Verbundeinlage als strukturelle Verstärkung für A-Säulen
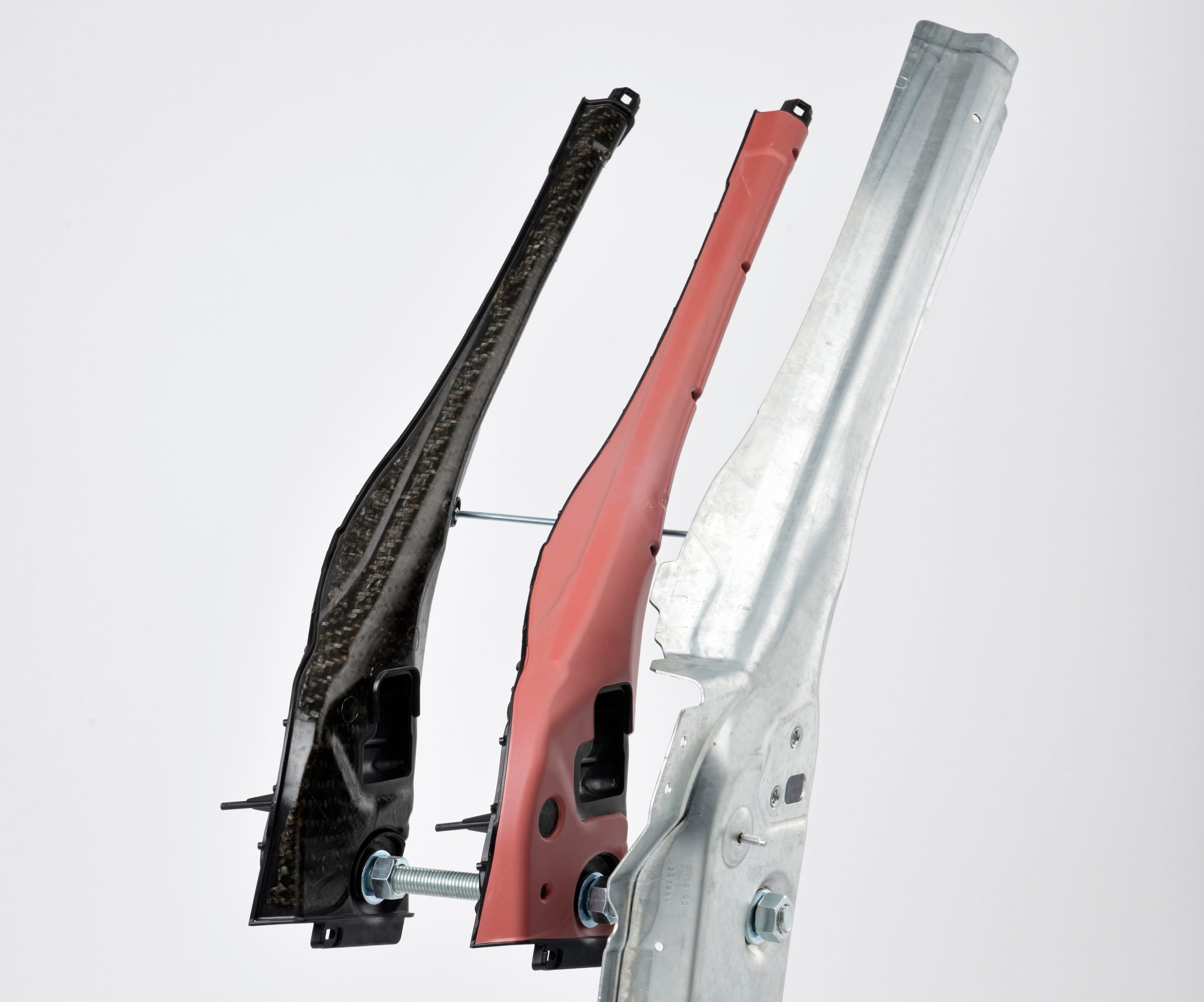
Die 3D-Hybrid-A-Säule ragt vom Fahrzeugschweller nach oben, nimmt die Türscharniere auf und hält die Windschutzscheibe seitlich fest. Quelle | LANXESS AG
Der Porsche (Stuttgart, Deutschland) 911 Cabriolet das in diesem Jahr auf den Markt kam, ist das erste Fahrzeug, das mit einer leichten Hybrid-A-Säule aus Metallverbundwerkstoff hergestellt wird, die für den Einsatz in Cabrios und Roadstern entwickelt wurde.
