Schneiden in die Tiefe und Enge
Die OSG EXOCARB® WXS®-Schaftfräserserie bietet eine zuverlässige Alternative für die Bearbeitung tiefer Kavitäten
Magnus Hoyer, OSG Deutschland
Eine Reihe von Herausforderungen, wie z. B. schlechte Spanabfuhr, Vibration, Rattern, Werkzeuginstabilität und schlechte Werkzeuglebensdauer, sind häufig mit der Bearbeitung tiefer Kavitäten verbunden. Bei tiefen Anwendungen werden die Seitenwände des Werkstücks zu Hindernissen für eine ordnungsgemäße Spanabfuhr. Die Spanabfuhr würde sich nur verschlechtern, je tiefer ein Fräser in ein Teil vordringt. Darüber hinaus können Werkzeughalter und Adapter aufgrund der hohen Kontur und der schmalen Stegumgebung mit dem Werkstück kollidieren. Bei Standard-Schneidwerkzeugen greifen die Schneiden vollständig in das Werkstück ein, was zu seitlichen Schnittkräften führt, die Vibrationen, Rattern und damit Werkzeugversagen auslösen können. Elektroerosionsbearbeitung (EDM) wird häufig als Alternative zur Bearbeitung tiefer Kavitäten verwendet, ist jedoch sehr zeitaufwändig und kostspielig.
Die Meissner AG, ein deutscher Hersteller von Prototypen, Produktionswerkzeugen und Formen, stand vor einer solchen Herausforderung bei der Produktion von Wassermantel-Kernwerkzeugen, die die Bearbeitung enger Taschen, schmaler Stege und hoher Konturen erfordern. Als Hersteller, der immer auf dem neuesten Stand der Produktionsanlagen und -technologien ist, hat Meissner festgestellt, dass selbst mit dem Einsatz der 5-Achs-Bearbeitung für diese Art von Arbeiten keine optimale Leistung erzielt werden kann.
Meissner wurde 1922 gegründet und hat seinen Hauptsitz in Biedenkopf-Wallau, Deutschland. Das Unternehmen bietet Dienstleistungen an, darunter die Entwicklung, Konstruktion und Herstellung von Prototypen sowie Produktionswerkzeugen und -formen für Kunden auf der ganzen Welt. Produktwerkzeuge können Werkzeuge zum Gießen von Motorblöcken, Zylinderköpfen, Autofelgenteilen aus verschiedenen Materialien, Blasformen für Kraftstofftanks und Einfüllrohre und mehr umfassen.
Meissner beschäftigt insgesamt 340 Mitarbeiter, davon etwa 50 Ingenieure. Meissner legt großen Wert auf hervorragende Produkte, Zuverlässigkeit und kontinuierliche Innovation. Meissner setzt moderne Geräte und Technologien mit praktisch allen CAD-Systemen der Automobilindustrie und einem CAD-basierten Datenmanagement ein, um eine effektive und effiziente Kommunikation mit seinen Kunden zu ermöglichen.
Meissner führt als eines der ersten Unternehmen in Deutschland die 5-Achs-Bearbeitung ein. Die Reduzierung der Zykluszeit und die Erhöhung der Präzision sind zwei große Vorteile von 5-Achs-CNC-Bearbeitungszentren. Produktingenieure bei Meissner stellen jedoch immer häufiger fest, dass es bei bestimmten Bauteilen nicht immer sinnvoll ist, auf eine 5-Achs-Bearbeitung zu setzen.
Dass das Potenzial eines 5-Achs-Bearbeitungszentrums nicht voll ausgeschöpft werden kann, zeigt sich laut Christoph Schwarz, Gruppenleiter Mechanische Fertigung bei Meissner, besonders bei der Bearbeitung von Wassermantel-Kernwerkzeugen.
„Mit diesen Werkzeugen haben wir enge Bereiche, enge Taschen, schmale Stege und hohe Konturen“, sagt Schwarz. „Den Schwenkbewegungen von Maschinen sind Grenzen gesetzt, was die Geschwindigkeiten und Vorschübe reduziert.“
Die Rotationsbewegungen belasten laut Schwarz auch die Werkzeuge stärker. Je nach Geometrie des Werkstücks ist ein 5-Achs-Bearbeitungszentrum also nicht immer sinnvoll. Meissner hat auch Werkstücke mit tiefen Kavitäten mit EDM bearbeitet, aber es ist zeitaufwändig und kostspielig.
„Mit der richtigen Werkzeugausstattung haben unsere Vergleiche gezeigt, dass wir bei bestimmten Werkstücken mit einem 3-Achs-Bearbeitungszentrum viel schneller sind“, so Schwarz.
Tiefe und enge Kavitäten erfordern meist sehr lange und dünne Werkzeuge. Die Durchbiegung des Werkzeugs ist ein häufiges Problem bei der Bearbeitung. Aus diesem Grund suchte Meissner nach einer Alternative, da weder 5-achsig schräg gefräst noch auf Erodieren gesetzt werden wollte.
