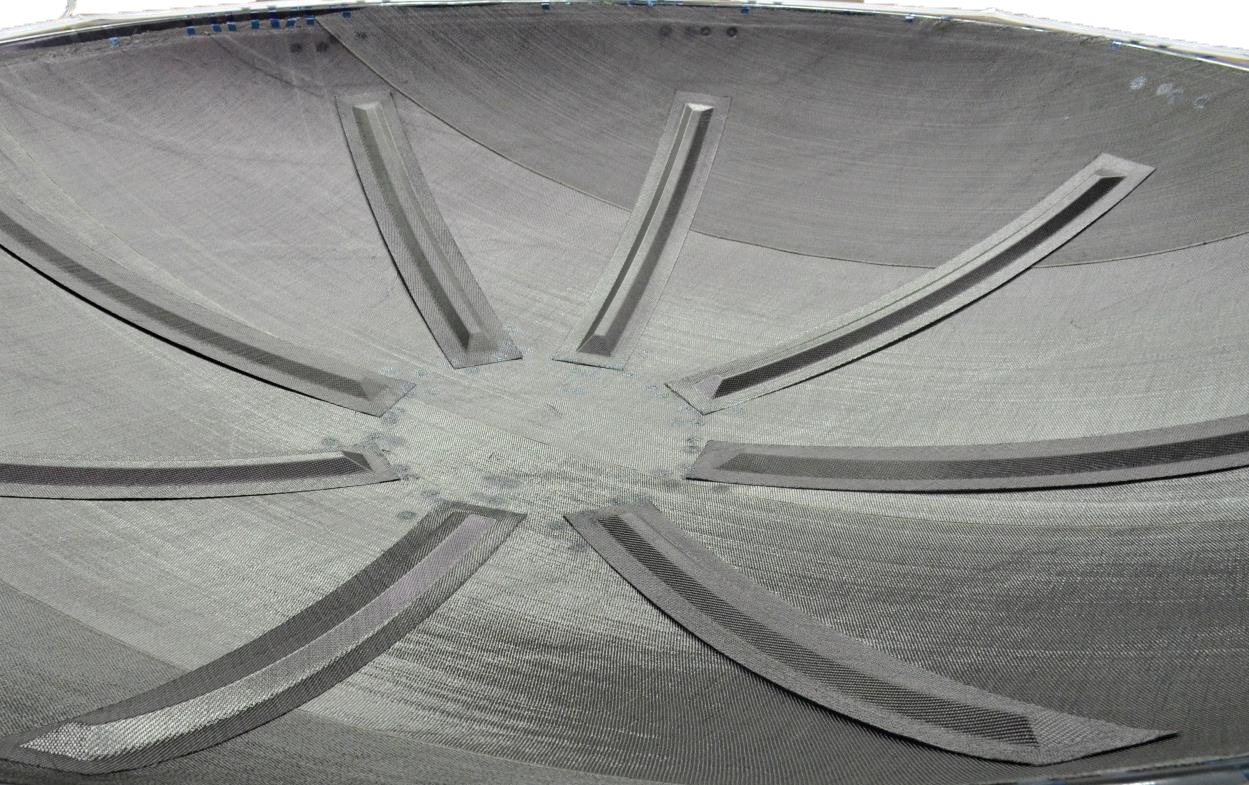
Preform und Greifer. Die Prozessschritte zur Herstellung des vakuumverpackten trockenen Vorformlings sind in Abb. 1 unten dargestellt. Dieses wurde mit RTM6-Epoxidharz unter Verwendung des von Airbus patentierten vakuumunterstützten Prozesses (VAP) infundiert, der eine semipermeable Membran verwendet, um die Porosität zu reduzieren. Das Preform-Layup umfasste zwei Sätze von 16 Lagen mit einer Länge von bis zu 5 Metern, wobei die volle Breite von 1,27 Metern des 5-Harness-Satin-Carbonfasergewebes verwendet wurde. Eingebettet zwischen diesen beiden Sets waren 25 komplex geformte Verstärkungsstücke mit einer Größe von bis zu 1,5 x 2,5 Metern. Acht Stringer wurden oben platziert.
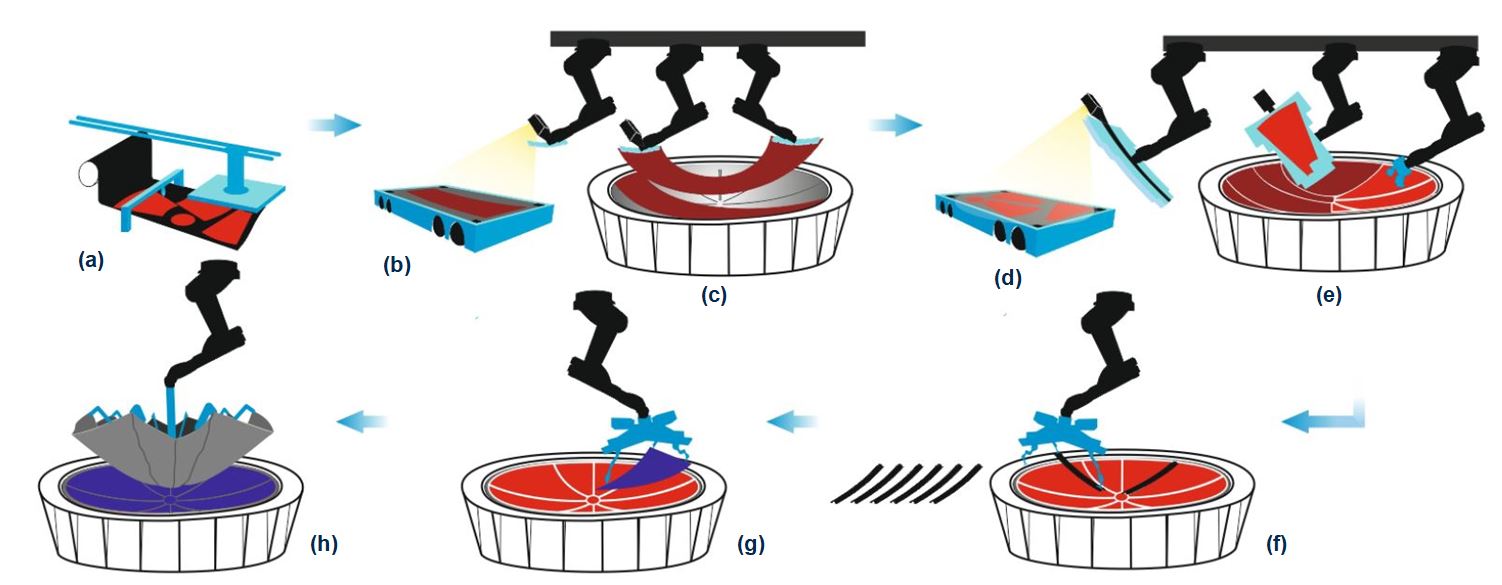
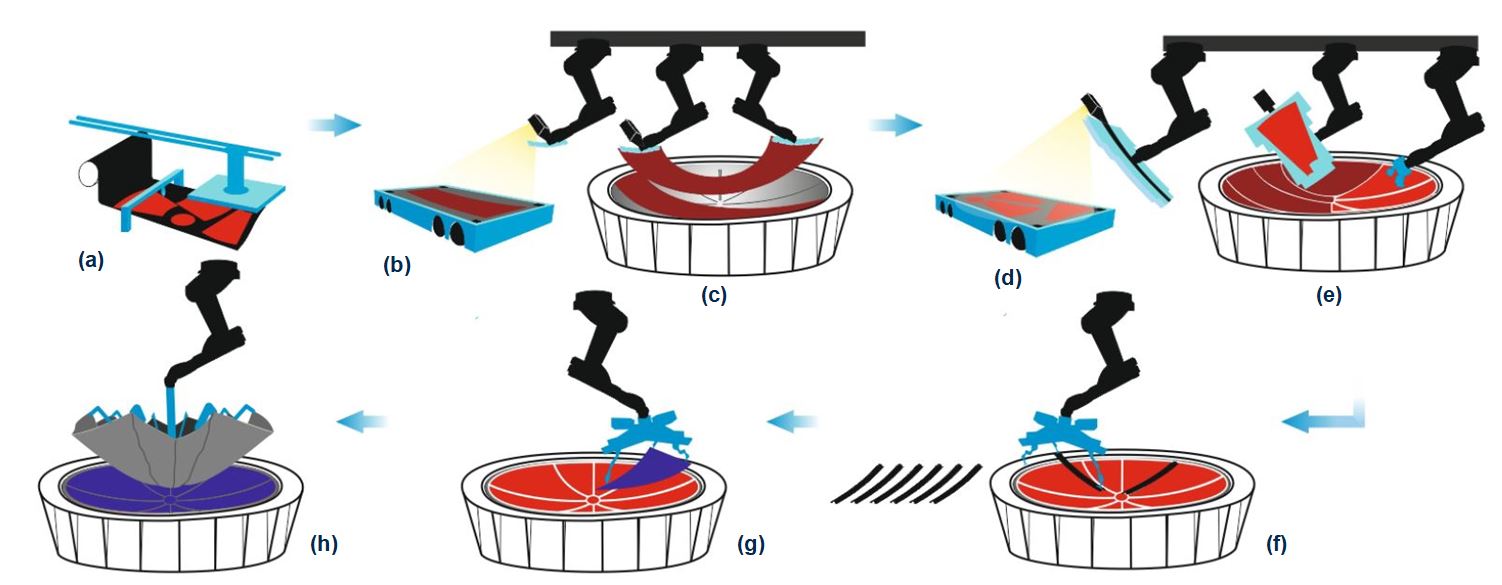
„Werkzeuge und Greifer zu entwickeln, die die nötige Präzision beim Drapieren und Handling erreichen, war eine der größten Herausforderungen“, sagt Larsen. Dies lag zum Teil an der komplexen Mischung von Lagen, die drei verschiedene Drapierungsmechanismen erforderte:
- Auftrag von Material über die gesamte Breite direkt von der Rolle, das sich der Form der Form anpassen muss.
- Drapieren von groß geschnittenen Strukturlagen wo zwei Roboter zusammenarbeiten, einer pro Stoffkante, um die Zielgeometrie der Form aufzunehmen und zu erstellen um sicherzustellen, dass sie sich vor dem Platzieren ohne Falten anpasst.
