Chemische Bearbeitung:Definition, Arbeitsprinzip, Typen, Anwendung, Vorteile [Hinweis &PDF]
Der chemische Bearbeitungsprozess wird auch als Ätzprozess bezeichnet. Dieser Prozess klingt aufgrund seiner einfachen Ausgaben wie Magie.
Dabei tauchen wir das Werkstück einfach in einen Tank mit chemischer Lösung und erhalten in wenigen Sekunden die gewünschte Struktur auf dem Werkstück. Dieser Bearbeitungsprozess ist keine Zauberei, sondern wissenschaftlich praktikabel. Bei diesem Verfahren wird ein stark saures oder alkalisches chemisches Reagenz verwendet, um Material vom Werkstück zu entfernen.
Dies ist ein uralter Prozess vor 400 v. Chr., als organische Chemikalien wie Zitronensäure und Milchsäure verwendet wurden, um Metalle zu ätzen, um die gewünschte Form von Rüstungen herzustellen.
Diese Technik wurde 1927 von einer schwedischen Firma namens „AktiebolagetSeparators“ weiterentwickelt und in den Handel gebracht.
Die chemische Bearbeitung ist ein Prozess der Materialentfernung, um eine gewünschte Form auf dem Werkstück zu erhalten, indem das Werkstück in ein starkes chemisches Reagenz getaucht wird.
Konstruktion oder Teile für die chemische Bearbeitung:
Es besteht aus den folgenden Teilen:
- Panzer
- Heizspirale
- Rührer und
- Werkstück
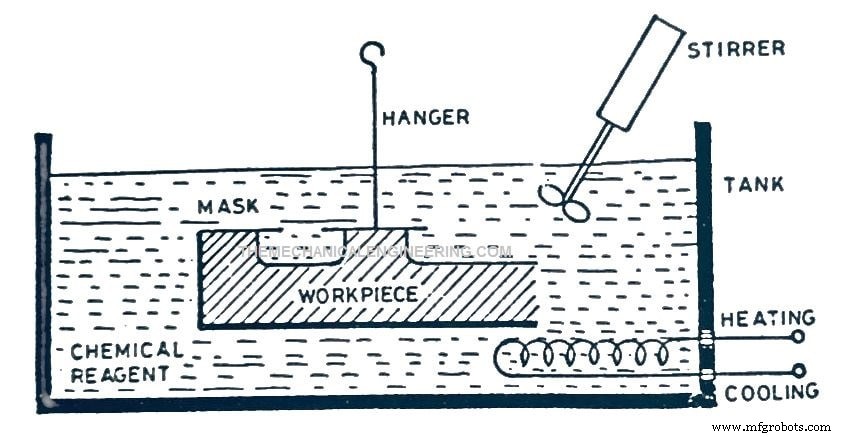
#1. Panzer:
Dieser Prozess hat einen Tank mit offenem Gesicht. Der Tank besteht aus starkem Metall, das mit Materialien beschichtet ist, die je nach Anwendung und Konzentration des chemischen Reagens nicht mit Ätzmitteln reagieren.
#2. Heizschlange:
An der untersten Stelle des Tanks ist eine Heizspirale montiert, um die Temperatur des Tanks auf einem konstanten Niveau zu halten. Praktisch ist, dass bei jedem Metallabtragsprozess die Wärmeentwicklung natürlich ist. Außerdem kühlt die Spule unter den erforderlichen Bedingungen.
#3. Rührer:
Ein Rührer wird in das Ätzmittel eingebracht, dessen Hauptzweck darin besteht, das Ätzmittel gleichmäßig zu mischen, um eine gleichmäßige Konzentration und Erwärmung entlang des Volumens des Ätzmittels aufrechtzuerhalten. Uns ist bekannt, dass sich die heißen Partikel immer oben ansammeln und die Kälte unten zurücklassen.
Um die Wärme gleichmäßig entlang des Ätzmittels zu verteilen, wird der Rührer verwendet. Der Rührer hilft auch dabei, gelöstes Metall aus dem Werkstück zu spülen und gleichzeitig die während der Bearbeitung durch Oxidation gebildeten Blasen aufzubrechen.
#4. Werkstück:
Bei kleinen Anwendungen wird das Werkstück durch einen Aufhänger im Ätzmittel gehalten. Die Länge des Aufhängers wird über einem verdeckten Bereich befestigt, damit die Befestigung des Werkstücks die Bearbeitungszone nicht stört.
