Transparentes Holz und andere Durchbrüche in der Holzwissenschaft
Vielseitig, klimaneutral, erneuerbar. Nein, das ist nicht der Marketing-Slogan für ein gerade neu entwickeltes Material, sondern drei wesentliche Merkmale eines altbekannten Werkstoffs – Holz – ein Werkstoff, der uns bis heute durch seine Wandlungsfähigkeit überrascht und immer wieder überrascht an der Spitze der Materialentwicklung. In diesem Artikel werde ich auf einige dieser spannenden Entwicklungen eingehen – von transparentem Holz bis hin zu karbonisierten Holzverbundwerkstoffen.
Zunächst eine kurze Auffrischung zum Thema Holz. Holz ist ein natürlicher Verbundstoff aus Zellulosefasern, die in eine Ligninmatrix eingebettet sind. Zellulose wirkt als lange Stäbe entlang des Stammes und verleiht dem Holz seine Zugfestigkeit, während die Ligninmatrix dem Holz seine Druckfestigkeit verleiht.
Abbildung 1:Grundlegende Mikrostruktur von Holz.
Dieser Artikel konzentriert sich auf drei Beispiele, die die Eigenschaften von Holz verbessern und seine Verwendungsmöglichkeiten erweitern, nämlich verdichtetes Holz, transparentes Holz und Nanobeschichtung für Holz. Wir werden auch Holz als Quelle für hochwertigen Kohlenstoff mit vorteilhafter Struktur erforschen.
Verdichtetes Holz
Holz ist aufgrund seines hohen spezifischen Moduls, seiner hohen Festigkeit, seiner geringen Kosten und seiner erneuerbaren Natur ein weit verbreitetes Konstruktionsmaterial [1]. Eine breitere Nutzung wird heute jedoch durch die hohe Varianz seiner Eigenschaften behindert [1]. Dies liegt an den vielfältigen Wachstumsbedingungen, denen ein Baum ausgesetzt sein kann (z. B. Bodentyp, Verfügbarkeit von Wasser und Nährstoffen), was zu unterschiedlichen Strukturen und Variationen in der Kornneigung, der Ringbreite und der Häufigkeit von Ästen führt [1][2 ].
Um diese natürlichen Schwankungen zu überwinden, haben Wissenschaftler und Ingenieure Holzwerkstoffprodukte entwickelt, darunter Brettsperrholz und Brettschichtholz (BSH) [1]. Diese haben die Holzeigenschaften stark verbessert und sind zu umweltfreundlichen Alternativen zu Stahl und Beton geworden [2]. Aktuelle Holzwerkstoffprodukte erfordern jedoch große Mengen an Klebstoffen und Metallbefestigungen, die ihre Nachhaltigkeit und Recyclingfähigkeit verringern, insbesondere wenn bestimmte Klebstoffe verwendet werden, da sie giftige Gase (z. B. Formaldehyd und flüchtige organische Verbindungen) abgeben [1].
Infolgedessen konzentrierte sich die Forschung auf eine Vielzahl von Alternativen und insbesondere auf verdichtetes Holz. Hier wird die Dichte des Holzes erhöht:
- Massenverdichtung: Im gesamten Volumen des Holzes [1] [2]
- Oberflächenverdichtung: Nur auf der Deckschicht des Holzes [2]
- Infiltrationsverdichtung: Im gesamten Volumen durch Imprägnierung von Hohlräumen mit geschmolzenen Metallen/Schwefel oder Polymeren [3]
Diese erhöhte Dichte führt zu verbesserten mechanischen Eigenschaften (Tabelle 1) und erweitert die verwendbaren Holzarten, da Holzarten mit geringer Dichte nun zu brauchbaren Konstruktionsmaterialien verarbeitet werden können [1]. Alle drei Methoden sind vielversprechend.