- Unterkunft für kleine, geformte Lagen bis zu 1,5 x 2,5 Meter .
„Für die kooperierenden Roboter haben wir Endeffektoren entwickelt, die aus sechs Modulen bestehen, die durch Kugelgelenke verbunden sind“, erklärt Larsen. „Dadurch kann sich der Endeffektor ähnlich einer Schlange verformen und sich der Zielgeometrie der Form anpassen. Integrierte Heizvorrichtungen aktivieren den Binder im Stoff während des Transports und der Formgebung und behält seine 3D-Form und Position nach dem Auflegen bei.“
Automatisiertes Drapieren und Platzieren
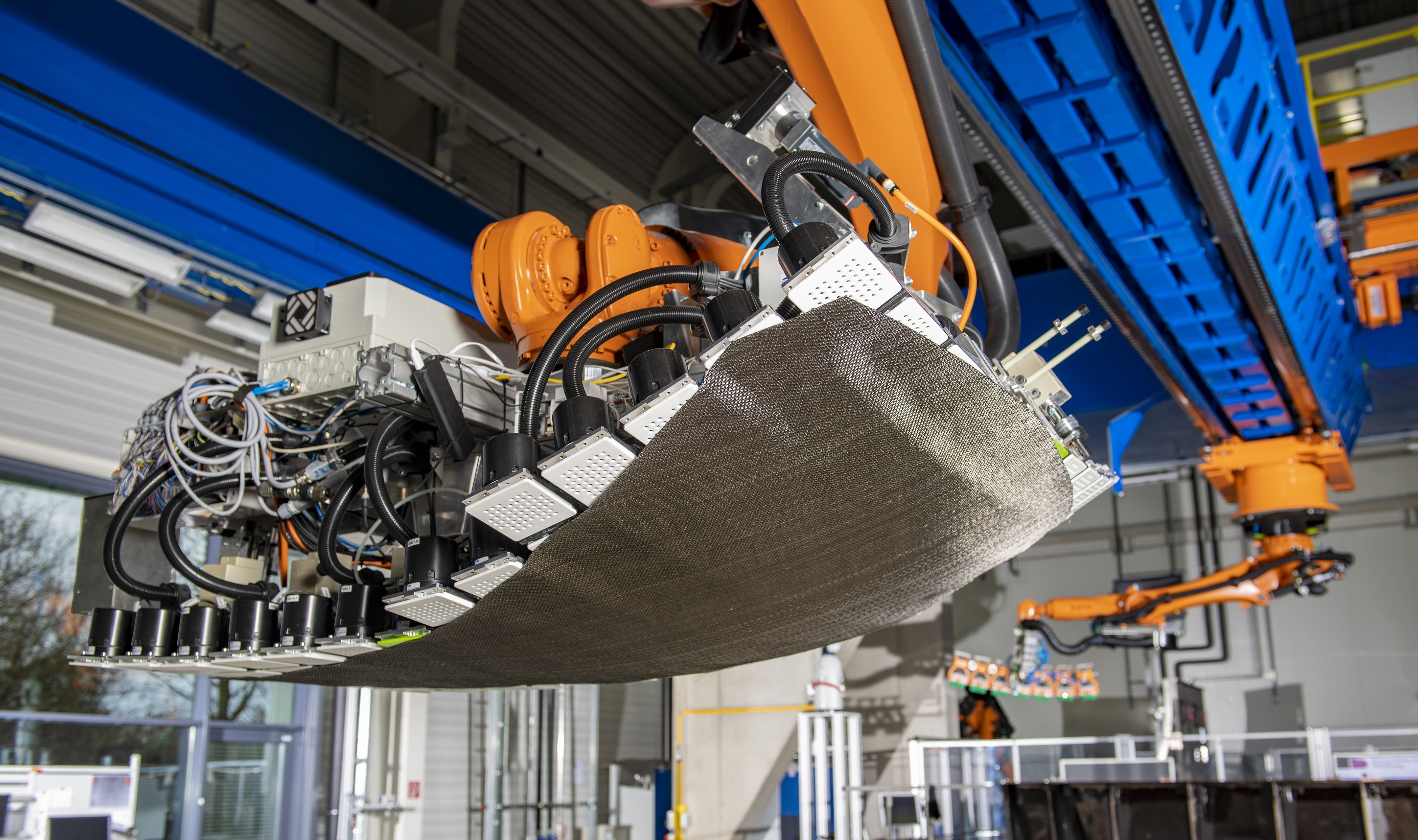
Der Endeffektor verfügt über einen Greifer, der 127 Module mit Vakuumsauger verwendet, um geschnittene Stofflagen aufzunehmen, dann in eine 3D-Form zu verwandeln und sie dann vor dem Einlegen in die Form zu erhitzen. Bildnachweis:Deutsches Zentrum für Luft- und Raumfahrt (DLR) Institut für Tragwerksplanung
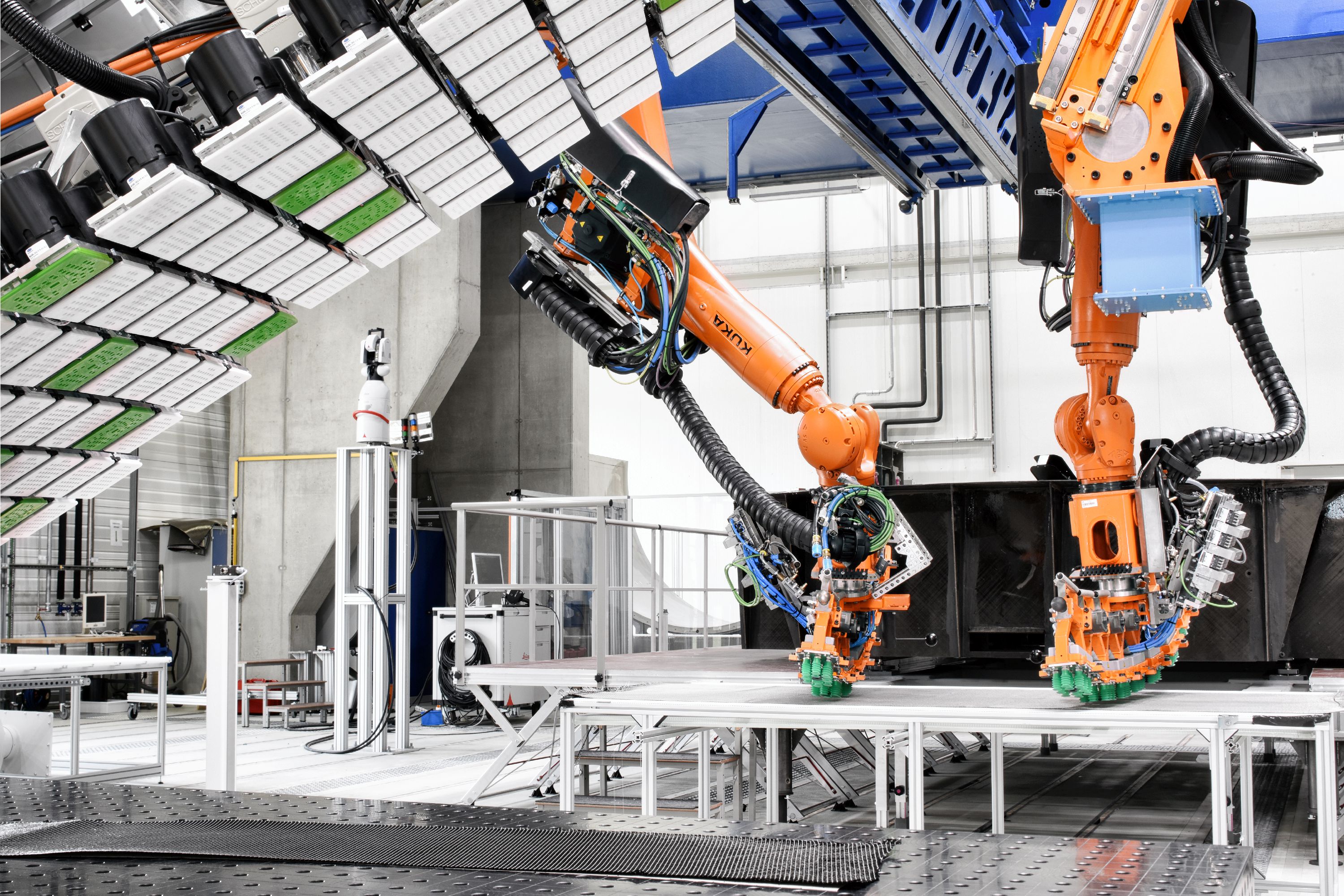
Hier sind sowohl der Greifer mit 127 Modulen (links) als auch kollaborierende Roboter (Hintergrund) zu sehen. Bildnachweis:Deutsches Zentrum für Luft- und Raumfahrt (DLR) Institut für Tragwerksplanung
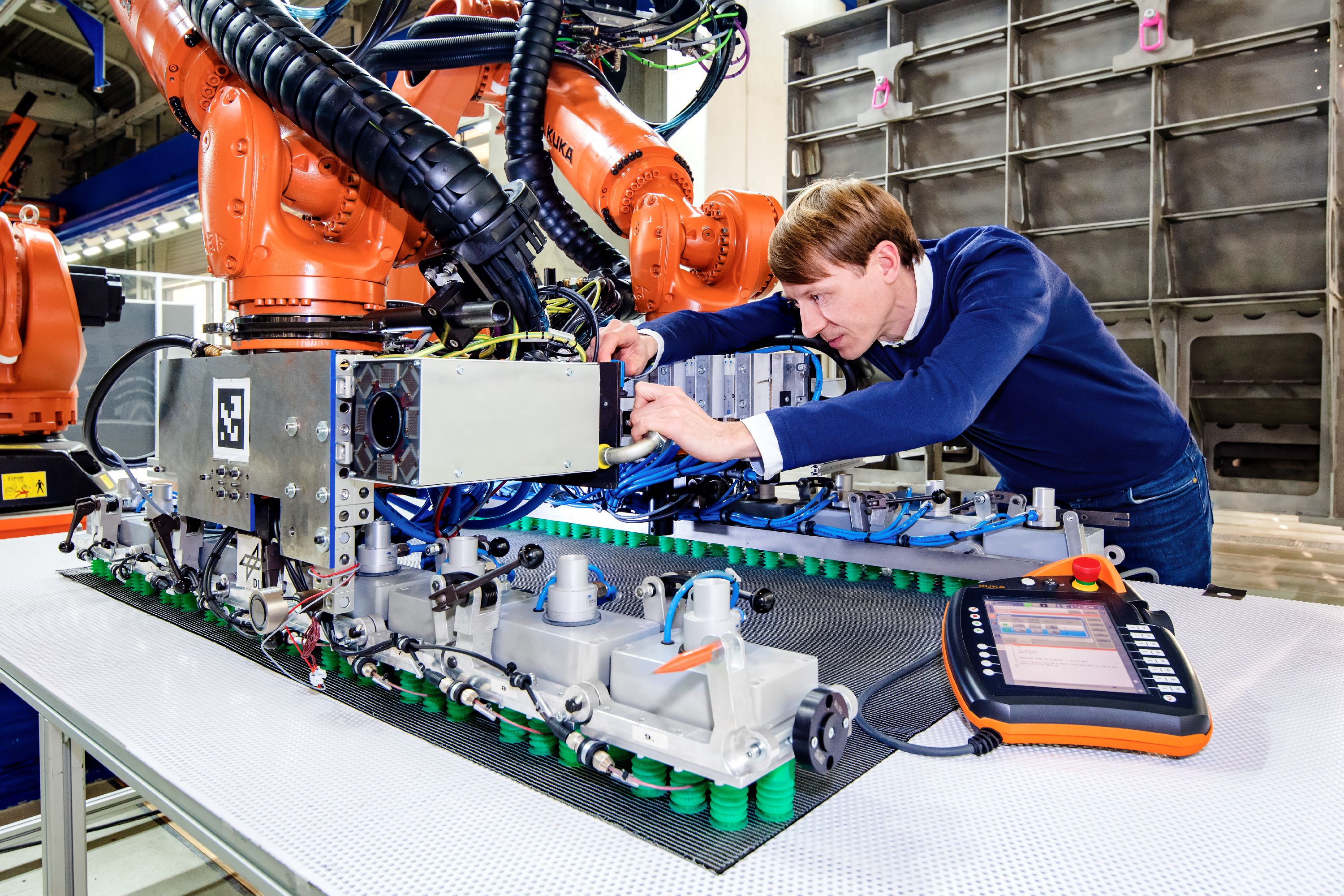
Für die kollaborierenden Roboter wurden Endeffektoren entwickelt, die sechs durch Kugelgelenke verbundene Module enthalten. Bildnachweis:Deutsches Zentrum für Luft- und Raumfahrt (DLR) Institut für Tragwerksplanung

