7 komplexe Designs durch 3D-Druck
Indem Ingenieure die Designflexibilität des 3D-Drucks nutzen, können sie selbst die anspruchsvollsten Ideen zum Leben erwecken.
3D-Druck ist eine Technologie, mit der Formen und Merkmale hergestellt werden können, die mit herkömmlichen Herstellungsverfahren nicht erreichbar sind. Um die Leistungsfähigkeit der Technologie zu demonstrieren, untersuchen wir 7 Beispiele beeindruckender Designs, die nur mit 3D-Druck erzielt wurden.
1. Bugattis 3D-gedruckter Titan-Bremssattel
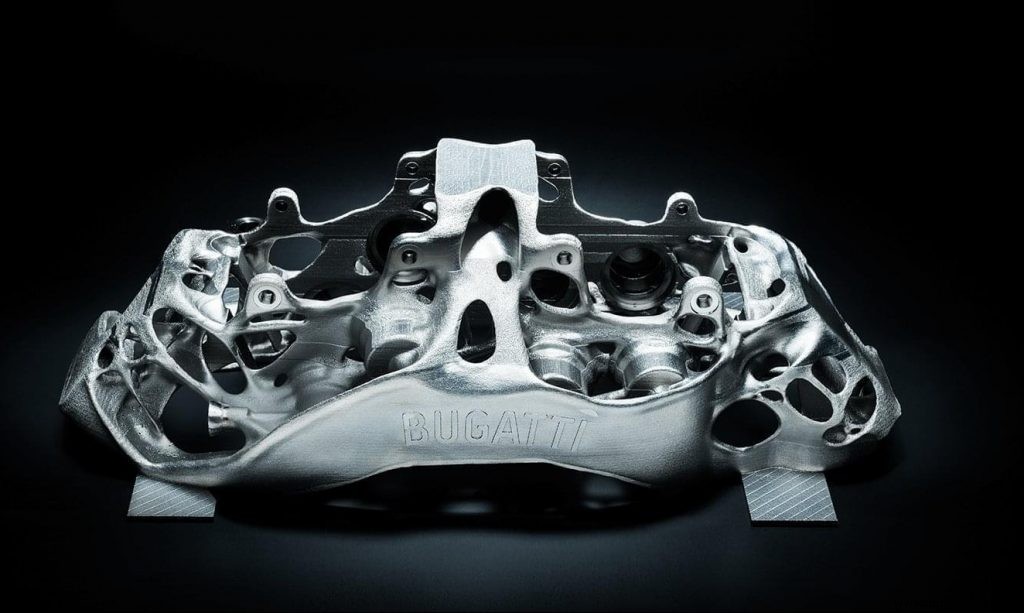
Anwendung:Automobil
Vorteile:Leichteres Gewicht, höhere Festigkeit
Der französische Autohersteller Bugatti nutzte die Designfreiheit des 3D-Drucks für seinen neuesten Supersportwagen Chiron und produzierte den angeblich stärksten Bremssattel der Welt – 3D-gedruckt in Titan.
Der Bremssattel funktioniert zwar wie ein normaler Bremssattel, ist aber durch die Kombination aus 3D-Druck und Titan deutlich stabiler und rund 40 % leichter als das derzeit verwendete Aluminiumteil.
Mit einem Metall-3D-Druckverfahren namens Selective Laser Melting konnte das Bugatti-Team mit einer Vielzahl von Geometrien und Wandstärken experimentieren, die mit herkömmlichen Fertigungstechniken nicht erreichbar sind.
Das Ergebnis:ein filigran geformter Bremssattel mit Wandstärken zwischen 1 mm und 4 mm.
Ende 2018 testete Bugatti den Bremssattel erfolgreich bei hohen Belastungen und jetzt bereitet das Unternehmen die Serienreife des Bauteils vor.
Bugatti ist jedoch nicht das einzige Unternehmen, das das Design von Bremssätteln revolutioniert. Das britische Automobiltechnologieunternehmen Carbon Performance nutzt den 3D-Druck ebenfalls, um „nachhaltige Designs“ für 3D-gedruckte Automobilteile, einschließlich Bremssättel, zu generieren.