Arten | Zugfestigkeit in Längsrichtung [MPa] | |
---|---|---|
Unkomprimiert | Komprimiert (80 %) | |
Eiche (Quercus) | 115,3 | 584,3 |
Pappel (Populus) | 55,6 | 431,5 |
Western Red Cedar (Thuja plicata) | 46,5 | 550,1 |
Östliche Weymouth-Kiefer (Pinus strobus) | 70.2 | 536,9 |
Bassholz (Tilia) | 52,0 | 587,0 |
Einer der limitierenden Faktoren für die Massenverdichtung sind die Holzzellwände (Lignin), die die Verdichtung behindern und keinen wesentlichen Beitrag zu den Eigenschaften des verdichteten Holzes leisten [3]. Gleichzeitig wird daran geforscht, Holz bis in den Nanobereich aufzuspalten und das delignifizierte Material Nanozellulose zu nutzen, das hervorragende Materialeigenschaften aufweist [3]. Die Forschung hat sich jedoch schwer getan, dies mithilfe des 3D- oder 4D-Drucks zu vergrößern/zusammenzubauen [3].
Eine Teillösung besteht darin, von einem Bottom-up-Ansatz zu einem Top-down-Ansatz zu wechseln, indem Holz vollständig entholzt und verdichtet wird. Effektiv fügt dies dem Verdichtungsprozess einen vorläufigen Schritt hinzu und trägt zur Bildung eines neuartigen Zellulose-Massenmaterials mit verbesserten mechanischen Eigenschaften im Vergleich zu verdichtetem Holz bei (Elastizitätsmodul ≈ 40 GPa und Zugfestigkeit ≈ 270 MPa) [3]. Außerdem kann es leicht zu komplexen Formen geformt werden [3], was weiter entfernte Anwendungen als strukturelle Anwendungen eröffnet und möglicherweise eine neue Art von faserverstärkten Bioverbundwerkstoffen einläutet.
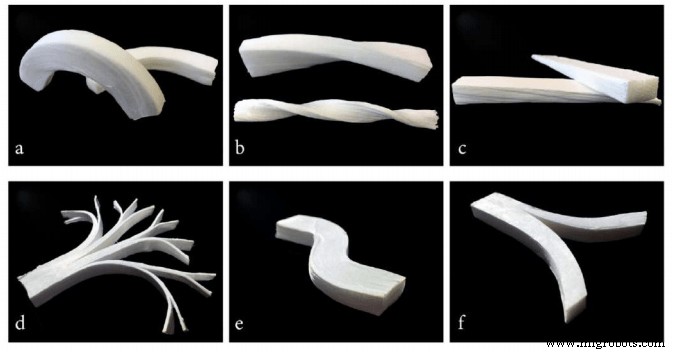
Abbildung 2:Die Zellulose-Schüttgüter lassen sich leicht in eine Vielzahl von geometrischen Formen bringen. [3]
Transparentes Holz
Wie Sie vielleicht bemerkt haben, ist das Holz in Abbildung 2 nahezu durchscheinend. Nun, es stellt sich heraus, dass transparentes Holz derzeit ein Untersuchungsgebiet ist, und der erste Schritt in diesem Prozess ist die Delignifizierung. Darauf folgt die Infiltration mit einem Polymer mit passendem Brechungsindex, wodurch ein nahezu transparentes Holz [4] mit einer gewissen Reststreuung aufgrund einiger Lücken entsteht, die durch das Schrumpfen des Polymers während der Polymerisation entstehen [4]. Da die Polymerinfiltration jedoch eine Form der Verdichtung ist, führt dies zu starkem und transparentem Holz. Die Polymerinfiltration reduziert auch die Anisotropie von Holz um bis zu einem Faktor von fünf [5]. Dies ist darauf zurückzuführen, dass die schwache Querrichtung des Holzes durch das Polymer verbessert wird, wodurch die Biegung der Zellwand, der dominierende Versagensmechanismus in dieser Richtung, unterdrückt wird [5].