Jeder Roboter nimmt eine Kante der großen Stofflage auf. Beim Transport der Lage arbeiten sie dann zusammen, um die erforderliche Zielgeometrie zu erstellen, bevor das Gewebe in die Form gelegt wird. Bildnachweis:Deutsches Zentrum für Luft- und Raumfahrt (DLR) Institut für Tragwerksplanung
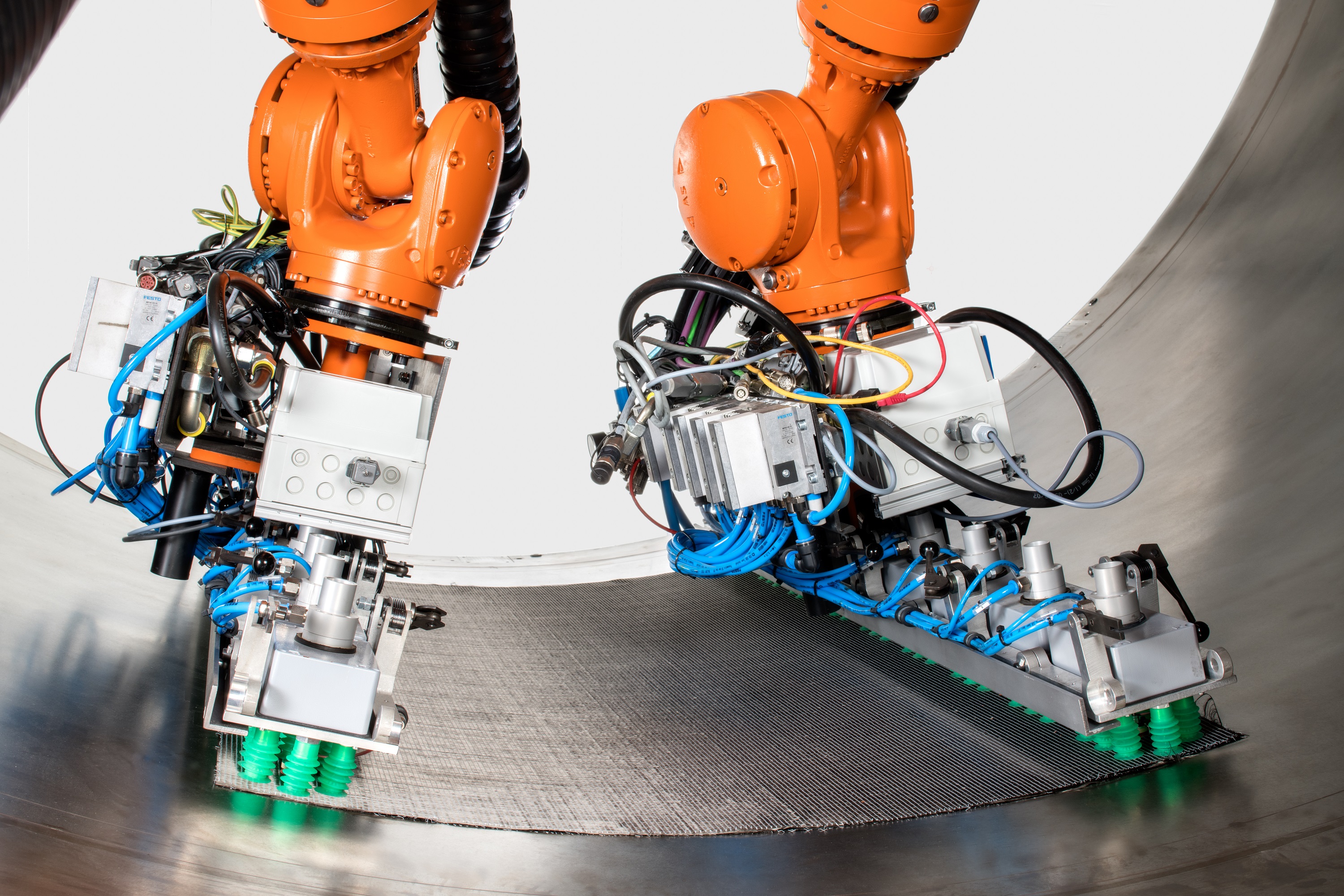
Bildnachweis:Deutsches Zentrum für Luft- und Raumfahrt (DLR) Institut für Tragwerksplanung
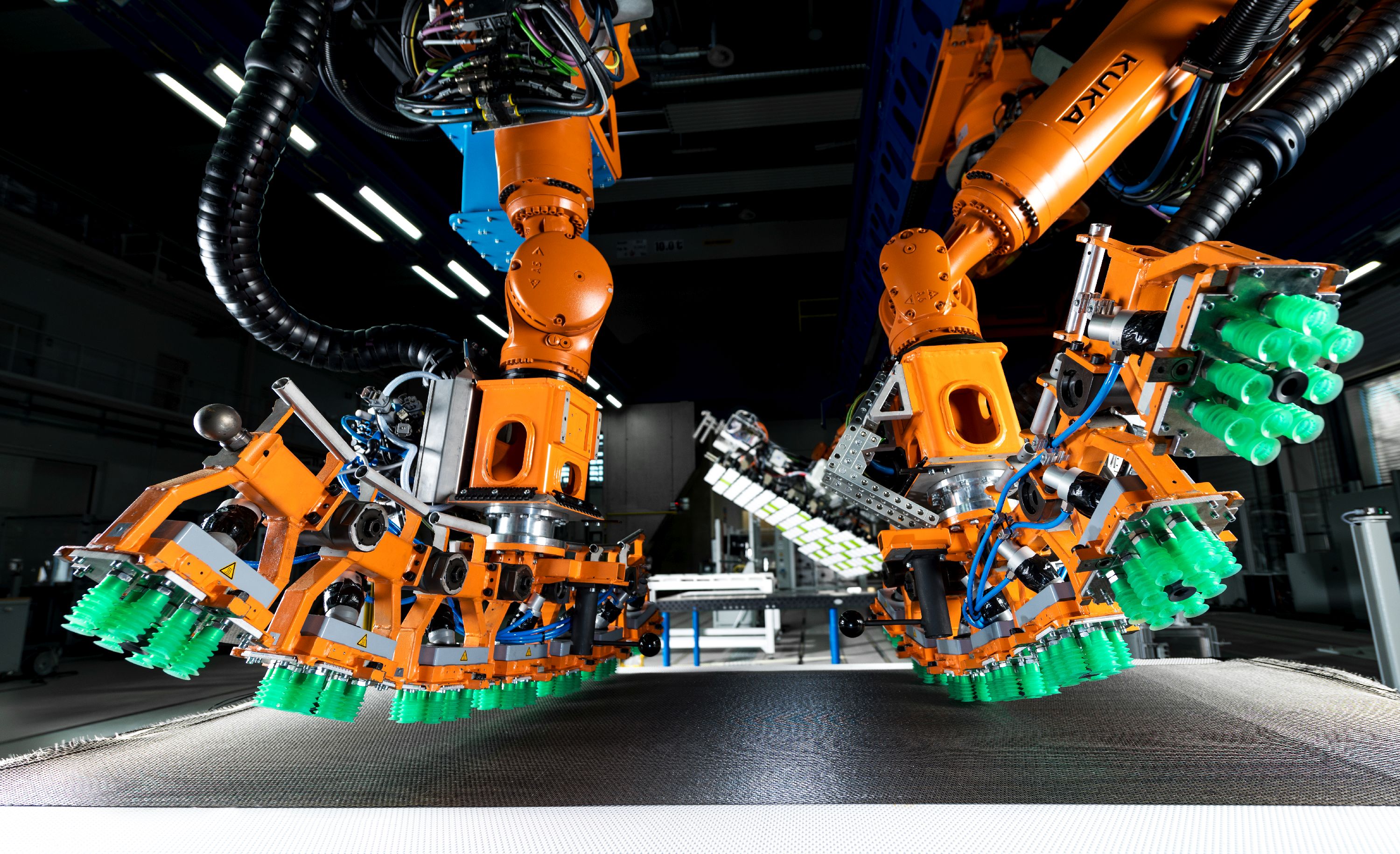
Nahaufnahme der kollaborativen Roboter-Endeffektoren. Bildnachweis:Deutsches Zentrum für Luft- und Raumfahrt (DLR) Institut für Tragwerksplanung
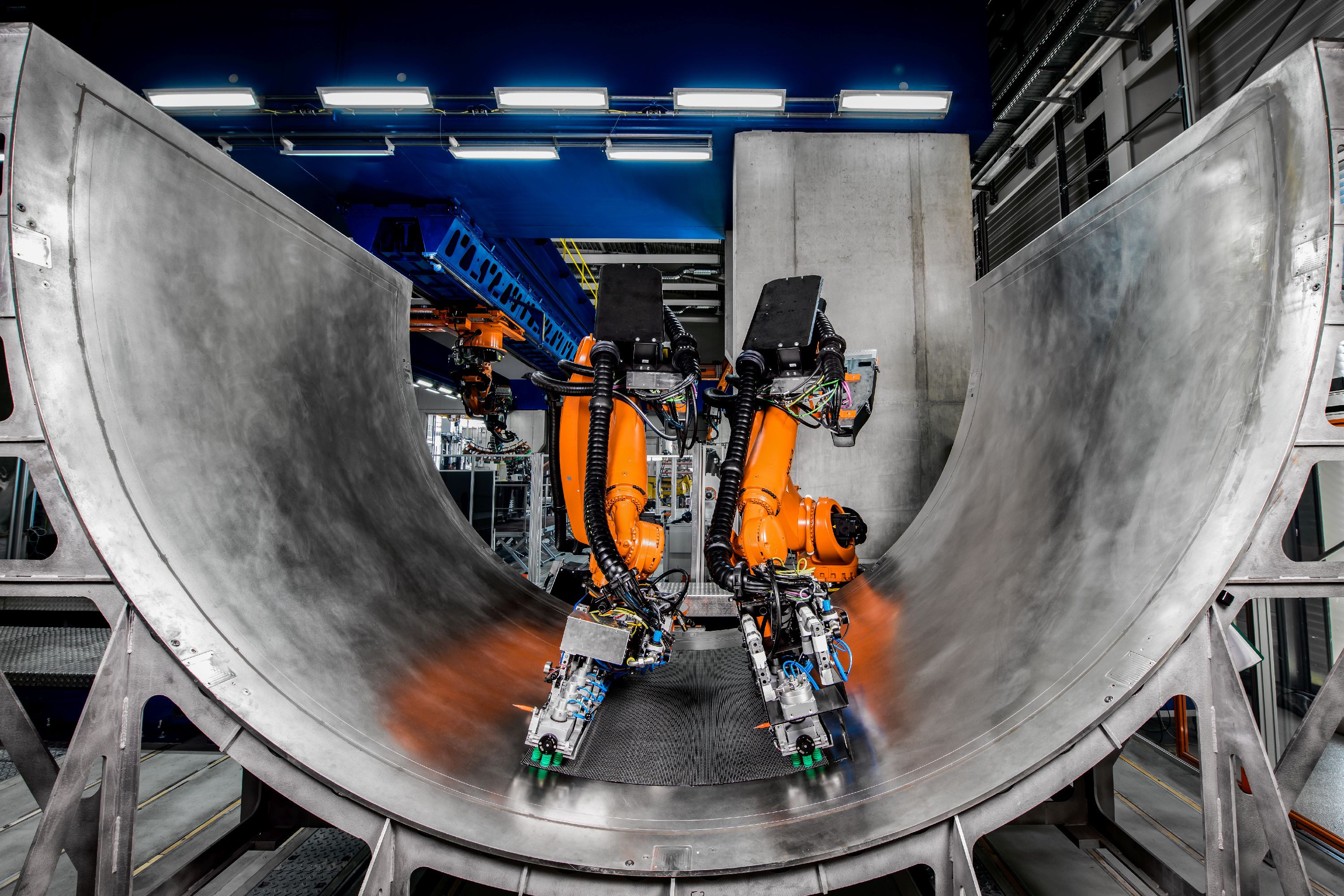
Dieses System, das das DLR zunächst für ein A320-Hinterdruckschott entwickelt hat, wurde nun auch für eine Rumpfplatte demonstriert und ist auf Basis der digitalen Konstruktionsdateien für eine Vielzahl großer Flugzeugstrukturen flexibel ausgelegt, ohne dass die Roboter neu eingelernt werden müssen. Bildnachweis:Deutsches Zentrum für Luft- und Raumfahrt (DLR) Institut für Tragwerksplanung
Vorherige NächsteFür die kleinen, geformten Lagen bis 1,5 mal 2,5 Meter wurde eine zweite Greiferart entwickelt, die 127 Module mit Vakuumsauger zur Aufnahme nutzt. „Dieser Greifer nimmt Material im 2D-Zustand auf und biegt es dann auf die Zielgeometrie um“, erklärt Malecha. „Es muss entscheiden, welches der 127 Module es