Ein 5-Schritte-Ansatz für erfolgreiche Industrie-4.0-Projekte
In meinem letzten Blogbeitrag „Industrie 4.0 gewinnt in Asien-Pazifik an Fahrt“ habe ich Einblicke in den aktuellen Stand von Industrie 4.0 im asiatisch-pazifischen Raum gegeben. Heute möchte ich einen genaueren Blick auf die Schritte werfen, die erforderlich sind, um einen erfolgreichen Proof of Concept (POC) für ein Industrie 4.0-Projekt zu erstellen. Ein POC-Projekt zeigt die Möglichkeiten der Industrie 4.0-Technologie bei geringem Risiko und überschaubarem Kapitaleinsatz. Dies sollte der erste Schritt einer Implementierung sein, nachdem die spezifischen Schwachstellen identifiziert wurden, die in Ihrem aktuellen Herstellungsprozess angegangen werden müssen.
Schritt 1:Festlegen der Geschäftsziele
Ein Großteil der Industrie 4.0-Projekte beginnt damit, dass Betriebsleiter versuchen, Probleme zu lösen oder ihre tägliche Arbeit auf dem Shopfloor zu verbessern. Daher besteht der erste Schritt des Ansatzes darin, die betrieblichen Probleme zu identifizieren und zu verstehen, mit denen sie ständig konfrontiert sind. Welche betrieblichen Fragen adressiert Industrie 4.0? Gibt es einzigartige Geschäftsziele oder Kundenanforderungen, die strenge Messungen erfordern? Anschließend müssen klare Kennzahlen festgelegt werden, die als Vergleichsgrundlage dienen.
Schritt 2:Prototyp erstellen
Der nächste Schritt besteht darin, einen Plan zu formulieren, um ein Test-POC-Projekt mit einem begrenzten Budget durchzuführen. Ziel der Erprobung ist die Optimierung durch manuelle Prozessverbesserungen auf Basis der Analyseergebnisse. Die Quantifizierung dieser Gewinne ist ein wichtiger Indikator (in der Validierungsphase) dafür, ob die Studie breiter ausgeweitet werden sollte.
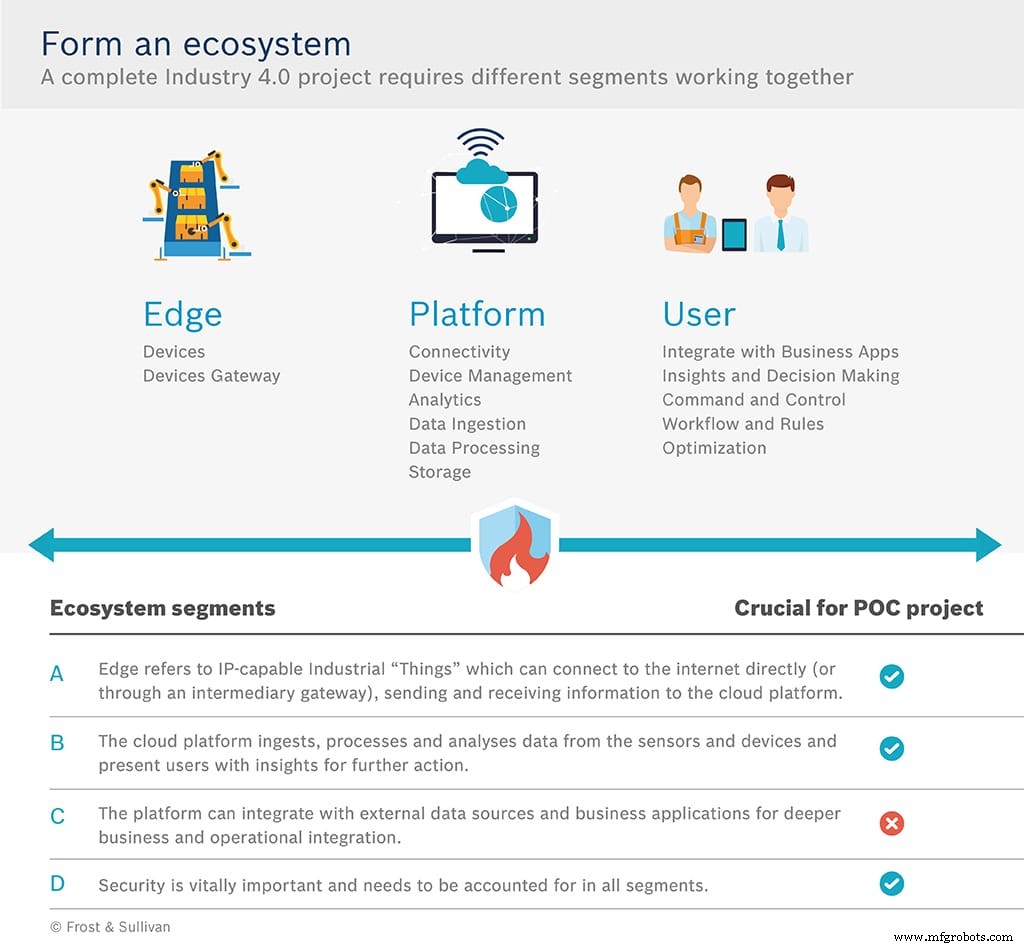
