Technologie, die auf die Bearbeitungsanforderungen der Werkstatt zugeschnitten ist
Sie müssen nicht lange suchen, um Werkzeugvoreinstellgeräte zu finden, die den Bearbeitungsanforderungen von Werkstätten nahezu jeder Größe gerecht werden. Der Wert der Offline-Werkzeugvoreinstellung – anstatt die Maschinenspindeln anzuhalten, um Werkzeuge abzutasten, während die Maschinen im Leerlauf sind – erweist sich weiterhin als unschätzbar, insbesondere für die kleinsten Einsteigerbetriebe. Größere Betriebe haben im Allgemeinen erkannt, dass Voreinstellwerkzeuge signifikante quantifizierbare Ergebnisse liefern. Zu diesen Vorteilen gehören laut Brendt Holden, President Haimer USA (Villa Park, IL), die Minimierung von Leerlaufzeiten und Ausschuss, die Senkung der Werkzeugkosten, die Erhöhung der Prozesssicherheit in der Produktion, die Verbesserung der Werkzeugstandzeiten und die Sicherstellung einer gleichbleibenden Produktqualität. „Eine Umfrage, die ich gesehen habe, identifizierte Voreinstelltechnologie ganz oben auf der Wunschliste für den Kauf von Geräten für 2017“, sagte Holden. „Das ist bemerkenswert für eine Investition in Technologien außerhalb der Chipherstellung.“
Anbieter von Präzisions-Voreinstelltechnik haben ihrerseits mit den Anforderungen vom kleinsten Lohnfertiger bis zum Großserienbetrieb Schritt gehalten. Voreinstellmodelle von Basismaschinen der Einstiegsklasse bis hin zu den neuesten anspruchsvollen automatisierten Systemen messen unter anderem Werkzeuglänge, Radius oder Durchmesser, Winkel und Radien. Die wirklichen Unterschiede von Modell zu Modell liegen in der Konstruktion, der Größe der gehandhabten Werkzeuge, der Verwendung hochentwickelter Bildgebungstechnologie und der Verfügbarkeit von Nachbearbeitungs- und RFID-Kommunikationsfunktionen, die beide immer wichtiger werden.
Die Voreinstelltechnologie wurde weiterentwickelt, um Fehler zu minimieren, die durch Bedienerinterpolation und -transkription verursacht werden. Die Erfassung von Messdaten und das direkte Laden in die NC-Steuerungen der Maschine werden durch Kamerasysteme, Laser sowie RFID- und maschinenlesbare Chips erleichtert, die eine nahtlose automatische Datenkommunikation ermöglichen. Das ultimative Ziel der Voreinstelltechnologie besteht darin, die Spindeln am Laufen zu halten und die Maschinen nicht im Leerlauf zu lassen.
Automatisierte Voreinstellung bringt Shops auf Erfolgskurs
Automatisierte Voreinstellung, die Zykluszeiten reduziert und genaue Versatzmessungen ohne zeitraubende manuelle Eingriffe sicherstellt, ist das Ergebnis einer kürzlichen Zusammenarbeit zwischen Rego-Fix Tool Corp. (Indianapolis, IN) und Zoller Inc. (Ann Arbor, MI). Beide Unternehmen haben einen innovativen Ansatz für ein automatisiertes Werkzeugvoreinstell- und Messsystem entwickelt. „Das als Venturion 600 bezeichnete System mit powRgrip-Klemmung macht praktisch jeden Bedienereingriff überflüssig und erhöht somit die Geschwindigkeit, Präzision und Wiederholbarkeit der Werkzeugvoreinstellung erheblich“, sagte David McHenry, Engineering and Technical Manager bei Rego-Fix.
„Durch die enge Zusammenarbeit mit unseren Kunden haben wir festgestellt, dass es eine große Nachfrage nach der Verwendung der powRgrip-Technologie als Teil eines automatisierten Voreinstellsystems gibt“, sagte McHenry. Venturion 600 mit powRgrip ermöglicht hochpräzises Spannen/Lösen, Messen und Voreinstellen von Werkzeugen aller Art. Die drehmomentstarke powRgrip-Spannzangen-Spanntechnologie arbeitet mit weniger als 3 μm Unrundheit und dämpft Vibrationen, um hervorragende Oberflächengüten bei Hochgeschwindigkeits-Bearbeitungsanwendungen zu erzielen.