festhält und welches es gleiten lässt, um die 2D-Schicht in eine 3D-Form zu verwandeln. Es ist also sehr ähnlich, wie Hände beim Drapieren funktionieren. Wir haben viele Experimente gemacht und Erfahrungen gesammelt, wo wir halten und wo wir loslassen. Die Kraft kann durch die Stärke des Moduls am Material angepasst werden.“
Inline-Inspektion. Optische Sensoren in den modularen Greifern überwachten den Drapierprozess. Nach dem Platzieren einer Lage prüft ein Endeffektor, der einen Leica T-Scan (Hexagon Manufacturing, Cobham, Großbritannien) und ein kamerabasiertes Faserwinkelmesssystem von Profactor (Steyr, Österreich) kombiniert, auf Qualität. „Wir haben zuerst die Faserwinkel gemessen und mit der CAD-Datei verglichen“, sagt Malecha, „und dann haben wir die Kanten jedes Teils gemessen und ihre Position mit der CAD-Datei verglichen.“
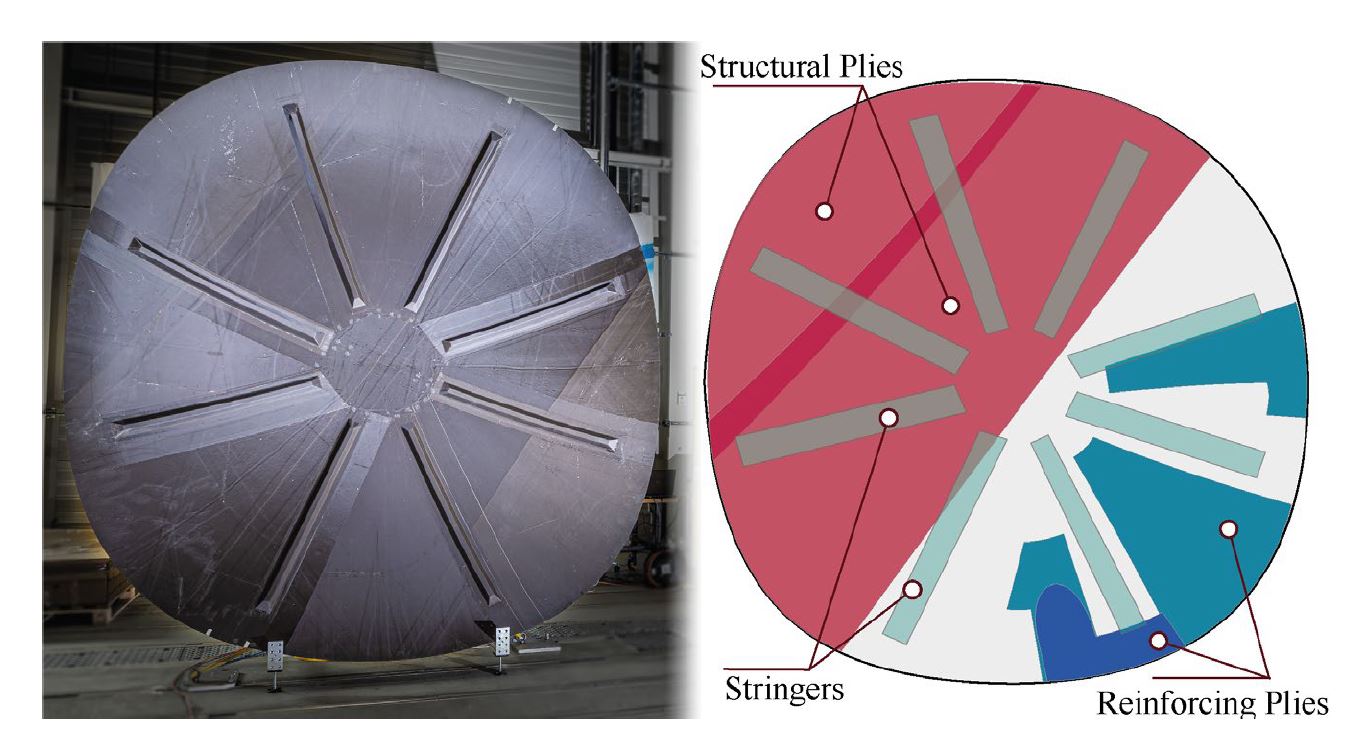
Stringer und Vakuumbeutel. Nach Fertigstellung des Vorformlings wurden oben acht Versteifungen (Stringer) angebracht. Für diese Aufgabe wurde der Multi Kinematic Gripper entwickelt und diente auch zum Aufbringen der Vakuumbeutel-Hilfsmaterialien. Dieser Greifer besteht aus drei kleinen und unabhängigen Robotern mit 6 Freiheitsgraden (DOF) und einem starren Arm, die alle am Mittelflansch eines 6-DOF-Industrieroboters montiert sind. Vakuumverpackungshilfsmittel – Abziehfolie, perforierte Trennfolie und