Für die Zwecke eines POC-Projekts ist es entscheidend, eine Cloud-Plattform zu nutzen, um Daten von den Sensoren zu sammeln sowie diese Daten zu verarbeiten und zu analysieren. Cloud Computing ermöglicht bequeme und kostengünstige Verbindungen von den Sensoren zur Plattform. Eine Testversion mit einer Industrie 4.0-Cloud-Plattform in einer öffentlichen Cloud ermöglicht die Erstellung einer kleinen Bereitstellung innerhalb kurzer Zeit zu minimalen Kosten, sodass keine Investitionen in Server und Ausrüstung erforderlich sind.
Schritt 3:Validierung der Ergebnisse
Nach Abschluss des POC-Projekts können die Ergebnisse der Studie quantifiziert und zur Genehmigung durch das Management validiert werden. Die von Sensoren der Pilotmaschinerie gesammelten Daten können verwendet werden, um Ineffizienzbereiche oder Probleme zu identifizieren, die möglicherweise zu schwerwiegenderen Fehlern führen können. Manager können diese Informationen anwenden, um Prozessverbesserungen zu definieren und Verschwendung zu reduzieren. Diese Verbesserungen sollten dann im Shopfloor für eine weitere Runde der Datenerhebung und -validierung implementiert werden. Anhand der in der Geschäftszielphase definierten Baseline können die Teams dann eine gründliche Analyse des neuen Status und der Situation im Vergleich zum Benchmark durchführen. In Bezug auf die wichtigsten Probleme, die von Fertigungsbetrieben identifiziert wurden, sind einige potenzielle Metriken:
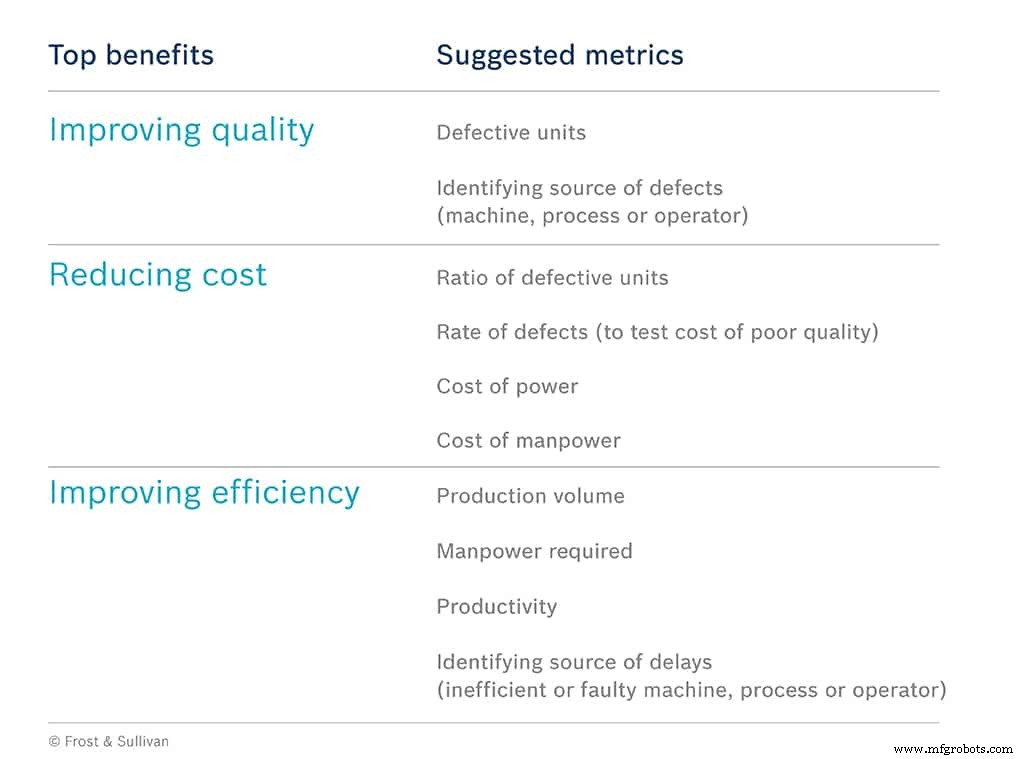
Schritt 4:Replizieren erfolgreicher Anwendungsfälle
Nachdem die Teams die Daten verifiziert und die Anwendungsfälle überprüft haben, kann der POC als Erfolg gewertet werden, wenn er die Projektziele erreicht hat. Da das System nun für den Pilotsatz von Sensoren und Geräten funktioniert, besteht der nächste Schritt darin, das Setup auf weitere Maschinen und Linien auszuweiten.