Um dies zu erreichen, verwendet Carbon Performance seine neue, KI-gestützte Softwareplattform. Die Plattform hilft bei der Entwicklung von Komponenten, die beispielsweise die Kraftstoffeffizienz eines Autos verbessern können.
Mit seiner Konstruktionssoftware und dem 3D-Druck ist Carbon Performance in der Lage, unter anderem aufgrund des geringeren Gewichts robustere und umweltfreundlichere Bremssättel herzustellen. Durch die Möglichkeit, Leichtmetallteile mit 3D-Druck herzustellen, wird weniger Material benötigt und der Produktionsprozess verursacht weniger Materialabfall als bei der subtraktiven Fertigung.
Leichtbaukonstruktionen sind einer der Hauptvorteile des 3D-Drucks. Da der Trend zu elektrischen und effizienteren Fahrzeugen weiter zunimmt, werden wir sehen, dass immer mehr Autohersteller den 3D-Druck erkunden, um leistungsstärkere, leichtere Autokomponenten zu entwickeln.
2. Generativ konstruierte Sitzhalterung von General Motor
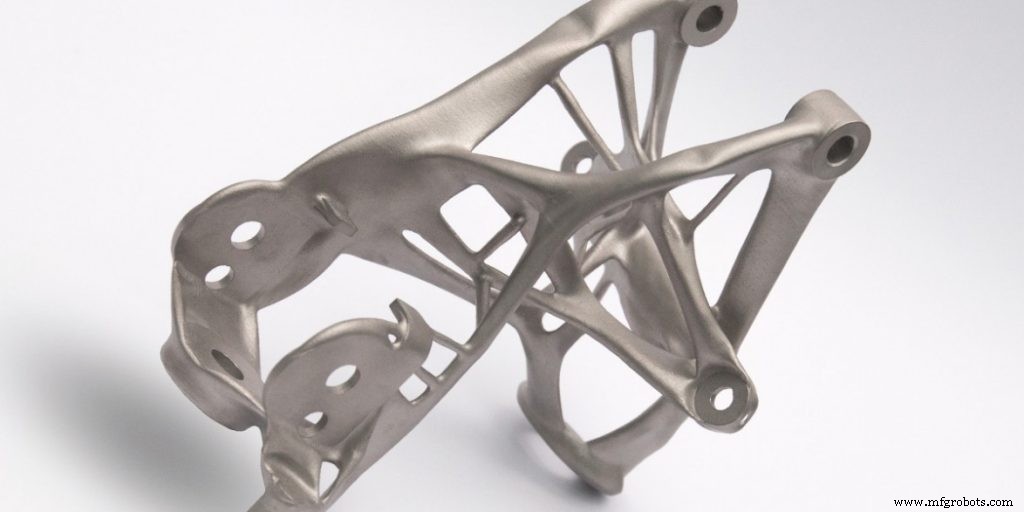
Anwendung:Automobil
Vorteil:Deutliche Gewichtseinsparung
General Motors (GM) hat vor kurzem eine 3D-gedruckte Version einer vorhandenen Sitzhalterung mit generativen Konstruktionswerkzeugen erstellt.
Generative Konstruktionssoftware verwendet fortschrittliche Algorithmen, um automatisch mehrere Konstruktionen zu generieren Varianten basierend auf bestimmten Parametern wie Gewicht, Material, Größe, Festigkeit und Herstellungsverfahren. Die nachfolgenden Designs zeichnen sich durch komplexe, organische Formen aus, die oft nur mit Hilfe des 3D-Drucks zum Leben erweckt werden können.
Dies war bei der Sitzhalterung von GM genau der Fall. Mit der generativen Konstruktionssoftware Fusion 360 von Autodesk wurden 150 Konstruktionsiterationen erstellt. GM wählte dann das Design aus, das den besten Kompromiss zwischen Gewicht, Leistung und Herstellbarkeit bietet.