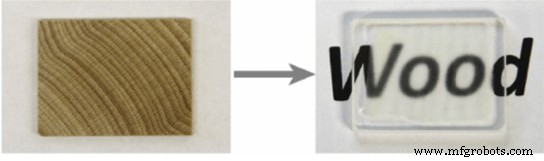
Abbildung 3:Vorher-Nachher-Bilder einer Holzprobe, die Delignifizierung und Polymerinfiltrationen unterzogen wurde.[4]
Abgesehen davon, dass es ein faszinierendes Material ist, hat es eine Vielzahl von Anwendungsmöglichkeiten, darunter transparente Dächer, Fenster und Abdeckungen für Solarmodule. Transparente Dächer, Profile und Fenster können Glas mit ihren überlegenen mechanischen Eigenschaften und Wärmedämmung ersetzen. Der hohe Trübungswert (Maß für die Lichtstreuung) von transparentem Holz bedeutet auch, dass es ein weicheres, diffuseres Licht liefert als herkömmliches Glas. Diese Lichtstreuung macht es auch zu einer sehr effektiven Solarmodulabdeckung, die den Lichtweg in der Solarzelle vergrößert und mehr Zeit für die Energiegewinnung lässt, was zu einer höheren Effizienz führt [4].
Nanobeschichtung für Holz
Hier betrachten wir Fälle, die über die Veränderung der Holzeigenschaften hinausgehen, wo die Beschichtung mit Nanomaterialien dazu beitragen kann, einige der Schwächen von Holz zu überwinden und seine mechanischen Eigenschaften zu verbessern [6]. Zu diesen Schwächen gehören Entflammbarkeit, Lichtabbau und Wasseraufnahme.
Die Nanobeschichtung von Holz kann auf zwei Arten erfolgen:Nanopartikel werden der Beschichtung hinzugefügt, um ihre Eigenschaften vor dem Auftragen zu verbessern, oder Nanopartikel werden direkt auf das Holz aufgebracht [6].
Das zweite Verfahren wurde verwendet, um die Entflammbarkeit von Holz durch Ablagerungen von TiO2/ZnO-Partikeln zu verringern. Sie werden zuerst in einer Lösung mit Ethanol gemischt und dann wird das mit der Lösung bedeckte Holz in einem Autoklaven versiegelt. Dies führt zur Bildung von Nanopartikeln mit Größen im Bereich von 80–200 nm auf der Oberfläche, was die Zeit bis zur Entzündung vervierfacht [7].
Photoabbau ist, wenn absorbierte UV-Strahlung zu Photooxidation führt, was zu einer Oberflächenverfärbung und einer starken Beeinträchtigung der mechanischen Eigenschaften führt. Hier erzeugt das Abscheiden einer ZnO-Schicht eine Nanopartikelschicht, die UV-induzierte Alterung und das Wachstum von Pilzen und mikrobiellen Erregern reduziert. Diese UV-Alterungsbeständigkeit ist darauf zurückzuführen, dass ZnO bevorzugt UV-Strahlung absorbiert und das darunter liegende Holz schützt [8]. Zur Verbesserung der mechanischen Eigenschaften kommt Nanosilica zum Einsatz. Nanosilica-Partikel besitzen eine hohe Härte und thermische Eigenschaften. Sie können reagieren, wenn Sol-Gel-Reaktionen mit Polymeren verwendet werden, um vernetzte Netzwerkstrukturen zu bilden, die auf Hölzern angewendet werden können [6].
Karbonisierte Holzwerkstoffe/Keramik
Diese Anwendung verwendet wohl das älteste synthetische Material, Holzkohle. Holzkohle ist karbonisiertes Zellmaterial, das durch Pyrolyse hergestellt wird. Es wurde bei der Erstellung von Höhlenzeichnungen verwendet [9]. Heutzutage verwenden wir Holzkohle immer noch für eine Vielzahl von Anwendungen, einschließlich Bio-Templates für fortschrittliche Keramik und Verbundwerkstoffe sowie zum Grillen. Das Karbonisieren von Holz ist ein zweistufiger Prozess [9].
- Schritt 1 ist die Zersetzung eines bioorganischen Materials (häufig Holz, aber auch Naturfasern und Papier) in eine Kohlenstoffvorlage.
- Schritt 2 ist die Umwandlung der Kohlenstoffvorlage durch Transformation oder Substitution in Keramik- oder Verbundstrukturen.
Beide Verfahren erfordern Infiltrationen des Kohlenstofftemplats durch ein ausgewähltes Material, da dieses von Natur aus ein poröses Medium ist. Das Material sollte entweder in einem gasförmigen, flüssigen oder nanopartikulären Zustand vorliegen [9].