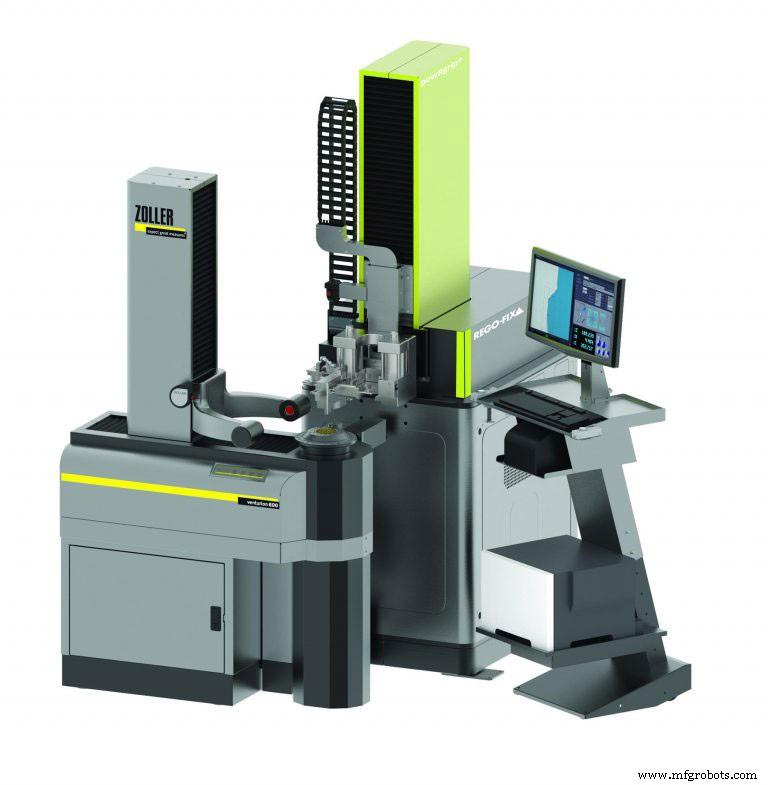
„Die Verbindung fortschrittlicher automatisierter Voreinstelltechnologien mit der von powRgrip erweitert die Anwendungsreichweite von powRgrip weiter, insbesondere in Produktionsumgebungen. Große Produktionsunternehmen – häufig in der Automobil- und Luft- und Raumfahrtbranche – benötigen die Konsistenz und Geschwindigkeit, die nur automatisierte Voreinstellsysteme mit hoher Wiederholgenauigkeit bieten können“, sagte McHenry.
Was macht das Venturion-System so leistungsfähig?
Im Betrieb bietet das Venturion 600 eine einfache und einfache Navigation in Bezug auf Eingabe und Bedienung. Werkstätten erstellen Profile für jedes verwendete Schneidwerkzeug und geben Parameter wie Messlängen und Durchmesser an. Wenn ein Bediener ein Werkzeug voreinstellt, platziert er es in einer Spannzange, dann in dem Voreinstellgerät, wählt die korrekten voreingestellten Informationen in der Software aus und startet das System. Das System misst dann das Schneidwerkzeug, drückt es hinein und misst erneut, um die endgültigen montierten Maße zu erreichen. Als Sicherheitsmerkmal muss der Bediener den Einpresszyklus manuell starten, um sicherzustellen, dass die Hände von der Maschine entfernt sind. Das System druckt dann die Werkzeugdaten aus oder exportiert sie auf einen RFID-Chip.
Die Voreinstellprodukte von Zoller umfassen Hardware für Werkzeugvoreinstellung, Messung, automatisierte Inspektion und Software. Alle Funktionen sind darauf ausgelegt, eine Komplettlösung zur Erfüllung von Prozesssicherheit und Rückverfolgbarkeit zu bieten. Alle gängigen Messfunktionen sind verfügbar, darunter Längs- und Quermaß, Radius, Zwei-Winkel-Technik sowie Rundlauf und Rundlauf.