Bei größeren Werkstücken werden mit Kautschuken und Polymeren beschichtete Vorrichtungen verwendet, um das Werkstück zu halten.
Arbeitsprinzip des chemischen Bearbeitungsprozesses:
Das Arbeitsprinzip der chemischen Bearbeitung basiert auf einem chemischen Ätzmittel. Ein Ätzmittel ist eine Mischung aus starken chemischen Säuren, die mit Metall reagieren. Wenn das Werkstück in das Ätzmittel getaucht wird, reagiert das Ätzmittel mit dem Werkstück, was eine gleichmäßige Auflösungsrate des Metalls vom Werkstück verursacht.
Um eine gewünschte Form oder Struktur zu erhalten, wird vor der Bearbeitung eine elementare Beschichtung auf das Werkstück aufgetragen, die nicht mit einem chemischen Reagenz namens „Maskant“ reagiert.
Eine lokalisierte Bearbeitung wird erreicht, indem eine geeignete Maske auf alle Bereiche aufgebracht wird, in denen das Ätzmittel nicht reagieren soll. Dadurch wird die Bearbeitungszone für den erforderlichen Metallabtrag freigelegt.
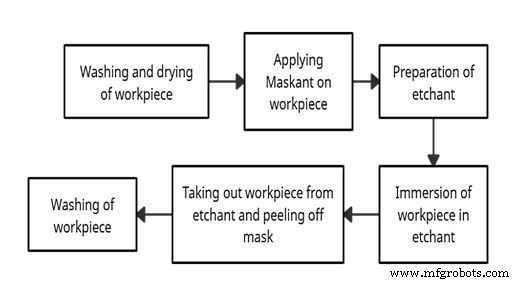
Die chemische Bearbeitung umfasst vier Hauptprozesse, die nacheinander durchgeführt werden:
#1. Reinigung:
Die Reinigung ist ein vorbereitender Prozess, um sicherzustellen, dass die Oberfläche des Werkstücks frei von Verunreinigungen, Rost und Fremdpartikeln ist. Es wird normalerweise durch Hochdruckwasserstrahlen, alkoholische Lösungen und verdünnte HCl durchgeführt.
Reinigungsbedarf :
- Unsachgemäße Reinigung führt zu schlechter Haftung des Maskierungsmittels, ungenauen Endabmessungen und unsachgemäßer Auflösung von Metall.
- Verunreinigungen wie Öl, Fett können zu Oxidation führen.
- Unsachgemäße Reinigung kann zum Ablösen des Maskierungsmittels führen, wodurch Ätzmittel unter die Maske fließen kann, wodurch die Geometrie beschädigt wird.
- Fremdpartikel können zu Kalkbildung führen.
Nach dem Waschen des Werkstücks wird das Werkstück unter Heißluftgebläsen getrocknet. Der Reinigungsprozess wird immer in fortschrittlichen CNC-Maschinen durchgeführt.
#2. Maskierung:
Es ist ein Prozess zum Auftragen von Maskierungsmittel auf die Oberfläche des Werkstücks. Das Werkstück wird mit einer Polymer- oder Gummischicht beschichtet.
Das Maskieren wird durchgeführt, um den Bereich, der keine maschinelle Bearbeitung erfordert, vor dem Ätzprozess zu schützen. Das Abdecken erfolgt über das gesamte Werkstück mit Ausnahme der zu bearbeitenden Bereiche.
#3. Radierung:
Dies ist der Prozess, bei dem der erforderliche Metallabtrag stattfindet. Nach perfekter Maskierung wird das Werkstück bei eingeschalteter Heizung und eingeschaltetem Rührer in den Tank mit dem chemischen Reagenz getaucht.
Sobald das Werkstück eingetaucht wird, beginnt das Ätzmittel mit den nicht maskierten Bereichen des Werkstücks zu reagieren. Die hochkonzentrierte Säure beginnt mit dem Werkstück zu reagieren und verändert dessen chemische Eigenschaften.
Durch diese Reaktion schmelzen die vordefinierten Portionen und lösen sich Schicht für Schicht vom Werkstück.
Bei diesem Verfahren ist die Schnittiefe direkt parallel zur Eintauchzeit des Werkstücks. Je länger sich das Werkstück im Ätzmittel befindet, desto mehr Metall wird entfernt. Je weniger Zeit, desto geringer die Schnitttiefe. Dies wird durch die Formel berechnet.
E=S/T
Wo,
- E =Ätzrate.