In diesem Schritt kann die Systemkomplexität dramatisch zunehmen, daher ist es für den Hersteller wichtig, sich mit einem vertrauenswürdigen Industrie-4.0-Partner zusammenzuschließen. Dieser Partner kann mit dem Hersteller zusammenarbeiten, um eine ganzheitliche Vision für die Umsetzung von Industrie 4.0 zu entwickeln, die darauf ausgelegt ist, erweiterte Ziele und Metriken zu erfüllen und in einem phasenweisen Ansatz bereitgestellt wird, damit der Betrieb nicht unterbrochen wird. Das anfängliche POC-Projekt mag mit einigen verbundenen Systemen gut funktioniert haben, aber was ist, wenn die neue erweiterte Implementierung dies auf Hunderte oder Tausende erhöht? Es können auch mehr Arten von Daten erfasst werden, von einfachen Temperatur- oder Drehmomenteinstellungen bis hin zu Daten wie Standort, Luftfeuchtigkeit oder Licht.
Die Erhöhung der Anzahl von Datenpunkten, Sensoren und vernetzten Maschinen wird zu einem drastischen Anstieg der Datenmenge führen. Eine einfache Möglichkeit, dies auszugleichen, besteht darin, die Cloud-Bereitstellungen zu nutzen, um die Rechen- und Speicherkapazität zu erweitern. Die Zunahme der Daten, die auf zentral gelegenen Servern gespeichert werden, erfordert jedoch auch strengere Sicherheitsmaßnahmen zum Schutz und zum Schutz der Daten, die für jedes Unternehmen von entscheidender Bedeutung sind. Gleichzeitig muss durch diese Maßnahmen sichergestellt werden, dass alle Daten dem autorisierten Personal leicht zugänglich sind.
Schritt 5:Durchführen eines globalen Rollouts
Nachdem Sie Ihren Proof of Concept erstellt und getestet haben, ist es Zeit für den letzten Schritt. Hier gilt es, durch die Erweiterung vernetzter Industrie-4.0-Systeme außerhalb des Werks in das breitere Ökosystem weitere Effizienz und Sichtbarkeit zu gewinnen.
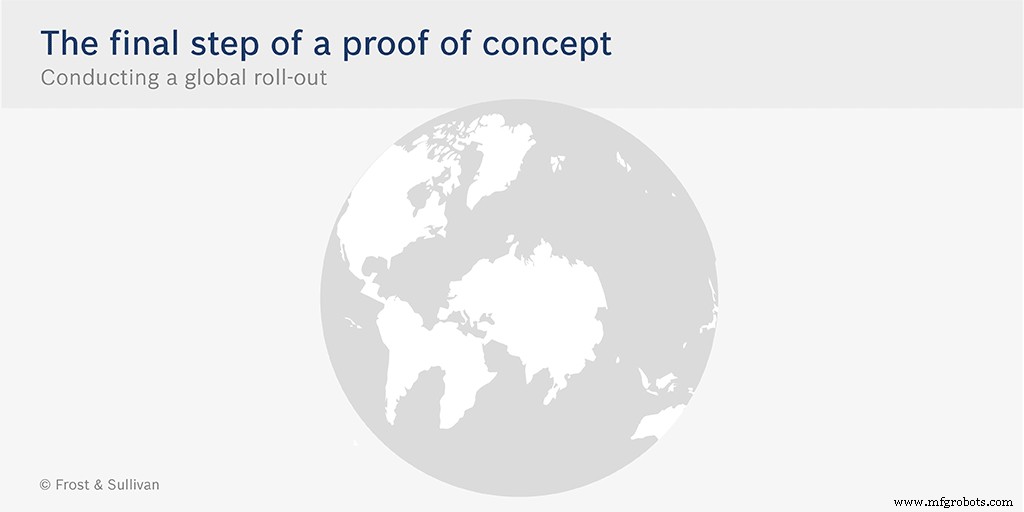
In einem vernetzten Ökosystem weniger Inventar halten
Durch die Ausweitung der Kommunikations- und Datenverfügbarkeit auf verbundene Lieferkettenpartner können Industrie 4.0-Systeme Informationssilos zu einer vernetzten Lieferkette verknüpfen. Das Ergebnis ist ein integrierter Workflow, der effizienter und dennoch so agil ist, wie es das Geschäft erfordert. Vernetzte Ökosysteme können die Just-in-Time (JIT)-Lieferung von Rohstoffen und Ersatzteilen sicherstellen und Fertigwaren effizient durch Logistikkanäle lenken. Dies reduziert überschüssige Lagerbestände und senkt die Logistikkosten, während gleichzeitig die Belieferung der Kunden beschleunigt wird. Es ermöglicht den Betreibern auch, schnell auf Marktveränderungen zu reagieren, wie beispielsweise einen plötzlichen Rückgang oder einen Anstieg der Bestellmenge.