Harzflussmedien (werkzeugseitige Hilfsmaterialien) – wurden vorgeschnitten und vorgefügt, für den Ort bestimmt, an dem sie platziert wurden. „Sie mussten nicht drapiert, sondern einfach platziert werden“, bemerkt Malecha. Die vorgefertigte semipermeable Membran wurde halbautomatisch über einen Endeffektor mit einem „schirmartigen“ Mechanismus aufgebracht, während das Aufbringen von Klebeband und äußerem Vakuumbeutel manuell blieb, aber auch automatisiert werden konnte.
Zykluszeit und -kosten. Für Malecha bestand die größte Herausforderung darin, das modulare, auf künstlicher Intelligenz (KI) basierende Manufacturing Execution System (MES) zur Überwachung und Steuerung der Prozesskette aufzubauen. „Wir mussten Datenmanagementsysteme aufbauen, die ganz unterschiedliche Prozesse zusammenführen und dann über das MES über einen Datenaustausch-Port steuern“, erklärt er. „Wir können sie nach Bedarf im laufenden Betrieb einsetzen und ermöglichen so mehr Flexibilität und einen breiteren Einsatz im Vergleich zu einer strengen Fertigungsreihenfolge.“
Die PROTEC NSR-Technologie wurde durch die Herstellung eines Demonstrators in Originalgröße im Januar 2019 validiert und erreichte bis Mitte 2019 einen Reifegrad von TRL 5-6. Im Vergleich zum heutigen Stand der Technik bei PAG verkürzt diese automatisierte Prozesskette die Taktzeit beim Rollenware-Auftrag um 58 % und beim Bestücken von geschnittenen Lagen um 50 %. Die Herstellungskosten für diese Vorgänge wurden um 11,5 % bzw. 31 % gesenkt.