- S =erforderliche Schnitttiefe.
- T =Zeit in Sekunden.
Die Werte der Ätzrate werden durch Experimente vorberechnet. Die Ätzrate hängt von der Konzentration des chemischen Reagens und der Art des zu bearbeitenden Werkstücks ab.
Die Schnitttiefe ergibt sich aus der Konstruktion. Somit kann die Zeit bis zum Eintauchen des Werkstücks in das Ätzmittel leicht berechnet werden.
#4. Demaskierung:
Demaskieren ist ein Prozess des Ablösens des Maskierungsmittels, das vor dem Ätzprozess aufgetragen wurde. Sobald das Maskierungsmittel von dem Werkstück entfernt ist, wird das Werkstück erneut einem Reinigungsvorgang zugeführt, wo jegliches übrig gebliebene Ätzmittel durch unter Druck stehendes kaltes Wasser weggewaschen wird. Das Werkstück ist dann getrocknet und bereit für den endgültigen Versand.
Arten der chemischen Bearbeitung:
1. Chemisches Mahlen (CHM):Diese Operation wird durchgeführt, um Taschen, Konturen auf dem Werkstück zu erhalten oder um Schüttgut vom Werkstück zu entfernen.
2. Chemische Gravur (CHE):Dieser Vorgang wird durchgeführt, um ein spezielles Design auf einem Werkstück mit hoher Präzision zu reproduzieren. B. Titel, Markennamen, Seriennummern usw.
3. Chemisches Polieren (CHP):Dieser Vorgang wird durchgeführt, um eine Feinbearbeitung oder Entgratung des Werkstücks vorzunehmen. Dies ist durch die Verwendung von leichter verdünnten chemischen Reagenzien möglich.
4. Fotochemische Bearbeitung (PCM):Photochemische Metallbearbeitung ist ein Verfahren zur Herstellung von spannungs- und rissfreien Bauteilen. PCM wird dort eingesetzt, wo Mikrodetails auf einem Werkstück bearbeitet werden sollen.
Dieser Prozess verwendet die chemische Bearbeitung (CHM) als primäre Technik, um Material und eine photoresistive Maske für Designzwecke zu entfernen. PCM ist ein fortschrittlicher Bearbeitungsprozess, dessen Ursprung in der chemischen Bearbeitung liegt.
Chemische Bearbeitungsanwendungen:
Die folgende Anwendung enthält:
- Gewichtsreduzierung bei komplexen Konturen, die mit herkömmlichen Methoden nicht möglich sind.
- Bearbeitung dünner und empfindlicher Bauteile.
- Wird verwendet, um die Konturen innerhalb eines Lochs zu bearbeiten.
- Verwendet in der Automobil- und Luftfahrtindustrie.
- Herstellung von feinen Sieben und Maschen.
- Entfernen von Metall, wo das Halten eines Werkstücks schwierig ist.
Vorteile der chemischen Bearbeitung:
Die folgenden Vorteile umfassen:
- Dieser Bearbeitungsprozess entfernt Metall gleichmäßig.
- Gute Oberflächengüte mit engen Toleranzen.
- Komplexe Konturen können einfach bearbeitet werden.
- Materialabtrag entlang aller Achsen gleichzeitig.
- Ein weniger erfahrener Bediener ist erforderlich.
- Am Werkstück entsteht keine mechanische Spannung.
- Niedrige Anschaffungskosten.
- Niedrige Bearbeitungskosten.
Chemische Bearbeitungsnachteile:
Zu den folgenden Nachteilen gehören:
- Geringere Sicherheit des Bedieners, ein geringfügiges Verschütten von Ätzmittel auf der Haut kann dem Bediener Schaden zufügen.
- Korrosionsgefahr nach Tagen der maschinellen Bearbeitung.
- Die maschinelle Bearbeitung von Legierungen kann zu einer schlechten Oberflächengüte führen.
- Der Prozess ist nicht umweltfreundlich.
- Die Entsorgung von Nebenprodukten kann zu Umweltschäden führen.
- Die Materialabtragungsrate (MRR) ist im Vergleich zu anderen Bearbeitungsverfahren geringer.
- Mögliche Blasenbildung, die zu einer unsachgemäßen Bearbeitung führen kann.
Wichtige Parameter:
Maskant: Maskantcan ist als ein Material definiert, das zum Beschichten des Werkstücks verwendet wird, um zu verhindern, dass der Teil des Werkstücks geätzt wird.