Das endgültige Design ähnelt kaum der Originalhalterung. 3D-gedruckt in Metall ist die neue Sitzhalterung 40 % leichter und 20 % stärker als das Original. Es wurde auch einteilig hergestellt, im Gegensatz zum Originalteil, das aus 8 Einzelteilen zusammengesetzt werden muss.
Die Fähigkeit des 3D-Drucks, komplexe Teile schneller und flexibler zu erstellen, macht die Technologie zu einer natürlichen Wahl für die Herstellung des neu gestalteten Bauteils. Der in diesem Beispiel gezeigte Vorteil ist die Teilekonsolidierung – die Möglichkeit, mehrere Teile als eine Komponente zu drucken und dadurch Montagezeiten und -kosten zu reduzieren.
Obwohl die Sitzhalterung von GM ein Proof-of-Concept bleibt, sieht das Unternehmen ein enormes Potenzial in der Kombination von 3D-Druck und generativer Designsoftware. Beide Technologien werden in der Zukunft des Fahrzeugbaus sicherlich eine Schlüsselrolle spielen, indem sie eine schnellere Konstruktion und Produktentwicklung sowie die Herstellung komplexer Automobilteile ermöglichen.
3. Das topologisch optimierte Hüftimplantat von Altair
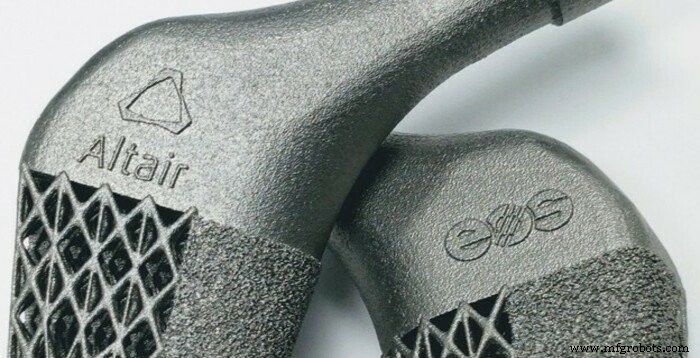
Anwendung:Medizin
Nutzen:Materialoptimierung
Topologieoptimierung ist eine generative Konstruktionstechnik, die es Konstrukteuren ermöglicht, fortschrittliche Algorithmen anzuwenden, um die Geometrie eines Teils zu optimieren. Mithilfe der Technologie kann die Materialverteilung eines Teils optimiert werden, um unnötiges Material aus dem Design zu entfernen.
Ein Unternehmen, das die Topologieoptimierung nutzt, ist das IT-Unternehmen Altair, das 3D-Druck mit Topologieoptimierung kombinierte, um ein verbessertes Hüftschaftimplantat.
3D-Druck bietet eine Reihe von Vorteilen für Hüftimplantate, einschließlich der Möglichkeit, ein Implantat an die spezifischen Belastungen anzupassen, die es tragen muss. Eine Software zur Topologieoptimierung erleichtert dies, indem sie es Ingenieuren ermöglicht, die verschiedenen Belastungsfälle zu berücksichtigen, die ein Hüftimplantat während seines Lebenszyklus sehen könnte.
Durch Eingabe von Parametern wie Lastfällen und Konstruktionsbeschränkungen optimiert die Software die Materialverteilung innerhalb eines definierten Materialvolumens. Dieser Prozess führt zu einem Design, das zeigt, wo Material entfernt werden kann, um das leistungsstärkste Hüftimplantat herzustellen.
Das Altair-Team verwendete diesen Ansatz, um die festen und halbdichten Bereiche des Implantats zu bestimmen, bevor die halbdichten Bereiche mit Gitterstrukturen gefüllt wurden, um das Implantat leichter zu machen.
Im Vergleich zu einem intakten Femur oder einem Femur mit einem handelsüblichen Implantat stellte das Team fest, dass das neue Design dazu beiträgt, die Belastungsgrenze auf etwa 10 Millionen Zyklen zu erhöhen. Das bedeutet, dass das Hüftimplantat das Joggen von Los Angeles nach New York und zurück überstehen könnte – zweimal.