Die Umwandlung beinhaltet das Mischen des Kohlenstofftemplats mit Si oder Ti in verschiedenen Formen, einschließlich Gas, geschmolzen oder Sol-Gel [ 9][10]. Bei der Substitution wird ein keramisches Oxid als Sol-Gel oder Nanopartikel auf die Schablone aufgebracht und anschließend gesintert [9][10].
Beide dieser Wege können entweder poröse oder dichte Materialien mit einer mikrozellulären Morphologie erzeugen, die auf der des ursprünglichen Holzes basiert [10]. Diese Form der Verarbeitung eröffnet eine Vielzahl von Designoptionen, da die Geometrie des Verbundwerkstoffs jetzt einfach geändert werden kann, indem die Holzschablone in die gewünschte Form gebracht wird – ein weitaus einfacherer Prozess als das Formen oder Bearbeiten des Endprodukts. Es besteht auch die Möglichkeit, die Morphologie der Materialien über die Wahl des Holzes für die Schablone anzupassen. Beispielsweise ergibt Weichholz eine monomodale Porenverteilung, während bestimmte Harthölzer eine multimodale Porenverteilung ergeben [10].
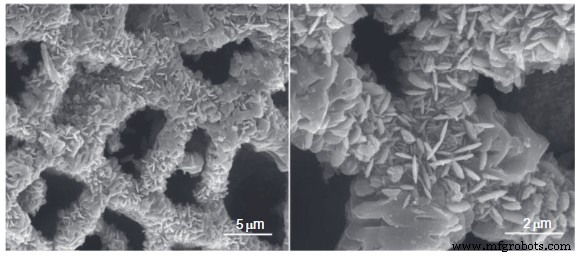
Abbildung 4:SEM-Aufnahme von TiC-Kristallen, die sich auf einem karbonisierten Holzsubstrat gebildet haben. [9]
Diese carbonisierten Holzverbundwerkstoffe müssen noch den Massenmarkt erreichen, werden aber für eine Vielzahl von Anwendungen in Betracht gezogen, bei denen sich ihre hohe Porosität (Filter, Wärmetauscher und Katalysatorträgerstrukturen) und ihre Formbarkeit (Keramikrohre und verschleißfeste Materialien) als vorteilhaft erweisen könnten für viele Anwendungen [9][10][11].
Kohlenstofffasern aus Holz
Kohlenstofffasern (CF) haben ein hervorragendes Verhältnis von Festigkeit zu Gewicht, was sie in Verbindung mit verstärkten Kunststoffen zu äußerst effektiven Leichtbau-Verbundwerkstoffen macht. Aufgrund ihrer relativ hohen Kosten sind sie jedoch hauptsächlich auf High-End-Anwendungen wie Windturbinenblätter, Formel-1-Autos und Luft- und Raumfahrtteile beschränkt. Sie müssen noch weit verbreitet in Automobilanwendungen, im Energiesektor und im Bauwesen eingesetzt werden [12], wo ihre Anwendung zu erheblichen Verbesserungen der Energieeffizienz und Verringerungen der CO2-Emissionen führen könnte. Beispielsweise kann eine Gewichtsreduzierung von 10 % bei einem Auto die Kraftstoffeffizienz um etwa 7 % verbessern [12].
Die hohen Kosten von CF sind darauf zurückzuführen, dass sie überwiegend (>96%) aus fossilbasiertem Polyacrylnitril (PAN) [12][13] hergestellt werden, einem relativ teuren Material. Es wird durch Lösungsspinnen, eine Reihe von thermischen Behandlungen (200-350 ºC) und Karbonisierung (> 1000 ºC) zu Kohlenstofffasern verarbeitet [12]. Um dieses Preisproblem zu überwinden, hat die Forschung versucht, kostengünstige Vorläufermaterialien zu finden, vorzugsweise aus erneuerbaren Quellen, um so die Verwendung fossiler Brennstoffe zu vermeiden.
Zwei Materialien haben sich als brauchbare Kandidaten herausgestellt, Lignin und Zellulose [12][13].