Bei der Auswahl des Maskierungsmitteltyps zu berücksichtigende Faktoren:
- Es sollte gegenüber dem verwendeten chemischen Reagens inert sein.
- Widerstandsfähig.
- Es sollte seine Eigenschaften während des Bearbeitungsprozesses nicht verändern.
- Hält auch Hitze aus.
- Es sollte sich zum Schneiden und Schreiben eignen.
- Es sollte gut am Werkstück haften.
- Verfügbarkeit und geringe Kosten.
Werkstückmaterial | Maskierungsmaterial |
Aluminium und seine Legierungen | Butylkautschuk, Polymer und Neopren |
Kupfer und seine Legierungen | Polymer |
Legierungen auf Eisenbasis | Butylkautschuk und Polymer |
Nickel | Neopren |
Magnesium | Polymer |
Titan | Polymer |
Chemical Machining Maskant-Technik:
Es gibt drei Haupttechniken zum Auftragen von Maskierungsmittel auf ein Werkstück.
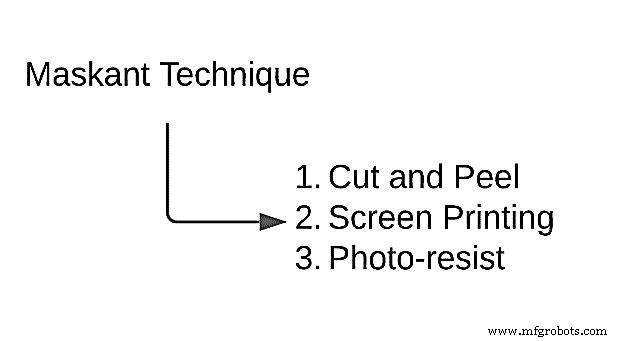
1. Schneiden und schälen:
Bei dieser Abdecktechnik wird das zu bearbeitende Werkstück zunächst in einen Tank mit flüssigem Abdeckmittel getaucht, ähnlich wie beim Beschichten.
Sobald das gesamte Werkstück beschichtet ist, wird das Werkstück herausgenommen und einige Minuten trocknen gelassen. Dann wird eine Anreißnadel verwendet, um die auf das Werkstück aufgebrachte Maskierungsmittelschicht zu schneiden.
Die Schnitte werden genau nach dem zu bearbeitenden Design ausgeführt. Sobald der Schneidvorgang abgeschlossen ist, wird das Maskierungsmittel von den zu ätzenden Bereichen entfernt. So funktioniert die Cut-and-Peel-Masking-Technik.
Diese Maskierungstechnik beinhaltet die Verwendung von relativ dicken Materialien wie Neopren, Butyl und Materialien auf Vinylbasis. Diese Technik wird ausschließlich für Chemical Milling Operations (CHM) eingesetzt.
Im Laufe der Zeit hat diese Technik die Produktion von Raketen, Flugzeugen und deren Strukturteilen erleichtert. Aufgrund der inerten Natur des Maskierungsmittels und der bei diesem Verfahren beteiligten Dicke von etwa 0,5 Zoll oder mehr bietet diese Technik Zugang zu einer extrem hohen chemischen Beständigkeit. Die Hauptverhandlung bei dieser Technik ist nur, dass diese Technik eine relativ geringe Qualitätstoleranz hat.
Materialien, die bei der Schnitt- und Schälmaskierungstechnik verwendet werden, sind Vinyl, Neoprenkautschuk, Materialien auf Butylbasis, Bienenwachs, Burgunderpech, das durch Fließen oder Tauchen oder durch Sprühbeschichtung aufgetragen wird. Die Dicke dieser Maskierungsmittel reicht von 0,03 bis 0,13 mm.
2. Siebdruck:
Diese Technik nutzt die herkömmliche Siebdrucktechnologie. Bei dieser Maskenanwendung werden feinmaschige Seiden- oder Edelstahlsiebe auf das Werkstück aufgebracht.
Ähnlich wie beim Drucken von Radium auf ein breites Blatt wird hier bei dieser Technik ein ganzes Design auf einen Siebdruck und SS-Netze gedruckt. Das Netz wird dann gegen die Oberfläche des Werkstücks gedrückt. Damit ist die Markierung der zu bearbeitenden Bereiche abgeschlossen.