Das neue Design trägt auch dazu bei, den Stress-Shielding um 57 % zu reduzieren. Stress Shielding bezieht sich auf die Verringerung der Knochendichte, die durch das Einsetzen eines Titanimplantats in einen Patienten verursacht wird und letztendlich zu Frakturen und Luxationen führen kann. Aus diesem Grund ist es wichtig, ein Implantat so nah wie möglich am ursprünglichen Knochengewebe zu entwerfen, um Stress-Shielding zu reduzieren und diese unerwünschten Effekte zu eliminieren.
Der 3D-Druck als Fertigungstechnologie ist die einzige Möglichkeit, solche Designs zum Leben zu erwecken. Es ermöglicht nicht nur komplexe Formen wie Gitter, sondern kann sie auch kostengünstiger herstellen als herkömmliche Verfahren.
Topologisch optimierte 3D-gedruckte Implantate finden derzeit erst ihren Weg in die Praxis. Es wird einige Zeit dauern, bis die Aufsichtsbehörden im Gesundheitswesen neue Standardisierungsmethoden für diese neuen Implantatdesigns entwickeln. Mit Blick auf die Zukunft ist jedoch klar, dass der 3D-Druck zu einer Schlüsseltechnologie für die Herstellung besser sitzender, langlebiger und leistungsfähiger Hüftimplantate für einen bestimmten Patienten werden wird.
4. Die 3D-gedruckte Fußgängerbrücke von MX3D
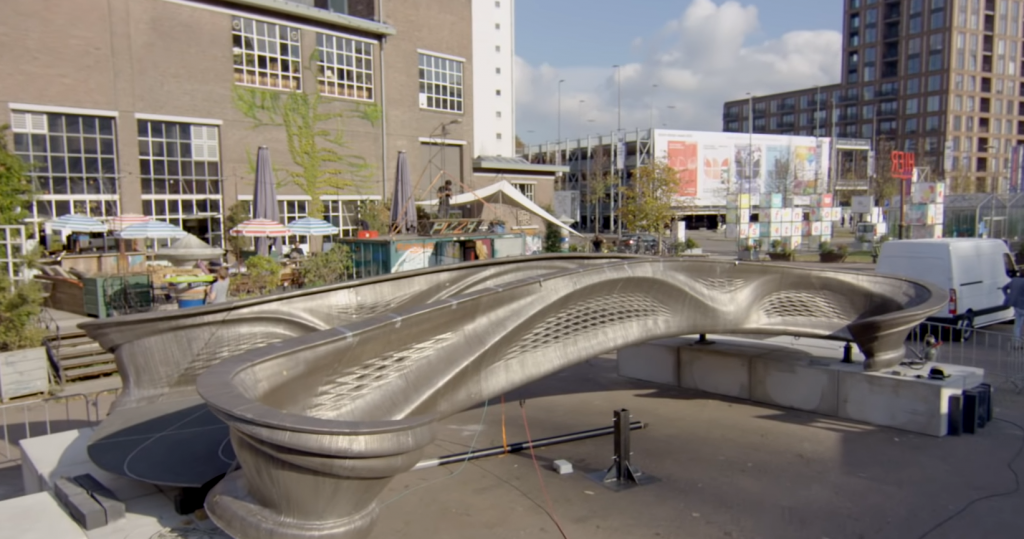
Anwendung:Bau
Nutzen:Innovatives Design
Die auf der Dutch Design Week 2018 vorgestellte 3D-gedruckte Fußgängerbrücke aus Edelstahl von MX3D ist eines der aufregendsten Designprojekte im Bereich des 3D-Drucks.
Durch das Anbringen von Schweißmaschinen an Roboterarmen konnte das MX3D-Team eine 12 Meter lange Brücke in 3D drucken, wodurch ein einzigartiges Aussehen und eine einzigartige Form erreicht wurden. Das Design der Brücke zum Beispiel ist organisch und stoffähnlich, mit vielen Kurven und komplizierten Details. Die Oberfläche der Brücke wurde ungeglättet gelassen, sodass die abgeschiedenen Stahlschichten sichtbar sind, die der Brücke ein raues, ungewöhnliches Finish verleihen.
