Thermoplaste auf der Suche nach Gewichtseinsparungen in der Luft- und Raumfahrt
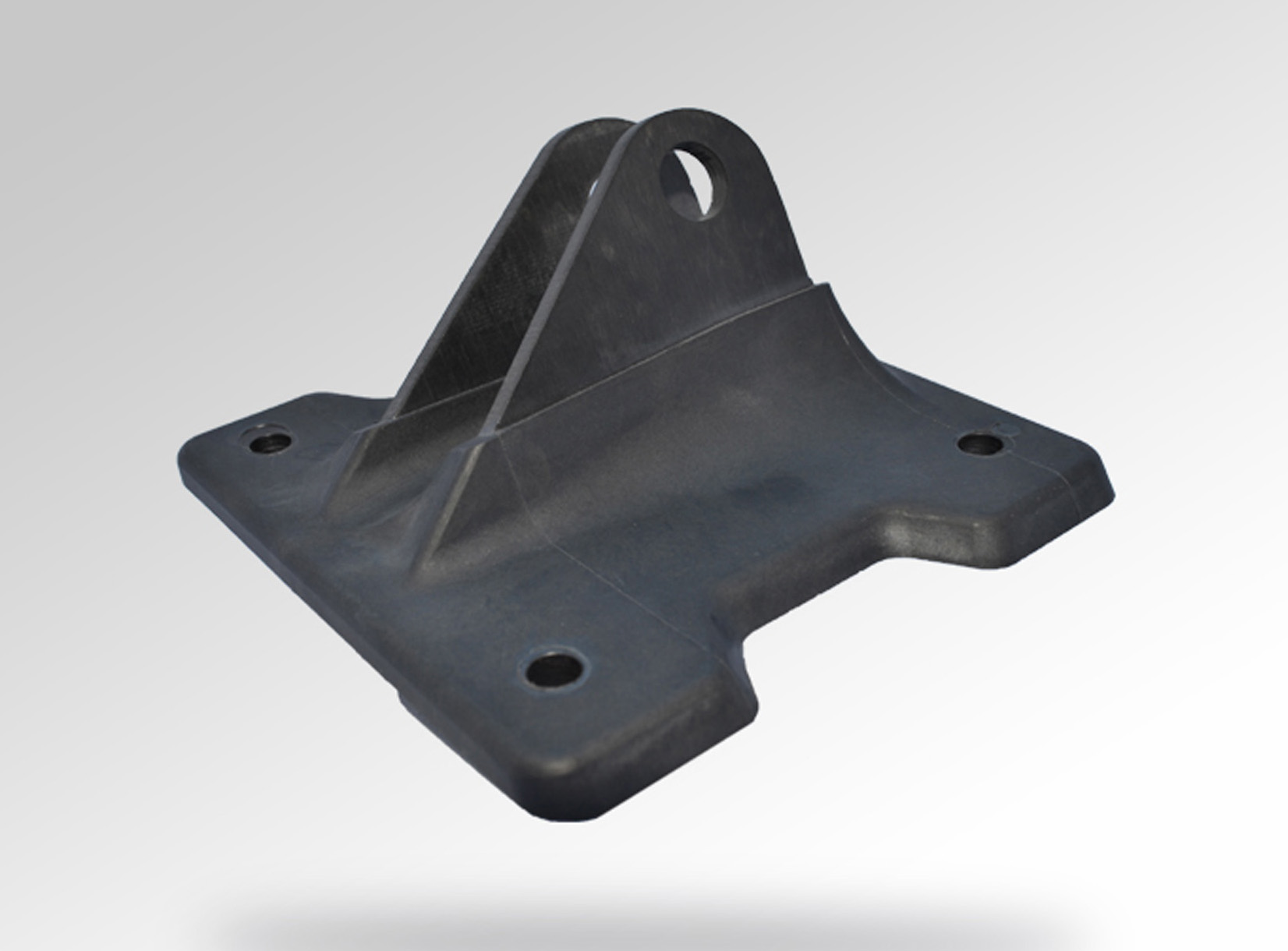
Die von Victrex, Tri-Mack und Safran Cabin entwickelte Halterung für Flugzeugablagebehälter enthält zwei Kohlefaser/PAEK-Einsätze, die mit einem PEEK-Harz umspritzt sind. Das Ergebnis war eine Massenreduzierung von 50 %, eine Kostensenkung von 20 % und eine wesentliche Verbesserung des Buy-to-Fly-Verhältnisses. Quelle | Victrex
Wenn es um die Umrüstung von metallischen Flugzeugstrukturen auf Duroplaste geht Kompositen wurden die meisten tief hängenden Früchte – Flügel, Rumpf und Leitwerk – gepflückt. In Flugzeugen der nächsten Generation werden thermoplastische Verbundwerkstoffe sicher auch bei großen Strukturen eine große Rolle spielen. In der Zwischenzeit gibt es jedoch heute Conversion-Möglichkeiten für Thermoplaste.