Dann wird eine Maskierungsmittelschicht auf das gesamte Werkstück gerollt. Das Anhaften des Maskierungsmittels auf dem Werkstück wird durch Trocknen und Backen erreicht. Sobald das Maskierungsmittel auf dem Werkstück haftet, werden die installierten Maschen von dem Werkstück entfernt, was zum Entfernen der Maske von den zu bearbeitenden Bereichen führt.
Der Siebdruck ist eine schnelle und kostengünstige Abdecktechnik für Großserien. Diese Technik ermöglicht auch den Zugang zu einem höheren Genauigkeitsgrad.
Die Maskendicke ist immer kleiner als 0,05 mm. Diese Maskierungstechnik eignet sich am besten für Teile mit einer Größe von weniger als 1,2 m × 1,2 m mit flachen Oberflächen und moderaten Konturen.
3. Photoresist:
Die Photoresist-Maskierungstechnik wird nur in dem photochemischen Bearbeitungsverfahren ausgeübt. Diese Technik ist in dieser autonomen Ära so vielseitig.
Die Verwendung der Photoresist-Maskierungstechnik schaltet den Prozess der chemischen Bearbeitung in einen anderen nicht-traditionellen Bearbeitungsprozess um, d. h. den Prozess der photochemischen Bearbeitung (PCM).
Bei dieser Technik wird ein Bild des Endproduktdesigns auf einen Film aus lichtempfindlichem Material gedruckt. Der Film hat die Eigenschaft, ultraviolette Lichtstrahlen anzuziehen und zu reflektieren.
Die bedruckte Folie wird sorgfältig und genau auf das zu bearbeitende Blech (Werkstück) gelegt und anschließend durch eine UV-Maschine geführt.
Zwischen IN und OUT des Werkstücks lässt aufgrund der Eigenschaft der Folie, das UV-Licht passieren zu lassen und zu reflektieren, nur die vorgedruckte Zone oder Markierungen auf der Folie das UV-Licht durch die Folie zum Werkstück.
Diese UV-Belichtung des Werkstücks glättet die bestimmten Teile, die für die chemische Bearbeitung vorkonstruiert wurden. Der Rest des Prozesses wird im photochemischen Bearbeitungsprozess durchgeführt.
Das bei dieser Technik verwendete Material hat kaum eine Dicke zwischen 1,27 mm und 1,5 mm. Diese Technik wird häufig bei der Herstellung von Leiterplatten, Halbleitern, elektronischen Chips, metallischen Computerkomponenten, kleinen Zahnrädern für Uhren usw. verwendet.
Ätzmittel:
Das Ätzmittel kann als eine Mischung aus verdünnten oder konzentrierten chemischen Säuren definiert werden, die mit Metall reagieren und es auflösen können.
Werkstückmaterial | Ätzmittel | Betriebstemp. ( o C) | Ätzrate (mm/min × 10 3 ) |
Aluminium und seine Legierungen | Na (OH) | 49 | 20-30 |
FeCl3 | 49 | 13-25 | 13-25 |
Messing oder Bronze | NH4 HF2 | 27 | 10-15 |
FeCl3 | 49 | 25 | 25 |
Lead | FeCl3 | 54 | |
Magnesiumlegierung | HNO3 | 32-49 | 25-50 |
Nickel | FeCl3 | 49 | 13-38 |
Titan | HNO3 HF | Umgebung | 13-25 |
Industrietechnik
- Honprozess:Definition, Teile oder Konstruktion, Arbeitsprinzip, Vorteile, Anwendung [Notizen mit PDF]
- Läppprozess:Definition, Wirkungsweise, Typen, Material, Vorteile, Anwendung [Notizen mit PDF]
- Quick-Return-Mechanismus:Definition, Typen, Funktionsprinzip, Anwendungen, Vorteile, Nachteile [Notizen mit PDF]
- Extrusionsprozess:Definition, Arbeitsprinzip, Typen, Anwendungen, Vor- und Nachteile [Notizen mit PDF]
- Was ist chemische Bearbeitung? - Arbeiten und Verfahren
- Reibschweißen:Prinzip, Arbeitsweise, Typen, Anwendung, Vor- und Nachteile
- Schleuderguss:Arbeitsprinzip, Typen, Anwendung, Vor- und Nachteile
- Extrusionsprozess:Arbeitsweise, Typen, Anwendung, Vor- und Nachteile
- Schleifstrahlbearbeitung – Teile, Arbeitsprinzip, Anwendung
- Ultraschallbearbeitungsprozess, Arbeitsprinzipien und Vorteile