Interessanterweise war der 3D-Druck nicht die einzige Spitzentechnologie, die für dieses Projekt. Um sowohl die Sicherheit als auch die optimierte Leistung der Brücke zu gewährleisten, ist die 3D-gedruckte Stahlkonstruktion mit einem Netzwerk von Sensoren ausgestattet, um den Zustand der Brücke zu überwachen, die Anzahl der Personen zu erfassen, die sie überqueren und Messungen wie Gewichtsverteilung und Luftqualität.
Das gesamte Projekt dauerte fast vier Jahre und nun soll die fertige Brücke noch in diesem Jahr in Amsterdam installiert werden.
5. GE Research entwickelt einen bioinspirierten Wärmetauscher
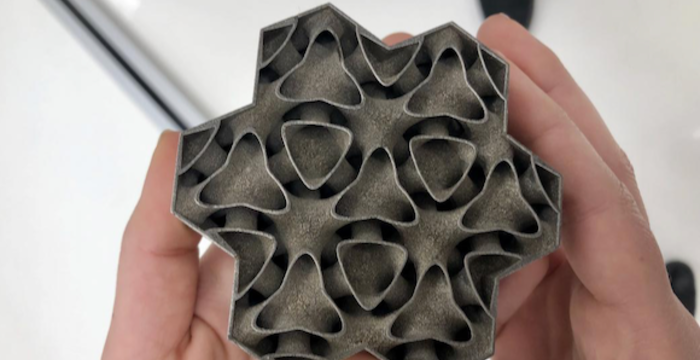
Anwendung:Energie
Vorteil:Verbesserte Leistung
GE Research entwickelt einen ultraeffizienten, emissionsarmen Wärmetauscher für Energieerzeugungsanlagen wie Gasturbinen. Um dies zu erreichen, entwickelte das Team überraschenderweise ein innovatives Design, das von der menschlichen Lunge inspiriert wurde.
Die menschliche Lunge ist einer der effizientesten und kompaktesten Wärmetauscher. Das Organ erfüllt seine Wärmeaustauschfunktion mit einem Netzwerk von Kapillaren, die den Blutfluss in kleine Ströme aufteilen. Dieses Netzwerk erwärmt die kühlere Luft, die wir einatmen, und reguliert gleichzeitig die Körpertemperatur.
Der Wärmetauscher von GE funktioniert ähnlich, jedoch bei viel höheren Temperaturen und Drücken. Das Bauteil verfügt über ein sich verzweigendes Kanalnetz, das heiße Luft aus einer Gasturbine ansaugt. Dieses Netzwerk ist mit einem anderen Netzwerk von Kanälen verflochten, die mit kälterem Arbeitsfluid gefüllt sind und in die entgegengesetzte Richtung verlaufen. Die heiße Luft und das kühle Fluid vermischen sich nicht, aber ihre unmittelbare Nähe ermöglicht es, die heiße Luft abzukühlen, wodurch die thermische Effizienz einer Gasturbine verbessert wird.
Entscheidend war, dass der 3D-Druck die einzige Technologie war, die in der Lage war, solch ein komplexes Design zu produzieren.
Sobald der Entwicklungsprozess abgeschlossen ist, wird GE in der Lage sein, einen Wärmetauscher in 3D zu drucken, der bei 250°C (450°F) Grad höher als die heutigen Wärmetauscher kostengünstig betrieben werden kann. Mit einer deutlich erhöhten Betriebstemperatur repräsentiert das 3D-gedruckte Bauteil eine neue Generation von Hochleistungswärmetauschern.