Ein solches Teil ist ein selten gesehener, aber sehr wichtiger Typ:innere Tragkonsolen. Dies sind die Halterungen (derzeit Aluminium, Edelstahl und Titan), die Schotten, Toiletten, Bordküchen und Gepäckaufbewahrungsbehälter an Boden und Rumpf eines Flugzeugs befestigen. Diese Halterungen gibt es in verschiedenen Formen und Größen, je nachdem, was befestigt wird. An sich wiegen diese Klammern nicht sehr viel. Da jedoch jedes Flugzeug Hunderte von Halterungen verbraucht, ist das Gesamtgewicht erheblich.
Der Flugzeuginnenausstattungsspezialist Safran Cabin (Huntington Beach, Kalifornien, USA) hat dies erkannt und sich kürzlich an den Spezialisten für thermoplastische Verbundwerkstoffe Victrex (Thornton Cleveleys, Großbritannien) und den Hersteller Tri-Mack Plastics Manufacturing (Bristol, RI, USA) gewandt, um einen Aluminium-Lagerbehälter umzurüsten Kabinenhalterung in neuem Design aus VICTREX AE 250 Kohlefaser/Polyaryletherketon (PAEK) unidirektionalem (UD) Band, umspritzt mit VICTREX PEEK (Polyetheretherketon) 150CA30 Polymer.
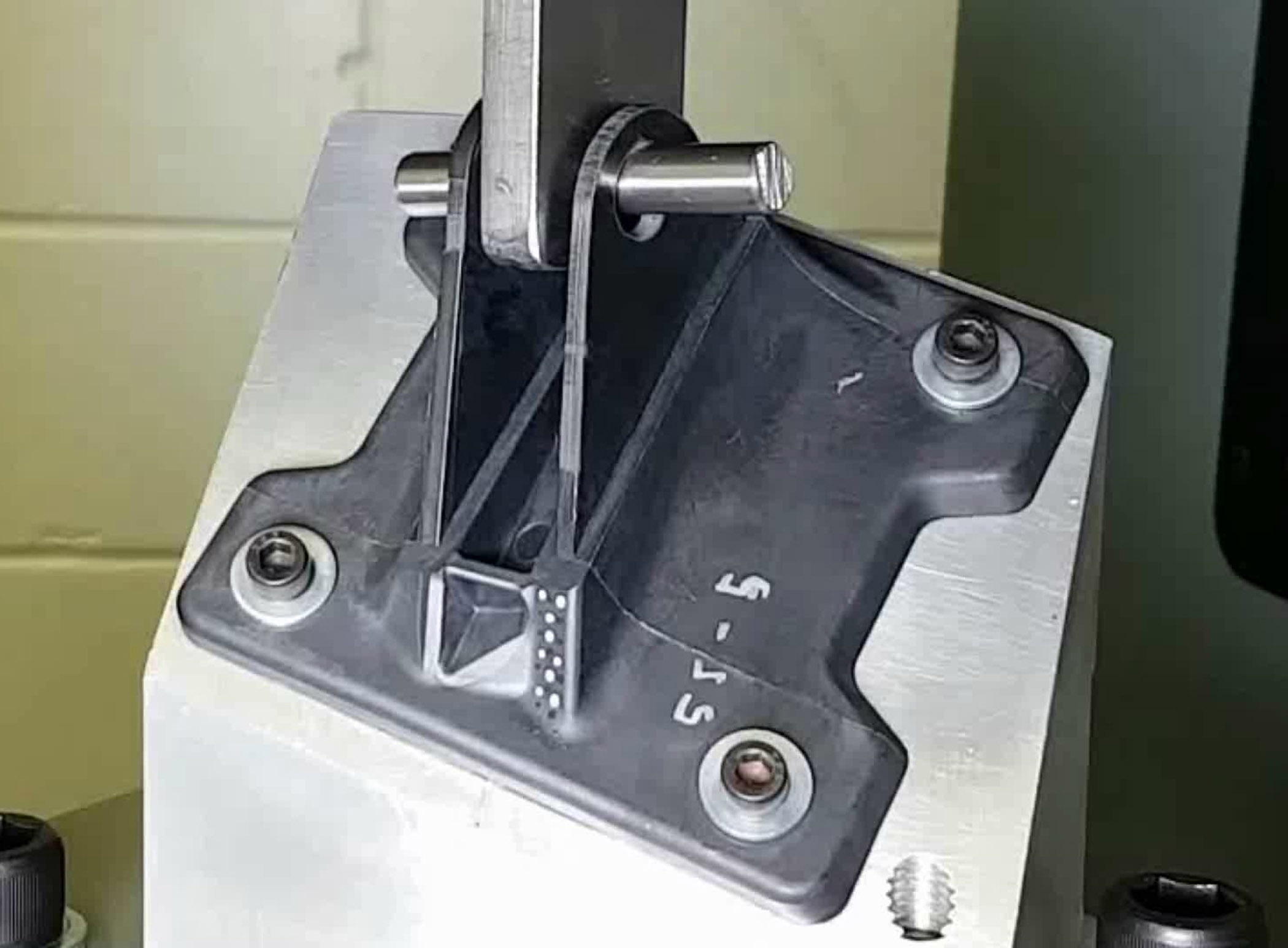
Physikalische Prüfung der umspritzten Halterung. Quelle | Victrex