Werkzeugidentifikation und Datenübertragung, insbesondere für kleine bis mittelständische Unternehmen, erfolgen ohne Netzwerkverbindung. Werkzeuge werden von den Zoller Einstell- und Messgeräten vermessen und die gemessenen Werkzeugdaten in einen QR-Code kodiert, der auf ein Etikett gedruckt wird. Sobald der QR-Code mit dem Lesegerät gescannt wurde, werden die Daten automatisch an die Steuerung der CNC-Maschine übertragen, wodurch die Möglichkeit von Fehlern durch manuelle Dateneingabe durch Eintippen ausgeschlossen wird.
Das Voreinstellsystem Venturion 600 verfügt über eine Zoller-Bildverarbeitungssoftware „pilot“ sowie eine intelligente Touchscreen-Bedienung und intuitive, ergonomische Bedienelemente, die den Workflow optimieren. Ausgestattet mit der Hochpräzisionsspindel „ace“ von Zoller liefert das System eine Rundlaufgenauigkeit von 0,00008″ (0,002 mm) und Werkzeugschnellwechselspannung. Eine CNC steuert die Spindel C Achse zur automatischen Fokussierung der Werkzeugschneide, während ein Drehgeber die vollautomatische Positionierung der Spindel auf den Nennwinkel und/oder die Auswertung des C ermöglicht Achse zum Messen.
Der Bediener muss das Werkzeug nicht manuell zwischen einem Messsystem und der mechanischen powRgrip-Werkzeughaltereinheit mit Venturion 600 bewegen. Das automatische Voreinstellgerät spannt das Werkzeug in weniger als 10 Sekunden, misst dann seine Höhe, bestimmt die Bearbeitungsoffsets und stellt es ein Werkzeug im Werkzeughalter – in nur einer Minute.
Haimer erwirbt bewährtes Voreinstellproduktportfolio
Die Haimer GmbH hat die Microset-Voreinstellgeräte-Produktlinie von DMG Mori übernommen und in Haimer Microset umbenannt. „Die Übernahme der Microset-Reihe von Voreinstellgeräten passt hervorragend zu unserem Lösungsportfolio, das Werkzeughalter, Schrumpfmaschinen und Auswuchtmaschinen sowie 3D-Sensoren und Vollhartmetall-Schneidwerkzeuge umfasst“, sagte Brendt Holden, Präsident von Haimer USA. Das Produktportfolio von Haimer Microset umfasst mehr als 29 Modelle, von der Einsteiger-UNO-Smart-Maschine bis zum linearen Schrumpfmodell VIO.
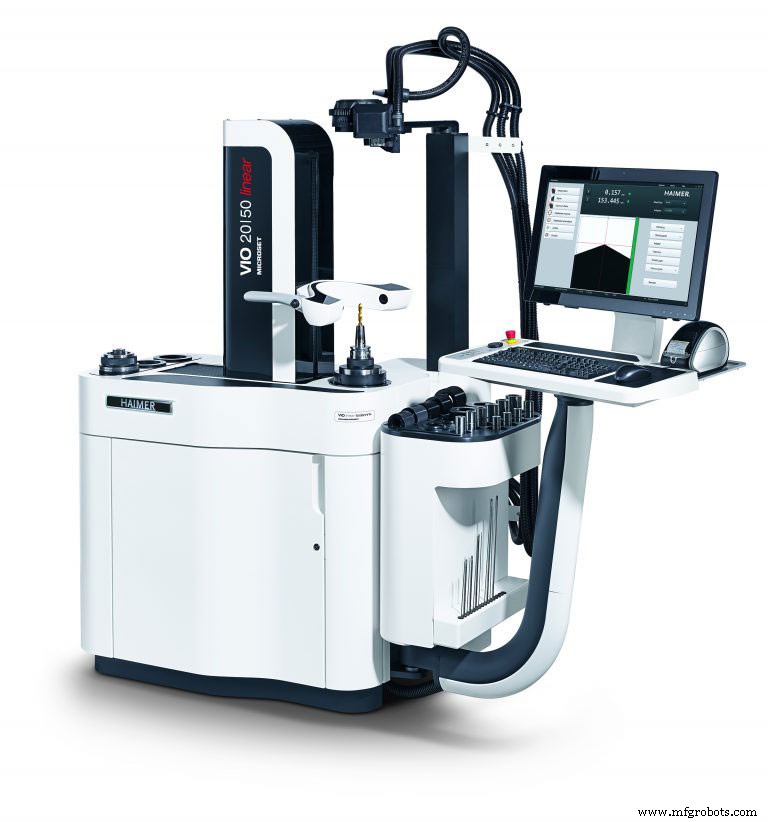