6. Die leichte Dachhalterung von BMW
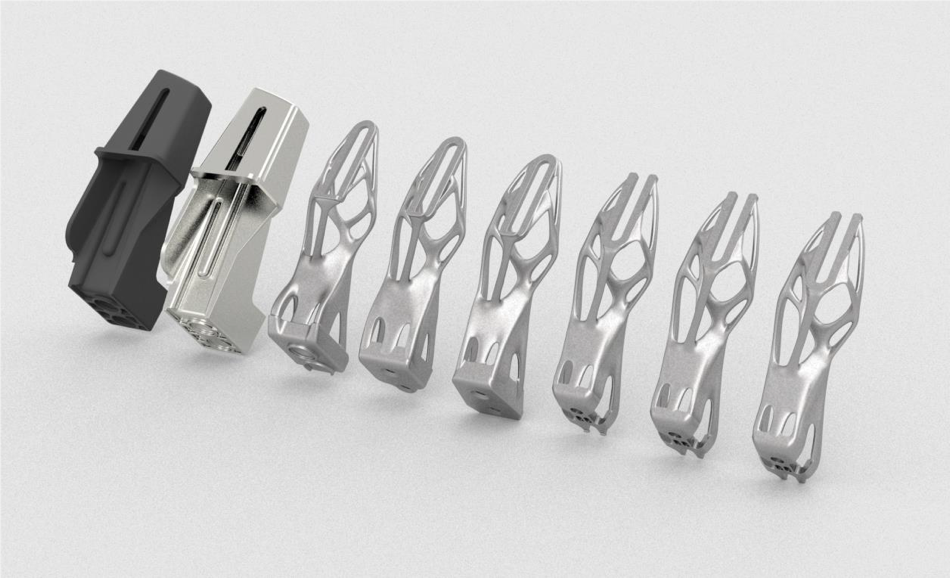
Anwendung:Automobil
Vorteil:Gewichtseinsparung
Im Jahr 2018 hat BMW seinen ikonischen i8 Roadster mit einer preisgekrönten 3D-gedruckten Metalldachhalterung auf den Markt gebracht.
Die Dachhalterung, ein kleines Bauteil, das beim Falten hilft und das Verdeck des Autos aufklappen, erforderte ein neues Design, um die Leistung des Dachfaltmechanismus zu maximieren. Um dieses Ziel zu erreichen, wandten sich die Ingenieure von BMW an Software zur Topologieoptimierung.
Mit dieser Software konnten Ingenieure Parameter wie das Gewicht, die Größe des Bauteils und die Belastung eingeben. Die Software generierte dann ein Design, das die Materialverteilung des Teils optimierte.
Der Entwurf des Ingenieurteams war unmöglich zu gießen. Das Team stellte fest, dass der einzige Weg, dieses Design zu ermöglichen, der Metall-3D-Druck war.
Dank der Selective Laser Melting (SLM)-Technologie haben die Ingenieure eine Metalldachhalterung entwickelt, die zehnmal steifer und 44 % leichter ist als die herkömmliche Alternative.
Das jetzt in Kleinserie produzierte Teil zeigt in Kombination mit der Leistungsfähigkeit von Topologieoptimierungstechniken ein enormes Leichtbaupotenzial für die Fahrzeugkonstruktion.
7. KW Micro Power und VELO3D arbeiten zusammen, um eine Mikroturbinenkomponente zu erneuern
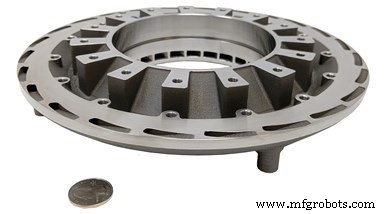
Anwendung:Energie
Vorteil:Komplexe interne Funktionen
Das Engineering-Unternehmen KW Micro Power arbeitet seit einigen Jahren an der Konstruktion eines Mikroturbinen-Generators, stand jedoch bei der Umsetzung dieser Konstruktion in die Produktion vor Herausforderungen. Eine zentrale Herausforderung lag in der Fertigung einer der Komponenten des Gerätes.
Bei der fraglichen Komponente handelt es sich um eine Titanscheibe mit komplexen inneren Kanälen, die zu einer effizienteren Abgasführung beitragen. Beim 3D-Druck in Metall benötigt dieses Bauteil Stützstrukturen, um ein Durchhängen oder Verziehen während des Druckprozesses zu verhindern.