Die Halterung verfügt über eine rechteckige Basis mit zwei vertikalen Einsätzen, die aus der Mitte der Basis herausragen. Die Basis hat an jeder Ecke ein eingeformtes Loch, um Befestigungselemente aufzunehmen; jeder Einsatz hat auch ein Loch in der Nähe seines Scheitels, um Befestigungsstifte und andere Hardware aufzunehmen. Der Einsatz besteht aus Kohlefaser/PAEK-Material; die Basis wird mit dem PEEK-Harz übergossen.
Victrex und Tri-Mack stellten in Zusammenarbeit mit Safran Cabin die Materialien, die Optimierung der Teilekonstruktion, die Verarbeitungs- und Werkzeugkompetenz zur Verfügung, die erforderlich sind, um Konstruktionsmerkmale zu realisieren und die wichtigsten Leistungsparameter zu erfüllen. Safran Cabin bietet Know-how in Design und Fertigung, um die Anwendbarkeit in Service- und Zertifizierungsumgebungen für die Luft- und Raumfahrt sicherzustellen.
Tim Herr, Director Aerospace bei Victrex, sagt, dass die Einsätze mit einer Fiberforge-Maschine von Dieffenbacher (Windsor, Ontario, Kanada) hergestellt werden, die Kohlefaser/PAEK-UD-Bänder zum Aufbau eines Laminats legt. Dieses Laminat wird pressverfestigt, kantenbeschnitten und dann wasserstrahlgeschnitten, um die Einsätze herzustellen. Beim Wasserstrahlschneiden wird jeder Einsatz an seiner Basis gewellt, um beim Umspritzen eine mechanische Verriegelungsoberfläche zu erzeugen.