„Eine erfolgreiche Bearbeitung erfordert sowohl leistungsstarke Maschinen als auch hochpräzise Werkzeugspanntechnik, die dafür sorgt, dass die Präzision von der Spindel bis zur Schneide übertragen wird“, so Holden. „Zu den Vorteilen der Voreinstellung gehören die Reduzierung von Ausschuss, die Minimierung zeitraubender Ausfallzeiten und die Bereitstellung genauerer Informationen in der Werkzeugmaschine zur Reduzierung von Ausschuss. Wir können die Werkzeugmaschine voll auslasten, weil wir keine Zeit damit verschwenden, Werkzeuge anzufassen oder ein Werkzeug manuell zu prüfen. Die ganze Zeit über läuft die Werkzeugmaschine, und dort findet sich die wahre Amortisation“, sagte Holden.
„Unsere Herausforderung besteht darin, die richtige Voreinstelltechnik auf die Bedürfnisse des Anwenders abzustimmen. Natürlich muss man mit der hochwertigen Konstruktion des Produkts beginnen, um genaue Messwerte zu erhalten, aber dann fragen wir unsere potenziellen Kunden, welche Bedürfnisse sie in den nächsten fünf Jahren haben könnten. Wollen sie beispielsweise Versatzdaten direkt an die Werkzeugmaschine übertragen“, sagte Holden.
Die Antwort auf die Frage, welches Voreinstellgerät zu wählen ist, findet sich in der Breite der Haimer Microset Voreinstellgeräte-Produktlinie. Einstellgeräte sind mit Werkzeugmaschinen aller Hersteller kompatibel und können bidirektional kommunizieren und nachbearbeiten. Die gemessenen Daten werden direkt an die NC-Steuerungen der Werkzeugmaschinen von Siemens, Heidenhain, FANUC, MAPPS und anderen übertragen, die über USB-Datenspeicher, Ethernet LAN oder RS232 verbunden sind. Darüber hinaus ist RFID-Kommunikation verfügbar. Haimer Microset Voreinstellgeräte können sowohl in der Werkstatt als auch in der Werkzeugkiste verwendet werden.
Die richtige Auswahl des Werkzeugvoreinstellgeräts treffen
Die größte Herausforderung für Betriebe aller Größen, insbesondere aber für Werkstätten, besteht darin, die richtige Auswahl und Wirtschaftlichkeit für die Auswahl eines Einstellgeräts zu treffen, und der einzige Weg, dies zu tun, besteht darin, die Werkzeuganforderungen der Werkstatt wirklich zu prüfen. „Wichtigste Überlegungen sind, das Budget der Werkstatt an die Voreinstellungsanforderungen anzupassen“, sagte Doug Sumner, Produktmanager für Werkzeugmesssysteme, BIG Kaiser Precision Tooling Inc. (Hoffman Estates, IL). „Informationen zu den Anforderungen der Werkstatt umfassen Haltergrößen, die größte Länge und den größten Durchmesser des Werkzeugs, Gesamttoleranzen und Automatisierungsgrad. Ebenso wichtig ist die Organisation der Werkzeugeinstellung in der Werkstatt“, sagt Sumner.