Die Hybrid-Metall-Verbundsäule enthält eine Einlage aus hochfestem Stahl, die im Inneren von einem umgeformten Rohling aus LANXESS (Pittsburgh, PA, USA) auf Polyamid 6-Basis Tepex dynalite 102-RG600(6)/47% kontinuierlich . getragen wird faserverstärkten thermoplastischen Verbund, und durch eine Rippenstruktur aus dem kurzglasfasergefüllten Durethan AKV30H2.0 auf Polyamid 66-Basis. Diese Struktur wird durch Reibung mit L-5235-Strukturschaum verbunden, der von L&L Products (Romeo, Michigan, USA) entwickelt wurde. LANXESS sagt, dass seine Tepex-Reihe thermoplastischer Verbundwerkstoffe besonders für Strukturbauteile in Pkw mit ihren hohen Sicherheitsanforderungen geeignet ist.
Die Festigkeit und Steifigkeit des Hybrid-Einsatzes sorgt dafür, dass die A-Säule Überschlägen genauso gut standhält wie bisherige Konstruktionen mit hochfesten Stahlrohren. Allerdings ist es 5 Kilogramm leichter. Die Gewichtsreduzierung erfolgt im „Gewächshaus“-Bereich des Fahrzeugs, wodurch der Fahrzeugschwerpunkt abgesenkt und dadurch die Fahrdynamik verbessert wird.
„Die hervorragende mechanische Performance der Hybrid-A-Säule zeigt, dass auch Hybrideinsätze auf Basis von Stahlblech, Tepex-Blanks, Polyamid 6 oder Polyamid 66-Varianten von Durethan als Hinterspritzmaterial und auf einem Strukturschaum wie L-5235 beachtliche Vorteile bieten Einsatzmöglichkeiten im strukturellen Karosserieleichtbau. Das gilt insbesondere für Elektrofahrzeuge, da ihnen durch ihre schweren Batterien eine hohe Aufprallmasse verliehen wird“, erklärt Henrik Plaggenborg, Leiter Tepex Automotive im LANXESS Geschäftsbereich High Performance Materials (HPM). „Die Gewichtsreduzierung erhöht auch die Reichweite der Elektrofahrzeuge, die diese Technologie nutzen.“
Weitere Anwendungsmöglichkeiten der Hybrid-Verbundelemente sind verstärkende Quer- und Längsträger, B- und C-Säulen, tragende Batterieteile oder sicherheitskritische Türkomponenten.
Die Hybrid-Verbundelemente wurden von L&L Products am Standort Straßburg, Frankreich entwickelt und hergestellt. Der erste Schritt bei der Herstellung der Verstärkungselemente ist das Umformen und Umspritzen der Tepex-Rohlinge in einem Arbeitsgang im Hybrid-Molding-Verfahren. Das resultierende Verbundbauteil wird dann mit einem Schaumbindesystem auf Epoxidbasis beschichtet, das sich als Reaktion auf Wärme ausdehnt. Das beschichtete Teil wird auf die Karosserie montiert und durchläuft damit das kathodische Tauchlackierverfahren (KTL). Durch die hohen Temperaturen des KTL-Verfahrens dehnt sich der Strukturschaum aus und verbindet sich mit dem hochfesten Stahlblech, das auch an der A-Säulenverkleidung befestigt ist, um die verstärkende Hybrideinlage zu erzeugen. Dieser letzte Schritt erfolgt in einem vollständig automatisierten Fertigungsprozess, der von Porsche entwickelt wurde und einer ständigen Qualitätskontrolle unterliegt.
Der Entwicklungsprozess der Einlegeteile und der A-Säule wurde durch den HiAnt-Kundendienst von LANXESS unterstützt. „Zu den Leistungen gehörten die Simulation der Umformung (Drapierung) der Tepex-Rohlinge, die Simulation des Füllens für das Hinterspritzen und die Berechnung des Verzugs. Außerdem haben wir Materialkennwerte ermittelt, um das mechanische Verhalten der A-Säule zu simulieren, und diese Werte Porsche zur Verfügung gestellt“, sagt Jean-Marie Olivé, Experte für Anwendungsentwicklung bei HPM.
Harz
- Verbundwerkstoffe verstehen
- Lanxess demonstriert Tepex-Verbundmaterial in der Anwendung von strukturellen Brackets
- UAMMI, Impossible Objects bauen Verbundteile für die US Air Force
- Impossible Objects arbeitet mit BASF für den 3D-Verbunddruck zusammen
- INEOS Styrolution baut Produktionsstätte für thermoplastischen Verbundwerkstoff StyLight
- AeroLas erforscht neue Spinntechnologie für thermoplastisches Hybridgarn
- Techsil bringt durchsichtigen Epoxidklebstoff für Verbundsubstrate auf den Markt
- Verbundwerkstoff + Metall:Hybridtechnologie mit Hohlprofil
- SABIC bringt Verbundplatten für Bau und Konstruktion auf den Markt
- Rhodes Interform fertigt Verbundpresse für AMRC