Mit den 2-schneidigen Torus- und Kugelfräsern von OSG scheint vor allem für das Konturschruppen und -schlichten von Kernwerkzeugen für Wassermäntel eine Lösung gefunden. Die Idee, die Torus- und Kugelfräser von OSG in Verbindung mit einem 3-Achs-Bearbeitungszentrum einzusetzen, entstand Anfang des Jahres aus einem anderen Projekt. Die Torus- und Kugelfräser aus der WXS®-Serie von OSG wurden aus vielen Gründen ausgewählt, erklärt Schwarz.
„Zunächst war es die positive Erfahrung. Bei Anfragen zeigte sich OSG stets bereit, die Lieferzeiten waren kurz und die Beratung kompetent“, so Schwarz. „Noch wichtiger war jedoch das mit diesen Schneidwerkzeugen erzielte Ergebnis.“
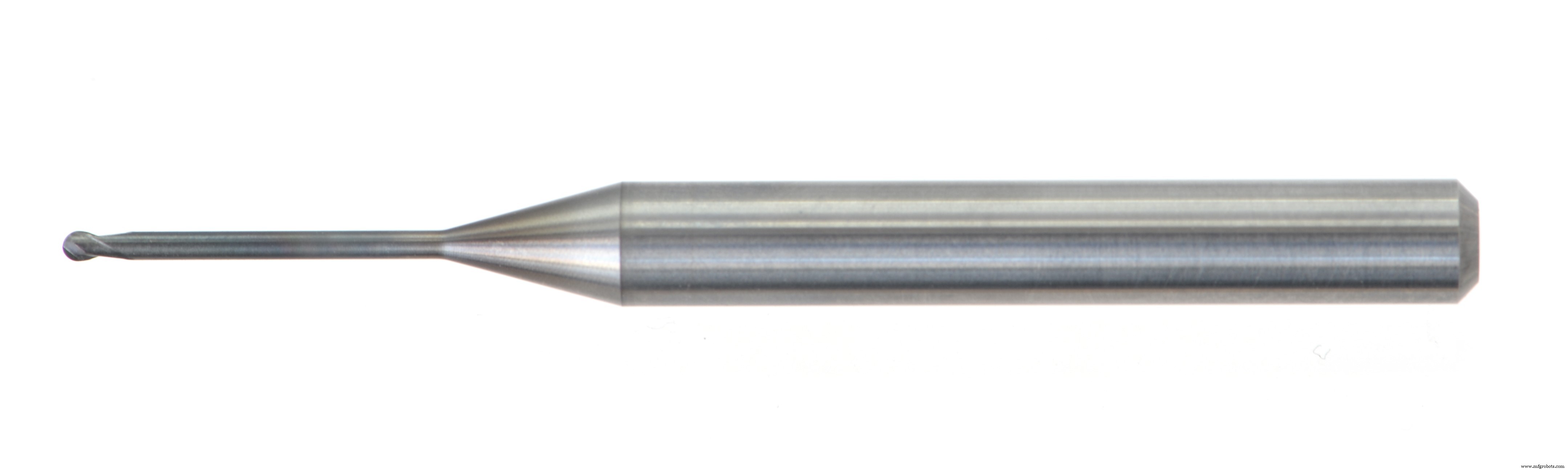
Während die Fräser der WXS®- und WXS-C-Serie aus der OSG-Zentrale in Japan stammen, werden Werkzeuge der EPL-Serie am deutschen Standort von OSG in Göppingen gefertigt. Die WXS®-Schaftfräserserie ist mit einer superharten Beschichtung mit Nanotechnologie für hohe Hitzebeständigkeit ausgestattet. Es wurde entwickelt, um in Arbeitsmaterialien über 50 HRC zu glänzen. Die OSG Original WXL®-Beschichtung hat eine Oxidationstemperatur von 1.300 °C, um höhere Spindeldrehzahlen und längere Standzeiten zu ermöglichen, selbst bei Hochgeschwindigkeits- oder Trockenbearbeitung. Seine einzigartige Werkzeuggeometrie ermöglicht hochwertiges und hochpräzises Fräsen auch unter schwierigen Bearbeitungsbedingungen. Neben dem WXS®-Schaftfräser ist der WXS-CRE ein 5-schneidiger Hochleistungs-Hartmetall-Schaftfräser mit Superradius, der für Materialien bis 65 HRC ausgelegt ist. Last but not least ist der EPL eine zweischneidige Hochleistungs-Schaftfräserserie mit langem Hals und Kugelkopf, die entwickelt wurde, um in Materialien mit 45 HRC und bis zu 60 HRC zu glänzen.
Am Wassermantel-Kernwerkzeug mit tiefen Kavitäten wurden Bearbeitungsversuche mittels 3-Achs-Fräsen durchgeführt. Unter identischen Bedingungen wurden Werkzeuge verschiedener Hersteller getestet. Laut Matthias Bassler, Bereichsleiter Produktion bei Meissner, fiel die Entscheidung zugunsten von OSG.