„In Lohnfertigern ist es nicht ungewöhnlich, dass Bediener ihre eigenen Werkzeugeinstellungen direkt in der Werkstatt vornehmen. Speroni-Maschinen sind werkstattgehärtet und wir ziehen es vor, dass die Voreinstellgeräte in der Werkstatt stehen. Es kommt darauf an, wie viele Maschinen und wie viele Werkzeuge pro Schicht im Einsatz sind. Zum Beispiel haben viele Zellen normalerweise einen Voreinsteller, der der Zelle zugeordnet ist“, sagte Sumner.
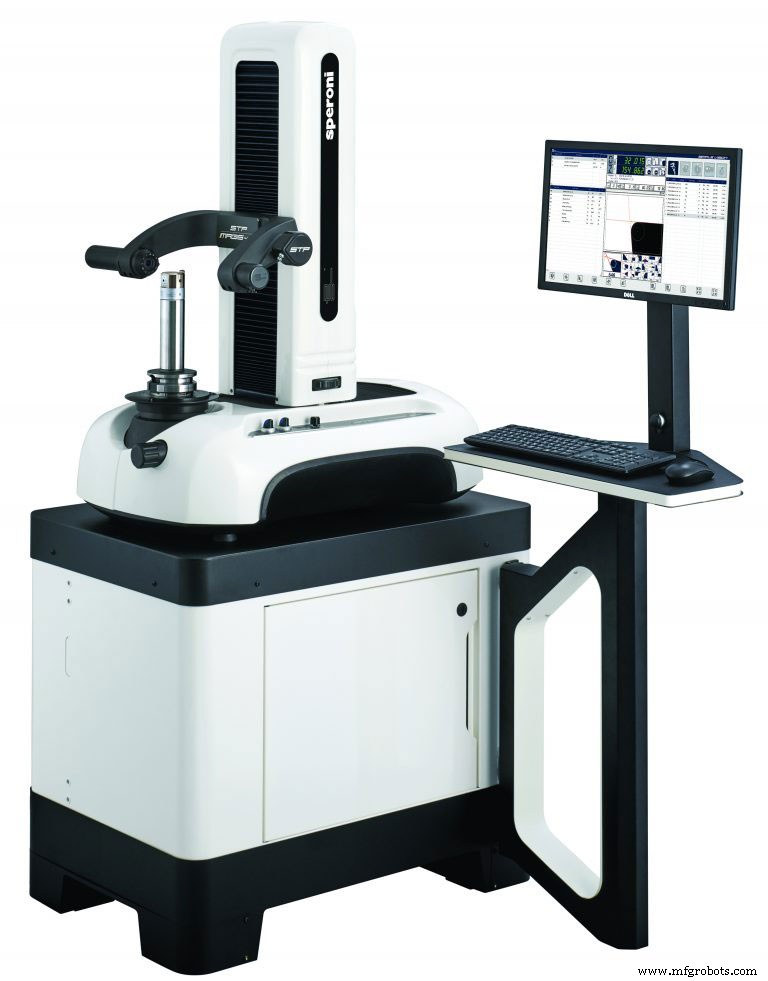
Die Voreinstelltechnologie von Speroni deckt alles ab, von Maschinen der Einstiegsklasse bis hin zu Maschinen, die für Betriebe mit höherer Produktion ausgelegt sind. „Unser Voreinstellgerät der Einstiegsklasse ist das Diaset, das mit einem Anzeigegerät oder einem optischen Projektor geliefert wird. Es ist ein perfektes Einstellgerät für Bohrer, Fräser und Bohrstangen mit einer Genauigkeit von plus minus einem Tausendstel. Für mittelgroße Anwendungen und Werkstätten mit Toleranzen unter einem Tausendstel gibt es das Speroni Magis Tischgerät für Durchmesser unter 14″ [356 mm] in verschiedenen Größen, einschließlich 16, 20, 24″ [400, 500, 600]. mm] in der Länge. Das Magis Benchtop-Werkzeugvoreinstell- und Messsystem verfügt über eine Benutzeroberfläche mit einem einzigen Bildschirm und ist mit manueller Bewegung, Schwerkraftvorschub oder mit Werkzeugklemmung und CNC-Spindel für Rundlaufprüfungen aufrüstbar.
