PEEK oder PEKK in zukünftigen TPC-Flugzeugstrukturen?
Was ist besser für die in-situ-Konsolidierung (ISC) von Thermoplast-Composite (TPC)-Bändern, die für die Herstellung von primären Flugzeugstrukturen entwickelt werden, Polyetheretherketon (PEEK) oder Polyetherketonketon (PEKK)? Diese Seitenleiste präsentiert die Debatte zwischen PEEK und PEKK, die Teil der größeren Diskussion ist, ob ISC wirklich ein einstufiger Prozess außerhalb des Autoklaven (OOA) ist können die Kosten- und Produktionsratenziele für die zukünftige Flugzeugproduktion erreichen – das sind 60-70 Flugzeuge/Monat für einen Single-Aisle-Jetliner des Typs A320 Neo. Die Alternative besteht darin, zwei Schritte zu verwenden :Auflegen von thermoplastischen Verbundbändern durch automatisierte Faserplatzierung (AFP) und anschließende Verfestigung in einem Autoklaven oder einer beheizten Presse. Weitere Informationen finden Sie unter „Konsolidieren thermoplastischer Verbund-Flugzeugstrukturen, Teil 1“ und „Teil 2“.
Sowohl PEEK als auch PEKK sind Mitglieder der breiteren Polyaryletherketone (PAEK)-Familie, die oft als Polyketone bezeichnet wird . „PEKK sieht PEEK sehr ähnlich und sein Kristallisationsverhalten ist ähnlich, aber seine Verarbeitungstemperatur beträgt 375 °C gegenüber 385°C für PEEK“, sagt Henri de Vries, leitender Wissenschaftler, Verbundwerkstoffe, in der Abteilung für Strukturtechnologie an der Niederländisches Zentrum für Luft- und Raumfahrt (NLR, Amsterdam). Das Fokker-Geschäft von NLR und GKN Aerospace (Redditch, Großbritannien) (Papendrecht und Hoogeveen, Niederlande) hat bei vielen TPC-Technologien in den Programmen TAPAS 1 und TAPAS 2 Pionierarbeit geleistet, darunter eine Torsionsbox mit 12 m Spannweite und zuletzt eine 6 m lange, 28 mm dicke CF/ Oberer Holm des PEKK-Triebwerkspylons, hergestellt aus AFP, aber in einem Autoklaven konsolidiert. (Siehe „Demonstratoren für thermoplastische Verbundwerkstoffe – EU-Fahrplan für zukünftige Flugzeugzellen“).
De Vries sieht PEKK als zugänglicher für AFP, „weil das Prozessfenster breiter ist . Sie müssen für PEEK bei 385-390 °C sein – daher ist eine Verarbeitung bei 360 °C nicht ideal. Mit PEKK ist die Verarbeitung jedoch auch bei 355°C recht gut. So ist nicht nur Ihre untere Grenze niedriger, sondern Sie haben auch etwas mehr Zeit, bevor das Material aushärtet, sodass die Gesamtzeit, die es in der Schmelze ist, etwas länger ist, daher bessere Konsolidierung .”