Lignin wird wegen seines hohen Kohlenstoffgehalts verwendet, der eine hohe CF-Ausbeute nach der Umwandlung ermöglicht [12]. Zellulose wird wegen ihrer vorteilhaften Molekularstruktur verwendet, die die Fähigkeit verleiht, CF mit gleichwertigen mechanischen Eigenschaften wie PAN CF zu erzeugen [13]. Beide Materialien leiden jedoch unter Problemen, da die strukturelle Heterogenität von Lignin bedeutet, dass das hergestellte CF schlechtere mechanische Eigenschaften aufweist, und der niedrige Kohlenstoffgehalt von Zellulose bedeutet, dass es eine niedrige Umwandlungsausbeute (10-30 %) hat [12][13].
Wie Sie sehen können, ist der Nachteil des einen der Vorteil des anderen. Daher kombinierten die Forscher diese beiden Materialien unter Verwendung von 70:30-Mischungen aus Weichholz-Kraftlignin und Kraftzellstoff (Zellulose) [12], die durch Trockenstrahl-Nassspinnen in Filamente umgewandelt wurden und dann durch Oxidation und Karbonisierung (1000 ºC) zu CF [ 13].
Eigenschaften | Vorläufermaterialien | |||
---|---|---|---|---|
Standard- und Zwischen-PAN [14][15] | Zellulose [12] | Lignin [12] | 70:30 Lignin-Cellulose-Mischung [12] | |
Zugmodul (GPa) | 200–400 | 500> | 30–60 | 76–77 |
Zugfestigkeit (MPa) | 4000–6000 | 2500> | 400–550 | 1070–1170 |
Ertrag (Gew.-%) | 40-55 | 10–30 | 40-55 | 38-40 |
Aus Tabelle 2 sehen wir, dass diese Mischung die mechanischen Eigenschaften im Vergleich zu Lignin verbessert und die Ausbeute im Vergleich zu Zellulose verbessert. Seine mechanischen Eigenschaften und seine Ausbeute bleiben jedoch niedriger als die von PAN CF. Dies ist kein großes Hindernis, da die vorgesehenen Anwendungen im Energie-, Bau- und Automobilbereich keine Zugfestigkeit von> 3 GPa erfordern, die von CF auf PAN-Basis geboten wird. Daher könnte die Mischung diese Anforderungen angemessen erfüllen.
Bis zur Massenproduktion sind noch einige Probleme zu lösen, wie z. B. dynamische Spannungen während der Herstellung und die Umstellung der Herstellung von Chargen auf kontinuierliche. Von einer kommerziellen Produktion sind wir noch Jahre entfernt [13]. Nichtsdestotrotz könnte Holz der Schlüssel zum Massenmarkt der Kohlefaser sein.
Schlussfolgerung
Hoffentlich hat dieser Artikel gezeigt, dass Holz als strukturelles/funktionelles Material und als Basis für die Verarbeitung zu neuartigen Materialien noch ungenutztes Potenzial hat. Dieser Artikel deckt einen kleinen Teil der aktuellen Fortschritte auf diesem Gebiet ab, und jedes dieser Themen verdient einen eigenen Artikel, einschließlich Hybridholzmaterialien oder Nanofüllstoffe für Holz. Um das ungenutzte Potenzial von Holz weiter hervorzuheben, forscht die Universität Kyoto aktiv daran, einen Holzsatelliten in den Weltraum zu schicken. Dies ist nur der Anfang, um das volle Potenzial von Holz auszuschöpfen.
Industrietechnik
- Holzbearbeitung und Epoxidharz
- Nachdenken über die Fertigung und ihre Zukunft
- Die Kunst und Wissenschaft der Standortauswahl
- Es ist an der Zeit, Ihre S&OP-, Daten- und Planungssysteme zu verbessern
- Wo Supply Chain IoT heute steht und wohin es geht
- Was ist 3D-Druck? – Typen und wie funktioniert er?
- Zustandsbasierte Wartung:was es ist und seine Vorteile
- Smart Manufacturing:was es ist und seine Vorteile
- Verschiedene Arten von Holzoberflächen und Veredelungsprodukten
- Holzarten und ihre Verwendung