Die Komplexität der inneren Merkmale des Bauteils machte es jedoch unmöglich, die Stützen nach der Produktion zu entfernen.
Um diese Herausforderung zu meistern, hat das Unternehmen mit VELO3D zusammengearbeitet, einem 3D-Druckerhersteller, der seine proprietäre 3D-Metalldrucktechnologie Intelligent Fusion entwickelt hat. Diese Technologie ermöglicht es dem Saphir-3D-Drucker von VELO3D, Teile mit minimalen Stützstrukturen und reduzierten Eigenspannungen zu drucken, die oft die Ursache für Verzug sind.
Dies wird durch einen patentierten berührungslosen Recoater erreicht, der verwendet wird, um eine frische Pulverschicht zu liefern, die geschmolzen und mit einem Laser verschmolzen wird. Wenn beim 3D-Drucken von Metall auf Pulverbasis Pulver auf eine andere Schicht aufgetragen wird, könnte ein Beschichter das Teil ablösen, wenn es nicht auf einer Bauplatte befestigt ist.
Beim Saphirsystem von VELO3D hat die Wiederbeschichtungsklinge keinen Kontakt mit dem Pulverbett. Sobald das Pulver aufgetragen ist, werden eine Schaberklinge und ein Vakuumprozess auf die Oberseite des Pulvers angewendet, um sicherzustellen, dass es absolut eben ist.
Wenn ein Beschichter die vorherige Pulverschicht nicht berührt, braucht ein Teil keine Unterstützung, um es auf einer Metallbauplatte zu verankern. In der Zwischenzeit ermöglichen Simulation und ein geschlossener Regelkreis, der den Drucker mit Strom versorgt, das Drucken komplexer interner Merkmale ohne Stützen.
Um die volle Leistung des Sapphire 3D-Druckers zu nutzen, half das Team von VELO3D KW Micro Power, das Design der Generatorkomponente weiter zu verbessern. Das fertige Teil ist 37 % leichter als das ursprüngliche Design und soll dank reduzierter Belastungen eine bessere Leistung erbringen. Aber noch wichtiger ist, dass das Design, das zuvor als nicht herstellbar galt, dank einer neuen Generation von Metall-3D-Drucktechnologien ermöglicht wurde.
Die komplexesten Ideen zum Leben erwecken
Der 3D-Druck bietet eine enorme Designflexibilität und ermöglicht es Designern und Ingenieuren, mit neuen Formen und Funktionen zu experimentieren, einschließlich topologisch optimierter Formen, Gitterstrukturen und Leichtbaukonstruktionen.
Mit so vielen Möglichkeiten, die der 3D-Druck eröffnet, ermöglicht die Technologie Herstellern die Herstellung innovativer Produkte mit optimierten und kundenspezifischen Designs, die mit herkömmlicher Fertigung unmöglich wären.
Um dieses Potenzial zu erschließen, ist es jedoch entscheidend, Konstruktionsprinzipien zu befolgen, die für die additive Fertigung einzigartig sind. Nur wenn Unternehmen die Möglichkeiten und Grenzen des 3D-Drucks kennen, können sie die Technologie nutzen, um ihre kreativsten Ideen zu verwirklichen.
3d Drucken
- Eine Einführung in den 3D-Druck mit Kunststoffen
- Interview mit einem Experten:Dr. Alvaro Goyanes von FabRx
- 3D-Druck mit Silikon – kommt die Zeit?
- Erste Schritte mit dem Keramik-3D-Druck
- Ein Leitfaden zum 3D-Druck mit HPs Multi Jet Fusion
- Eine kurze Anleitung zum 3D-Druck mit Binder Jetting
- Drucken der Sicherung 1 mit der Sicherung 1
- KUHMUTE gestaltet Mobilität mit SLS-3D-Druck neu
- Hochgeschwindigkeits-3D-Druck mit AION500MK3
- 3D-Druckverbundwerkstoffe mit Endlosfasern