Thermoplastisches RPB
„Dieses Projekt startete 2018 mit PAG und dem Institut für Verbundwerkstoffe (IVW, Kaiserslautern, Deutschland), um zu zeigen, was mit thermoplastischen Verbundwerkstoffen in Großteilen und Primärstrukturen möglich ist“, erklärt Dr. Stefan Jarka, Projektleiter Fast Lane RPB und Experte für Schweißtechnik am ZLP Augsburg. „Ein RPB ist nicht wirklich primär, weil die mechanischen Anforderungen nicht so hoch sind wie bei einem Flügel oder Rumpf, aber es zeigt, was für große, flache, leicht gekrümmte Strukturen möglich ist. In nur vier Monaten entwickelten wir einen Demonstrator A320 RPB als Beispiel für die Umrüstung einer bestehenden Aluminiumstruktur auf thermoplastische Verbundwerkstoffe.“
Dieser Demonstrator verwendete Cetex-Kohlefaser (CF)-Gewebe/Polyphenylensulfid (PPS)-Organoblech (Toray Advanced Composites, Nijverdal, Niederlande) und Widerstandsschweißen. Ein Widerstandselement zwischen den beiden zu verschweißenden Oberflächen erzeugt Wärme und verbleibt in der verschweißten Struktur. GKN Fokker (Hoogeveen, Niederlande) verwendet diese Technik seit Jahrzehnten zur Herstellung von Flugzeugfahrwerkklappen und festen Vorderkanten. Für diesen A320 RPB verwendete das ZLP-Team ein CF-Widerstandselement anstelle eines herkömmlichen Edelstahlgewebes.