De Vries fügt hinzu, dass PEKK für das Pressformen interessant ist, die schnellere Option für die Konsolidierung in einem zweiten Schritt im Vergleich zum Vakuumieren und Zyklieren in einem Autoklaven. „Die älteren Sorten von PEKK (DS) waren für das Pressformen zu langsam, aber die neueren Sorten (FC) sind besser und auch günstiger als PEEK.“
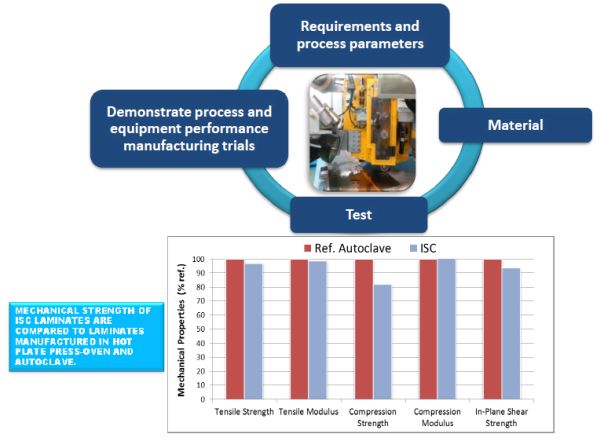
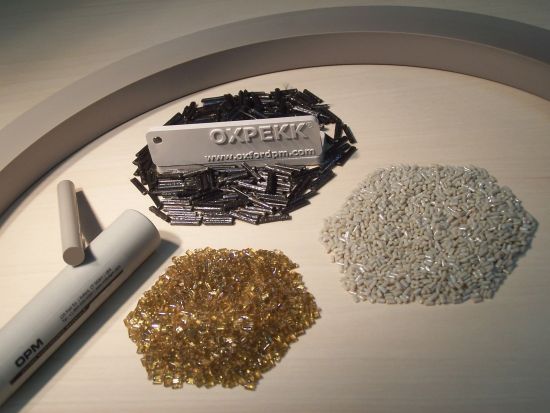
„Oxford Performance Materials (OPM) arbeitet seit 2000 mit PEKK zusammen“, sagt DeFelice und „entwickelt sowohl Materialien als auch Anwendungstechnologien. Alle heute auf dem Markt befindlichen PEKK-Produkte werden nach der DuPont-Methode hergestellt .“ Er erklärt, dass im Grunde alle Polyketone gleichzeitig entwickelt wurden, als Reaktion auf die Notwendigkeit einer verbesserten Feuer-, Rauch- und Toxizitätsleistung (FST) in Flugzeuginnenräumen, die durch die neuen FAA-Bestimmungen in den 1990er Jahren gefährdet wurde . Die Vorschriften kamen jedoch nie zustande und der anfängliche Markt für PEEK und PEKK verflüchtigte sich. So gliederte ICI PEEK an Victrex aus und DuPont verkaufte PEKK an Fiberite, das von Cytec übernommen wurde, das wiederum von Solvay übernommen wurde. DeFelice sagt, dass Arkema ein Partner von OPM wurde, um PEKK-Know-how zu erwerben, und schließlich ein PEKK-Produkt mit der DuPont-Methode entwickelt hat. Als Ergebnis dieser Partnerschaft wurde Arkema die zweite Quelle für PEKK in der Verbundwerkstoffindustrie.
„Hexcel hat auch in OPM investiert“, sagt DeFelice. (Hier machen wir eine kurze Ablenkung, um die Übernahme des additiven Fertigungsgeschäfts von OPM in der Luft- und Raumfahrt und Verteidigung durch Hexcel zu erklären. „Wir haben eine additive Fertigungstechnologie entwickelt, die selektives Laserschmelzen (SLM) mit kohlenstofffaserverstärktem PEKK verwendet, das bei Boeing, Northrop Grumman und anderen qualifiziert ist.“ für AEROSPACE-Anwendungen. Dies war attraktiv für Hexcel, der bereits ein . war wesentlicher Anteilseigner von OPM.“ So erwarb Hexcel im Dezember 2017 das Luftfahrt- und Verteidigungsgeschäft (A&D) von OPM (South Windsor, CT, USA). OPM unterhält jedoch sein 3D-PEKK-Druckgeschäft außerhalb der Luft- und Raumfahrt und Verteidigung und entwickelt seine Kerntechnologien für die Materialwissenschaft weiter.
„PEKK ist nicht gleich PEKK“, versichert DeFelice. „Solvay und Arkema praktizieren die DuPont-Methode, die Hochtemperatursynthese (HTS) verwendet , so dass es etwas schneller läuft, was die Kosten senkt. Es hat jedoch auch seine Nachteile.“ Er erklärt, dass es anfänglich Probleme mit der Schmelzestabilität und Reinheit des PEKK-Polymers gab, die es DuPont erschwerten, Teile herzustellen. Im Laufe der Zeit verbesserte sich das DuPont-Verfahren, ebenso wie das Polymer etwas, und die Teile wurden reproduzierbarer. Über die oben genannten additiven Fertigungstechnologien hinaus hat OPM beispielsweise Spritzguss- sowie Folienanwendungen mit PEKK entwickelt.