„Wir schauen nicht auf die letzte Sekunde, aber Zeit ist auch ein wichtiger Faktor für uns“, sagte Bassler.
„Wir haben sehr viele, sehr zeitaufwändige Veredelungsoperationen. Qualität, Standzeit und Prozesssicherheit sind dabei von enormer Bedeutung. Eventuell notwendige Nacharbeiten – aus welchen Gründen auch immer – würden sich enorm auf die Kosten auswirken. Unsere Tests haben gezeigt, dass wir bei diesem Material beim Einsatz von Werkzeugen anderer Hersteller einen zusätzlichen Arbeitsgang durchlaufen mussten. Bei OSG hingegen lief alles gut“, sagte Bassler.
Neben der Produktivität hat Meissner auch strenge Anforderungen an die Maßhaltigkeit sowie die Oberflächengüte. Kernwerkzeuge sind mit einer optimalen Bearbeitungsallianz von 0,3 mm vorgefertigt. Nach der Endbearbeitung müssen die Toleranzen auf allen Ebenen innerhalb des vorgegebenen Toleranzbereichs von 0,03 mm liegen. Solche Ergebnisse erfordern natürlich eine entsprechende Programmierung.
„Um die Arbeit richtig zu machen, muss zunächst die Werkzeugreihenfolge festgelegt werden“, sagt Christoph Rothenpieler, CAM-Programmierer bei Meissner.
„Die Werkzeuge zum Schruppen und Vorschlichten sollten so gewählt werden, dass später beim Schlichten möglichst wenig Durchbiegung auftritt. Nur so kann eine optimale Kontur vorbereitet werden“, ergänzt Rothenpieler.
Die Voraussetzungen für das Erreichen dieser Präzision hängen stark vom Bearbeitungszentrum und den Zerspanungswerkzeugen ab. Hier liefern Bearbeitungszentren von Hermle die besten Ergebnisse. 80 Prozent der Finishing-Arbeiten werden auf diesen Maschinen ausgeführt. OSG Sales Manager Uli Blöcher weiß, worauf es bei Zerspanungswerkzeugen wirklich ankommt.
„Die Unterschiede zwischen den Werkzeugen werden in erster Linie durch die Wahl des Hartmetalls, die Geometrie der Schneiden, die Steifigkeit der Kegel und vor allem durch das Substrat oder die Arbeitsweise des Werkzeugs an den Schneiden bestimmt“, sagt Blöcher.
Die EXOCARB® WXS®-Serie von OSG bietet einzigartige Schneidwerkzeuggeometrien, die darauf ausgelegt sind, schnellere Zykluszeiten bei tiefen Anwendungen zu ermöglichen. Die Spiralschnitt-Technologie der Schneidgeometrie trägt dazu bei, Vibrationen und Rattern zu minimieren, wodurch ein stabiles Konturfräsen ermöglicht wird.
Schauen Sie sich dieses kurze Video an, um einen Vergleich der Wärmeentwicklung zwischen OSGs EXOCARB® WXS® und einem Mitbewerber-Schaftfräser aus D2-Werkzeugstahl zu sehen:
Meissners Suche nach einer alternativen Bearbeitungslösung hat es ihnen ermöglicht, eine Reihe von 3-Achsen-Bearbeitungszentren wiederzubeleben, während ihre 5-Achsen-Bearbeitungszentren mit anderen Jobs in voller Produktion laufen können.
Mit den richtigen Werkzeugen kann ein 3-Achsen-Bearbeitungszentrum ein 5-Achsen-Bearbeitungszentrum übertreffen, um die Rentabilität zu maximieren. Die Werkzeuge von OSG zeigen, dass das Schneiden von tiefem und schmalem Material auf einer 3-Achse mit minimalem Rattern, Zykluszeit und Rüstzeit möglich ist, während gleichzeitig die Abtragsrate und die Standzeit des Werkzeugs erhöht werden. Manchmal kann das Hinterfragen einer etablierten Methode der erste Schritt zum Fortschritt sein.
Zuvor im SHAPE IT Magazine vorgestellt.
Industrietechnik
- Die Hauptunterschiede zwischen 3-Achsen- und 5-Achsen-Bearbeitung
- Fertigung maschinell bearbeiteter Teile:Was sind die Vorteile der Hochgeschwindigkeitsbearbeitung?
- NADCAP-Zertifizierung und ihre Anwendung auf die Präzisionsbearbeitungsindustrie
- Bearbeitung, Disruption und die kommenden Jahre
- Edelstahl:Die besten Produkte zum Schneiden, Schleifen und Finishen
- Schneiden von Titan und HRSA-Metallen:Bearbeitbarkeit, Kühlmittel und mehr
- Wie wählt man den richtigen Fräser und die richtige Programmierung für CNC aus?
- Drehzentrum und die dazugehörige Bearbeitung
- Die Drehmaschinenbearbeitung ist vielseitig und weit verbreitet
- Konventionelle und nicht konventionelle Arten von Bearbeitungsprozessen