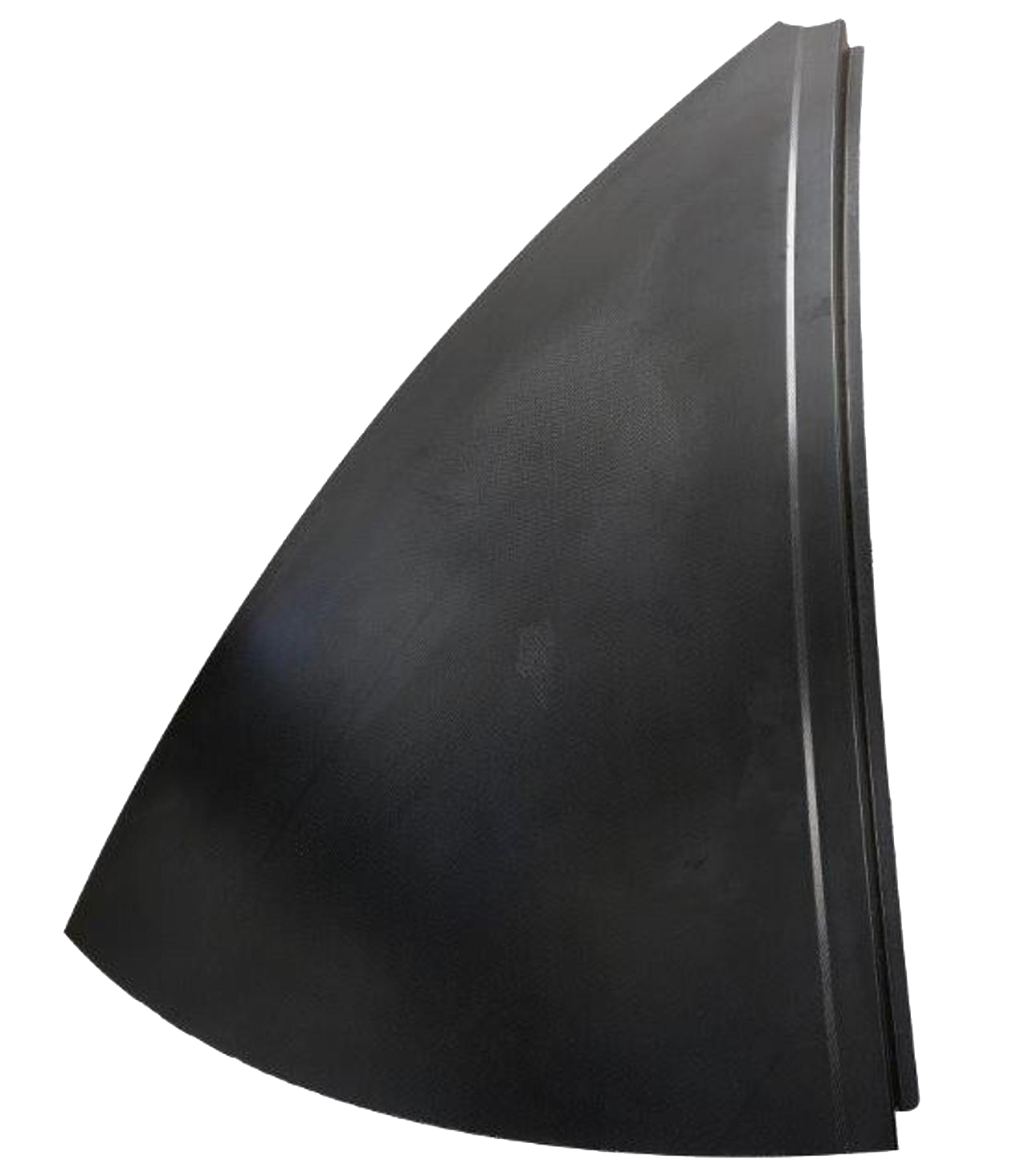
„Der thermoplastische Verbundwerkstoff RPB sollte gleich oder günstiger sein, aber das Material ist viel teurer“, bemerkt Larsen. Daher waren niedrigere Produktionskosten aufgrund der Automatisierung entscheidend, ebenso wie die Verwendung von acht identischen Blütenblattabschnitten. „Diese Abschnitte wurden benötigt, um die doppelt gekrümmte Form des Teils zu formen“, erklärt Jarka. „Das Thermoformen als ein einziges Teil würde eine sehr große Presse erfordern, die zu teuer wäre. So wurden vom IVW acht kleinere Profile mit abgestimmten Metallwerkzeugen pressgeformt und von uns automatisiert geschweißt. Der Automatisierungsgrad beim thermoplastischen Pressformen ist höher als bei duroplastischen Verbundwerkstoffen. Sie verwenden meistens abgestimmte Metallwerkzeuge, wobei eine hohe, aber konstante Temperatur das Hauptproblem ist, aber dies macht den automatisierten Presszyklus auch sehr schnell.“
Die Gesamtprozessschritte für den Demonstrator RPB sind in Bild 2 dargestellt. „Das von uns verwendete Schweißverfahren war nicht neu“, sagt Jarka, „muss aber weiterentwickelt werden, um die 1,5 Meter langen [und 40 Millimeter- breite] Nähte für das 3-Meter-Durchmesser und integrieren ein Qualitätsprüfsystem. Zunächst wurden die Bauteile mit einer Positionierlehre in der richtigen Position fixiert und anschließend mit elektrischer Energie die Kunststoffschmelze in der Schweißzone erzeugt.“
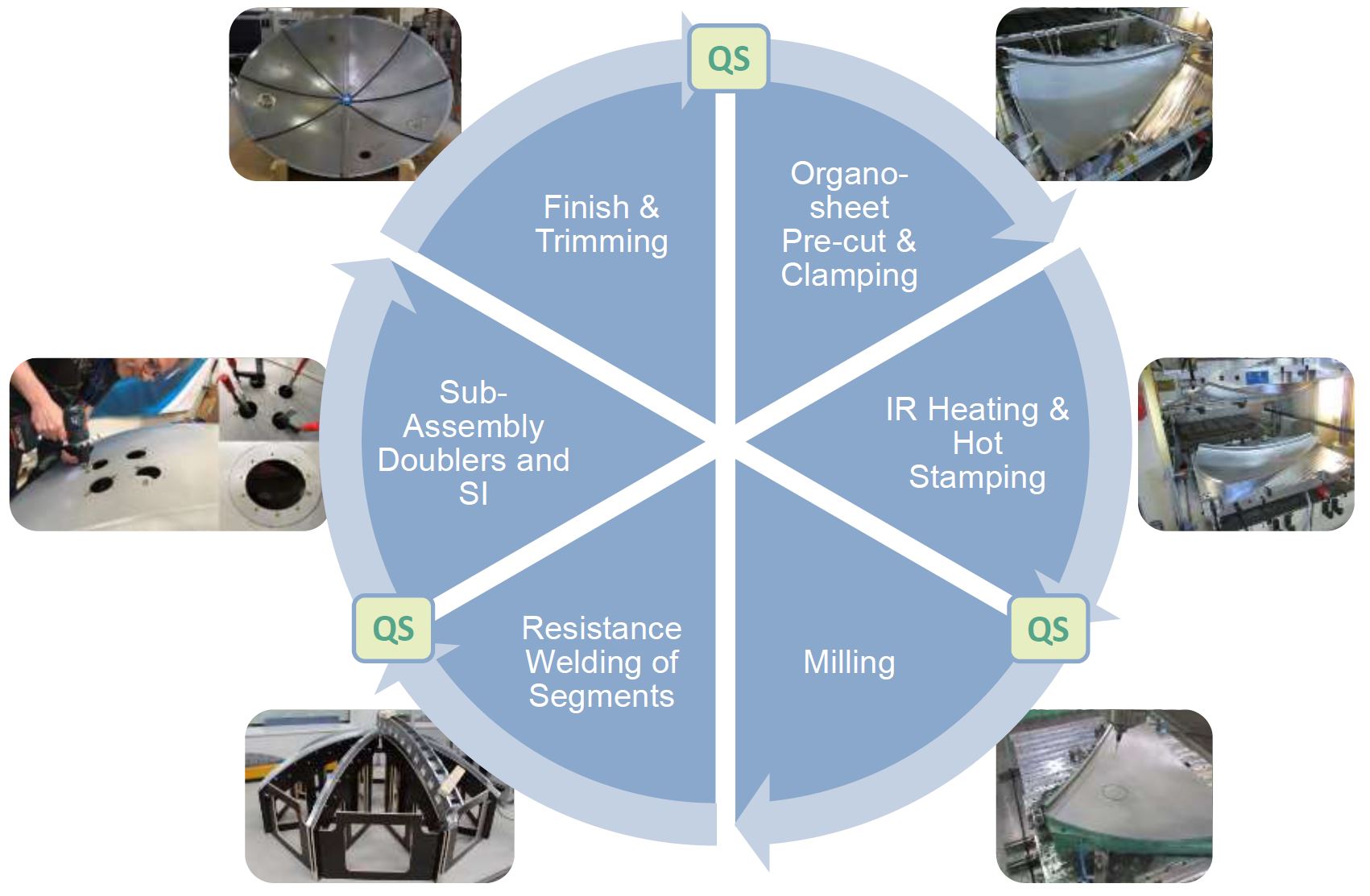
Abb. 2. Verfahrensschritte für thermoplastisches RPB
Prozessschritte zur Herstellung von acht Abschnitten (unten) aus stanzgeformtem CF/PPS-Organoblech, die anschließend durch Widerstandsschweißen zu einer Demonstrator-A320-Schottwand verbunden wurden. Bildnachweis:Deutsches Zentrum für Luft- und Raumfahrt (DLR) Institut für Baukonstruktion und Konstruktion
QA integrieren. „Wir haben es mit Thermografie versucht, sowohl blitzlampen- als auch ultraschallaktiviert, aber damit lässt sich die Schweißzone nicht so einfach vermessen“, erklärt Jarka. „Thermografie ist sehr schnell, aber es lässt sich nicht leicht sagen, ob Sie eine gute Konsolidierung haben.“ Stattdessen verwendeten sie einen Standardprüfstand, um mehrere geschweißte Proben herzustellen und Strom, Spannung und Temperatur zu messen. „Wir haben sie dann mit Ultraschallprüfung (UT) geprüft und Korrelationen zwischen Prozessparametern und guter Konsolidierung hergestellt“, sagt Larsen. „Wenn wir gute Parameter haben, dann haben wir ein gutes Teil. Wir haben auch eine Prozesssimulation erstellt, um die während des Schweißens gewonnenen Daten mit der von uns erstellten Ausgangsbasis zu vergleichen.“
Automatisierung und Zykluszeit. „Der gesamte Prozess war sehr schnell, im Maßstab von Automobilteilen“, sagt Jarka. „Wir haben in unserem Test 2019 TRL 3 erreicht und sind seitdem auf TRL 4 gereift. Wir werden TRL 6 bis Ende 2021 erreichen.“ Vor der Pandemie hatte PAG angekündigt, den thermoplastischen RPB bis 2021 in Produktion zu bringen. Obwohl die Zukunft weniger klar ist, wird der thermoplastische RPB immer noch als Ermöglicher des „Rumpfs von morgen“ angesehen, indem das Gewicht von 41 auf 35 Kilogramm reduziert wird und Montagezeit um 75 % und die Gesamtkosten der Teile um mehr als 10 %.