„Das Ein-Kamera-System mit seiner benutzerfreundlichen Steuerung kann Höhe und Durchmesser messen, die Schnittwegmessung des Werkzeugs durch Drehen des Werkzeugs und Arretieren in größter Höhe und größtem Durchmesser sowie Rundlaufprüfungen durchführen. Magis ist unser Bestseller mit Längen von 400, 500 und 600 mm und Durchmessern von 14″ [356 mm]. Mit dem Magis garantieren wir einen Rundlauf von 0,0003″ [0,008 mm] 16″ [406 mm] außerhalb der Spindel“, sagte Sumner.
Speroni Futura ist ein hochpräzises modulares Werkzeugvoreinstellsystem, das entwickelt wurde, um eine wiederholbare Genauigkeit von 1 μm zu erreichen. Die Futura ist in einer Vielzahl von Konfigurationen erhältlich, von einer einfachsten manuellen Maschine bis hin zu einer vollständigen CNC-Maschine. Zu den optionalen Konfigurationen gehören eine zweite Kamera zur Inspektion, CAD/CAM-Integration und RFID. Mit der Speroni Futura und ihrer hochpräzisen Spindel garantieren wir einen maximalen Rundlauf von 0,0001″ [0,003 mm] 16″ außerhalb der Spindel.“
Für den vollautomatischen Betrieb ist das Speroni Futura AutoShrink ein integriertes Voreinstell- und Schrumpfsystem, das von Speroni S.P.A. entwickelt wurde. für die Autoindustrie. Das neueste System wurde als „hands-off“, vollautomatische (bedienerunabhängige) absolut sichere Lösung in Bezug auf die Funktionalität und seine unübertroffene Einstellgenauigkeit von ±2,5 µm eingeführt.
Werkzeug-ID-Verwaltung eliminiert Knopfdruck
Koma Precision Inc. (East Windsor, CT) hat das TID-System (Tool Identification Software) in seine Elbo Controlli-Reihe von Voreinstellprodukten aufgenommen. TID ist ein Werkzeugidentifikationssystem, das eine Schnittstelle zwischen den Werkzeugvoreinstellgeräten von Elbo Controlli und der NC-Steuerung der Maschine herstellt. Das System umfasst einen 2D-Datamatrix-Leser und eine vollständig anpassbare GUI, um Daten direkt von der CNC-Maschine zum Werkzeugvoreinstellgerät zu übertragen.
In der Praxis wird das Werkzeug mit dem Einstellgerät vermessen. Der Datamatrix-Code wird zum Speichern und Aktualisieren mit dem 2D-Lesegerät gescannt. Das Werkzeug wird aus dem Einstellgerät entnommen und zur CNC-Maschine gebracht, wo das Maschinenmodell auf einem Laptop oder Tablet ausgewählt wird. Sobald die Werkzeugdaten in die Werkzeugdatenbank eingelesen sind, wird das Werkzeug ausgewählt und die geladenen Daten erscheinen auf der NC-Steuerung.
„Das TID-System eliminiert nicht nur Maschinenfehler und manuelles Drücken von Knöpfen, sondern sendet auch Werkzeugdaten direkt an die Maschinensteuerung. Die Daten sind anpassbar an Länge und Durchmesser von Werkzeugen, Winkel und Radien sowie Werkzeugverschleiß und Werkzeugstandzeit. Der Benutzer kann Informationen über die erwartete Standzeit laden. Sobald QR-Codes gescannt werden, um die Maschine zu aktualisieren, wird die verbleibende Werkzeuglebensdauer angezeigt“, sagte Tim Murray, Produktmanager von Elbo Controlli, Koma Precision.
„Im Sortiment von Elbo Controlli sind acht Modelle verfügbar. TID ist mit den Modellen Sethy Six, Hathor 6, 66B kompatibel. E46L- und E46TW-Modelle und passt wirklich in Geschäfte, ob klein oder groß und mit 25 oder 25.000 Werkzeugen“, sagte Murray. „Es ermöglicht jedem, Daten schnell hochzuladen, ohne dass jemand den Knopf drücken muss, um die Werkzeuglänge oder den Durchmesser einzugeben. Unabhängig davon, ob Sie sich für eine Einstiegsmaschine, eine Mid-Level-Hathor 6 oder eine High-End-E46L entscheiden, müssen Benutzer, die eine Voreinstellung in Betracht ziehen, Informationen über die maximale Länge und den maximalen Durchmesser von Werkzeugen, das maximale Werkzeuggewicht, die erforderliche Nachbearbeitung und das direkte Senden von Daten bereitstellen und Wiederholbarkeit und Toleranzen verschiedener Arten von Messungen, die erforderlich sind.