Erfassung hochwertiger verderblicher Waren
Ein weiterer Vorteil des Beitritts zum breiteren Ökosystem wäre die Möglichkeit, sicherzustellen, dass sensible Güter innerhalb bestimmter Parameter und Fristen ordnungsgemäß geliefert werden. Nehmen Sie die Lebensmittel- und Getränkeindustrie, in der die Komplexität und die Kosten, die mit der Verfolgung frischer Produkte vom Feld bis zum Verbraucher verbunden sind, seit langem ein wichtiges Anliegen sind. Es besteht ein dringender Bedarf an Echtzeiteinblicken und -informationen zu Lieferkettentransaktionen. Intelligente Geräte werden jetzt zwischen den Produktchargen platziert, um wichtige Informationen zwischen den wichtigsten Teilnehmern der Wertschöpfungskette zu übertragen und sicherzustellen, dass die frischen Produkte im besten Zustand das richtige Ziel erreichen.
Ausweitung von Industrie 4.0 auf vernetzte Fabriken
Das ultimative Ziel wäre es, mehrere Fabriken zu verbinden, um den maximalen Nutzen aus Industrie 4.0-Systemen zu ziehen. Je mehr Maschinen an das System angeschlossen sind, desto mehr Daten werden aus der Produktion gesammelt, wodurch ein umfangreicherer Datensatz entsteht. Dies bietet dem Management einen konsolidierten Überblick über die globalen Operationen und ein vollständiges Bild der Produktion, um eine bessere Entscheidungsfindung zu unterstützen. Diese Entscheidungen könnten zu optimierten manuellen Prozessen führen, um die Effizienz zu verbessern, oder zu einer vorausschauenden Fehlererkennung, um Ausfallzeiten zu vermeiden. Ein weiterer Vorteil besteht darin, dass Analysen dieses größeren Datensatzes Fehler in ähnlichen Maschinen erkennen können, wodurch immer genauere vorausschauende Wartungspläne erstellt werden, die letztendlich ungeplante Ausfallzeiten reduzieren.
Prozessverbesserung durch Lernen von einem Team
Da nun alle Systeme auf einer einzigen konsolidierten Plattform vereint sind, können Teams problemlos Prozesse analysieren, die erfolgreiche Metriken und Best-Practice-Verbesserungen aufzeigen, und sie dann zur Implementierung in anderen Fabriken auf der ganzen Welt freigeben. In ähnlicher Weise können auch Schritte zur Problemlösung zur Überwindung von Problemen geteilt und umgesetzt werden.
Industrietechnik
- Fragen und Antworten mit einem Industrie-4.0-Lösungsarchitekten
- Lean Production trifft auf Industrie 4.0
- Instandhaltungsprojekte mit Auszeichnung der Verteidigungsindustrie ausgezeichnet
- Ein dreistufiger Ansatz für eine erfolgreiche IoT-Einführung
- Vorbereitung auf Industrie 4.0
- Vor- und Nachteile von Industrie 4.0
- Nachhaltigkeit:Die Herausforderung von Industrie 4.0
- Automatisierung in der Industrie 4.0
- Die Umsetzung eines Qualitätsansatzes in der Branche
- Arbeitsanweisungen in Industrie 4.0