„Aber wir haben immer gesehen, dass PEKK anders gemacht und verbessert werden könnte“, sagt DeFelice. „Nun, wenn Sie zu den ursprünglichen Spielern zurückkehren, gab es tatsächlich einen dritten, und das war Raychem , das an BASF verkauft wurde, die PAEK einfach aufgab. Aber die Technologie von Raychem war für die Niedertemperatursynthese (LTS) . Das ist ganz anders als bei HTS.“ Er stellt fest, dass anstelle von Polymer Flocken die muss dann gemahlen werden vor dem Mischen mit Lösungsmittel usw. für Prepreg- und 3D-Druckanwendungen ermöglicht diese patentierte LTS-Technologie die Herstellung eines Pulvers mit Kugelform das ist kontrollierbar. Da LTS ein „kaltes“ Verfahren ist, ist es auch in Bezug auf das Molekulargewicht und die Molekülstruktur des fertigen Polymers viel besser kontrollierbar. Der Prozess ist jedoch langsamer, also etwas kostspieliger. „Aber es ist auch möglich, direkt zum Pulver zu gehen, ohne kein Mahlschritt “, sagt DeFelice. „Dies hilft also, die langsamere Verarbeitung auszugleichen.“
Dieses neue Produkt, OXPEKK-LTS , bietet das Beste aus zwei Welten:einen kontrollierbaren Prozess, der ein Produkt mit einem kugelförmigen Polymerpulver herstellt. „Beim Schleifen erhält man gezackte ‚Felsen‘ aus Polymer, die schwer gleichmäßig zu stapeln sind beim Beschichten und Imprägnieren eines Bandes“, erklärt DeFelice. „Die runde Form von OXPEKK-LTS ermöglicht mehr Präzision während der Bandherstellung. Jetzt können wir das Band verbessern und echte OOA-Verarbeitung ermöglichen durch in-situ-Konsolidierung, die durch die aktuelle Maßtreue des Bandes behindert wird.“
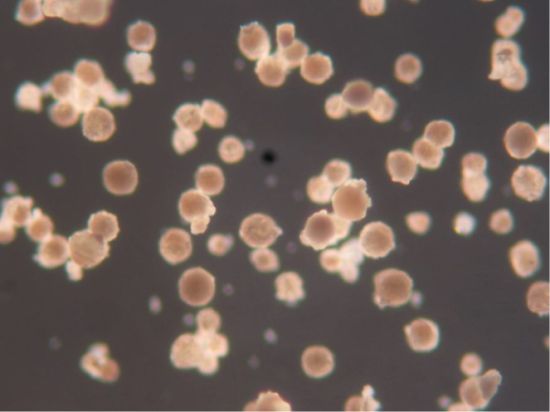
Die kugelförmigen Partikel in OXPEKK-LTS ermöglichen ein gleichmäßigeres thermoplastisches Band,
Dies trägt dazu bei, in-situ-konsolidierte primäre Verbundflugzeugstrukturen in einem Schritt außerhalb des Autoklaven (OOA) zu erreichen. QUELLE:Oxford Performance Materials.
Ist es also möglich, besseres Klebeband zu produzieren und trotzdem den Preis von PEEK zu erreichen? „Die Kosten, über die Airbus und ihre Zulieferer für Primärstrukturen aus Verbundwerkstoff diskutieren, sind viel komplizierter als nur die Kosten für Polymerrohstoffe“, kontert DeFelice. „Rohmaterial ist definitiv ein Teil der Gesamtkosten der Komponenten, aber der Herstellungsprozess und die Leistung sind die wichtigsten Kostenelemente. Erstens ist die Druckfestigkeit von PEKK viel höher als PEEK, was ein wesentlicher Vorteil ist. Sie können eine viel bessere Ermüdung erreichen Leistung in der Verbundstruktur, was wiederum bedeutet, dass Sie leichtere Strukturen entwickeln können die nicht so viel Material benötigen. Mit anderen Worten, wir bieten eine Möglichkeit, höhere Festigkeits-Gewichts-Verhältnisse zu erreichen . Aber wir ermöglichen auch ISC, sodass diese leichteren Strukturen jetzt in einem Schritt hergestellt werden , nicht zwei.“
Aber OPM hört hier nicht auf. DeFelice behauptet, dass alle Kohlenstofffasern, die in verwendet werden, Polyketon Prereg für Luft- und Raumfahrtanwendungen wird ohne Dimensionierung verwendet . Dies ist von entscheidender Bedeutung, da die auf die Faser aufgebrachte Schlichte es ermöglicht, alle verschiedenen Verarbeitungsschritte mit Vorhersehbarkeit, reduzierter Beschädigung und Wiederholbarkeit zu durchlaufen. „Niemand in der Luft- und Raumfahrt verwendet Kohlefasern als Schlichte für die thermoplastische Primärstruktur von PAEK, da alle bekannten Schlichten die mechanischen Eigenschaften nachteilig beeinflussen “, erklärt er.