Ultrapräzises Werkzeugmessen mit MIDA Diamond VTS
Die visuelle Werkzeugmesseinrichtung MIDA Diamond VTS der neuen Generation von Marposs Corp. wurde entwickelt, um den Genauigkeitsbedarf in der Mikrofertigung in Branchen wie der Luft- und Raumfahrt, der Luftfahrt, der Biomedizin und dem Formenbau zu decken, in denen höchste Präzision für Teile und Formen erforderlich ist. Die dabei eingesetzten Werkzeuge werden immer kleiner und erreichen Durchmesser von 0,1 mm oder weniger. Infolgedessen definieren diese Mikrowerkzeuge die Regeln der Werkzeugmessung auf der Maschine neu, wo herkömmliche Antasttechniken einfach nicht verwendet werden können.
Die neue kompakte MIDA Diamond VTS zeichnet sich durch eine reduzierte Maschinentischfläche und eine Wiederholgenauigkeit von 0,2 μm aus, die durch die begrenzten Tischabmessungen nicht beeinträchtigt wird. Das VTS-System misst Werkzeugabmessungen durch die Verarbeitung von Bildern, die von einer CCD-Kamera aufgenommen wurden. Zu den relevanten Parametern gehören Längen- und Durchmessermessung, Werkzeugrundlauf, Fräserradius, Werkzeugmitte, Einzelfräserintegrität und thermische Drift der Maschinenachse. Das VTS ist in der Lage, Werkzeuge mit einem Durchmesser von nur 10 μm zu prüfen und erreicht dank einer Systemauflösung von 0,1 μm Wiederholgenauigkeitswerte von 0,2 μm.
VTS misst Werkzeuge, während sie mit voller Spindeldrehzahl rotieren. Dadurch, dass der Anwender die Spindel zur Kontrolle des Werkzeugs nicht abbremsen muss, verkürzt sich die Voreinstellzeit und die Messgenauigkeit wird erhöht. VTS kann auch zur manuellen Analyse von Werkzeugoberflächen verwendet werden. Ein kontinuierliches Frontlicht ermöglicht es dem Bediener, die beleuchtete Werkzeugoberfläche auf einem PC-Monitor zu sehen, wodurch der Bediener die Integrität des Schneidwerkzeugs beurteilen kann.
Die VTS-Einheit ist für die Installation im Maschinenarbeitsbereich konzipiert und verfügt über ein doppeltes Schutzsystem, um eine hohe Beständigkeit gegen raue Maschinenumgebungen zu bieten. Pneumatische Verschlüsse bedecken und schützen die optische Linse, wenn VTS nicht arbeitet. Darüber hinaus bildet ein Luftstrom aus dem optischen Fenster eine Luftbarriere, die Späne und Kühlmitteltropfen abweist, die Verschlussseite sauber hält und die optische Linse schützt, wenn der Verschluss geöffnet ist.
Automatisierungssteuerung System
- Doppelspindel-Technologie ein Segen für Autohersteller
- Werkzeugdurchbiegung in der CNC-Bearbeitung
- Strategien zur Verringerung der Werkzeugdurchbiegung bei der CNC-Bearbeitung
- 5-Achsen-Bearbeitung mit Fusion 360
- Bearbeitungsgrundlagen:Werkzeuglängenversatz
- Abstechen mit Y-Achsen-Bearbeitung
- Werkzeuglebensdauer, Skalierbarkeit treiben neues Denken in der Bearbeitung voran
- Drehzentrum und Maschinentechnik
- Bearbeitungsprozess und Werkzeugmaschine verstehen
- CNC-Bearbeitungszentrum-Technologie