Anschließend werden die Einsätze in ein Werkzeug eingelegt, gefolgt vom Umspritzen des PEEK. „Beim Umspritzen“, sagt Herr, „schaffen wir eine sehr starke Verbindung zwischen der PAEK-Verbundeinlage und dem spritzgegossenen PEEK-Material.“ Der Schlüssel zu diesem Enabler ist laut Herr die einzigartige Kombination von PAEK und PEEK. Das PAEK, stellt er fest, hat eine Prozesstemperatur von etwa 40 °C unter der von PEEK. Dieses Temperatur-Delta ermöglicht eine innige und dauerhafte Verbindung zwischen den beiden Teilen. „Ohne die Erfindung von PAEK“, argumentiert Herr, „wäre ein derartiger Hybridguss unmöglich gewesen.“
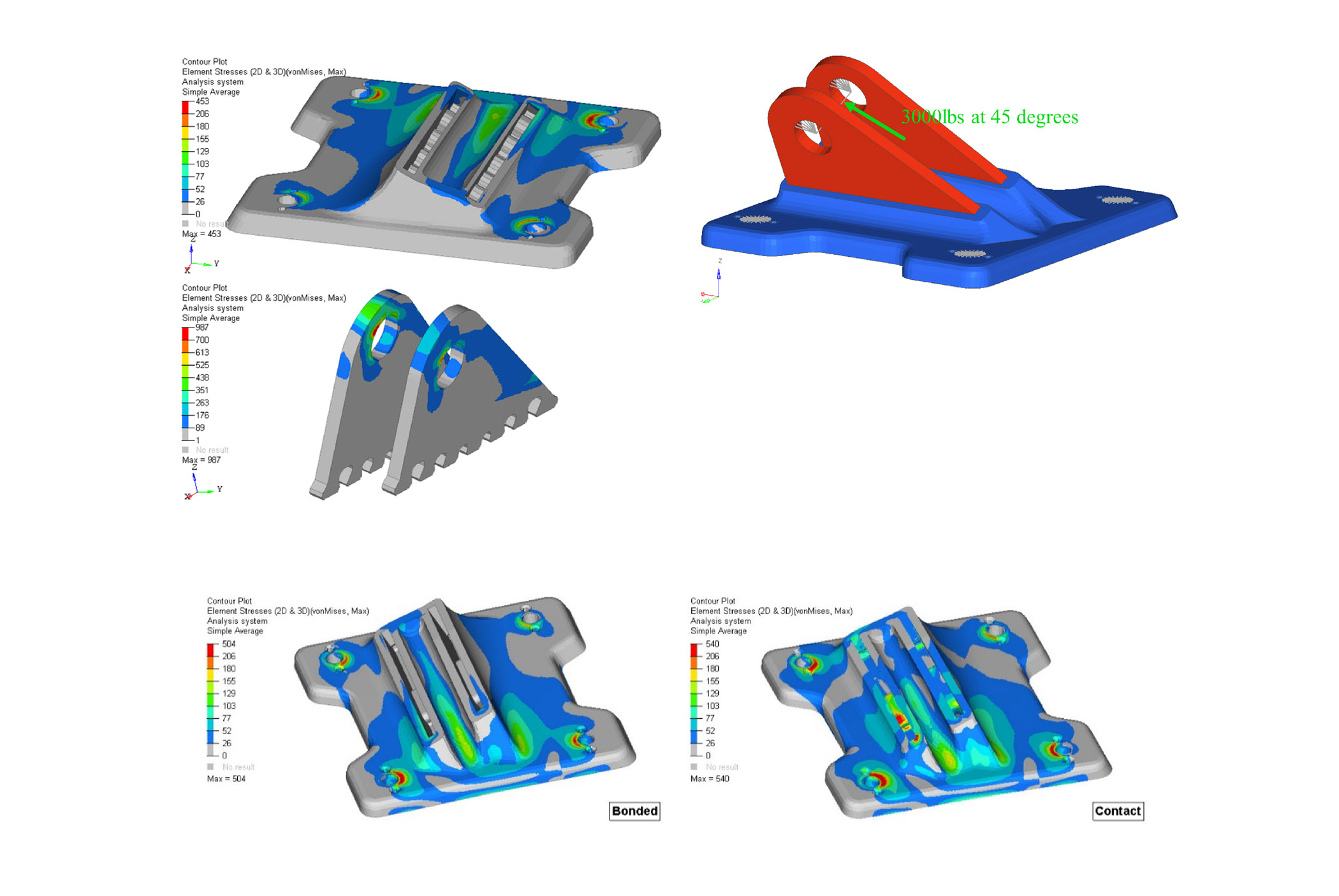
Entwerfen Sie Simulationsbilder der Halterungsleistung unter Lastbedingungen. Quelle | Victrex
Diese Konstruktions-/Prozesskombination erforderte umfangreiche Simulationen, Analysen, Prototypenerstellung und physikalische Tests, durch die Victrex mehrere Konstruktions- und Prozessfehler identifizierte, darunter Einlagenverformung, Harzflussverzögerungen, Bindungs-/Schnittstellenfehler und Hohlräume. Dies schickte Designer zurück ans Reißbrett, um das Design zu optimieren, und Fertigungsingenieure zurück an die Spritzgießmaschine, um Prozessoptimierungen vorzunehmen. Die endgültige Design/Prozess-Kombination überwand diese Herausforderungen und bewies die Realisierbarkeit eines thermoplastischen Composite-umspritzten Brackets.