Eine kurze Anmerkung hier. Matthias Schubert, technischer Service für Teijin Carbon in Europa, widerspricht. „Wir haben eine Sondergröße für PAEK verwendet Thermoplasten seit vielen Jahren“, erklärt er. „Dies war notwendig, weil Standardschlichten aufgrund ihrer Epoxidchemie, die sich bei PAEK-Verarbeitungstemperaturen zersetzt, etwas ausgasen. Unsere Schlichte erhöht tatsächlich die Harzhaftung , was etwa 20 % höher ist als bei Carbonfasern ohne Schlichte .“ Er merkt an, dass dies durch transversale 4-Punkt-Biegetests gemessen wurde und auf die kontrollierte Initialisierung kristalliner Strukturen an der Faser-Harz-Grenzfläche zurückgeführt werden kann. (Beachten Sie, dass diese Größenentwicklung von Jean-Philippe Canart von Teijin Carbon America im Blog „PEEK vs. PEKK vs. PAEK“ erklärt wird.)
„Mit OXPEKK LTS haben wir auch proprietäre Chemie das PEKK in Lösung bringen und als Schlichte verwenden das wird die Beschleunigung weiter beschleunigen und Bandleistung verbessern .“ sagt DeFelice. Dies reicht bis hin zur in-situ-Konsolidierung. „Jetzt zeichnet sich also ein extrem starker Business Case für große Primärstrukturen ab, die mit dieser Technologie hergestellt werden.“
Was ist mit dickeren Bändern? NLR hat angekündigt, ein Band mit einer Dicke von 0,25 Zoll zu haben, das weiter dazu beiträgt, Produktionsraten von 60-70 Flugzeugen/Monat zu erreichen. „Geschwindigkeit widerspricht der Treue im Prozess und Leistung in der endgültigen Struktur“, sagt DeFelice. „Es ist also immer ein Gleichgewicht zwischen diesen gegensätzlichen Faktoren. Die Physik runder Polymerpartikel im Prepregg ist gut etabliert. Wir glauben, dass wir diese Partikel kontrollieren können, was dann mehr Hebel gibt, um das erforderliche Gleichgewicht zu erreichen zur Herstellung großer OOA-Primärstrukturen, die Kosten- und Leistungsziele erfüllen. Wir verfügen über sehr leistungsstarke Tools, um diese Technologie dorthin zu bringen, wo Airbus und andere sie haben wollen.“
Die Erfolgsbilanz von OPM, neue Wege zu beschreiten, gibt dem Unternehmen Vertrauen. „Niemand sonst hat qualifizierten 3D-Druck mit PEKK und Kohlefaser für Raumfahrzeuge mit einer vollen B-Basis zugelassen“, sagt DeFelice, „und niemand sonst hat Schädel-, Wirbelsäulen- und orthopädische Implantate mit FDA-Zulassung, zertifizierter Biokompatibilität und Leistung entwickelt. Wir sind zuversichtlich, dass wir Lösungen für thermoplastische PEKK-Verbundwerkstoffe für Flugzeuge anbieten können.“
OXPEKK LTS wird bis Ende dieses Jahres zu Entwicklungszwecken eingeführt. Das Produkt wird Anfang 2019 im Handel erhältlich sein.
Harz
- Die Zukunft des Live-TV
- Die Zukunft ist…Industrie 4.0
- Die Zukunft ist…Zusammenarbeit
- PEEK medizinische Implantate
- Hochviskoses PEEK für Spritzguss und Extrusion
- Zukünftige Verschlüsse und Verschlüsse:Mehr HDPE, mehr PCR
- Wird KI in Zukunft der Personalabteilung zugute kommen?
- Die Zukunft der Rechenzentren
- Energiezukunft vor Ort
- Aufbau einer Zukunft in Florida