Vergleich von TS- und TP-Kompositen
„Die thermoplastischen Prozesse sind so schnell, dass man im Vergleich zu Aluminium billiger sein kann und sogar eine Produktionsrate von 100 Flugzeugen pro Monat erreicht“, sagt Jarka. „Der RPB ist eine gute Anwendung für das thermoplastische Schweißen, aber auch für die Automatisierung“, sagt Malecha. „Das flüssiggeformte RPB aus Trockenfasern ist teurer zu automatisieren.“
„Aber diese Automatisierung ist interessant, weil man durch die Automatisierung nur einiger Teilprozesse echte Vorteile erzielen könnte“, sagt Larsen. „Zum Beispiel könnten wir durch die Automatisierung der Hilfsmittel die Vakuumverpackung in etwa einer Stunde abschließen, etwa zehnmal schneller als der manuelle Prozess.“ Er räumt jedoch ein, dass die Kosten ein Haupthindernis für die Umsetzung einer solchen Verbesserung sind. „Die Kosten für digitale Werkzeuge, Roboter und Entwicklung sind zu hoch für ein einzelnes Teil wie das RPB. Aber wenn wir einen modularen Ansatz entwickeln könnten, bei dem Sie dieses System für viele Teile verwenden könnten, könnten diese Kosten breiter gestreut werden, was es angesichts des reduzierten Zeit- und Arbeitsaufwands erschwinglich macht.“ ZLP hat dies tatsächlich erreicht, wie in CW . erklärt 's Juli 2020 Feature:"Composites 4.0:Digitale Transformation, adaptive Produktion, neue Paradigmen."
„Es gibt noch nicht viele Vergleiche zwischen duroplastischen und thermoplastischen Verbundstrukturen“, sagt Malecha. „Aber wir beginnen, duroplastische und thermoplastische Verfahren zu vergleichen.“ Das nächste Ziel sei es, zu zeigen, dass thermoplastische Bindenähte die für Flugzeugtragflächen und -rümpfe erforderlichen Eigenschaften aufweisen. Und diese Leistung muss zum Beispiel auch bei großen, integrierten Liquid Moulding Wings gezeigt werden. Genau das haben sich die MFFD- und WOT-Programme zum Ziel gesetzt. Und wir erwarten ihre Ergebnisse sowie die aus vielen anderen Clean Sky 2- und EC-Projekten, um die nächsten Schritte aufzuzeigen.
Harz
- Blog:Spritzgießen von Flüssigsilikonkautschuk
- EconCore Produktionstechnologie für thermoplastische Wabenplatten
- Karl Mayer startet Produktionslinie für thermoplastische UD-Bänder
- INEOS Styrolution baut Produktionsstätte für thermoplastischen Verbundwerkstoff StyLight
- Herone-Produktionstechnologie gewinnt JEC Innovation Award
- Thermoplastumspritzte Duroplaste, 2-Minuten-Zyklus, eine Zelle
- LANXESS erweitert Produktionskapazität für endlosfaserverstärkte thermoplastische Verbundwerkstoffe
- Airtech bringt Hochtemperatur-Vakuumverpackungsmaterialien für das thermoplastische Formen auf den Markt
- Finex-Verfahren zur Herstellung von flüssigem Eisen
- Automatisierte Produktion von Ölbohrkupplungen