Die ersten Prototyp-Brackets wurden bei Tri-Mack hergestellt. Im Vergleich zum Original-Aluminiumteil erzielte der Prototyp-Verbundwerkstoff 20 % Kosteneinsparungen, 50 % Gewichtseinsparungen und ein fünfmal besseres Buy-to-Fly-Verhältnis.
„Wir müssen auf viele Anforderungen an Flugzeughalterungen und ähnliche Strukturteile reagieren, wobei jeder Fall viele Belastungs-, Zwangs- und Expositionsbedingungen aufweist“, sagt Tyler Smithson, R&T-Ingenieur bei Safran Cabin. "Der Schlüssel zum Erfolg liegt in der Entwicklung einer flexiblen Verbundwerkstoffplattform, die für mehrere Projekte verwendet werden kann, wodurch wir die Teileanzahl und die Konstruktionskomplexität reduzieren, die Markteinführungszeit verkürzen und die Zeit bis zum Umsatz verkürzen."
Victrex sagt, dass der Hybrid-Overmolding-Prozess eine skalierbare, wiederholbare Technologie ist, die das Potenzial hat, kommerziellen Luft- und Raumfahrtkunden dabei zu helfen, Ausschussraten zu reduzieren, Zykluszeiten zu beschleunigen, die Teilekonsolidierung zu beschleunigen und Sekundäroperationen zu reduzieren.
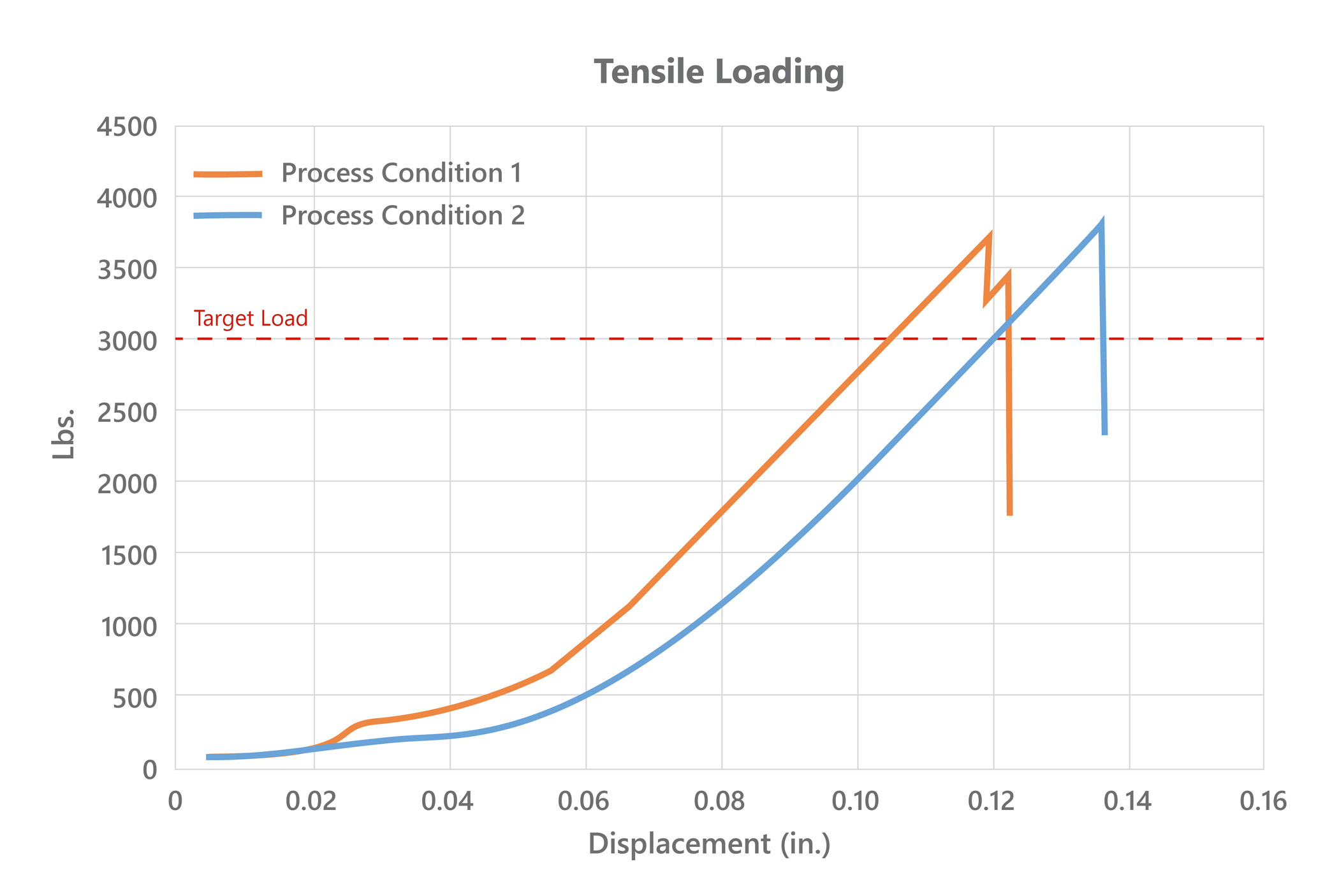
Die Testergebnisse nach der zweiten Design-Iteration der Halterung zeigten eine wesentliche Verbesserung der Belastungsgrenzen und Versagensbedingungen. Quelle | Victrex
„Wir bei Victrex sind stolz auf unsere Erfolgsbilanz bei der Einführung ‚disruptiver‘ technologischer Ansätze in den von uns bedienten Sektoren und nutzen unser Know-how in der Verarbeitung und Leistung von PAEK-Materialien, um den Kommerzialisierungsprozess zu beschleunigen“, kommentiert Herr. „Hybrid-Overmolding und VICTREX AE 250-Verbundwerkstoffe gehören sicherlich zu dieser Kategorie, aber dies ist erst der Anfang. Wir testen unser Angebot an Verbundwerkstoffen weiterhin mit Unterstützung unserer Kunden und Partner, um das volle Potenzial dieser Materialien zu demonstrieren.“
Derzeit ist die Halterung für die Endprüfung und Qualifizierung von Serienteilen vorgesehen. „Das Ziel ist es, das Composite-Bracket später im Jahr 2019 in Betrieb zu nehmen. Wir haben alles in unserer Macht Stehende getan, um zu demonstrieren, dass dieses Bracket leistungsfähig ist“, sagt Herr.
Frank Ferfecki von Victrex, Tyler Smithson von Safran und Chris Bjerregaard von Tri-Mack halten auf der CAMX 2019 im Anaheim Convention Center (Anaheim, Kalifornien, USA) am Dienstag, den 24. September, einen Vortrag über die Entwicklung der Safran-Hybridhalterung:30 Uhr, in Raum 201D
Harz
- Hamilton Aerospace für Wartungsschulungen gelobt
- Vespel®:Das Luft- und Raumfahrtmaterial
- Feuer ohne das Gewicht standhalten
- Sensorfolie für die Luft- und Raumfahrt
- Danke für die Erinnerungen!
- Was sind die Vorteile der Verwendung von Wasserstrahlen für Luft- und Raumfahrtlegierungen?
- Der Markt für Luft- und Raumfahrtkomponenten und Präzisionsflugzeugkomponenten
- Auftragsfertigung für die Luft- und Raumfahrtindustrie
- Was sind die wichtigen Richtlinien für das Design von Leiterplatten für die Luft- und Raumfahrt? -II
- Stickstofferzeugung in der Luft- und Raumfahrtindustrie